Российские нанотехнологии, 2024, T. 19, № 2, стр. 214-220
Изменение тонкой структуры природного графита в процессе механического диспергирования
А. Г. Фазлитдинова 1, *, В. А. Тюменцев 1
1 Челябинский государственный университет
Челябинск, Россия
* E-mail: fazlitdinovaag@mail.ru
Поступила в редакцию 16.10.2023
После доработки 22.01.2024
Принята к публикации 22.01.2024
Аннотация
Методом рентгеновской дифракции изучено изменение тонкой структуры природного графита, измельченного в планетарной мельнице в атмосфере воздуха и Ar + 10%CH4. Профили экспериментально наблюдаемых асимметричных максимумов 002 графита раскладывали на минимальное количество симметричных компонент, описываемых функцией Пирсона VII. Асимметричные максимумы 002 могут быть представлены как суперпозиция минимального количества симметричных компонент разложения. При этом вычисленные значения межплоскостных расстояний (d002) компонент разложения достаточно близки к значениям d002 метастабильных состояний (фаз), приведенных ранее в литературе. Показано, что процесс диспергирования и структурных преобразований развивается по пути последовательного формирования компонент с увеличенным межплоскостным расстоянием d002 в диапазоне от ∼3.36 до ∼3.55/3.68 Å. Диспергирование не сводится только к уменьшению размеров частиц графита. Замена атмосферы воздуха на Ar + 10%CH4 оказывает наиболее существенное влияние на диспергирование графита в первые ~40 мин.
ВВЕДЕНИЕ
Особенности фазового перехода “рентгеноаморфного” углеродного материала в графит при высокотемпературной обработке, а также аморфизации структуры графита в процессе длительного механического диспергирования или нейтронного облучения были предметом многочисленных исследований. Например, в [1–5] получены данные по монотонному росту размеров областей когерентного рассеяния (ОКР) и уменьшению межплоскостного расстояния d002 по мере повышения температуры или увеличения продолжительности изотермической обработки как хорошо графитирующихся углеродных материалов, так и трудно графитирующихся углеродных волокон. В [6–8] показано, что по мере повышения температуры или продолжительности высокотемпературной обработки изменение d002 может развиваться ступенчато, наблюдаются плато при значениях, равных 3.36, 3.37, 3.40, 3.425 и 3.44 Å [6]. В [8] методами рентгеноструктурного анализа (РСА), спектроскопии комбинационного рассеяния света и просвечивающей электронной микроскопии исследована структура углеродного материала (предварительно карбонизованное при 900°С полимерное волокно), прошедшего термообработку в интервале температур 1400–2800°С. Были выделены четыре этапа графитации углеродных волокон. Межплоскостные расстояния d002 в зависимости от температуры обработки изменяются ступенчато (наблюдаются плато при значениях ~3.45 и ~3.42 Å).
В процессе длительного механического диспергирования [6, 9–18] или нейтронного облучения [6, 19] графита наблюдается ступенчатое увеличение значений d002 и происходит частичная аморфизация материала. На зависимостях изменения межплоскостного расстояния графита от условий обработки, опубликованных в [12, 15], также наблюдаются плато при значениях d002, равных ~3.38, 3.40, 3.425, 3.44 и 3.55/3.68 Å. Согласно [6, 12, 15] такое изменение d002 может быть обусловлено формированием метастабильных углеродных фаз, различающихся значением межплоскостного расстояния. Одновременное присутствие нескольких таких фаз в исследуемых углеродных материалах обусловливает асимметрию профиля экспериментально наблюдаемых дифракционных максимумов 002. Постепенное изменение компонентного состава материала в процессе термообработки, а также при механическом диспергировании или радиационном воздействии приводит к достаточно плавному смещению центра тяжести таких максимумов.
