Российские нанотехнологии, 2020, T. 15, № 3, стр. 344-351
ПОЛУЧЕНИЕ ВОДОРОДА ВЫСОКОТЕМПЕРАТУРНЫМ ЭЛЕКТРОЛИЗОМ ВОДЫ
Г. Н. Волощенко *
Национальный исследовательский центр “Курчатовский институт”
Москва, Россия
* E-mail: geornik1@yandex.ru
Поступила в редакцию 09.06.2020
После доработки 09.06.2020
Принята к публикации 29.06.2020
Аннотация
Рассмотрен вопрос высокотемпературного электролиза для получения водорода с помощью электроэнергии и высокопотенциального тепла. Приведены расчетные данные эффективности такого производства и характеристик рассматриваемых устройств, особенности их использования, а также вариант конструкции электролизера для данной области применения, обеспечивающие оптимальные условия для функционирования электрохимических модулей с наноструктурными электролитом и катализаторами электродов.
ВВЕДЕНИЕ
Высокотемпературные электрохимические устройства, электролизеры и топливные элементы длительное время разрабатываются во всем мире и уже находят свое практическое применение [1]. Причем высокотемпературный электролиз рассматривается как перспективный и эффективный способ производства водорода [2, 3].
Высокотемпературным твердооксидным электролизом воды для получения водорода в рамках атомно-водородной энергетики Институт атомной энергетики им. И.В. Курчатова начал заниматься с начала 80-х годов прошлого века. Тогда же были разработаны основные подходы к анализу электрохимических и тепломассообменных процессов, характерных для высокотемпературных устройств. Основные особенности этих процессов в отличие от низкотемпературных определяются тем, что электролиз происходит в газовой фазе, следовательно, с одной стороны, образуется смесь водяного пара с водородом, с другой стороны, теплоемкость газовых реагентов мала по сравнению с жидкостью и не может обеспечивать термостабилизацию электролизера. С учетом этих факторов в настоящей работе представлена методика расчета и моделирования высокотемпературных устройств, позволяющая также разрабатывать высокотемпературные электролизеры для производства водорода.
ФОРМУЛИРОВКА ЗАДАЧИ
Исследованием и разработкой, в том числе моделированием, высокотемпературных электрохимических устройств занимаются многие исследователи [4–10]. Однако получаемые результаты показывают, что некоторые особенности высокотемпературных устройств не учитываются, что приводит, в частности, к большим перепадам температур внутри топливных элементов, достигающим сотни и больше градусов, что нельзя считать допустимым [11, 12]. В этом плане разработанные нами аналитические подходы и конструкторские решения являются оправданными, так как позволяют обеспечить минимальный градиент температуры как в топливном элементе, так и в электролизере.
В основу расчетов и последующего моделирования положены такие известные электрохимические закономерности, сформулированные для условий работы высокотемпературных устройств с учетом распределенного электрохимического процесса, как уравнение Нернста для расчета локальной электродвижущей силы (ЭДС) реакции, закон Ома для расчета локальной плотности тока электролиза, закон Фарадея для расчета изменения расхода реагента, закон сохранения энергии для расчета локального теплового потока электролизера, уравнение теплоемкости для расчета изменения локальной температуры реагентов.
Подробно разработанные нами подходы анализа работы высокотемпературных твердооксидных устройств изложены в [13–20].
Основным преимуществом высокотемпературного электролиза является возможность его работы в режиме поглощения тепла, что снижает расход электроэнергии.
В настоящей работе проанализируем характеристики установки на основе высокотемпературного твердооксидного электролизера (ВТЭ) для крупномасштабного производства водорода. В качестве источника электрической и тепловой энергии для удобства расчета используем высокотемпературный газовый реактор с температурой теплоносителя 950°С. Схема циркуляции теплоносителя представлена на рис. 1.
Теплоноситель поступает в электролизер и отдает некоторую часть тепла, после чего подается в турбомашинный цикл (ТМЦ), где производится электроэнергия, необходимая для электролиза. После ТМЦ теплоноситель подается в низкотемпературную часть ВТЭ, где нагревает и испаряет воду, необходимую для электролиза.
