Российские нанотехнологии, 2024, T. 19, № 2, стр. 203-213
Антибактериальные и малодефектные покрытия на основе графеновых чернил
С. Е. Димитриева 1, С. А. Баскаков 2, 3, *, Ю. В. Баскакова 2, 3
1 Физический институт им. П.Н. Лебедева РАН
Москва, Россия
2 ФИЦ проблем химической физики и медицинской химии РАН
Черноголовка, Россия
3 ООО “ГРАФЕНОКС”
Черноголовка, Россия
* E-mail: graphenox@gmail.com
Поступила в редакцию 10.11.2023
После доработки 12.12.2023
Принята к публикации 12.12.2023
Аннотация
Разработана оригинальная методика получения графеновых чернил на органической основе методом микромеханической эксфолиации графита в 1-метил-2-пирролидоне (NMP) с последующим выделением графеновых частиц сменой растворителя и стабилизацией их этилцеллюлозой. Показано, что выход графеновых частиц методом микромеханической эксфолиации в NMP более чем в 2 раза превышает аналогичный параметр при использовании диметилформамида (ДМФА) в качестве растворителя. Графеновые чернила на органической основе могут быть использованы в качестве антибактериальных, антикоррозионных покрытий, обладающих высокой адгезией и низкой дефектностью. Исследования показали высокую бактерицидную эффективность графеновых чернил 98.11–99.98% на примере Pseudomonas aeruginosa и Staphylococcus epidermidis, что характеризует разработанный композит как эффективное антибактериальное средство.
ВВЕДЕНИЕ
Графен представляет собой структуру sp2-гибридизованных атомов углерода, соединенных в тонкий, толщиной в 1 атом, слой [1, 2]. Графеновые материалы включают в себя различные структуры: чистый/природный графен, оксид графена (ОГ), восстановленный ОГ, графеновые нанопластины, графеновые слои, полученные методом химического осаждения паров (CVD-метод). Графеновые материалы обладают выдающимися свойствами, включая высокую механическую прочность, большую площадь поверхности, жесткость, отличную биосовместимость, великолепные электро- и теплопроводящие свойства, низкую газопроницаемость и др. [2–6]. Графен и его модификации имеют большой потенциал применения в различных областях, включая энергетику (аккумуляторы, топливные элементы), гибкую электронику, механические, оптические и биосенсоры, композиционные материалы с улучшенными характеристиками и многое другое [7–9].
Использование графена в передовых медицинских применениях, таких как генная инженерия, тканевая инженерия, инновационное протезирование, таргетная терапия, биовизуализация, биосенсоры, может дать существенные положительные результаты и высокие достижения [10–12]. Многие исследовательские работы показали наличие антибактериальной эффективности графена как против грамположительных, так и против грамотрицательных бактерий [13, 14]. Сила антибактериального воздействия зависит от многих факторов, таких как площадь и толщина графеновых частиц, наличие или отсутствие функциональных групп и их состав, тип бактериального агента, время выдержки, pH среды и пр. [15–20]. Более того, недавние исследования показали, что графеновые материалы, такие как ОГ и его производные, обладают противовирусной активностью широкого спектра действия в отношении вирусов псевдобешенства (PRV), РНК-содержащих вирусов эпидемической диареи свиней (PEDV), а также коронавируса SARS-CoV-2 (COVID 2019) [21–23].
Несмотря на выдающиеся свойства графена, он имеет некоторые ограничения в отдельных приложениях, требующих определенных характеристик, например хорошей дисперсности в некоторых жидких средах для создания малодефектных покрытий [24].
Малофункциализированный графен имеет плохую диспергируемость и высокую склонность к агрегации из-за сильных межплоскостных взаимодействий, ограничивающих его антибактериальное применение. Это ограничение можно преодолеть, включив полимерный дисперсант в графен для образования стабильной дисперсии графен–полимер (чернила) и предотвращения его агрегации [25].
В течение последних десяти лет чернила на основе графена использовались для изготовления проводящих компонентов для ряда передовых применений в печатной электронике с использованием различных видов печати: струйной [26, 27], трафаретной [28, 29], 3D-печати [30]. Недавно было получено несколько нанокомпозитов полимер–графен для усиления антибактериальной активности с использованием полимерных матриц, таких как поливиниловый спирт (ПВС) [31, 32], хитозан [33–36], поли(молочная кислота) (PLA) [37], поли-N-винилкарбазол (ПВК) [38, 39] и поли-L-лизин (PLL) [40].
Однако многие из разработанных полимер-графеновых композитов не подходят для нанесения устойчивых, бездефектных покрытий с высокой адгезией и антибактериальными свойствами, поэтому задача совершенствования графеновых композиций и методов их получения является актуальной, в частности для пищевой промышленности, где требуется активная защита разного вида поверхностей, производственного оборудования, системы вентиляции, спецодежды от органических и бактериальных загрязнений, в том числе биопленок.
