Российские нанотехнологии, 2020, T. 15, № 6, стр. 741-748
ВЛИЯНИЕ ВЕЛИЧИНЫ ЗАГРУЗКИ ПЛАТИНЫ НА ЭЛЕКТРОХИМИЧЕСКИЕ ПАРАМЕТРЫ НАПЫЛЕННЫХ МАГНЕТРОНОМ ГАЗОДИФФУЗИОННЫХ ЭЛЕКТРОДОВ
Н. А. Иванова 1, *, Е. В. Кукуева 1, Б. Л. Шапир 1, Е. С. Кудинова 1, С. В. Акелькина 1, О. К. Алексеева 1
1 Национальный исследовательский центр “Курчатовский институт”
Москва, Россия
* E-mail: ivanovana.1989@mail.ru
Поступила в редакцию 10.06.2020
После доработки 23.08.2020
Принята к публикации 31.08.2020
Аннотация
Проведено исследование влияния загрузки платины на структуру, плотность и равномерность нанесения распыленной магнетроном платиновой пленки, а также на электрохимические характеристики напыленных электродов, такие как электрохимически активная поверхность платины (ЭАП), долговечность электродов и электрохимические характеристики мембранно-электродных блоков топливного элемента в целом. Показано, что с ростом содержания платины в образцах от 0.15 до 1.65 мг/см2 наблюдается укрупнение диаметра индивидуальных частиц платины от 1.5 до 3.8 нм и агломератов частиц от 5 до 12 нм соответственно. Происходит снижение ЭАП катализаторов за счет роста толщины распыленной пленки и частичного перекрывания активных центров электрокатализатора. При этом платиновая пленка представляет собой наноструктурированный каталитический слой с высокой степенью равномерности нанесенного металла. Каталитические слои, полученные напылением платины с помощью магнетрона в импульсном режиме, характеризуются высокими значениями активной поверхности вплоть до 112 м2/г и улучшенной долговечностью за счет сильного взаимодействия активных центров и углеродных частиц подложки, что подтверждается результатами рентгенофазового анализа. Потери ЭАП платины в процессе стресс-тестирования для напыленных электродов составили около 20%, что в 2 раза ниже, чем для каталитических слоев на основе порошковых платиновых электрокатализаторов. Вольтамперные характеристики топливного элемента с напыленными электродами в качестве катода растут с увеличением толщины платиновой пленки. Максимальные характеристики были получены для электродов с толщиной платиновой пленки около 100 и 200 нм, получены значения 0.43 и 0.52 А/см2 при напряжении, равном 0.5 В.
ВВЕДЕНИЕ
Развитие распределенной сети автономного маломощностного генерирования делает перспективным развитие водородной энергетики, в частности топливных элементов с твердым полимерным электролитом (ТЭ с ТПЭ) как электрохимических источников тока [1, 2]. Снижение содержания платины [3, 4] и увеличение активности и долговечности электрокатализаторов [5–9] важны для коммерциализации и повсеместного внедрения ТЭ с ТПЭ. В настоящее время большинство научных работ посвящено модифицированию химических методов синтеза с целью создания многокомпонентных электрокатализаторов с повышенными значениями эффективности и долговечности [10–12]. Это приводит к значительному усложнению процесса синтеза электрокатализаторов и снижает воспроизводимость полученных результатов из-за большого количества параметров и условий, которые требуют контроля во время приготовления электрокатализаторов и от которых зависит его конечная структура [13–16].
