Нефтехимия, 2019, T. 59, № 2, стр. 200-206
Трансформация прекурсоров палладия, нанесенных на алюмооксидный носитель, в процессе восстановительной активации
А. И. Ласкин 1, *, И. Р. Ильясов 1, А. А. Ламберов 1
1 Казанский (Приволжский) федеральный университет
Казань, Россия
* E-mail: artemka166@mail.ru
Поступила в редакцию 17.01.2018
После доработки 15.10.2018
Принята к публикации 14.07.2018
Аннотация
Исследована трансформация солей палладия, нанесенных на алюмооксидный носитель, при изотермической обработке в восстановительной атмосфере с целью определения оптимальной температуры восстановления Pd/Al2O3-катализатора. Установлено, что ацетилацетонат Pd характеризуется более сильным взаимодействием с поверхностными центрами оксида алюминия, по сравнению с ацетатным комплексом. Это определяет меньший диаметр формирующихся частиц активного компонента для первого прекурсора во всем температурном интервале восстановительных обработок. Оптимальной температурой восстановления нанесенных солей палладия является 500°С, при которой образуются частицы палладия, характеризующиеся максимальной конверсией метилацетилена и пропадиена с высокой селективностью превращения в пропилен. Системы, активированные при температуре до 400°С, обладают низкой активностью в гидрировании метилацетилена и пропадиена, что обусловлено неполным восстановлением палладия из его солей с формированием окисленных и координационно-ненасыщенных форм активного компонента.
В настоящее время очистка товарных алкенов от примесей ацетиленовых и диеновых углеводородов (УВ) методом селективного гидрирования играет одну из главных ролей в технологии производства полимеров, так как к содержанию этих примесей в мономерах, предъявляются достаточно жeсткие требования [1–3]. Несмотря на большое количество экспериментальных исследований в области селективного гидрирования ацетиленовых УВ на металлических катализаторах, задача увеличения выхода целевого продукта при одновременном обеспечении высокой активности и стабильной работы катализатора в условиях промышленной эксплуатации до настоящего времени полностью не решена.
Одним из самых распространенных способов получения металлических катализаторов, в том числе палладиевых, является нанесение исходных соединений на носители с последующей их активацией в окислительно-восстановительных средах. Электронные и геометрические характеристики частиц активного компонента во многом определяются уже на стадии нанесения соединений металла [4–8]. При этом последующие окислительно-восстановительные активации являются определяющими в эксплуатационных характеристиках катализатора [9–12]. Поэтому изучение процессов, происходящих на поверхности носителя, в частности реакций восстановления прекурсоров палладия с формированием их активных форм, имеет чрезвычайно важное значение для приготовления высокоэффективных катализаторов.
ЭКСПЕРИМЕНТАЛЬНАЯ ЧАСТЬ
Процесс получения катализаторов заключается в нанесении растворов соединений палладия на алюмооксидный носитель методом пропитки.
При синтезе катализаторов в качестве исходных соединений использовали ацетат (99.9%) и ацетилацетонат (99.9%) Pd, полученные по методикам [13] и [14], соответственно. При синтезе катализаторов использовали δ-модификацию, полученную изотермической обработкой при 900°С экструдатов промышленного γ-Al2O3 производства “Редкинский катализаторный завод” (ТУ 6-68-5808009-306-85).
Нанесение ацетатата и ацетилацетоната Pd на носитель δ-Al2O3 в количествах, обеспечивающих содержание металла в катализаторе 0.3 мас. %, осуществляли методом пропитки из органических растворителей: хлористого метилена и бензола соответственно. Пропитку носителя растворами осуществляли при перемешивании в течение 2 ч с последующей сушкой при 40°С для образцов из ацетата палладия и 80°С – для ацетилацетоната палладия. Для каталитических испытаний катализаторов восстановление проводили непосредственно в реакторе в токе водорода в течение 2 ч.
Сравнительные испытания образцов катализаторов осуществляли в лабораторной установке проточного типа с изотермическим реактором. Объем загружаемого катализатора составлял 0.1 г. В качестве исходного углеводородного потока использовали пропан-пропиленовую фракцию (табл. 1).
Таблица 1.
