Российские нанотехнологии, 2021, T. 16, № 2, стр. 215-221
ДИЗАЙН НАНОСПЛАВНЫХ КАТАЛИЗАТОРОВ ДЛЯ ПРОЦЕССОВ ПОЛУЧЕНИЯ ВОДОРОДА
Д. И. Потемкин 1, 2, 3, *, П. В. Снытников 1, 2, С. Д. Бадмаев 1, 2, А. М. Горлова 1, 2, А. В. Задесенец 1, 4, Е. Ю. Филатов 1, 4, П. Е. Плюснин 1, 4, Ю. В. Шубин 1, 4, С. В. Коренев 1, 4, В. А. Собянин 2
1 Новосибирский государственный университет
Новосибирск, Россия
2 Институт катализа им. Г.К. Борескова СО РАН
Новосибирск, Россия
3 Новосибирский государственный технический университет
Новосибирск, Россия
4 Институт неорганической химии им. А.В. Николаева СО РАН
Новосибирск, Россия
* E-mail: potema@catalysis.ru
Поступила в редакцию 16.06.2020
После доработки 16.06.2020
Принята к публикации 22.07.2020
Аннотация
Использование нанесенных наночастиц сплавов металлов в качестве активного компонента позволяет модифицировать активность, селективность и стабильность традиционных монометаллических нанесенных гетерогенных катализаторов. Описан подход к направленному синтезу биметаллических порошков и нанесенных катализаторов на основе разложения двойных комплексных солей в порах носителей. Эффективность предложенной стратегии ранее была показана на примере катализаторов для процессов получения и очистки водорода: Pt0.5Co0.5/SiO2- и Au0.4Cu0.6/CeO2-катализаторов избирательного окисления СО. В настоящей работе получены нанопорошки Pt0.5M0.5 (M = Fe, Co, Cu), Pt0.33Ag0.67 и нанесенные катализаторы Pt0.5Cu0.5/Ce0.75Zr0.25O2 и Pt–CuOx/Ce0.75Zr0.25O2. Показано, что нанопорошки обладают каталитической активностью в реакции избирательного окисления СО в избытке Н2, а нанесенные Pt–Cu-катализаторы – в реакции низкотемпературной паровой конверсии СО.
ВВЕДЕНИЕ
Необходимость стабилизации и улучшения текущей неблагоприятной климатической ситуации, связанной с высокими концентрациями парниковых газов в атмосфере, способствует росту количества исследований в области водородной энергетики [1, 2]. На сегодняшний день водород является одной из главных альтернатив углеводородному топливу, в несколько раз превосходя его по энергетической ценности [3, 4]. С другой стороны, для получения водорода используется преимущественно углеродсодержащее сырье [4]. В связи с этим высокую актуальность имеет задача разработки каталитических систем и процессов, позволяющих получать водород с минимальными затратами энергии и выбросами углеродсодержащих соединений, а также катализаторов очистки водородсодержащего газа.
Водородно-воздушные топливные элементы с протонобменной мембраной (ПОМТЭ), интегрированные с системой генерации водорода из удобных для транспортировки и хранения жидких топлив (метанол, бензин или дизельное топливо), считаются одними из наиболее перспективных энергоустановок для мобильных транспортных платформ [5, 6]. Для питания ПОМТЭ требуются водородсодержащие смеси с высоким содержанием водорода (более 50 об.%) и концентрацией СО, который является каталитическим ядом для анодных катализаторов ПОМТЭ, ниже 0.001 об.% [7]. Конверсия жидких топлив в очищенный от СО водородсодержащий газ должна проводиться непосредственно на борту мобильной транспортной платформы в компактном конвертере по реакциям паровой или воздушной конверсии с последующей очисткой от СО в две стадии по реакциям паровой конверсии и избирательного окисления СО [8]. По этой причине требуется разработка новых активных и селективных катализаторов для снижения габаритов конвертера и обеспечения высокой эффективности системы получения водорода. В области дизайна катализаторов паровой конверсии СО важно обеспечить высокую активность катализаторов при температурах ниже 250°С, устойчивость к спеканию при температурах до 400°С и полное отсутствие активности в отношении нежелательных побочных реакций метанирования СО и СО2 [9, 10]. А для катализаторов избирательного окисления СО важными параметрами являются высокая активность и селективность в отношении окисления СО в большом избытке водорода при температурах ниже 200°С [11–13].