Перспективным методом синтеза электрокатализаторов для ТЭ является метод магнетронного распыления (МР). Количество исследований в этой области непрерывно растет [3, 4, 7, 17–27]. Магнетронное распыление позволяет создавать на поверхности газодиффузионных электродов (ГДЭ) равномерное покрытие наноструктурированного металла с развитой поверхностью, что положительно влияет на значение электрохимически активной поверхности (ЭАП) платины даже при ультранизких загрузках [27], а также регулировать свойства пленок в зависимости от используемого режима напыления [22, 26, 28]. Существуют различные режимы для получения Pt-напыленных электродов: напыление с постоянным током (DC – direct current), среднечастотное импульсное напыление. Ранее было показано, что наиболее популярны три режима нанесения платины, а именно распыление на постоянном токе без приложения напряжения смещения к подложке, режим DC при подаче импульсного напряжения смещения на подложку и импульсный режим распыления с частотой 100 кГц. В [7, 28] показаны преимущества импульсного режима распыления платины для создания каталитических покрытий с высокими электрохимическими характеристиками. Каталитические слои, нанесенные в процессе МР, обладают большей стабильностью по сравнению с каталитическими слоями на основе аморфной сажи. Это явление в основном связывают со структурой полученного распыленного магнетроном каталитического слоя, которая представляет собой наноструктурированную пленку металлической платины [3, 4, 22, 29], и сильной связью платины и углерода подложки [7], что препятствует агломерации частиц платины в процессе работы ТЭ. Свойства полученных поверхностных пленок платины во многом зависят от структуры газодиффузионного слоя, который используется в качестве подложки для распыления, а также плотности нанесения платины [7]. В [20, 29] показаны ухудшения свойств напыленных электродов с ростом величины платиновой загрузки, в частности наблюдается снижение ЭАП. Однако ультратонкие пленки нанесенных катализаторов демонстрируют неоднозначные результаты при испытаниях в составе мембранно-электродных блоков (МЭБ) ТЭ.
ЭКСПЕРИМЕНТАЛЬНАЯ ЧАСТЬ
Материалы. В качестве подложки для распыления платины использовали газодиффузионный слой – углеродную бумагу марки ELAT® LT 1400 (FuelCellsEts, College Station, Техас, США). Для процесса распыления использовали Pt-мишень с добавками графита (диаметр мишени 42 мм, толщина 1 мм). Pt-мишень с добавками графита получали прессованием Pt-порошка (размер частиц 10–50 нм) с порошком реакторного графита (размер частиц 0.1–10 мкм). Концентрация Pt в композитных мишенях составляла 60 об. %, что соответствует доле поверхности Pt в композитной мишени [28].
Изготовление каталитических слоев. Для осаждения катализаторов использовали систему МР, состоящую из лабораторной установки с постоянным током собственного производства отделения электрохимических и водородных технологий (ОЭВТ) НИЦ “Курчатовский институт” (МИР-1) и биполярного источника питания APEL-SB-5BP-1300 (ООО “Прикладная электроника”, Россия). Основные параметры установки представлены в [7, 26, 28].
Распыление Pt проводили в биполярном импульсном режиме с частотой 100 кГц. Ток магнетрона составлял 0.16–0.17 А, напряжение – 450 В, рабочий газ – аргон, давление – 9.3 × 10–3 мбар (0.93 Па).
Углеродные подложки помещали во вращающуюся чашу из нержавеющей стали, что обеспечивало более равномерное осаждение катализатора. Скорость вращения чаши составляла 10 об./мин, расстояние между мишенью и поверхностью подложки – 65 мм. Размер подложки находился в диапазоне от 9 до 12 см2. Перед осаждением поверхность подложки предварительно очищали нагреванием до 125°С в вакууме.
Время распыления Pt составляло от 1.5 до 30 мин. Были получены образцы Pt-напыленных электродов Pt/ELAT с плотностью загрузки платины 0.15, 0.2, 0.4, 0.8 и 1.65 мг/см2.
Микроструктура и элементный состав. Для исследования морфологии и микроструктуры ГДЭ с платиновыми каталитическими слоями использовали сканирующий/просвечивающий электронный микроскоп (С/ПЭМ) Titan 80–300 (Thermo-Fisher Scientific, Beverly, MA, USA). Массовое содержание Pt в образцах определяли с помощью метода энергодисперсионной рентгеновской спектроскопии (ЭРС), использовали спектрометр EDX (EDAX, Mahwah, NJ, USA).
Анализ структуры нанесенной Pt-пленки также проводили методами рентгенофазового анализа (РФА). Данный метод использовали для обнаружения наличия кристаллической структуры платины для нанесенных каталитических слоев. Образцы изучали на рентгеновском дифрактометре Bruker D8 (Bruker, Германия). Съемку дифрактограмм проводили в CuКα-излучении в интервале углов дифракции 2ϑ = 10°–70°, шаг по углу Δ2ϑ = 0.02°, экспозиция в точке 1 с. В процессе съемки образец вращался со скоростью 20 об./мин.
