Российские нанотехнологии, 2022, T. 17, № 6, стр. 730-736
ИССЛЕДОВАНИЕ ВЛИЯНИЯ ГИДРОМЕХАНИЧЕСКОГО ВОЗДЕЙСТВИЯ НА МАССИВ ГОРИЗОНТАЛЬНО ОРИЕНТИРОВАННЫХ УГЛЕРОДНЫХ НАНОТРУБОК
Н. А. Вовк 1, 2, М. А. Тархов 1, Н. В. Порохов 1, Е. Р. Тимофеева 1, А. М. Тагаченков 1, М. В. Шибалов 1, *, И. В. Трофимов 1, А. М. Мумляков 1, А. В. Коновалов 1, Е. В. Зенова 1, В. В. Сень 1
1 Институт нанотехнологий микроэлектроники РАН
Москва, Россия
2 Национальный исследовательский университет “Высшая школа экономики”
Москва, Россия
* E-mail: shibalov.m@inme-ras.ru
Поступила в редакцию 25.08.2021
После доработки 01.10.2021
Принята к публикации 01.10.2021
Аннотация
Исследовано влияние гидромеханического воздействия на массив горизонтально ориентированных углеродных нанотрубок (УНТ) во время создания функционального слоя будущих приборов. Слой УНТ формировался методом нанесения спреем. Продемонстрирован метод контроля поверхностного сопротивления слоя нанотрубок, нанесенного на поверхность подложки, до и после гидромеханического воздействия. Проведены исследования поверхности пластин с УНТ методом сканирующей электронной микроскопии и спектроскопии комбинационного рассеяния света. Представлена оригинальная технология равномерного нанесения слоя УНТ с заданными свойствами. Полученные результаты показывают, что предлагаемая технология позволяет получать на поверхности подложки слой УНТ с заданным значением поверхностного сопротивления, зависящего от концентрации используемой суспензии и последующей обработки получаемых слоев.
ВВЕДЕНИЕ
Углеродные нанотрубки (УНТ) – наноразмерный материал, обладающий уникальными физико-химическими свойствами как для фундаментальных, так и для прикладных исследований [1, 2]. В настоящее время проводится множество работ по созданию структур и приборов на основе УНТ для нужд электроники, биологии, промышленности [3–5]. Параметры УНТ, такие как диаметр, электропроводность, длина, зависят от способа их синтеза [6–8].
Современная электроника стремится к внедрению новых материалов в приборы, увеличению быстродействия и уменьшению размеров устройств. Интегрирование УНТ в приборы подразумевает создание функционального слоя для таких приборов, как транзистор на основе УНТ [9], диод Шоттки [10] и так далее. Известны несколько способов формирования слоев из УНТ: каталитический синтез [11], нанесение суспензии с УНТ [12]. В методе нанесения суспензии параметры слоя из УНТ зависят от способа ее осаждения на подложку [13, 14], ее состава [15, 16], внешнего воздействия после нанесения слоя на пластину [5].
При нанесении слоя УНТ из суспензии присутствуют проблема равномерности распределения УНТ по всей поверхности пластины и наличие конгломератов, увеличивающих количество дефектов при проведении дальнейших технологических операций. Известен технологический подход, позволяющий частично решить данные недостатки, предполагающий ультразвуковую (УЗ) обработку образцов в жидкости для улучшения равномерности слоя УНТ и достижения заданного поверхностного сопротивления [5]. Однако этот метод сильно сужает диапазон характеристик получаемого слоя УНТ и не решает проблему устранения дефектов до уровня изготовления опытных серий разрабатываемых устройств.
В данной работе исследовался метод обработки слоя УНТ гидромеханическим воздействием, так как он позволяет равномерно обрабатывать пластины различных размеров и толщин, а также широко применяется в микроэлектронике. Основная идея предлагаемого метода воздействия на слой с УНТ заключается в последовательной многократной обработке поверхности вращающейся подложки струей жидкости.
В соответствии с принципами обработки поверхности гидромеханическим воздействием, подробно описанными в [17], во время обработки на частицу, находящуюся на поверхности подложки, воздействуют различные силы (рис. 1). Как видно из рис. 1, основными силами, удерживающими частицу на поверхности подложки, являются сила Ван-дер-Ваальса Fvdw-s, электростатическая сила притяжения между частицей и подложкой Fel-s и прижимная сила со стороны потока воды Fload. Силами, инициирующими передвижение частицы по подложке, являются горизонтальная проекция силы со стороны потока воды вдоль подложки на частицу Fw, вертикальная проекция силы со стороны потока воды на частицу Fw⊥, сила гидродинамического сопротивления сдвигу FD, сила трения скольжения частицы по подложке Ff-s и сила Кориолиса Fcor, возникающая за счет вращения пластины.
