Нефтехимия, 2019, T. 59, № 3, стр. 350-356
Переработка тяжелых нефтяных остатков методом фильтрационного горения
Е. А. Салганский 1, *, С. В. Глазов 1, В. М. Кислов 1, М. В. Салганская 1, 2, Ю. Ю. Цветкова 1
1 Институт проблем химической физики РАН
Черноголовка, Россия
2 Московский государственный университет имени М.В. Ломоносова
Москва, Россия
* E-mail: sea@icp.ac.ru
Поступила в редакцию 01.08.2018
После доработки 15.10.2018
Принята к публикации 10.12.2018
Аннотация
Разработана схема двухстадийной утилизации отходов глубокой переработки тяжелых остатков нефти (гудрона) методом фильтрационного горения с получением в качестве конечного продукта тепловой энергии, и определены оптимальные условия переработки. Первая стадия представляет собой процесс газификации гудрона с получением горючего аэрозоля, состоящего из низкокалорийного газа с теплотой сгорания примерно 1.4 МДж/м3, и до 80% от массы исходного гудрона мелкодисперсных капель, сходных с ним по составу. На второй стадии происходило сжигание аэрозоля с получением тепловой энергии. Рассмотрены варианты утилизации исходного гудрона и гудрона с добавкой (до 5%) углеродного топлива. Установлено, то добавка углеродного топлива позволяет стабилизировать фронт горения.
Определяющее значение для развития всей нефтеперерабатывающей промышленности РФ имеет глубокая переработка тяжелых остатков нефти с целью получения из них дополнительных ресурсов моторных топлив и сырья для нефтехимии. Тем не менее, в связи многочисленностью возможных химических превращений, а также с большим объемом перерабатываемого сырья, даже процессы глубокой переработки нефти являются источником огромного количества высокотоксичных отходов, представляющих серьезную опасность для окружающей среды [1–3]. Переработка подобных отходов представляет значительные сложности, поскольку на настоящий момент универсальных приемлемых методов утилизации не разработано [4, 5].
Режим фильтрационного горения со сверхадиабатическими разогревами может быть использован не только для переработки твердых горючих, но и для сжигания горючих жидкостей [6, 7]. Сущность предлагаемого метода в этом случае заключается в том, что жидкое горючее смешивают с твердым инертным теплоносителем, имеющим достаточно высокую температуру плавления для предотвращения спекания, и в таком виде загружают в реактор [8, 9]. В качестве теплоносителя могут быть использованы как отходы огнеупорных изделий, например, крошка шамотного кирпича, так и специальные изделия, например, кольца Рашига. Для проведения процесса переработки в режиме фильтрационного горения загруженная в реактор масса отходов должна быть достаточно газопроницаема. Роль пористого каркаса в этом случае играет теплоноситель, а жидкое горючее может попадать в зону химических реакций с этим теплоносителем, который пропитан или покрыт слоем горючего. По мере приближения волны горения твердый материал постепенно прогревается, легкокипящие компоненты жидкости испаряются, а остальные подвергаются пиролизу. Коксовый остаток попадает в зону окисления, где сгорает с выделением тепла. Процесс сгорания коксового остатка обеспечивает самоподдерживающийся режим всего процесса. Продукты пиролиза вместе с продуктами горения выносятся газовым потоком в холодную зону и конденсируются в горючий аэрозоль.
Преимущества предлагаемого способа газификации – высокий КПД, низкие требования к калорийности [10], влажности [11] и фракционному составу газифицируемого топлива [12], высокие экологические показатели газификации [13, 14]. Золошлаковые продукты газификации проходят через высокотемпературную окислительную зону, благодаря чему практически свободны от остатков углерода и недогоревших органических веществ. Эти особенности позволяют осуществить некоторые промышленные процессы в чрезвычайно эффективном и низкозатратном режиме, основанном на теплоэффективности волны горения [15, 16]. Таким образом, становится возможным сочетание высоких экологических характеристик технологического процесса с энергетической и экономической эффективностью комплексного производства.
Цель настоящей работы – экспериментальное исследование закономерностей фильтрационного горения тяжелых остатков нефтепереработки в сверхадиабатическом режиме, а также определение пределов устойчивости процесса.