Электрохимические измерения. Циклические вольтамперограммы (ЦВА) регистрировали в лабораторных ТЭ по методике, аналогичной представленной в [30–32]. Площадь ТЭ составляла 1 см2. Перед регистрацией ЦВА катодную область ячейки деаэрировали потоком азота в течение 1 ч. Анод ячейки, куда подавали поток водорода, служил динамическим стандартным водородным электродом (СВЭ) сравнения и противоэлектродом одновременно. ЦВА регистрировали с использованием потенциостата Solartron 1285 (Solartron Metrology, West Sussex, UK) в потенциодинамическом режиме. Исследования проводили при 25°С. Регистрацию проводили по методике, аналогичной представленной в [33]. Для получения стабильной потенциодинамической кривой электроды предварительно циклировали в диапазоне от –0.2 В до 1.2 В со скоростью развертки 20 мВ/с до стабилизации формы ЦВА.
Площадь ЭАП платины рассчитывали, используя область ЦВА с пиками адсорбции и десорбции водорода в диапазоне от 0.05 до 0.4 В относительно СВЭ, как представлено в [7, 32].
Стресс-тест электродов на долговечность. Стабильность электрокаталитических свойств Pt-напыленных электродов определяли с помощью ускоренного стресс-теста (УСТ) на долговечность. УСТ может проводиться в различных условиях, что отражено в [30, 31]. В настоящей работе электроды подвергали стресс-тестированию путем многократного циклирования потенциала в диапазоне потенциалов +0.8–+1.3 В (против СВЭ) со скоростью развертки 0.1 В с–1. Ячейку предварительно насыщали кислородом. Промежуточные ЦВА были записаны с шагом в 300 циклов.
Определение характеристик мембранно-электродных блоков. Образцы напыленных электродов вошли в состав МЭБ площадью 1 см2, помещенного в термостатируемую водородно-кислородную топливную ячейку, с целью дальнейшего определения вольт-амперных характеристик (ВАХ) в качестве катода. В качестве анодного катализатора использовали катализатор Pt40/C10 (40 мас. % Pt на углеродной саже марки Vulcan XC-72 с 10 мас. % политетрафторэтилена). Плотность загрузки платины на анод составляла 0.1 мг/см2. Использовали мембрану марки Nafion® 212 (DuPont) толщиной 50.8 мкм; ГДС – ELAT® LT 1400. Расход кислорода поддерживали равным 1.5 см3/с, водорода – 3 см3/с. Использовали рабочие газы, насыщенные водой до относительной влажности, равной 100%. Регистрацию ВАХ проводили с помощью потенциостата “Solartron 1280” в диапазоне потенциалов от 0.9 до 0.1 В в потенциодинамическом режиме со скоростью развертки 0.2 мВ с–1, рабочая температура ячейки – 35°С.
РЕЗУЛЬТАТЫ И ИХ ОБСУЖДЕНИЕ
Структурные характеристики напыленных электродов. В работе получены Pt-напыленные электроды с загрузкой металла от 0.15 до 1.65 мг/см2. Все электроды получены в аналогичных условиях в импульсном режиме МР, различалась только продолжительность синтеза (от 1.5 мин до получаса). На рис. 1 представлены ПЭМ-изображения Pt-электродов с различной загрузкой платины. Каталитические слои, полученные методом МР, представляли собой наноструктурированную пленку металла со средним размером частиц от 1.5 до 3.8 нм (для электродов с содержанием платины соответственно 0.15 и 1.65 мг/см2). С ростом количества платины наблюдается как рост толщины платиновой пленки, так и укрупнение индивидуальных частиц платины (рис. 1) и агломератов частиц (рис. 2). Аналогичный результат был получен для ультранизких загрузок активного металла до 0.4 мг/см2 в [7, 21]. Однако в настоящей работе показано, что диаметр частиц и агломератов удваивается при увеличении загрузки платины более чем на порядок от 0.15 до 1.65 мг/см2. Это говорит об эффективности метода импульсного МР для получения Pt-покрытий с высокой степенью дисперсности частиц в широком диапазоне концентраций платины и о возможности использования таких нанесенных покрытий в качестве электрокатализаторов даже при значительной толщине Pt-пленки (около 200 нм, табл. 1). Полученные в данном случае каталитические частицы по размерам в среднем ниже, чем частицы платины для коммерческих катализаторов состава Pt40/C (40 мас. % Pt на углеродной саже марки Vulcan XC-72), средний размер частиц платины по данным [34, 35] для катализатора такого состава – 3.5–4.5 нм. При этом по данным ЭРС содержание платины в напыленном каталитическом слое составляет около 40 мас. % при плотности напыления платины 1.65 мг/см2 (табл. 1).
