Российские нанотехнологии, 2021, T. 16, № 5, стр. 635-643
ДРЕВНЕРУССКАЯ ЧЕРНЬ: ЭКСПЕРИМЕНТАЛЬНОЕ МОДЕЛИРОВАНИЕ И ИССЛЕДОВАНИЯ МИКРОСТРУКТУРЫ
А. Ю. Лобода 1, *, А. В. Мандрыкина 1, И. Е. Зайцева 2, Е. Ю. Терещенко 1, 3, Е. Б. Яцишина 1
1 Национальный исследовательский центр “Курчатовский институт”
Москва, Россия
2 Институт археологии РАН
Москва, Россия
3 Институт кристаллографии им. А.В. Шубникова ФНИЦ “Кристаллография и фотоника” РАН
Москва, Россия
* E-mail: lobodaau@mail.ru
Поступила в редакцию 24.01.2021
После доработки 15.02.2021
Принята к публикации 15.02.2021
Аннотация
Представлены результаты структурных исследований модельных черневых составов, воспроизводящих исторические составы черни крестов-энколпионов из Суздальского Ополья. Проанализированы особенности формирования фаз черневой массы на разных этапах ее расплавления. Сравнение результатов моделирования и исторической черни показало, что микроструктурные особенности археологических образцов соответствуют формированию черни расплавлением.
ВВЕДЕНИЕ
Чернь (ит. niello) представляет собой сплав металлов с серой, наносимый на поверхность изделий из золота, серебра, меди, бронзы и латуни для их декоративной отделки [1–3].
Одни из самых ранних записей о черневом искусстве оставил Плиний Старший в I в. н.э. [4]. Технологические особенности создания и нанесения черни изложены в “Записке о разных искусствах” монаха Теофила (XII в.) и трактате о ювелирном искусстве Бенвенуто Челлини (XVI в.) [1, 2, 5].
Известно много способов приготовления черни, так как почти каждый крупный мастер вносил некоторые изменения в пропорции компонентов состава. От состава черни зависит как ее прочность, так и цвет, варьирующийся от светло-серого до бархатисто-черного [1]. Металлические компоненты составов могут немного различаться, но, как правило, в состав черни входят Cu, Ag, Pb или Sn в различных пропорциях. Для лучшего ошлаковывания черни и предохранения ее от окисления в процессе варки в состав добавляют флюс [2]. В технологических указаниях к изготовлению черни отмечается, что полученный материал должен быть твердым и хрупким как стекло, если его куски по-прежнему можно сгибать, то чернь следует еще раз расплавить [2]. Полученный материал измельчают в порошок и наносят на подготовленную поверхность металла сухим или мокрым способом. Края изделия и места пайки, а также участки поверхности, которые необходимо защитить от попадания черни, обмазывают огнеупорной глиной, размешанной в воде [2].
Чернение было одним из ярких феноменов древнерусского ювелирного ремесла. Чернью украшались серебряные и бронзовые створки крестов-энколпионов, содержавших священные реликвии, а также ювелирные украшения. Основные приемы декорирования древнерусских изделий черневой массой описаны в [6], детальный анализ предметов с чернью из древнерусских кладов представлен в [7]. Позднее в российской литературе обобщающие работы по древнерусской черни не публиковались. В научный оборот вводились отдельные предметы с чернью без анализа состава черневой массы [8]. Опубликован только состав черни металлической накладки на гребень из Старой Ладоги [9].
Проблемам технологии изготовления изделий с чернью посвящена довольно обширная зарубежная литература. В 1980–1990 гг. были развернуты специальные исследовательские программы, имевшие своей целью изучение археологических предметов с чернью разных эпох для определения технологии чернения и этапов ее эволюции [6–19]. В последующие годы с открытием доступа к новейшему научному оборудованию исследователи вновь обращаются к проблемам черни.
Цель данной работы – моделирование процесса изготовления и нанесения на медный сплав черни, состав которой близок к историческим образцам, для изучения изменений черневой массы в ходе плавления, а также выявление последовательности изменения элементного состава формирующихся фаз черни, наблюдаемых в готовом изделии.