МЕТОДИКА ЭКСПЕРИМЕНТА
Экспериментальное исследование газификации образца тяжелых остатков нефтепереработки в режиме сверхадиабатического горения проведено на кварцевой лабораторной установке, которая состоит из вертикального цилиндрического реактора-газификатора, снабженного системами подачи воздуха, дожигания образующегося продукт-газа, а также средствами измерения температуры и определения состава газообразных продуктов. Схема установки представлена на рис. 1. Диаметр рабочей части кварцевого реактора-газификатора (1) составлял 46 мм.
Рис. 1.
Схема установки для исследования фильтрационного горения: 1 – реактор-газификатор, 2 – инертный наполнитель, 3 – воспламенительный состав, 4 – исследуемая смесь горючего с теплоносителем, 5 – электроспираль предварительного прогрева, 6 – компрессор, 7 – волна фильтрационного горения, 8 – ампула для проб газа, 9 – расходомеры, 10 – вентили, 11 – алюминиевый экран, 12 – дожигатель, 13 – воздуховодная трубка дожигателя, 14 – электроспираль для воспламенения продукт-газа, 15 – термопары, 16 – компьютер для сбора данных по температурам и расходам, 17 – отвод для отбора проб газообразных продуктов.
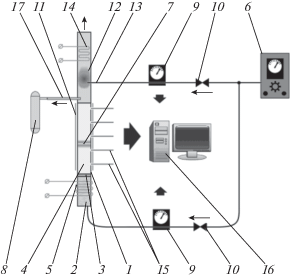
До начала эксперимента в нижнюю часть цилиндрического реактора-газификатора помещали твердый инертный наполнитель. Сверху на него насыпали воспламенительный состав (3) в виде небольшого количества легко воспламеняющегося горючего (1 г опилок и 2 г угля). Исследуемую исходную смесь (4) горючего с теплоносителем засыпали поверх воспламенительного состава в среднюю часть реактора-газификатора.
После предварительного прогрева нижней части реактора-газификатора с помощью электрической спирали (5) для возникновения волны фильтрационного горения, достаточно было с помощью компрессора (6) начать подачу воздуха в реактор. Фильтруясь через предварительно разогретый инертный наполнитель, воздух быстро прогревался до температуры 400°С, что приводило к возгоранию воспламенительного состава. При этом температура резко возрастала до 1000°С, благодаря чему в исследуемой смеси формировалась волна фильтрационного горения, характеризующаяся узкой высокотемпературной зоной (7). Далее, при непрерывной подаче воздуха в нижнюю часть реактора-газификатора, волна горения распространялась снизу вверх по исследуемой смеси. Благодаря прозрачности кварцевых стенок реактора продвижение высокотемпературной зоны можно было наблюдать визуально.
В течение опыта в реактор подавали воздух комнатной температуры, поскольку для проведения процесса не требовалось внешних источников тепла. Расход воздуха контролировали с помощью расходомера (9) и вентиля (10). Волна горения проходила по загруженной исследуемой смеси до верхнего уровня, после чего процесс горения прекращался сам собой. После опыта твердый остаток представлял собой смесь теплоносителя с некоторым количеством золы.
Для уменьшения теплопотерь наружную поверхность реактора-газификатора закрывали алюминиевым экраном (11). Верхняя часть реактора обычно служила дожигателем (12) выносимых горючих газов и легколетучих компонентов. Для этого туда подавали необходимое количество воздуха через воздуховодную трубку (13). Поджигание продуктов газификации осуществляли электроспиралью (14).
Температуру в волне фильтрационного горения измеряли с помощью термопар (15), спаи которых были размещены на внутренней боковой стенке реактора-газификатора. Информация с термопар выводилась через АЦП на компьютер (16). Кроме того, в реакторе имелся боковой отвод (17), через который в течение эксперимента периодически отбирали пробы газообразных продуктов в специальные стеклянные ампулы (8). Пробы анализировали на хроматографе Хроматек Кристалл 5000.
Эксперименты проводили на составе, где в качестве модели тяжелых нефтяных остатков выступал гудрон. Элементный анализ гудрона показал следующий состав: С – 85.0%, Н – 9.3%, S – 3.3%, О – 0.8%, N – 0.6%, зольность – 1.0%. Образец гудрона при комнатной температуре представлял собой густую, высоковязкую массу, при нагреве до 50оС размягчался, а при температуре 80оС превращался в жидкость. При температурах выше 300оС начинался пиролиз содержащихся в нем веществ.
