Российские нанотехнологии, 2020, T. 15, № 6, стр. 749-756
МЕТОД МАГНЕТРОННОГО РАСПЫЛЕНИЯ ДЛЯ НАНЕСЕНИЯ Ni-КАТАЛИЗАТОРА ПРОЦЕССА СИНТЕЗА МАССИВОВ УГЛЕРОДНЫХ НАНОТРУБОК
Е. С. Кудинова 1, Е. А. Воробьева 1, 2, Н. А. Иванова 1, *, В. В. Тишкин 1, О. К. Алексеева 1
1 Национальный исследовательский центр “Курчатовский институт”
Москва, Россия
2 Научно-исследовательский институт ядерной физики им. Д.В. Скобельцына Московского государственного университета им. М.В. Ломоносова
Москва, Россия
* E-mail: ivanovana.1989@mail.ru
Поступила в редакцию 10.06.2020
После доработки 20.08.2020
Принята к публикации 20.08.2020
Аннотация
Представлено исследование по оптимизации метода нанесения Ni-катализатора роста углеродных нанотрубок (УНТ) на газодиффузионные слои (ГДС) (преимущественно углеродные ткани) методом магнетронного распыления. Впервые подобран режим магнетронного распыления Ni-катализатора, позволяющий получать равномерное покрытие металла на ГДС, необходимое для успешного синтеза УНТ. Показано, что распыление Ni в режиме постоянного тока с подачей импульсного напряжения смещения на подложку с частотой 100 кГц и временем подачи отрицательного импульса 7 мкс позволяет получить оптимальное наноструктурированное покрытие металла с низкой удельной поверхностью и с высокой степенью равномерности нанесения на всю площадь подложки. Нанесенное Ni-покрытие выступает в качестве катализатора роста УНТ. На ГДС с нанесенным Ni-катализатором методом пиролитического газофазного осаждения выращены массивы УНТ со средним диаметром 40 и 80 нм для гидрофобного и гидрофильного ГДС соответственно. Массивы УНТ получены непосредственно на всей поверхности углеродных подложек с высокой степенью равномерности. Установлено, что диаметр нанотрубок в основном определяется структурой используемого ГДС.
ВВЕДЕНИЕ
В настоящее время рост энергопотребления человечества ведет к активному развитию всех отраслей энергетики. Развитие альтернативных источников энергии, не требующих использования углеводородов, является особенно актуальным в условиях ухудшающейся экологической ситуации [1]. Особое место среди альтернативной энергетики занимает водородная энергетика. Широкомасштабное развитие водородной энергетики позволит восполнить энергодефицит в отдаленных регионах [2, 3] за счет применения топливных элементов (ТЭ) с твердым полимерным электролитом (ТПЭ) как в мобильных устройствах [4], так и на стационарных установках [5, 6].
Одним из главных компонентов мембранно-электродных блоков (МЭБ) ТЭ является носитель электрокатализатора, значительно влияющий на долговечность электрокатализатора и ресурс работы электродов ТЭ. Недостатками используемых в настоящее время носителей, например углеродной сажи, являются их коррозия и деградация каталитического слоя во время работы ТЭ [7]. В настоящее время ведутся разработки новых эффективных носителей электрокатализаторов на основе соединений углерода, например таких, как восстановленный оксид графена, нановолокна, а также углеродные нанотрубки (УНТ) и их массивы [8]. Полые цилиндрические графитовые структуры, называемые УНТ, являются уникальным современным материалом для науки и техники. Массивы УНТ являются перспективными носителями электрокатализаторов для ТЭ [9, 10] благодаря равномерной матричной структуре, а также механической прочности [11], высокой электропроводности, химической стабильности и развитой поверхности [12]. УНТ используются в качестве носителей гибридных электрокатализаторов [13], что обеспечивает высокую стабильность электродов на их основе и незначительную потерю мощности ТЭ в результате стресс-тестирования (всего на 4%). В исследованиях [14, 15] УНТ также использовались в качестве носителя и наносились на газодиффузионные слои (ГДС) в виде микропористого слоя. Так, в [13–15] отмечены снижение сопротивления, увеличение количества каталитических центров и повышение мощности ТЭ.