Анализ профиля асимметричного дифракционного максимума 002 графитов и образующихся в процессе диспергирования углеродных материалов проведен в [12–15, 18]. Так, в [13, 15] выполнено деление асимметричного дифракционного максимума 002 графита на две компоненты. Межплоскостное расстояние одной из компонент изменяется ступенчато по мере увеличения продолжительности диспергирования и принимает значения 3.40, 3.63 и 3.68 Å [15], вторая компонента, возможно, обусловлена рассеянием от аморфной фазы. В [18] проводилось разделение асимметричного дифракционного максимума 002 на три и четыре компоненты. Предполагалось, что асимметрия максимума обусловлена структурным переходом гексагонального графита сначала в состояние турбостратного углерода, который по мере увеличения продолжительности диспергирования переходит в аморфный материал. Также имеются данные по влиянию газовой среды на процесс диспергирования углеродного материала [9, 17]. Показано, что в атмосфере инертного газа (Ar, N2) диспергирование углеродного материала развивается более активно. В атмосфере, содержащей кислород, наблюдается замедление структурных превращений графита. Однако в литературе отсутствуют методика анализа профиля дифракционного максимума 002 и детальный анализ последовательности структурного перехода графита в процессе диспергирования. Наблюдаемая асимметрия характерного дифракционного максимума 002 на протяжении всего процесса диспергирования свидетельствует о неоднородности углеродного материала по фазовому составу. Выявление закономерностей изменения тонкой структуры графита в процессе диспергирования может представлять практический интерес.
Методика исследования изменения тонкой структуры углеродных материалов, основанная на анализе профиля дифракционных максимумов 002, 004 и 006, подробно обсуждалась в [20–23]. Показано, что асимметрия таких максимумов и положение центра тяжести существенно зависят от режимов получения углеродного волокна. Для анализа профиля максимумов применялась программа Origin, с помощью которой экспериментально наблюдаемые асимметричные максимумы разделяли на минимальное число симметричных компонент, описываемых функцией Гаусса или Войта. Было установлено, что вычисленные по положению центров тяжести компонент разложения значения d002 соответствуют метастабильным состояниям (фазам) из числа возможных, перечисленных выше [6, 12].
В данной работе методом РСА и растровой электронной микроскопии изучено изменение тонкой структуры углеродного материала в процессе длительного диспергирования природного графита в планетарной мельнице в атмосфере воздуха и Ar + 10%CH4.
ОБЪЕКТЫ И МЕТОДЫ ИССЛЕДОВАНИЯ
Исследования проведены на порошковом природном графите. Его измельчение осуществляли при длительном механическом диспергировании в планетарной мельнице Fritsch Pulverisette 6 в размольном стакане из карбида вольфрама (80 мл) при комнатной температуре со скоростью 400 об./мин как в атмосфере воздуха (длительность размола до 2700 мин), так и в среде Ar + 10%CH4 (продолжительность размола до 1500 мин). Масса мельничного шарика диаметром 10 мм из карбида вольфрама – 4 г, отношение массы 30 шариков к массе порошка графита составило ∼120/1. Частицы исходного графита имеют размеры от 100 до 300 мкм, рис. 1а (изображения получены с помощью сканирующего электронного микроскопа (СЭМ) JEOL JSM-6510LA). После 1500 мин размола в атмосфере воздуха встречаются отдельные частицы размером до 50 мкм, а также частицы неправильной формы размером от ~1 до ~10 мкм (рис. 1б). В процессе диспергирования образца в газовой среде Ar + 10%CH4 наблюдаются частицы размером от 0.5 до 40 мкм, рис. 1в.
Рис. 1.
СЭМ-изображения исходных частиц природного графита (а), после диспергирования в планетарной мельнице в течение 1500 мин в атмосфере воздуха (б) и Ar + 10%CH4 (в).
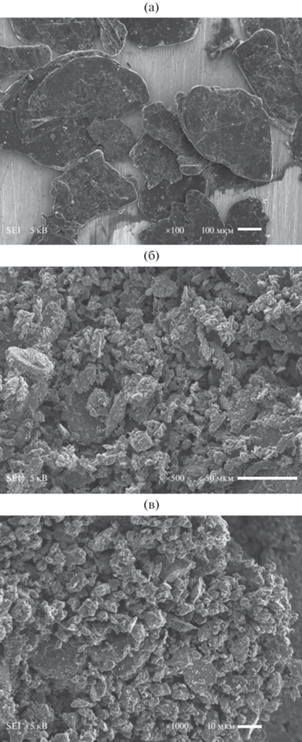
Рентгенодифракционные исследования выполнены в геометрии Брегга–Брентано (CuKα-излучение, θ/θ-сканирование с шагом 0.025°). Дифрактометр D8 Advance, Bruker, инструментальное уширение максимума 002 βинстр = 0.06°, в качестве эталона для определения βинстр использовали поликристаллический кварц. Удаление линии фона и дуплета CuKα2 проводили с помощью программы EVA, входящей в пакет DIFFRAC Plus.
