Нефтехимия, 2019, T. 59, № 4, стр. 423-427
Влияние химического состава цеолитных катализаторов на их каталитические свойства в реакции алкилирования изобутана бутиленами
И. М. Герзелиев 1, *, В. А. Темникова 1, О. В. Денискин 1, М. Н. Басханова 1, Д. О. Хусаимова 1, А. Л. Максимов 1
1 Институт нефтехимического синтеза им. А.В. Топчиева РАН
Москва, Россия
* E-mail: gerzeliev@ips.ac.ru
Поступила в редакцию 11.03.2019
После доработки 13.03.2019
Принята к публикации 14.03.2019
Аннотация
Представлены результаты исследований по влиянию химического состава цеолитных катализаторов в CaLaHХ форме на их каталитические свойства в реакции алкилирования изобутана бутиленами. Установлены оптимальные концентрации оксидов металлов (в мас. %: Na 0.5, Ca – 0.6, La – 18.3), при которых конверсия бутиленов находится в пределах 97–100 мас. %, выход алкилата близок к теоретическому (95–100 мас. %), селективность по триметилпентанам (ТМП) находится на уровне 73 мас. %. Наблюдается достаточно четкая корреляция между оптимальным химическим составом образцов катализаторов с их кислотностью, определенной по термодесорбции аммиака.
В основе процесса получения высокооктанового компонента бензина – изооктана, придающего высокую стабильность и детонационную стойкость товарному бензину, лежит реакция алкилирования изобутана бутиленами с получением алкилата, не содержащего ароматических углеводородов (УВ) и сернистых соединений [1]. В промышленности процесс проводят на катализаторах (серная и фтористоводородная кислота), оказывающих негативное воздействие на окружающую среду и требующих дополнительного оборудования для хранения свежих и отработанных кислот, блоков разделения продуктов реакции от кислот и так далее [2]. Альтернативой кислотам являются безопасные твердые катализаторы, в частности на основе цеолитов типа FAU в катионзамещенной форме [3, 4]. Известно, что высокую активность и селективность показывают катализаторы на основе цеолита, если степень замещения натрия в последнем составляет не менее 98%, а в составе содержатся катионы кальция и редкоземельных элементов [3, 5, 6]. Большинство исследований последних лет базируются на использовании катализаторов на основе цеолита Y [7].
Вместе с тем, в отечественной промышленности освоено производство цеолитов типа Х, гранулированных без связующих веществ [2]. Использование таких цеолитов в качестве основы для катализаторов представляется перспективным направлением, поэтому нами была поставлена работа и проведены исследования по определению влияния содержания оксидов натрия, кальция и лантана в составе катализаторов алкилирования изобутана бутиленами, синтезированных на основе цеолита типа Х, гранулированных без связующих веществ.
ЭКСПЕРИМЕНТАЛЬНАЯ ЧАСТЬ
Методика проведения ионного обмена
Для проведения ионного обмена использовали одинаковую по массе навеску цеолита NaX российского производства, гранулированного без связующих (мольное соотношение Si/Al = 1.6, содержание оксида натрия – 16.5 мас.%) в расчете на абсолютно сухое вещество. Ионный обмен проводили во вращающемся автоклаве (1 об./с), при температуре 155°С, в течении 6 ч. В качестве солей металлов использовали нитраты кальция, лантана и аммония. Массовое соотношение раствор/гранулы = 8 :1. Прокаливание образцов катализатора осуществляли после последнего ионного обмена (1.5 ч при 300°C и 2.5 ч при 450°C).
Физико-химические методы исследования образцов катализаторов
Анализ химического состава проводили с использованием рентгенофлуоресцентного спектрометра ARL PERFORM’X 2500 (ThermoFisherScientific). Перед анализом образцы катализатора навеской 200 мг прессовали в таблетку с борной кислотой.