УНТ могут быть синтезированы рядом методов. К ним относят электродуговое распыление, каталитическое разложение углеводородов (CVD – chemical vapor deposition), лазерную абляцию и другие. Метод CVD ввиду его простоты является одним из наиболее распространенных для получения массивов УНТ, однако требует использования катализаторов [16]. Катализаторы могут использоваться непосредственно в процессе синтеза УНТ либо могут быть нанесены на поверхность подложки [17, 18]. В качестве катализаторов могут выступать переходные элементы, такие как никель, медь, кобальт, железо и другие [10, 13–19], однако для успешного роста УНТ необходимо подобрать плотность нанесения металла, толщину слоя и т.д.
Для нанесения металлов на подложку, как правило, требуются многоступенчатые химические процессы. Эта проблема решается с помощью метода магнетронного распыления (МР), который позволяет наносить наноструктурные покрытия металлов в одну стадию и обладает высокой эффективностью и воспроизводимостью результатов. В [20–23] описаны методы нанесения ферромагнитных катализаторов для роста нанотрубок, таких как Fe и Ni, в том числе с использованием МР. В [20] особое внимание уделено морфологии поверхности катализатора, структуре промежуточного слоя (для предотвращения диффузии) и толщине самой каталитической пленки. Показано, что длина УНТ зависит от указанных выше параметров. В [24, 25] подчеркнута важность термообработки подложки перед началом синтеза нанотрубок. На параметры получаемых катализаторов влияют также условия распыления, такие как давление рабочего газа, напряжение, расстояние до мишени, режим работы магнетрона [26]. К текущему моменту существует ограниченное количество работ по нанесению катализаторов для роста УНТ методом МР, несмотря на все его достоинства. Основной сложностью для нанесения ферромагнитных материалов методом МР является магнитный момент, способный шунтировать поле планарного магнетрона [27].
В настоящей работе исследованы особенности синтеза Ni-катализатора методом магнетронного распыления для роста УНТ, которые могут быть выращены непосредственно на ГДС электродов для повышения эффективности и стабильности работы ТЭ.
ЭКСПЕРИМЕНТАЛЬНАЯ ЧАСТЬ
Используемые материалы. Распыление никеля проводили на углеродные ткани, выступающие в роли газодиффузионных слоев ТЭ. В качестве подложек использовали следующие углеродные ткани (табл. 1): ELAT® LT1400 с нанесенным гидрофобным микропористым слоем (МПС) и гидрофильная углеродная ткань производства Санкт-Петербург, Россия (введено обозначение “Cloth”). Размер исследуемых образцов ГДС составил 35 × 35 мм. Образцы располагали в центре чаши для обеспечения равномерности нанесения покрытия на всю площадь подложки.
Все ГДС предварительно обработаны в камере магнетрона в идентичных условиях, которые описаны далее. После загрузки образца углеродной ткани проводили откачку системы диффузионным насосом (для заливки ловушек насоса использовали жидкий азот) до вакуума, равного 8 × × 10–5 мм рт.ст., одновременно с нагревом до температуры 125–130°С. Затем подложка остывала до температуры 35–45°С, после чего начинался процесс подачи напряжения и зажигания магнетронного разряда. Предварительная обработка подложки позволила удалить воду и другие легколетучие примеси с поверхности образцов для лучшей адгезии напыляемого катализатора. Температурный режим нагрева ограничен использованием углеродных материалов с высокой степенью спекания частиц.