Высокотемпературный электролизер, схема которого представлена на рис. 2, состоит из электролизных модулей, собранных в секции, последовательно размещенные внутри корпуса. Между секциями расположены промежуточные теплообменники, по которым циркулирует теплоноситель, предназначенные для подогрева внешнего реагента с целью поддержания температурного режима на уровне 900°С. Внешним реагентом, омывающим модули с внешней стороны, является смесь водяного пара и водорода. В процессе прохождения секций от входа электролизера к выходу за счет электролиза содержание водорода в смеси увеличивается, а водяного пара уменьшается. Внутренним реагентом, проходящим внутри модулей, является выделяющийся кислород, а также его смесь с воздухом при использовании последнего для снижения ЭДС-реакции электролиза.
Для рекуперации тепла реагентов используются теплообменники-рекуператоры внешнего и внутреннего реагентов. Поскольку рекуператоры не могут догреть входящие реагенты до рабочей температуры ВТЭ, используются догреватели внешнего и внутреннего реагентов за счет тепла теплоносителя. Рекуперативный теплообменник внешнего реагента соединен с низкотемпературной частью электролизной установки, обеспечивающей, с одной стороны, водоподготовку, нагрев и испарение воды, поступающей в виде пара на вход теплообменника-рекуператора, а с другой стороны, конденсацию воды из смеси с водородом и его дальнейшую утилизацию. Водяной пар, проходя теплообменник-рекуператор, нагревается за счет тепла смеси водорода и водяного пара после электролиза до температуры меньше рабочей примерно на 50°С. Догрев пара до рабочей температуры происходит в зоне догрева за счет тепла теплоносителя от реактора. Аналогично проходит процесс термостатирования с внутренним реагентом.
Конструкция высокотемпературного электрохимического устройства защищена авторским свидетельством СССР [21] и патентом на полезную модель РФ [22].
На рис. 3–5 представлены схемы электролизных секций трубчатого и планарного типа и схема секции с рекуперативным теплообменником и зоной догрева внутреннего реагента. Разработанная авторами конструкция позволяет обеспечить стабильный температурный баланс, а также высокую надежность устройства за счет простой замены секций, в случае необходимости, в процессе работы электролизера.
Для определения характеристик и оценки эффективности применения высокотемпературного электролиза для крупномасштабного производства водорода на основе публикаций [23–26] разработана математическая модель водородпроизводящей установки, составлена программа и проведены расчеты параметров установки.
Высокотемпературный газовый реактор обеспечивает работу электролизной установки подводом тепла и электроэнергии, производимой в ТМЦ с КПД 40%. Общий расход тепла реактора состоит в общем случае из расхода на нагрев и испарение воды, догрев водяного пара и воздуха до рабочей температуры, тепла на электролиз в виде подогрева внешнего реагента в промежуточных теплообменниках и выработку электроэнергии в ТМЦ с КПД 40%. Если весь расход тепла реактора направить на выработку электроэнергии, то получим эквивалентную электрическую мощность на выработку водорода и сможем определить эквивалентный удельный расход электроэнергии WудЭкв, определяющий в отличие от удельного расхода только электроэнергии WудЭл общую эффективность высокотемпературного электролиза воды.
РЕЗУЛЬТАТЫ РАСЧЕТОВ И ИХ ОБСУЖДЕНИЕ
Приведенные ниже результаты расчетов выполнены для трубчатых элементов диаметром 10 мм при производительности электролизера 100 нм3Н2/ч и рабочей температуре установки 900°С. Однако результаты расчетов применимы и для секций с планарными электролизными элементами. Работу электролизера рассчитывали в режиме постоянного напряжения в диапазоне от 0.9 до 1.35 В. В качестве базового рассматривали режим чистого электролиза без продувки воздухом внутреннего анодного пространства. Основными переменными выбраны рабочее напряжение электролиза U, коэффициент разбавления кислорода kzO2 и режим разбавления 1 или 2. Коэффициент kzO2 менялся от 0 для базового режима до 50-кратного разбавления. Режим разбавления 1 соответствовал подаче воздуха в каждую секцию, равную подаче в первую секцию, а режим 2 соответствовал подаче воздуха в каждую секцию пропорционально выделяющемуся в ней кислороду. Основными результатами расчетов были мольная доля водорода на выходе из электролизера NH2вых, средняя плотность тока электролиза по длине рабочей зоны ixср, расход электроэнергии на электролиз Nэл, расход тепла на электролиз Qэл, расход тепла на догрев воздуха Qдогр, расход тепла на нагрев воды до 100°С QH2Oнагр, ее испарение QН2Оисп и догрев QH2Oдогр, производительность по водороду для данного режима работы ПрH2, объем модульного пространства, так называемой рабочей зоны, Vмод. На основании полученных результатов рассчитывали такие параметры, как эквивалентный удельный расход электроэнергии WудЭкв, удельная производительность водорода Пруд на единицу объема рабочей зоны, суммарный расход тепла на подготовку воды к электролизу QH2Oсум. На рис. 6 представлена часть этих параметров.