В настоящем исследовании был решен ряд задач для получения графеновых чернил (ГЧ) высокого качества, которые формируют тонкие малодефектные покрытия с высокой адгезией. Модифицирован метод механической эксфолиации с целью повышения эффективности процесса получения основы ГЧ. Исследованы механические и физико-химические свойства графеновых частиц и покрытий, получаемых при нанесении ГЧ на различные субстраты. Показаны высокие антибактериальные свойства разработанных графеновых дисперсий.
МАТЕРИАЛЫ И МЕТОДЫ
Материалы. В работе использовали графит марки ГК-1 (графит карандашный, зольность 1.0 мас. %, ГОСТ 4404-78); 1-метил-2-пирролидон (АО “ЭКОС-1”), изготовленный по ТУ 2633-036-44493179-99; N,N-диметилформамид х.ч. (АО “ЭКОС-1”), изготовленный по ГОСТ 20289-74; изопропиловый спирт х.ч. (АО “ЭКОС-1”), изготовленный по ТУ 2632-181-44493179-2014; ацетон х.ч. (АО “ЭКОС-1”), изготовленный по ТУ 2633-018-44493179-98; этилцеллюлозу (Sigma-Aldrich) с содержанием этоксильных групп 48.0–49.5 мас. %.
Методика получения графеновых чернил. ГЧ, которые представляют собой суспензию графеновых частиц в органическом растворителе, получали собственным оригинальным способом. Основу чернил (графеновые частицы) получали методом мокрого помола графита в планетарно-шаровой мельнице (ПШМ). Для этого 20 г графита помещали в размольный стакан объемом 500 мл и добавляли 200 мл N-метилпироллидона (NMP) или N,N-диметилформамида (ДМФА) и 70 шаров диаметром 15 мм. Стакан помещали в ПШМ RETSCH PM100 (Германия) и проводили размол при 450 об./мин. Время размола составляло от 1 до 6 ч, после чего графитовую суспензию центрифугировали при 3000 g в течение 5 мин. Полученная после центрифугирования суспензия имела черный цвет, при сильном разбавлении она была прозрачна на просвет, видимой агрегации не наблюдалось.
Графеновые частицы, полученные механической жидкостной эксфолиацией графита, использовали для приготовления чернил. Использование суспензии графена в NMP в качестве чернил во многих приложениях будет иметь определенные трудности, связанные с долгим временем сушки покрытия, так как NMP имеет низкую летучесть и высокую температуру кипения (206°С), а также чрезвычайно высокую подвижность. Поэтому для приготовления чернил был использован метод смены растворителя. Осаждение графеновых частиц из суспензии в NMP выполняли добавлением дистиллированной воды в объеме 15–20%. После этого осадок декантировали с помощью центрифуги и многократно промывали ацетоном и сушили.
Для получения чернил сухой графеновый порошок 15 г засыпали в 1 л изопропанола и обрабатывали ультразвуковым диспергатором в течение 25–30 мин, при необходимости охлаждая емкость. Далее добавляли 2 г порошка этилцеллюлозы в качестве стабилизатора графена и повторно озвучивали 15 мин. Полученные чернила имели концентрацию нелетучих веществ 17 г/л.
Методы исследования. Для оценки дефектности на микроуровне использовали метод сканирующей электронной микроскопии (СЭМ). Образцы графенового покрытия наносили на кремниевую пластинку однократным погружением с последующей сушкой. Микрофотографии получали на сканирующем электронном микроскопе Zeiss SUPRA 25 (энергия электронов 3.4 кВ, давление в камере 2 × 10–5 Пa). Оптические микрофотографии поверхности чернил были получены с помощью цифрового USB-микроскопа (Andonstar ADSM302 HDMI, Китай).
Спектры комбинационного рассеяния света (КРС) измеряли с помощью микроскопа-спектрометра Bruker Senterra. Длина волны возбуждения 532 нм, мощность лазера 2 мВт в точке образца с перетяжкой пучка 1 мм.
Для определения гидрофобных свойств поверхности измеряли контактный угол смачивания на приборе OCA 20 (Data Physics Instruments GmbH) при комнатной температуре.
Шероховатость поверхности образцов оценивали по ГОСТ Р ИСО 4287-2014 “Национальный стандарт Российской Федерации. Геометрические характеристики изделий (GPS). Структура поверхности. Профильный метод. Термины, определения и параметры структуры поверхности”. Для выполнения исследования использовали профилометр Mitutoyo SJ-210 (Япония).
