Нефтехимия, 2019, T. 59, № 4, стр. 410-416
Влияние cвязующего на свойства катализаторов на основе цеолитов семейства MWW в реакции алкилирования бензола пропиленом
И. М. Герзелиев 1, *, В. П. Жмылев 1, Д. О. Хусаимова 1, А. В. Шкуропатов 2, Е. Е. Князева 1, 2, О. А. Пономарева 1, 2, И. И. Иванова 1, 2, А. Л. Максимов 1
1 Институт нефтехимического синтеза им. А.В. Топчиева РАН
Москва, Россия
2 Московский государственный университет имени М.В. Ломоносова, Химический факультет
Москва, Россия
* E-mail: gerzeliev@ips.ac.ru
Поступила в редакцию 10.03.2019
После доработки 13.03.2019
Принята к публикации 14.03.2019
Аннотация
Изучено влияние природы связующего компонента (Al2O3, SiO2, каолин) на физико-химические и каталитические свойства в реакции алкилирования бензола пропиленом цеолитных катализаторов на основе иерархического цеолита структуры MWW. Лучшие результаты получены при использовании Al(OH)3 в качестве прекурсора для Al2O3. Данный прекурсор не влияет негативно на кислотные свойства катализатора, что, в свою очередь, увеличивает выход целевого продукта реакции кумола. Добавление каолина в этот катализатор не влияет на прочностные характеристики, но приводит к снижению количества кислотных центров в образце.
Изопропилбензол (кумол) – важный промежуточный продукт в нефтехимической промышленности для производства фенола и ацетона. Основная часть кумола производится путем алкилирования бензола пропиленом. Традиционные процессы с использованием катализаторов SPA (твердая фосфорная кислота) и алкилирование по Фриделю–Крафтсу (AlCl3) для промышленного производства кумола вызывают множество проблем, в частности, негативное влияние на окружающую среду и коррозию оборудования [1, 2]. В настоящее время интерес к изучению и разработке новых эффективных экологически чистых цеолитных катализаторов, которые могут работать при относительно низких соотношениях бензола и пропилена, постоянно растет с целью снижения эксплуатационных расходов [2].
В алкилировании бензола низшими олефинами проявляют каталитическую активность такие цеолиты, как BEA, MFI и MWW [3]. Наиболее активным среди них оказался цеолит со структурой BEA, однако его каталитическая активность стабильна лишь при относительно больших разбавлениях пропилена бензолом (мольное соотношение безнол/пропилен 6–8). Структура MWW оказалась немного менее активной, однако она сохраняет каталитические свойства при мольном соотношении бензол/пропилен на уровне 3–4, что позволяет значительно снизить затраты энергии на рециркуляцию бензола и выделение целевого продукта [4].
Кристаллы цеолита со структурой MWW представляют собой слоистые образования, единичные пластинки которых имеют толщину 2.5 нм и содержат две независимые системы микропор: синусоидальные поры, ограниченные 10-членными кремний-кислородными кольцами, и поры, по форме похожие на песочные часы, основания которых являются 12-членными кольцами. Алкилирование бензола низшими олефинами протекает с участием бренстедовских кислотных центров (БКЦ), расположенных в 12-членных полостях. Диффузия реагентов и продуктов внутри кристалла ограничена межслоевым пространством цеолита, поэтому в данной работе использован иерархический цеолит со структурой MWW (ИЦ-MWW), содержащий дополнительную систему мезопор, полученную методом рекристаллизации [5].
Поскольку в промышленности применяют катализаторы, полученные со связующим, что позволяет получить образцы с высокой прочностью гранул, то важной задачей является изучение влияния связующего компонента на физико-химические и каталитические свойства образцов. В настоящее время в литературе такие данные о катализаторах структуры MWW не представлены.
Цель данной работы – изучение влияния природы связующего компонента (Al2O3, SiO2, каолин) на физико-химические и каталитические свойства цеолита структуры MWW в алкилировании бензола пропиленом.
ЭКСПЕРИМЕНТАЛЬНАЯ ЧАСТЬ
Исходный цеолит MWW синтезировали по методике [6] с использованием в качестве темплата гексаметиленимина (ГМИ) из реакционной смеси состава 0.09Na2O ⋅ 0.033Al2O3 ⋅ SiO2 ⋅ 0.5ГМИ ⋅ ⋅ 45H2O. В качестве исходных реагентов использовали силикагель, алюминат натрия, гидроксид натрия, гексаметиленимина (99%, Aldrich) и дистиллированную воду. Гидротермальную обработку проводили при температуре 150°C в течение 5 сут при перемешивании, после чего полученный цеолит отмывали на воронке Бюхнера дистиллированной водой и сушили при 95°C.