Рис. 6.
Зависимость эквивалентного удельного расхода электроэнергии WудЭкв, удельного расхода электроэнергии WудЭл, мольной доли водорода на выходе из электролизера NH2вых и удельной производительности водорода Пруд от напряжения U при базовом режиме электролиза.
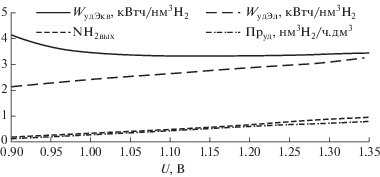
При росте напряжения электролиза возрастает концентрация водорода на выходе NH2вых, растет удельная производительность электролизера Пруд и удельные затраты электроэнергии WудЭл, в то время как эквивалентные затраты WудЭкв снижаются до напряжения 1.1–1.15 В, а затем несколько возрастают. Причиной этого служит в основном существенное снижение тепловых затрат на воду, как видно на рис. 7. Здесь видна и характерная особенность высокотемпературного электролиза: сумма электрической Nэл и тепловой Qэл энергий на электролиз не зависит от напряжения.
Рис. 7.
Зависимость расхода электроэнергии на электролиз Nэл, суммарного расхода тепла на подготовку воды к электролизу QH2Oсум, расхода тепла на электролиз Qэл от напряжения U при базовом режиме электролиза.
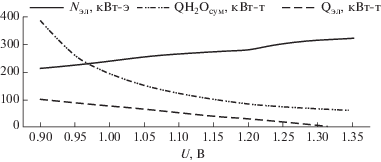
Рис. 8.
Зависимость эквивалентного удельного расхода электроэнергии WудЭкв от напряжения электролиза U при режимах разбавления 1 и 2 и коэффициенте разбавления кислорода kzO2, равном 0, 10 и 50.
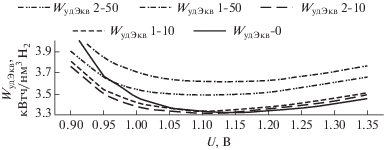
Рис. 9.
Зависимость тепла на догрев воздуха Qдогр от напряжения электролиза U при режимах разбавления 1 и 2 и коэффициенте разбавления кислорода kzO2, равном 10 и 50.
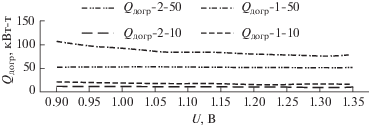
Рассмотрим зависимость основного параметра, характеризующего процесс электролиза, WудЭкв от напряжения, коэффициента разбавления kzO2 и режимов разбавления 1 и 2 кислорода (рис. 8). Как можно заметить, зависимость WудЭкв от U имеет явно выраженный минимум в диапазоне напряжений 1.05–1.2 В, при этом значения WудЭкв в режиме 1 больше, чем в режиме 2, что связано большим расходом воздуха и, следовательно, тепловой энергии на догрев воздуха (рис. 9). Таким образом, предпочтительным является режим разбавления пропорционально количеству кислорода в каждой секции.
Для определения оптимальных параметров разбавления были построены зависимости WудЭкв в суженном диапазоне значений kzO2 и напряжений. Эти данные представлены на рис. 10 и 11. Полученные результаты позволяют утверждать, что минимальный расход энергии на производство водорода на уровне 3.3 кВтч/нм3Н2 может быть получен при напряжении 1.09–1.1 В при коэффициенте разбавления кислорода от 2 до 3. При этом собственно расход электроэнергии составляет 2.63 кВтч/нм3Н2.