Адгезию покрытий измеряли по ГОСТ 32702.2–2014 (ISO 16276-2:2007) “Материалы лакокрасочные. Определение адгезии методом Х-образного надреза”. Настоящий стандарт устанавливает метод определения адгезии (устойчивости к отслаиванию) Х-образным надрезом лакокрасочных покрытий, предназначенных для антикоррозионной защиты стальных конструкций. Покрытие должно быть прорезано до окрашиваемой поверхности. Сопротивление систем защитных лакокрасочных покрытий адгезионному или когезионному разрушению определяют методом Х-образного надреза и оценивают по качеству, используя шкалу от 0 до 5 баллов (от минимального до максимального разрушения). Метод Х-образного надреза может быть использован на покрытиях любой толщины, включая твердые покрытия. Для этого метода делают два надреза под углом друг к другу в форме буквы “X”. На место надреза накладывают липкую ленту и пальцем плотно прижимают ее к покрытию, а затем удаляют под определенным углом вместе с отслоившимися участками покрытия. Результат данного определения выражают в баллах в соответствии с наблюдаемыми разрушениями. При применении данного метода покрытие прорезают до окрашиваемой поверхности, используя хорошо наточенный режущий инструмент.
Испытания на коррозионную устойчивость выполняли на стальных пластинах марки 20 (100 × 100 мм). Пластины на 10 сут помещали в стеклянную емкость, на дно которой устанавливали стакан со 100 мл 1 М соляной кислоты. Пластины располагали так, чтобы не было контакта с жидкостью, они находились в контакте только с газовой фазой (парами соляной кислоты).
Цифровая микроскопия была выполнена на микроскопе ADSM302 Andonstar, оборудованном камерой 12 mpx с максимальным увеличением 560×.
Для определения выхода графеновых частиц в разных растворителях были проведены следующие операции. 20 г графита помещали в размольный стакан объемом 500 мл и добавляли 200 мл растворителя (NMP или ДМФА) и 70 шаров. Смесь обрабатывали в ПШМ RETSCH PM100 при 450 об./мин в течение часа. Далее отбирали 1 мл смеси графит/растворитель и центрифугировали при 5000 об./мин. Точно отобранный объем супернатанта высушивали на предметном стекле и по разнице масс определяли концентрацию графеновых частиц. Затем смесь обрабатывали еще 1 ч и операции повторяли.
Для исследования антибактериальных свойств разработанного покрытия использовали смесь микроорганизмов, содержащую Pseudomonas aeruginosa и Staphylococcus epidermidis, предоставленную АО “КБК Черемушки”.
Для получения тестовой бактериальной суспензии микроорганизмы культивировали в аэробных условиях при 37°С на триптон-соевом бульоне (TSB) до концентрации не менее 1 × 105 КОЕ/см3. Ночную (18-часовую) культуру наносили на исследуемое покрытие (чернила). Покрытие ГЧ наносили непосредственно на чашки Петри. После высыхания покрытие орошали 1 мл микробной суспензии, далее чашки помещали в термостат при 37°С на сутки, после чего в каждую чашку добавляли по 2 мл фосфатного буфера, выдерживали 1 ч, разрушали с помощью стерильной иглы. Не менее 1 мл жидкости асептически собирали и переносили на питательную среду для количественного определения микроорганизмов.
РЕЗУЛЬТАТЫ И ИХ ОБСУЖДЕНИЕ
На рис. 1 можно видеть образец суспензии графена в NMP и полученные из нее ГЧ на органической основе (изопропиловом спирте).
Рис. 1.
Образцы суспензии графена в NMP (а) и полученные из нее графеновые чернила на основе изопропилового спирта (б).
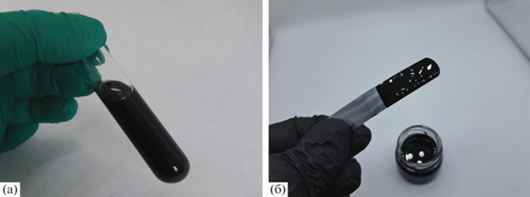
Микроскопический анализ графеновых частиц показал, что в большинстве они представляют собой плоские структуры с неровными краями и размерами от 50 до 400 нм.
На рис. 2 представлены СЭМ-изображения графеновых частиц, полученных при мокром помоле, и слоя ГЧ после нанесения их на кремниевую пластинку.
Рис. 2.
СЭМ-изображения графеновых частиц после размола и центрифугирования (а) и покрытия на основе графеновых чернил (б).
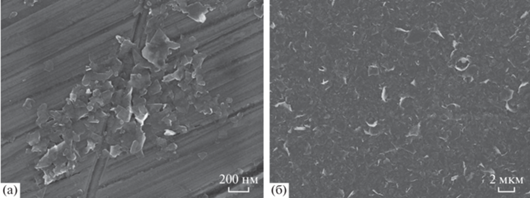
Химическая структура графена делает его хорошо подходящим для спектроскопии КРС. Атомы углерода, упакованные в гексагональную решетку с образованием sp2-связей, приводят к появлению сильно поляризуемых π-связей, дающих интенсивный сигнал КРС [41, 42]. Поэтому данный метод исследования может использоваться для оценки качества и толщины графена. Поскольку спектроскопия КРС является неразрушающим методом, имеет высокое пространственное и спектральное разрешение, она хорошо подходит для сбора подробной информации о графеновых материалах как в виде пленки, так и порошков.
