Нефтехимия, 2019, T. 59, № 2, стр. 143-151
Математическое моделирование нестационарного процесса пиролиза углеводородов
Ф. А. Самедов 1, А. Ю. Морозов 1, Н. А. Самойлов 1, *, Т. Р. Просочкина 1, **
1 Уфимский государственный нефтяной технический университет
Башкортостан, Уфа, Роcсия
* E-mail: naum.samoilow@yandex.ru
** E-mail: agidel@ufanet.ru
Поступила в редакцию 07.04.2017
После доработки 15.10.2018
Принята к публикации 13.02.2018
Аннотация
Выполнено математическое моделирование кинетики пиролиза углеводородов (УВ) с использованием в качестве сырья пропан-бутановой фракции. Проведено сопоставление расчетных данных и результатов обследования работы промышленных печей пиролиза при существенном спорадическом изменении состава сырья. Выполнена адаптация математической модели к работе реальной печи пиролиза. Доказана адекватность адаптированной математической модели и ее приемлемость для оперативного управления процессом пиролиза. Получены регрессионные уравнения для последующего использования в системах автоматического регулирования процесса.
Процесс пиролиза относится к крупнотоннажным процессам формирования сырьевых ресурсов большого числа нефтехимических производств. Совершенствование процесса идет в двух основных направлениях – модернизация технологии (совершенствование горелочных устройств [1–3], инициирование процесса пиролиза [4–7], использование катализаторов [8–11] и ряд других технологических приемов) и поиск оптимальных режимов процесса на базе его математического моделирования с использованием как детерминированных [11–16 ], так и стохастических [11, 17, 18] моделей. Наибольший интерес представляет моделирование процесса пиролиза по детерминированным математическим моделям, которые позволяют всесторонне проанализировать процесс и сформировать стратегию оптимизации процесса.
Для формирования адекватного представления о моделируемом процессе желательно использовать достаточно полную математическую модель. Объем модели определяется формированием теоретических маршрутов химических реакций, охватывающих процесс пиролиза УВ. Объем кинетической модели у различных авторов исследования процесса пиролиза существенно разнится. Так, например, в [19] механизм пиролиза описывается 303 реакциями с участием 177 компонентов после агрегирования близких с позиции физико-химических свойств компонентов в модели кинетики пиролиза. При решении оптимизационных задач пиролиза различного вида сырья объем решаемой задачи сокращался. В частности, при пиролизе бензина в [19] после отсечения (дискриминации) незначимых реакций рассматривалось уже 177 реакций с 53 компонентами (включая псевдокомпоненты). При решении оптимизационных задач пиролиза ШФЛУ изучалось уже 118 реакций с 41 компонентoм, при решении задач пиролиза бутановой фракции – 84 реакции с 41 компонентoм, при решении задач пиролиза смеси этан-пропан – 36 реакций с 13 компонентами [19]. Можно назвать три существенные проблемы, возникающие при обработке подобных математических моделей значительного объема. Во-первых, усложняется определение численных значений физико-химических параметров модели, резко возрастает объем вычислений и перерабатываемой информации. Во-вторых, большое число компонентов реакционной смеси затрудняет анализ результатов расчета в силу проявления дополнительных (и, как правило, в модели не учитываемых) эффектов взаимодействия. В-третьих, усложняется сопоставление расчетных и опытных (особенно промышленных) данных, поскольку экспериментально фиксируются далеко не все теоретически возможные компоненты реакционной смеси. В связи с громоздкостью задачи пиролиза в последние годы разработан ряд новых подходов к решению этой задачи [20–23], однако во многих случаях авторы ограничиваются только изложением формируемых схем решения [21, 22].
Общей особенностью задач, решаемых при моделировании процесса пиролиза, является постоянство состава исходного сырья. Однако в реальных условиях, особенно при поставках сырья пиролиза одновременно с нескольких предприятий, наблюдаются сильные колебания состава сырья. Так, например, в ходе обследования печей пиролиза, работающих на пропан-бутановой смеси УВ, компаундируемой из поставок газа от трех нефтеперерабатывающих предприятий содержание пропана в сырье лежало в пределах от 14 до 71 мас. %, а бутана – от 24 до 86 мас. %; при этом пропан-бутановая смесь могла содержать в качестве примеси от 0 до 10 мас. % пентана. Колебания состава носят спорадический характер, непредсказуемы и меняются по величине практически непрерывно. При отборе сырья пиролиза на анализ в течение ноября 2016 г. через каждые восемь часов из 84 отобранных проб только 3 смежные восьмичасовые пробы имели равные попарно составы. На рис. 1 показано характерное изменение состава сырья пиролиза за первые пять суток ноября 2016 г. Для возможности оперативного управления процессом пиролиза в промышленных пиролизных печах необходимо реализовать математическое моделирование процесса на достаточно простых и быстро обрабатываемых моделях.
Рис. 1.
Характерное изменение состава сырья пиролиза в течение пяти суток: 1 – пропан, 2 – н-бутан, 3 – н-пентан.