Рекристаллизацию проводили путем гидротермальной обработки при 110°C в два этапа. На первом этапе происходит частичное растворение структуры цеолита в щелочном растворе бромида (1-гексадецил)триметиламмония. На втором этапе продукты растворения цеолита образуют мезопористую фазу с образованием микро-мезопористой структуры ИЦ-MWW.
Полученный ИЦ-MWW прокаливали при 550°C в токе воздуха в течение 8 ч, после чего проводили 5-ти кратный ионный обмен в 0.1 М растворе NH4NO3 с последующим прокаливанием при 550°C для получения протонированной формы цеолита.
Для приготовления цеолитсодержащих катализаторов использовали несколько связующих веществ. Оксид алюминия – традиционный связующий, используемый при приготовлении цеолитсодержащих катализаторов. Обычно конечной формой оксида алюминия в катализаторе является γ-Al2O3, для получения которой используют различные прекурсоры. При приготовлении образцов со связующим в качестве прекурсоров для Al2O3 были использованы бемит AlOOH (SASSOL) и гидроксид алюминия Al(OH)3 (“Промышленные катализаторы”, г. Рязань). Также в качестве связующего был использован оксид кремния, прекурсором для которого являлся силиказоль, представляющий собой коллоидную поликремневую кислоту. В качестве добавки, используемой для регулирования прочностных и текстурных характеристик образцов, был взят каолин – природный слоистый алюмосиликат.
Цеолитсодержащие катализаторы готовили из расчета 70 мас. % ИЦ-MWW и 30 мас. % связующего. При использовании каолина его брали в количестве 20% от массы связующего вещества. После замешивания порошка ИЦ-MWW и связующего вещества смесь формовали в гранулы цилиндрической формы размером 5 × 4 мм, высушивали при температуре 90°С и прокаливали при 550°С в течение 6 ч. Для определения характеристик пористой структуры связующих веществ были приготовлены гранулы из прекурсоров.
Содержание связующего в катализаторе контролировали методом рентгенофлуоресцентного анализа (РФА) в ЦКП при ИНХС РАН на приборе Thermo Scientific ARL Perform'X с родиевой трубкой 3.5 кВт.
Для определения механической прочности образцов со связующим на раздавливание был использован международный нормативный документ ASTM D6175-03.
Концентрацию кислотных центров (КЦ) в цеолитах определяли с использованием метода температурно-программированной десорбции аммиака (ТПД NH3). Навеску массой 150–200 мг прокаливали в токе гелия при 500°C, затем образец охлаждали до 60°C и насыщали аммиаком в токе газовой смеси NH3/N2 (1/9) в течение 30 мин. Затем образец нагревали до 100°C и отдували физически адсорбированный аммиак в токе гелия в течение 60 мин. Анализ проводили в диапазоне температур от 100 до 800°C со скоростью нагрева 8°C/мин; десорбированный аммиак регистрировали детектором по теплопроводности.
Изотермы низкотемпературной адсорбции азота получали на автоматическом поромере ASAP2000 (Micromeritics, США). Объем микропор определяли с использованием метода t-plot.
Изучение морфологии синтезированных образцов проводили методом сканирующей электронной микроскопии (СЭМ) на электронном микроскопе Hitachi 4 Tabletop Microscope TM3030Plus. Напряжение на ускоряющем электроде 15 кВ.
Эксперименты по исследованию каталитических свойств катализаторов проводили на лабораторной проточной установке [7] со стальным реактором. Загрузка катализатора составляла 1.5 см3.
Перед проведением каждого эксперимента осуществляли дегидратацию катализатора в токе аргона (расход 15 мл/мин на 1 см3 катализатора) со ступенчатым поднятием температуры и выдержкой: 120°C – 1 ч, 300°C – 1.5 ч, 400°C – 1 ч, 500°C – 1 ч. Эксперименты проводили при стандартных условиях: температура 205°C, атмосферное давление, мольное соотношение бензол : пропилен = 8 : 1, скорость подачи бензола 13.2 г/г ч, пропилена 0.9 г/г ч. Продолжительность опыта составила 240 мин с отбором проб каждые 40 мин.
