Нефтехимия, 2019, T. 59, № 3, стр. 325-332
Совместные превращения н-гексадекана, гексена-1 и циклогексана на бицеолитных катализаторах крекинга
О. В. Потапенко 1, *, К. С. Плехова 1, Д. Б Гилязутдинов 1, О. В. Кроль 1, Т. П. Сорокина 1, В. П. Доронин 1
1 Институт проблем переработки углеводородов СО РАН
Омск, Россия
* E-mail: potap@ihcp.ru
Поступила в редакцию 12.10.2018
После доработки 01.11.2018
Принята к публикации 10.12.2018
Аннотация
Рассмотрены особенности превращения н-гексадекана, гексена-1, циклогексана и их смесей на бицеолитных катализаторах совместного крекинга легких и тяжелых фракций. Максимальный выход олефинов достигается при использовании в качестве сырья гексена-1 (выход С2–С4-олефинов достигает 66.8 мас. %), обладающего максимальной реакционной способностью в условиях крекинга. Совместные превращения н-гексадекана и гексена-1 не указывают на наличие значимого взаимодействия между компонентами. Присутствие в сырье циклогексана оказывает существенное воздействие на превращение н-гексадекана, что обусловлено высокой донорно-водородной способностью нафтенов. Установлено, что соотношение цеолитов HРЗЭY и P/HZSM-5 в композиции катализатора оказывает существенное влияние на величину взаимодействия между компонентами сырья. Использование углеводородов, содержащие “меченые” атомы водорода (дейтерия), позволило оценить распределение водорода нафтена между основными газообразными продуктами.
ВВЕДЕНИЕ
В структуре современного нефтеперерабатывающего завода особое место занимает процесс каталитического крекинга. Данный процесс обеспечивает высокую глубину переработки нефти и является основным источником непредельных углеводородов (УВ) – этилена, пропилена и бутиленов, изобутана и высокооктанового компонента товарного бензина [1, 2]. Соотношение продуктов крекинга может изменяться в очень широких пределах. В случае преобладания легких продуктов (главным образом олефинов) говорят о нефтехимической направленности процесса, в случае преобладания бензиновой фракции – о топливной. Классический вариант каталитического крекинга подразумевает использование в качестве сырья тяжелых нефтяных фракций: вакуумных дистиллятов, мазута, различных нефтяных остатков [1–5]. Нефтехимический вари-ант процесса допускает возможность использования в качестве сырья легких углеводородных фракций – керосино-газойлевых [6], бензиновых [7] и даже бутан-бутиленовой фракций [8]. Как правило, использование легкого сырья и необходимость увеличения глубины крекинга предполагает осуществление процесса в жестком режиме – высоких температурах и соотношениях катализатор : сырье, существенно превышающих соответствующие показатели для классического варианта крекинга по топливному варианту (см. табл. 1). Условия процесса обуславливают необходимость применения отдельного реактора крекинга [9] или автономной установки, предназначенной для переработки только легкого сырья.
Особое внимание к процессу каталитического крекинга нефтехимической направленности уделено в работе С.Н. Хаджиева [10]. Автором описан целый ряд таких технологий: CPP (RIPP + + Kellog) [11], MIP-GCP (RIPP) [12], PetroFCC (UOP) [13], HPFCC (Grace Davison) [14] и другие. Перечисленные процессы проводятся при повышенной температуре, c увеличенной кратностью циркуляции катализатора и использованием катализатора на основе модифицированного цеолита ZSM-5. Выход пропилена может достигать 20% и более. В процессе MAXOFIN (KBR) [15] используется рециркуляция бензина в отдельный лифт-реактор, что позволяет гибко изменять выходы продуктов крекинга.
В ряде случаев возникает необходимость совместной переработки легких и тяжелых нефтяных фракций в процессе каталитического крекинга. Существенные отличия в реакционной способности, молекулярной массе компонентов и групповом составе создают ряд сложностей для совместного крекинга в одном реакторе: нарушение гидродинамики, снижение времени контакта, конкурентная сорбция. С одной стороны, присутствие в сырье легких олефинов, обладающих высокой реакционной способностью в условиях кислотного катализа, приводит к их прочной сорбции на активных центрах катализатора и препятствует крекингу крупных молекул сырья [16]. С другой стороны, присутствие в легких фракциях парафинов и нафтенов, содержащих 5–8 атомов углерода, обладающих низкой реакционной способностью, обуславливает необходимость использования более активных катализаторов, что для крекинга вакуумных дистиллятов необоснованно. В работах [16, 17] описывается возможность совместной переработки бензиновых фракций и вакуумных дистиллятов в условиях каталитического крекинга в одном реакторе. Для решения вышеописанных проблем совместной переработки предлагается использование специализированных катализаторов и разделение зон крекинга легкой и тяжелой фракций либо в отдельных реакторах [4, 17, 18], либо по высоте одного реактора [4, 16]. В последнем случае бензин с низкой реакционной способностью вводится в низ лифт-реактора, где контактирует со свежим катализатором при повышенной температуре; а тяжелое сырье вводится на некоторой средней точке реактора, где вступает в контакт с частично закоксованным катализатором при обычной температуре крекинга.