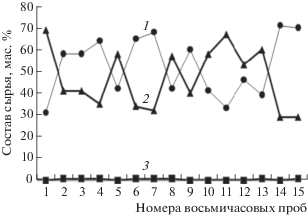
Сопоставление данных промышленных пробегов пиролизной печи и результатов ее моделирования осложняется ограниченностью данных о работе печи по показаниям приборов: известны только количество и состав сырья, температура и давление реакционной смеси на выходе из зоны реакции и состав реакционной смеси по этилену и пропилену после ее закаливания, то есть после удаления из реакционной смеси смол и коксовых частиц.
В связи с этим в данной работе были рассмотрены некоторые аспекты моделирования кинетики пиролиза пропан-бутановой смеси в широком диапазоне ее состава.
РАСЧЕТНАЯ ЧАСТЬ
Анализ процесса пиролиза УВ выполняли на базе модели кинетики пиролиза, предложенной Жоровым Ю.М., Васильевой Н.И. и Панченковым Г.М. [12], в основе которой лежит несколько упрощенная схема процесса, позволяющая, тем не менее, рассчитать концентрации основных компонентов реакционной смеси в широком диапазоне температур процесса.
Модель кинетики пиролиза включает следующие 7 реакций с учетом 11 компонентов реакционной смеси, учитывающих как состав сырья, так и состав продуктов реакций:
(1)
${{{\text{С }}}_{{\text{2}}}}{{{\text{Н }}}_{{\text{6}}}}({{N}_{{\mathbf{1}}}})\quad \to {\text{0}}{\text{.47}}{{{\text{С }}}_{2}}{{{\text{Н }}}_{{\text{4}}}}({{N}_{{\mathbf{2}}}}) + 0.53{\text{С }}{{{\text{Н }}}_{4}}({{N}_{{\mathbf{3}}}}),$(2)
$\begin{gathered} {{{\text{С }}}_{{\text{3}}}}{{{\text{Н }}}_{{\text{8}}}}({{N}_{{\mathbf{4}}}}) \to 0.32{{{\text{С }}}_{{\text{2}}}}{{{\text{Н }}}_{{\text{4}}}}({{N}_{2}}) + 0.34{{{\text{С }}}_{{\text{2}}}}{{{\text{Н }}}_{{\text{6}}}}({{N}_{{\mathbf{1}}}}) + \\ + \,\,0.16{{{\text{С }}}_{{\text{3}}}}{{{\text{Н }}}_{{\text{6}}}}({{N}_{{\mathbf{5}}}}) + 0.18{\text{С }}{{{\text{Н }}}_{{\text{4}}}}({{N}_{{\mathbf{3}}}}), \\ \end{gathered} $(3)
$\begin{gathered} {{{\text{С }}}_{{\text{4}}}}{{{\text{Н }}}_{{{\text{10}}}}}({{N}_{{\mathbf{6}}}}) \to 0.10{{{\text{С }}}_{{\text{4}}}}{{{\text{Н }}}_{{\text{6}}}}{\text{(}}{{N}_{{\mathbf{7}}}}) + 0.32{{{\text{С }}}_{{\text{2}}}}{{{\text{Н }}}_{{\text{4}}}}({{N}_{{\mathbf{2}}}}) + \\ + \,\,0.27{{{\text{С }}}_{{\text{3}}}}{{{\text{Н }}}_{{\text{6}}}}({{N}_{{\mathbf{5}}}}) + 0.15{{{\text{С }}}_{{\text{2}}}}{{{\text{Н }}}_{{\text{6}}}}({{N}_{{\mathbf{1}}}}) + 0.16{\text{С }}{{{\text{Н }}}_{{\text{4}}}}({{N}_{3}}), \\ \end{gathered} $(4)
$\begin{gathered} {{{\text{С }}}_{{\text{5}}}}{{{\text{Н }}}_{{{\text{12}}}}}({{N}_{{\mathbf{8}}}}) \to 0.16{{{\text{С }}}_{{\text{3}}}}{{{\text{Н }}}_{{\text{6}}}}({{N}_{{\mathbf{5}}}}) + 0.37{{{\text{С }}}_{{\text{2}}}}{{{\text{Н }}}_{{\text{6}}}}{\text{(}}{{N}_{{\mathbf{1}}}}) + \\ + \,\,0.35{{{\text{С }}}_{{\text{2}}}}{{{\text{Н }}}_{{\text{4}}}}({{N}_{{\mathbf{2}}}}) + 0.12{\text{С }}{{{\text{Н }}}_{{\text{4}}}}({{N}_{{\mathbf{3}}}}), \\ \end{gathered} $(5)
${{{\text{С }}}_{{\text{2}}}}{{{\text{Н }}}_{{\text{4}}}}({{N}_{{\mathbf{2}}}}) \to 0.15{{{\text{C}}}_{{\text{2}}}}{{{\text{Н }}}_{{\text{2}}}}({{N}_{{\mathbf{9}}}}) + 0.85{{{\text{Н }}}_{{\text{2}}}}({{N}_{{{\mathbf{10}}}}}),$(6)