Рис. 1.
Силы, воздействующие на частицу на поверхности пластины во время гидромеханической обработки [17].
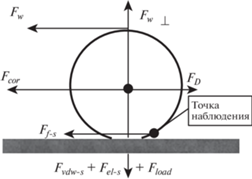
Перемещение частицы вдоль поверхности подложки под воздействием водяного потока и вращения пластины происходит тогда, когда результирующая сила воздействия потока Fbreakout = = ${{F}_{{\text{D}}}} + ~{{F}_{{{\text{f - s}}}}}~ + {{F}_{{\text{w}}}} + {{F}_{{{\text{w}} \bot }}} + {{F}_{{{\text{cor}}}}}~$ в состоянии преодолеть силу адгезии Fadhesoin = ${{F}_{{{\text{vdw - s}}}}} + {{F}_{{{\text{el - s}}}}}$ + Fload, т.е. ${{F}_{{{\text{breakout}}}}}$ ≥ ${{F}_{{{\text{adhesoin}}}}}$.
Взаимодействие, определяющее силу адгезии между УНТ и подложкой из SiO2, определяется в первую очередь силой Ван-дер-Ваальса, а само взаимодействие описывается потенциалом Леннарда–Джонса [18]:
(1)
$U(r) = 4{{\varepsilon }}\left( {\frac{{{{\sigma }^{{12}}}}}{{{{r}^{{12}}}}} - \frac{{{{\sigma }^{6}}}}{{{{r}^{6}}}}} \right),$Таким образом, большие наслоения УНТ должны легко размываться до более тонкого слоя, а свободные от УНТ области пластины, наоборот, будут заполняться нанотрубками. Варьируя исходное количество нанесенных УНТ и время обработки гидромеханическим воздействием, на поверхности подложки можно получать слои УНТ с необходимыми характеристиками.
ОБЪЕКТЫ И МЕТОДЫ ИССЛЕДОВАНИЯ
В качестве подложек использовали кремниевые пластины диаметром 100 мм, на поверхности которых был сформирован слой термического оксида кремния толщиной 200 нм. Для нанесения слоев применяли водную суспензию собственного приготовления на основе УНТ Таунит-М с использованием холата натрия (C24H39NaO5) в качестве поверхностно-активного вещества для предотвращения коагуляции частиц в суспензии. Суспензию последовательно разбивали 5 раз по 60 мин с помощью УЗ-диспергатора с рабочей частотой 22 кГц и выходной мощностью 100 Вт. После каждого этапа УЗ-обработки диспергатором проводили фильтрацию полученной суспензии для получения однородной взвеси.
Для нанесения спреем использовали пульверизатор с емкостью для суспензии, в качестве газа-носителя – азот особой чистоты марки 6.0. Приготовленную суспензию наносили спреем при постоянном давлении азота 2.5 атм на нагретую до 200°C подложку (рис. 2). Суспензию последовательно наносили под углом 60° к подложке для обеспечения покрытия слоем УНТ всей поверхности пластины. Выходное сопло пульверизатора обеспечивало распыление суспензии в виде струи тумана (аэрозоля), что позволило оптимизировать процесс нанесения и сушки суспензии из УНТ. Нагрев подложки осуществляли с помощью нагревательного элемента с молибденовым столиком до заданной температуры. Был проведен ряд экспериментов по подбору оптимальной рабочей температуры столика нагревателя в диапазоне от 20 до 300°С, в результате чего было установлено, что значение температуры столика нагревателя 200°С является оптимальным для осуществления процесса испарения воды из суспензии на поверхности пластины с минимальным образованием капель. При температуре более 200°С изменений в результате высыхания суспензии не было, а при температурах менее 200°С подложка остывала слишком быстро, в результате чего образовывались капли суспензии на поверхности пластины. Образование на пластине капель с характерным размером более 0.2 мм при сушке суспензии ведет к агрегации УНТ в одной из областей пластины, где образовалась капля, что является негативным эффектом при создании однородного слоя УНТ по пластине.