Размеры ОКР углеродного материала в направлении 002 (L002) вычисляли по формуле Шеррера: L = K · λ/β cos θ, где θ – угол рассеяния, λ – длина волны рентгеновских лучей, β – интегральная ширина максимума. Форм-фактор K составляет 0.89 для L002 [1]. В процессе диспергирования графита в атмосфере воздуха в течение 2700 мин были записаны рентгенограммы 20 проб. Временной интервал отбора проб составлял 5 мин, затем 10 мин, далее при продолжении диспергирования увеличивался от 30 до 300 мин.
Наблюдаемая экспериментально асимметрия профиля дифракционного максимума 002, как отмечалось в [6, 12, 13, 15, 18], может быть обусловлена одновременным присутствием в материале компонент, различающихся размерами ОКР и величиной межплоскостного расстояния. Поэтому получаемая по центру тяжести и интегральной ширине асимметричных максимумов информация о среднем значении межплоскостного расстояния и средних размерах ОКР не отражает реальной структуры материала. В связи с этим профили дифракционных асимметричных максимумов 002 раскладывали с помощью программы Origin 8 на компоненты, описываемые функцией Пирсона. Минимальное количество таких компонент разложения определяли совпадением суммарного максимума компонент с профилем экспериментально полученного максимума (коэффициент детерминации R2 находится в пределах 0.985–0.999).
РЕЗУЛЬТАТЫ ЭКСПЕРИМЕНТА
Структурные изменения графита в процессе длительного диспергирования в планетарной мельнице иллюстрируют рентгенограммы, приведенные на рис. 2. Интегральная ширина (с учетом инструментального уширения) дифракционного максимума 002 исходного графита и прошедшего диспергирование в течение 5 мин составляет 0.266° и 0.354° соответственно. На начальном этапе диспергирования образца профиль дифракционного максимума 002 практически не изменяется. По мере увеличения продолжительности диспергирования графита более ~250 мин на рентгенограммах образцов наблюдается существенное изменение интегральной ширины и асимметрии максимумов 002. Асимметрия дифракционных максимумов 002 ограничивает применение формулы Шеррера для оценки средних размеров ОКР. Тем не менее средние размеры ОКР и средние межплоскостные расстояния d002 были вычислены по интегральной ширине и центру тяжести таких асимметричных максимумов. На рис. 3а показано, что процесс структурных изменений графита можно разделить на два временных интервала. Первоначально при диспергировании графита до ~250 мин значения межплоскостных расстояний остаются почти неизменными и составляют ~3.38 Å. По мере увеличения продолжительности диспергирования до 2700 мин значения d002 постепенно возрастают до ~3.45 Å. Вычисленные значения средних размеров ОКР практически линейно уменьшаются в течение всего процесса диспергирования (до 2700 мин) от ~34 до ~5 нм, рис. 3б.
Рис. 2.
Изменение профиля дифракционных максимумов 002 образцов природного графита в зависимости от продолжительности диспергирования в атмосфере воздуха и результаты разделения асимметричных максимумов на компоненты.
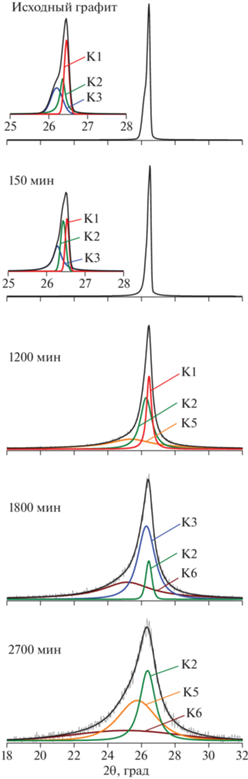
Рис. 3.
Изменение межплоскостного расстояния d002 (а) и средних размеров ОКР L002 (б) природного графита в процессе диспергирования в атмосфере воздуха и газовой среде Ar + 10%CH4.
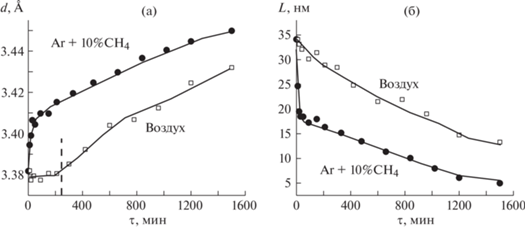
Рассмотрим влияние газовой среды на процесс диспергирования природного графита. Как следует из данных, приведенных на рис. 3б, в процессе диспергирования графита в атмосфере Ar + 10%CH4 в течение первых 40–50 мин наблюдается активное уменьшение средних размеров L002 от ~34 до ~18 нм. В этом же временном интервале наблюдается резкое увеличение среднего значения межплоскостного расстояния d002 от ~3.38 до ~3.41 Å. Продолжение механического диспергирования углеродного материала сопровождается постепенным уменьшением средних размеров ОКР L002 до ~5 нм. При этом среднее значение межплоскостного расстояния d002 плавно увеличивается до ~3.45 Å.