${{{\text{С }}}_{{\text{2}}}}{{{\text{Н }}}_{{\text{4}}}}({{N}_{{\mathbf{2}}}}) \to {\text{п о л и м е р ы }}\,\,({{N}_{{{\mathbf{11}}}}}),$(7)
${{{\text{С }}}_{{\text{3}}}}{{{\text{Н }}}_{{\text{6}}}}({{N}_{{\mathbf{5}}}}) \to {\text{п о л и м е р ы }}\,\,({{N}_{{{\mathbf{11}}}}}),$Математическая модель кинетики пиролиза представляет собой систему из 18 уравнений, состоящую из 7 алгебраических экспоненциальных уравнений для расчета констант скорости реакций и 11 простых дифференциальных уравнений, учитывающих изменение концентраций каждого из компонентов реакционной смеси в ходе пиролиза:
(15)
$\begin{gathered} {{d{{N}_{1}}} \mathord{\left/ {\vphantom {{d{{N}_{1}}} {d\tau }}} \right. \kern-0em} {d\tau }} = --{{K}_{1}}{{N}_{1}} + 0.34{{K}_{2}}{{N}_{4}} + \\ + \,\,0.15{{K}_{3}}{{N}_{6}} + 0.37{{K}_{4}}{{N}_{{8\quad\quad}}}, \\ \end{gathered} $(16)
$\begin{gathered} {{d{{N}_{2}}} \mathord{\left/ {\vphantom {{d{{N}_{2}}} {d\tau }}} \right. \kern-0em} {d\tau }} = 0.47{{K}_{1}}{{N}_{1}} + {{0.32}^{.}}{{K}_{2}}{{N}_{4}} + 0.32{{K}_{3}}{{N}_{6}} + \\ + \,\,{{0.35}^{.}}{{K}_{4}}{{N}_{8}}--{{K}_{5}}{{N}_{2}}--{{K}_{6}}{{N}_{2}}, \\ \end{gathered} $(17)
$\begin{gathered} {{d{{N}_{3}}} \mathord{\left/ {\vphantom {{d{{N}_{3}}} {d\tau }}} \right. \kern-0em} {d\tau }} = 0.53{{K}_{1}}{{N}_{1}} + 0.18{{K}_{2}}{{N}_{4}} + 0.16{{K}_{3}}{{N}_{6}} + \\ + \,\,0.12{{K}_{4}}{{N}_{8}}, \\ \end{gathered} $(18)
${{d{{N}_{4}}} \mathord{\left/ {\vphantom {{d{{N}_{4}}} {d\tau }}} \right. \kern-0em} {d\tau }} = --{{K}_{2}}{{N}_{4}},$(19)
$\begin{gathered} {{d{{N}_{5}}} \mathord{\left/ {\vphantom {{d{{N}_{5}}} {d\tau }}} \right. \kern-0em} {d\tau }} = 0.16{{K}_{2}}{{N}_{4}} + 0.27{{K}_{3}}{{N}_{6}} + \\ + \,\,0.16{{K}_{4}}{{N}_{8}}--{{K}_{7}}{{N}_{5}}, \\ \end{gathered} $(20)
${{d{{N}_{6}}} \mathord{\left/ {\vphantom {{d{{N}_{6}}} {d\tau }}} \right. \kern-0em} {d\tau }} = --{{K}_{3}}{{N}_{6}},$(21)
${{d{{N}_{7}}} \mathord{\left/ {\vphantom {{d{{N}_{7}}} {d\tau }}} \right. \kern-0em} {d\tau }} = 0.1{{K}_{3}}{{N}_{6}},$(22)
${{d{{N}_{8}}} \mathord{\left/ {\vphantom {{d{{N}_{8}}} {d\tau }}} \right. \kern-0em} {d\tau }} = --{{K}_{4}}{{N}_{8}},$(23)
${{d{{N}_{9}}} \mathord{\left/ {\vphantom {{d{{N}_{9}}} {d\tau }}} \right. \kern-0em} {d\tau }} = 0.15{{K}_{5}}{{N}_{2}},$(24)
${{d{{N}_{{10}}}} \mathord{\left/ {\vphantom {{d{{N}_{{10}}}} {d\tau }}} \right. \kern-0em} {d\tau }} = 0.85{{K}_{5}}{{N}_{2}},$(25)
${{d{{N}_{{11}}}} \mathord{\left/ {\vphantom {{d{{N}_{{11}}}} {d\tau }}} \right. \kern-0em} {d\tau }} = {{K}_{6}}{{N}_{2}} + {{K}_{7}}{{N}_{5}},$К0j – предэкспоненциальный множитель, с–1;
Р0 – давление пиролиза, ата;
Еj – энергия активации j-ой реакции, Дж/моль;
Т – температура пиролиза, К;
R – универсальная газовая постоянная (R = = 8.31 Дж/моль К);
τ – время реакции, с;
Ni – концентрация i-го компонента в момент времени τ, кг/м3.
Стехиометрические коэффициенты в уравнениях (1)–(7) и (15)–(25), а также численные значения энергий активации и предэкспоненциальных множителей в уравнениях (8)–(14) взяты из [12]. Система смешанных дифференциальных и алгебраических уравнений (8)–(25) решалась методом Рунге–Кутта первого порядка.