В мировом научном сообществе в последние годы наблюдается рост интереса к исследованию каталитических свойств биметаллических наночастиц [14, 15]. С одной стороны, он обусловлен появлением методов направленного синтеза таких систем с высокой дисперсностью, а с другой – с постепенным исчерпанием потенциала традиционных монометаллических систем. Переход от монометаллических к биметаллическим каталитическим системам кратно увеличивает количество возможных составов (сочетания различных металлов) и структур активных центров катализаторов (сплавы, сегрегированные частицы, интерметаллиды, металл-оксидные структуры и др.). Поэтому особенно актуальными становятся разработка и усовершенствование подходов к определению корреляций между структурой материалов и их каталитическими свойствами в различных реакциях.
При приготовлении биметаллических катализаторов или наночастиц основной задачей являются получение частиц с одинаковым, изначально заданным соотношением металлов и исключение формирования монометаллической фазы. К сожалению, простыми методами (совместная или последовательная пропитка растворами солей металлов) этого добиться практически невозможно, поэтому большинство существующих на данный момент и подходящих для таких целей процедур достаточно сложны. Однако решить эту задачу просто и эффективно позволяет использование в качестве предшественников двойных комплексных солей (ДКС), содержащих в своем составе комплексный катион одного металла и комплексный анион другого металла. Процедура приготовления нанесенных катализаторов схематично представлена на рис. 1 и состоит в последовательной или совместной пропитке носителя растворами, содержащими комплексные катионы и анионы металлов, сушке с образованием наночастиц ДКС в порах носителя и последующем разложении в токе Н2, Не или воздуха с образованием наночастиц сплавов или металл-оксидных структур. При этом состав наночастиц сплавов определяется стехиометрией ДКС.
Эффективность применения этого подхода неоднократно продемонстрирована авторами настоящей статьи. Так, в [16–19] для синтеза биметаллических частиц была использована ДКС [Pt(NH3)4][Co(C2O4)2(H2O)2] · 2H2O, полученная при смешении растворов комплексов [Pt(NH3)4](NO3)2 ⋅ 2H2O и (NH4)2[Co(C2O4)2] ⋅ 2H2O. Методами рентгенофазового анализа (РФА) и просвечивающей электронной микроскопии (ПЭМ) было подтверждено, что продуктом ее термического разложения в токе Не при 400°С в течение 2 ч является твердый раствор Pt0.5Co0.5 [16–19], в то время как в токе воздуха при 300°С за то же время формируются нанокомпозитные частицы Pt–Co3O4 [16]. В случае нанесенных на SiO2 частиц [17] образование ДКС происходило непосредственно на носителе, который последовательно пропитывали растворами монометаллических комплексов-предшественников. Путем последовательной пропитки CeO2, γ-Al2O3 и SiO2 растворами комплексов [Au(en)2](NO3)3 и (NH4)2[Cu(C2O4)2] · 2H2O, которая приводила к формированию на поверхности носителей плохо растворимой в воде ДКС [Au(en)2]2[Cu(C2O4)2]3 · · 8H2O, были получены и испытаны в реакции избирательного окисления СО Au–Cu-катализаторы [20]. В [21] ДКС [RhEn3]2[Pd(NO2)4]3 была использована для получения биметаллического катализатора Pd–Rh/γ-Al2O3. Способ получения биметаллических частиц из ДКС, не требующий прокаливания/восстановления при высоких температурах, описан в [22]. Раствором ДКС [Pd(NH3)4][AuCl4]2 в ацетоне при температуре –15°С пропитывали пористый кремний (PSi), содержащий поверхностные атомы Н. За счет этих атомов и происходило восстановление металлов. В результате на поверхности носителя были сформированы частицы твердого раствора Pd0.25Au0.75 и небольшое количество частиц Pd. Для сравнения: замена раствора [Pd(NH3)4][AuCl4]2 на водно-этанольный раствор комплексов H2[PdCl4] и H[AuCl4] (по 2 мас. % Pd и Au в катализаторе) привела к образованию на поверхности частиц твердого раствора Pd0.35Au0.65 и частиц Pd [22]. Учитывая, что изначально заданное соотношение металлов соответствовало стехиометрии Pd0.65Au0.35, можно заключить, что в случае смеси хлоридных комплексов металлов количество образующихся монометаллических частиц Pd намного больше по сравнению с ДКС. Таким образом, первый подход позволил получить активный компонент с более высоким содержанием биметаллической фазы. Кроме того, показано, что он обладает более высокой селективностью в реакции синтеза Н2О2 из Н2 и О2 [22].