Рассмотрим результаты анализа профилей дифракционных максимумов 002, характерных для графита, с целью исследования изменения тонкой структуры углеродного материала в процессе механического диспергирования. В [6, 12] предполагалось, что асимметрия максимумов обусловлена одновременным присутствием в углеродном материале компонент, различающихся по размерам ОКР и величине межплоскостного расстояния. Поэтому детально проанализировав профиль максимумов, можно получить дополнительную информацию о закономерностях изменения тонкой структуры исследуемого материала. Как следует из данных, приведенных на рис. 4 и в табл. 1, в процессе диспергирования в атмосфере воздуха весь период диспергирования графита можно разделить на четыре временных интервала. В первом интервале (продолжительность до ∼1000 мин) межплоскостные расстояния компонент разложения близки к значениям 3.36, 3.37 и 3.40 Å (коэффициент R2 находится в пределах от 0.994 до 0.998), что соответствует компонентам К1, К2 и К3. При дальнейшем диспергировании углеродного материала появляются метастабильные состояния с увеличенными значениями межплоскостных расстояний. Первоначально вместо компоненты К3 формируется компонента К5 (d002 ~ 3.44 Å). Затем при диспергировании графита от 1500 до 2500 мин в углеродном материале формируются компоненты К2, К3 и К6 со значениями d002 ~ 3.37, 3.40 и 3.55 Å. В следующем интервале вместо компоненты К3 появляется компонента К5, фазовый состав представлен компонентами К2, К5 и К6 со значениями межплоскостных расстояний ~3.37, 3.44 и 3.55 Å.
Рис. 4.
Изменение значений межплоскостных расстояний компонент разложения асимметричного дифракционного максимума 002 природного графита в зависимости от продолжительности диспергирования в атмосфере воздуха (а) и Ar + 10%CH4 (б).
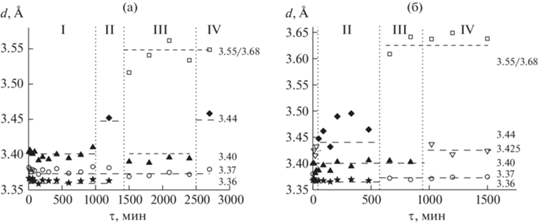
Таблица 1.
Значения средних размеров L002 и межплоскостных расстояний d002 ОКР компонент разложения асимметричных максимумов 002 природного графита в процессе диспергирования
Продолжи-тельность дисперги-рования, мин | Параметры структуры компонент разложения | |||||||||||
---|---|---|---|---|---|---|---|---|---|---|---|---|
K1 = 3.36, Å | K2 = 3.37, Å | K3 = 3.40, Å | K4 = 3.425, Å | K5 = 3.44, Å | K6 = 3.55/3.68, Å | |||||||
d1, Å | L1, нм | d2, Å | L2, нм | d3, Å | L3, нм | d4, Å | L4, нм | d5, Å | L5, нм | d6, Å | L6, нм | |
Атмосфера воздуха | ||||||||||||
0 | 3.368 | ~57 | 3.380 | ~49 | 3.400 | ~23 | ||||||
20, 40, 60, 90, 150, 210, 300, 420, 600, 780, 960 | 3.363 | от 50 до 38 | 3.378 | от 40 до 30 | 3.400 | от 34 до 10 | ||||||
1200 | 3.363 | ~38 | 3.381 | ~20 | 3.452 | ~5 | ||||||
1500, 1800, 2100, 2400 | 3.371 | от 20 до 13 | 3.392 | от 9 до 5 | 3.538 | ~2 | ||||||
2700 | 3.379 | ~8 | 3.458 | ~3 | 3.549 | ~1 | ||||||
Газовая среда Ar + 10%CH4 | ||||||||||||
0 | 3.368 | ~57 | 3.380 | ~49 | 3.400 | ~23 | ||||||
10, 20, 30 | 3.368 | от 40 до 30 | 3.390 | от 23 до 18 | 3.424 | от 8 до 6 | ||||||
50, 90, 150, 210, 330, 480 | 3.368 | от 30 до 18 | 3.395 | от 18 до 12 | 3.465 | от 4 до 2.5 | ||||||
660, 840 | 3.371 | от 18 до 15 | 3.404 | от 11 до 5 | 3.625 | ~1.5 | ||||||
1020, 1200, 1500 | 3.373 | от 15 до 10 | 3.426 | ~3 | 3.641 | ~1 |