На рис. 3 видно, что полученные КРС-спектры отчетливо проявляют характерные спектральные сигналы графитовых слоев, т.е. G- и 2D-полосы. В то время как пик G связан с относительным движением sp2-атомов углерода и указывает на присутствие графена. D-полоса – это пик, который указывает на наличие дефектов в структуре графена. Его можно отследить, чтобы выделить области с особенно высоким содержанием дефектов. Чем интенсивнее эта полоса, тем выше уровень беспорядка внутри структуры образца. Этот пик вызван дыхательной модой sp2-колец углерода, и они должны находиться рядом с дефектом, чтобы быть КРС-активным [43, 44]. 2D-пик является вторым порядком пика D и всегда виден даже в отсутствие пика D. Известно, что отношение интенсивностей I(D)/I(G) возрастает с ростом количества дефектов в структуре графена [45]. Для полученного графенового порошка отношение интенсивностей полос D/G составляет 0.57, в то время как для СVD-графена оно имеет значение 0 [46–48].
Важной характеристикой метода получения ГЧ является выход графеновых частиц при размоле графита в органических растворителях. В табл. 1 и на рис. 4 представлены результаты исследования выхода графеновых частиц механической эксфолиацией в разных растворителях и при разном времени размола. Из таблицы видно, что концентрация графеновых частиц в NMP выше таковой для ДМФА более чем в 2 раза при одном и том же времени размола. Сравнивая результаты, полученные методом жидкостной ультразвуковой эксфолиации (например, [49]) и полученные в настоящем исследовании, можно констатировать, что разработанный метод мокрого помола графита эффективнее более чем в 10 раз.
Таблица 1.
Зависимость концентрации (мг/мл) графеновых частиц в чернилах от времени размола и типа растворителя
Время размола, ч | Концентрация графена, мг/мл | |
---|---|---|
NMP | ДМФА | |
1 | 1.2 | 0.5 |
2 | 1.6 | 0.7 |
3 | 2.5 | 1.0 |
4 | 3.3 | 1.3 |
5 | 3.9 | 1.7 |
6 | 4.1 | 1.9 |
Полученные ГЧ хорошо наносятся на поверхности различного типа (бумага, ткани, стекло, полимеры). При нанесении на металлические поверхности можно создавать антикоррозионные проводящие покрытия для электродов источников тока и в целом для защиты поверхности металлов от негативного влияния окружающей среды. На рис. 5 представлены фотографии алюминиевой детали до (а) и после (б) нанесения ГЧ микрокапельным методом, а также СЭМ-изображение поверхности пленки, образующейся из ГЧ (в, г). Видно, что чернила образуют сплошную тонкую глянцевую поверхность.
Рис. 5.
Оптические фотографии алюминиевой детали до (а) и после (б) нанесения ГЧ микрокапельным методом; СЭМ-изображения поверхности пленки чернил при разном разрешении (в, г).
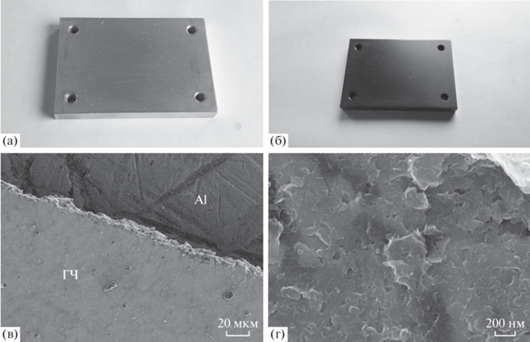
Важным показателем надежности и долговечности графеновых покрытий является адгезия. Ее оценку проводили согласно ГОСТ 32702.2-2014 по 5-балльной системе, где 0 баллов – отслаивания покрытия после удаления липкой ленты не происходит, 5 баллов – покрытие удаляется полностью. На рис. 6 приведены фотографии испытаний покрытий ГЧ на адгезию на алюминиевой (а, б), медной (в, г) и нержавеющей фольге (д, е). По результатам тестирования установлено, что данные покрытия обладают высокой адгезией ко всем типам металлов, исследованных в работе. Из рис. 6 можно видеть, что отслаивания или удаления покрытия клейкой лентой не происходит, результаты испытания согласно ГОСТ 32702.2-2014 можно оценить в 0 баллов.
Результаты проведенного испытания ГЧ на коррозионную устойчивость показали, что они имеют высокую устойчивость в условиях длительного воздействия паров 1 М соляной кислоты. На рис. 7 представлены фотографии образцов высокоуглеродистой стальной пластины марки 20 (а) после выдерживания в парах соляной кислоты. Видно, что пластина без покрытия чернилами (рис. 7б) имеет множественные очаги коррозии по всей поверхности. Пластина на рис. 7в частично покрыта ГЧ. Результат выдерживания этой пластины в коррозионных условиях изображен на рис. 7г. Затем защитное графеновое покрытие с пластины удалили с помощью растворителя, и можно видеть (рис. 7д), что поверхность, которая была защищена ГЧ, очагов коррозии не имеет, а незащищенные участки поверхности подверглись коррозионному воздействию. Результаты испытания однозначно указывают, что ГЧ можно использовать для нанесения тонких антикоррозионных покрытий на стальные поверхности.