Изготовление образцов. Все эксперименты по нанесению никеля выполнены на установке МИР-1 в НИЦ “Курчатовский институт” [28, 29]. Магнетронная распылительная система представляет собой вакуумную камеру, снабженную помимо вводов напряжения и тока системой откачки, системой водного охлаждения мишени и системой подачи газов. Расстояние от дна чаши магнетрона до мишени составляет 85 мм. Давление аргона во всех экспериментах составило 6 × × 10–3–7 × 10–3 мм рт.ст., время распыления 5 мин. Наряду с обычной системой питания постоянного тока использовали импульсный источник питания APEL-SB-5BP-1300 как для питания магнетрона (в импульсном режиме распыления – IM), так и для подачи напряжения смещения на подложку при работе магнетрона в DC-режиме (DCV – режим распыления на постоянном токе с подачей напряжения смещения). Характеристики режимов МР приведены в табл. 2.
Таблица 1.
Характеристики используемых ГДС
Марка ГДС | Толщина, мм | Плотность, г/м2 | Объемная плотность, г/см3 | Пористость, % | Содержание углерода, % |
---|---|---|---|---|---|
ELAT® | 0.454 | 170 | 0.377 | 63 | 99.5 |
«Cloth» | 0.61 | 190 | 0.42 | 58 | 99.5 |
Таблица 2.
Характеристики режимов магнетронного распыления
Тип процесса | DC | DCV | IM |
---|---|---|---|
Напряжение магнетрона, В | –420 | –420–450 | –550 |
Сила тока магнетрона, А | 0.2 | 0.2 | 0.19–0.33 |
Напряжение смещения, В | –400 | ||
Сила тока смещения, А | <0.01 | ||
Время подачи отрицательного импульса, мкс | 7 | 7 | |
Частота импульсов, кГц | 100 | 100 | |
Использование источника питания APEL-SB-5BP-1300 | нет, подложка заземлена | да | да, подложка заземлена |
Толщина Ni-мишени – 2 мм, диаметр – 75 мм. Для образцов, полученных методом МР никеля на ГДС, введено обозначение Ni/ГДС. Напыление никеля на ГДС марки ELAT® LT1400 проводили в DC, DCV и в импульсном (IM) режимах, получены образцы NiDC/ELAT, NiDCV/ELAT и NiIM/ELAT соответственно. Для образца “Сloth” нанесение никеля проводили только в режиме DCV, получен образец NiDCV/Cloth. Для всех образцов с нанесенным Ni-покрытием плотность нанесения была равной и составила около 0.15 мг/см2.
Структурные исследования металлического покрытия. Образцы Ni/ELAT исследовали методом сканирующей электронной микроскопии (СЭМ) на приборе Versa 3D DualBeam (FEI, США), а также на просвечивающем электронном микроскопе (ПЭМ) марки Titan™ 80–300 S/TEM (FEI, США) (80–300 кВ, пространственное разрешение по точкам 0.07–0.08 нм). Для определения размеров нанотрубок использован метод СЭМ, прибор Helios 434 (FEI, США).
Синтез нанотрубок. На всех Ni-напыленных ГДС углеродные нанотрубки выращивали методом CVD на установке пиролитического газофазного осаждения в МГУ им. М.В. Ломоносова (Россия) [30]. CVD-реактор представлял собой кварцевую трубку размером 2.5 × 100 см, помещенную в печь с автоматическим контролем температуры. В реактор подавали жидкий прекурсор для роста УНТ (циклогексан) с растворенным в нем катализатором (ферроцен) и газ-носитель (азот). Ферроцен, растворенный в циклогексане, применяли для продолжения роста нанотрубок после того, как произойдет зауглероживание напыленного Ni-катализатора на подложке. Поток газа регулировался автоматически. Испарение жидкости происходило в начале трубки при температуре около 200°С. Далее реагент попадал в высокотемпературную часть реактора, где разлагался при температуре 750–950°С. Предосажденные на ГДС частицы никеля служили каталитическими центрами для роста массивов УНТ из углерода, образованного из пиролизированного циклогексана. Время синтеза УНТ для всех образцов составило 30 мин.