ОБЪЕКТЫ И МЕТОДЫ ИССЛЕДОВАНИЯ
В качестве “эталонов” для модельных образцов выбрали два энколпиона XI–XII вв. из Суздальского Ополья: с рисунками Распятия и Оранты из селища Федосьино (шифр С-34) (рис. 1а) и с изображениями крестов из селища Суворотское 8 (шифр С-12) (рис. 1б). Микропробы черни отбирали с участков с нарушениями черневого заполнения. Элементный состав металла и черневого декора данных крестов исследовали ранее в НИЦ “Курчатовский институт” [10]. На основании имеющихся данных изготовили два модельных состава черни:
– состав 1, основанный на данных о составе черни креста С-34 (Cu – 22.5, Pb – 53, Sn – 0.5, S – 11.5%).
– состав 2, основанный на данных о составе черни креста С-12 (Cu – 43, Pb – 35, Sn – 2, S – 14.5%).
Оба состава использовали для создания модельных образцов черни на медном сплаве.
Для получения металлической основы модельных образцов изготовили сплав меди с добавлением Zn, Pb и Sn (Cu 84.3%, Pb 3.5%, Sn 1.2%, Zn 10.8%), близкий по составу к медному сплаву крестов С-12 и С-34 [10]. Слиток отливали в изложницу в той же печи, что и чернь, откатывали в вальцах для уплощения и разделяли на мелкие пластины. На пластины гравировкой наносили канавки для черни, поверхность зашлифовывали.
Получаемые в ходе эксперимента образцы черни изучали на разных стадиях плавления. Таким образом, фазовый состав черневой массы исследовали на десяти образцах, два из которых были извлечены из археологических объектов (образцы С-12 и С-34), а восемь получены в ходе экспериментов по моделированию процесса создания черневого состава и нанесения его на металл (образцы 1–8, табл. 1).
Таблица 1.
Параметры приготовления модельных образцов
Образец | Состав черни | Флюс | Способ нанесения |
---|---|---|---|
1 | 1 | 0.1 | 1 |
2 | 1 | 2 | 1 |
3 | 2 | 2 | 1 |
4 | 1 | 0.2 | 2 |
5 | 1 | 1 | 2 |
6 | 2 | 1 | 1 |
7 | 2 | 1 | 1 |
8 | 1 | 1 | 1 |
Из-за малого размера исторические образцы черни фиксировали в эпоксидной смоле и зашлифовывали. Шесть модельных образцов, представляющих собой пластины из медного сплава с нанесенными на них экспериментальными черневыми составами, также зашлифовывали.
Исследования объектов проводили методом растровой электронной микроскопии (РЭМ) с энергодисперсионным рентгеновским микроанализом (ЭРМ) на двухлучевом растровом электронно-ионном микроскопе с фокусированным ионным пучком Versa 3D (Thermo Fisher Scientific) с системой ЭРМ (EDAX) при ускоряющем напряжении 30 кВ в режиме высокого вакуума (2 × × 10–3 Па). Изображения образцов получали регистрацией обратно рассеянных электронов.
ЭКСПЕРИМЕНТ ПО МОДЕЛЬНОМУ ИЗГОТОВЛЕНИЮ ЧЕРНИ
Эксперимент по изготовлению и наложению черни состоял из двух основных этапов:
– изготовление первичной черневой массы (два состава) в литьевой печи при температуре ~750°С.
Состав 1. Навеска компонентов перед плавкой составила: Cu – 4.4, Pb – 10.6, Sn – 1.1, S – 23.1 г.
Состав 2. Навеска компонентов перед плавкой составила: Cu – 8.4, Pb – 7.0, Sn – 4.0, S – 30 г;
– нанесение черни на металлические пластины.
Полученные черневые составы измельчали в порошок перетиранием между полированными кусками мрамора.
В качестве флюса использовали порошок буры (натриевая соль тетраборной кислоты), вскипяченный в воде. Измельченный порошок черни смешивали с флюсом в разных пропорциях и закладывали в канавки на пластинах двумя способами:
– способ 1 (Сп 1) – закладывание порошка в канавки “с горкой” и расплавление на открытом огне.
– способ 2 (Сп 2) – заливание расплавленной в тигле черни на пластину с канавками.
