Нефтехимия, 2019, T. 59, № 3, стр. 333-349
Перспективы применения наноразмерных цеолитов в нефтехимии: синтез и каталитические свойства (обзор)
Л. И. Родионова 1, *, Е. Е. Князева 1, 2, С. В. Коннов 2, И. И. Иванова 1, 2
1 Московский государственный университет имени М.В. Ломоносова, Химический факультет
Москва, Россия
2 Институт нефтехимического синтеза им. А.В. Топчиева РАН
Москва, Россия
* E-mail: liudmilarodionova@gmail.com
Поступила в редакцию 01.11.2017
После доработки 15.09.2018
Принята к публикации 10.12.2018
Аннотация
Обзор посвящен особенностям получения и каталитического действия цеолитов с наноразмерными кристаллами. Приведены примеры успешного синтеза наноразмерных цеолитов структурного типа FAU, MFI, BEA, MOR и их использования в таких процессах нефтепереработки и нефтехимии, как каталитический крекинг, гидрокрекинг, гидроизомеризация, олигомеризация, трансалкилирование, конверсия метанола и ацетона в олефины и других процессах. Рассмотрены успехи и перспективы применения наноразмерных цеолитов в сларри-реакторах, представляющих собой трехфазные системы, в которых индивидуальные частицы цеолитов диспергированы в жидкой среде.
Современные тенденции стратегического развития нефтехимической отрасли, связанные с увеличением глубины переработки сырья, ростом доли новых процессов и технологий, а также увеличением селективности процессов, обуславливают новые, повышенные требования к катализаторам, в частности, к цеолитным катализаторам, играющим ключевую роль в процессах нефтехимии и нефтепереработки. В этой области основным направлениeм развития является создание каталитических систем на основе наноразмерных цеолитов и микро-мезопористых материалов [1]. Перспективы использования этих систем обусловлены следующими факторами: увеличением доступности активных кислотных центров и уменьшением диффузионных ограничений при транспорте молекул – участников реакции, которые приводят к увеличению эффективности цеолитного кристалла, а также сокращением диффузионного пути продуктов реакции, обеспечивающим высокую стабильность работы катализатора [2].
В настоящем обзоре обсуждаются основные достижения в области синтеза наноразмерных цеолитных систем и перспективы их применения в процессах нефтехимии и нефтепереработки. Рассмотрены 2 основных направления их использования: 1) в проточных каталитических системах и реакторах с движущимся слоем катализатора в составе сформованных со связующим катализаторов; 2) в сларри-реакторах в виде индивидуальных частиц цеолитных катализаторов, диспергированных в жидкой среде. В то время как первое направление является достаточно традиционным, использовать цеолитные катализаторы в сларри-реакторах начали совсем недавно. Большой вклад в развитие этого направления внес академик С.Н. Хаджиев [3–5], светлой памяти которого авторы посвящают настоящий обзор.
Успехи в области синтеза наноразмерных цеолитов
К настоящему моменту в литературе накоплено большое количество сведений по направленному синтезу наноразмерных цеолитов различных структурных типов с заданными характеристиками: размером нанокристаллов, морфологией, химическим составом и кислотными свойствами (рис. 1, табл. 1). Среди всего многообразия цеолитных структур наибольшее внимание уделялось цеолитам FAU, BEA, MFI, MOR, а также некоторым типам силикоалюмофосфатов с цеолитной структурой, которые широко используются в промышленности в процессах нефтехимии и газохимии.
Рис. 1.
Микрофотографии наноразмерных цеолитов: агрегаты цеолита FAU (Y), полученные при соотношении H2O/SiO2 23.2 (a) и 12.2 (б) [11]; агрегаты (в) и индивидуальные кристаллы (г) цеолита MFI, полученные при ингибировании поверхности молекулами фениламинопропилтриметоксисилана (ФАПТМС) [17]; нанокристаллы цеолита BEA, полученные при разном соотношении (C2H5)4NOH/Al2O3 равном 30 (д) и 10 (е) [20].
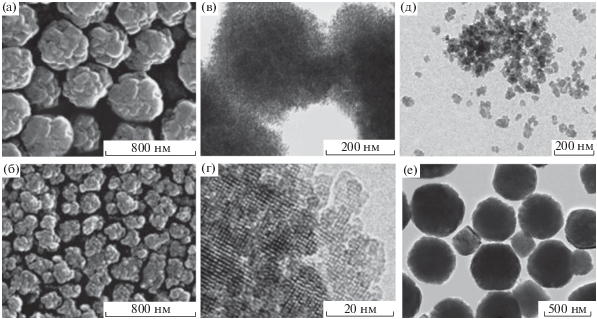
Таблица 1.
Методы синтеза наноразмерных цеолитов
Цеолит | Метод синтеза | Примечание | Исходные реагенты | Условия кристаллизации | Si/Al | Размер кристаллов, нм | Ссылки | |
---|---|---|---|---|---|---|---|---|
Т, °C | τ, ч | |||||||
FAU | Гидротермальный синтез | Коллоидные частицы | Силикагель Al(OC3H7)3, NaOH, (CH3)4NOH, H2O | 100 | 50 | 2.15 | 40–80 | 6 |
Многостадийный гидротермальный синтез с периодическим добавлением микроколичеств NaOH | Выход 43% за 10 последовательных этапов | Si(OC2H5)4, Al(OC3H7)3, NaOH, (CH3)4NOH, (CH3)4NBr, H2O | 90 послед. этапы 90 |
144 48 |
1.8 | 50–60 | 7 | |
Многостадийный гидротермальный синтез | Периодическое добавление 0.1 М раствора NaOH. Отношение Na2O/Al2O3 в начальной смеси 0.032, в конечной 0.43 | Si(OC2H5)4, Al(OC3H7)3, NaOH, (CH3)4NOH, H2O | 95 | 144 | н/у | 20–30 | 8 | |
Гидротермальный синтез 2 стадии, битемплатный синтез |
Содержание второго темплата TMABr/ТМАОН 0.50. Увеличение выхода на 180% |
Силиказоль, Al(OC3H7)3, (CH3)4NOH, (CH3)4NBr, H2O |
Комн. 100 |
72 90–216 |
2.4 | 30–40 | 9 | |
Гидротермальный синтез в отсутствиe темплата | Выход до 80% | Силиказоль, Al(OH)3, NaOH, H2O |
Комн. 100 |
24 12 |
2.1 | 400 | 10 | |
Реакционная смесь готовится при Т = 4°C | Силиказоль, пудра метал. Al, NaOH, H2O |
Комн. 120 |
24 1.1 |
2.1 | 70 | |||
Трехстадийный гидротермальный синтез, без использования темплата | Изучение влияния воды | Силиказоль, Al(OC3H7)3, NaOH, H2O |
Комн. 38 60 |
24 24 48 |
1.5–1.8 | Агрегаты (190–600) из крист. (0–45) | 11 | |
Парофазная кристаллизация | Вода на дне автоклава 9–12 г/г геля, выход 80% | Аэросил, NaAlO2, NaOH, H2O | 50 90 |
6 18 |
Si/Al = 2.25 | 200–400 | 12 | |
MFI | Синтез стабильной суспензии цеолита | Синтез из прозрачного геля | Al2(SO4)3, Si(OC2H5)4, (C3H7)4NOH, NaOH |
Комн. 98 |
12–14 60 |
98–150 | 13 | |
Гидротермальный синтез | Синтез из прозрачного геля | Силикагель, Al2(SO4)3, (C3H7)4NOH |
80 | 240 | 50 | Агрегаты (300–400) из нанокристаллов (20–30) | 14 | |
Две стадии, использование коллоидных затравок (30%) | Si(OC2H5)4, Al2(SO4)3, (C3H7)4NOH |
48 | 70 | 100 | 14 | |||
Гидротермальный синтез в инертной матрице |
Исходный гель наносится на сажу пропиткой по влагоемкости, затем подвергается гидротермальной кристаллизации | Al(OC3H7)3, (C3H7)4NOH, Si(OC2H5)4, cажа |
Комн. 180 |
3 48 |
50 и 100 | 20–40 | 15 | |
Гидротермальный синтез | Изучение влияния соотношения OH–/SiO2 | Силикагель, Al(NO3)3, (C3H7)4NBr, NaOH |
160 | 48–72 | 12.5 | 30–40 | 16 | |
Гидротермальный синтез с использованием зародышей с ингибированием поверхности | Поверхность зародышей ингибируется прививкой молекулы фениламинопропилтриметоксисилана (ФАПТМС) | Al(OC3H7)3, (C3H7)4NOH, Si(OC2H5)4 |
90 170 |
6 120 |
45 | 10–20 | 17 | |
Гидротермальный синтез с использованием кристаллических затравок | Затравка: Al(OC3H7)3 (C3H7)4NOH Si(OC2H5) 4 |
NaAlO2, NaOH, силикагель, 5% затравки |
Комн. 140 180 |
3 24 24 |
30–80 | Агрегаты
с однородными ортогональными нанокристаллами (70–100) |