Рис. 1.
ПЭМ-изображения каталитических слоев, полученных методом импульсного магнетронного распыления на ГДС марки ELAT®, с содержанием платины 0.15 (а), 0.4 (б), 0.8 (в) и 1.65 (г) мг/см2.
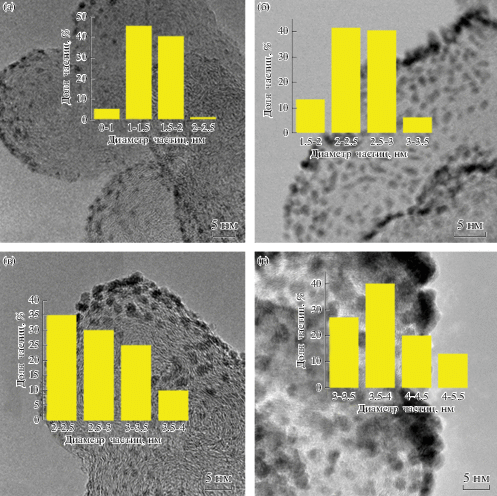
Рис. 2.
СЭМ-изображения каталитических слоев, полученных методом импульсного магнетронного распыления на ГДС марки ELAT®, с содержанием платины 0.15 (а), 0.4 (б), 0.8 (в) и 1.65 (г) мг/см2.
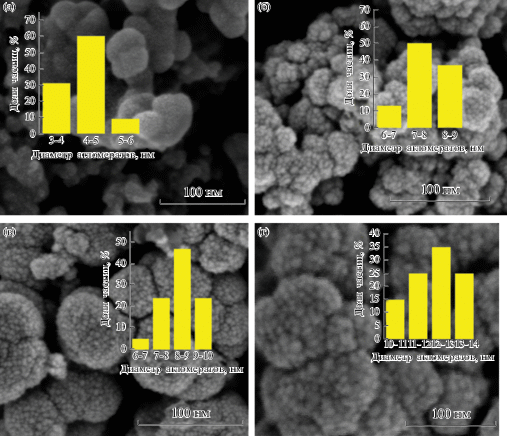
Таблица 1.
Основные параметры Pt-напыленных электродов
Электрод | Загрузка платины, мг/см2 | Толщина Pt-пленки, нм | Содержание Pt, мас. % (ЭРС) | Средний диаметр частиц, ПЭМ, нм |
---|---|---|---|---|
1 | 0.15 | 12 | 1 | 1.5 |
2 | 0.2 | 25 | 8 | 1.9 |
3 | 0.4 | 50 | 19 | 2.5 |
4 | 0.8 | 100 | 27 | 3.1 |
5 | 1.65 | 200 | 40 | 3.8 |
Отсутствие пиков, характерных для кристаллической решетки платины, на дифрактограммах в случае низких значений толщины пленки металла объясняется наноразмером кристаллических частиц, за счет чего ток ребер и дефектов перекрывается с характерным током уменьшенных граней нанокристаллов [6], и на дифрактограммах отсутствуют выраженные пики платины (рис. 3, кривая 1). Еще одной причиной может являться частичное включение атомов углерода подложки в кристаллическую структуру Pt-частиц, что вызывает дефектность граней и, как следствие, размывает характерные пики кристаллитов платины до гало [7]. Включение углерода подложки в структуру Pt-кристаллитов обеспечивает сильное взаимодействие между платиновыми активными центрами и подложкой в случае напыленных магнетроном каталитических слоев. Сформированные пики от кристаллической решетки платины четко выражены на дифрактограммах образцов с содержанием платины выше 1.5 мг/см2 (рис. 3, кривая 2). Это связано с ростом толщины пленки чистых кристаллитов платины и укрупнением Pt-частиц. Содержание металлической платины в восстановленном состоянии Pt (0) в каталитической слое превышает 93 мас. %.