Поскольку основной задачей данной работы была оценка возможности оперативного использования математической модели пиролиза для регулирования работы печи пиролиза в условиях спорадически изменяющегося состава сырья, то для ускорения расчетов был принят изотермический характер процесса. В основе этого допущения легли ранее выполненные расчеты адиабатического процесса пиролиза н-пентана [24]. Тепловые эффекты протекающих при пиролизе реакций имеют разный знак: реакции расщепления исходного сырья (реакции (1)–(4)) эндотермичны и требуют затрат тепла, в то время как побочные реакции полимеризации и расщепления этилена на ацетилен и водород (реакции (5)–(7)) протекают с выделением тепла. Этим объясняется экстремальный характер зависимости температуры реакционной среды и суммарного теплового эффекта процесса пиролиза от времени. Вначале, когда в ходе процесса преобладают целевые реакции, протекающие с большой скоростью, температура из-за положительного (эндотермичного) суммарного теплового эффекта реакций уменьшается на 100–120°С. По прошествии некоторого времени, например, 0.5 с при начальной температуре пиролиза 840°С, побочные реакции приобретают достаточную скорость, начинается существенное выделение тепла и температура начинает повышаться. Как показано в табл. 1, конечные показатели пиролиза при изотермическом и адиабатическом режимах близки. Если учесть дополнительный теплоподвод к реакционной смеси в зону пиролиза за счет сжигания топлива в печи порядка 140 000 кДж/(м2 ч), то при снижении температуры адиабатического процесса на 100°С средний тепловой эндотермический эффект реакций деструкции составляет около 5 кДж/моль и расходе сырья 120 кмоль/ч теплосъем на деструкцию составит 600 000 кДж/ч, то есть при поверхности реакционной трубы около 5 м2 теплосъем на деструкцию вполне компенсируется теплоподводом. Таким образом, принятое допущение об изотермичности процесса пиролиза при его моделировании достаточно корректно.
Таблица 1.
Сопоставление параметров процесса пиролиза в адиабатическом и изотермическом режимах при одинаковой начальной температуре пиролиза н-пентана 840°С
Параметры | Адиабатический режим | Изотермический режим |
---|---|---|
Максимальный выход этилена, мас. % | 39.5 | 39.5 |
Время максимального выхода этилена, с | 1.5 | 0.4 |
Максимальная селективность процесса по этилену, % | 39.7 | 39.4 |
Максимальный выход пропилена, мас. % | 14.4 | 15.1 |
Время максимального выхода пропилена, с | 1.1 | 0.2 |
Максимальная селективность процесса по пропилену, % | 16 | 15.5 |
Выход смол пиролиза, мас. %, к моменту времени от начала процесса | ||
0.2 с | 0.3 | 1.5 |
0.4 с | 1.5 | 7.5 |
1.0 с | 4.0 | 19.0 |
С целью сопоставления опытных данных (состав продуктов реакции после закаливания – резкого охлаждения реакционной смеси до 130°С) и расчетных данных (состав реакционной смеси на выходе из печи) расчетные концентрации целевых непредельных компонентов этилена и пропилена пересчитывались на основании допущения о том, что при закаливании из реакционной смеси (пирогаза) в подсмольную воду уходят смолы пиролиза. В качестве примера в табл. 2 приведены результаты расчета кинетики пиролиза по математической модели и соответствующие опытные данные пробега печи П-2 установки пиролиза при переработке смеси пропан–н-бутан (концентрация н-бутана равна 59 мас. % при температуре 1103 К (830°С) и давлении 1.5 ата в течение 1.4 с. Как следует из данных этой таблицы, в которой приведена часть расчетных данных, при принятой форме обработки расчетных материалов расчетное содержание этилена и пропилена достаточно близко к экспериментальным данным. Необходимо отметить, что при пиролизе смеси пропан–н-бутан сырьевые компоненты практически полностью подвергаются превращению за 1.2–1.4 с, а оптимальное время максимального выхода целевых продуктов составляет 0.8–1.0 с. В реакционной смеси на выходе из печи кроме этилена и пропилена находится значительное количество ценного компонента бутадиена (до 6 мас. %), а также образуется более 47 мас. % побочных продуктов, в том числе около 32 мас. % газовых компонентов (метан, этан и водород) и до 15 мас. % смолистых веществ. Необходимо отметить, что при аналитическом определении состава пирогаза обнаружено незначительное содержание пропадиена (0.09 мас. %), который не учитывается математической моделью, но не зафиксирован ацетилен (0.4 мас. %). По-видимому, пирогазе ацетилен не был обнаружен в из-за растворения его в подсмольной воде при закаливании пирогаза.
Таблица 2.