18 | |
ВЕА | Гидротермальный синтез | Размер кристаллов возрастает с ростом отношения SiO2/Al2O3 в реакционной смеси, уменьшением содержания темплата и ростом разбавления РС | Аэросил, NaAlO2, (C2H5)4NOH NaOH, H2O |
135 | 20–34 | 160–200 | 19 | |
Гидротермальный синтез | Смешивание свежеприготовленных растворов аэросила (C2H5)4NOH и пудры Al в (C2H5)4NOH. Изучениe влияния соотношения (C2H5)4NOH /Al2O3 | Аэросил, пудра Al, (C2H5)4NOH |
140 | 48–192 | 23.8 19.2 15.8 |
500 200 30 |
20 | |
Двухстадийный гидротермальный синтез с мезотемплатом | Мезотемплат−спиртовой раствора бромида цетилтриметиламмония (ЦТМАБ). Выход 85% |
Аэросил, AlOOH, (C2H5)4NOH |
140–170 | 7–14 дней |
25 | Нанокристаллы (20–30), агрегаты (400–600) | 21 | |
Парофазная кристаллизация с использованием зародышей | Содержание зародышей цеолита BEA 1–10%. Вода на дне автоклава | Аэросил, Al2(SO4)3, (C2H5)4NOH, NaOH |
140 | 28 | 11.6 | агрегаты (200–300) из первичных кристаллов (20–30) | 22 | |
Парофазная кристаллизация сухого геля в присутствии ПАВ (ЦТМАБ) | Высушивание геля перед кристаллизацией в течение 6−7 ч при 90°С | Силиказоль, Al2(SO4)3, (C2H5)4NOH, NaOH |
175 | 24 | 12.5–100 | 40–60 | 23 | |
MOR | Гидротермальный синтез | Изучение влияния щелочной среды | Na2SiO3, Al(NO3)3, Si(OC2H5)4 |
175 | 24 | Наносферы (20–30) нм, игольчатые кристаллы толщиной (50), длина 3 мкм | 24 | |
Гидротермальный синтез | Кристаллическая затравка 5 мас. % | NaAlO2, силикагель, NaOH |
150 | 24–48 | 17 | 62–110 | 25 |
Таблица 2.
Процессы нефтепереработки и нефтехимии с использованием наноразмерных цеолитных катализаторов
Процесс | Катализатор | Ссылки |
---|---|---|
Каталитический крекинг | Ультрастабильный цеолит FAU (Y), нанесенный на алюмосиликатную матрицу, с добавками цеолита MFI | 26, 27, 28 |
Гидрокрекинг | NiW–FAU NiMo–EA Ni2P–BEA |
29 30 31 |
Изомеризация | Pt/BEA | 32, 33 |
Олигомеризация | MFI | 34, 35 |
Трансалкилирование и диспропорционирование толуола | MFI | 36, 37 |
Разложение гидропероксида кумола в фенол и ацетон | MFI | 38 |
Конверсия метанола | MFI Fe–MFI |
39 40 |
Конверсия глицерина в акролеин | MFI | 41 |
Конверсия ацетона | MFI | 42 |
FAU. Цеолиты структурного типа FAU (Y) являются одними из наиболее востребованных цеолитов, так как составляют основу катализаторов таких важнейших процессов как каталитический крекинг и гидрокрекинг. Кристаллический каркас цеолита Y образован сочетанием вторичных структурных единиц – усеченных кубооктаэдров через шестигранные призмы. Цеолит Y обладает трехмерной пористой структурой, 12-членные кольца размером 0.74 нм ограничивают вход в полости размером около 1.3 нм. Наличие полостей в цеолите Y делает его структуру наиболее развитой и ажурной по сравнению с другими цеолитами.
Одним из основных методов синтеза нанокристаллического цеолита FAU является гидротермальная кристаллизация с использованием значительных количеств органического темплата (CH3)4NOH и низким содержанием Na в реакционной смеси,что приводит к образованию нанокристаллов размером менее 100 нм [6]. Однако основной проблемой синтеза нанокристаллического цеолита FAU является крайне низкий выход, связанный с незначительным содержанием натрия в реакционной смеси, что приводит к падению скорости кристаллизации. Авторами [7] был разработан метод увеличения выхода нанокристаллического цеолита FAU, заключающийся в коррекции содержания натрия в реакционной смеси путем периодического допирования микроколичеств NaOH в кристаллизующуюся смесь. В результате за 10 последовательных циклов синтеза выход нанокристаллического цеолита FAU с кристаллами размером 50–60 нм был увеличен до 43%. Метод получил развитие в работе [8], где в реакционную смесь каждые 12 ч вводили раствор 0.1 М NaOH до тех пор, пока соотношение Na2O/Al2O3 не увеличилось от 0.032 до 0.43; при этом размер кристаллов цеолита после 144 ч синтеза при 95°С составил 20–30 нм.
Существенный недостаток гидротермального синтеза нанокристаллического цеолита FAU – высокая концентрация гидроксид-ионов, обусловленная высокой концентрацией темплата – гидроксида четвертичного алкиламмония, приводящая к выщелачиванию смеси и низкому соотношению Si/Al в итоговом цеолите. В работе [9] было показано, что использование битемплатного синтеза со смесью (CH3)4NOH и (CH3)4NBr в мольном отношении 1 : 1 позволяет увеличить выход нанокристаллического цеолита FAU с размерами около 30–40 нм на 73%. Авторами [10] разработаны условия направленного синтеза нанокристаллов цеолита FAU из неорганических реакционных смесей на основе силиказоля. Показано, что получению нанокристаллического цеолита с размером кристаллов 10 и 70 нм способствует приготовление реакционной смеси из охлажденных до 4°С растворов с последующей выдержкой при комнатной температуре в течение суток, в результате которой происходит образование однородных по размеру (около 20 нм) коллоидных частиц еще до кристаллизации.
Бестемплатный трехстадийный синтез, предложенный в работе [11], позволил при снижении соотношения H2O/SiO2 с 23.2 до 12.2 уменьшить размеры агрегатов цеолита FAU, состоящих из нанокристаллов размером 20–80 нм, с 200 до 600 нм (рис. 1а и 1б).
В работе [12] была изучена возможность использования метода парофазной кристаллизации для получения нанокристаллического цеолита FAU с использованием реакционной смеси на основе аэросила, алюмината натрия и гидроксида натрия. После смешивания исходных реагентов и гомогенизации реакционной смеси ее упаривали в течение 6 ч при температуре 50°С, а затем кристаллизовали в парах воды при 90°С в течение 18 ч. Отношение массы воды на дне автоклава к массе геля составляло 9–12. Сравнение c нанокристаллическим образцoм, полученным в тех же условиях методом гидротермальной кристаллизации, показало, что в условиях парофазной кристаллизации образуются кристаллы цеолита FAU размером 200–400 нм, тогда как в условиях гидротермальной кристаллизации размер кристаллов возрастает до 700–800 нм.
MFI. Высококремнистый синтетический цеолит MFI (ZSM-5) относится к семейству пентасилов. Основа кристаллической решетки цеолитов этого семейства – сдвоенные вторичные структурные единицы 5–1, формирующие линейные цепочки, дальнейшее соединение которых происходит через четырех-, пяти- и шестичленные кольца. В результате пористая структура цеолита MFI образована пересекающимися прямыми и синусоидальными каналами с сечением эллиптической формы с размером поперечников около 5.5 Å. Цеолит MFI нашел широкое применение в нефтеперерабатывающей и нефтехимической промышленности благодаря свойствам своей пористой структуры, широкому диапазону отношений Si/Al, гидрофобности и высокой термической устойчивости. К числу реакций углеводородов (УВ), протекающих на цеолитах типа MFI, относятся крекинг, изомеризация, олигомеризация, ароматизация, алкилирование, диспропорционирование и другие реакции.