РЕЗУЛЬТАТЫ И ИХ ОБСУЖДЕНИЕ
Структура Ni-покрытия на подложке. Создание равномерного Ni-покрытия с заданными свойствами играет важнейшую роль для синтеза УНТ. Метод МР позволяет создавать равномерные покрытия металлов, однако в данном случае распределение металла по подложке характеризуется определенной зависимостью от используемого режима распыления. Структура углеродного подслоя в значительной степени определяет как размер индивидуальных частиц металла, так и агломератов частиц в процессе МР. Для платины данные закономерности представлены в [31]. Показано, что при росте плотности нанесения наблюдаются рост диаметра дендритов платины и укрупнение индивидуальных платиновых частиц [32]. Структура нанесенного покрытия зависит от использованного режима распыления. Основываясь на близких значениях коэффициента распыления никеля и платины [33, 34], аналогичной зависимости можно ожидать для Ni-покрытий.
На рис. 1 представлена исходная структура поверхности образца углеродной ткани ELAT® LT1400. Нанесенное покрытие никеля представляет собой наноструктурированную пленку Ni-частиц, осажденных на поверхность ГДС (рис. 2). Процесс распыления никеля в режиме DC был крайне не равномерным и не контролируемым, удовлетворительных условий для успешного нанесения никеля получено не было. В дальнейшем данный процесс для распыления никеля на ГДС не применялся. Были исследованы образцы ГДС с никелем, нанесенным в режимах DCV и IM.
Рис. 2.
ПЭМ-изображение наночастиц никеля (а) с распределением частиц по размерам (б) и СЭМ-изображение агломератов частиц (в) с их распределением по размерам (г) для Ni-покрытия, напыленного в импульсном режиме. ПЭМ-изображение наночастиц никеля (д) с распределением частиц по размерам (е) и СЭМ-изображение агломератов частиц (ж) с их распределением по размерам (з) для Ni-покрытия, напыленного в режиме DCV.
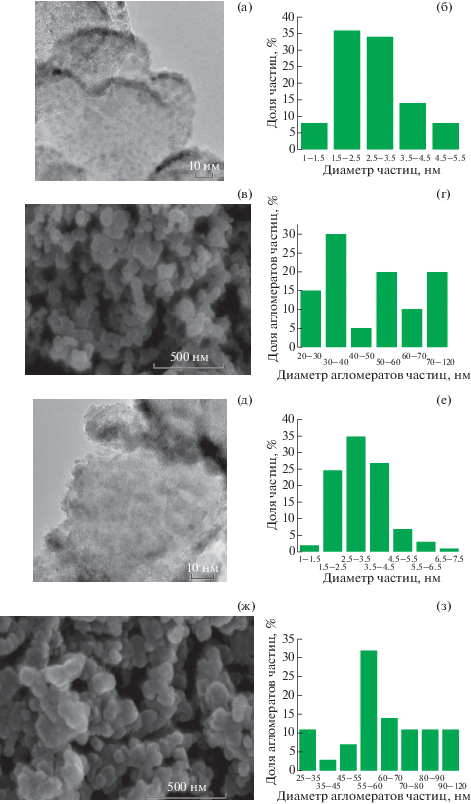
В IM-режиме получено Ni-покрытие со средним размером индивидуальных частиц ~2.5–3.5 нм, 70% от общего числа частиц характеризуются диаметром от 2.0–3.5 нм (рис. 2а, 2в). Наночастицы образуют агломераты в форме столбцов-дендритов диаметром от 18 до 100 нм, причем наблюдается значительная неравномерность в распределении диаметров дендритов (рис. 2б, 2г). Агломераты по диаметрам можно разделить на две фракции: фракцию мелких столбцов диаметром до 30 нм (45% от общего числа) и фракцию крупных агломератов диаметром более 70 нм (40% от общего числа).