Кислотные свойства определяли методом термопрограммируемой десорбции (ТПД) аммиака на приборе ChemiSorb 2750 фирмы Micromeritics. Образцы катализатора помещали в кварцевый реактор и обрабатывали в токе гелия при 500°С в течение 1 ч. В токе осушенного аммиака, разбавленного азотом, при температуре 60°С проводили насыщение образцов в течение 15 мин. Удаление физически адсорбированного аммиака вели при 100°С в токе сухого гелия (скорость подачи 30 см3/мин) в течение 1 ч, после чего образцы охлаждали до 60°С. Для получения кривой ТПД образцы нагревали со скоростью 8 град/мин до 800°С в токе гелия (30 см3/мин). Обработку полученных данных проводили с помощью программ ChemiSoftTPx и Origin 60. Для проведения анализа использовали образцы катализатора фракций 0.5–0.25 мм, масса навески 0.1 г.
Исследование каталитических свойств катализаторов осуществляли на лабораторной проточной установке алкилирования изобутана бутиленами со стационарным слоем катализатора в режиме “АСР” (алкилирование в “структурированном” режиме) по методу, описанному в [1, 2, 8].
РЕЗУЛЬТАТЫ И ИХ ОБСУЖДЕНИЕ
Было синтезировано три серии образцов катализаторов. В первой серии изменяли содержание оксида натрия (0.3–2.1 мас. %), при относительно постоянном количестве кальция CaO – 0.6 мас. % и лантана La2O3 – 18.6 мас. %. Во второй серии изменяли содержание оксида кальция (0.5–1.3 мас. %), при относительно постоянном количестве натрия Na2O – 0.6 мас. % и лантана La2O3 – 18.6 мас. %. В третьей – изменяли содержание оксида лантана (13–21 мас. %), при относительно постоянном количестве кальция CaO – 0.6 мас. % и натрия Na2O – 0.6 мас. %.
Критериями для сравнительной оценки активности катализаторов служило достижение следующих показателей: активность, конверсия бутиленов – максимум 100 мас. % и выход алкилата от бутиленов в сырье от теоретического максимума 204 мас. %; селективность, содержание в алкилате – триметилпентаны (ТМП) – максимум 100 мас. %; диметилгексаны (ДМГ) – минимум 0 мас. %; С8‑прочие – минимум 0 мас. %; суммарное содержание УВ, выкипающих выше изооктановой фракции (∑C9+) – минимум 0 мас. %.
Результаты исследований представлены ниже.
Как следует из рис. 1 изменение количества оксида натрия в образцах катализатора алкилирования в пределах 0.5–0.8 мас. % практически не сказывается на показателях реакции (рис. 1а), которые находятся в следующих пределах, мас. %: конверсия – 99–100, выход алкилата – 99.5–100.0, селективность по ТМП – 69.4–72.6, образование тяжелых продуктов реакции С9+ – не выше 7, С8-прочие – не более 2.15. Необходимо отметить некоторое падение показателей процесса при снижении содержания Na2O с 0.5 до 0.4 мас. %, синхронное со снижением общей кислотности сильных кислотных центров (КЦ) и увеличениeм кислотных центров средней силы (рис. 1а). Полученный эффект вероятно связан с тем, что дополнительные операции ионного обмена, необходимые для достижения пониженных значений оксида натрия, приводят к снижению степени кристалличности на 10%, а также с переходом сильных КЦ, в средние КЦ.
Рис. 1.
Каталитические показатели реакции алкилирования изобутана бутиленами в зависимости от содержания оксидов натрия в катализаторе: (а) конверсия (×), выход алкилата (▲), селективность по триметилпентанам (⚫), С8-прочим (–), ΣС9+ (◆), а также концентрация КЦ – сумма КЦ (◼), средние КЦ (×|) и сильные КЦ (+); (б) селективность по индивидуальным ТМП; (в) селективность по ДМГ.