Для контролируемого равномерного распределения УНТ по пластине применяли метод гидромеханического воздействия поверхности пластины, для чего использовали стандартную серийную установку для резки и отмывки пластин. Во время обработки вращающуюся со скоростью 1000 об./мин поверхность пластины с нанесенным слоем УНТ последовательно обрабатывали потоком деионизированной воды давлением 4.5 атм от центра пластины к краю и обратно (рис. 3).
Варьирование свойств слоя из УНТ осуществляли изменением количества наносимой суспензии. Для проведения исследований были изготовлены образцы с различными объемами нанесенной суспензии УНТ (10, 20, 40, 80, 120 мл). Каждый образец последовательно подвергали многократным циклам обработки методом гидромеханического воздействия с целью получения однородного слоя УНТ по пластине. После каждого цикла обработки проводили анализ полученного слоя УНТ.
Для исследования морфологии слоев из УНТ использовали метод сканирующей электронной микроскопии (СЭМ). На рис. 4a приведены снимки поверхности центральной части образца с УНТ после нанесения 40 мл суспензии до проведения операции гидромеханической обработки пластины. Изначальное распределение УНТ по пластине (рис. 4a) вызвано агрегацией частиц вследствие образования капель при сушке суспензии. На рис. 4б и 4в изображена поверхность пластины со слоем УНТ после четырех и девяти циклов гидромеханической обработки соответственно. На изображении УНТ после четырех циклов обработки (рис. 4б) отсутствуют дефекты от капель на поверхности пластины: в результате гидромеханического воздействия УНТ с плохой адгезией размылись по пластине, и образовался тонкий слой УНТ. Из рис. 4в видно, что c увеличением количества циклов гидромеханического воздействия однородность и равномерность слоя УНТ увеличиваются, но толщина слоя уменьшается.
Рис. 4.
СЭМ-изображения центральной области пластины после нанесения УНТ: до обработки (а), после четырех (б) и девяти циклов обработки гидромеханическим воздействием (в). Белыми кругами выделен пример агрегации, возникающей в результате высыхания капель.
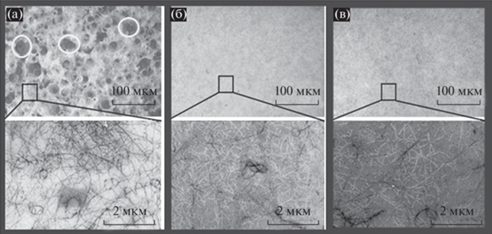
Для определения поверхностного сопротивления слоя УНТ до и после гидромеханического воздействия проводили измерения поверхностного сопротивления четырехзондовым методом. Методика измерения состоит в том, что с помощью двух внешних зондов через поверхность исследуемого материала пропускают электрический ток, а между двумя внутренними зондами измеряют разность электрических потенциалов вольтметром с высоким входным сопротивлением. В результате зависимость тока от разности потенциалов на поверхности слоя с УНТ, измеренная в 21 точке, позволяет построить карту поверхностного сопротивления исследуемого слоя по всей площади пластины.
Полученные карты поверхностного сопротивления, приведенные на рис. 5, позволяют оценить динамику изменения электрических характеристик слоя УНТ после различного количества циклов гидромеханического воздействия. Значения сопротивления легенд всех карт нормированы к максимальному значению сопротивления образца до проведения обработки. Карта распределения сопротивления представляет собой квадратный участок со стороной 70 мм, центр которого находится в центре пластины, а нижняя часть параллельна базовому срезу пластины.
Рис. 5.
Карты распределения поверхностного сопротивления слоев с УНТ, измеренные четырехзондовым методом, для пластины до обработки (а), после четырех (б) и после девяти циклов обработки гидромеханическим воздействием соответственно (в).
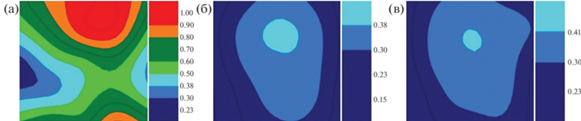
Из карты распределения поверхностного сопротивления (рис. 5а) видно, что после нанесения суспензии на пластину большая часть УНТ находится в центральной и нижней области, так как суспензия наносилась со стороны базового среза пластины. На рис. 5б показано распределение сопротивления слоя УНТ по пластине после четырех циклов обработки гидромеханическим воздействием, на рис. 5в – влияние на сопротивление слоя УНТ после девяти циклов обработки гидромеханическим воздействием.