Состав пропан-пропиленовой фракции
Наименование компонента | Содержание, мас. % |
---|---|
Пропан | 6.88 |
Пропилен | 88.87 |
Метилацетилен | 1.58 |
Пропадиен | 2.37 |
Испытания катализаторов проводили в условиях неполной конверсии при скорости подачи пропан-пропиленовой фракции 1000 ч–1, температуре 15°С и мольном соотношении водорода к ацетиленам 1.2 : 1.
Углеводородный состав исходной пропан-пропиленовой фракции и продуктов гидрирования определяли методом ГХ на приборе Хромос ГХ-1000 с пламенно-ионизационным детектором и капиллярной колонкой Valco PLOT VP-Alumina KCl длиной 50 метров с фазой оксида алюминия 10 мкм.
По результатам хроматографического анализа рассчитывали:
– конверсию метилацетилена и пропадиена, как отношение интегрального количества прореагировавшего метилацетилена и пропадиена к количеству метилацетилена и пропадиена в исходном сырье:
– селективность по пропилену, как отношение интегрального количества образовавшегося пропилена к интегральному количеству превращенного метилацетилена и пропадиена:
– скорость гидрирования метилацетилена и пропадиена (мкмоль/(гкат ч), как суммарное количество прореагировавшего метилацетилена и пропадиена в течение одного часа испытаний на единице массы М катализатора:
– число оборотов реакции TOF (ч–1), как отношение скорости гидрирования метилацетилена и пропадиена к количеству поверхностных доступных для реагирующих молекул атомов палладия:
Определение удельной поверхности, порометрического объема проводили на анализаторе Autosorb iQ MP Quantachrome (США). Удельную поверхность Sуд определяли методом низкотемпературной адсорбции азота, исходя из принятой площади поверхности молекулы азота 0.162 нм2. Плотность азота в нормальном жидком состоянии – 0.808 г/см3. Точность измерения Sуд ± 3%. Изотермы адсорбции азота получали при –196°С после дегазации образца при 300°С до остаточного давления 0.013 Па. Порометрический объем и распределение пор по размерам рассчитывали по десорбционной ветви изотермы, пользуясь стандартной процедурой Баррета–Джойнера–Халенды [3]. Точность измерения ±13%.
Определение кислотных свойств оксида алюминия осуществляли при помощи анализатора AutoChem 2950 HP. Для этого образец в количестве 0.5 г загружали в кварцевый реактор с последующей дегазацией в электрической печи прибора при 550°С, скорость подъема температуры 10°С/мин. Cкорость подачи газа носителя (Не) 10 мл/мин. Затем образец насыщали смесью 10% NH3 в He в при комнатной температуре в течение часа, после чего образец продували гелием при 100°С для удаления физически сорбированного аммиака. Спектры десорбции записывали в температурном диапазоне от 25–700°С.
Термопрограммируемое восстановление (ТПВ) водородом проводили в кварцевом реакторе на приборе AutoChem 2950 HP, совмещенным с масс-спектрометром Cirrus II фирмы Micromeritics. Образец катализатора восстанавливали в токе 5% H2 + Ar при нагреве до 700°С со скоростью 10°С/мин.
Хемосорбционное титрование монооксидом углерода проводили в кварцевом реакторе на приборе AutoChem 2950 HP фирмы Micromeritics. Образец катализатора предварительно восстанавливали в реакторе в атмосфере водорода в течение 2 ч и осушали при той же температуре в течение 2 ч, далее охлаждали в токе аргона до 25°С. После этого проводили титрование катализатора порциями монооксида углерода в токе гелия до полного насыщения поверхности образца. Дисперсность палладия рассчитывали из мольного соотношения Pd : CO = 1 : 1.
РЕЗУЛЬТАТЫ И ИХ ОБСУЖДЕНИЕ
В наших предыдущих работах [15] было показано, что использование в качестве носителя δ-Al2O3, характеризующегося низкой кислотностью, позволяет уменьшить количество образующихся олигомеров на поверхности катализатора в реакциях селективного гидрирования ацетиленовых и диеновых соединений. Поэтому при синтезе катализаторов использовали δ-модификацию, полученную изотермической обработкой при 900°С экструдатов промышленного γ-Al2O3 (ТУ 6-68-5808009-306-85).
Пористая структура носителя δ-Al2O3 характеризуется бимодальным распределением пор по размерам с максимумами при 40 и 83 Å (рис. 1).