Все полученные модельные пластины с черневой массой запиливали напильником, затем шлифовали наждачной бумагой в порядке уменьшения фракции абразивного зерна. В результате получили заполированные модельные образцы черни на пластинах (рис. 1в).
Количество флюса, добавленное в состав образца, оказало значительное влияние на скорость его расплавления:
– Ф 0.1. Черневой состав 2 без добавления буры расплавился на пластине не до конца (образец 1);
– Ф 0.2. Черневой состав 2 без добавления буры, плавка которого проходила в тигле, расплавился полностью, после чего расплавленный состав налили на пластину (образец 4);
– Ф 1. Добавление малого количества буры (один к десяти по весу черневой массы) значительно ускорило расплавление черневого состава (образцы 5–8);
– Ф 2. Дальнейшее увеличение количества буры (четыре к десяти по весу черневой массы) в черневом составе (образцы 2 и 3) привело к уменьшению времени его расплавления по сравнению с экспериментом Ф 1.
РЕЗУЛЬТАТЫ И ИХ ОБСУЖДЕНИЕ
Исследование исторических образцов черневых составов методом РЭМ/ЭРМ позволило определить элементный состав и особенности микроструктур, сформировавшихся в процессе плавления черневой массы (табл. 2).
Таблица 2.
Элементный состав исторических образцов черни
С-12 (рис. 2) | С-34 (рис. 3) | ||||||||||||
---|---|---|---|---|---|---|---|---|---|---|---|---|---|
Обл. 1 | Обл. 2 | Обл. 3 | Обл. 4 | Обл. 1 | Обл. 2 | Обл. 3 | Обл. 4 | Обл. 5 | |||||
S | 19.1 | 20.1 | 9.5 | 6.9 | 15.7 | 13.7 | 14.3 | 14.1 | 12.8 | 12.4 | 18.1 | ||
Pb | 15.0 | 4.3 | 47.3 | 83.5 | 17.7 | 23.9 | 23.2 | 90.4 | 86.9 | 21.1 | |||
Cu | 26.4 | 75.1 | 35.2 | 8.3 | 35.5 | 80.6 | 83.6 | 81.1 | 62.5 | 63.5 | 7.9 | 10.7 | 60.2 |
Sn | 5.4 | 1.1 | 0.2 | 0.2 | 0.1 | 0.5 | 0.1 | ||||||
Zn | 38.9 | 1.3 | 29.9 | 0.6 | 0.9 | 0.2 | |||||||
Fe | 0.6 | 0.4 | 0.8 | 0.9 | 0.2 | 0.3 | 0.2 | 0.4 | 0.5 | 1.0 | 1.3 | 0.3 | |
Ni | 0.2 | 0.5 | 0.4 | 0.2 | 0.2 | 0.1 | 0.2 | 0.3 | 0.6 | 0.7 | 0.2 |
РЭМ/ЭРМ-исследование шлифа черни образца С-12 показало наличие четырех областей (рис. 2, табл. 2): мелких темных областей Cu–S–Pb–Zn (области 1), темных областей Cu–S–Pb (области 2), серых областей со светлыми дендритами Pb–Cu–S–Sn (области 3) и светлых конгломератов Pb–Cu–Sn (области 4).
В образце С-34 методом РЭМ/ЭРМ обнаружили пять различных областей (рис. 3, табл. 2): мелкие темные области Cu–Pb–S–Zn–Sn (области 1), темные области Cu–S (области 2), серые области со светлыми дендритами Cu–Pb–S–Sn (области 3), светлые конгломераты Cu–Pb–Sn (области 4), а также серые области Cu–Pb–S–Sn (области 5).
Исследования РЭМ/ЭРМ модельных образцов черни, изготовленных в ходе эксперимента, проводили дважды: после первичного переплавления черневых составов и после нанесения черни на металлические пластины.
После первого этапа эксперимента – переплавления всех компонентов черни – определили общий элементный состав черневой массы 1 и 2:
– состав 1. Cu 18.8–31.7, Pb 53.2–62.3, Sn 3.2–3.5, S 6.4–10.2%;
– состав 2. Cu 43.9–77.2, Pb 7.8–29.8, Sn 3.4–12.3, S 7.5–12.2%.