При комнатной температуре гудрон трудно измельчить, а при нагреве он плавится и превращается в газонепроницаемую массу. При фильтрационном горении для достижения требуемых параметров важно наличие пористого газопроницаемого каркаса, обеспечивающего равномерную фильтрацию газа-окислителя. Теплоноситель создает такой каркас, что обеспечивает существование плоского фронта горения [8].
В настоящей работе были опробованы два варианта создания пористой газопроницаемой среды, содержащей гудрон. В первом варианте гудрон нагревали до температуры 80°С и перемешивали в жидком состоянии с нагретым теплоносителем. Поскольку после прекращения нагрева гудрон быстро остывал, то теплоноситель с нанесенным на него слоем гудрона слипался в единую массу. После этого смесь теряла подвижность и обеспечить равномерную загрузку в реактор было очень трудно. В связи с этим в первых пробных экспериментах часто наблюдали сильное искривление фронта горения. Кроме того, температура фронта при горении этих смесей была низкой, что не обеспечивало полноту сгорания исследуемого материала.
В связи с этим было принято решение в дальнейших экспериментах использовать другой вариант приготовления смеси. Гудрон охлаждали (при этом он становился хрупким), затем раскалывали на кусочки нужного размера, и механически смешивали с частицами твердого теплоносителя.
В ряде экспериментов проводили отбор проб жидких углеводородов (пиролизных смол), выносимых из реактора с газообразными продуктами горения. В этом случае лабораторная установка дополнялась системой сбора смол, а дожигание продуктов в верхней части кварцевой трубы не проводили.
РЕЗУЛЬТАТЫ И ИХ ОБСУЖДЕНИЕ
Для определения максимального содержания гудрона в шихте, при котором имеет место устойчивое протекание процесса газификации, провели серию экспериментов с постепенным увеличением содержания гудрона. Содержание гудрона в экспериментах варьировали от 20 до 40 мас. %. В качестве теплоносителя использовали либо крошку шамотного кирпича ПД5/Ш8, либо высокопористую керамику на основе оксида алюминия. Характерный размер шамотной крошки составлял 3–5 мм. Характерный размер пор керамики также составлял 3–5 мм, на вид она представляла собой губчатый материал. В качестве газообразного окислителя использовали воздух. Удельный расход воздуха в экспериментах не изменялся и составлял 680 м3/(ч м2).
На рис. 2 представлены зависимости температуры в разных сечениях по высоте реактора от времени при газификации шихты, содержащей 20% гудрона и 80% крошки шамотного кирпича. Термопары пронумерованы от Т1 до Т4 снизу-вверх по реактору (см. рис. 1). После подачи воздуха по шихте распространялась волна горения с максимальным значением температуры 600–650°С. В дожигателе, где сгорали газообразные продукты, температура держалась на уровне около 600°С (кривая – Flame). На 24 мин проведения эксперимента факел в дожигателе погасал, что свидетельствовало о завершении пиролиза гудрона. Однако процесс при этом не прекращался, и температура в реакторе поддерживалась на уровне 600°С еще в течение 15 мин. При этом происходило окисление коксового остатка пиролиза гудрона; волна окисления продолжала продвижение по реактору, о чем свидетельствует последовательный рост температуры на термопарах.
Рис. 2.
Зависимости температуры в разных сечениях реактора от времени при газификации шихты, содержащей 20% гудрона и 80% крошки шамотного кирпича. Термопары пронумерованы от Т1 до Т4 снизу-вверх по реактору.
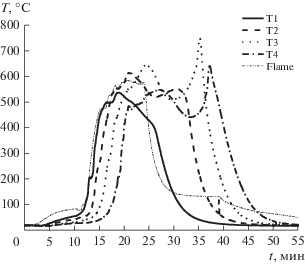
Таким образом, при газификации шихты, содержащей 20% гудрона и 80% крошки шамотного кирпича, узкого фронта горения не наблюдалось. Из рисунка видно, что практически по всей длине реактора температура держится на уровне 500–600°С.
После проведения эксперимента твердый остаток, выгруженный из реактора, представлял собой теплоноситель с небольшим количеством золы. Выгруженные твердые продукты не содержали недогоревший углерод (коксовый остаток) и органику. Зольный остаток содержал минеральную часть гудрона и пыль шамотного кирпича.