Для пленки никеля, полученной в DCV-режиме распыления (рис. 2д, 2ж), средний размер частиц никеля ~3.0 нм (диаметр более 85% частиц находится в диапазоне 1.5–4.5 нм). Ni-пленка сформирована из агломератов никеля столбчатой структуры (рис. 2ж, 2з) с диаметрами столбцов от 25 до 116 нм. Более половины от общего числа агломератов никеля составляет фракция со средним диаметром агломератов от 50 нм. Пленка никеля, полученная в режиме DCV, характеризуется менее развитой поверхностью и плотной структурой.
Массивы УНТ на газодиффузионных слоях. Для ткани ELAT® равномерный рост УНТ наблюдается для образцов с никелем, нанесенным в режиме DCV. Средний диаметр полученных нанотрубок для образца NiDCV/ELAT составил 40–50 нм (рис. 3а, 3б), что соотносится со средним размером агломератов нанесенного никеля (рис. 4 з). Нанотрубки были также успешно синтезированы на образце NiDCV/Cloth (рис. 3г, 3д), полученном в DCV-режиме распыления никеля. Диаметр нанотрубок составил 80–90 нм. Для образца NiIM/ELAT, на который осаждение никеля проводили в импульсном режиме, роста нанотрубок не наблюдалось (рис. 3в), на ткани сформировался слой аморфного углерода с фрагментами толстостенных дефектных нанотрубок толщиной более 150 нм. Это объясняется структурой нанесенного катализатора, полученной в IM-режиме нанесения никеля. Режим IM характеризуется меньшей плотностью плазмы, что мешает равномерному нанесению покрытия с низкопористой структурой металлической пленки. На ГДС наблюдалось формирование развитой структуры агломератов со средним размером менее 30 либо более 75 нм.
Рис. 3.
СЭМ-изображения массива углеродных нанотрубок, выращенных на образцах NiDCV/ELAT (а, б), NiIM/ELAT (в) и NiDCV/Cloth (г, д).
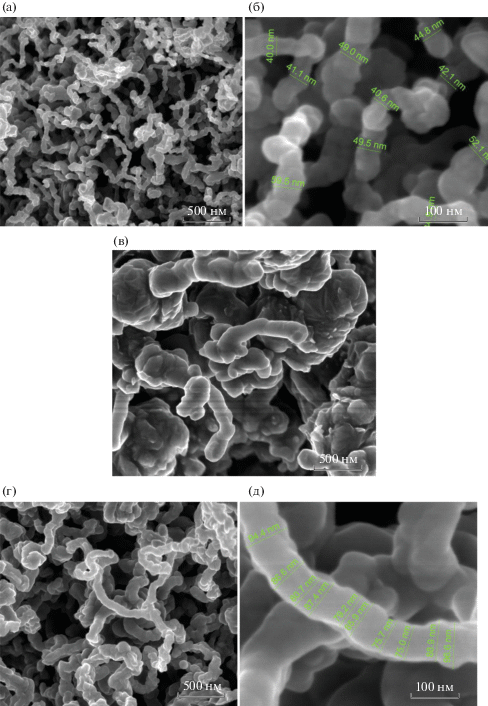
Формирование высокоразвитой поверхности при напылении никеля в IM-режиме препятствовало росту УНТ. Низкая шероховатость подложки является необходимым условием роста УНТ, в том числе ориентированных массивов УНТ с характерным диаметром до 50 нм. Как правило, УНТ выращивают на гладких, беспористых подложках. В исследовании [35] показано, что наилучшие результаты по выращиванию УНТ дает сапфировая подложка, обладающая минимальной шероховатостью и высокой кристалличностью. Это подтверждает преимущества использования DCV-режима распыления, который обеспечил плотное покрытие Ni-катализатора с низкоразвитой поверхностью и узким распределением агломератов по размерам (рис. 2ж) и позволил, сформировав однородную пленку никеля на поверхности ГДС, снизить пористость углеродной ткани, предотвратив диффузию частиц катализатора в глубь ГДС. Использование DCV-режима нанесения никеля предпочтительнее по сравнению с импульсным режимом распыления. Это связано с увеличением плотности плазмы вблизи самой подложки [15, 16]. DCV предотвращает образование дуг, которые могут разрушить подложку или привести к значительной агломерации наносимых частиц, что снижает тепловую нагрузку на носитель.