Кинетика пиролиза и сопоставление расчетных и экспериментальных данных пиролиза смеси пропан–н-бутан
Параметры | Состав продуктов пиролиза, мас. % | |||||||||||
---|---|---|---|---|---|---|---|---|---|---|---|---|
этан | этилен | метан | пропан | пропилен | бутан | бутадиен | С5+ | ацетилен | водород | смолы | этилен + + пропилен |
|
Расчетные составы реакционной смеси до отделения продуктов полимеризации при времени пиролиза τ | ||||||||||||
τ = 0.2 с | 9.646 | 17.182 | 10.175 | 17.924 | 11.117 | 29.874 | 2.913 | 0 | 0.020 | 0.115 | 1.034 | 28.299 |
τ = 0.4 с | 10.705 | 25.606 | 16.780 | 7.836 | 15.759 | 15.126 | 4.387 | 0 | 0.067 | 0.381 | 3.363 | 41.355 |
τ = 0.6 с | 9.004 | 29.312 | 21.085 | 3.426 | 17.304 | 7.659 | 5.134 | 0 | 0.126 | 0.717 | 6.259 | 46.616 |
τ = 0.8 с | 6.799 | 30.449 | 23.827 | 1.498 | 17.415 | 3.878 | 5.512 | 0 | 0.191 | 1.080 | 9.352 | 47.864 |
τ = 1.0 с | 4.857 | 30.184 | 25.618 | 0.655 | 16.866 | 1.963 | 5.704 | 0 | 0.256 | 1.449 | 12.449 | 47.05 |
τ = 1.2 с | 3.360 | 29.166 | 26.776 | 0.286 | 16.035 | 0.994 | 5.801 | 0 | 0.319 | 1.809 | 15.453 | 45.21 |
Расчетные составы реакционной смеси после отделения продуктов полимеризации при времени пиролиза τ | ||||||||||||
τ = 0.2 с | 9.747 | 18.460 | 10.203 | 18.111 | 10.206 | 30.185 | 2.943 | 0 | 0.022 | 0.124 | 0 | 16.817 |
τ = 0.4 с | 11.077 | 28.253 | 17.141 | 8.108 | 14.736 | 15.652 | 4.540 | 0 | 0.074 | 0.419 | 0 | 42.989 |
τ = 0.6 с | 9.605 | 33.403 | 22.097 | 3.654 | 16.635 | 8.170 | 5.477 | 0 | 0.144 | 0.815 | 0 | 50.038 |
τ = 0.8 с | 7.500 | 35.924 | 25.794 | 1.652 | 17.274 | 4.278 | 6.081 | 0 | 0.244 | 1.271 | 0 | 53.198 |
τ = 1.0 с | 5.549 | 36.899 | 28.669 | 0.748 | 17.297 | 2.243 | 6.516 | 0 | 0.312 | 1.767 | 0 | 54.196 |
τ = 1.2 с | 3.976 | 36.941 | 31.000 | 0.339 | 17.016 | 1.176 | 6.863 | 0 | 0.403 | 2.286 | 0 | 53.967 |
Экспериментальный состав пирогаза промышленной печи после его закаливания: | ||||||||||||
τ – ориентировочно 1.1 с | 6.26 | 37.68 | 24.20 | 7.07 | 16.32 | 1.44 | 3.47 | 2.21 | 0.09* | 1.26 | 0 | 54.00 |
РЕЗУЛЬТАТЫ И ИХ ОБСУЖДЕНИЕ
Так как гидродинамическая обстановка в трубчатом змеевике печи пиролиза корректно описывается моделью идеального вытеснения, то время выхода максимальных концентраций этилена и пропилена теоретически должно быть различным при существенном изменении расхода сырья, поскольку при одинаковом времени пребывания реакционной смеси в змеевике концентрации целевых компонентов на выходе из змеевика в принципе могут существенно отличаться от оптимальных (рис. 2, белая точка). При низких расходах сырья по сравнению с базовым время пребывания реакционной смеси в змеевике увеличится и позиция экстремума выхода, например, этилена сместится влево и часть этилена начнет расходоваться в побочных реакциях, а при высоких расходах сырья время пребывания реакционной смеси в змеевике увеличится уменьшится, позиция экстремума выхода этилена сместится вправо и концентрация этилена не сможет достичь экстремального значения (рис. 2, черные точки).
Рис. 2.
Теоретическое влияние расхода исходного сырья на концентрацию этилена на выходе из змеевика печи пиролиза при одинаковом времени пребывания реакционной смеси в змеевике τП: 1 – базовый расход сырья, 2 – расход сырья меньше базового, 3 – расход сырья больше базового.
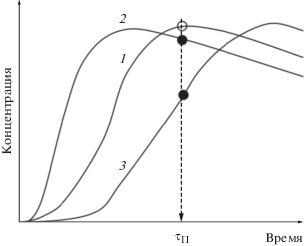
Расчетный анализ кинетики пиролиза пропан-н-бутановой смеси показал, что процесс пиролиза является весьма устойчивым к колебаниям расходов исходного сырья в широких пределах 5–7 т/ч и состава исходного сырья в пределах 21–84 мас. % по н-бутану.
Обеспечение максимальных выходов этилена и пропилена из зоны реакции печи пиролиза (за вычетом смол) достигается регулировкой температуры реакционной среды на выходе из печи в пределах всего 1–5°С от 825 до 830°С при соответствующем изменении констант скоростей реакций (табл. 3) и почти сорокапроцентном изменении расхода сырья (рис. 3). Как следует из рис. 3, оптимальное время пиролиза в рассмотренном диапазоне температур составляет около 1.2 с для обеспечения максимального выхода этилена и около 0.9 с для пропилена. Увеличение расхода сырья при одновременном увеличении температуры пиролиза приводит к увеличению времени максимального выхода этилена и пропилена на 0.1–0.2 с. При этом суммарный расчетный выход целевых непредельных углеводородов при расходе сырья 5–7 т/ч обеспечивался на уровне 53.5–53.7 мас. % при времени пиролиза 0.9–1.2 с, а практическое их содержание в пирогазе составило соответственно 54.2 и 53.05 мас. %, то есть относительная погрешность расчета не превышала 1.3 отн. %.
Таблица 3.