В экспериментах по газификации шихты, содержащей 30% гудрона и 70% губчатой керамики максимальное значение температуры составило около 900°С. Как и в предыдущем случае, факел в дожигателе горел не все время и погасал на 17 мин. После этого в течение 10 мин происходило окисление коксового остатка. Узкого фронта горения также не наблюдали, большая часть реактора быстро прогревалась до высокой температуры. В отличие от составов с 20% гудрона, после проведения эксперимента выгруженные твердые продукты содержали небольшое количество недогоревшего коксового остатка. В основном коксовый остаток содержался в самых верхних слоях засыпки.
Зависимости температуры в разных положениях реактора от времени при газификации шихты, содержащей 40% гудрона и 60% губчатой керамики, аналогичны представленным на рис. 2. Максимальное значение температуры горения составляло 800–850°С. Процесс газификации проходил аналогично предыдущим экспериментам, однако в данном случае наблюдали снижение скорости роста температуры в интервале 400–450°С. Это явление объясняется значительными временными затратами на пиролиз гудрона. В этих экспериментах также не наблюдали узкого фронта горения, т.е. значительная часть длины реактора находилась при высокой температуре. После проведения эксперимента в губчатой керамике, особенно в верхней части загрузки, обнаружено заметное количество несгоревшего коксового остатка. Поэтому дальнейшее увеличение содержания гудрона сочли нецелесообразным.
Из представленных результатов можно сделать вывод, что оптимальное содержание гудрона в шихте находится в интервале от 20 до 30 мас. %. При большем содержании гудрона твердые продукты содержат заметное количество недогоревшего коксового остатка.
Одним из основных управляющих параметров газификации является расход воздуха, поскольку производительность процесса напрямую зависит от этой величины. Однако при увеличении расхода воздуха могут возникнуть проблемы, в частности, увеличение перепада давления внутри реактора, нарушение сплошности среды и др. Для определения оптимального значения удельного расхода воздуха провели серию экспериментов, в которой расход воздуха варьировали от 350 до 1000 м3/(ч м2). Исходная шихта состояла из гудрона и губчатой керамики. Содержание гудрона во всех экспериментах оставалось постоянное и равное 30%.
На рис. 3 представлены зависимости температуры в разных сечениях реактора от времени при значении удельного расхода воздуха равном 350 м3/(ч м2). Максимальное значение температуры горения не превышало 600°С. По визуальным наблюдениям узкого фронта горения не наблюдалось, имело место свечение большей части длины реактора. Горение газообразных продуктов в дожигателе происходило только до 35-й мин проведения эксперимента, после чего происходило догорание коксового остатка в реакторе. После выгрузки твердые продукты сгорания содержали заметное количество непрореагировавшего коксового остатка.
Рис. 3.
Зависимости температуры в разных сечениях реактора от времени при значении удельного расхода воздуха 350 м3/(ч м2).
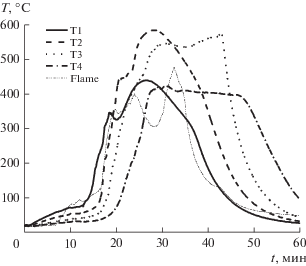
Зависимости температуры в разных сечениях реактора от времени при значении удельного расхода воздуха 680 м3/(ч м2) аналогичны предыдущему случаю. Максимальное значение температуры в этом эксперименте составляло около 900°С. Как и в предыдущем эксперименте, факел в дожигателе горел не все время и погас на 17-й мин. После этого в течение 10 мин происходило окисление коксового остатка. Как и в предыдущем эксперименте, большая часть длины реактора имела высокую температуру, т.е. узкого фронта горения также не наблюдали. После проведения эксперимента твердые продукты содержали небольшое количество недогоревшего коксового остатка, в основном, в верхней части засыпки.
Эксперимент с удельным расходом воздуха, равным 1000 м3/(ч м2), было решено провести без теплоизолирующего алюминиевого экрана с целью проведения визуального наблюдения за ходом процесса. Напротив третьей термопары (кривая – Т3) была помещена дополнительная термопара (кривая – Т3С), спай которой находился в центре реактора. Зависимости температуры в разных сечениях реактора от времени для удельного расхода воздуха, равного 1000 м3/(ч м2), представлены на рис. 4. Вследствие больших боковых теплопотерь максимальное значение температуры горения на стенке реактора не превысило 600°С. Однако в центре реактора (термопара Т3С) температура горения достигала 1000°С.