Величина удельной поверхности оксида составляет Sуд = 95.8 м2/г, порометрический объем равен Vп = 0.282 см3/г (табл. 2). Вклад пор диаметром менее 50 Å в общее поровое пространство незначителен и составляет 3.6%. Доля мезопор 50–150 Å максимальна – 85.1%; доля крупных пор –11.4%.
Таблица 2.
Текстурные характеристики носителя
Параметр | ∑ | Распределение порометрического объема Vп (см3/г) [Sуд (м2/г)] и его доля (%), приходящаяся на поры диаметром (Å) | |||||||
---|---|---|---|---|---|---|---|---|---|
<50 | 50–100 | 100–150 | >150 | ||||||
Vп, см3/г | 0.282 | 0.010 | 3.6 | 0.189 | 67.3 | 0.050 | 17.8 | 0.032 | 11.4 |
Sуд, м2/г | 95.8 | 7.1 | 7.5 | 73.0 | 76.2 | 13.0 | 13.6 | 2.6 | 2.7 |
Рис. 2.
Масс-спектры ТПВ водородом для индивидуальных солей: (а) ацетата палладия; (б) ацетилацетоната палладия.
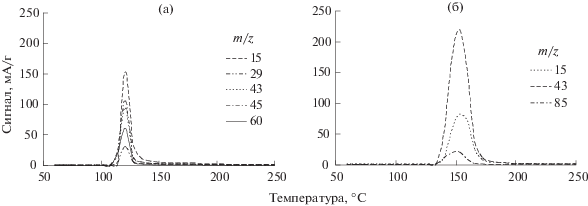
Суммарная концентрация кислотных центров Бренстеда и Льюиса алюмооксидного носителя $N_{{{\text{к }}{\text{.ц }}}}^{{{\text{о б щ }}}}$ (мкмоль/г), согласно данным термопрограммируемой десорбции аммиака, равна 77.6 мкмоль/г. При этом наибольший вклад в общее количество кислотных центров приходится на центры средний силы (Ed = 110–130 кДж/моль), их доля составляет 58.0% (45.0 мкмоль/г). Вклад слабых и сильных центров равен 31.1% (24.1 мкмоль/г) и 13.5% (10.5 мкмоль/г), соответственно (табл. 3).
Таблица 3.
Концентрация кислотных центров носителя по данным термопрограммируемой десорбции аммиака
$N_{{{\text{к }}{\text{.ц }}}}^{{{\text{о б щ }}}}$, мкмоль/г | Распределение $N_{{{\text{к }}{\text{.ц }}}}^{{{\text{о б щ }}}}$, (мкмоль/г) и их доли (%) | |||||
---|---|---|---|---|---|---|
слабые Ed < 100 |
средние 100 < Ed < 130 |
сильные Ed < 130 |
||||
мкмоль/г | % | мкмоль/г | % | мкмоль/г | % | |
77.6 | 24.1 | 31.1 | 45.0 | 58.0 | 10.5 | 13.5 |
Для анализа влияния поверхностных свойств оксида алюминия на процесс восстановительной активации солей палладия были проведены исследования восстановления исходных комплексов палладия и нанесенных на поверхность δ-Al2O3 методом температурно-программируемого восстановления водородом, совмещенного с масс-спектроскопией.
Восстановление индивидуальных солей палладия (рис. 2) показало полное разложение ацетата и ацетилацетоната Pd в атмосфере водорода в температурных областях 110–150°С и 130–200°С с максимумами при 111 и 147°С, с выделением уксусной кислоты и ацетилацетона, соответственно. При этом в масс-спектрах отмечаются фрагменты m/z, характерные для соответствующих анионов: m/z = = 15 (${\text{CH}}_{{\text{3}}}^{{\text{ + }}}$), 29 (HCO+), 43 (CH3–CO+), 45 (COOH+), 60 (CH3–COOH+), 85 (CH3–C(O)–CH2–CO+).