Основные активные компоненты катализаторов топливной и нефтехимической направленности – цеолиты типов Y и ZSM-5. Смещение в сторону тех или иных продуктов крекинга достигается изменением соотношения цеолитов указанных типов. Для повышения стабильности цеолитов в условиях регенерации они (цеолиты) подвергаются различным обработкам: введению катионов редкоземельных элементов [19–21], модифицированием соединениями фосфора [22–24], снижению содержания оксида натрия, ультрастабилизации, увеличению мезопористости [21, 25] и другие.
Цель настоящей работы – анализ основных направлений превращения модельных соединений в процессе совместного каталитического крекинга н-гексадекана и легких УВ, обладающих различной реакционной способностью (гексена-1 и циклогексана, в т.ч. циклогексана-d12), на бицеолитных катализаторах крекинга.
ЭКСПЕРИМЕНТАЛЬНАЯ ЧАСТЬ
Приготовление катализаторов. Исследуемые в работе катализаторы относятся к катализаторам композиционного типа. Каталитическая система включает в себя активный (цеолитный) компонент и матрицу. Последняя состоит из аморфного алюмосиликата, оксида алюминия и бентонитовой глины (монтмориллонит), взятых в равных долях. Цеолитный компонент варьировали с использованием цеолитов HРЗЭY и P/HZSM-5. Фосфорсодержащий цеолит P/HZSM-5 (содержание фосфора 4%) получали путем пропитки цеолита HZSM-5 (Zeolist International, Si/Al = 80) раствором (NH4)2HPO4 с последующей сушкой и прокаливанием при 650°С.
Компоненты катализатора гомогенизировали а затем формовали частицы с размером от 50 до 250 мкм. Далее катализатор сушили при 100°С и прокаливали при 650°С. Готовые катализаторы подвергали термопаровой обработке при 788°С в течение 5 ч в среде 100%-ного водяного пара в соответствии с ASTM D 4463. Всего было приготовлено 3 образца, отличающихся содержанием цеолитов Y и ZSM-5 (в мас. % в готовом катализаторе): 1) 10/30; 2) 20/20 и 3) 30/10.
Исследование катализаторов. Пористую структуру образцов исследовали методом низкотемпературной адсорбции азота на приборе ASAP-2020 (“Micromeritics”, США). Удельную площадь поверхности (SБЭТ) определяли методом БЭТ. Общий объем пор адсорбции (Vадс) измеряли методом адсорбции азота при P/P0 = 0.99. Перед выполнением исследования образцы предварительно прокаливали при 650°С.
Суммарное количество кислотных центров цеолитов определяли методом температурно-программируемой десорбции аммиака (ТПД-NH3) на высокоточном хемосорбционном анализаторе A-utoChem-2920 (“Micromeritics”) с использованием смеси 6 об. % NH3 в гелии. Перед экспериментами образцы нагревали до 650°С в потоке 10 об. % О2 в гелии, выдерживали при этой температуре в течение 1 ч и затем охлаждали в потоке гелия до 100°С. Адсорбцию аммиака проводили при той же температуре в течение 60 мин с последующей продувкой гелием при 100°С в течение 1 ч для удаления физически адсорбированного аммиака. ТПД аммиака проводили в интервале температур 100–600°С, скорость нагрева измерительной ячейки с образцом составляла 10°С/мин.
Химический состав компонентов и катализаторов определяли, разлагая образцы в минеральных кислотах (серная, хлорная, фтористоводородная) с последующим анализом раствора методами атомно-адсорбционной спектрометрии на приборе Shimadzu AA-6300 (Япония) и атомно-эмиссионной спектрометрии с индуктивно-связанной плазмой (AES-ICP) на приборе Varian 710-ES (США).