Рис. 4.
Зависимости температуры в разных сечениях реактора от времени при значении удельного расхода воздуха 1000 м3/(ч м2).
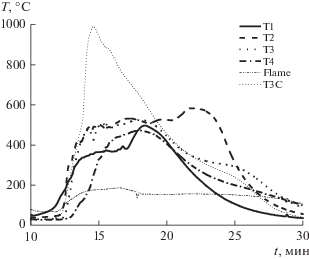
Визуальное наблюдение за фронтом горения показало, что газификация гудрона происходила нестабильно и хаотично, продвижения узкого фронта горения по реактору не наблюдали. При выгрузке твердые продукты горения содержали заметное количество коксового остатка, который в основном находился возле стенок реактора, где температура была значительно снижена из-за отсутствия теплоотражающего экрана.
В табл. 1 представлены максимальные значения температуры горения и скорости газификации гудрона в зависимости от удельного расхода воздуха. Скорость газификации гудрона рассчитывали, как отношение массы загруженного гудрона к времени процесса. При увеличении расхода воздуха, как максимальная температура горения, так и скорость газификации гудрона возрастали, что находится в согласовании с теоретическими представлениями [18].
Таблица 1.
Зависимость максимального значения температуры горения и скорости газификации гудрона в зависимости от удельного расхода воздуха
Уд. расход воздуха, м3/(ч м2) | 350 | 680 | 1000 |
---|---|---|---|
Температура горения, °С | 580 (у стенки) | 920 (у стенки) | 995 (в центре) |
Скорость газификации, г/с | 0.043 | 0.100 | 0.136 |
Из представленных результатов можно сделать вывод, что оптимальное значение удельного расхода воздуха близко к 680 м3/(ч м2). При меньшем значении расхода воздуха твердые продукты содержат заметное количество недогоревшего коксового остатка. При большем значении расхода заметно проявляется неустойчивость фронта горения и его отклонение от горизонтального положения.
Результаты предыдущих экспериментов показали, что при газификации шихты, состоящей из гудрона и теплоносителя, не реализуется узкого фронта горения. Высокотемпературная область занимает значительную длину реактора, и во всей этой области происходит окисление и пиролиз гудрона с образованием коксового остатка. В технологическом плане такой режим горения неприемлем, поскольку могут возникнуть сложности с выгрузкой горячих продуктов и загрузкой новой порции шихты. Для решения этой проблемы необходимо увеличить содержание горючей части шихты. Увеличение содержания гудрона, как показали результаты проведенного исследования, приводит к неустойчивости газификации. Поэтому было предложено вводить в состав шихты небольшое количество не пиролизующегося горючего, такого как древесный или каменный уголь, нефтяной кокс и др. Для оптимизации затрат необходимо определить минимальное содержание дополнительно вводимого горючего компонента, при котором в системе будет формироваться узкий устойчивый фронт горения. Как правило, для реализации устойчивого процесса фильтрационного горения требуется небольшое количество (несколько процентов) горючего [10].
На рис. 5 представлены зависимости температуры в разных положениях реактора от времени при газификации шихты, содержащей 20% гудрона, 5% дополнительного горючего и 75% крошки шамотного кирпича. В качестве дополнительного горючего был добавлен березовый активированный уголь марки БАУ-А с характерным размером частиц 3–5 мм. Линии одного типа, но разной толщины представляют показания термопар, расположенных в одном сечении друг против друга. Жирные линии представляют показания платино-платинородиевых термопар, спаи которых не защищены экраном и располагаются на внутренней стенке реактора (Т1–Т3). Тонкие линии представляют показания хромель-алюмелевых термопар, спаи которых защищены металлическим кожухом (Т1_1−Т3_3). Торец металлического кожуха также располагался на внутренней стенке реактора. Из графика видно, что показания противоположных термопар в разных сечениях реактора практически воспроизводят друг друга. Это свидетельствует о том, что фронт был плоский и горизонтальный. Показания хромель-алюмелевых термопар несколько ниже показаний платино-платинородиевых термопар вследствие большей инерционности.
Рис. 5.
Зависимости температуры в разных положениях реактора от времени при газификации шихты, содержащей 20% гудрона, 5% угля и 75% шамота.
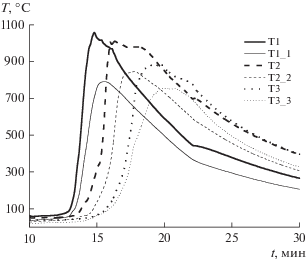
Из графика видно, что температурный профиль волны горения соответствует нормальной тепловой структуре, с крутым передним фронтом и пологим задним [18]. Реализуется плоский и относительно узкий фронт горения, что свидетельствует о устойчивости процесса при 5% дополнительного горючего.
Анализ состава газообразных продуктов газификации дал следующий результат, в об. %: CO2 – 14.7, Ar – 0.9, N2 – 70.6, CO – 6.5, CH4 – 1.0, H2 – 2.2. Преобладающим продуктом окисления горючего материала является CO2. Небольшое содержание метана связано с пиролизом гудрона в волне горения. Теплота сгорания газообразных продуктов составляет 1416 кДж/м3. Такой состав продуктов характерен для волн фильтрационного горения нормальной структуры.
Помимо газообразных компонентов в составе продуктов газификации присутствовали жидкие продукты пиролиза гудрона, пробы которых были отобраны и проанализированы. Элементный состав жидких продуктов пиролиза показал следующий результат: С – 84.8%, Н – 10.7%, S – 2.5%, О – 1.6%, N – 0.4%. Т.о., состав жидких продуктов пиролиза практически совпадает с составом исходного образца гудрона. Эксперименты по осаждению жидких продуктов пиролиза показали, что при необходимости можно выделить более трети от исходно загруженной массы гудрона в виде жидких продуктов и вернуть их на повторную или дополнительную переработку.
Попадая в зону горения, большая часть гудрона пиролизуется и уносится из реактора газовым потоком, оставшаяся часть окисляется кислородом воздуха. Оценить количество пиролизовавшегося гудрона можно из соотношения массовых скоростей газификации березового угля и смеси гудрона и березового угля. При этом делается справедливое предположение, что в смеси березового угля с гудроном березовый уголь сгорает полностью, а гудрон частично сгорает и частично пиролизуется. Наши оценки показали, что 70–80% от исходного гудрона пиролизовалось и не участвовало в реакциях окисления.
Таким образом, результаты проведенных экспериментов показывают, что добавление небольшого количества горючего материала к смеси гудрона с теплоносителем способствует устойчивости газификации. Реализуется плоский и относительно узкий фронт горения уже при добавлении около 5% дополнительного горючего. Причем в случае использования мелкодисперсного материала устойчивость фронта горения несколько повышалась по сравнению со случаем использования кускового горючего.
ЗАКЛЮЧЕНИЕ
На примере модельного образца гудрона показана принципиальная возможность утилизации методом фильтрационного горения со сверхадиабатическими разогревами тяжелых нефтепродуктов, остающихся после переработки нефти. Таким образом, можно замкнуть цикл нефтепереработки, ликвидировав наиболее проблемный с экологической точки зрения вид отходов. Образующееся при этом тепло целесообразно использовать на энергопотребляющих участках нефтеперерабатывающего комплекса.
Для устойчивого проведения процесса используется твердый теплоноситель, а также в состав шихты необходимо добавлять 4–5 мас. % углеродного (коксоподобного) горючего материала. В качестве дополнительного горючего может быть использован нефтяной кокс, каменный или древесный уголь, сажа и т.п. Оптимальное содержание нефтеотходов находится в интервале 20–30 мас. %. При большем количестве нефтеотходов твердые продукты будут содержать заметное количество недогоревшего углеродного остатка. Оптимальное значение удельного расхода воздуха близко к значению 700 м3/(ч м2). При меньшем значении расхода воздуха твердые продукты также содержат заметное количество недогоревшего коксового остатка. При большем значении расхода начинает заметно проявляться неустойчивость фронта горения и его отклонение от горизонтального положения.
Газообразные продукты газификации представляют собой аэрозоль, содержащий газообразные продукты сгорания и жидкие продукты пиролиза. Элементный состав жидких продуктов пиролиза практически совпадает с элементным составом исходных нефтеотходов. Сжигание аэрозоля в энергетическом устройстве типа котла позволит обеспечить тепловой энергией энергопотребляющие участки нефтеперерабатывающего комплекса.
Работа выполнена при финансовой поддержке Государственного заданияпо тем. карте ИПХФ РАН № 0089-2019-0018, Программы фундаментальных исследований Президиума РАН № 39.