В отличиe от индивидуальных солей палладия, спектры температурно-программируемого восстановления солей, нанесенных на δ-Al2O3, характеризуются наличием двух широких областей поглощения водорода. Так, восстановление ацетата палладия происходит при 50–250°С и 300–600°С, а ацетилацетоната палладия – при 80– 250°С и 300–550°С (рис. 3). Эти отличия обусловлены взаимодействием исходных солей палладия с поверхностными кислотными центрами оксида алюминия. Последующее разбиение данных спектров на Гауссовы составляющие показало, что восстановление ацетата палладия протекает с формированием четырех максимумов поглощения водорода разной интенсивности: двух в низкотемпературной области при 90 и 140°С, двух в высокотемпературной при 420 и 510°С.
Рис. 3.
Спектры ТПВ водородом для нанесенных солей палладия на δ-Al2O3: (а) ацетата палладия; (б) ацетилацетоната палладия.
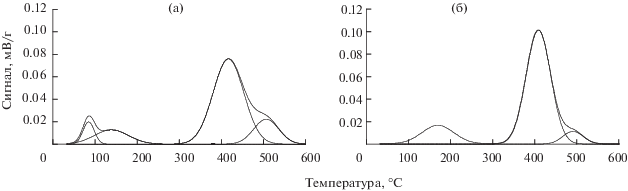
Для ацетилацетонатного комплекса характерно наличие трех максимумов при 170, 410 и 495°С (табл. 4). При этом более низкие температуры восстановления ацетата палладия, по сравнению с ацетилацетонатным комплексом, вероятно, обусловлены его менее сильным взаимодействием с поверхностными кислотными центрами с преобладанием физической адсорбции.
Таблица 4.
Результаты ТПВ водородом солей палладия, нанесенных на δ-Al2O3
Образец | ${{Q}_{{{{{\text{H}}}_{{\text{2}}}}}}}$, мкмоль/г | Температурный интервал пиков (ТИ) и соответствующее количество потребляемого водорода (${{Q}_{{{{{\text{H}}}_{{\text{2}}}}}}}$, мкмоль/г) | |||||||||||
---|---|---|---|---|---|---|---|---|---|---|---|---|---|
ТИ | Tmax, °С | ${{Q}_{{{{{\text{H}}}_{{\text{2}}}}}}}$ | TИ | Tmax, °С | ${{Q}_{{{{{\text{H}}}_{{\text{2}}}}}}}$ | TИ | Tmax, °С | ${{Q}_{{{{{\text{H}}}_{{\text{2}}}}}}}$ | TИ | Tmax, °С | ${{Q}_{{{{{\text{H}}}_{{\text{2}}}}}}}$ | ||
Pd(Ac)2/ δ-Al2O3 |
238.7 | 37–135 | 85 | 14.4 | 37–250 | 139 | 26.3 | 300–545 | 416 | 158.5 | 400–600 | 508 | 39.6 |
Pd(Acac)2/ δ-Al2O3 |
216.5 | – | – | – | 70–295 | 170 | 38.8 | 310–515 | 408 | 162.4 | 425–560 | 495 | 15.3 |
В высокотемпературной области от 300 до 600°С для обеих солей палладия, согласно масс-спектрометрии (рис. 4), характерно протекание реакции восстановления органических остатков до метана. Такая глубина восстановления, вероятно, обусловлена взаимодействием органического остатка с атомарным водородом, формирующимся на частицах палладия, восстановление которых происходит при более низких температурах.
Рис. 4.
Масс-спектры ТПВ водородом для солей палладия, нанесенных на δ-Al2O3: (а) ацетата палладия;( б) ацетилацетоната палладия.
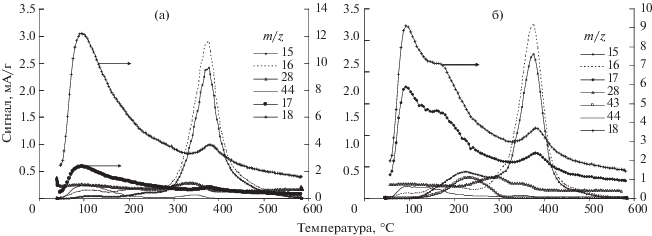
Для последующего анализа трансформации солей активного компонента на поверхности алюмооксидного носителя проводили оценку дисперсности палладия после восстановления образцов катализатора в изотермических условиях при стационарной температуре в температурном диапазоне 150–600°С.