Рис. 7.
Фотографии образцов в процессе исследования антикоррозионных свойств ГЧ: а – исходная стальная пластина марки 20, б – пластина после выдержки в парах соляной кислоты в течение 10 сут, в – пластина, частично покрытая слоем чернил, г, д – пластина в после испытания и удаления графенового слоя растворителем соответственно.
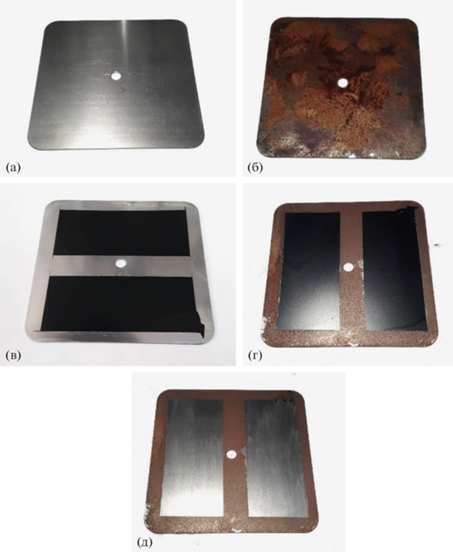
При разработке антибактериальных порытый важно сохранить их высокую бездефектность на микроуровне. Для этого был выполнен анализ покрытий на основе ГЧ с помощью сканирующего электронного и цифрового микроскопов. На рис. 8 представлены электронные и цифровые микрофотографии слоя ГЧ. Из рисунка видно, что чернила образуют плотное непористое покрытие, состоящее из графеновых частиц, связанных между собой этилцеллюлозой (темные участки – графеновые частицы, светлые – полимер), не имеющее видимых дефектов (трещин, вздутий, шагрени). На рис. 8в можно видеть покрытие ГЧ на медной фольге, полученное на цифровом микроскопе при увеличении ×48, демонстрирующее отсутствие таких дефектов.
Рис. 8.
СЭМ-изображения графеновых чернил на кремниевой пластине (а, б); цифровое микроскопическое изображение медной фольги в области окрашивания ГЧ (в).
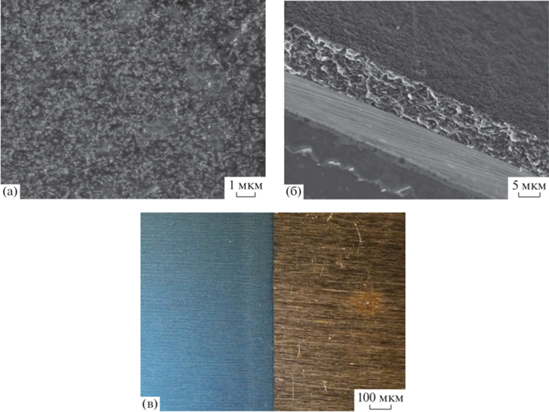
Для оценки шероховатости поверхности ГЧ был проведен анализ профиля поверхности алюминиевой фольги с графеновым покрытием и без него с помощью портативного профилометра Mitutoyo SJ-210. Полученные диаграммы показали, что профиль поверхности ГЧ практически полностью повторяет профиль чистой фольги, так как чернила наносятся тончайшим слоем (не более 1 мкм), поскольку размер частиц графена, находящийся в пределах 50–400 нм, легко позволяет это сделать. Перепад высот в профиле ГЧ и чистой фольги не более 1.0 мкм.
В табл. 2 представлены значения основных параметров шероховатости по ГОСТ Р ИСО 4287-2014. Для измерения неровности поверхности используют несколько определяющих параметров: Ra – значение исследуемого профиля с возможным отклонением (среднеарифметическим), Rz – высота измеряемых неровностей, определяемая по 10 основным точкам, Rq – среднеквадратичное отклонение оцениваемого профиля. Эти параметры измеряются в микрометрах. Из данных табл. 2 видно, что ГЧ имеют несколько большую шероховатость по сравнению с исходной фольгой, однако это отклонение не существенно и находится в пределах 12–20%. Таким образом, можно сделать общий вывод, что ГЧ образуют бездефектные покрытия с малой шероховатостью и высокой адгезией к металлическим поверхностям.
Таблица 2.