Рис. 10.
Зависимость эквивалентного удельного расхода электроэнергии WудЭкв от напряжения электролиза U при режиме разбавления 2 и коэффициенте разбавления кислорода kzO2, равном 0, 2, 3, 5, 10 и 15.
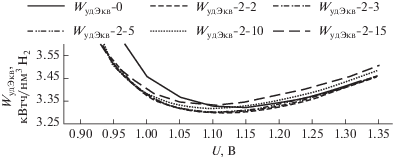
Рис. 11.
Зависимость эквивалентного удельного расхода электроэнергии WудЭкв от напряжения электролиза U при коэффициенте разбавления кислорода kzO2 от 0.5 до 7.
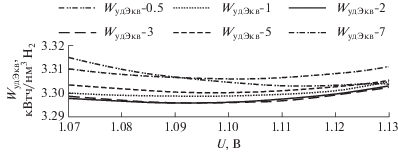
На рис. 12 и 13 для сокращенного диапазона напряжений представлены значения удельной производительности Пруд и средней плотности тока ixср, а на рис. 14 – энергетическая диаграмма работы водородпроизводящей установки в оптимальном режиме. Для оценки градиентов температуры, возникающих при электролизе с поглощением тепла, приводим на рис. 15 расчетные данные градиента температуры dTx в расчете на один ряд модулей от входа в электролизер (Num = 1) до выхода из электролизера (Num = 200). Знак минус указывает на то, что процесс электролиза проходит с поглощением тепла. Оценка градиентов температуры нужна, с одной стороны, для определения числа рядов модулей по потоку внешнего реагента в одной секции так, чтобы охлаждение потока было в допустимых пределах, не ухудшающих работу модулей, а с другой стороны, для расчета параметров промежуточных теплообменников, обеспечивающих нагрев потока реагентов и поддержание заданной рабочей температуры.
Рис. 12.
Зависимость удельной производительности водорода Пруд от напряжения электролиза U при коэффициенте разбавления кислорода kzO2 от 0 до 5.
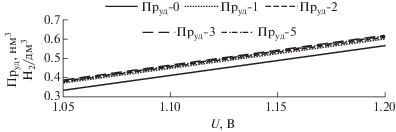
ЗАКЛЮЧЕНИЕ
На основе разработанной модели водородпроизводящей установки проанализированы варианты ее работы при различных начальных условиях. Выбраны основные параметры оценки эффективности установки, показано, что возможна эффективная работа установки при общих затратах энергии на уровне 3.3 кВтч/нм3Н2, в том числе электроэнергии на уровне 2.6 кВтч/нм3Н2.
Описано устройство электролизной части установки, обеспечивающей эффективный подвод тепла к электролизным модулям при термостабилизированном режиме работы установки, как для цилиндрических, так и для планарных модулей, а также разработана схема соединения электролизной части с источником тепловой и электрической энергии.
Работа выполнена при финансовой поддержке Министерства науки и высшего образования Российской Федерации в рамках соглашения о предоставлении грантов из федерального бюджета в виде субсидий в соответствии с пунктом 4 статьи 78.1 Бюджетного кодекса Российской Федерации № 075-15-2019-1847 от 04.12.2019 г. (уникальный идентификатор проекта RFMEFI60419X0243).
Список литературы
Progress in SOFC Technology Development at FuelCell Energy. 20th Annual Solid Oxide Fuel Cell (SOFC) Project Review Meeting. Washington, DC, April 30, 2019
John Bøgild Hansen // Faraday Discuss. 2015. V. 182. P. 9. https://doi.org/10.1039/C5FD90071A
Jakub Kupecki, Konrad Motylinski, Stanisław Jagielski et al. // Energy Conversion and Management 2019. V. 199. P. 111934. https://doi.org/10.1016/j.enconman.2019.111934
Qiuwan Shen, Lina Sun, Baowen Wang // Int. J. Electrochem. Sci. 2019. V. 14. P. 1698. www.electrochemsci.org
Stefan Fogel, Holger Kryk, Uwe Hampel // Int. J. Hydrogen Energy. 2019. V. 44. № 18. P. 9188. https://doi.org/10.1016 /j.ijhydene.2019.02.063
Mathiesen B.V., Ridjan I., Connolly D. et al. Technology data for high temperature solid oxide electrolyser cells, alkali and PEM electrolysers. Department of Development and Planning, Aalborg University. 2013.