После второго этапа эксперимента для модельных образцов 1–8 (табл. 1) методом РЭМ/ЭРМ уточняли элементный состав и распределение элементов по фазам.
Модельный образец 1 (порошок черни без добавления флюса) растекся слабо. РЭМ/ЭРМ-исследование шлифа черни данного образца показало наличие в нем двух фаз: основную массу – Cu–S–Pb–Zn–Sn (зона 1 на рис. 4, табл. 3) и светлые включения – Pb–Cu–S (зона 2 на рис. 4, табл. 3).
Рис. 4.
РЭМ-изображение в обратно рассеянных электронах образца 1. Цифрами 1, 2 обозначены области различного состава.
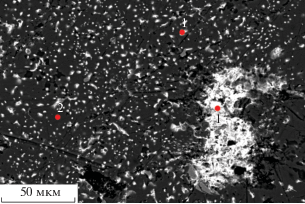
Таблица 3.
Элементный состав модельных образцов черни
образец 1 (состав 1, Сп 1, Ф 0.1, рис. 4) | |||||||
S | Pb | Cu | Sn | Zn | Fe | Ni | |
зона 1 | 11.4 | 3.5 | 83.2 | 1.5 | 0.3 | 0.1 | |
11.8 | 2.9 | 83.4 | 1.5 | 0.3 | 0.1 | ||
зона 2 | 1 | 89.3 | 8.4 | 0.3 | 0.8 | 0.3 | |
1.2 | 84.2 | 12.9 | 0.4 | 0.7 | 0.5 | ||
образец 2 (состав 1, Сп 1, Ф 2, рис. 5) | |||||||
S | Pb | Cu | Sn | Zn | Fe | Ni | |
обл. 1 | 20.7 | 9.4 | 10.5 | 2 | 57 | 0.4 | |
19 | 14.4 | 8.1 | 1.9 | 56.2 | 0.4 | ||
обл. 2 | 12.2 | 3.3 | 82.3 | 1.9 | 0.3 | 0.1 | |
12 | 3.7 | 80.9 | 3.1 | 0.3 | 0.1 | ||
обл. 3 | 13.1 | 38.2 | 41.5 | 6.2 | 0.3 | 0.5 | 0.2 |
13 | 36.9 | 42.4 | 6.7 | 0.4 | 0.5 | 0.2 | |
обл. 4 | 93.1 | 3.4 | 1.2 | 0.7 | 1 | 0.6 | |
обл. 5 | 12 | 25.4 | 60.8 | 0.7 | 0.6 | 0.4 | 0.1 |
12.1 | 24.6 | 61.8 | 0.5 | 0.6 | 0.4 | 0.1 | |
образец 3 (состав 2, Сп 1, Ф 2, рис. 6) | |||||||
S | Pb | Cu | Sn | Zn | Fe | Ni | |
обл. 1 | 19 | 9.8 | 17 | 3.3 | 50.4 | 0.3 | 0.2 |
18.4 | 11.7 | 20.7 | 3.3 | 45.3 | 0.4 | 0.2 | |
обл. 2 | 11.4 | 2 | 81.99 | 2.96 | 1.31 | 0.28 | 0.14 |
12.1 | 4.03 | 83.03 | 0.44 | 0.26 | 0.13 | ||
обл. 3 | 13.2 | 28.4 | 49 | 8.5 | 0.6 | 0.3 | |
12.8 | 29 | 47.6 | 9.3 | 0.5 | 0.6 | 0.3 | |
обл. 4 | 95.1 | 1.9 | 1.5 | 0.9 | 0.5 | ||
обл. 5 | 7.1 | 62.4 | 29.1 | 0.7 | 0.5 | 0.4 | |
1 | 67.5 | 31 | 0.3 | 0.1 | |||
образец 4 (состав 1, Сп 2, Ф 0.2, рис. 7) | |||||||
S | Pb | Cu | Sn | Zn | Fe | Ni | |
обл. 1 | 18.6 | 9 | 10 | 1.6 | 60.1 | 0.4 | 0.2 |
обл. 2 | 11.5 | 3.6 | 83.7 | 1 | 0.3 | 0.1 | |
11.5 | 2.8 | 84.2 | 1 | 0.3 | 0.2 | ||
обл. 3 | 13 | 42.7 | 39.1 | 4.2 | 0.3 | 0.5 | 0.2 |
обл. 4 | 1.6 | 94.1 | 2.6 | 0.4 | 0.3 | 0.7 | 0.4 |
1.9 | 94.7 | 1.7 | 0.3 | 1 | 0.5 | ||
обл. 5 | 11.7 | 25.1 | 61.7 | 0.5 | 0.5 | 0.4 | 0.1 |