Наблюдалось уменьшение ЭАП от 112 до 50 м2/г с ростом плотности нанесения платины от 0.15 до 1.65 мг/см2 (рис. 4а). Это происходит из-за роста толщины Pt-пленки (табл. 1) и за счет укрупнения частиц (рис. 2) и агломератов (рис. 3) платины, а также частичного перекрывания активных центров электрокатализатора. Поскольку напыленный каталитический слой представляет собой наноструктурированную пленку платины с агломератами в форме дендритов (рис. 2), то с увеличением толщины пленки и диаметра дендритов они частично соединяются, перекрывая часть активных Pt-центров, что снижает ЭАП платины (рис. 4а). Напыленные каталитические слои характеризуются высокими значениями ЭАП в сравнении с каталитическими слоями на основе электрокатализатора Pt/C, для которых средние значения ЭАП составляют 50–60 м2/г в диапазоне массовой концентрации платины 20–40% [33].
Рис. 4.
ЦВА (а), результаты УСТ (б, белые столбцы – до УСТ, черные столбцы – после УСТ) и ВАХ (в) для каталитических слоев электродов, полученных методом импульсного магнетронного распыления.
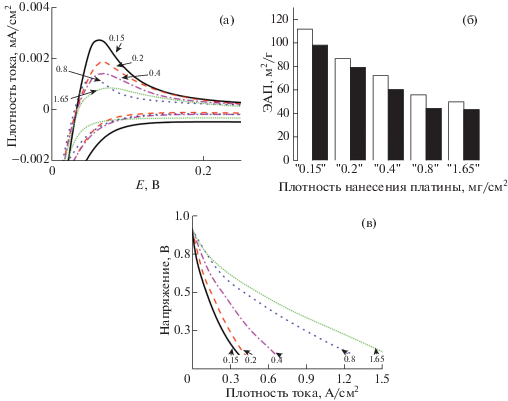
По результатам УСТ (рис. 4б) установлено, что потери ЭАП для напыленных электродов составляют около 20%, что в 2 раза ниже, чем для каталитических слоев на основе электрокатализатора Pt/C. Отметим, что значение ЭАП выходит на плато после 1500 циклов для каталитических слоев, полученных методом МР, в отличие от каталитических слоев на основе катализаторов состава Pt\C (где С – углеродная сажа), полученных методом химического восстановления платины, для которых наблюдается дальнейшая деградация в процессе УСТ [33]. Повышенная долговечность напыленных магнетроном каталитических слоев обеспечивается сильным взаимодействием Pt-частиц и углерода подложки, что замедляет процессы деградации каталитических слоев в УСТ. Полученный результат не зависит от плотности нанесения платины и толщины нанесенной Pt-пленки.
На рис. 4в представлены ВАХ для мембранно-электродных блоков с напыленными магнетроном электродами в качестве катода. В работе ТЭ электроды с толщиной нанесенного слоя электрокатализатора ниже 20 нм показали низкий результат. Значение плотности тока в рабочей зоне ВАХ увеличивалось с ростом толщины нанесенной Pt-пленки. Максимальные ВАХ получены для электродов с толщиной Pt-пленки около 100 и 200 нм, получены значения 0.43 и 0.52 А/см2 при напряжении, равном 0.5 В (табл. 2). Эти значения в среднем несколько ниже, чем для МЭБ с катодом на основе катализаторов состава Pt/C, что может объясняться затруднениями в распределении и отводе воды в силу плотной структуры Pt-пленки. Однако оптимизация толщины каталитического слоя платины, полученного методом МР, позволила получить электрохимические характеристики для МЭБ с катодом на основе напыленной платины, сравнимые по абсолютной величине с МЭБ с катодом на основе электрокатализаторов состава Pt/C.