Впервые коллоидный нанокристаллический цеолит MFI был синтезирован Пирссоном и соав. путем кристаллизации чистого гомогенного раствора при 98°С в течение 60 ч с получением коллоидного раствора с размерами кристаллов цеолита 98–150 нм [13]. Начиная с 2000-х гг., растет интерес к синтезу нанокристаллических цеолитов MFI с размером кристаллов 20–100 нм и развитой площадью поверхности. Авторы [14] проводили сравнение разных синтетических подходов к получению нанокристаллического цеолита MFI. Хорошо воспроизводимыми синтезами цеолита MFI с отношением Si/Al = 60 и с размером кристаллов менее 100 нм являются гидротермальная кристаллизация с использованием тетраэтоксисилана в качестве источника кремния и синтез с использованием коллоидных затравок силикалита.
Среди новых подходов к синтезу наноразмерных цеолитов MFI можно отметить синтез цеолита в структурированной инертной матрице, позволяющий получить цеолиты MFI соотношением Si/Al = 50 и 100 и размером нанокристаллов 20–40 нм. Недостатком данного метода, кроме сложности синтетической процедуры, является также увеличение размеров нанокристаллов при термическом удалении инертной матрицы до 35–70 нм [15]. Получение нанокристаллического цеолита MFI гидротермальным синтезом без использования инертных носителей возможно путем уменьшения соотношения SiO2/Al2O3 и увеличения соотношения OH–/SiO2 в реакционной смеси. Авторами [16] продемонстрированно, что уве-личение соотношения OH–/SiO2 в реакционной смеси от 0.2 до 0.3 приводит к уменьшению нанокристаллов цеолита от 40 до 30 нм и изменению их морфологии с кубической до сферической, что авторы связывают c равновесным растворением образующихся кристаллов цеолита в ходе гидротермального синтеза при повышенном отношении OH–/SiO2.
Рост нанокристаллов цеолита в ходе гидротермального синтеза с использованием органического темплата может быть ингибирован химическим модифицированием поверхности нанокристаллов. Авторам [17] удалось ограничить размер нанокристаллов цеолита MFI до 10–20 нм путем прививки молекулы фениламинопропилтриметоксисилана (ФАПТМС) к поверхности кристалла. По окончании синтеза нанокристаллы образуют агрегаты размером 200–300 нм (рис. 1в), обладающие развитой внешней поверхностью до 320 м2/г.
Альтернативный метод получения нанокристаллических цеолитов MFI – синтез с использованием затравок, который является более экологичным и экономически выгодным, поскольку не связан с использованием дорогостоящих органических темплатов. Использование кристаллических затравок позволило получить агрегаты с однородными ортогональными наночастицами размером примерно 70–100 нм в широком диапазоне отношений Si/Al от 30 до 80 [18].
BEA. Цеолит Бета (BEA) представляет собой широкопористый высококремнистый цеолит с трехмерной системой пересекающихся каналов с двенадцатичленными кольцами. В местах пересечения каналов образуются полости диаметром 6.68 Å. Возможность синтезировать цеолит ВЕА в широком диапазоне Si/Al (от 3 до 100) позволяет варьировать силу и концентрацию кислотных центpов на поверхности цеолита, что делает его перспективным катализатором процессов нефтехимии и нефтепереработки, таких как алкилирование, гидроалкилирование и изомеризация. Первые попытки синтезировать нанокристаллический цеолит BEA с использованием метода гидротермального синтеза были предприняты в конце 1990-х гг. в присутствии катиона тетраэтиламмония в качестве темплата. Уменьшение соотношения Si/Al в исходном геле от 200 до 8 приводит к уменьшению размера кристаллов цеолита от 100 до 10 нм [19]. Авторы [20] продемонстрировали, что увеличение соотношения (C2H5)4NOH/Al2O3 в реакционной смеси от 10 до 30 при фиксированном Si/Al, равном 25, приводит к уменьшению размера нанокристаллов цеолита BEA от 500 до 30 нм (рис. 1д и 1е) и сопровождается изменением морфологии нанокристаллов от сферической до кубической. При этом отношение Si/Al в цеолите уменьшается от 23.8 до 15.8.
Нанокристаллический цеолит BEA с широким диапазоном отношений Si/Al от 15 до 200 в виде сфероидных агрегатов размером 400–600 нм из первичных нанокристаллов 20–30 нм был получен при добавлении мезотемплата, в качестве которого использовали спиртовой раствор бромида цетилтриметиламмония (ЦТМАБ) [21].
Основной недостаток синтезов нанокристаллического цеолита BEA – высокое содержание в реакционной смеси дорогостоящего темплата. В работе [22] был предложен экономичный способ получения нанокристаллического цеолита ВЕА, основанный на парофазной конденсации с использованием одновременно темплата ТЕАОН и зародышей цеолита ВЕА. Высококристаллический цеолит BEA в виде сростков нанокристаллов размером 20–30 нм с развитой микро-мезопористой структурой был получен с использованием низкой концентрации темплата (ТЕАОН/SiO2 = = 0.1) и содержанием кристаллической затравки 1–10% от массы SiO2 в реакционной смеси. В работе [23] изучали кристаллизацию сухого геля в присутствии добавок ПАВ (ЦТМАБ) и было показано, что при увеличении содержания ЦТМАБ размер нанокристаллов цеолита ВЕА уменьшается от 80 до 40 нм.
MOR. Цеолит морденит (MOR) нашел широкое применение в качестве основы катализаторов для таких промышленных процессов, как изомеризация легких бензиновых фракций (С5–6), изомеризация ксилолов, трансалкилирование толуола. Морденит относится к широкопористым цеолитам, каналы которого образованы двенадцатичленными кремнекислородными кольцами с диаметром около 0.7 нм. Он кристаллизуется без использования темплата, отношение SiO2/Al2O3 в цеолите около 10. Синтез нанокристаллического цеолита MOR осложнен из-за необходимости присутствия в реакционной смеси значительных количеств натрия, что приводит к агломерации наночастиц. Авторы [24] проводили систематическое исследование влияния параметров гидротермального синтеза нанокристаллического морденита на размер и морфологию наночастиц. Наночастицы MOR с размером от 10 до 50 нм были получены гидротермальной кристаллизацией геля с отношением Si/Al, равном 5, приготовленного из раствора силиката натрия или тетраэтоксисилана в гидроксиде натрия с использованием алюмината натрия в качестве источника алюминия при 175°С в течение 24 ч. Наибольшее влияние на размер и морфологию кристаллов оказывает использование щелочной среды. Присутствие NaOH приводит к образованию либо сферических, либо игольчатых кристаллов размером около 50 нм, в то время как синтез в водной среде способствует образованию аморфных частиц неправильной формы. MOR с нанокристаллами размером 62 нм был получен гидротермальной кристаллизацией геля с низким отношением Si/Al с добавлением кристаллической затравки, при температуре 150°С в течение 48 ч [25]. Наибольшее влияние на размер нанокристаллов оказывает отношение Si/Al в реакционной смеси: снижение этого отношения с 30 до 15 приводит к уменьшению размера нанокристаллов цеолита от 110 до 62 нм. Дальнейшее уменьшение отношения Si/Al невозможно из-за образования, кроме морденита, примесной фазы анальцима.
Применение наноразмерных цеолитов в традиционных каталитических системах
Нанокристаллические цеолитные катализаторы находят свое применение как в процессах нефтепереработки и нефтехимии, так и в процессах газохимии и превращения возобновляемого сырья. В табл. 2 приведены процессы, в которых используются наноразмерные цеолитные катализаторы.
Каталитический крекинг. Процесс каталитического крекинга – важнейший процесс мирового топливно-энергетического комплекса, в ходе которого нефтяные фракции в высокотемпературном диапазоне перерабатываются в широкую фракцию легких углеводородов (ШФЛУ), бензиновую фракцию и газойль. Используемый в процессе катализатор – микросферический цеолитный катализатор, состоящий из ультрастабильного цеолита Y, нанесенного на аморфную алюмосиликатную матрицу, с добавками цеолита MFI, обладает существенным недостатком, связанным с несоответствием размера каналов цеолита и тяжелых нефтяных остатков, в результате чего реакция протекает лишь на внешней поверхности кристалла цеолита. Решением существующей проблемы является использование нанокристаллических цеолитов с развитой внешней поверхностью кристалла, что увеличивает доступность активных центров катализатора для тяжелых УВ. Кроме того, размер нанокристаллов, по данным [26], может влиять на селективность катализаторов крекинга вакуумного газойля (ВГО). Как показывают кривые, представленные на рис. 2а, по селективности образования бензиновой фракции катализаторы на основе наноразмерых цеолитов Y (FAU) и инертного связующего оксида кремния образовывали ряд нано-FAU-25 > нано-FAU-40 > > нано-FAU-100, где 25, 40 и 100 – размер цеолитных нанокристаллов. Эта последовательность сохранялась для величин выходов бензиновой фракции и фракции легкого газойля [26].