Влияние рабочего диапазона температур на константы скоростей реакций
Параметры | Значения констант скоростей реакции, с−1 | ||||||
---|---|---|---|---|---|---|---|
К1 | К2 | К3 | К4 | К5 | К6 | К7 | |
Температура 825°С | 2.04 | 3.72 | 3.16 | 18.99 | 0.066 | 0.29 | 0.33 |
Температура 830°С | 2.17 | 4.13 | 3.4 | 20.81 | 0.07 | 0.31 | 0.35 |
Увеличение значений констант при увеличении температуры на 5°С, % | 6.37 | 11.02 | 7.59 | 9.58 | 6.06 | 6.89 | 6.06 |
Рис. 3.
Влияние температуры процесса пиролиза на кинетику образования этилена (кривые 1, 2) и пропилена (кривые 3, 4): 1, 3 – температура пирогаза на выходе из печи 825°С, расход сырья 5 т/ч, 2, 4 – температура пирогаза на выходе из печи 830°С, расход сырья 7 т.
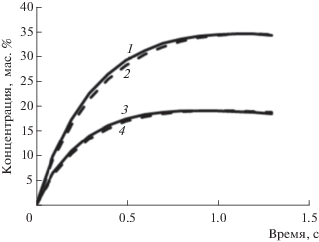
В табл. 4 приведена выборка сравнения результатов расчетов кинетики пиролиза (время пиролиза 1 с) с учетом “закаливания” и опытных данных при одинаковой производительности печи по сырью (6 т/ч) и температуре пиролиза 828°С при существенном колебании состава исходного сырья.
Таблица 4.
Влияние состава исходного сырья на состав пирогаза
Содержание н-бутана в сырье, мас. % | Опытное содержание непредельных углеводородов в пирогазе, мас. % |
Расчетное содержание непредельных углеводородов в пирогазе, мас. % |
||||
---|---|---|---|---|---|---|
С2Н4 | С3Н6 | С2Н4 + С3Н6 | С2Н4 | С3Н6 | С2Н4 + С3Н6 | |
27 | 36.38 | 16.55 | 52.93 | 36.457 | 16.244 | 52.701 |
29 | 36.30 | 16.59 | 52.89 | 36.328 | 16.433 | 52.761 |
30 | 36.94 | 16.81 | 53.75 | 36.264 | 16.527 | 52.721 |
34 | 37.86 | 16.66 | 54.52 | 36.006 | 16.904 | 53.000 |
37 | 37.20 | 16.99 | 54.19 | 35.813 | 17.188 | 53.001 |
39 | 34.69 | 17.57 | 52.28 | 35.684 | 17.376 | 53.060 |
50 | 37.27 | 16.70 | 53.97 | 34.973 | 18.416 | 53.389 |
53 | 37.50 | 16.96 | 54.46 | 34.779 | 18.700 | 53.479 |
53 | 36.71 | 16.58 | 53.29 | 34.779 | 18.700 | 53.479 |
57 | 36.53 | 15.51 | 52.04 | 34.544 | 19.079 | 53.623 |
65 | 37.69 | 16.88 | 54.57 | 34.003 | 19.838 | 53.841 |
66 | 37.28 | 16.77 | 54.05 | 33.938 | 19.932 | 53.870 |
Анализ данных табл. 4 показал, что данные экспериментального пробега печи пиролиза имеют погрешность на уровне 0.4–0.7 мас. % для параллельных опытов (выделены в табл. 3 полужирным шрифтом) и достаточно близки результатам расчетов. Обработка всего массива экспериментальных и расчетных данных по 84 опытным точкам показала, что рассмотренная математическая модель вполне адекватна и приемлема для описания процесса пиролиза в заводской печи: расчетные критерии Фишера составили F = 6.15 для расчета выхода этилена, F = 6.19 для расчета выхода пропилена и F = 1.82 для расчета совокупности выхода этилена и пропилена при табличном значении F = 13.60 при уровне вероятности ошибочности гипотезы об адекватности 0.01 [25].
При более жестком подходе к оценке адекватности с принятием уровня вероятности ошибочности гипотезы об адекватности уже 0.05 табличное значение критерия Фишера F равно 5.67, что свидетельствует об адекватности расчетов суммы непредельных УВ при значительной ошибке результатов расчетов отдельно по этилену и пропилену. Как математическая модель, так и результаты экспериментов показали, что по мере увеличения содержания н-бутана в сырье при пиролизе несколько возрастает суммарный выход целевых непредельных углеводородов. Однако при этом расчеты характеризуются снижением выхода этилена при возрастании выхода пропилена (табл. 4), что не соответствует термодинамическим предпосылкам: содержание пропилена в пирогазе должно уменьшаться, поскольку молекула н-бутана преимущественно расщепляется на две молекулы этилена, тогда как опытные пробеги показали практическое постоянство содержания пропилена в пирогазе при увеличении выхода этилена по мере утяжеления сырья. Некоторое несоответствие расчетных и опытных данных можно объяснить тем, что исходная математическая модель рассматривает пиролиз газового бензина, содержащего как некоторое количество легкого компонента этана, так и более тяжелых компонентов – пентановой фракции С5+. Для обеспечения возможности оперативного управления процессом пиролиза пропан-н-бутановой фракции на базе математической модели пиролиза была предпринята попытка коррекции математической модели пиролиза с целью повышения уровня ее адекватности с позиций закономерного увеличения выхода этилена при возрастании содержания н-бутана в сырье. Коррекция заключалась в уточнении значений стехиометрических коэффициентов в уравнениях (1)–(3), обеспечивающих минимизацию невязок экспериментальных и расчетных выходов этилена; уравнения (1), (2) и (3) после коррекции имеют вид:
Коррекция модели позволила обеспечить существенное снижение отклонения результатов расчетов от опытных данных (табл. 5) при качественном совпадении тенденций изменения выходов непредельных углеводородов при варьировании состава исходного сырья.