Далее полученные образцы исследовали методом комбинационного рассеяния света (КРС). На рис. 6 приведены спектры КРС для подложки с 80 мл наносимой суспензии с УНТ, снятые при длине волны излучения λ = 532 нм, времени накопления 20 с, выходной мощности лазера 5 мВт.
Рис. 6.
Обзорный спектр КРС слоя УНТ в центре пластины до и после проведения пяти циклов обработки гидромеханическим воздействием.
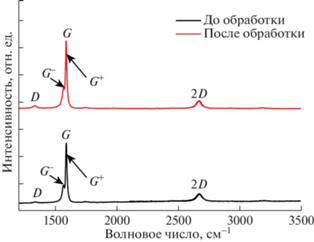
Типичные пики высокой интенсивности для УНТ находятся в диапазоне волновых чисел от 1000 до 3500 см–1 [19]. Полученные пики позволяют провести оценку таких параметров УНТ, как проводимость, дефектность. В соответствии с литературными данными G-мода (тангенциальная мода) в диапазоне 1550–1600 см–1 вызвана наличием sp2-гибридизации углерода и оптическими колебаниями двух смежных атомов углерода в решетке УНТ [20]. G+-пик указывает на колебания вдоль оси УНТ [21], пик G– связан с колебаниями, перпендикулярными оси направления УНТ [22]. Пик D в области 1300–1350 см–1 обусловлен двойным резонансом, который возможен только при наличии дефектов, и для идеальных кристаллов не проявляется [23]. Область 2D-мод 2700 см–1 представляет собой результат двухфононного рассеяния и наблюдается в спектрах независимо от степени дефектности, но меняется от длины волны возбуждения [24].
Таким образом, спектр КРС (рис. 6) показывает, что поверхностный проводящий слой подложки до и после циклов обработки гидромеханическим воздействием состоит из УНТ по пику G 1550–1600 см–1sp2-гибридизации и 2D 2700 см–1 графеновой плоскости. Спектры до и после обработки различаются по интенсивности из-за уменьшения толщины слоя УНТ на подложке.
Анализ спектров в области 1300–1350 см–1 позволяет утверждать, что количество аморфной фазы не увеличивается при использовании обработки слоя УНТ гидромеханическим воздействием, так как интенсивность D-пика не растет. Это также подтверждается СЭМ-изображениями слоя УНТ: трубки действительно имеют структурные дефекты в виде скруток и изгибов, но в аморфную фазу как до обработки, так и после УНТ не переходят.
Согласно экспериментальным данным [25, 26] значения полуширины на полувысоте 2D-мод у многостенных УНТ составляют ~60 см–1 и одностенных УНТ ~30 см–1. Из полученных спектров КРС (рис. 6) можно сделать вывод, что УНТ с двумя и более стенками частично смываются с поверхности пластины. После трех циклов обработки гидромеханическим воздействием значения полуширины на полувысоте 2D-мод не меняются (рис. 7).
Рис. 7.
Зависимость отношения значений интенсивностей полуширины на полувысоте 2D-мод от количества циклов гидромеханического воздействия для образцов с различным объемом нанесенной суспензии с УНТ.
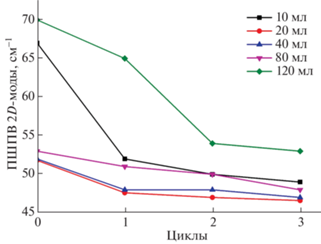
В зависимости от количества наносимой суспензии с УНТ и от количества проведенных циклов обработки гидромеханическим воздействием положение 2D-пиков не меняется.
РЕЗУЛЬТАТЫ И ИХ ОБСУЖДЕНИЕ
Проведенные исследования позволяют построить графики зависимости среднего поверхностного сопротивления слоя УНТ от количества циклов обработки гидромеханическим воздействием (рис. 8). На рис. 8 видно, что увеличение количества циклов обработки поверхности образцов приводит к выходу на плато значений их усредненного удельного поверхностного сопротивления, что подтверждает наличие на поверхности подложек определенной концентрации УНТ, слабо изменяющейся с увеличением циклов обработки, но сильно зависящей от объема наносимой суспензии. Результаты, приведенные на рис. 8, означают, что при обработке гидромеханическим воздействием большие наслоения УНТ размываются до более тонкого слоя с большим сопротивлением, а области пластины с малой плотностью УНТ, образованные при нанесении малых объемов суспензии, наоборот, заполняются с уменьшением сопротивления получаемого слоя. Варьируя исходное количество нанесенных УНТ и время обработки гидромеханическим воздействием, на поверхности подложки можно получать слои УНТ с необходимыми характеристиками.