Каталитические испытания. В качестве компонентов сырья были использованы циклогексан (“Sigma-Aldrich”), гексена-1 (“Sigma-Aldrich”) и н-гексадекан (“Sigma-Aldrich”) без дополнительной очистки. Исследованы превращения смесей н-гексадекана и легкого УВ с массовыми соотношениями 100 : 0, 95 : 5, 90 : 10, 85 : 15 и 80 : 20. При этом н-гексадекан рассматривается как модельное сырье, отражающее тяжелое сырье крекинга, циклогексан – легкое сырье с низкой реакционной способностью, гексен-1 – легкое сырье с высокой реакционной способностью. Выбор “легких” модельных соединений обусловлен типичным составом промышленных бензиновых фракций – прямогонной фракции 62–85°С и бензина замедленного коксования. Дополнительно исследованы превращения смесей модельных УВ, содержащих 0.1% (1000 ppm) дейтерия из дейтерированной формы циклогексана (циклогексан-d12, ABCR GmbH & Co KG).
Исследование каталитических свойств образцов проводили на лабораторной установке с неподвижным слоем катализатора. Катализатор загружали в реактор в количестве 3 г. Реактор помещали в электропечь, обеспечивающую изотермический нагрев слоя катализатора до 590°С. Газообразные продукты анализировали на газовом хроматографе ГХ-1000, снабженном капиллярной колонкой (SiO2, 30 м × 0.32 мм) и пламенно-ионизационным детектором. Компонентный состав бензинов определяли на хромато-масс-спектрометре Shimadzu GCMS-QP2010, оборудованном колонкой HP-1ms (60 м × 0.25 мм × 0.25 мкм) и дополнительным пламенно-ионизационным детектором.
Содержание изотопов водорода (соотношение H/D) в продуктах крекинга определяли на изотопном хромато-масс-спектрометре DELTA V Advantage (Thermo Fisher Scientific). На первом этапе газообразные продукты крекинга разделяли на хроматографической колонке. Далее продукты попадали в высокотемпературный (1420 °С) пиролитический реактор (GCТC-MS), где происходило разложение УВ на углерод и водород. Полученный водород (H2 и HD) поступал в масс-спектрометр, где происходило разделение и регистрация ионов с m/z равным 2 (${\text{H}}_{2}^{ + }$) и 3 (HD+). Подробное описание методики представлено в работе [26].
Содержание кокса на катализаторе измеряли по потере массы при прокаливании образца катализатора на воздухе при 650°C.
Для оценки количественного вклада реакций межмолекулярного переноса водорода использовали коэффициент переноса водорода (HTC, Hydrogen Transfer Coefficient), отражающий отношение селективностей образования бутанов к бутиленам [27]. Значение коэффициентов переноса водорода рассчитывали по формуле:
где HTC – коэффициент переноса водорода; Sбутаны, Sбутилены – селективность образования бутанов и бутиленов, соответственно.РЕЗУЛЬТАТЫ И ИХ ОБСУЖДЕНИЕ
Свойства катализаторов. Физико-химические характеристики используемых компонентов приведены в табл. 2.
Таблица 2.
Физико-химические характеристики компонентов катализаторов
Компонент катализатора | Содержание, мас. % | Sуд, м2/г | Vпор, см3/г | Vмикро, см3/г | Кислотность по ТПД аммиака, мкмоль/г | |
---|---|---|---|---|---|---|
Na2O | РЗЭ2О3 | |||||
Цеолит HРЗЭY | 0.65 | 4.27 | 661 | 0.371 | 0.229 | 1398 |
Цеолит P/HZSM-5 | 0.06 | – | 284 | 0.170 | 0.094 | 255 |
Аморфный алюмосиликат | 0.17 | – | 454 | 0.400 | – | 397 |
Оксид алюминия | 0.05 | – | 275 | 0.530 | – | 386 |
Бентонитовая глина | 0.07 | – | 78 | 0.070 | 0.014 | 72 |
Максимальной кислотностью обладает цеолит HРЗЭY. Несмотря на относительно низкое содержание редкоземельных элементов, кислотность цеолита по данным температурно-программируемой десорбции аммиака достигает 1398 мкмоль/г. Модифицированный фосфором цеолит типа HZSM-5 характеризуется значительно меньшей кислотностью – 255 мкмоль/г. Кислотность компонентов матрицы убывает в следующем порядке “аморфный алюмосиликат” ≈ “оксид алюминия” > > “бентонитовая глина”. Большой объем микропор цеолита типа Y свидетельствует о высокой кристалличности цеолита. Все компоненты катализаторов отличаются низким содержанием натрия и его влияние на термостабильные и каталитические свойства катализаторов будет незначительным.
Превращение индивидуальных соединений. Материальный баланс крекинга индивидуальных соединений представлен в табл. 3.
Таблица 3.