Параметры шероховатости измеренных образцов
Образец | Rq, мкм | Rz, мкм | Ra, мкм |
---|---|---|---|
ГЧ | 0.158 ± 0.08 | 0.769 ± 0.052 | 0.128 ± 0.011 |
Фольга | 0.139 ± 0.06 | 0.588 ± 0.032 | 0.114 ± 0.009 |
Для антибактериальных покрытий важным параметром является степень смачивания поверхности водой. Чем хуже поверхность будет смачиваться, тем дольше она будет защищена от биологических загрязнений и биопленок. Смачивание – это физическое взаимодействие жидкости с поверхностью твердого тела или другой жидкости. Смачивание бывает двух видов: иммерсионное (вся поверхность твердого тела контактирует с жидкостью) и контактное (состоит из трех фаз – твердая, жидкая, газообразная.) Смачивание зависит от соотношения между силами сцепления молекул жидкости с молекулами (или атомами) смачиваемого тела (адгезия) и силами взаимного сцепления молекул жидкости (когезия).
Если жидкость контактирует с твердым телом, то существуют две возможности смачивания:
– молекулы жидкости притягиваются друг к другу сильнее, чем к молекулам твердого тела. В результате силы притяжения между молекулами жидкости собирают ее в капельку. В этом случае говорят, что жидкость не смачивает поверхность;
– молекулы жидкости притягиваются друг к другу слабее, чем к молекулам твердого тела. В результате жидкость стремится прижаться к поверхности, расплывается по ней. В этом случае говорят, что жидкость смачивает поверхность.
Степень смачивания характеризуется углом смачивания. Краевой угол смачивания (КУС) – это угол, образованный касательными плоскостями к межфазным поверхностям, ограничивающим смачивающую жидкость, а вершина угла лежит на линии раздела трех фаз.
Был проведен анализ смачиваемости водой поверхности ГЧ в зависимости от количества наносимых слоев (от 1 до 3). На рис. 9 приведены фотографии капли воды на поверхности ГЧ: а – один, б – два, в – три слоя. Измеренный КУС находится в пределах 62°–64° и практически не зависит от количества слоев нанесения. Поверхности с КУС больше 60° считаются слабогидрофильными.
Рис. 9.
Измерение КУС поверхности ГЧ в зависимости от количества слоев нанесения: а – один, б – два, в – три слоя; г – образцы чернил с одним, двумя и тремя слоями (слева направо).
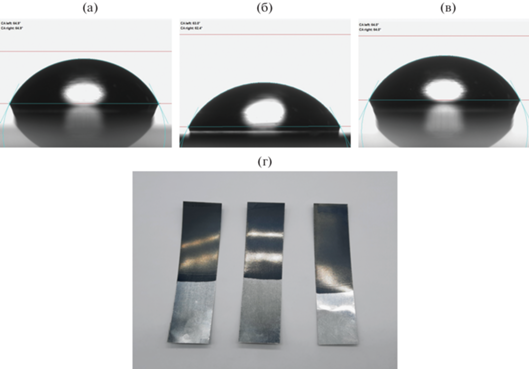
Было проведено исследование антибактериальных свойств покрытия на основе разработанных чернил. Смесь микроорганизмов, содержащую Pseudomonas aeruginosa и Staphylococcus epidermidis, культивировали для получения тестовой бактериальной суспензии в аэробных условиях при 37°С на TSB до концентрации не менее 1 × 105 КОЕ/см3. Ночную (18-часовую) культуру наносили на исследуемое покрытие (чернила). Разработанное покрытие ГЧ на органическом растворителе наносили непосредственно на чашки Петри. После высыхания покрытие орошали 1 мл микробной суспензии, далее чашки помещали в термостат при 37°С на сутки. Затем в каждую чашку добавляли по 2 мл фосфатного буфера, выдерживали 1 ч, разрушали с помощью стерильной иглы. Не менее 1 мл жидкости асептически собирали и переносили на питательную среду для количественного определения микроорганизмов. Результаты представлены на рис. 10.
Рис. 10.
Отношение микробиологической загрязненности образцов материала до (серый цвет) и после (черный цвет) выдержки на исследуемом покрытии.
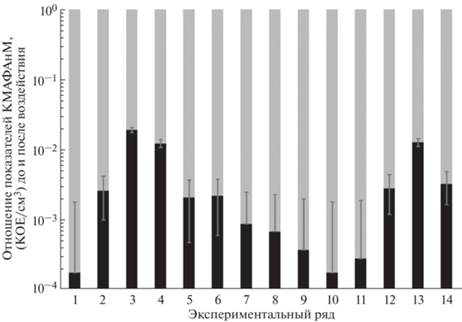
Существовал некоторый разброс значений измерений начальной обсемененности и количества микроорганизмов после экспозиции с исследуемым материалом. Рассчитанный по экспериментальным данным коэффициент корреляции Пирсона составил 0.25, что характеризует зависимость между исходной массой микроорганизмов и конечным их числом как достаточно слабую. При этом эффективность обеззараживания (рис. 10) составила от 98.11 до 99.98% со значением медианы 99.78% и средним значением 99.58%. Максимальное количество выживших микроорганизмов составило 7 × 103 КОЕ/см3, минимальное – 30 КОЕ/см3.
Таким образом, исследования показали высокую бактерицидную эффективность ГЧ (98.11–99.98%), что характеризует разработанный композит как эффективное антибактериальное средство.