11.7 | 25.1 | 61.7 | 0.5 | 0.6 | 0.3 | 0.2 | |
образец 5 (состав 1, Сп 2, Ф 1, рис. 8) | |||||||
S | Pb | Cu | Sn | Zn | Fe | Ni | |
обл. 1 | 18.1 | 16.3 | 14.8 | 1.9 | 48.4 | 0.3 | 0.2 |
17.4 | 15.4 | 15.4 | 2 | 49.3 | 0.3 | 0.2 | |
обл. 2 | 11.6 | 3.3 | 84.1 | 0.8 | 0.3 | 0.1 | |
обл. 3 | 12.4 | 40.1 | 42.9 | 3.4 | 0.5 | 0.5 | 0.2 |
12.1 | 43.3 | 41.4 | 2.1 | 0.4 | 0.5 | 0.2 | |
обл. 4 | 1.2 | 93.3 | 3.3 | 0.5 | 0.3 | 1 | 0.5 |
обл. 5 | 11.8 | 24.8 | 61.8 | 0.4 | 0.5 | 0.4 | 0.2 |
11.8 | 25.7 | 61 | 0.4 | 0.5 | 0.5 | 0.1 | |
образец 6 (состав 2, Сп 1, Ф 1, рис. 9) | |||||||
S | Pb | Cu | Sn | Zn | Fe | Ni | |
обл. 1 | 18.2 | 9 | 14.7 | 2.2 | 55.4 | 0.4 | 0.2 |
обл. 2 | 10.4 | 3.2 | 84.9 | 1.2 | 0.3 | 0.2 | |
9.8 | 7.1 | 80.9 | 0.1 | 1.8 | 0.3 | 0.1 | |
10.2 | 3.1 | 84.8 | 0.2 | 1.3 | 0.3 | 0.1 | |
обл. 3 | 11.3 | 48.2 | 9.5 | 30.4 | 0.5 | 0.2 | |
11.6 | 49.8 | 9.5 | 28.7 | 0.5 | |||
обл. 4 | 0.9 | 91 | 3.5 | 2.8 | 0.3 | 1 | 0.5 |
89.9 | 3.8 | 4.7 | 1.1 | 0.6 | |||
обл. 5 | 30.4 | 2 | 0.4 | 0.3 | 67 | ||
30.2 | 1.9 | 0.5 | 0.3 | 67.3 | |||
образец 7 (состав 2, Сп 1, Ф 1, рис. 10) | |||||||
S | Pb | Cu | Sn | Zn | Fe | Ni | |
обл. 1 | 19.2 | 8.2 | 8.7 | 1.8 | 61.6 | 0.4 | 0.1 |
обл. 2 | 10.9 | 1.2 | 0.3 | 3.4 | 0.1 | 84.1 | |
11.6 | 1.2 | 0.3 | 2.6 | 0.1 | 84.2 | ||
обл. 3 | 13.1 | 32.7 | 45.2 | 8 | 0.4 | 0.5 | 0.2 |
13.2 | 32 | 45.8 | 8 | 0.3 | 0.5 | 0.2 | |
обл. 4 | 1.1 | 91.1 | 2.4 | 4.3 | 0.8 | 0.4 | |
0.2 | 88.8 | 3.6 | 5.2 | 0.5 | 1.1 | 0.6 | |
0.7 | 92.1 | 2.7 | 3.2 | 0.2 | 0.7 | 0.5 | |
обл. 5 | 31.2 | 1.6 | 0.4 | 0.2 | 66.6 | ||
образец 8 (состав 1, Сп 1, Ф 1, рис. 11) | |||||||
S | Pb | Cu | Sn | Zn | Fe | Ni | |
обл. 1 | 19.7 | 9.7 | 15.8 | 1.8 | 52.4 | 0.4 | 0.2 |
18.7 | 11.6 | 16.6 | 1.5 | 51.3 | 0.3 | 0.2 | |
обл. 2 | 12 | 2.7 | 0.3 | 0.1 | 84.9 | ||
11.6 | 3.8 | 0.3 | 0.2 | 84.1 | |||
обл. 3 | 12.1 | 45.3 | 6.5 | 34.9 | 0.7 | 0.5 | |
12.4 | 36.9 | 43.8 | 5.8 | 0.4 | 0.5 | 0.3 | |
обл. 4 | 4.5 | 67.4 | 26.1 | 0.5 | 0.3 | 0.9 | 0.4 |
3.2 | 83.2 | 10.5 | 1.2 | 0.4 | 0.9 | 0.6 | |
обл. 5 | 12.3 | 21 | 64.8 | 0.4 | 0.9 | 0.5 | 0.2 |
12.7 | 22.9 | 63.2 | 0.4 | 0.5 | 0.3 |