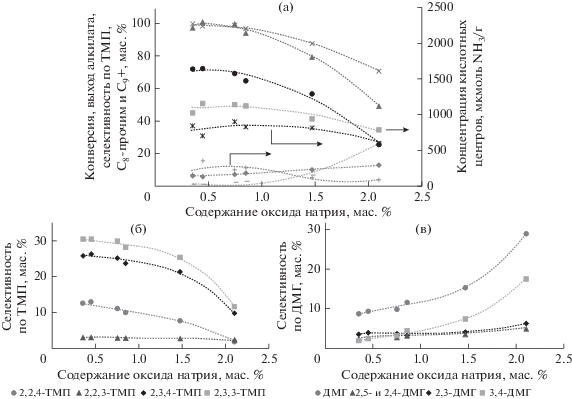
Как видно из рис. 1б увеличение степени ионного обмена натрия приводит к уменьшению количества высокооктановых компонентов (2,2,4-ТМП – ОЧИМ (октановое число исследовательским методом) 100.0; 2,3,3-ТМП – ОЧИМ 102.9; 2,3,4-ТМП – ОЧИМ 101.3). Существенное снижение качества продуктов и показателей процесса алкилирования происходит при увеличении остаточного содержания Na2O выше 1.00 мас. %: конверсия опускается до 77 мас. %, выход алкилата от бутиленов в сырье – до 49.5 мас. %, селективность по ТМП – до 25.8 мас. % (рис. 1б), снижается количество высокооктановых УВ, соответственно (рис. 1в) наблюдается рост побочных продуктов, таких как 2,5- и 2,4-ДМГ (диметилгексаны) – ОЧИМ 55.5 и 65.2 соответственно, 2,3-ДМГ – ОЧИМ 71.3 и 3,4-ДМГ – ОЧИМ 76.3, образование значительного количества УВ, выкипающих выше изооктановой фракции ΣС9+ до 12.8 мас. %, а содержание С8-прочие – до 27.3 мас. %. Указанные закономерности коррелируются снижением как сильных, так и средних КЦ. Оптимальная концентрация оксида натрия находится в пределах 0.5 мас. % (концентрация оксидов кальция и лантана при этом составляет 0.6 и 18.3 мас. %, соответственно), при котором наблюдаются самые лучшие показатели (конверсия 99 мас. %, выход алкилата 100.0 мас. %, селективность по ТМП – 72.6 мас. %, ΣС9+ – 5.8 мас. %); этим условиям соответствует и максимальное значение сильных кислотных центров.
Результаты исследований второй серии катализаторов с изменением содержания оксида Са представлены на рис. 2.
Рис. 2.
Каталитические показатели реакции алкилирования изобутана бутиленами в зависимости от содержания оксидов кальция в катализаторе: (а) конверсия (×), выход алкилата (▲), селективность по триметилпентанам (⚫), С8-прочим (–), ΣС9+ (◆), а также концентрация КЦ – сумма КЦ (◼), средние КЦ (×|) и сильные КЦ (+); (б) селективность по индивидуальным ТМП; (в) селективность по ДМГ.