В настоящей работе продемонстрирован подход к синтезу биметаллических нанопорошков и нанесенных катализаторов, основанный на использовании ДКС в качестве предшественников активной фазы. Представлены данные по активности полученных этим методом нанопорошков Pt0.5M0.5 (M = Fe, Co, Cu), Pt0.33Ag0.67 в реакции избирательного окисления СО и нанесенных катализаторов Pt0.5Cu0.5/Ce0.75Zr0.25O2 и Pt-CuOx/Ce0.75Zr0.25O2 в низкотемпературной паровой конверсии СО.
ЭКСПЕРИМЕНТАЛЬНАЯ ЧАСТЬ
Синтез нанопорошков и нанесенных катализаторов. Нанопорошок Pt был получен термическим разложением комплекса [Pt(NH3)4](NO3)2 · · 2H2O в токе Не при 400°С в течение 2 ч.
Нанопорошок Pt0.5Fe0.5 был приготовлен термическим разложением ДКС [Pt(NH3)5Cl][Fe(C2O4)3], синтезированной путем смешения растворов [Pt(NH3)5Cl]Cl3 и K3[Fe(C2O4)3], в токе Н2 или воздуха при температуре 400°С в течение 1 ч (скорость нагрева 10 К/мин). Нанопорошок Pt0.5Co0.5 был приготовлен разложением ДКС [Pt(NH3)4][Co(C2O4)2(H2O)2] · 2H2O, синтезированной путем смешения растворов [Pt(NH3)4]Cl2 и (NH4)2[Co(C2O4)2(H2O)2], в токе Не при 400°С в течение 2 ч (скорость нагрева 10 К/мин).
Нанопорошки Pt0.5Cu0.5 и Pt–CuOx были приготовлены термическим разложением ДКС [Pt(NH3)4][Cu(C2O4)2], синтезированной путем смешения растворов Cu(NO3)2 и [Pt(NH3)4](NO3)2 + K2C2O4, в токе Н2 или воздуха при температуре 400°С в течение 1 ч (скорость нагрева 10 К/мин).
Нанопорошок Ag0.67Pt0.33 был приготовлен термическим разложением комплекса Ag2[PtCl6], синтезированного путем смешения растворов AgNO3 и K2[PtCl6], в токе Н2 при температуре 500°С в течение 1 ч (скорость нагрева 10 К/мин).
Катализатор 1.9 мас. % Pt + 0.6 мас. % Cu/Ce0.75Zr0.25O2 (Pt0.5Cu0.5/CZ) получен пропиткой носителя Ce0.75Zr0.25O2 (ООО “Экоальянс”) раствором, содержащим соответствующее количество ДКС [Pt(NH3)4][Cu(C2O4)2]. После пропитки катализатор сушили при 80°С, затем восстанавливали в токе Н2 при 350°С в течение одного часа. Катализатор Pt–CuOx/CZ получали аналогично, но на этапе прокаливания заменили Н2 на воздух.
Физико-химические методы исследования. Рентгенофазовый анализ образцов проводили на дифрактометре ДРОН-RM4 (CuKα-излучение, графитовый монохроматор на отраженном пучке, детектор сцинтилляционный с амплитудной дискриминацией). Образцы готовили нанесением суспензии в спирте на полированную сторону кюветы из плавленого кварца. В качестве внешнего эталона использовали образец поликристаллического кремния (a = 5.4309 Å), приготовленный аналогичным образом. Регистрацию дифрактограмм проводили в пошаговом режиме в диапазоне углов 2θ 5°–120°. Параметры металлических фаз уточнены по всему массиву данных с помощью прикладной программы Powder Cell 2.4. Состав полученных биметаллических твердых растворов определяли с помощью градуировочных кривых зависимости объема, приходящегося на атом (V/Z, где V – объем элементарной ячейки, Z – число структурных единиц или, в данном случае, атомов в ней), от концентрации одного из металлов.
Образцы нанопорошков и нанесенных катализаторов изучали методом ПЭМ на микроскопе JEM 2010 (JEOL, Япония).