Продукты реакции анализировали на газовом хроматографе Shimadzu GC2030 с пламенно-ионизационным детектором и капиллярной колонкой (DB-1, 100 м 0.25 мм 0.50 μм).
РЕЗУЛЬТАТЫ И ИХ ОБСУЖДЕНИЕ
На фотографиях, полученных методом сканирующей электронной микроскопии (рис. 1), можно видеть, что MWW представляет собой диски диаметром около 1 мкм и высотой 100 нм. Рекристаллизация мало влияет на морфологию кристаллов MWW.
Характеристики пористой структуры и кислотных свойств ИЦ-MWW и связующих веществ, используемых для приготовления цеолитсодержащих образцов, приведены в табл. 1. Как следует из данных этой таблицы, текстурные свойства использованных связующих веществ отличаются, в части, присутствием микропор (образцы Al2O3/ бемит и Al2O3/гидроксид) и диаметром мезопор. Кроме того, связующие вещества Al2O3, полученные из разных прекурсоров, обладают собственной кислотностью; концентрация КЦ для этого типа связующего составила 350 и 560 мкмоль NH3/г. В отличие от Al2O3, оксид кремния, полученный из силиказоля, характеризовался очень низкой кислотностью (табл. 1).
Таблица 1.
Физико-химические свойства ИЦ-MWW и связующих компонентов
Цеолитный компонент | Связующее | Характеристики пористой структуры | а0, мкмоль NH3/г | ||||
---|---|---|---|---|---|---|---|
вещество | прекурсор | SБЭТ, м2/г | Vпор, см3/г | Vмикропор, см3/г | Диаметр мезопор, нм | ||
ИЦ-MWW | – | – | 530 | 0.565 | 0.142 | 3 | 880 |
– | Al2O3 | Бемит | 300 | 0.420 | 0 | 7 | 350 |
– | Al2O3 | Al(OH)3 | 260 | 0.154 | 0.083 | 3 | 560 |
– | SiO2 | Силиказоль | 180 | 0.174 | 0 | 4 | 120 |
– | Каолин | Каолин | 18 | 0.040 | 0 | – | – |
Условия приготовления и физико-химические свойства образцов со связующим приведены в табл. 2, а изотермы низкотемпературной адсорбции азота – на рис. 3.
Таблица 2.
Физико-химические свойства цеолитсодержащих катализаторов
Образец | Состав образца | МПр1, кг/мм2 | Характеристики пористой структуры образцов со связующим | а0, мкмоль NH3/г | ||||
---|---|---|---|---|---|---|---|---|
цеолитный компонент | связующее | SБЭТ, м2/г | Vпор, см3/г | Vмикропор, см3/г | $V_{{{\text{м и к р о п о р }}}}^{2}$, см3/г | |||
№ 1 | 70% ИЦ-MWW | 30% Al2O3 (бемит) | 2.8 | 350 | 0.340 | 0.075 | 0.107 | 730 |
№ 2 | 70% ИЦ-MWW | 30% Al2O3 (Al(OH)3) | 0.6 | 440 | 0.343 | 0.087 | 0.124 | 800 |
№ 3 | 70% ИЦ-MWW | 24% Al2O3 + 6% каолин | 0.6 | 410 | 0.318 | 0.087 | 0.124 | 740 |
№ 4 | 70% ИЦ-MWW | 30% SiO2 | 1.1 | 410 | 0.383 | 0.098 | 0.140 | 580 |
№ 5 | 70% ИЦ-MWW | 24% SiO2 +6% каолин | 0.7 | 370 | 0.330 | 0.095 | 0.135 | 620 |
Экспериментальный образец № 1 был получен с использованием в качестве связующего бемита. Как следует из представленных в табл. 2 характеристик этого образца это обеспечивало прочность гранул на уровне 2.8 кг/мм2. Однако в ходе приготовления образца № 1 происходила частичная блокировка микропор активной цеолитной фазы, на что указывают смещение изотермы адсорбции азота вниз по оси ординат (рис. 1а) и уменьшенная величина объема микропор, рассчитанная на основании этой изотермы (табл. 2). Это может быть связано с особенностями связующего, размер частиц которого не превышает 300 нм. В то же время, кривые распределения пор по диаметру для ИЦ-MWW, Al2O3 (бемит) и образца № 1, приведенные на рис. 3, показывают следующее: присутствие двух максимумов на кривой распределения для образца № 1 подтверждает сохранение мезопор от ИЦ-MWW (поры 3 нм) и Al2O3 (бемит) (поры 7 нм). Однако уменьшение интенсивности максимумов на кривых распределения чистых материалов и катализатора может указывать на взаимное влияние цеолитного компонента и связующего, приводящее к блокировке не только микропор ИЦ-MWW, но и мезопор.