ЗАКЛЮЧЕНИЕ
В работе получены Pt-напыленные электроды с загрузкой металла от 0.15 до 1.65 мг/см2 в аналогичных условиях в импульсном режиме распыления магнетроном. Все напыленные каталитические слои представляют собой наноструктурированную пленку металла со средним размером частиц от 1.5 до 3.8 нм (для электродов с содержанием платины соответственно 0.15 и 1.65 мг/см2). С ростом количества платины на порядок наблюдается как рост толщины Pt-пленки, так и укрупнение вдвое индивидуальных частиц платины и агломератов частиц. Отсутствие пиков от кристаллической решетки платины на дифрактограммах в случае низких значений толщины пленки объясняется наноразмером кристаллических частиц, за счет чего ток ребер и дефектов перекрывается с характерным током уменьшенных граней нанокристаллов, и на дифрактограммах отсутствуют выраженные пики платины. Еще одной причиной является частичное включение атомов углерода подложки в кристаллическую структуру Pt-частиц, что вызывает дефектность граней и, как следствие, размывает характерные пики кристаллитов платины до гало на дифрактограмме. Включение углерода подложки в структуру Pt-кристаллитов обеспечивает сильное взаимодействие между платиновыми активными центрами и подложкой в случае напыленных магнетроном каталитических слоев. Наблюдается уменьшение ЭАП от 112 до 50 м2/г с ростом плотности нанесения платины от 0.15 до 1.65 мг/см2. Это происходит из-за роста толщины Pt-пленки и за счет укрупнения частиц и агломератов платины, а также частичного перекрывания активных центров электрокатализатора. Поскольку напыленный каталитический слой представляет собой наноструктурированную пленку платины с агломератами в форме дендритов, то с увеличением толщины пленки и диаметра дендритов они частично соединяются, перекрывая часть платиновых активных центров, что снижает электрохимически активную поверхность платины. Напыленные каталитические слои характеризуются высокими значениями ЭАП в сравнении с каталитическими слоями на основе электрокатализатора Pt/C. В результате ускоренного стресс-тестирования установлено, что потери ЭАП для напыленных электродов составляют около 20%, что в 2 раза ниже, чем для каталитических слоев на основе электрокатализатора Pt/C. Отметим, что значение ЭАП выходило на плато после 1500 циклов для электродов, полученных методом МР, в отличие от катализаторов состава Pt\C (где С – углеродная сажа), полученных методом химического восстановления платины. Улучшенная долговечность обеспечивается сильным взаимодействием Pt-частиц и углерода подложки, что замедляет процессы деградации каталитических слоев в УСТ, удваивая ресурс работы электродов. Полученный результат не зависит от плотности нанесения платины и толщины нанесенной Pt-пленки. Максимальные ВАХ были получены для электродов с толщиной Pt-пленки около 200 нм, получены значения 0.52 А/см2 при напряжении 0.5 В, что сравнимо со значениями для коммерческих МЭБ.
Работа выполнена при финансовой поддержке Министерства науки и высшего образования РФ (уникальный идентификатор проекта RFMEFI60417X0171).
Список литературы
Maggio G., Nicita A., Squadrito G. // Int. J. Hydrogen Energy. 2019 V. 44. P. 11371. https://doi.org/10.1016/j.ijhydene.2019.03.121
Zhang Z., Zhou J., Zong Z. et al. // Int. J. Hydrogen Energy. 2019. V. 44. P. 28305. https://doi.org/10.1016/j.ijhydene.2019.09.028
Sievers G., Vidakovic-Koch T., Walter C. et al. // J. Appl. Electrochem. 2018. V. 48. P. 221. https://doi.org/10.1007/s10800-018-1149-7
Khan A., Nath B. K., Chutia J. // Electrochim. Acta. 2014. V. 146. P. 171. https://doi.org/10.1016/j.electacta.2014.08.116
Banham D., Ye S. // ACS Energy Lett. 2017. V. 2. P. 629. https://doi.org/10.1021/acsenergylett.6b00644