На начальном этапе диспергирования природного графита в газовой среде Ar + 10%CH4 наблюдаются существенные изменения в компонентном составе материала (рис. 4б, табл. 1). Дифракционный максимум 002 графита, прошедшего диспергирование в течение первых 10 мин, содержит компоненты со значениями межплоскостных расстояний 3.36, 3.40 и 3.425 Å (метастабильные состояния К1, К3 и К4). Этот компонентный состав сохраняется в течение ~30 мин диспергирования. Увеличение диспергирования до 480 мин обусловило появление компоненты К5 вместо К4. В следующем временном интервале диспергирования до ~840 мин компоненты К1 и К5 не наблюдаются, формируются новые К2 и К6 (образец содержит метастабильные состояния К2, К3 и К6, значение R2 ~ 0.992). После диспергирования в интервале 1020–1500 мин фазовый состав углеродного материала представлен компонентами К2, К4 и К6.
ОБСУЖДЕНИЕ РЕЗУЛЬТАТОВ
В настоящее время объектами активных теоретических и экспериментальных исследований стали наноструктурные углеродные материалы, которые являются перспективными для нанотехнологий. В этом плане определенный практический интерес представляет изучение продуктов механического диспергирования графита. В работе показано, что процесс диспергирования не сводится только к уменьшению размеров частиц графита. Наблюдаются появление асимметрии максимумов 002, постепенное смещение центров тяжести в сторону уменьшения брэгговского угла 2θ. Среднее значение d002, вычисленное по центру тяжести таких асимметричных максимумов, постепенно увеличивается. Это обусловлено формированием в процессе механического диспергирования новых ОКР с увеличенным значением межплоскостного расстояния d002. Данные о компонентном составе и размерах ОКР таких метастабильных состояний могут быть получены в результате анализа профиля асимметричного дифракционного максимума 002 исследуемого углеродного материала. Показано, что вычисленные значения d002 метастабильных состояний находятся в достаточно хорошем соответствии с приведенными в [6, 12] данными 3.36, 3.37, 3.40, 3.425, 3.44 и 3.55/3.68 Å. Углеродный материал, полученный в процессе длительного диспергирования графита, гетерогенен, имеет несколько метастабильных состояний. Наблюдаемые изменения компонентного состава по мере увеличения продолжительности механического диспергирования графита развиваются путем последовательного образования ОКР, отличающихся увеличенным значением межплоскостного расстояния. Области существования метастабильных состояний определяются условиями механического воздействия на графит. Размеры ОКР углеродного материала по мере перехода к метастабильным состояниям, соответствующим увеличенным значениям d002, уменьшаются. Диспергирование углеродного материала в среде Ar + 10%CH4 обусловливает ускорение фазовых превращений материала, переход к метастабильным состояниям с большим значением d002.
Таким образом, полученные данные позволяют предположить, что переход углеродного материала в менее равновесное состояние развивается через ряд метастабильных. Необходимо учитывать, что свойства конечного продукта, получаемого при механическом диспергировании, определяются не только дисперсностью, но и структурой углеродных частиц.
ВЫВОДЫ
Механически диспергируемый в планетарной мельнице углеродный материал гетерогенен по дисперсному составу, его компонентный состав определяется условиями получения.
Переход углеродного материала в новое состояние при механическом диспергировании обусловлен рядом метастабильных превращений.
С увеличением продолжительности механического диспергирования графита происходит формирование в углеродном материале компонент, межслоевое расстояние d002 которых приближается к таковому турбостратного углерода. Поэтому свойства конечного продукта, получаемого при механическом диспергировании, будут определяться не только дисперсностью, но и структурой углеродных частиц.
Замена атмосферы воздуха на Ar + 10%CH4 стимулирует структурные преобразования, оказывает наиболее существенное влияние на процесс диспергирования графита в первые ~40 мин.