Рис. 2.
Влияние размера кристаллов цеолита на его каталитические свойства в процессах нефтепереработки: а – цеолит FAU (Y), каталитический крекинг ВГО [26]; б – цеолит MFI, каталитический крекинг нафты [27]; в – цеолит FAU (Y), гидрокрекинг ВГО. ◻ – Конверсия ВГО, ◼ – селективность образования средних дистиллятов [29].
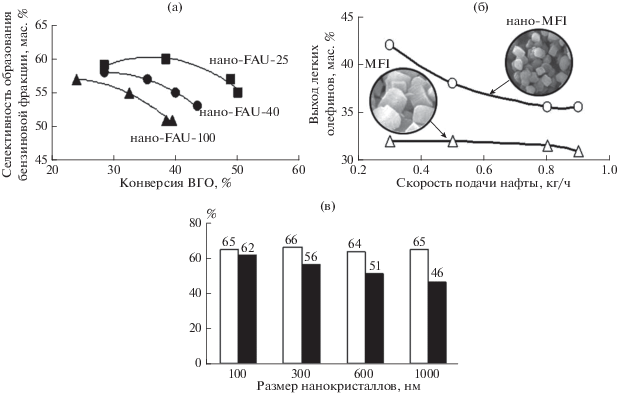
По данным [27], совершенствование катализатора этого процесса связано, в том числе, с уменьшением размеров кристаллов цеолита MFI, присутствие которого в составе катализатора обеспечивает рост выхода пропилена и бутенов за счет превращения линейных и моноразветвленных алкенов. Для наноразмерного цеолита MFI и его микрокристаллического аналога в составе микросферического катализатора крекинга (пилотная установка, режим кипящего слоя, температура 680°С) получены зависимости выхода легких олефинов С2–С4 от массовой скорости подачи сырья (рис. 2б). Из представленных зависимостей следует, что катализатор на основе наноразмерного цеолита MFI (диаметр СЭМ-изображения на рисунке соответствует 5 мкм) превосходит промышленный катализатор на основе цеолита MFI с размером кристаллов около 2 мкм по выходу олефинов в широком диапазоне скоростей подачи нафты. По мнению авторов [27], этот факт связан с ростом крекирующей активности катализатора за счет увеличения числа доступных активных центров в наноразмерном цеолите.
Использование наноразмерных цеолитных катализаторов в процессе каталитического крекинга позволяет также повысить стабильность работы катализатора, что было продемонстрировано авторами [28] на примере крекинга н-гексана, циклогексана и метилциклогексана на нанокристаллических цеолитах MFI. Увеличение стабильности работы наноразмерного цеолита MFI (90 нм) по сравнению с его макрокристаллическим аналогом (2300 нм) происходит за счет увеличения внешней поверхности кристалла и большей доступности активных центров внутри пор, а также за счет сокращения диффузионного пути молекул реагентов и продуктов. Исследование дезактивации катализаторов показало, что при крекинге н-гексана количество кокса на наноразмерном цеолите составляет 13% после 15 ч эксперимента, при этом конверсия н-гексана падает незначительно. Анализ пористой структуры наноразмерного MFI после катализа свидетельствует о незначительном падении площади поверхности и объема микропор, что авторы объясняют накоплением кокса на развитой внешней поверхности без блокировки пор и активных центров цеолита.
Гидрокрекинг ВГО. Гидрокрекинг вакуумного газойля является промышленным процессом для производства ценных нефтепродуктов, таких как бензин и средние дистилляты, из тяжелых УВ. Средние дистилляты, полученные в процессе гидрокрекинга, представляют собой смесь дизельного топлива с высоким цетановым числом и низким содержанием серы. Решающую роль в процессе играет выбор катализатора гидрокрекинга, совмещающего гидрирующую и крекирующую функции. Широкое использование цеолита FAU (Y), как одного из основных компонентов катализаторов гидрокрекинга вакуумного газойля, обусловлено его высокой кислотностью. Однако эффективность коммерческого цеолита Y не может обеспечить максимальный выход средних дистиллятов из-за высокой крекирующей активности цеолита, связанной с большим вкладом вторичных процессов крекинга, ведущих к образованию большого количества легких дистиллятов. Среди возможных методов увеличения эффективности цеолита FAU (Y) в гидрокрекинге ВГО авторы [29] выделяют уменьшение размера кристаллов цеолита. Гидрокрекинг ВГО с использованием катализаторов, приготовленных на основе цеолита FAU (Y) с размерами кристаллов 100, 300, 600 и 1000 нм, аморфного алюмосиликата и гидрирующих компонентов никеля и вольфрама, изучали в работе [29]. В интервале температур 340–370°С активность катализаторов росла с уменьшением размера нанокристаллов, наибольшей активностью обладал катализатор, приготовленный на основе цеолита FAU (Y) с размером кристаллов 100 нм, высокая крекирующая активность которого, по мнению авторов, связана только с увеличением числа доступных кислотных центров на поверхности мелких кристаллов. Как показано на рис. 1в, при близких значениях конверсии ВГО (около 65%), этот же образец характеризовался наибольшей селективностью образования средних дистиллятов, что авторы связывали с сокращением диффузионного пути первичных продуктов крекинга и предотвращением реакций вторичного крекинга [29]. Схожие результаты были получены авторами [30] для мягкого гидрокрекинга ВГО при умеренных давлениях (3.0–5.0 МПа) и в диапазоне температур 375–425°С с использованием в качестве кислотного компонента катализатора нанокристаллического цеолита BEA. Авторы продемонстрировали увеличение каталитической активности катализатора в реакциях гидроочистки, гидрообессери-вания и гидродеазотирования при уменьшении размера кристалла цеолита ВЕА от 200 до 10 нм. Кроме того было показано, что с уменьшением размера кристаллов селективность в средние дистилляты растет, а в газообразные продукты – падает, что авторы также объясняют уменьшением диффузионного пути первичных продуктов крекинга и предотвращением реакций вторичного крекинга.
Нанокристаллические цеолиты ВЕА были изучены авторами [31] в процессе гидрокрекинга полиароматических УВ (смеси 15% фенантрена и 85% 1-метилнафталина) в бензол, толуол и ксилол (БТК-фракцию) при 380°С и 6 МПа в составе Ni2P/BEA-катализатора. Выход БТК-фракции на нанокристаллическом катализаторе Ni2P/BEA-нано составил 42.3%, что значительно превышало выход на микрокристаллическом катализаторе (30.5%). В продуктах реакции с использованием в качестве катализатора Ni2P/BEA-микро преобладают алкилтетралин и гидрированный фенантрен, что свидетельствует о меньшей крекирующей активности образца на основе микрокристаллического цеолита, по сравнению с нанокристаллическим. Авторы связывают более высокую крекирующую активность образца на основе нанокристаллического цеолита с наличием межкристаллических мезопор, образующихся при агломерации нанокристаллов, обеспечивающих высокую дисперсность Ni2P-фазы и доступность кислотных центров цеолита. Кроме того, переход от использования микрокристаллического цеолита к нанокристаллическому повышает стабильность работы катализатора за счет меньшего коксования.
Гидроизомеризация парафинов. Гидроизомеризация нормальных парафинов является одним из наиболее перспективных путей переработки нефтяных фракций в высокооктановое бензиновое топливо. Pt-содержащие широкопористые цеолиты, такие как цеолит MOR и ВЕА, являются эффективными катализаторами этого процесса. Однако к существенным недостаткам этих катализаторов относятся диффузионные ограничения транспорта крупных молекул в их пористой системе, приводящие к снижению селективности процесса по полиразветвленным изоалканам, имеющим наиболее высокое октановое число. Использование наноразмерных цеолитов способствует снятию диффузионных ограничений за счет большей доступности кислотных центров. Изучение влияния размерного эффекта в реакции изомеризации н-гептана было проведено на Pt-содержащих цеолитах BEA в присутствии и отсутствии бензола в сырье [32]. Конверсия н-гептана выше на микрокристаллическом BEA за счет большего содержания в нем бренстедовских кислотных центров (БКЦ), однако изомеризующая активность у нанокристаллического образца больше: при конверсии 75% селективность в изогептаны составляет для образца на основе нанокристаллического цеолита ВЕА 93%, а на его микрокристаллическом аналоге достигает значения 75%. Авторы объясняют наблюдаемую закономерность ростом скорости диффузии разветвленных гептанов в нанокристаллах, что уменьшает вклад вторичных процессов крекинга с образованием легких алканов.