ЗАКЛЮЧЕНИЕ
Разработана оригинальная методика получения графеновых чернил на органической основе методом микромеханической эксфолиации, заключающаяся в получении графеновых частиц из графита в 1-метил-2-пирролидоне в процессе ударно-сдвиговых деформаций, с последующим получением чернил сменой растворителя и стабилизацией эфиром целлюлозы.
Показано, что выход графеновых частиц по методу микромеханической эксфолиации в NMP более чем в 10 раз выше по сравнению с традиционной ультразвуковой эксфолиацией.
Исследования показали высокую бактерицидную эффективность ГЧ (98.11–99.98%). Наблюдается снижение обсемененности на 2–3 порядка, что характеризует разработанный композит как эффективное антибактериальное средство.
Графеновые чернила на органической основе могут быть использованы в качестве антибактериальных, антикоррозионных покрытий с высокой адгезией и устойчивостью к образованию дефектов на металлических поверхностях разного типа. Чернила можно наносить с помощью распылителя (краскопульта, аэрографа) или изготавливать в виде баллонного спрея.
Работа выполнена при поддержке Министерства науки и высшего образования Российской Федерации (в рамках проекта № 075-15-2020-775 и государственного задания № 124013000757-0) и Центра компетенции НТИ “Цифровое материаловедение: новые материалы и вещества”.
Список литературы
Geim A.K., Novoselov K.S. // Nat. Mater. 2007. V. 6. P. 183. https://doi.org/10.1038/nmat1849
Geim A.K. // Science. 2009. V. 324. P. 1530. https://doi.org/10.1126/science.1158877
Zhang Y., Tang T., Girit C. et al. // Nature. 2009. V. 459. P 820. https://doi.org/10.1038/nature08105
Balandin A., Ghosh S., Bao W. et al. // Nano Lett. 2008. V. 8. P. 902. https://doi.org/10.1021/nl0731872
Blake P., Brimicombe P., Nair R. et al. // Nano Lett. 2008. V. 8. P. 1704. https://doi.org/10.1021/nl080649i
Morozov S.V., Novoselov K.S., Katsnelson M.I. et al. // Phys. Rev. Lett. 2008. V. 100. P. 016602. https://doi.org/10.1103/PhysRevLett.100.016602
Aïssa B., Memon N.K., Ali A., Khraisheh M.K. // Front. Mater. 2015. V. 2. P. 58. https://doi.org/10.3389/fmats.2015.00058
Choi W., Lahiri I., Seelaboyina R. et al. // Crit. Rev. Solid State Mater. Sci. 2010. V. 35. P. 52. https://doi.org/10.1080/10408430903505036
Urade A.R., Lahiri I., Suresh K.S. // J. Minerals, Metals Materials Society (TMS). 2023. V. 75. P. 614https://doi.org/10.1007/s11837-022-05505-8
Sharma J., Sharma S., Ajay, Sharma L.K. // Materials Today: Proceedings. 2022. V. 63. P. 542. https://doi.org/10.1016/j.matpr.2022.03.662
Chung C., Kim Y.-K., Shin D. et al. // Acc. Chem. Res. 2013. V. 46. P. 2211. https://doi.org/10.1021/ar300159f
Krzysztof T., Wychowaniec J.K., Litowczenko J. // Nanomaterials. 2018. V. 8. P. 944. https://doi.org/10.3390/nano8110944
Al-Thani R.F., Patan N.K., Al-Maadeed M.A. // J. Biol. Sci. 2014. V. 14. P. 230. https://doi.org/10.1088/1757-899X/518/6/06201
Hu W., Peng C., Luo W. et al. // ACS Nano. 2010. V. 4. P. 4317. https://doi.org/10.1088/1757-899X/518/6/062012
Zou X., Zhang L., Wang Z. et al. // J. Am. Chem. Soc. 2016. V. 138. P. 2064. https://doi.org/10.1021/jacs.5b11411
Akhavan O., Ghaderi E. // ACS Nano. 2010. V. 4. P. 5731. https://doi.org/10.1021/nn101390x
Gurunathan S., Han J.W., Dayem A.A. et al. // Int. J. Nanomed. 2012. V. 7. P. 5901. https://doi.org/10.2147/IJN.S37397
Liu S., Zeng T.H., Hofmann M. et al. // ACS Nano. 2011. V. 5. P. 6971. https://doi.org/10.1021/nn202451x
Carpio I.E.M., Santos C.M., Wei X. et al. // Nanoscale. 2012. V. 4. P. 4746. https://doi.org/10.1039/C2NR30774J
Chen J., Peng H., Wang X. et al. // Nanoscale. 2014. V. 6. P. 1879. https://doi.org/10.1039/C3NR04941H
Fukuda M., Islam M.S., Shimizu R. et al. // ACS Appl. Nano Mater. 2021. V. 4. P. 11881. https://doi.org/10.1039/D3NA00084B
Seifi T., Kamali Ali R. // Rev. Med. Drug Discov. 2021. V. 11. P. 100099. https://doi.org/10.1016/j.medidd.2021.100099
Du X., Xiao R., Fu H. et al. // Mater. Sci. Eng. C. 2019. V. 105. P. 110052. https://doi.org/10.1007/s13205-021-02689-9
Dreyer D.R., Park S., Bielawski C.W. et al. // Chem. Soc. Rev. 2010. V. 39. P. 228. https://doi.org/10.1039/B917103G
Santos C.M., Mangadlao J., Ahmed F. et al. // Nanotechnol. 2012. V. 23. P. 395101.