Для образцов, синтезированных из ацетата палладия, зависимость дисперсности от температуры восстановления носит экстремальный характер с широким максимумом при температуре восстановления 300–400°С (табл. 5). Образец, восстановленный при 150°С, характеризуется средним диаметром частиц 3.2 нм, что определяет удельную величину поверхности металла, доступную для реагирующих молекул, 157.8 м2/г, а дисперсность – 35.4%. Увеличение температуры восстановительной обработки от 150 до 300 и 400°С сопровождается уменьшением диаметра частиц с 3.2 до 2.9 и 2.7 нм и ростом доступной поверхности металла 157.8 до 170.2 и 184.1 м2/г, соответственно, что обусловлено полнотой разложения комплекса палладия. Последующий рост температуры восстановления до 600°С приводит к значительному снижению удельной поверхности металла до 113.3 м2/г, что обусловлено интенсивным протеканием процессов спекания и агломерации с ростом диаметра частиц металла до 4.4 нм. Последнее, вероятно, связано с низкой прочностью связывания исходного комплекса палладия и формирующихся из него металлических частиц с поверхностными кислотными центрами оксида алюминия.
Таблица 5.
Результаты хемосорбционного титрования монооксидом углерода катализаторов, синтезированных нанесением ацетатного и ацетилацетонатного прекурсоров на δ-Al2O3
Образец | Т, °С | C (Pds), мкмоль/г | D, % | Sуд (Pd), м2/гPd | d, нм |
---|---|---|---|---|---|
Pd(Ac)2/δ-Al2O3 | 150 | 9.8 | 35.4 | 157.8 | 3.2 |
300 | 10.7 | 38.2 | 170.2 | 2.9 | |
400 | 11.6 | 41.3 | 184.2 | 2.7 | |
500 | 8.5 | 29.3 | 130.6 | 3.8 | |
600 | 7.1 | 25.4 | 113.3 | 4.4 | |
Pd(Acac)2/δ-Al2O3 | 150 | 13.4 | 46.7 | 208.1 | 2.4 |
300 | 15.6 | 54.7 | 243.6 | 2.0 | |
400 | 16.1 | 57.7 | 256.9 | 1.9 | |
500 | 14.3 | 50.5 | 225.0 | 2.2 | |
600 | 10.7 | 38.0 | 169.4 | 2.9 |
Увеличение температуры восстановления катализаторов на основе ацетилацетонатного комплекса, как и для первой системы, сопровождается ростом дисперсности металла в температурном диапазоне от 150 до 400°С и ее последующим уменьшением при температуре 500–600°С (табл. 5). При этом для ацетилацетонатной системы данное снижение дисперсности металла меньше, чем для ацетатного образца. Это обусловлено более высокой устойчивостью частиц металла к агрегации, вероятно, в результате более прочного взаимодействия ацетилацетонатного комплекса и частиц металла на его основе с поверхностными кислотными центрами, о чем свидетельствуют спектры ТПВ–Н2.
Каталитические характеристики экспериментальных образцов определяли в реакции гидрирования метилацетилена и пропадиена в пропан-пропиленовой фракции (табл. 6). Согласно полученным результатам, увеличение температуры восстановительной обработки катализаторов на основе ацетата и ацетилацетоната палладия с 150 до 400°С сопровождается ростом конверсии метилацетилена и пропадиена на 13.9 и 9.6%, что обусловлено увеличением количества поверхностных атомов палладия (табл. 7). При этом значения селективности превращения метилацетилена и пропадиена в пропилен остаются на том же самом уровне. Последующий рост температуры изотермической обработки до 500°С, несмотря на снижение дисперсности палладия, приводит к значительному росту конверсии метилацетилена и пропадиена. Это, вероятно, связано со структурированием частиц палладия и снижением количества координационно-ненасыщенных центров, обладающих низкой электронной плотностью на валентных орбиталях. Последнее приводит к прочной хемосорбции молекул ненасыщенных УВ с блокированием поверхности активного компонента. Катализаторы, термически активированные при 600°С, характеризуются более низкой конверсией метилацетилена и пропадиена, по сравнению с образцами, восстановленными при 500°С, что может быть обусловлено последующей агрегацией частиц палладия со снижением количества поверхностных атомов и их координационной ненасыщенностью.
Таблица 6.