Влияние размера частиц и наличия межкристаллитных границ изучалось в реакции гидроизомеризации н-пентана на Pt-содержащем цеолите BEA [33]. Для этого были приготовлены 4 образца с разным размером частиц: BEA–P-1340, BEA–P-830, BEA–P-250, представляющие собой поликристаллиты цеолита ВЕА, состоящие из нанокристаллов размера 30–40 нм и BEA–S-225, представляющий собой монокристаллический цеолит ВЕА с размером кристаллов 225 нм. Из табл. 3 видно, что увеличение температуры реакции приводит к росту частоты оборотов реакции, нормированной на количество БКЦ для всех катализаторов. Наиболее существенный рост наблюдается для монокристаллического цеолита: так, при температуре 380°С частота оборотов реакции на этом катализаторе почти в 2 раза выше по сравнению с его поликристаллическими аналогами. Авторы объясняют полученную закономерность меньшим содержанием БКЦ в монокристаллическом цеолите, что при температуре реакции 305°С, когда скорость реакции определяется только скоростью химических превращений, приводит к меньшим значения TOF по сравнению с поликристаллическими аналогами. При переходе к повышенным температурам существенное влияние на скорость реакции начинают оказывать процессы диффузии и TOF для поликристаллических образцов становится ниже, чем для монокристаллического из-за наличия межкристаллитных границ, затрудняющих диффузию реагентов.
Таблица 3.
Изомеризация н-пентана на Pt-содержащем цеолите BEA при разных температурах [33]
Катализатор | TOF, с–1 | Кол-во БКЦ, ммоль/г | ||
---|---|---|---|---|
305°С | 341°С | 380°С | ||
BEA–P-1340 | 0.33 | 0.59 | 0.74 | 0.187 |
BEA–P-830 | 0.40 | 0.73 | 1.00 | 0.165 |
BEA–P-280 | 0.38 | 0.93 | 1.44 | 0.192 |
BEA–S-250 | 0.13 | 0.87 | 2.31 | 0.064 |
Олигомеризация олефинов. Олигомеризация легких алкенов – важный процесс получения высокооктановых добавок к бензину, дизельного топлива, пластификаторов, масел и поверхностно-активных веществ. Эффективными катализаторами олигомеризации являются среднепористые цеолиты MFI, размер пор которых достаточен для образования внутри олигомеров, но препятствует образованию ароматических структур, ведущих в закоксовыванию образца. Существенный вклад в активность и селективность катализатора в процессе олигомеризации вносит внутрикристаллическая диффузия. В работе [34] изучали олигомеризацию бутан-бутиленовой фракции на катализаторах Н-MFI, представляющих собой агломераты нанокристаллов MFI (40–70 нм). Было продемонстрировано, что с уменьшением размера агломератов в ряду Н-MFI (2000–3000 нм) – Н-MFI (800–1500 нм) – Н-MFI (100–300 нм) увеличивается количество БКЦ на внешней поверхности от 1.8 до 27.5 мкмоль/г и растет начальная скорость конверсии бутенов от 3.4 до 31.2 г/гкат ч. Авторами предложен механизм действия БКЦ в олигомеризации бутенов в зависимости от их локализации в цеолите MFI (рис. 3).
Показано, что БКЦ на внешней поверхности кристалла обладают высокой активностью в реакциях изомеризации олигомеров, гидридного переноса, крекинга, циклизации и ароматизации, что приводит к ускоренному коксообразованию и росту доли легких УВ в продуктах. БКЦ внутри цеолитных кристаллов малоэффективны в связи с диффузионными ограничениями транспорта реагентов и продуктов во внутрикристаллических порах. Наиболее эффективны в олигомеризации БКЦ, находящиеся в приповерхностном слое кристалла, которые совмещают преимущества высокой активности (вследствие малых диффузионных ограничений) и стабильности к коксообразованию, благодаря формселективности. Для повышения эффективности и стабильности катализатора олигомеризации бутан-бутиленовой фракции было предложено проводить процесс на наноразмерном цеолите MFI с модифицированной внешней поверхностью кристалла, приводящей к отравлению кислотных центров на внешней поверхности. Стабильность работы этого катализатора по сравнению с промышленным аналогом была протестирована в условиях ускоренной дезактивации [35]. Было показано, что срок службы модифицированного нанокристаллического цеолитa был увеличен в 3 раза по сравнению с промышленным катализатором.
Трансалкилирование и диспропорционирование толуола. Процессы трансалкилирования и диспропорционирования толуола – важнейшие промышленные процессы нефтехимии, приводящие в образованию широкого круга ароматических УВ, являющихся важными прекурсорами для полимерной и химической промышленности. В настоящее время наиболее часто используемыми катализаторами этих процессов являются цеолиты MOR, FAU (Y) и MFI, основными недостаткaми которых являются диффузионные ограничения при транспорте крупных ароматических молекул, например триметилбензолов. Авторы [36] изучали размерный эффект в реакциях диспропорционирования толуола и алкилирования толуола метанолом на цеолите MFI. Для обеих реакций наблюдались одинаковые закономерности: рост размера кристаллов цеолита от 300 нм до 4 мкм приводил к падению конверсии толуола и выходов бензола, триметилбензолов и ксилолов, при этом селективность по п-ксилолу увеличивалась. Этот эффект авторы объясняли снижением внешней поверхности кристаллов при увеличении их размера и появлением диффузионных затруднений. п-Ксилол является первичным продуктом алкилирования толуола и скорость его диффузии из пор цеолита выше, чем для о- и м-изомеров, которые изомеризуются в п-ксилол в порах цеолита. Увеличение диффузионного пути молекул в кристаллах цеолита большего размера, таким образом, приводит к большей селективности по п-ксилолу.
В работе [37] изучали трансалкилирование бензола 1,2,4-триметилбензолом (ТМБ) в проточном реакторе при 400°С, 3 МПа и отношении бензол/ТМБ, равном 1/1, на нано- и микрокристаллических цеолитах MFI. Было показано, что за 48 ч эксперимента конверсия бензола снижается с 30 до 18% для микрокристаллического образца и с 52 до 48% для нанокристаллического, при этом количество кокса, накопленного на микрокристаллическом цеолите составляет 1.7%, а на его нанокристаллическом аналоге 3.8%. Авторы сделали вывод, что процесс трансалкилирования бензола ТМБ протекает на внешней поверхности цеолита и в устьях пор, о чем свидетельствуют большие конверсии для нанокристаллического образца.
Промышленным катализатором трансалкилирования толуола является широкопористый цеолит MOR, однако исследования каталитической активности нанокристаллического цеолита MOR до сих пор проведено не было.
Селективное разложение гидропероксида кумола в фенол и ацетон. В работе [38] изучали активность наноцеолитных катализаторов на основе цеолита MFI в процессе селективного разложения гидропероксида кумола в жидкой среде при температуре 60°С. Было продемонстрировано, что уменьшение размера кристаллов с 90 до 18 нм приводит к значительному росту конверсии от 60 до 94%; этот факт авторы связывают с увеличением доступности активных центров цеолита для крупной молекулы гидропероксида кумола за счет увеличения внешней поверхности катализатора.
Конверсия метанола в олефины. В течение последних десятилетий активное развитие получили процессы превращения метанола в УВ олефинового и бензинового ряда, позволяющие синтезировать широкий спектр УВ из газа и угля. Среди катализаторов этих процессов широкое распространение получили цеолиты типа MFI и силикоалюмофосфаты SAPO-34, однако основной проблемой их использования является высокая скорость дезактивации. Одним из распространенных решений этой проблемы является создание вторичных мезопор в структуре цеолита, что облегчает транспорт крупных молекул и снижает скорость накопления кокса. Переход к нанокристаллическим катализаторам, в свою очередь, позволяет решить проблему быстрой дезактивации за счет снижения диффузионных затруднений.