Превращение индивидуальных модельных соединений (неподвижный слой катализатора, 590°С, WHSV = 2.5 ч–1)
Соотношение Y/ZSM-5 в катализаторе | 30/10 | 20/20 | 10/30 |
---|---|---|---|
н-Гексадекан | |||
C1–C4 -н-парафины, мас. % | 22.60 | 23.10 | 21.70 |
С2–С4-олефины, мас. % | 49.40 | 51.60 | 56.70 |
Изобутан, мас. % | 9.30 | 7.80 | 5.70 |
Жидкие продукты, мас. % | 15.50 | 15.10 | 14.50 |
Кокс, мас. % | 3.20 | 2.40 | 1.40 |
HTC | 1.11 | 1.00 | 0.90 |
Соотношение С2 : С3 : С4-олефинов | 0.4 : 1 : 0.6 | 0.5 : 1 : 0.6 | 0.6 : 1 : 0.5 |
Гексен-1 | |||
C1–C4-н-парафины, мас. % | 14.80 | 13.00 | 12.80 |
С2–С4-олефины, мас. % | 61.00 | 66.80 | 63.40 |
Изобутан, мас. % | 5.40 | 4.90 | 4.80 |
Жидкие продукты, мас. % | 14.80 | 12.80 | 17.30 |
Кокс, мас. % | 4.00 | 2.50 | 1.70 |
HTC | 0.45 | 0.40 | 0.42 |
Соотношение С2 : С3 : С4-олефинов | 0.3 : 1 : 0.5 | 0.4 : 1 : 0.5 | 0.6 : 1 : 0.6 |
Циклогексан | |||
C1–C4-н-парафины, мас. % | 11.10 | 11.50 | 17.80 |
С2–С4 олефины, мас. % | 21.60 | 27.80 | 37.20 |
Изобутан, мас. % | 4.40 | 3.80 | 3.70 |
Жидкие продукты, мас. % | 60.90 | 54.50 | 38.70 |
Кокс, мас. % | 2.00 | 2.50 | 2.50 |
HTC | 1.63 | 0.88 | 0.64 |
Соотношение С2 : С3 : С4-олефинов | 0.3 : 1 : 0.3 | 0.4 : 1 : 0.4 | 0.6 : 1 : 0.6 |
Максимальной реакционной способностью в условиях каталитического крекинга (высокая температура, катализатор кислотного типа) обладает гексен-1. Основными продуктами его превращения являются более низкомолекулярные олефины – этилен, пропилен и бутилены. Суммарный выход легких олефинов превышает 65 мас. %. Изменение состава цеолитного компонента не оказывает существенного влияния на суммарный выход олефинов, но значительно изменяет соотношение “этилен : пропилен : бутилены”. Увеличение доли цеолита ZSM-5 приводит к увеличению селективности образования более низкомолекулярных соединений – этилена и пропилена. Превращение гексена-1 на исследуемых катализаторах характеризуется минимальным значением коэффициента переноса водорода, что свидетельствует о преимущественном протекании реакций крекинга относительно реакций переноса водорода. Снижение соотношения цеолитов Y/ZSM-5 в каталитической системе способствует снижению данной характеристики (HTC) и уменьшению выхода кокса.
Превращение н-гексадекана также протекает с преимущественным образованием легких олефинов, выход которых достигает 56,7 мас. %. В отличии от превращения гексена-1 каталитический крекинг н-С16H34 приводит к образованию большого количества насыщенных УВ С1–С4. При этом увеличение в каталитической системе доли широкопористого цеолита типа Y приводит к увеличению выхода насыщенных соединений. Так, выход изобутана при переходе от системы “10/30” к “30/10” увеличивается в 1.63 раза.
Циклогексан является наиболее устойчивой молекулой в исследуемых условиях. Применение катализатора с высоким содержание цеолита типа Y не обеспечивает требуемого превращения циклогексана. В случае использования катализатора “30/10” наблюдается минимальный выход олефинов С2–С4, который не превышает 22 мас. %. Увеличение доли узкопористого цеолита ZSM-5 способствует резкому увеличению выхода олефинов (с 21.6 до 37.2 мас. %) и снижению вклада реакций переноса водорода. В случае превращения циклогексана наблюдается максимальное значение коэффициента переноса водорода (1.63), что связано с высокой [H]-донорной способностью нафтеновых УВ [28].
Превращение смесей н-гексадекан + гексен-1. Превращение смесей “парафин–олефин” – модельная реакция исследования совместного крекинга смесей вакуумного газойля и бензиновых фракций с высоким содержанием непредельных соединений. Материальный баланс крекинга смесей представлен в табл. 4. На рис. 1 представлена зависимость выхода легких олефинов (экспериментального и рассчитанного по аддитивности из превращения чистых углеводородов) от состава исходного сырья.
Таблица 4.