Таблица 5.
Сводная характеристика результатов моделирования процесса пиролиза по исходной и откорректированной математической модели
Показатели | Значения показателей | |||
---|---|---|---|---|
средние | минимальные | максимальные | линия тренда при росте содержания н-бутана в сырье | |
Исходная модель | ||||
Температура, °С | 1102 | 1098 | 1106 | ![]() |
Концентрация этилена, мас. % | 35.068 | 32.839 | 36.996 | |
Концентрация пропилена, мас. % | 18.370 | 15.565 | 21.644 | |
Концентрация этилена и пропилена, мас. % | 53.437 | 52.651 | 54.484 | |
Откорректированная модель | ![]() |
|||
Температура, °С | 1102 | 1098 | 1106 | |
Концентрация этилена, мас. % | 36.970 | 36.858 | 37.085 | |
Концентрация пропилена, мас. % | 17.008 | 16.471 | 17.636 | |
Концентрация этилена и пропилена, мас. % | 53.978 | 53.393 | 54.721 | |
Экспериментальные данные | ![]() |
|||
Температура, °С | 1102 | 1098 | 1106 | |
Концентрация этилена, мас. % | 36.812 | 34.180 | 38.670 | |
Концентрация пропилена, мас. % | 16.642 | 15.510 | 17.720 | |
Концентрация этилена и пропилена, мас. % | 53.454 | 50.760 | 55.760 |
Откорректированная математическая модель вполне адекватно характеризует образование непредельных УВ (рис. 4) и полностью приемлема для описания процесса пиролиза в заводской печи: расчетные критерии Фишера составили F = = 4.14 для расчета выхода этилена, F = 2.62 для расчета выхода пропилена и F = 2.37 для расчета совокупности выхода этилена и пропилена при табличном значении F = 5.67 при уровне вероятности ошибочности гипотезы об адекватности 0.05.
Рис. 4.
Зависимость содержания непредельных углеводородов в пирогазе от содержания н-бутана в сырье: 1 – этилен; 2 – пропилен; 3 – сумма этилена и пропилена; точки – опытный пробег печи пиролиза, линии – расчет по скорректированной математической модели.
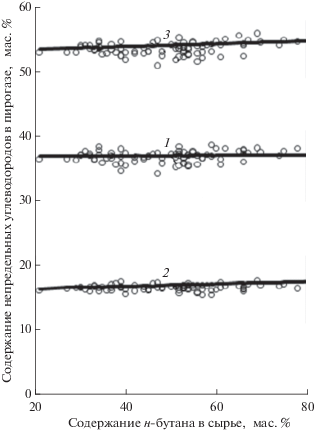
Обработка массива полученных расчетных данных позволила разработать уравнения регрессии, удобные для использования в системах регулирования процесса пиролиза и позволяющие рассчитать ожидаемый выход этилена YЭ (мас. %), пропилена YП (мас. %) и суммы непредельных УВ YНУ (мас. %) на выходе из печи в зависимости от содержания н-бутана XБ (мас. %) в исходном сырье:
с коэффициентами корреляции 0.88, 0.97 и 0.97 соответственно.На основе откорректированной математической модели пиролиза проанализировано влияние изменения фракционного состава сырья на результаты процесса пиролиза. В частности, последовательное утяжеление состава исходного сырья за счет ввода в него фракции С5+ в количестве 20–80 мас. % (концентрации пропана и н-бутана принимались равными) показало, что при этом концентрация этилена в пирогазе несколько возрастает (с 37 до 42 мас. %), пропилена – убывает (с 17.5 до 14.4 мас. %), но суммарное содержание этилена и пропилена увеличивается с 54.5 до 56.4 мас. % (рис. 5а). Последовательное облегчение состава исходного сырья за счет ввода в него этана в количестве 20–80 мас. % (концентрации пропана, н-бутана и фракции С5+ принимались равными) показало, что при этом концентрация этилена в пирогазе несколько уменьшается (с 38 до 36 мас. %), пропилена – существенно убывает (с 14.7 до 5.4 мас. %), также уменьшается с 52.7 до 41.5 мас. % (концентрации пропана, н-бутана и фракции С5+ принимались равными) показало, что при этом концентрация этилена в пирогазе несколько уменьшается (с 38 до 36 мас. %), пропилена – существенно убывает (с 14.7 до 5.4 мас. %), также уменьшается с 52.7 до 41.5 мас. % суммарное содержание этилена и пропилена (рис. 5а), что подтверждается результатами обследования печей пиролиза, работающих на различных видах сырья.
ВЫВОДЫ
Проектирование оптимального реакционного змеевика печи пиролиза УВ требует учета пяти математических моделей: кинетической, гидродинамической, энергетической, тепловой, импульса, одновременное решение которых усложняется тем, что начальные условия интегрирования разных моделей с распределенными параметрами в дифференциальной форме лежат на противоположных концах реакционного змеевика. Поскольку формирование условий трансверсальности в данной ситуации затруднительно, то целесообразно поэтапное решение задачи [26]. В связи с этим рассмотренную откорректированную модель пиролиза можно рассматривать как первый этап оптимизации.