Список литературы
Колмаков Г.А., Гришин Д.Ф., Зорин А.Д., Занозина В.Ф. // Нефтехимия. 2007. Т. 47. № 6. С. 411 [Petrol. Chemistry. 2007. V. 47. № 6. P. 379].
Бернадинер И.М., Бернадинер М.Н. // Твердые бытовые отходы. 2010. № 9. С. 18.
Колмаков Г.А., Занозина В.Ф., Каратаев Е.Н., Гришин Д.Ф., Зорин А.Д. // Нефтехимия. 2006. Т. 46. № 6. С. 414 [Petrol. Chemistry. 2006. V. 46. № 6. С. 384].
Павлов Г.И., Кочергин А.В., Ситников О.Р., Кочергина К.А., Гармонов С.Ю. // Вестник Казанского технологического университета. 2011. № 19. С. 168.
Кадиев Х.М., Батов А.Е., Дандаев А.У., Кадиева М.Х., Окнина Н.В., Максимов А.Л. // Нефтехимия. 2015. Т. 55. № 6. С. 522.
Manelis G.B., Glazov S.V., Salgansky E.A., Lempert D.B., Gudkova I.Yu., Domashnev I.A., Kolesnikova A.M., Kislov V.M., Kolesnikova Yu.Yu. // Intern. J. of Heat and Mass Transfer. 2016. V. 92. P. 744.
Какуткина Н.А. // Физика горения и взрыва. 2008. Т. 44. № 4. С. 21 [Combustion Explosion and Shock Waves. 2008. V. 44. № 4. P. 388].
Зайченко А.Ю., Глазов С.В., Салганский Е.А., Кислов В.М., Подлесный Д.Н., Жаворонков А.И., Салганская М.В. // Теоретические основы химической технологии. 2017. Т. 51. № 5. С. 525 [Theor. Foundations of Chem. Engineering. 2017. V. 51. № 5. P. 673].
Зайченко А.Ю., Глазов С.В., Салганский Е.А., Кислов В.М., Подлесный Д.Н., Салганская М.В., Цветков М.В. // Теоретические основы химической технологии. 2018. Т. 52. № 4. С. 473 [Theor. Foundations of Chem. Engineering. 2018. V. 5. № 4. P. 574].
Амелин И.И., Салганский Е.А., Волкова Н.Н., Жолудев А.Ф., Алексеев А.П., Полианчик Е.В., Манелис Г.Б. // Известия Академии наук. Серия хим. 2011. № 6. С. 1125 [Russian Chem. Bulletin, Intern. Edition. 2011, V. 60. № 6. Р. 1150].
Салганская М.В., Глазов С.В., Салганский Е.А., Кислов В.М., Жолудев А.Ф., Манелис Г.Б. // Химическая физика. 2008. Т. 27. № 1. С. 27 [Russian J. of Phys. Chemistry, В. 2008. V. 2. № 1. P. 71].
Salgansky E.A., Zaichenko A.Yu., Podlesniy D.N., Salganskaya M.V., Toledo M. // Int. J. of Hydrogen Energy. 2017. V. 42. P. 11017.
Toledo M., Utria K., Gonzalez F., Zuniga J., Saveliev A. // Int. J. Hydrogen Energy. 2012. V. 37. № 8. P. 6942.
Манелис Г.Б., Глазов С.В., Салганский Е.А., Лемперт Д.Б. // Успехи химии. 2012. Т. 81 № 9. С. 855 [Russian Chem. Rev. 2012. V. 81. № 9. P. 855].
Koshkin B. Yu., Bunev V.A., Babkin V.S., Laevsky Yu.M. // Combustion and Flame. 1995. V. 103. P. 143.
Howell J.R., Hall M.J., Ellzey J.L. // Progress in Energy and Combustion Science. 1996. V. 22. № 2. P. 121.
Salgansky E.A., Kislov V.M., Glazov S.V., Salganskaya M.V. // J. of Combustion. 2016. Article ID 9637082. 2016. P. 7.
Салганский Е.А., Фурсов В.П., Глазов С.В., Салганская М.В., Манелис Г.Б. // Физика горения и взрыва. 2003. Т. 39. № 1. С. 44 [Combustion, Explosion and Shock Waves. 2003. V. 39. № 1. P. 37].
Дополнительные материалы отсутствуют.