Ligang Wang, Ming Chen, Rainer Küngas et al. // Renewable and Sustainable Energy Reviews. 2019. № 110. P. 174. www.elsevier.com/locate/rser.
Rinaldi G., Diethelm S., Oveisi E. et al. // Fuel Cells. 2017. V. 17. № 4. P. 541. www.fuelcells.wiley-vch.de
Hiroyuki Shimada, Toshiaki Yamaguchi, Toshio Suzuki et al. // J. Ceram. Soc. Jpn. 2016. V. 124. № 3. P. 213. https://doi.org/10.2109/jcersj2.15274
Ligang Wang, Johannes Dull, Francois Marechal, Jan Van herle // Int. J. Hydrogen Energy. 2019. V. 44. P. 9529.
Mohamed Zaghloul, Kevin P. Chen. Probing Temperature Profiles in Solid Oxide Fuel Cell During its Operation with 5-mm Spatial Resolution and its Implication for Optimization. Proceedings 20th Annual Solid Oxide Fuel Cell (SOFC) Project Review Meeting Washington, DC. 2019.
Naveen Karri, BrianKoeppel, Jie Bao, Kurtis Recknagle. Influence of Anode Creep on the Structural Reliability of Solid Oxide Fuel Cells. Proceedings 20th Annual Solid Oxide Fuel Cell (SOFC) Project Review Meeting Washington, DC. 2019.
Волощенко Г.Н., Коровин Н.В. // Электрохимия. 1984. Т. 20. № 9. С. 1261.
Волощенко Г.Н., Коровин Н.В., Пекарский А.Н. // Электрохимия. 1986. Т. 22. № 8. С. 1115.
Коровин Н.В., Волощенко Г.Н., Смирнов В.Н. // Электрохимия. 1984. Т. 20. № 9. С. 1258.
Коровин Н.В., Волощенко Г.Н., Смирнов В.Н. // Электрохимия. 1987. Т. 23. № 5. С. 709.
Коровин Н.В., Волощенко Г.Н., Вагин В.Ф. // Электрохимия. 1987. Т. 23. № 4. С. 462.
Волощенко Г.Н. // Альтернативная энергетика и экология. 2012. № 8. С. 19.
Волощенко Г.Н. // Альтернативная энергетика и экология. 2013. № 3/2. С. 10.
Волощенко Г.Н., Смирнов В.Н., Вагин В.Ф., Славнов Ю.А. // Сборник научных трудов № 169. М.: МЭИ, 1988. С. 23.
Волощенко Г.Н., Коровин Н.В., Пахомов В.П. и др. Авторское свидетельство СССР № 1741472. Устройство для получения водорода. 1988 г.
Волощенко Г.Н., Пахомов В.П. Гибридная энергоустановка. Патент РФ на полезную модель № 119523 от 20.08.2012 г.
Волощенко Г.Н. Расчет параметров высокотемпературного электролизера воды с твердооксидным электролитом. Свидетельство о регистрации программы для ЭВМ №2011617364 от 21.09.2011.
Волощенко Г.Н. Расчет параметров высокотемпературного электролизера воды с твердооксидным электролитом с визуализацией результатов расчетов. Свидетельство о регистрации программы для ЭВМ № 2011617961 от 12.10.2011.
Волощенко Г.Н. Трехмерная модель высокотемпературного электролизера со сниженным расходом электроэнергии для термоэлектрохимического цикла. Свидетельство о регистрации программы для ЭВМ № 2014663195 от 18.12.2014.
Волощенко Г.Н. Расчет рекуперативного теплообменника водяной пар/водород/кислород для высокотемпературного электролизера с твердооксидным электролитом. Свидетельство о регистрации программы для ЭВМ № 2012618136 от 07.09.2012.
Дополнительные материалы отсутствуют.
Инструменты
Российские нанотехнологии