Остальные модельные образцы показали общее характерное фазовое разделение. Во всех случаях черневая масса хорошо растеклась. В образцах 2–8 зафиксировали образование пяти областей. Цвет области отражает контраст, обусловленный средним значением электронной плотности (рис. 5–11, табл. 3): мелкие темные области – Cu–Pb–S–Zn (обл. 1, табл. 3), крупные темные области – Cu–Pb–S (обл. 2, табл. 3), серые области со светлыми дендритами – Cu–Pb–S–Sn (обл. 3, табл. 3), светлые конгломераты – Pb–Sn (обл. 4, табл. 3), серые области – Cu–Sn–Pb (обл. 5, табл. 3).
Рис. 7.
РЭМ-изображение в обратно рассеянных электронах образца 4. Цифрами 1–5 обозначены области различного состава.
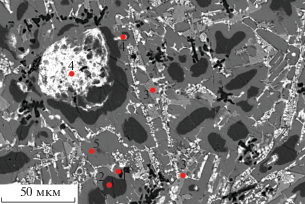
После нанесения модельной черни на металлические пластины в ее составе наблюдали заметное содержание цинка, хотя исходные составы 1 и 2 его не содержат. Видимо, при взаимодействии расплавленной черневой массы с металлической основой цинк, как наиболее легкоплавкая часть металла, переходит в состав черни и принимает участие в формировании фаз (табл. 3). Вероятно, аналогичный процесс происходил при создании исторических образцов.
Во всех образцах не обнаружили следов флюса, вероятно, в процессе переплавки флюс либо выгорает, либо выходит на поверхность и удаляется при шлифовании образца.
Зона контакта металла и черневой вставки имеет структуру, отличную от основной черневой массы, характеризующуюся более высокой пористостью, а также распределенными непосредственно вдоль края металла менее расплавленными областями черневой массы, которые образуются в процессе диффузионного сцепления расплавляемого порошка черни с поверхностью металла (рис. 12).
Рис. 12.
РЭМ-изображение в обратно рассеянных электронах образца 6. Зона контакта черневой массы с металлом.
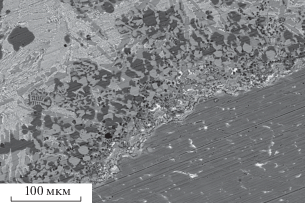
Сопоставление модельных образцов показало, что все экземпляры, кроме образца 1, представляют собой набор фаз, схожих по составу, но различающихся количественным соотношением элементов. Систематических различий в структуре черни, расплавленной на металлической пластине (Сп 1) и залитой на металл в расплавленном виде (Сп 2), не обнаружили.
Образец 1 представляет собой спекшуюся, но слабо расплавившуюся массу (рис. 4). Чернь данного образца характеризуется выделением конгломератов Pb–Cu–S и сформированной областью Cu–S–Pb–Zn–Sn. Изучение и сравнение данной микроструктуры с другими объектами (образцы 2–8) позволили проследить последовательность образования фаз при расплавлении черневой массы.