Превращение смесей н-гексадекан + гексен-1 (неподвижный слой катализатора, 590°С, WHSV = 2.5 ч–1)
Соотношение Y/ZSM-5 в катализаторе | 30/10 | 20/20 | 10/30 |
---|---|---|---|
Сырье: 95% гексадекана : 5% гексена-1 | |||
C1–C4-н-парафины, мас. % | 20.40 | 17.30 | 18.70 |
С2–С4-олефины, мас. % | 48.40 | 53.00 | 58.70 |
Изобутан, мас. % | 10.10 | 9.40 | 6.30 |
Жидкие продукты, мас. % | 17.70 | 17.10 | 15.20 |
Кокс, мас. % | 3.40 | 3.30 | 1.00 |
HTC | 1.10 | 0.98 | 0.76 |
Соотношение С2 : С3 : С4-олефинов | 0.4 : 1 : 0.6 | 0.4 : 1 : 0.5 | 0.6 : 1 : 0.6 |
Сырье: 90% гексадекана : 10% гексена-1 | |||
C1–C4-н-парафины, мас. % | 20.30 | 19.50 | 20.50 |
С2–С4-олефины, мас. % | 47.90 | 52.40 | 55.40 |
Изобутан, мас. % | 9.60 | 8.50 | 6.20 |
Жидкие продукты, мас. % | 18.90 | 17.00 | 16.49 |
Кокс, мас. % | 3.30 | 2.70 | 1.50 |
HTC | 1.04 | 0.98 | 0.82 |
Соотношение С2 : С3 : С4-олефинов | 0.4 : 1 : 0.6 | 0.5 : 1 : 0.5 | 0.6 : 1 : 0.6 |
Сырье: 85% гексадекана : 15% гексена-1 | |||
C1–C4-н-парафины, мас. % | 19.40 | 19.10 | 20.20 |
С2–С4-олефины, мас. % | 51.90 | 56.00 | 55.70 |
Изобутан, мас. % | 8.40 | 7.90 | 6.40 |
Жидкие продукты, мас. % | 17.10 | 15.10 | 15.80 |
Кокс, мас. % | 3.20 | 1.90 | 1.90 |
HTC | 0.88 | 0.88 | 0.82 |
Соотношение С2 : С3 : С4-олефинов | 0.4 : 1 : 0.6 | 0.5 : 1 : 0.5 | 0.6 : 1 : 0.6 |
Сырье: 80% гексадекана : 20% гексена-1 | |||
C1–C4-н-парафины, мас. % | 18.50 | 18.40 | 17.30 |
С2-С4-олефины, мас. % | 51.70 | 54.80 | 59.60 |
Изобутан, мас. % | 8.90 | 7.60 | 5.60 |
Жидкие продукты, мас. % | 17.30 | 17.00 | 15.60 |
Кокс, мас. % | 3.70 | 2.20 | 1.80 |
HTC | 0.86 | 0.83 | 0.69 |
Соотношение С2 : С3 : С4-олефинов | 0.3 : 1 : 0.6 | 0.4 : 1 : 0.5 | 0.5 : 1 : 0.5 |
Рис. 1.
Зависимость выхода суммы С2–С4-олефинов от содержания н-гексадекана в смеси “н-гексадекан + гексен-1” на катализаторах: 1 – 10/30, 2 – 20/20, 3 – 30/10, пунктирная линия – значения по аддитивности, сплошная – по экспериментальным данным.
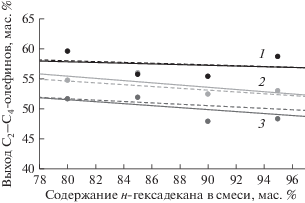
Превращение молекул н-гексадекана и гексена-1 при содержании последнего в смеси менее 20 мас. % протекает независимо друг от друга. При этом выход легких олефинов при каталитическом крекинге смеси может рассматриваться как сумма выходов, полученных при превращении индивидуальных компонентов, пропорционально их содержанию. Влияние состава цеолитного компонента катализатора на соотношение реакций крекинга и переноса водорода также полностью повторяет соответствующие закономерности при превращении чистых гексена-1 и н-гексадекана.
Превращение смесей н-гексадекан + циклогексан. Превращение смесей “парафин–нафтен” – модельная реакция исследования совместного крекинга смесей вакуумного газойля и бензиновых фракций с высоким содержанием нафтенов. Материальный баланс крекинга смесей представлен в табл. 5. На рис. 2 представлена зависимость выхода легких олефинов (экспериментального и рассчитанного по аддитивности из превращения чистых углеводородов) от состава исходного сырья.
Таблица 5.