Параметры полученных УНТ. Для образца гидрофобной ткани ELAT LT 1400 внешний диаметр УНТ оказался в 2 раза меньше, чем для ткани марки “Сloth”. На диаметр полученных нанотрубок могут оказывать влияние несколько факторов. В [36] авторы объясняют полученный размер нанотрубок механизмом их роста (получены МУНТ с внешним диаметром 50 нм и внутренним 27 нм). Однако в настоящей работе все массивы УНТ выращены в идентичных условиях, что исключает влияние условий синтеза [37].
В первую очередь в качестве факторов, влияющих на параметры УНТ, следует выделить структуру подложки и размер агломератов Ni-катализатора. Гидрофобная поверхность ткани ELAT обеспечивает лучшую адгезию катализатора и уменьшает вероятность образования крупных агломератов. Углеродная ткань ELAT обладает большей пористостью (табл. 1), что позволяет большему количеству наночастиц укрепиться в мелких порах по сравнению с тканью марки Cloth. Размер нанесенных Ni-агломератов непосредственно влияет на диаметр синтезируемых УНТ. Исследование [38] показывает, что диаметр УНТ, выращенных на каталитических Ni-частицах, приблизительно равен диаметру самих частиц в случае, если частицы нанесены на гладкую кремниевую подложку. В настоящей работе диаметр нанотрубок коррелирует с диаметром Ni-агломератов на поверхности ГДС. В [39] авторы изучали процесс роста УНТ в зависимости от толщины наносимого катализатора (Co и Ni).
Рассматривая преимущества предварительно осажденного катализатора, необходимо провести сравнение с идентичной методикой синтеза УНТ, но с различием в нанесении катализатора. В [30] катализатор впрыскивали в соединении с прекурсором непосредственно в реактор. Синтез УНТ проводили на кремниевых подложках. Получены равномерные массивы ориентированных нанотрубок диаметром от 20 до 60 нм и высотой от 150 мкм до 1 мм. Авторы [30] отмечают, что на данные параметры могут влиять механизмы роста УНТ, связанные с распределением железа в процессе роста массивов. Близкие размеры полученных нанотрубок говорят об эффективности использования напыленного магнетроном Ni-катализатора в процессе роста УНТ.
Основываясь на изложенном выше, диаметр полученных в настоящей работе нанотрубок в большей степени определяется структурой использованной подложки, которая влияет как на размер агломератов нанесенного металла, так и на условия проведения синтеза УНТ. Значительная неоднородность структуры исходных ГДС привела к возникновению локального переизбытка или недостатка катализатора, изменению температуры, что повлияло на структуру синтезированных УНТ.
ЗАКЛЮЧЕНИЕ
Проведена оптимизация процесса магнетронного распыления Ni-катализатора роста углеродных нанотрубок на газодиффузионные слои. Исследованы различные режимы нанесения каталитических слоев: на постоянном токе, на постоянном токе с подачей импульсного напряжения смещения и импульсный режим. Применение режима на постоянном токе характеризуется крайней нестабильностью процесса, катализатор на подложку практически не был нанесен. Формирование высокоразвитой поверхности при напылении никеля в импульсном режиме препятствует росту УНТ на поверхности ГДС. Данное покрытие не может выступать в роли катализатора синтеза УНТ. Благодаря конструкции мишени и магнетрона, а также подбору параметров процесса удалось добиться эффективного распыления Ni-катализатора в режиме с постоянным током и подачей импульсного напряжения смещения на подложку. Таким образом, метод магнетронного распыления на постоянном токе с подачей импульсного напряжения смещения на подложку позволил создать на поверхности ГДС плотную наноструктурированную пленку никеля со средним размером частиц 3 нм. Полученная плотная высокооднородная пленка с низкой удельной поверхностью и узким распределением агломератов никеля по размерам была успешно использована в качестве катализатора роста массива УНТ в процессе пиролитического газофазного осаждения непосредственно на ГДС. Диаметры полученных нанотрубок составили 40–60 нм при использовании в качестве подложки углеродной ткани марки ELAT® LT 1400, что сравнимо с представленными в литературе аналогами. На размеры синтезированных УНТ в большей степени оказали влияние использованная подложка и диаметр полученных агломератов никеля.