На втором этапе оптимизации на основе оптимальной продолжительности реакции, обеспечивающей максимальный выход целевых продуктов, определяется необходимый ориентировочный объем реакционной части змеевика при заданной производительности печи по сырью. Это позволяет далее последовательно рассчитывать: диаметр и число параллельно работающих реакционных труб змеевика, необходимый оптимальный теплоподвод к реакционной среде в единичной реакционной трубе для компенсации тепловых эффектов, распределение тепловых нагрузок по горелкам печи при допущении линейного изменения температуры дымовых газов от максимальной температуры горения до температуры на перевале. На третьем этапе выполняется оптимизация математической модели с позиций выбранного критерия оптимальности, позволяющая сформировать оптимальное распределение тепловых нагрузок между горелками печи пиролиза для обеспечения оптимального режима протекания реакций в реакционной части радиантного змеевика печи. Подобная оптимизированная математическая модель может быть использована не только на стадии проектирования печи, но и служить основой системы автоматизированного управления процессом пиролиза в промышленной печи.
Список литературы
Катин В.Д., Колмогоров А.Н. // Нефтепереработка и нефтехимия. 1994. № 6. С. 31.
Катин В.Д. // Нефтепереработка и нефтехимия. 1994. № 4. С. 41.
Малиновский А. С., Черных С. П., Мухина Т. Н. // Химическая промышленность. 1991. № 7. С. 396.
Антипов Ю.В., Корулькин М.Ю., Макаров В.В. // Нефтепереработка и нефтехимия. 1996. № 3. С. 33.
Антипов Ю.В., Корулькин M.Ю., Макаров В.В. // Нефтепереработка и нефтехимия. 1997. № 2. С. 23.
Бабаш С.Е., Стрекаловский Б.А., Тюкавин Г.Н. // Химическая промышленность. 1993. № 5. С. 165.
Глебов Л.С., Глебова Е.В. // Нефтехимия. 2015. Т. 55. № 3. С. 250 [Petrol. Chemistry. 2015. V. 55. № 3. P. 238].
Черных С.П., Адельсон С.В., Мухина Т.Н. // Химическая промышленность. 1993. № 5. С. 161.
Барабанов НЛ. // Нефтепереработка и нефтехимия. 1995. № 4. С. 26.
Урманцев У.Р., Хлесткин Р.Н., Самойлов Н.А., Терентьев В.С. // Химическая промышленность. 2000. № 8. С. 36.
Шекунова В.М.. Цыганова Е.И., Диденкулова Ю.А. // Вестник Нижегородского университета им. Н.И. Лобачевского. 2014. № 1(1). С. 92.
Жоров Ю.М. Моделирование физико-химических процессов нефтепереработки и нефтехимии. М.: Химия, 1978. 376 с.
Кравцов А.В., Сваровская Н. А., Тризна А.Г. // Химическая промышленность. 1995. № 2. С. 112.
Кравцов А.В., Сваровская Н.А., Зеленко И.Ю. // Химическая промышленность. 1999. № 7. С. 30.
Жоров Ю.М., Волохова Г.С., Васильева И.И., Копинке Ф.-Д. // Нефтехимия. 1984. Т. 24. № 1. С. 38 .
Чащин А.И. Автореф. дис. ... канд. техн. наук. Томск. Томский политехнический институт, 1986. 16 с.
Доломатов М.Ю., Амирова С.И. // Нефтепереработка и нефтехимия. 1991. № 8. С. 49.
Амирова С.И., Доломатов М.Ю. // Нефтепереработка и нефтехимия. 1994. № 2. С. 32.
Зеленко И.Ю. Автореф. дис. ... канд. техн. наук. Томск, ТПИ. 1999. 23 с.
Левуш С.С., Федевич О.Е., Кит Ю.В. // Катализ и нефтехимия. 2005. № 13. С.58.
Фафурин А.В., Чигвинцев И.Р. // Вестник Казанского технологического университета. Т. 16. № 14. 2013. С. 37.
Губайдуллин И.М., Пескова Е.Е., Стадниченко О.А. В сб. Информационные технологии и нанотехнологии-2016. Самара, 2016. С. 630.
Битюгов В.К., Тихомиров С.Г., Арапов Д.В., Саввин С.С. // Вестник Воронежского государственного ун-та инженерных технологий. 2015. № 3. С. 79. Doi: 10.20914/2310-1202-2015-3-79-84
Самойлов Н.А., Галиуллин Д.Р. // Химическая промышленность сегодня. 2003. № 6. С. 25.
Самойлов Н.А. Моделирование в химической технологии и расчет реакторов. Уфа: Монография, 2005. 216 с.
Самойлов Н.А. Материалы Всероссийской конференции “Химия и химическая технология: достижения и перспективы”, Кемерово, 2016. http:// conf42.ru/XiXT_2016/pages/Articles/ximia_i_ximicheskaya_ tehnologiya_organicheskix_veshestv_i_nefteximii/ Samoylov.pdf.
Дополнительные материалы отсутствуют.