Превращение смесей н-гексадекан + циклогексан (неподвижный слой катализатора, 590°С, WHSV = = 2.5 ч–1)
Соотношение Y/ZSM-5 | 30/10 | 20/20 | 10/30 |
---|---|---|---|
Сырье: 95% гексадекана : 5% циклогексанa | |||
C1–C4-н-парафины, мас. % | 21.10 | 19.40 | 21.40 |
С2–С4-олефины, мас. % | 47.10 | 51.50 | 52.90 |
Изобутан, мас. % | 10.80 | 9.50 | 6.80 |
Жидкие продукты, мас. % | 18.20 | 17.30 | 17.60 |
Кокс, мас. % | 2.90 | 2.40 | 1.30 |
HTC | 1.18 | 1.09 | 0.84 |
Соотношение С2 : С3 : С4-олефинов | 0.4 : 1 : 0.6 | 0.4 : 1 : 0.5 | 0.7 : 1 : 0.7 |
Сырье: 90% гексадекана : 10% циклогексанa | |||
C1–C4-н-парафины, мас. % | 25.80 | 18.90 | 20.50 |
С2–С4-олефины, мас. % | 41.80 | 50.50 | 52.70 |
Изобутан, мас. % | 9.40 | 9.30 | 6.20 |
Жидкие продукты, мас. % | 19.10 | 18.90 | 19.30 |
Кокс, мас. % | 3.90 | 2.40 | 1.40 |
HTC | 1.40 | 1.07 | 0.86 |
Соотношение С2 : С3 : С4-олефинов | 0.5 : 1 : 0.6 | 0.4 : 1 : 0.5 | 0.6 : 1 : 0.6 |
Сырье: 85% гексадекана : 15% циклогексанa | |||
C1–C4-н-парафины, мас. % | 23.80 | 18.50 | 21.70 |
С2–С4-олефины, мас. % | 41.90 | 42.60 | 50.10 |
Изобутан, мас. % | 9.40 | 11.30 | 7.00 |
Жидкие продукты, мас. % | 20.80 | 23.70 | 20.10 |
Кокс, мас. % | 4.10 | 3.90 | 1.10 |
HTC | 1.31 | 1.30 | 0.92 |
Соотношение С2 : С3 : С4-олефинов | 0.6 : 1 : 0.6 | 0.3 : 1 : 0.6 | 0.6 : 1 : 0.6 |
Сырье: 80% гексадекана : 20% циклогексанa | |||
C1–C4-н-парафины, мас. % | 19.60 | 19.80 | 19.70 |
С2–С4-олефины, мас. % | 41.40 | 45.50 | 52.20 |
Изобутан, мас. % | 10.50 | 9.70 | 6.50 |
Жидкие продукты, мас. % | 25.20 | 22.20 | 20.30 |
Кокс, мас. % | 3.40 | 2.80 | 1.20 |
HTC | 1.36 | 1.22 | 0.81 |
Соотношение С2 : С3 : С4-олефинов | 0.4 : 1 : 0.6 | 0.4 : 1 : 0.5 | 0.6 : 1 : 0.6 |
Рис. 2.
Зависимость выхода суммы С2–С4-олефинов от содержания н-гексадекана в смеси “н-гексадекан + + циклогексан” на катализаторах: 1 – 10/30, 2 – 20/20, 3 – 30/10, пунктирная линия – значения по аддитивности, сплошная – по экспериментальным данным)
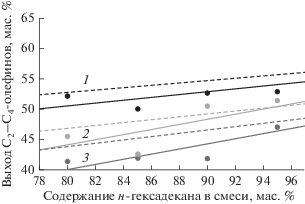
Крекинг модельных смесей “н-гексадекан–циклогексан” указывает на наличие существенного взаимодействия между компонентами, которое оказывает влияние на состав получаемых продуктов крекинга. Присутствие циклогексана, характеризуемого высокой донорно-водородной способностью, приводит к резкому увеличению вклада реакций переноса водорода и снижению селективности образования легких олефинов. При этом увеличение в составе катализатора доли широкопористого цеолита типа Y приводит к увеличению взаимодействия между компонентами при совместном превращении. Так, при превращении модельной смеси “10 мас. % циклогексана + + 90 мас. % н-гексадекана”, на катализаторе, содержащем 30 и 10 мас. % цеолитов Y и ZSM-5, соответственно, наблюдаемое значение коэффициента переноса водорода составляет 1.40.
Превращение дейтерий-содержащего сырья. Для оценки влияния взаимодействия между компонентами при превращении смеси “н-гексадекан–циклогексан” на направления превращения углеводородов на различных катализаторах были исследованы превращения дейтерий-содержащего сырья. При этом дейтерий вводился в виде циклогексана-d12, т.е. меченые атомы дейтерия содержались только в одном УВ. Распределение дейтерия между газообразными продуктами крекинга представлены в табл. 6.