Рис. 2.
Изотермы низкотемпературной адсорбции-десорбции азота на активной фазе катализатора ИЦ-MWW и образцов, приготовленных с различными связующими.
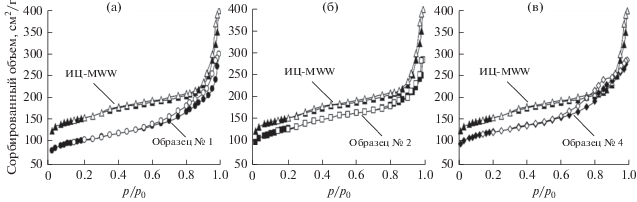
Рис. 3.
Кривые распределения пор по диаметру: 1 – ИЦ-MWW, 2 – связующее Al2O3 (бемит), 3 – образец № 1.
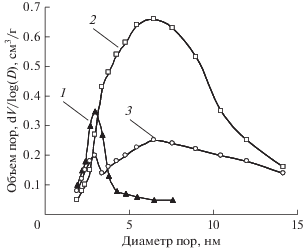
Как следует из данных табл. 2, замена бемита привела к ухудшению прочностных характеристик катализаторов: механическая прочность гранул образцов катализаторов № 2–5 уменьшилась до 0.6–1.1 кг/мм2. Добавление каолина в состав катализатора в количестве 20% от количества связующего не имело положительного эффекта. Очевидно, снижение прочности гранул связано с морфологическими особенностями ИЦ-MWW, представляющими собой плоские диски диаметром около 1 мкм и толщиной около 100 нм. Полученные данные позволяют предположить, что существует оптимальная величина размера частиц связующего, способная обеспечить взаимное ориентирование частиц активной фазы катализатора и частиц связующего для достижения высокой прочности гранул. Как показывают данные табл. 2, экспериментальные образцы катализаторов № 2–5 с низкой прочностью гранул характеризуются высокими значениями объемов микропор. При этом приведенные величины объемов микропор, т.е. пересчитанные с учетом содержания активной фазы в катализаторе 70%, близки величине объема микропор в исходном образце ИЦ-MWW (табл. 1). Эти данные указывают на слабое взаимодействие ИЦ-MWW – связующее в катализаторе, что может служить причиной их низкой прочности.
Как следует из величин концентрации КЦ, определенных по методу ТПД аммиака (табл. 2) и кривым термодесорбции аммиака (рис. 4), независимо от типа связующего, концентрация КЦ в экспериментальных образцах всегда ниже, чем в цеолитной фазе ИЦ-MWW. Анализ кривых ТПД аммиака на рис. 4 показывает, что взаимодействие цеолитного компонента и связующего сопровождается количественными и качественными изменениями кислотных свойств экспериментальных образцов. Количественные изменения, связанные с уменьшением концентрации как сильных, так и слабых кислотных центров имеют место в ряду: ИЦ-MWW > образец № 1 > образец № 2 > образец № 4. Качественные изменения проявляются в положении высокотемпературного пика на кривой ТПД, который смещается в сторону низких температур в ряду: ИЦ-MWW > образец № 2 > образец № 1 > образец № 4. Это свидетельствует об уменьшении силы кислотных центров для экспериментальных образцов в указанной последовательности.
Интересным оказывается влияние каолина на кислотные свойства экспериментальных образцов. Как показывают данные табл. 2, добавки каолина к Al(OH)3 приводят к уменьшению концентрации кислотных центров в образцах № 2 и № 3, тогда как добавки каолина к силиказолю приводят к увеличению концентрации кислотных центров образцов № 4 и № 5. Сопоставление профилей ТПД экспериментальных образцов (рис. 5) показывает, что в случае Al(OH)3 снижение кислотности происходит за счет слабых кислотных центров, что следует из уменьшения интенсивности низкотемпературного максимума (рис. 5а). В случае SiO2 увеличение концентрации кислотных центров происходит за счет прироста сильных центров, на что указывает увеличение интенсивности высокотемпературного пика (рис. 5б).
Таким образом, использование связующих веществ различных типов позволяет регулировать в широком диапазоне прочностные, текстурные и кислотные характеристики экспериментальных образцов.