Сравнение нанокристаллического и мезопористого цеолита MFI с микрокристаллическим аналогом в конверсии метанола в УВ бензинового ряда при 370°С и 0.1 МПа в реакторе проточного типа было проведено в работе [39]. После 10 ч эксперимента конверсия метанола составила 100, 70 и 50% для нанокристаллического (120 нм), мезопористого (300 нм) и микрокристаллического (более 1 мкм) цеолита MFI соответственно. При этом, основными продуктами при использовании нанокристаллического цеолита MFI были С1–С4 парафины и легкие олефины, суммарная селективность по которым составляет 54%, а селективность в ароматические УВ падала по сравнению с мезопористым цеолитом MFI с 46.9 до 34.2%. Авторы связывают наблюдаемые закономерности с большей доступностью сильных кислотных центров в нанокристаллическом цеолите из-за развитой внешней поверхности и отсутствия диффузионных ограничений.
Размерный эффект в реакции превращения метанола в пропилен изучали на примере железосодержащего цеолита MFI с отношением Si/Fe 107 в работе [40]. Зависимости конверсии метанола и распределения продуктов реакции от времени для макрокристаллического Fe–MFI и его нанокристаллического аналога, представленные на рис. 4а, демонстрируют более высокую стабильность работы во времени и меньшее соотношение пропилен/этилен для нанокристаллического цеолита. Наблюдаемая закономерность связана, по мнению авторов, с образованием большего количества ароматических УВ на макрокристаллическом Fe–MFI, из которых в результате вторичных превращений и образуется этилен и коксовые отложения.
Конверсия глицерина в акролеин. Зависимости, представленные на рис. 4б, иллюстрируют различия в каталитических свойствах цеолитов MFI с одинаковым отношением Si/Al, равным 65, с кристаллами размером 20–60 нм и 20 мкм, в реакции дегидратации глицерина с получением акролеина [41]. Перспективность этого процесса связана с возможностью превращений органических соединений, получаемых из возобновляемых растительных источников сырья. Зависимости изменения конверсии глицерина (кривые 1 и 3, рис. 4б) и селективности образования акролеина (кривые 2 и 4, рис. 4б) во времени показывают бóльшую эффективность нанокристаллического цеолита MFI по сравнению с цеолитом MFI с кристаллами микронного размера, что, по мнению авторов, связано с ростом доступности сильных БКЦУ, необходимых для протекания реакции [41].
Конверсия ацетона в олефины. Высокая активность нанокристаллических цеолитов MFI была достигнута в процессе синтеза легких олефинов из ацетона в проточной установке при атмосферном давлении и 400°С [42]. Зависимости конверсии ацетона и селективности в ароматические продукты и фракцию С2–С4 демонстрируют высокую скорость дезактивации катализатора на основе микрокристаллического цеолита с размером кристаллов 2 мкм, по сравнению с его нанокристаллическим аналогом с размером кристаллов 30 нм. Авторы предполагают, что превращение ацетона и образование промежуточных продуктов протекает на приповерхностых кислотных центрах, малое содержание которых в микрокристаллическом цеолите приводит к быстрой дезактивации за счет блокировки пор. Для нанокристалического образца конверсия ацетона незначительно меняется со временем, однако селективность по ароматическим продуктам превышает селективность по целевым легким алкенам. Авторы связывают наблюдаемую закономерность с развитой внешней поверхностью наноцеолита, на которой образовавшиеся в процессе превращения ацетона алкены легко взаимодействуют друг с другом на близко расположенных кислотных центрах с образованием ароматических молекул. Для решения этой проблемы авторами было проведено селективное отравление кислотных центров на внешней поверхности методом каталитического крекинга силана с использованием дифенил-силана, в результате которого было отравлено около 30% кислотных центов на внешней поверхности нанокристаллического цеолита. Конверсия ацетона при этом уменьшилась незначительно с 99.7 до 97.6%, а селективность в ароматические продукты значительно упала с 54.3 до 35.6 с одновременным ростом селективности в целевые продукты с 28.2 до 45.3%, что подтверждает предположение авторов об образовании ароматических продуктов на кислотных центрах, расположенных на внешней поверхности цеолита.
Применение наноразмерных цеолитов в сларри-реакторах
Каталитические системы на основе сларри-реакторов представляют собой трехфазные системы, в которых твердый катализатор диспергирован в жидкой среде. При этом жидкой средой может являться как инертное вещество, так и превращающееся сырье, а газообразная фаза может быть представлена реагентами или продуктами. Наиболее распространенными сларри-реакторами являются реакторы с механическим перемешиванием среды, в которых используются механические перемешивающие устройства разного типа, а также барботажные сларри-реакторы, в которых жидкая среда с диспергированным катализатором перемешивается за счет барботируемуго газа через слой суспензии катализатора.
В настоящее время сларри-технологию рассматривают как наиболее прогрессивный способ осуществления гетерогенно-каталитических реакций с участием газообразного сырья [43]. Ее основными преимуществами являются простота конструкции и более низкие капитальные затраты на строительство крупномасштабных реакторов. Сларри-реакторы применяются в сильно экзотермичных реакциях. Интенсивный отвод тепла обычно обеспечивается разнообразными охладителями, погруженными в реакционную среду, а перемешивание с помощью барботажа газа или различными перемешивающими устройствами обеспечивает эффективный отвод тепла за счет улучшения коэффициента теплопередачи между реакционной средой и охладителями, а также отличный контроль температуры и отсутствие перегревов в разных частях реакционной среды.
Другое преимущество сларри-реакторов – высокая производительность каталитического процесса, что связанно с возможностью использования в таком реакторе тонко- или ультрадисперсной каталитической суспензии, причем устойчивость суспензии и эффективность катализа при использовании сларри-технологии тем выше, чем меньше размер каталитического зерна. При этом наибольшего эффекта можно достичь, применяя в сларри-реакторе катализаторы на основе наночастиц, диспергированных в жидкостях. Катализатор поддерживается в состоянии тонкодисперсной суспензии, и процесс по своим параметрам и результатам приближается к гомогенным системам. При уменьшении размера каталитических частиц увеличивается площадь активной поверхности катализатора, снижается внутридиффузионное торможение, улучшаются массоперенос и теплопередача, в результате возрастает скорость реакции, замедляются дезактивационные процессы. Наиболее перспективными в данном случае являются ультрадисперсные суспензии с наноразмерными частицами катализатора [5]. Основные эффекты от использования наноразмерных цеолитов в сларри-реакторах аналогичны описанным выше для проточных реакторов.
Конверсия диметилового эфира/метанола в низшие олефины. В последнее время все большую актуальность приобретают исследования различных путей синтеза низших олефинов (этилена и пропилена) из альтернативного сырья. Одним из перспективных направлений является получение низших олефинов на цеолитных и силикоалюмофосфатных катализаторах из природного газа через синтез газ, метанол или диметиловый эфир (ДМЭ) [44]. Процесс превращения метанола в низшие олефины впервые был предложен фирмой Mobil в 1977 г. [45] и в настоящее время реализован рядом крупных компаний [46], в частности UOP, ExxonMobil, Lurgi, DICP. Недостатки предложенных процессов – жесткие условия проведения реакции, стремительная дезактивация катализатора, а также высокая степень разбавления исходного сырья инертным газом. Поэтому большой интерес представляет поиск новых путей осуществления синтеза олефинов из метанола. В этом отношении перспективным представляется проведение этого процесса в сларри-реакторе [47].
Академиком С.Н. Хаджиевым были инициированы и успешно реализованы исследования по использованию наноразмерных цеолитов в каталитических превращениях метанола и ДМЭ в олефины в сларри-реакторах [48–52]. Авторами [48] были изучены каталитические свойства кристаллических силикоалюмофосфатов со структурой шабазита (CHA) в конверсии метанола в низшие олефины (сларри-реактор, 400°С, среда полидиметилсилоксан). Средний размер кристаллов катализаторов составлял 400 нм (нано-CHA) и 1 мкм (микро-CHA), но при этом силикоалюмофосфаты обладали одинаковой концентрацией кислотных центров – около 1400 мкмоль/г. Как показывают представленные на рис. 5а кривые дезактивации образцов, образец нано-СНА был более активен в изученном интервале времени, что, по мнению авторов, связано со снижением для этого образца диффузионных ограничений, как для молекул метанола, так и для продуктов реакции [48].