Pozio A., De Francesco M., Cemmi A. et al. // J. Power Sources. 2002. V. 105. P. 13. https://doi.org/10.1016/S0378-7753(01)00921-1
Ivanova N.A., Alekseeva O.K., Fateev V.N. et al. // Int. J. Hydrogen Energy. 2019. V. 44. P. 29529. https://doi.org/10.1016/j.ijhydene.2019.04.096
Speder J., Zana A., Spanos I. et al. // J. Power Sources. 2014. V. 261. P. 14. https://doi.org/10.1016/j.jpowsour.2014.03.039
Bezmalinovic D., Simic B., Barbir F.// J. Power Sources. 2015. V. 294. P. 82. https://doi.org/10.1016/j.jpowsour.2015.06.047
Nakazato Y., Kawachino D., Noda Z. et al. // J. Electrochem. Soc. 2018. V. 165. P. 1154. https://doi.org/10.1149/2.0311814jes
Du L., Shao Y., Sun J., Yin G. et al. // Nano Energy. 2016 V. 29. P. 314. https://doi.org/10.1016/j.nanoen.2016.03.016
Wang H., Wang X., Zheng J. et al.// J. Nanosci. Nanotechnol. 2014. V. 15. P. 3662. https://doi.org/10.1166/jnn.2015.9274
Li M., Zhou W.P., Marinkovic N.S. et al. // Electrochim. Acta. 2013. V. 104. P. 454. https://doi.org/10.1016/j.electacta.2012.10.046
Ni H.J., Lv C.C., Wang X.H. et al. // Adv. Mater. Res. 2011 V. 399–401. P. 1408. DOI: 10.4028/www.scientific.net/AMR.399-401.1408
Remy E., Onana F.F., Heitzmann M. et al. // Electrochem. Soc. 2014. V. 111. P. 542
Zhang N., Zhang S., Du C. et al. // Electrochim. Acta. 2014. V. 117. P. 413. https://doi.org/10.1016/j.electacta.2013.11.139
Bieloshapka I., Jiricek P., Vorokhta M. et al. // Appl. Surf. Sci. 2017. V. 419. P. 838. https://doi.org/10.1016/j.apsusc.2017.05.035
Ostroverkh A., Dubau M., Johánek V. et al. // Fuel Cells. 2018. V. 18. P. 51. https://doi.org/10.1002/fuce.201700137
De Lucas-Consuegra A., De La Osa A.R., Calcerrada A.B. et al. // J. Power Sources. 2016. V. 321. P. 248. https://doi.org/10.1016/j.jpowsour.2016.05.004
Brault P. // Surf. Coat. Technol. 2011. V. 205. P. 15. https://doi.org/10.1016/j.surfcoat.2011.01.052
Mougenot M., Caillard A., Brault P. et al. // Int. J. Hydrogen Energy. 2011. V. 36. P. 8429. https://doi.org/10.1016/j.ijhydene.2011.04.080
Alexeeva O.K., Fateev V.N. // Int. J. Hydrogen Energy. 2016. V. 41. P. 3373. https://doi.org/10.1016/j.ijhydene.2015.12.147
Tian Z.Q., Lim S.H., Poh C.K. et al. // Adv. Eng. Mater. 2011. V. 1. P. 1205. https://doi.org/10.1002/aenm.201100371
Neyerlin K.C., Gu W., Jorne J., Gasteiger H.A. // J. Electrochem. Soc. 2007. V. 154. P. B279 https://doi.org/10.1149/1.2400626
Kim H.T., Lee J.K., Kim J. // J. Power Sources. 2008. V. 180. P. 191. https://doi.org/10.1016/j.jpowsour.2008.02.031
Fateev V.N., Alekseeva O.K., Porembskiy V.I. et al. // Alternative Energy Ecology. 2017. V. 27. P. 88.
Coutanceau C., Brault P., Caillard A. et al. // ECS Transactions. 2011. V. 41. P. 1151. https://doi.org/10.1149/1.3635648
Alekseeva O.K., Mikhalev A.I., Lutikova E.K. et al. // Catalysts. 2018. V. 8. P. 1. https://doi.org/10.3390/catal8120665
Hirano S., Kim J., Srinivasan S. // Electrochim. Acta. 1997. V. 42. P. 1587. https://doi.org/10.1016/S0013-4686(96)00320-9
Аваков В.Б., Алиев А.Д., Богдановская В.А. и др. // Журн. физ. химии. 2015. № 89. С. 861. https://doi.org/10.7868/S0044453715050064
Кузов А.В., Тарасевич М.Р., Богдановская В.А. и др. // Электрохимия. 2016. № 52. С. 790.
Labbé F., Asset T., Chatenet M. et al. // Electrocatalysis. 2019. V. 10. P. 156. https://doi.org/10.1007/s12678-018-0505-z
Spasov D.D., Ivanova N.A., Pushkarev A.S. et al. // Catalysts. 2019. V. 9. P. 803 https://doi.org/10.3390/catal9100803
Pushkarev A.S., Pushkareva I.V., Ivanova N.A. et al. // Catalysts. 2019. V. 9. P. 271. https://doi.org/10.3390/catal9030271
Labbé F., Disa E., Ahmad Y. et al. // Microporous Mesoporous Mater. 2018. V. 271. P. 1. https://doi.org/10.1016/j.micromeso.2018.05.019
Дополнительные материалы отсутствуют.
Инструменты
Российские нанотехнологии