Работа выполнена при поддержке Российского фонда фундаментальных исследований (проекты № 20-08-00927, 18-29-23030).
Список литературы
Guozhu M., Xi L., Huibin D. et al. // Renew. Sustain. Energy Rev. 2015. V. 48. P. 276. https://doi.org/10.1016/j.rser.2015.03.094
Chade D., Miklis T., Dvorak D. // Renew. Energy. 2015. V. 76. P. 204. https://doi.org/10.1016/j.renene.2014.11.023
Ghenai C., Bettayeb M., Brdjanin B., Hamid A.K. // Case Studies Thermal Eng. 2019. V. 14. P. 100497. https://doi.org/10.1016/j.csite.2019.100497
Gwangwoo H., Yong K.K., Joong B.K. et al // Appl. Energy. 2020. V. 259. P. 114175.
Kelly N.A., Gibson T.L., Ouwerkerk D.B. // Int. J. Hydrogen Energy. 2011. V. 326. P. 15803. https://doi.org/10.1016/j.ijhydene.2011.08.058
Hanke-Rauschenbach R., Bensmann B., Millet P. // Compendium of Hydrogen Energy: Hydrogen Production and Purification. W. P. Series in Energy. 2015. P. 179. https://doi.org/10.1016/B978-1-78242-361-4.00007-8
Mamat M.S., Grigoriev S.A., Dzhus K.A.et al. // Int. J. Hydrogen Energy. 2010. V. 35. P. 7580. https://doi.org/10.1016/j.ijhydene.2010.04.147
Mardle P., Ji X., Wu J. et al. // Appl. Catal. B. 2020. V. 260. P. 118031. https://doi.org/10.1016/j.apcatb.2019.118031
Плеханова Ю.В., Тарасов С.Е., Быков А.Г. и др. // Российские нанотехнологии. 2018. Т. 13. № 9–10. С. 77.
Venkataraman A., Amadi E.V., Chen Y., Papadopoulos C. // Nanoscale Res. Lett. 2019. V. 14. P. 47. https://doi.org/10.1186/s11671-019-3046-3
Крестинин А.В. // Российские нанотехнологии. 2019. Т. 14. № 9–10. С. 18. https://doi.org/10.21517/1992-7223-2019-9-10-18-34
Булярский С.В. Углеродные нанотрубки: технология, управление свойствами, применение. Ульяновск: Стержень, 2011. 480 с.
Moghadam Esfahani R.Z., Vankova S.K., Bradley E. // Renew. Energy. 2020. V. 154. P. 913. https://doi.org/10.1016/j.renene.2020.03.029
Chinnasa P., Ponhan W., Swatsitang E. // Mater. Today: Proceedings. 2019. V. 17. P. 1344. https://doi.org/10.1016/j.matpr.2019.06.154
Show Y., Takahashi K. // J. Power Sources. 2009. V. 190. P. 322. https://doi.org/10.1016/j.jpowsour.2009.01.027
Shah K.A., Tali B.A. // Mater. Sci. Semicond. Process. 2016. V. 41. P. 67. https://doi.org/10.1016/j.mssp.2015.08.013
Lin J., Yang Y., Zhang H. et al. // J. Alloys Compd. 2018. V. 745. P. 817. https://doi.org/10.1016/j.jallcom.2018.02.252
Wu X., Mu F., Zhao H. // J. Mater. Sci. Technol. 2020. V. 55. P. 16. https://doi.org/10.1016/j.jmst.2019.05.063
Елецкий А.В. // Успехи физ. наук. 1997. Т. 169. № 9. С. 945.