Исследование каталитической активности. Реакцию избирательного окисления СО изучали в проточном U-образном кварцевом реакторе (внутренний диаметр 3 мм) при атмосферном давлении и загрузке катализатора в реактор 25 мг (фракция ≤ 0.1 мм). Температуру измеряли хромель-алюмелевой термопарой, помещенной в центр слоя катализатора.
Каталитические эксперименты проводили в смеси следующего состава, об.%: 1.0 CO, 1.0 O2 и H2 – баланс; при скорости подачи реакционной смеси 80 000 см3 г–1 ч–1 (14 000 см3 г–1 ч–1 для Pt). Перед каждым экспериментом катализатор восстанавливали в течение 1 ч в Н2 при 200°С, затем катализатор выдерживали 1 ч в реакционной смеси при 25°С, после чего каталитические свойства определяли в нескольких циклах подъема/снижения температуры. Каталитические характеристики всех образцов были стабильны в течение не менее 20 ч в нескольких циклах повышения/снижения температуры.
Протекание реакции избирательного окисления СО характеризовали конверсией СО (XCO) и селективностью по СО (SCO), которые вычисляли по следующим выражениям:
Реакцию низкотемпературной паровой конверсии СО изучали в проточном U-образном кварцевом реакторе (внутренний диаметр 3 мм) при атмосферном давлении и загрузке нанесенного катализатора 125 мг (фракция 0.2–0.5 мм) или 50 мг нанопорошка. Температуру измеряли хромель-алюмелевой термопарой, помещенной в центр слоя катализатора.
Каталитические эксперименты проводили в смеси следующего состава, об.%: 10 CO, 15 СО2, 30 Н2О и 45 H2. Отклонение от заданных концентраций не превышало 1 об.%. Скорость подачи реакционной смеси составляла 30 000 см3 г–1 ч–1 для нанесенных катализаторов и 75 000 см3 г–1 ч–1 для нанопорошков. Перед экспериментами катализаторы Pt0.5Cu0.5/CZ и Pt0.5Cu0.5 восстанавливали в течение одного часа в Н2 при 350°С, катализаторы Pt–CuOx/CZ и Pt–CuOx также при 350°С в течение одного часа выдерживали в токе Ar, затем каталитические свойства определяли в нескольких циклах подъема/снижения температуры. Каталитические характеристики катализаторов были стабильны в течение не менее 20 ч в нескольких циклах повышения/снижения температуры.
Протекание реакции паровой конверсии СО характеризовали конверсией СО (XCO), которую рассчитывали по выражению, приведенному выше для окисления СО. Образования метана в ходе реакции не наблюдалось, поэтому селективность по целевой реакции полагали равной 100%.
Состав и концентрации компонентов газовой фазы в ходе избирательного окисления и паровой конверсии СО определяли при помощи хроматографа “ХРОМОС ГХ-1000”, оснащенного детектором по теплопроводности (колонка – молекулярные сита CaA) и пламенно-ионизационным детектором (колонка Porapak Q) с метанатором. Чувствительность по СО, СН4 и СО2 составляла ~1 ppm, по О2 и Н2 ~10 ppm. Концентрацию Н2О определяли по остатку из-за невозможности корректного определения напрямую. Разбаланс по углероду во всех экспериментах не превышал 1 отн.%.
РЕЗУЛЬТАТЫ И ИХ ОБСУЖДЕНИЕ
Фазовый состав и размеры области когерентного рассеяния (ОКР) свежеприготовленных биметаллических порошков были определены методом РФА (табл. 1). Как видно из данных таблицы, почти все нанопорошки, полученные в инертной или восстановительной атмосфере, содержат только одну фазу твердого раствора изначально заданной стехиометрии. В случае образца Pt0.5Fe0.5 соотношение металлов в основной фазе близко к ожидаемому, а доля обогащенной платиной фазы незначительна.
Таблица 1.