Таким образом, использование связующих веществ различных типов позволяет регулировать в широком диапазоне прочностные, текстурные и кислотные характеристики экспериментальных образцов.
Как следует из результатов проведенных каталитических экспериментов (рис. 6–8) по алкилированию бензола пропиленом, исследованные образцы можно условно разбить на три группы, которые существенно отличаются по своим показателям. В первую группу входит один образец № 2, который по всем основным показателям (выход кумола, конверсия бензола и селективность по кумолу) проявляет высокую стабильность во времени. Во вторую группу входят образцы № 1, 3, показатели которых по сравнению с образцом № 2 менее стабильны во времени, однако снижение происходит достаточно плавно. Третья группа состоит из двух образцов № 4 и 5, показатели которых во времени резко снижаются. Полученные зависимости позволяют сделать вывод о том, что конверсия бензола определяется количеством кислотных центров в образцах.
Рис. 6.
Зависимость выхода кумола от продолжительности опыта: 1 – образец № 2, 2 –образец № 1, 3 – образец № 3, 4 – образец № 5, 5 – образец № 4.
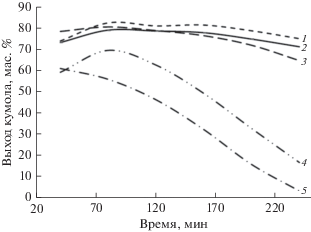
Рис. 7.
Зависимость селективности по кумолу от продолжительности опыта: 1 – образец № 1, 2 – образец № 2, 3 – образец № 3, 4 – образец № 5, 5 – образец № 4.
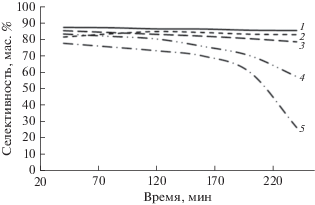
Рис. 8.
Зависимость конверсии бензола от продолжительности опыта: 1 – образец № 2, 2 – образец № 1, 3 – образец № 3, 4 – образец № 5, 5 – образец № 4.
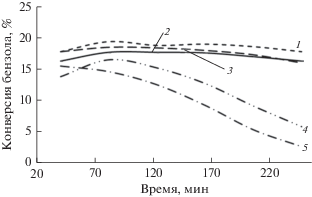
Полученные результаты испытаний, проведенных на лабораторной проточной установке, позволяют сделать вывод, что лучшим по активности и стабильности из исследованных катализаторов в реакции алкилирования бензола пропиленом является образец № 2 со следующими средними показателями: выход кумола – 78.8%; селективность по кумолу – 83.3%; конверсия бензола –18.7%.
ЗАКЛЮЧЕНИЕ
На основании полученных результатов можно сделать вывод, что результаты каталитических испытаний достаточно четко коррелируют с кислотностью экспериментальных образцов. Использование Al(OH)3 отечественного производства в качестве прекурсора для Al2O3 не влияет негативно на кислотные свойства катализатора, что в свою очередь поддерживает высокий выход целевого продукта реакции. Добавление каолина в этот катализатор не влияет прочностные характеристики, но снижает кислотность и, как следствие, выход кумола падает.
БЛАГОДАРНОСТИ
Работа выполнена при финансовой поддержке Министерства науки и высшего образования Российской Федерации (уникальный идентификатор прикладных научных исследований RFMEFI60717X0167).
Список литературы
Perego C., Ingallina P. // Catalysis Today. 2002. V. 73. № 3. P. 3.
Degnan T.F., Jr., Morris Smith C., Venkat Chaya R. // Applied Catalysis A: General. 2001. V. 221. № 283. P. 283.
Corma A., Martinez-Soria V., Schnoeveld E. // J. Catal. 2000. V. 192. P. 163.
Пономарева О.А., Князева Е.Е., Шкуропатов А.В., Иванова И.И., Герзелиев И.М., Хаджиев С.Н. // Нефтехимия. 2017. Т. 57. № 6. С. 769 [Petrol. Chemisrty. 2017. V. 57. № 6. Р. 754].
Ivanova I. I., Knyazeva E. E. // Chem. Soc. Rev. 2013. V. 42. P. 3671.
Dıáz U., Fornes V., Corma A. // Micropor. Mesopor. Mater. 2006. V. 90. № 1–3. P. 73.
Герзелиев И.М., Остроумова В.А., Жмылев В.П., Хаджиев С.Н. // Журнал прикладной химии. 2018. Т. 87. № 6. С. 832.
Дополнительные материалы отсутствуют.