Таблица 6.
Распределение дейтерия сырья в газообразных продуктах крекинга при превращении модельных смесей (1% циклогексана-d12, неподвижный слой катализатора, 590°С, WHSV = 2.5 ч–1)
Тип сырья | Циклогексан | н-Гексадекан−циклогексан | ||||
---|---|---|---|---|---|---|
Cоотношение цеолитов Y/ZSM-5 в катализаторе | 30/10 | 20/20 | 10/30 | 30/10 | 20/20 | 10/30 |
Распределение дейтерия сырья, мас. % | ||||||
Метан | 1.7 | 1.2 | 0.8 | 0.3 | 0.3 | 0.2 |
Этан | 1.1 | 1.4 | 1.3 | 0.4 | 0.5 | 0.5 |
Этилен | 4.8 | 8.3 | 13.9 | 2.2 | 4.0 | 6.4 |
Пропан | 14.0 | 14.3 | 14.8 | 2.9 | 3.6 | 4.4 |
Пропилен | 14.9 | 21.0 | 28.5 | 9.2 | 11.1 | 12.2 |
Изобутан | 7.2 | 6.1 | 4.0 | 2.8 | 2.5 | 2.2 |
н-Бутан | 2.6 | 2.6 | 2.5 | 1.1 | 1.2 | 1.3 |
Бутилены | 3.2 | 8.0 | 13.5 | 4.8 | 5.5 | 7.4 |
Сумма | 49.4 | 62.9 | 79.3 | 35.3 | 42.9 | 51.6 |
Увеличение доли узкопористого цеолита типа ZSM-5 в композиции катализатора крекинга способствует превращению циклогексана с образованием преимущественно непредельных соединений. Об этом свидетельствует увеличение доли дейтерия сырья перераспределяемое в этилен, пропилен и бутилены. Увеличение доли широкопористого цеолита типа Y приводит к росту перераспределения дейтерия в изобутан, который может рассматриваться как основной продукт реакции межмолекулярного переноса водорода, образуемый из трет-бутильного карбокатиона. Содержание дейтерия в нормальных насыщенных продуктах крекинга не зависит от состава каталитической системы. Совместные превращения циклогексана и н-гексадекана приводят к снижению суммарной доли дейтерия переносимой в газообразные продукты крекинга, что может являться следствием конкурентных превращений на кислотных центрах катализатора.
ЗАКЛЮЧЕНИЕ
В работе рассмотрены особенности превращения н-гексадекана, гексена-1, циклогексана и их смесей на бицеолитных катализаторах совместного крекинга легких и тяжелых фракций.
Максимальный выход олефинов (66.8 мас. %) достигается при использовании в качестве сырья гексена-1, обладающего максимальной реакционной способностью в условиях крекинга и низкой донорно-водородной способностью. Совместные превращения н-гексадекана и гексена-1 не указывают на наличие значимого взаимодействия между компонентами. Суммарный выход легких олефинов при превращении смеси может рассматриваться как сумма соответствующих величин, получаемых при превращении индивидуальных соединений, пропорционально их содержанию в исходном сырье.
Присутствие в сырье циклогексана оказывает существенное воздействие на превращение н-гексадекана, что обусловлено высокой донорно-водородной способностью нафтенов. Присутствие циклогексана приводит к резкому увеличению вклада реакций переноса водорода и снижению селективности образования легких олефинов. Увеличение содержания циклогексана в сырье от 5 до 20 мас. % приводит к увеличению разницы между наблюдаемыми и рассчитанными по аддитивности выходами легких олефинов.
Установлено, что соотношение цеолитов HРЗЭY и P/HZSM-5 в композиции катализатора оказывает существенное влияние на величину взаимодействия между компонентами сырья, оцениваемую по значению коэффициента переноса водорода. При этом увеличение доли широкопористого цеолита типа Y приводит к росту взаимодействия между компонентами при совместном превращении.
Использование УВ, содержащих меченные атомы водорода (дейтерия), позволило оценить распределение водорода сырья между основными газообразными продуктами крекинга. Узкопористый цеолит P/HZSM-5 в композиции катализатора крекинга способствует превращению циклогексана с образованием преимущественно этилена, пропилена и бутиленов. Широкопористый цеолит HРЗЭY способствует перераспределению дейтерия в изобутан, который может рассматриваться как основной продукт реакции межмолекулярного переноса водорода, образуемый из трет-бутильного карбокатиона.
БЛАГОДАРНОСТИ
Авторы выражают благодарность сотрудникам Лаборатории аналитических и физико-химических методов исследования ИППУ СО РАН Гуляевой Т.И., Бабенко А.В., Измайлову Р.Р., Киреевой Т.В.