Фазовый состав нанопорошков (данные РФА)
Образец | Фазовый состав | Размер ОКР, нм |
---|---|---|
Pt0.5Cu0.5 | Упорядоченный твердый раствор (интерметаллид, пр. гр. R3m) состава Pt0.5Cu0.5 | 15 |
Pt0.5Co0.5 | Неупорядоченный твердый раствор состава Pt0.5Co0.5 (пр. гр. Fm3m) | 9 |
Pt0.5Fe0.5 | Смесь частично упорядоченного твердого раствора Fe0.55Pt0.45 (пр. гр. P4/mmm) и не-большого количества неупорядоченного твердого раствора Fe0.15Pt0.85 (пр. гр. Fm3m) | – |
Pt0.33Ag0.67 | Неупорядоченный твердый раствор состава Pt0.33Ag0.67 (пр. гр. Fm3m) | 5 |
Pt–CuOx | Смесь Pt, CuxPt1 –xO и ничтожно малого количества CuO | 4 (Pt) |
Данные ПЭМ в целом согласуются с данными РФА, из рис. 2 видно, что материалы представлены достаточно крупными (10–100 нм) агрегатами кристаллитов, размер которых соответствует данным РФА. Для ряда систем анализ межплоскостных расстояний и данные EDX-спектроскопии свидетельствуют о наличии некоторой неоднородности получаемых частиц по составу.
При исследовании нанесенных Pt–Cu-катализаторов анализ межплоскостных расстояний на снимках ПЭМ выявил наличие на поверхности носителя высокодисперсных (порядка 2 нм) частиц Pt (рис. 3). Размер частиц биметаллического компонента не удалось определить из-за их низкой контрастности. На рентгенограммах (не приведены) не наблюдалось рефлексов активного компонента.
Таким образом, несмотря на наличие неоднородностей, соотношение металлов в основной фазе нанопорошков в среднем было близко к заданному. Это подтверждает эффективность подхода к синтезу, основанному на разложении ДКС, который позволяет гарантированно и достаточно просто получать биметаллические наночастицы. В то же время использованный метод имеет ограничения по контролю размера и морфологии наночастиц по сравнению с подходами, основанными на получении золей металлических частиц в присутствии поверхностно-активных веществ.
Катализаторы на основе Pt исследовали в реакции избирательного окисления СО, протекающей в восстановительных условиях. СО2 и Н2О были единственными продуктами реакций окисления СО и Н2 соответственно. Образования метана и других продуктов гидрирования не наблюдалось. Полученные температурные зависимости конверсии СО и селективности представлены на рис. 4. Видно, что окисление СО на чистой Pt начинается при Т > ~150°C. В этом случае имеет место эффект блокировки поверхности Pt адсорбированным СО [23]. Полная конверсия СО наблюдается при температурах 190–240°С при очень низкой скорости потока смеси. Дальнейшее увеличение температуры приводит к ускорению реакции окисления водорода, которая поглощает весь имеющийся в системе кислород. Поэтому снижение конверсии СО при высоких температурах на Pt и других нанопорошках обусловлено именно конкуренцией между реакциями окисления СО и Н2 и дефицитом кислорода в системе.
Рис. 4.
Температурные зависимости конверсии СО (a) и селективности (б) при избирательном окислении СО на нанопорошках Pt0.5Cu0.5, Pt0.5Co0.5, Pt0.5Fe0.5, Pt0.33Ag0.67 и Pt. Состав смеси (об.%): 1 СО + 1 О2 + 98 Н2. Объемная скорость: 80 000 см3 г–1 ч–1. Эксперимент для Pt проводили при пониженном потоке 14 000 см3 г–1 ч–1.
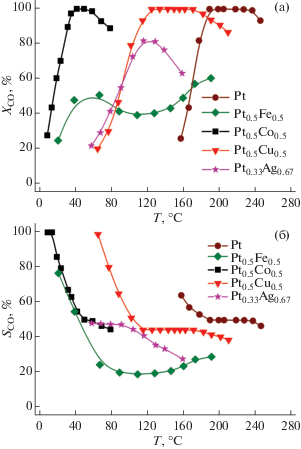
Введение Fe и Ag существенно снижает температуру протекания окисления СО (рис. 4а). Однако нанопорошки Pt0.5Fe0.5 и Pt0.33Ag0.67 оказались неселективными в реакции, преимущественно катализируя окисление Н2.