He P., Derby B. // 2D Mater. 2017. V. 4. P. 021021. https://doi.org/10.1002/admi.201700944
Su Y., Du J., Sun D. et al. // Nano Res. 2013. V. 6. P. 842. https://doi.org/10.1007/s12274-013-0362-2
Arapov K., Rubingh E., Abbel R. et al. // Adv. Funct. Mater. 2016. V. 26. P. 586. https://doi.org/10.1002/adfm.201504030
Xu Y., Schwab M.G., Strudwick A.J. et al. // Adv. Energy Mater. 2013. V. 3. P. 1035. https://doi.org/10.1007/s12274-017-1451-4
Secor E.B., Gao T.Z., Dos Santos M.H. et al. // ACS Appl. Mater. Interfaces. 2017. V. 9. P. 29418. https://doi.org/10.1021/acsomega.2c01069
Xu Y., Hong W., Bai H. et al. // Carbon. 2009. V. 47. P. 3538. https://doi.org/10.1016/j.carbon.2009.08.022
Liang J., Huang Y., Zhang L. et al. // Adv. Funct. Mater. 2009. V. 19. P. 2297. https://doi.org/10.1002/adfm.200801776
Lim H., Huang N., Loo C. // J. Non-Cryst. Solids. 2012. V. 358. P. 525. https://doi.org/10.1016/j.jnoncrysol.2011.11.007
Lu B., Li T., Zhao H. et al. // Nanoscale. 2012. V. 4. P. 2978. https://doi.org/10.1039/C2NR11958G
Mazaheri M., Akhavan O., Simchi A. // Appl. Surf. Sci. 2014. V. 301. P. 456. https://doi.org/10.1016/j.apsusc.2014.02.099
Ko T.Y., Kim S.Y., Kim H.G. et al. // Chem. Lett. 2012. V. 42. P. 66. https://doi.org/10.1246/cl.2013.66
Liu C., Shen J., Yeung K.W.K. et al. // ACS Biomater. Sci. Eng. 2017. V. 3. P. 471. https://doi.org/10.1021/acsbiomaterials.6b00766
Santos C.M., Tria M.C.R., Vergara R.A.M.V. et al. // Chem. Commun. 2011. V. 47. P. 8892. https://doi.org/10.1088/0957-4484/23/39/395101
Musico Y.L.F., Santos C.M., Dalida M.L.P. et al. // ACS Sustain. Chem. Eng. 2014. V. 2. P. 1559. https://doi.org/10.1021/sc500044p
Some S., Ho S.-M., Dua P. et al. // ACS Nano. 2012. V. 6. P. 7151. https://doi.org/10.1021/acsnano.6b05109
Ni Z., Wang Y., Yu T. et al. // Nano Res. 2008. V. 1. P. 273. https://doi.org/10.1007/s12274-008-8036-1
Ferrari A.C., Basko D.M. // Nature Nanotechnology. 2013. V. 8. P. 235. https://doi.org/10.1038/nnano.2013.46
Ferrari A.C. // Solid State Commun. 2007. V. 147. P. 47. https://doi.org/10.1016/j.ssc.2007.03.052
Ferrari A.C., Meyer J.C., Scardaci V. et al. // Phys. Rev. Lett. 2006. V. 97. P. 187401. https://doi.org/10.1103/PhysRevLett.97.187401
Shulga Y.M., Martynenko V.M., Muradyan V.E. et al. // Chem. Phys. Lett. 2010. V. 498. P. 287. https://doi.org/10.1134/S0018143912020099
Costa M.C.F., Sousa M.R.M., Larrudé D.R.G. et al. // eXPRESS Polym. Lett. 2019. V. 13. P. 52. https://doi.org/10.3144/expresspolymlett.2019.6
Chen Z., Wang Z., Li X. et al. // ACS Nano. 2017. V. 11. P. 4507. https://doi.org/10.1021/acsnano.6b08027
Yu C., Li D., Wu W. et al. // J. Mater. Sci. 2014. V. 49. P. 8311. https://doi.org/10.1007/s10853-014-8539-y
Ali S., Nasir H. // Nano Hybrids and Composites. 2017. V. 14. P. 17. https://doi.org/10.4028/www.scientific.net/NHC.14.17
Дополнительные материалы отсутствуют.
Инструменты
Российские нанотехнологии