Работа выполнена в рамках государственного задания ИППУ СО РАН в соответствии с Программой фундаментальных научных исследований государственных академий наук на 2013–2020 годы по направлению V. 46, проект № V.46.2.4 (номер госрегистрации в системе ЕГИСУ НИОКТР AAAA-A17-117021450095-1).
Список литературы
Sadeghbeigi R. Fluid Catalytic Cracking Handbook. New York: Elsevier, 2012. 361 p.
Khadzhiev S.N., Gerzeliev I.M., Kapustin V.M., Kadiev Kh.M., Dement’ev K.I., Pakhmanova O.A. // Petrol. Chemistry. 2011. V. 51. № 1. P. 32.
Cerqueira H.S., Caeiro G., Costa L., Ramôa Ribeiro F. // J. of Molecular Catalysis A: Chemical. 2008. V. 292. № 1–2. P. 1.
Солодова Н.Л., Терентьева Н.А. // Вестник казанского технологического университета. 2012. Т. 15. № 1. С. 141.
Крекинг нефтяных фракций на цеолитсодержащих катализаторах. Под ред. C.H. Хаджиева. М.: Химия, 1982. 280 с.
Harandi Mohsen N., Owen Hartley // Patent US 5372704A (ExxonMobil Oil Corp). 1990.
Bari Siddiqui M. A., Aitani A. M., Saeed M. R., Al-Khattaf S. // Topics in Catalysis. 2010. V. 53. № 19–20. P. 1387.
Altynkovich E.O., Potapenko O.V., Sorokina T.P., Doronin V.P., Gulyaeva T.I., Talzi V.P. // Petrol. Chemistry. 2017. V. 57. № 3. P. 215.
Chunyi Li, Chaohe Yang, Honghong Shan // Ind. Eng. Chem. Res. 2007. V. 46. P. 4914.
Khadzhiev S.N., Gerzeliev I.M., Demen’tev K.I. // Petrol. Chemistry. 2013. V. 53. № 6. P. 357.
Xieqing W., Chaogang X., Zaiting L., Genquan Z. // Practical Advances in Petrol. Processing. Springer, 2006. P. 149.
Jun L., Wei L., Zhonghong Q., Huiping T., Yuxia Z. // Studies in Surface Science and Catalysis. 2007. V. 166. P. 55.
Houdek J.M., Andersen J. // ARTC 8th Annual Meeting, Kuala Lumpur, 2005.
Park Y.K., Lee Ch.W., Kang N.Y., Choi W.C., Choi S., Oh S.H., Park D.S. // Catal. Surv. Asia. 2010. V. 14. P. 75.
Kowalski J.A. Patent US № 5888378. 1997.
A. Corma, F.V. Melo, L. Sauvanaud, F. Ortega // Catalysis Today. 2005. V.107–108. P. 699.
Palmas P., Mehlberg R. Patent US № 8137631. (UOP LLC). 2012.
Lomas D.A Patent US № 6287522. (UOP LLC). 2001.
Wang Xiaoning, ZhaoZhen, Xu Chunming, Duan Aijun, Zhang Li, Jiang Guiyuan. // J. of Rare Earths. 2007. V. 25. № 3. P. 321.
Pouria R., Vafi L, Karimzadeh R// J. of Rare Earths. 2017. V. 35. № 6. P. 542.
Доронин В.П., Сорокина Т.П., Липин П.В., Потапенко О.В., Короткова Н.В., Горденко В.И. // Катализ в промышленности. 2014. № 5. С. 9.
Blasco T, Corma A., Martínez-Triguero J.// J. of Catalysis, 2006. V. 237. № 2. P. 267.
Yajun Ji, Honghui Yanga, Qiang Zhang, Wei Yana // J. Solid State Chemistry. 2017. V. 251. P. 7.
Jian Ding, Meng Wang, Luming Peng, Nianhua Xue, Yimeng Wang, Ming-Yuan He. // Applied Catalysis A: General. 2015. V. 503. P. 147.
Yajun Ji, Honghui Yang, Wei Yan // Catalysts. 2017. V. 7. № 12. P. 367.
Hilkert A.W., Douthitt C.B., Schlüter H.J., Brand W.A. // Rapid Commun. Mass Spectrom, 1999. V. 13. P. 1226.
Francisco J. Passamonti F.J., De la Puente G., Sedran U. // Catalysis Today. 2008. V. 133–135. P. 314.
Potapenko O.V., Doronin V.P., Sorokina T.P. // Petrol. Chemistry. 2012. V. 52. № 1. P. 55.
Дополнительные материалы отсутствуют.