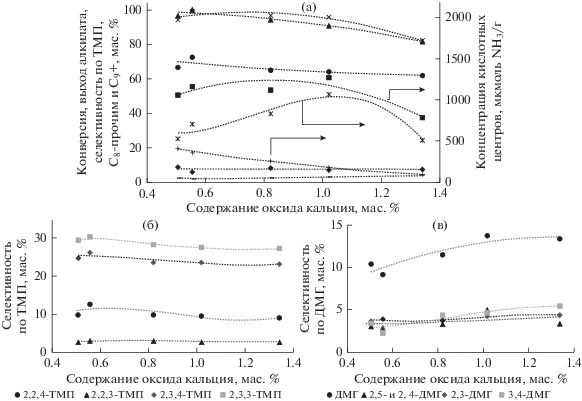
Как можно видеть из рис. 2а показатели имеют оптимум при значениях оксида кальция в районе 0.6 мас. %, при котором конверсия составляет – 99 мас. %, выход алкилата – 100.0 мас. %, селективность по ТМП 72.6 мас. %, причем выходы высокооктановых УВ, таких как 2,2,4-ТМП, 2,3,3-ТМП и 2,3,4-ТМП, достигают своего пика (рис. 2б), в то время как образование менее ценных ДМГ (3,4-, 2,5- и 2,4-ДМГ) понижается (рис. 2в). Увеличение количества оксида Са в образцах катализаторов алкилирования в пределах от 0.6 до 1.0 мас. % практически не сказывается на показателях, которые находятся в оптимальных пределах: конверсия 95–99 мас. %, выход алкилата – 94.6–100.0 мас. %, селективность по ТМП – 64.9–72.6 мас. %. При дальнейшем увеличении количества оксида кальция до 1.3 мас. % наблюдается плавное снижение качества продуктов и показателей процесса: конверсии бутиленов до 83 мас. %, выхода алкилата до 81.9 мас. %, селективности по ТМП до 62.2 мас. %, а содержание С8-прочие до 4.2 мас. %, которые являются вероятно следствием снижения количества сильных и средних кислотных центров. На рис. 2б и 2в показано, что при увеличении концентрации оксидов кальция наблюдается снижение количества высокооктановых УВ (ТМП) в продуктах и увеличение на 5 мас. % ДМГ. При уменьшении CaO с 0.6 до 0.5 мас. % наблюдается снижение конверсии с 99 до 95 мас. %, выхода алкилата со 100.0 до 97.1 мас. %, селективности по ТМП с 72.6 до 67.2 мас. %, повышение С8-прочие с 1.4 до 2.1 мас. %, ΣС9+ с 5.8 до 8.7 мас. %; при этом данные результаты коррелируются со снижением количества средних КЦ (рис. 2а). Полученные результаты могут свидетельствовать о том, что кальций в образцах является стабилизирующим катионом, необходимым для удаления натрия из труднодоступных участков цеолита в ходе ионных обменов. Оптимальное количество оксида кальция в образцах составляет 0.6 мас. %.
Полученные каталитические показатели образцов катализаторов третьей серии с разным содержанием оксида La представлены на рис. 3.
Рис. 3.
Каталитические показатели реакции алкилирования изобутана бутиленами в зависимости от содержания оксидов натрия в катализаторе: (а) конверсия (×), выход алкилата (▲), селективность по триметилпентанам (⚫), С8-прочим (–), ΣС9+ (◆), а также концентрация КЦ – сумма КЦ (◼), средние КЦ (×|) и сильные КЦ (+); (б) селективность по индивидуальным ТМП; (в) селективность по ДМГ
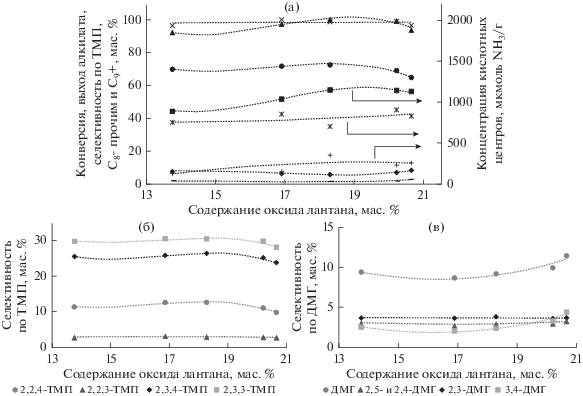
Изменение количества оксида лантана в образцах катализатора алкилирования (рис. 3а) с 16.9 до 20.2 мас. % практически не сказывается на показателях, которые находятся в следующих пределах: конверсия 99–100 мас. %, выход алкилата – 97.5–100.0 мас. %, селективность по ТМП – 69.4–72.6 мас. %, образование тяжелых продуктов реакции С9+ не превышает 7 мас. %. Следует отметить, что повышение количества оксида лантана выше 18.6 мас. %, при котором наблюдается максимальное значение концентраций сильных КЦ (рис. 2а), а выход алкилата достигает 100 мас. % приводит к некоторому ухудшению качества алкилата за счет увеличения количества УВ фракции ДМГ (рис. 3в), с соответствующим снижением селективности по ТМП (рис. 3а, б) и конверсии по бутиленам. При снижении количества оксида лантана в образце катализатора с 16.9 до 13.8 мас. % и увеличении с 20.2 до 20.5 мас. % также наблюдается некоторое ухудшение качества алкилата за счет увеличения количества более тяжелых УВ фракции С9+ и С8-прочие (рис. 3в), с соответствующим снижением селективности по ТМП (рис. 3б) и конверсии по бутиленам. Оптимальная концентрация оксида лантана находится в пределах 18.6 мас. % (концентрация оксидов натрия и кальция при этом составляет по 0.6 мас. %), при которой наблюдаются самые лучшие показатели (конверсия 99 мас. %, выход алкилата 100.0 мас. %, селективность по ТМП – 72.7 мас. %, ΣС9+ – 5.8 мас. %); этим условиям соответствует и максимальное значение сильных КЦ.
Таким образом, для получения качественного продукта и оптимальных показателей процесса алкилирования изобутана бутиленами необходимо использовать катализаторы, в которых количество оксида Na находится в пределах 0.4–0.8 мас. % (оптимально 0.5 мас. %), оксида Ca – 0.5–1.0 мас. % (оптимально 0.6 мас. %), а содержание оксида La – от 16.9 до 20.2 мас. % (оптимально 18.3 мас. %), при которых конверсия бутиленов находится в пределах 97–100 мас. %, выход алкилата – 95–100 мас.%, высокая селективность по триметилпентанам находится на уровне 73 мас. %. Наблюдается достаточно четкая корреляция между оптимальным химическим составом образцов катализаторов и их кислотностью по термодесорбции аммиака.
БЛАГОДАРНОСТИ
Работа проведена при финансовой поддержке Министерства науки и высшего образования Российской Федерации (Соглашение № 14.607.21.0170, уникальный идентификатор прикладных научных исследований RFMEFI60717X0170).
Список литературы
Герзелиев И.М., Цодиков М.В., Хаджиев С.Н. // Нефтехимия. 2009. Т. 49. № 1. С. 3 [Petrol. Chemistry. 2009. V. 49. № 1. P. 59].
Хаджиев С.Н., Герзелиев И.М., Окнина Н.В., Кузьмин А.Е., Саитов З.А. // Патент РФ № 2637 922. 2016.
Хаджиев С.Н., Герзелиев И.М., Ведерников О.С., Клейменов А.В., Кондрашев Д.О., Окнина Н.В., Кузнецов С.Е., Саитов З.А., Басханова М.Н. // Катализ в промышленности. 2016. Т. 6. С. 42.
Liu Ch., van Santen R.A., Poursaeidesfahani A., Vlugt Th.J.H., Pidko E.A., Hensen E.J.M. // American Chemical Society: Catalysis. 2017. V. 7. P. 8613.
Zhuang Y., Ng F.T.T. // Appl. Catal. A: Gen. 2000. V. 190. № 1–2. P. 137.
Рабо Д. Химия цеолитов и катализ на цеолитах. М: Мир, 1980. 420 с.
Chen Zh., Gao F., Ren K., Wu Q., Luo Yan., Zhou H., Zhang M., Xu Q. // Royal Society of Chemistry: Advances. 2018. V. 8. P. 3392.
Герзелиев И.М., Остроумова В.А., Басханова М.Н., Саитов З.А., Темникова В.А., Хусаимова Д.О. // Нефтехимия. 2017. Т. 57. № 6. С. 205 [Petrol. Chemistry. 2017. V. 57. № 12. P. 1182].
Дополнительные материалы отсутствуют.