Рис. 8.
Зависимость среднего поверхностного сопротивления слоя УНТ от количества циклов обработки гидромеханическим воздействием.
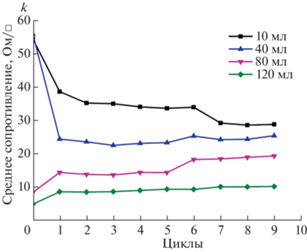
Сравнительный анализ полученных СЭМ-изображений с приведенными в [5] показывает, что:
– УЗ-обработка может привести к удалению с поверхности пластины большой части слоя УНТ, чего не происходит при обработке гидромеханическим воздействием;
– количество дефектов в функциональном слое при использовании обработки гидромеханическим воздействием меньше, чем при использовании метода, приведенного в [5];
– слой УНТ после четырех циклов обработки гидромеханическим воздействием может использоваться, например, для создания транзисторов на основе УНТ [5], имеющих характерные линейные размеры ~50 мкм с длиной функциональных слоев из УНТ ~1 мкм.
Сравнительный анализ СЭМ-изображений слоев УНТ из [27] и приведенных на рис. 4 демонстрирует, что метод нанесения спреем с последующей обработкой гидромеханическим воздействием позволяет получить слои УНТ с лучшей однородностью, чем метод нанесения слоя окунанием подложки в суспензию. Метод, описанный в [27], неприменим для создания интегральных схем из-за слишком толстого слоя УНТ и большого количества вертикально ориентированных УНТ, а образование крупных агрегатов в данном методе ведет к плохой адгезии трубок к подложке, что может привести к удалению трубок при дальнейших операциях литографии при изготовлении планарных структур.
Из всего перечисленного выше можно сделать вывод, что предлагаемый нами метод формирования функциональных слоев УНТ имеет ряд преимуществ по сравнению с методом [5]: более дешевый, технологичный (требует меньшего количества оборудования, так как нет дополнительных операций по нанесению фоторезиста), экологически чистый. В дальнейшем планируем изготовить приборы на основе УНТ, а также улучшить метод по созданию суспензии с УНТ.
ВЫВОДЫ
Продемонстрирован технологичный метод получения слоя из УНТ нанесением спреем на подложки диаметром 100 мм.
Использование метода обработки гидромеханическим воздействием поверхности подложки со слоем УНТ, нанесенного спреем, позволяет получить однородные слои УНТ с заданным поверхностным сопротивлением.
Среднее поверхностное сопротивление слоя УНТ слабо зависит от увеличения циклов обработки гидромеханическим воздействием после проведения первого цикла.
В результате обработки слоя УНТ гидромеханическим воздействием часть УНТ с двумя и более стенками смываются с поверхности пластины.
Полученные образцы могут использоваться в качестве функциональных слоев УНТ для разработки таких приборов, как транзистор на основе УНТ, диод Шоттки.
Авторы выражают благодарность Е.В. Латипову за съемку спектров КРС (ИНМЭ РАН).
Работа выполнена при финансовой поддержке Министерства науки и высшего образования РФ (проект № 0004-2019-0004). При выполнении работы использовано оборудование, входящее в УНУ “КУТГИ” Института нанотехнологий микроэлектроники РАН.