Дальнейшее расплавление черневого состава исследовали на примере микроструктур образцов 2–8. Установлено, что расплавление черни приводит к развитию двух первичных зон, которые затем постепенно исчезают, приводя к формированию новых фаз. Из области Cu–S–Pb–Zn–Sn (зона 1) (рис. 4) и конгломератов, преимущественно содержащих свинец Pb–Cu–S (зона 2 и области 4) (рис. 4), постепенно формируются серые зоны со светлыми дендритами Cu–Pb–S–Sn (области 3). В некоторых образцах дендриты частично сохраняют форму конгломератов (рис. 7, 8). Из серого поля Cu–Sn–Pb (области 5) также постепенно начинают формироваться мелкие дендриты. Таким образом, идеально растворенная черневая масса должна представлять собой серую область с достаточно равномерными светлыми дендритами (области 3) и отдельными свинцовыми конгломератами (области 5), которые можно условно назвать “финальными” фазами. Однако такой идеальной картины не наблюдали ни в одном модельном образце, все они представляют собой массу разной степени расплавления.
Весь массив исследованных образцов разделяется на три категории:
– образец со слабо расплавившимся составом (образец 1);
– образцы с хорошо расплавившимся составом, быстро нагретые до расплавления черни (образцы 2–5);
– образцы с хорошо расплавившимся составом, медленно нагретые до расплавления черни (образцы 6–8).
Между образцами второй и третьей группы наблюдается значительная разница.
Быстрое расплавление черни на образцах 2 и 3 (рис. 5 и 6 соответственно) достигалось за счет увеличения количества добавленного в порошок черни флюса. Черневые составы образцов 4 и 5 (рис. 7 и 8 соответственно), содержащие меньшее количество флюса, подвергались интенсивному нагреву в тигле, а уже затем наливались на пластину. Микроструктура всех образцов второй группы крайне неоднородна, в ней в полной мере представлены все описанные выше фазы: первичные (зоны 1 и 2), переходные (области 1, 2, 5) и финальные (области 3 и 4).
Чернь образцов третьей группы (образцы 6–8, рис. 9–11 соответственно) готовили при продолжительном равномерном нагреве с малым количеством флюса. В микроструктурах данных образцов наблюдаются более равномерный рост дендритов в финальных фазах (область 3) и меньшее количество переходных областей (области 1, 2, 5).
Следовательно, образование однородной дендритной структуры в массе черни зависит не только от достижения определенной температуры, но и от времени расплавления. При этом образцы, приготовленные из состава 2 с меньшим содержанием свинца, быстрее образуют финальную область 3 с равномерными дендритами (образцы 3, 6, 7). Образцы с составом черни 1 при схожих условиях нагрева дольше сохраняют неоднородную структуру (образцы 2, 4, 5, 8).
Определить температуру, достигнутую мастером при изготовлении древних изделий с чернью, по количеству и соотношениям фаз в расплавленной черневой массе сложно, так как экспериментальное моделирование показало, что добавление даже малого количества флюса при плавке значительно понижает температуру плавления черни. Большое количество флюса в черневой массе позволяет ей расплавиться быстрее, однако ее структура остается неоднородной. При этом исследование образцов методами РЭМ/ЭРМ позволило установить, что после расплавления в изделии не остается следов флюса, а значит его количество, использованное при плавке, определить невозможно.
ЗАКЛЮЧЕНИЕ
В результате исследования различных по степени и условиям расплавления образцов черневых масс, моделирующих два состава исторической черни с крестов-энколпионов, найденных в Суздальском Ополье, определен элементный состав образовавшихся в черневой массе фаз, а также выявлена последовательность фазообразования в процессе расплавления черни на изделиях.
Сопоставление модельных и исторических образцов выявило наличие одинакового набора фаз во всех черневых массах (кроме образца 1) как в модельных образцах 2–8, так и в исторических С-12 и С-34. Однако в каждом образце количественное соотношение фаз было индивидуальным и зависело как от степени расплавления черни, так и от особенностей ее элементного состава.