Результаты каталитических испытаний катализаторов, синтезированных нанесением ацетатного и ацетилацетонатного прекурсоров на δ-Al2O3
Образец | Т, °С | WМА, ммоль/(г ч) | WПД, ммоль/(г ч) | WМАПД, ммоль/(г ч) | КМАПД, % | SПП, % |
---|---|---|---|---|---|---|
Pd(Ac)2/δ-Al2O3 | 150 | 0.19 | 0.45 | 0.64 | 36.4 | 79.9 |
300 | 0.19 | 0.43 | 0.62 | 34.9 | 78.7 | |
400 | 0.21 | 0.43 | 0.64 | 36.0 | 81.8 | |
500 | 0.28 | 0.60 | 0.87 | 49.4 | 83.0 | |
600 | 0.20 | 0.46 | 0.66 | 37.3 | 75.9 | |
Pd(Acac)2/δ-Al2O3 | 150 | 0.16 | 0.36 | 0.51 | 29.0 | 77.4 |
300 | 0.19 | 0.45 | 0.63 | 35.9 | 68.4 | |
400 | 0.19 | 0.46 | 0.66 | 37.1 | 80.3 | |
500 | 0.23 | 0.58 | 0.81 | 45.8 | 74.9 | |
600 | 0.22 | 0.50 | 0.72 | 40.7 | 76.4 |
Т – температура восстановления, °С; WМА – скорость превращенного метилацетилена, ммоль/(г ч); WПД – скорость превращенного пропадиена, ммоль/(г ч); WМАПД – суммарная скорость превращенного метилацетилена и пропадиена, ммоль/(г ч); КМАПД – конверсия метилацетилена и пропадиена, %; SПП – селективность по пропилену, %.
Таблица 7.
Результаты хемосорбционного титрования монооксидом углерода и каталитических испытаний катализаторов, синтезированных нанесением ацетатного и ацетилацетонатного прекурсоров на δ-Al2O3
Образец | Т, °С | C (Pds), ммоль/г |
D, % | d, нм | КМАПД, % | SПП, % | WМАПД, ммоль/(г ч) | TOFМАПД, ч–1 |
---|---|---|---|---|---|---|---|---|
Pd(Ac)2/δ-Al2O3 | 150 | 9.8 | 35.4 | 3.2 | 36.4 | 79.9 | 0.64 | 65.4 |
300 | 10.7 | 38.2 | 2.9 | 34.9 | 78.7 | 0.62 | 57.5 | |
400 | 11.6 | 41.3 | 2.7 | 36.0 | 81.8 | 0.64 | 54.8 | |
500 | 8.5 | 29.3 | 3.8 | 49.4 | 83 | 0.87 | 102.9 | |
600 | 7.1 | 25.4 | 4.4 | 37.3 | 75.9 | 0.66 | 92.2 | |
Pd(Acac)2/δ-Al2O3 | 150 | 13.4 | 46.7 | 2.4 | 29.0 | 77.4 | 0.51 | 38.2 |
300 | 15.6 | 54.7 | 2.0 | 35.9 | 78.4 | 0.63 | 40.5 | |
400 | 16.1 | 57.7 | 1.9 | 37.1 | 80.3 | 0.66 | 40.8 | |
500 | 14.3 | 50.5 | 2.2 | 45.8 | 74.9 | 0.81 | 56.6 | |
600 | 10.7 | 38.0 | 2.9 | 40.7 | 76.4 | 0.72 | 67.1 |
Т – температура восстановления, °С; C (Pds) – концентрация поверхностных атомов палладия, ммоль/г; D – дисперсность активного компонента, %; d – средний диаметр нанесенных частиц палладия, нм; WМАПД – суммарная скорость превращенного метилацетилена и пропадиена, ммоль/(г ч); КМАПД – конверсия метилацетилена и пропадиена, %; SПП – селективность по пропилену, %; TOF – число оборотов катализатора, ч–1.