Работа выполнена при финансовой поддержке фонда перспективных научных исследований ФГБОУ ВО “Челябинского государственного университета” 2023/10.
Список литературы
Liu F., Wang H., Xue L. et al. // J. Mater. Sci. 2008. V. 43. № 10. P. 4316. https://doi.org/10.1007/s10853-008-2633-y
Wen Ya, Lu Y., Qin X., Xiao H. // Mater. Sci. Forum. 2011. V. 686. P. 778. https://doi.org/10.4028/www.scientific.net/MSF.686.778
Tyumentsev V.A., Belenkov E.A., Shveikin G.P., Podkopaev S.A. // Carbon. 1998. V. 36. № 7/8. P. 845. https://doi.org/10.1016/S0008-6223(97)00143-7
Samoilov V.M., Verbets D.B., Bubnenkov I.A. et al. // Inorgan. Mater.: Appl. Res. 2018. V. 9. № 5. P. 890. https://doi.org/10.1134/S2075113318050258
Zhao J., Yang L., Li F. et al. // Carbon. 2009. V. 47. № 3. P. 744. https://doi.org/10.1016/j.carbon.2008.11.006
Lachter J., Bragg R.M. // Phys. Rev. B. 1986. V. 33. № 12. P. 8903. https://doi.org/10.1103/PhysRevB.33.8903
Kawamura K., Bragg R.H. // Carbon. 1986. V. 24. № 3. P. 301. https://doi.org/10.1016/0008-6223(86)90231-9
Vazquez-Santos M.B., Geissler E., Laszlo K. et al. // J. Phys. Chem. C. 2012. V. 116. № 1. P. 257. https://doi.org/10.1021/jp2084499
Ong T.S., Yang H. // Carbon. 2000. V. 38. № 6. P. 2077. https://doi.org/10.1016/S0008-6223(00)00064-6
Salver-Disma F., Tarascon J.-M., Clinard C., Rouzaud J.-N. // Carbon. 1999. V. 37. № 12. P. 1942. https://doi.org/10.1016/S0008-6223(99)00059-7
Tadjani M., Lechter J., Kabret T.S., Bragg R.H. // Carbon. 1986. V. 24. № 4. P. 447. https://doi.org/10.1016/0008-6223(86)90266-6
Aladekomo J.B., Bragg R.H. // Carbon. 1990. V. 28. № 6. P. 897. https://doi.org/10.1016/0008-6223(90)90338-Y
Kirian I., Rud A., Lakhnik A. // Materials Science. Non-Equilibrium Phase Transformations. 2021. V. 7. № 1. P.11.
Xing T., Li L.H., Hou L. et al. // Carbon. 2013. V. 57. P. 515. https://doi.org/10.1016/j.carbon.2013.02.029
Shen T.D., Ge W.Q., Wang K.Y. et al. // NanoStructured Materials. 1996. V. 7. № 4. P. 393. https://doi.org/10.1016/0965-9773(96)00010-4
Mendoza-Duarte J.M., Martinez-Sanchez R., Estrada-Guel I. // Microsc. Microanal. 2013. V. 19. P. 1598. https://doi.org/10.1017/S1431927613009987
Touzik A., Hentsche M., Wenzel R., Hermann H. // J. Alloys Compd. 2006. V. 421. P. 141. https://doi.org/10.1016/j.jallcom.2005.08.090
Li Z.Q., Zhou Y. // Physica B. 2010. V. 405. P. 1004.
Khandaker M.U., Nawi S.N.M., Sani S.F.A. et al. // Radiat. Phys. Chem. 2022. V. 201. P. 110498. https://doi.org/10.1016/j.radphyschem.2022.110498
Тюменцев В.А., Фазлитдинова А.Г. // ЖТФ. 2016. Т. 86. № 3. С. 62. https://doi.org/10.1134/S106378421603021X
Чуриков В.В., Тюменцев В.А., Подкопаев С.А. // Журн. прикл. химии. 2010. Т. 83. № 6. С. 938. https://doi.org/10.1134/S107042721006011X
Тюменцев В.А., Фазлитдинова А.Г., Подкопаев С.А. // ЖТФ. 2019. Т. 89. № 12. С. 1862.
Тюменцев В.А., Фазлитдинова А.Г. // Заводская лаборатория. Диагностика материалов. 2019. Т. 85. № 11. С. 31.
Дополнительные материалы отсутствуют.
Инструменты
Российские нанотехнологии