Список литературы
Wong H.-S.P., Akinwande D. // Carbon Nanotube and Graphene Device Physics. 2010. P. 233. https://doi.org/10.1017/cbo9780511778124.010
Scarselli M., Castrucci P., Crescenzi M. // J. Phys.: Condens. Matter. 2012. V. 24. № 31. P. 36. https://doi.org/10.1088/0953-8984/24/31/313202
Peng L., Zhang Z., Wang S. // Mater. Today. 2014. V. 17. № 9. P. 433. https://doi.org/10.1016/j.mattod.2014.07.008
Camilli L., Passacantando M. // Chemosensors. 2018. V. 6. № 4. P. 62. https://doi.org/10.3390/chemosensors6040062
Hills G., Lau C., Wright A. et al. // Nature. 2019. V. 572. № 7771. P. 595. https://doi.org/10.1038/s41586-019-1493-8
Hamzah N., Mohd Yasin M.F., Mohd Yusop M.Z. et al. // J. Mater. Chem. 2017. V. 5. № 48. P. 2511. https://doi.org/10.1039/C7TA08668G
Chen J., Xu X., Zhang L., Huang S. // Nano-Micro Lett. 2015. V. 7. № 4. P. 353. https://doi.org/10.1007/s40820-015-0050-8
He Z., Maurice J.-L., Gohier A. et al. // Chem. Mater. 2011. V. 23. № 24. P. 5379. https://doi.org/10.1021/cm202315j
Keshavarzian P., Sarikhani R. // Circuits, Syst. Signal Process. 2013. V. 33. № 3. P. 665. https://doi.org/10.1007/s00034-013-9672-6
Yang M.H., Teo K.B.K., Milne W.I., Hasko D.G. // Appl. Phys. Lett. 2005. V. 87. № 25. P. 1. https://doi.org/10.1063/1.2149991
Deck C.P., Vecchio K. // Carbon. 2006. V. 44. № 2. P. 267. https://doi.org/10.1016/j.carbon.2005.07.023
Datsyuk V., Kalyva M., Papagelis K. et al. // Carbon. 2008. V. 46. № 6. P. 833. https://doi.org/10.1016/j.carbon.2008.02.012
Jeong M., Lee K., Choi E. et al. // Nanotechnology. 2012. V. 23. № 50. P. 1. https://doi.org/10.1088/0957-4484/23/50/505203
Shi Y., He L., Deng Q. et al. // Micromachines. 2019. V. 10. № 5. P. 330. https://doi.org/10.3390/mi10050330
Cui H., Yan X., Monasterio M., Xing F. // Nanomaterials. 2017. V. 7. № 9. P. 262. https://doi.org/10.3390/nano7090262
Tian Y., Zhang X., Geng H.-Z. et al. // RSC Adv. 2017. V. 7. № 83. P. 53018. https://doi.org/10.1039/c7ra10092b
Xu K., Vos R., Vereecke G. et al. // J. Vac. Sci. Technol. B. 2005. V. 23. № 5. P. 2160. https://doi.org/10.1116/1.2052713
Xiao J., Dunham S., Liu P. et al. // Nano Lett. 2009. V. 9. № 12. P. 4311. https://doi.org/10.1021/nl9025488
Dresselhaus M.S., Dresselhaus G., Sait R., Jorio A. // Phys. Rep. 2005. V. 409. № 2. P. 47. https://doi.org/10.1016/j.physrep.2004.10.006
Jorio A., Pimenta M.A., Filho A.G.S. et al. // New J. Phys. 2003. V. 5. № 139. P. 1. https://doi.org/10.1088/1367-2630/5/1/139
Hadjiev V.G., Warren G.L., Sun L. et al. // Carbon. 2010. V. 48. № 6. P. 1750. https://doi.org/10.1016/j.carbon.2010.01.018
Brown S.D.M., Jorio A., Corio P. et al. // Phys. Rev. B. 2001. V. 63. № 15. P. 155414.1. https://doi.org/10.1103/physrevb.63.155414
Ghasempour R., Narei H. // CNT Basics and Characteristics. Carbon Nanotube-Reinforced Polymers. 2018. P. 24. https://doi.org/10.1016/b978-0-323-48221-9.00001-7
Sharma H., Agarwal D.C., Shukla A.K. et al. // J. Raman Spectrosc. 2012. V. 44. № 1. P. 12. https://doi.org/10.1002/jrs.4136
Graf D., Molitor F., Ensslin K. et al. // Nano Lett. 2007. V. 7. № 2. P. 238. https://doi.org/10.1021/nl061702a
Ferrari A.C., Meyer J.C., Scardaci V. et al. // Phys. Rev. Lett. 2006. V. 97. № 18. P. 187401. https://doi.org/10.1103/PhysRevLett.97.187401
Song Y.I., Kim G.Y., Choi H.K. et al. // Chem. Vap. Depos. 2006. V. 12. № 6. P. 375. https://doi.org/10.1002/cvde.200506442
Дополнительные материалы отсутствуют.
Инструменты
Российские нанотехнологии