Анализ значений TOF (табл. 7) также свидетельствует о зависимости адсорбционных свойств нанесенных частиц палладия от их электронного состояния. Так, для катализаторов, синтезированных с использованием ацетата и ацетилацетоната палладия, восстановленных в диапазоне 150–400°С, величины TOF имеют значения 54.8–65.4 ч–1 и 38.2–40.8 ч–1, соответственно; для катализаторов, восстановленных при 500–600°С, эти значения больше – 92.2–102.9 ч–1 и 56.6–67.1 ч–1, соответственно. Более низкие значения TOF для катализаторов, восстановленных при более низких температурах, обусловлены более прочной хемосорбцией ацетиленового и диенового УВ на электронно-дефицитных частицах палладия. Их формирование возможно в результате неполного восстановления солей палладия и наличия координационно-ненасыщенных поверхностных атомов активного компонента.
ЗАКЛЮЧЕНИЕ
Для выбора оптимальной температуры восстановительной обработки Pd/δ-Al2O3-катализаторов проведено исследование трансформации различных прекурсоров палладия, нанесенных на поверхность алюмооксидного носителя.
Показано, что ацетилацетонат палладия характеризуется более сильным взаимодействием с функциональными группами поверхности оксида алюминия, по сравнению с ацетатным комплексом.
Установлено, что катализаторы, синтезированные с использованием ацетилацетонатного прекурсора, характеризуются меньшим диаметром частиц палладия во всем диапазоне температур восстановительной обработки, по сравнению с образцами на основе ацетата палладия. При этом независимо от типа прекурсора палладия наименьший размер частиц активного компонента с максимальной концентрацией поверхностных атомов палладия формируется при температуре 400°С.
Катализаторы, изотермически обработанные при 150–400°С, характеризуются низкой конверсией метилацетилена и пропадиена, что обусловлено неполным восстановлением палладия из его солей с формированием окисленных и координационно-ненасыщенных форм активного компонента. Оптимальная температура восстановления катализаторов 500°С, при которой отмечается максимальная конверсия метилацетилена и пропадиена с высокой селективностью превращения в пропилен.
Работа выполнена за счет средств субсидии, выделенной в рамках государственной поддержки Казанского (Приволжского) федерального университета в целях повышения его конкурентоспособности среди ведущих мировых научно-образовательных центров.
Список литературы
Zea H., Lester K., Datye A.K., Rightor E., Gulotty R., Waterman W. // Appl. Catal. A. 2005. V. 282. P. 237.
Borodzinski A., Bond G.C. // Catal. Rev.: Sci. Eng. 2008. V. 50. P. 379.
Panpranot J., Kontapakdee K., Praserthdam P. // Appl. Catal. A. 2006. V. 314. P. 128.
Voort P.V.D., Mitchell M.B., Vansant E.F., White M.G. // Interface Science. 1997. V. 5. P. 169.
Dossi C.,Psaro R., Fusi A., Recchia S., Dal Santo V., Sordelli L. // Thermochim. Acta. 1998. V. 317. P. 157.
Daniell W., Landes H., Fouad N. E., Knozinger H. // J. of Mol. Catalysis A: Chemical. 2002. V. 178. P. 211.
Kinnunen N.M., Suvanto M., Moreno M.A., Savimaki A., Kallinen K., Kinnunen T.-J.J., Pakkanen T.A. // Appl. Catal. A: General. 2009. V. 370. P. 78.
Toebes M., Van Dillen J., De Jong K. // J/ of Mol. Catalysis A: Chemical. 2001. V. 173. P. 75.
Praserthdam P., Ngamsom B., Bogdanchikova N., Phatanasri S., Pramotthana M. // Appl. Catal. A: General. 2002. V. 230. P. 41.
Shim W., Lee J., Kim S. // Applied Catalysis B: Environmental. 2008. V. 84. P. 133.
Liu J., Wang H., Chen Y., Yang M., Wu Y. // Catal. Commun. 2014. V. 46. P. 11.
Gurrath M., Kuretzky T., Boehm H.P., Okhlopkova L.B., Lisitsyn A.S., Likholobov V.A. // Carbon. 2000. V. 38. P. 1241.
Столяров И.П., Демина Л.И., Черкашина Н.В. // Журн. неорг. химии. 2011. Т. 56. № 10. С. 1611.
Kunstle G., Siegl H. / Patent USA. № IF3960909. 1976.
Ламберов А.А., Халилов И.Ф., Ильясов И.Р., Бикмурзин А.Ш., Шатилов В.М., Назмиева И.Ф. // Журн. Приклад. химии. 2011. № 8. С. 1320.
Дополнительные материалы отсутствуют.