Нанопорошки Pt0.5Co0.5 и Pt0.5Cu0.5 показали высокие активность и селективность в реакции избирательного окисления СО, обеспечивая полную конверсию СО при низких температурах: 45–50°С для Pt0.5Co0.5 и 120–170°С для Pt0.5Cu0.5, т.е. в условиях, когда поверхность Pt еще достаточно плотно покрыта адсорбированными молекулами СО. Высокие конверсии СО на нанопорошках Pt0.5Co0.5 и Pt0.5Cu0.5 достигаются при селективностях 50–100% (рис. 4б). При этом окисление водорода начинается в тот момент (или в той точке реактора), когда весь СО уже израсходован. Иными словами, при низких температурах на поверхности частиц нанопорошков Pt0.5Co0.5 и Pt0.5Cu0.5 окисление водорода не протекает, пока в смеси присутствует СО, что и обеспечивает их высокую селективность.
В качестве объяснений такого поведения могут быть предложены следующие:
– бифункциональный характер катализаторов Pt0.5Co0.5 и Pt0.5Cu0.5, где СО активируется на атомах Pt, а О2 на атомах второго металла (Cu, Co) – “географический эффект” или “эффект ансамбля”;
– изменение теплоты адсорбции СО и/или Н2, О2 за счет изменения электронной структуры биметаллических наночастиц – “электронный” или “лигандный” эффект.
Свойства Pt–Cu-систем были исследованы в реакции низкотемпературной паровой конверсии СО. Нанопорошки Pt0.5Cu0.5 и Pt–CuOx не продемонстрировали активности при температурах ниже 350°С (рис. 5). В то же время в присутствии нанесенных аналогов, несмотря на гораздо меньшее содержание в них активного компонента, конверсия СО при 350°С составляет 45 и 30% для Pt–CuOx/CZ и Pt0.5Cu0.5/CZ соответственно. В условиях реакции паровой конверсии СО помимо целевой реакции могут протекать нежелательные побочные реакции метанирования оксидов углерода. Поэтому одной из основных характеристик катализаторов паровой конверсии является их селективность. Для катализаторов Pt0.5Cu0.5, Pt–CuOx, Pt–CuOx/CZ и Pt0.5Cu0.5/CZ выходная концентрация метана в ходе экспериментов не превышала 0.02 об. %. Иными словами, катализаторы были полностью селективны в отношении паровой конверсии СО.
Рис. 5.
Зависимость конверсии СО от температуры в ходе низкотемпературной паровой конверсии СО в присутствии Pt0.5Cu0.5, Pt–CuOx (50 мг, скорость потока 75 000 см3 г–1 ч–1), Pt0.5Cu0.5/CZ и Pt–CuOx/CZ (125 мг, скорость потока 30 000 см3 г–1 ч–1). Состав смеси (об.%): 10СО + 15CО2 + 45Н2 + 30H2O.
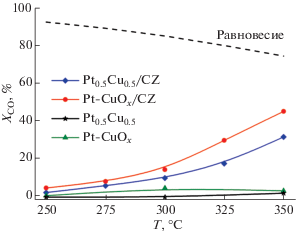
Несмотря на то что равновесная степень превращения не достигалась на Pt–CuOx/CZ и Pt0.5Cu0.5/CZ, очевидно, что высокая дисперсность активного компонента является важным параметром, существенно влияющим на активность катализатора. С другой стороны, активность нанесенных катализаторов по сравнению с нанопорошками также может быть связана со свойствами носителя, который, согласно [24–27], может принимать участие в каталитическом цикле. Для более однозначных выводов о причинах наблюдаемых явлений необходимо более детальное изучение нанесенных Pt–Cu катализаторов.
ЗАКЛЮЧЕНИЕ
Представлен простой и эффективный подход к синтезу нанесенных и массивных биметаллических наночастиц путем термического разложения двойных комплексных солей. Методами рентгенофазового анализа и просвечивающей электронной микроскопии подтверждено, что полученные таким способом в инертной или восстановительной атмосфере порошки сплавов практически не содержат монометаллической фазы, а стехиометрия биметаллической в среднем соответствует заданной. Порошки Pt0.5Co0.5, Pt0.5Cu0.5, Pt0.5Fe0.5 и Pt0.33Ag0.67 продемонстрировали активность в реакции избирательного окисления СО в избытке водорода при более низких температурах по сравнению с порошком чистой Pt; в случае Co- и Cu-содержащих образцов конверсия СО достигала 100%. Порошки Pt0.5Cu0.5 и Pt–CuOx, полученные из одной ДКС в восстановительной и окислительной атмосфере соответственно, не обладают активностью в реакции низкотемпературной паровой конверсии СО. В то же время в присутствии нанесенных катализаторов Pt0.5Cu0.5/CZ и Pt–CuOx/CZ, содержащих меньшее количество металлов на поверхности, конверсия СО при 350°С достигает 30 и 45% соответственно. Исследованные каталитические системы перспективны для применения в процессах получения и очистки водорода для питания топливных элементов, а предложенный подход к синтезу катализаторов достаточно прост и эффективен и может быть адаптирован для приготовления широкого спектра каталитических систем.