Salunke P., Yarmolenko S., Neralla S. et al. Proc. of the 14th Int. Mech. Eng. Congress IMECE 2007. Nov 11–15, 2007, Seattle, WA, USA.
Tang Z., Poh C.K., Tian Z. et al. // Electrochim. Acta. 2011. № 56. P. 4327. https://doi.org/10.1016/j.electacta.2011.01.035
Thurakitseree T., Pakpum C. // Appl. Mechanics Mater. 2019. № 891. P. 195. https://doi.org/10.4028/www.scientific.net/AMM.891.195
Baro M., Hussain A.A., Pal A.R. // RSC Adv. 2014. № 87. P. 46970. https://doi.org/10.1039/C4RA07833K
Hart A.J., Slocum A.H., Royer L. // Carbon. 2006. № 44. P. 348. https://doi.org/10.1016/j.carbon.2005.07.008
Moshkalyov S.A., Moreau A.L., Guttierrez H.R. et al. // Mater. Sci. Eng. B. 2004. № 112. P. 147. https://doi.org/10.1016/j.mseb.2004.05.038
Alexeeva O.K., Fateev V.N. // Alternative Energy Ecology (ISJAEE). 2015. № 7. P. 14. https://doi.org/10.15518/isjaee.2017.25-27.088-099
Sidelev D.V., Krivobokov V.P. // Vacuum. 2019. V. 160. P. 418. https://doi.org/10.1016/j.vacuum.2018.12.001
Alekseeva O.K., Mikhalev A.I., Lutikova E.K. et al. // Catalysts. 2018. V. 8. № 12. P. 665. https://doi.org/10.3390/catal8120665
Baranov I.E., Porembskii V.I., Lyutikova E.K. et al. // Chemical Problems. 2019. № 4. P. 489.
Chechenin N.G., Chernykh P.N., Vorobyeva E.A., Timofeev O.S. // Appl. Surf. Sci. 2013. V. 275. P. 217. https://doi.org/10.1016/j.apsusc.2012.12.162
Ivanova N.A., Alekseeva O.K., Fateev V.N. et al. // Int. J. Hydrogen Energy. 2019. V. 44. P. 29529. https://doi.org/10.1016/j.ijhydene.2019.04.096
Alekseeva O.K., Mikhalev A.I., Lutikova E.K. et al. // Catalysts. 2018. V. 8. P. 665. https://doi.org/10.3390/catal8120665
Кузьмичев А.И. Магнетронные распылительные системы. Кн. 1. Введение в физику и технику магнетронного распыления. Киев: Аверс, 2008. 244 с.
Ostroverkh A., Johánek V., Dubau M. et al // Int. J. Hydrogen Energy. 2019. V. 44. P. 19344. https://doi.org/10.1016/j.ijhydene.2018.12.206
Guellatia O., Béginb D., Antoni F. et al. // Mater. Sci. Eng. B. 2018. V. 231. P. 11. https://doi.org/10.1016/j.mseb.2018.03.001
Xie Z., Guofen Chen G., Yu X. et al. // Int. J. Hydrogen Energy. 2015. V. 40. P. 8958. https://doi.org/10.1016/j.ijhydene.2015.04.129
Lin J., Yang Y., Zhang H. et al. // Ceram. Int. 2020. V. 46. P. 3837. https://doi.org/10.1016/j.ceramint.2019.10.107
Koji H., Furuta H., Sekiya K. et al. // Diamond Relat. Mater. 2013. V. 36. P. 1. https://doi.org/10.1016/j.diamond.2013.02.002
Lee M.W., Haniff M.A., Teh A.S. et al. // J. Experimental Nanosci. 2014. V. 10. № 16. P. 1232.
Дополнительные материалы отсутствуют.
Инструменты
Российские нанотехнологии