Аналогичные закономерности по влиянию размера кристаллов цеолитов на их активность получены авторами [50] при изучении конверсии ДМЭ в олефины в присутствии магнийсодержащих цеолитов MFI со средним размером кристаллов 1600, 700 и 80 нм (сларри-реактор, 300°С, среда – углеводородное масло Dowtherm PR). Как следует из диаграмм, представленных на рис. 5б, уменьшение размера цеолитных кристаллов от 1600 до 80 нм приводило к росту конверсии ДМЭ и выхода олефинов С2–С4 более чем в три раза.
Авторы [49] исследовали особенности механизма дезактивации наногетерогенного силикоалюмофосфата со структурой CHA (SAPO-34) в процессе конверсии метанола в низшие олефины в сларри-реакторе барботажного типа с использованием полидиметилсилоксана (ПДМС) в качестве среды для диспергирования катализатора. Было показано, что в сларри-реакторе происходит изменение механизма дезактивации катализатора по сравнению с традиционным механизмом, установленным для реактора с неподвижным слоем катализатора (рис. 6).
Рис. 6.
Механизм дезактивации катализатора в сларри-реакторе и реакторе с неподвижным слоем катализатора.
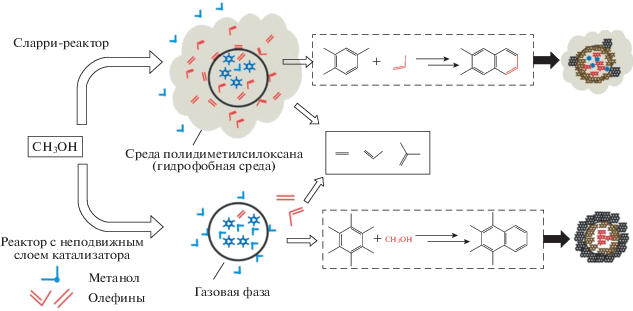
При проведении процесса в сларри-реакторе олефины, образующиеся на катализаторе, из-за высокой растворимости в дисперсионной среде остаются в приповерхностном слое в устьях пор катализатора, а метанол легко переходит в газовую фазу. В результате, поликонденсированные ароматические молекулы кокса образуются путем алкилирования олефинами ароматических молекул в приповерхностном слое катализатора и устьях пор, при этом внутренняя поверхность катализатора не дезактивируется, но становится недоступной для молекул реагентов.
В проточном реакторе с неподвижным слоем катализатора дезактивация протекает по-другому. Поликонденсированные ароматические соединения образуются в результате вторичной реакции метилирования ароматических соединений внутри пор катализатора.
Особенности дезактивации цеолитного катализатора в сларри-реакторе позволили авторам сделать вывод, что увеличение стабильности работы катализатора возможно двумя путями: уменьшением содержания олефинов в дисперсионной среде при изменении парциального давления метанола и селективного отравления активных центров на внешней поверхности катализатора. Авторами было продемонстрированно, что селективное отравление кислотных центров кристаллов катализатора оксидом кремния позволяет существенным образом повысить стабильность работы катализатора во времени. Конверсия метанола через 200 мин эксперимента на образце, подвергнутом обработке SiO2, возросла на 40% по сравнению с образцом с немодифицированной внешней поверхностью.
Алкилирование изоалканов олефинами. Алкилирование легких изоалканов, таких как изобутан, низшими олефинами, преимущественно пропиленом и бутиленами, имеет в настоящее время большое значение для получения высокооктановых добавок к топливу. Цеолитные катализаторы обладают высокой активностью в этом процессе, однако подвержены стремительной дезактивации, что не позволяет использовать традиционные реакторы с неподвижным слоем катализатора, поскольку требует частых циклов замены и регенерацией катализатора.
Компанией Shell в 1996 г. была предложена технология по алкилированию изобутана на основе сларри-реактора с механическим перемешиванием с использованием низкокремнистого цеолита BEA (Si/Al 15) [53]. Проведение процесса в сларри-реакторе позволило добиться существенного повышения стабильности работы катализатора во времени до 200 ч за счет высокой активности катализатора и низкой концентрации олефинов в реакторе, что препятствовало кокосообразованию. Компания Mobil запатентовала технологию на основе сларри-реактора с циркулирующим катализатором, в котором использовались частицы цеолита с размером 20–200 мкм [54]. В качестве катализаторов были выбраны цеолиты с достаточно крупным размером пор для адсорбции 2,2,4-триметилпентана, такие как ZSM-3, ZSM-4, ZSM-12, ZSM-18, ZSM-20, BEA, L, MOR, FAU и MCM-22, которые могут быть модифицированы редкоземельными элементами.
Следует отметить, что наноразмерные цеолиты пока не были исследованы в процессах алкилирования в сларри-реакторах, однако можно предположить, что использование наноцеолитов позволит решить проблему быстрой дезактивации катализатора, существенно сдерживающую внедрение данного процесса в промышленность.
Гидроконверсия тяжелых остатков. Гидроконверсия является одним из самых эффективных путей по превращению тяжелых углеводородных остатков в транспортное топливо. Основные катализаторы, используемые в гидроконверсии тяжелых остатков, – сульфиды переходных металлов (Mo, W, Fe и т.д.). На основе данных катализаторов разработано большое количество технологий с использованием сларри-реактора, часть из них, такие как Veba Combi Cracker, UOPUniflex, PDVSA HDH-Plus и Eni Slurry Technology были внедрены в промышленность [55]. Однако даже современные высокотехнологичные процессы не позволяют достичь полной конверсии УВ. Решением данной проблемы может быть подход, предложенный компанией Eni [56, 57], который основывается на совместном использовании катализаторов гидроконверсии (сульфид молибдена) и крекинга (цеолит HY). Было показано, что использование такой системы “двойного катализатора” позволяет существенно повысить продуктивность технологии в течение первых 20 ч и не снижать конверсию УВ по сравнению с системой с одним катализатором достаточно долгое время. Комбинация катализатора крекинга с катализатором гидроконверсии на основе молибдена привела к созданию стабильной каталитической системы, позволяющей минимизировать образование кокса и предотвратить дезактивацию катализатора крекинга.
Дальнейшие перспективы в данной области могут быть связаны с использованием наноразмерного цеолита Y, что будет способствовать увеличению устойчивости катализатора к дезактивации, по аналогии с примерами описанными вы-ше.
Использование наноразмерных цеолитов в реактивных двигателях
Принципиально новая область использования наноразмерных цеолитов описана в работе [58], авторами которой предложено допирование в количестве 100 ppm цеолита ВЕА с размером кристаллов около 20 нм в реактивное топливо JP-10 для изменения режима сгорания топлива в реактивных двигателях путем сочетания термического и каталитического крекинга.
ЗАКЛЮЧЕНИЕ
Анализ литературных данных по синтезу наноразмерных цеолитов FAU, MFI, BEA и MOR показал, что наноцеолиты могут быть синтезированы в широком диапазоне размеров кристаллов от 20 до 300 нм, при этом индивидуальные кристаллы имеют склонность к образованию агломератов размерами от 100 до 600 нм. Основными преимуществами наноразмерных цеолитов являются увеличение доступности активных центров и сокращение диффузионного пути при транспорте реагентов и продуктов реакции в кристалле. Увеличение доступности активных центров приводит к повышению эффективности работы катализатора и росту селективности по целевым продуктам в таких процессах, как каталитический крекинг, гидрокрекинг, олигомеризация, конверсия глицерина и др. Уменьшение диффузионного пути молекул продуктов внутри пор способствует росту стабильности работы катализаторов в процессах гидроизомеризации, каталитического крекинга, олигомеризации, конверсии метанола и ацетона в олефины.
Использование цеолитов с наноразмерными кристаллами в сларри-реакторах в процессах конверсии метанола и ДМЭ в олефины, приводит к увеличению стабильности работы катализатора за счет увеличения внешней поверхности кристалла. Дальнейшие перспективы применения наноцеолитных катализаторов в сларри-реакторах связаны с процессами гидроконверсии тяжелых остатков и алкилированием изоалканов олефинами.
Приведенные данные иллюстрируют высокую эффективность наноразмерных цеолитов как в проточных каталитических системах и реакторах с движущимся слоем катализатора в составе сформированных со связующим катализаторов, так и в сларри-реакторах в виде индивидуальных частиц цеолитов, диспергированных в жидкой среде, и свидетельствуют о широких перспективах их использования для усовершенствования существующих и создания новых процессов нефтепереработки, нефтехимии и газохимии.
Исследование выполнено за счет гранта Российского научного фонда (проект № 14-23-00094).