При интерпретации микроструктур исторических образцов черни необходимо учитывать ряд фактов, выявленных в результате проведенных в данной работе модельных экспериментов:
– способ нанесения черни на пластину не повлиял на итоговую микроструктуру массы;
– хрупкость исследованных черневых составов не позволяет создавать черневой узор на изделии вбиванием полос черни в канавки, как предполагали некоторые исследователи [10, 11];
– изменения в составе черни оказывают значительное влияние как на время расплавления черневой массы, так и на итоговую микроструктуру состава, что приводит к необходимости индивидуального исследования каждого изделия с чернью;
– наличие и количество использованного при плавке черни флюса не детектируется в составе получаемого образца, но оказывает значительное влияние на температуру плавления черневой массы и, как выяснилось в ходе модельного эксперимента, на ее микроструктуру;
– цинк, обнаруженный в составе черни, может попадать в нее при нагреве цинксодержащей металлической основы;
– более пористая и зернистая структура зоны контакта черни и металла может отличаться по своим физическим свойствам от основной черневой массы. В перспективе именно более быстрое разрушение этой зоны может приводить к образованию пустот между черневой вставкой и металлической канавкой, которые наблюдаются на многих археологических объектах.
Согласно результатам проведенной работы можно предположить, что чернь на крестах С-12 и С-34 была создана расплавлением черневой массы. Оба образца демонстрируют хорошее расплавление черни и высокую фазовую неоднородность, что может указывать на недолговременное температурное воздействие. Более детальное определение условий расплавления черни в исторических образцах на данном этапе работы невозможно и требует дальнейшего изучения.
Список литературы
Постникова-Лосева М.М., Платонова Н.Г. Русское черневое искусство. М.: Искусство, 1972. 144 с.
Флеров А.В. Материаловедение и технология художественной обработки металлов. М.: Высшая школа, 1981. 288 с.
Макаров Н.А., Зайцева И.Е., Грешников Э.А. // Археологические вести. 2017. № 23. С. 291.
Плиний Старший. Естественная история / Пер. Тароняна Г.А. М.: Ладомир, 1994. Книга XXXIII.XX.
Теофил Пресвитер // Сообщения Центральной научно-исследовательской лаборатории по консервированию и реставрации музейных художественных ценностей. 1963. Вып. 7. Кн. 23–24.
Рыбаков Б.А. Ремесло Древней Руси. М.: Наука, 1948. 803 с.
Макарова Т.И. Черневое дело Древней Руси. М.: Наука, 1986. 166 с.
Ениосова Н.В. // Древнерусский некрополь Пскова X–начала XI века. Т. II. СПб.: Нестор-История, 2016. С. 518.
Горлов К.В., Григорьева Н.В. // Археологические вести. Вып. 23. СПб.: ИИМК РАН, 2017. С. 285.
Зайцева И.Е., Грешников Э.А., Велигжанин А.А. и др. // Российская археология. 2019. № 3. С. 51.
Грешников Э.А., Терещенко Е.Ю., Велигжанин А.А. и др. Труды V (XXI) Всероссийского археологического съезда в Барнауле – Белокурихе: сборник научных статей: в 3 т. / отв. ред. Деревянко А.П., Тишкин А.А. Т. III. Барнаул: Изд-во Алт. ун-та, 2017. С. 23.
Колобылина Н.Н., Грешников Э.А., Васильев А.Л. и др. // Кристаллография. Т. 62. № 4. 2017. С. 543.
La Niece S. // Antiquaries J. 1983. V. 63. № 2. P. 279.
Moss A.A. // Studies in Conservation. V. 1. № 2. The international Institute for the Concervation of Museum Objects. L. 1953. P. 49.
Northover P., La Niece S. // From Mine to Microscope – Advances in the Study of Ancient Technology / Eds. Shortland A.J. et al. Oxford: Oxbow, 2009. P. 2060.
Nors N.A., MacLeod I.D. // Conservation of Marine Archaeological Objects / Ed. Colin Pearson. L.: Butterworths, 1987. P. 68.
Petersen K. S. // J. Danish Archaeology. 1994–1995. № 12. P. 133.
Petersen K.S. Metalhandvsrk og handvsrkspladser frayngre germansk jernalder, vikingetid og tidlig middelalder Rapport fra et seminar pa Hollufgard den 22. Oktober 2001 Re-digeret af Mogens Bo Henriksen // Skrifter fra Odense Bys Museer V. 9 Odense. 2002. P. 63.
Wolters J. // Europäische Technik im Mittelalter 800–1200. Berlin. 1996. S. 169.
Дополнительные материалы отсутствуют.
Инструменты
Российские нанотехнологии