Авторы выражают благодарность Е.Ю. Герасимову за исследование образцов нанопорошков и нанесенных катализаторов методом просвечивающей электронной микроскопии.
Работа выполнена при финансовой поддержке Российского научного фонда (проект № 19-73-00157).
Список литературы
Thomas J.M., Edwards P.P., Dobson P.J., Owen G.P. // J. Energy Chem. 2020. V. 51. P. 405.
Abdin Z., Zafaranloo A., Rafiee A. et al. // Renew. Sustain. Energy Rev. 2020. V. 120. P. 109620.
Hwang H.T., Varma A. // Curr. Opin. Chem. Eng. 2014. V. 5. P. 42.
Nazir H., Louis C., Jose S. et al. // Int. J. Hydrogen Energy. 2020. V. 45. № 27. P. 13777.
Felseghi R.A., Carcadea E., Raboaca M.S. et al. // Energies. 2019. V. 12. P. 4593.
Staffell I., Scamman D., Velazquez Abad A. et al. // Energy Environ. Sci. 2019. V. 12. № 2. P. 463.
Ohi J.M., Vanderborgh N., Voecks G. // Safety, Codes and Standards Program. U.S. Department of Energy. 2016. P. 1.
Mishra A., Prasad R. // Bull. Chem. React. Eng. Catal. 2011. V. 6. № 1. P. 1.
Navarro R.M., Peña M.A., Fierro J.L.G. // Chem. Rev. 2007. V. 107. № 10. P. 3952.
LeValley T.L., Richard A.R., Fan M. // Int. J. Hydrogen Energy. 2014. V. 39. № 30. P. 16983.
Huang S., Hara K., Fukuoka A. // Energy Environ. Sci. 2009. V. 2. № 10. P. 1060.
Chin P., Sun X., Roberts G.W., Spivey J.J. // Appl. Catal. A. 2006. V. 302. № 1. P. 22.
Quinet E., Piccolo L., Daly H. et al. // Catal. Today. 2008. V. 138. № 1. P. 43.
Wei Z., Sun J., Li Y. et al. // Chem. Soc. Rev. 2012. V. 41. № 24. P. 7994.
Yu W., Porosoff M.D., Chen J.G. // Chem. Rev. 2012. V. 112. № 11. P. 5780.
Potemkin D.I., Filatov E.Y., Zadesenets A.V., So-byanin V.A. // Catal. Commun. 2017. V. 100. P. 232.
Potemkin D.I., Konishcheva M.V., Zadesenets A.V. et al. // Kinet. Catal. 2018. V. 59. № 4. P. 514.
Potemkin D.I., Saparbaev E.S., Zadesenets A.V. et al. // Catal. Ind. 2018. V. 10. P. 62.
Potemkin D.I., Filatov E.Y., Zadesenets A.V. et al. // Mater. Lett. 2020. V. 260. P. 126915.
Potemkin D.I., Semitut E.Y., Shubin Y.V. et al. // Catal. Today. 2014. V. 235. P. 103.
Vedyagin A.A., Shubin Y.V., Kenzhin R.M. et al. // Top. Catal. 2019. V. 62. № 1. P. 305.
Potemkin D.I., Maslov D.K., Loponov K. et al. // Front. Chem. 2018. V. 6. P. 85.
Snytnikov P.V., Belyaev V.D., Sobyanin V.A. // Kinet. Catal. 2007. V. 48. № 1. P. 93.
Shido T., Iwasawa Y. // J. Catal. 1992. V. 136. № 2. P. 493.
Germani G., Schuurman Y. // AlChE J. 2006. V. 52. № 5. P. 1806.
Jacobs G., Graham U.M., Chenu E. et al. // J. Catal. 2005. V. 229. № 2. P. 499.
Montini T., Melchionna M., Monai M., Fornasiero P. // Chem. Rev. 2016. V. 116. № 10. P. 5987.
Дополнительные материалы отсутствуют.
Инструменты
Российские нанотехнологии