Список литературы
Valtchev V., Tosheva L. // Chem. Rev. 2013. V. 113. № 8. P. 6734.
Bellussi G., Carati A., Millini R. // In book “Zeolites and Catalysis. Synthesis, Reactions and Applications”. Ed. Cejka J., Corma A., Zones S. Wiley–VCH, 2010. P. 449.
Khadzhiev S.N. // Petrol. Chemistry. 2011. V. 51. № 1. P. 1.
Khadzhiev S.N. // Petrol. Chemistry. 2016. V. 56. № 6. P. 465.
Khadzhiev S.N., Kolesnichenko N.V., Ezhova N.N. // Petrol. Chemistry. 2016. V. 56. № 2. P. 77.
Mintova S., Valtchev V. // Studies in Surface Science and Catalysis. 1999. V. 125. P. 141.
Song W., Grassian V.H., Larsen S.C. // Chem. Commun. 2005. P. 2951.
Morales-Pacheco P., Domínguez J.M., Bucio L., Alvarez F., Sedran U., Falco M. // Catal. Today. 2011. V. 166. P. 25.
Holmberg B.A., Wang H., Norbeck J.M., Yan Y. // Microporous Mesoporous Mater. 2003. V. 59. P. 13.
Awala H., Gilson J.-P., Retoux R., Boullay P., Goupil J.-M., Valtchev V., Mintova S. // Nature Materials. 2015. V. 14. P. 447.
Huang Y., Wang K., Dong D., Li D., Hill M.R., Hill A.J., Wang H. // Microporous Mesoporous Mater. 2010. V. 127. P. 167.
Hu D., Xia Q.-H., Lu X.-H., Luo X.-B., Liu Z.-M. // Mater. Res. Bull. 2008. V. 43. P. 3553.
Persson A.E., Schoeman B.J., Sterte J., Otterstedt J.-E. // Zeolites. 1995. V. 15. № 7. P. 611.
Reding G., Mäurer T., Kraushaar-Czarnetzki B. // Microporous Mesoporous Mater. 2003. V. 57. P. 83.
Schmidt I., Madsen C., Jacobsen C.J.H. // Inorg. Chem. 2000. V. 39. P. 2279.
Yamamura M., Chaki K., Wakatsuki T., Okado H. // Zeolites. 1994. V. 14. P. 643.
Serrano D.P., Aguado J., Escola J.M., Rodríguez J.M., Peral Á. // Chem. Mater. 2006. V. 18. P. 2462.
Wu G., Wu W., Wang X., Zan W., Wang W., Li C. // Microporous Mesoporous Mater. 2013. V. 180. P. 187.
Camblor M.A., Mifsud A., Perez-Pariente J. // Zeolites. 1991. V.1 1. P. 792.
Ding L., Zheng Y. // Mater. Res. Bull. 2007. V. 42. P. 584.
Kong L., Chen H., Tai J., Shen J., Zhang S., Chen J. // Mater. Lett. 2009. V. 63. P. 343.
Cheng X., Mao J., Lv X., Hua T., Cheng X., Long Y. Tang Y. // J. Mater. Chem. A. 2014. V. 2. P. 1247.
Sakthivel A., Iida A., Komura K., Sugi Y., Chary K.V.R. // Microporous Mesoporous Mater. 2009. V. 119. P. 322.
Sharma P., Rajaram P., Tomar R. // J. Coll. Interf. Sci. 2008. V. 325. P. 547.
Hincapie B.O., Garces L.J., Zhang Q., Sacco A., Suib S.L. // Microporous Mesoporous Mater. 2004. V. 67. P. 19.
Vuong G.-T., Hoang V.-T., Nguyen D.-T., Do T. // Appl. Catal. A: Gen. 2010. V. 382. P. 231.
Kang N.Y., Woo S.I., Lee Y.J., Bae J., Choi W.C., Park Y.-K. // J. Mater. Sci. 2016. V. 51. P. 3735.
Konno H., Tago T., Nakasaka Y., Ohnaka R., Nishimura J., Masuda T.// Microporous Mesoporous Mater. 2013. V. 175. P. 25.
Cui Q., Zhou Y., Wei Q., Tao X., Yu G., Wang Y., Yang J. // Energy Fuels. 2012. V. 26. P. 4664.
Camblor M.A., Corma A., Martinez A., Martinez-Soria V., Valencia S. // J. Catal. 1998. V. 179. P. 537.
Kim Y.-S., Cho K.-S., Lee Y.-K. // J. Catal. 2017. V. 351. P. 67.
Arribas M.A., Martinez A. // Catal. Today. 2001. V. 65. P. 117.
Ye G., Sun Y., Guo Z., Zhu K., Liu H., Zhou X., Coppens M.-O. // J. Catal. 2018. V. 360. P. 152.
Popov A.G., Pavlov V.S., Ivanova I.I. // J. Catal. 2016. V. 335. P. 155.
Орлов С. // Сибирская нефть. 2017. № 138. С. 16.
Shiralkar V.P., Joshi P.N., Eapen M.J., Rao B.S. // Zeolites. 1991. V. 11. P. 511.
Cheng X., Wang X., Long H. // Microporous Mesoporous Mater. 2009. V. 119. P. 171.
Kumar K.P., Selvin R. // Int. J. Materials Engineering Innovation, 2010. V. 1. № 3/4. P. 417.
Rownaghi A.A., Hedlund Y. // Ind. Eng. Chem. Res. 2011. V. 50. P. 11872.
Taniguchi T., Yoneta K., Nakaoka S., Nakasaka Y., Yokoi T., Tago T., Masuda T. // Catal. Lett. 2016. V. 146. P. 442.
Jia C.-J., Liu Y., Schmidt W., Lu A.-H., Schüth F. // J. Catal. 2010. V. 269. P. 71
Tago T., Konno H., Sakamoto M., Nakasaka Y., Masuda T. // Appl. Catal. A: Gen. 2011. V. 403. P. 183.
Wang T., Wang J., Jin Y. // Ind. Eng. Chem. Res. 2007. V. 46. P. 5824.
Mokrani T., Scurrell M. // Cat. Rev. 2009. V. 51. P. 1
Chang C.D., Silvestri A.J. // J. Catal. 1977. V. 47. P. 249.
Stöcker M. // Microporous Mesoporous Mater. 1999. V. 29. P. 3.
Хаджиев С.Н., Колесниченко Н.В., Ежова Н.Н., Коростелева И.Г., Яшина О.В., Хиврич Е.Н. // Патент РФ № 0002547838. 2015.
Konnov S.-V., Pavlov V.S., Ivanova I.I., Khadzhiev S.N. // Petrol. Chemistry. 2016. V. 56. № 12. P. 1154.
Konnov S.V., Pavlov V.S., Kots P.A., Zaytsev V.B., Ivanova I.I. // Catal. Sci. Technol. 2018. V. 8. P. 564.
Kolesnichenko N.V., Konnov S.V., Pavlov V.S., Yashina O.V., Ezhova N.N., Khadzhiev S.N. // Petrol. Chemistry. 2017. V. 57. № 7. P. 576.
Kolesnichenko N.V., Pavlov V.S., Stashenko A.N., Yashina O.V., Ezhova N.N., Konnov S.V., Khadzhiev S.N. // Reac. Kinet. Mech. Cat. Online publication.
Khadzhiev S.N., Maksimov A.L., Tret’yakov V.F., Talyshinskii R.M., Ilolov A.M. // Petrol. Chemistry. 2018. V. 58. № 8. P. 613.
De Jong K.P., Mesters C.M.A.M., Peferoen D.G.R., Van Brugge P.T.M., De Groot C. // Chem. Eng. Sci. 1996. V. 51. № 10. P. 2053.
Huang T.J., Shinnar R. // Patent US № 5292.981.1994.
Rispoli G., Bellussi G., Panariti N., Tagliabue L. // Patent US. № 2011/0005976 A1. 2011.
Bellussi G., Rispoli G., Molinari D., Landoni A., Pollesel P., Millini R., Panariti N., Montanari E. // Catal. Sci. Technol. 2013. V. 3. P. 176.
Bellussi G., Rispoli G., Landoni A., Millini R., Molinari D., Montanari E., Moscotti D., Pollesel P. // J. Catal. 2013. V. 308. P. 189.
Sun W., Liu G., Wang L., Zhang X. // Fuel. 2015. V. 144. P. 96.
Дополнительные материалы отсутствуют.