Нефтехимия, 2019, T. 59, № 5, стр. 524-528
Глубокая очистка вакуумного газойля методом окислительного обессеривания
А. В. Акопян *, Д. А. Плотников, П. Д. Поликарпова, А. А. Кедало, С. В. Егазарьянц, А. В. Анисимов, Э. А. Караханов
Московский государственный университет имени М.В. Ломоносова, Химический факультет
119991 Москва, Россия
* E-mail: arvchem@yandex.ru
Поступила в редакцию 21.02.2019
После доработки 12.04.2019
Принята к публикации 13.05.2019
Аннотация
Исследована возможность применения каталитической системы на основе муравьиной кислоты и соли переходного металла в присутствии пероксида водорода для обессеривания негидроочищенного вакуумного газойля. Подобраны условия эффективного окисления сероорганических соединений и максимального извлечения окисленных соединений из сырья. Показано, что катализаторы на основе солей вольфрама являются наиболее эффективными катализаторами окислительного обессеривания тяжелого сырья. В оптимальных условиях степень обессеривания вакуумного газойля составила 89%.
В современном мире постоянно ужесточаются требования к сырью, поступающему на переработку, а также вводятся экологические стандарты для выпускаемых топлив [1, 2], при этом содержание сероорганических веществ в добываемом сырье непрерывно растет, что ведет к ухудшению его качества. Для снижения выбросов оксидов серы, образующихся в процессе сжигания сернистых соединений, в атмосферу и нейтрализации отравляющего действия серы на катализаторы процессов нефтепереработки необходимо удалять сероорганические соединения из углеводородного сырья [3, 4]. В связи с этим проблема обессеривания как легких, так и тяжелых нефтяных фракций является актуальной.
В настоящее время существует ряд методов, направленных на удаление сероорганических соединений из тяжелых фракций: гидроочистка, биодесульфуризация, экстракционные методы, акватермолиз и окислительное обессеривание [5–9]. Одним из наиболее распространенных процессов является каталитическая гидроочистка, в которой сернистые соединения разрушаются с образованием сероводорода и углеводородной части, которая сохраняется в составе целевых жидких продуктов [10, 11]. При этом использование гидроочистки для обессеривания тяжелых нефтяных фракций сопряжено с большим расходом водорода и жесткими условиями, что ведет к удорожанию процесса [12]. Альтернативными доступными способами удаления сероорганических соединений из тяжелого нефтяного сырья являются окислительное обессеривание, адсорбция, экстракция и биодесульфуризация [6, 13, 14]. Наиболее эффективный способ безводородного обессеривания тяжелых нефтяных фракций включает в себя окисление сернистых соединений с последующим их извлечением методом экстракции или адсорбции [5, 15]. В качестве окислителей чаще всего используют пероксид водорода, поскольку он является экологичным окислителем [16]. В качестве катализаторов окислительного обессеривания хорошо зарекомендовали себя соли переходных металлов, таких как молибден и вольфрам, т.к. в присутствии пероксида водорода они способны образовывать активные в окислении сернистых соединений пероксокомплексы [17, 18].
ЭКСПЕРИМЕНТАЛЬНАЯ ЧАСТЬ
В качестве сырья в работе был использован вакуумный газойль (ВГ) московского НПЗ с содержанием общей серы 14 800 ppm, а также следующие реактивы: (NH4)2MoO4 (ч. д. а., PrimeChemicalsGroup), пероксид водорода (37%, PrimeChemicalsGroup), (NH4)2WO4 (ч. д. а., PrimeChemicalsGroup), VOSO4 (ч. д. а., PrimeChemicalsGroup), муравьиная кислота концентрированная, плотность 1.22 г/см3 (х. ч.), ацетон (ч., Компонент-Реактив), Неонол АФ 9-6 (Нижнекамскнефтехим), тетрабутиламмония бромид (ТБАБ, SigmaAldrich), диметилформамид (х. ч., Компонент-Реактив), ацетонитрил (х. ч., Компонент-Реактив), N-метилпирролидон (х. ч., Компонент-Реактив), вода дистиллированная (ГОСТ 6709).
Определение содержания общей серы в углеводородных фракциях проводили на рентгено-флуоресцентном анализаторе серы СПЕКТРОСКАН SL с относительной погрешностью 3% в диапазоне определяемых концентраций от 7 ppm до 5000 ppm по ASTMD 4294-10 [19]. Принцип действия прибора основан на методе рентгенофлуоресцентной энергодисперсионной спектрометрии, являющемся арбитражным методом определения массовой доли серы в дизельном топливе и допустимым методом определения массовой доли серы в неэтилированном бензине.
Приготовление каталитической смеси. В 1.3 мл дистиллированной воды растворяли 0.0018 моль соли переходного металла ((NH4)2MoO4, (NH4)2WO4, VOSO4), смесь перемешивали в течение 5 мин, добавляли 6.5 мл муравьиной кислоты и перемешивали еще 3 мин. Затем к полученному раствору добавляли 0.2 г неонола АФ 9-6 и 0.1 г ТБАБ и продолжали перемешивание в течение 20 мин.
Обессеривание вакуумного газойля. В реактор, снабженный магнитной мешалкой, добавляли 20 мл вакуумного газойля, необходимое количество 37%-ного пероксида водорода и приготовленной каталитической смеси, исходя из мольных соотношений Н2О2 : S от 2 : 1 до 10 : 1 и НСООН : S = 1 : 1 и 10 : 1. Реакцию проводили при 40–80°С в течение 2–12 ч. После окончания окисления реакционную смесь промывали 20 мл дистиллированной воды для удаления остатков каталитической окислительной системы. Далее окисленный вакуумный газойль экстрагировали 20-ю мл полярного растворителя (диметилформамид, N-метилпирролидон, ацетонитрил) при температуре 20–120°С. Очищенный от сернистых соединений вакуумный газойль анализировали на содержание серы.
РЕЗУЛЬТАТЫ И ИХ ОБСУЖДЕНИЕ
В качестве объекта исследования использовали негидроочищенный вакуумный газойль с исходным содержанием серы 14 800 ppm.
Поскольку вакуумный газойль является тяжелым сырьем и содержит большое количество ароматических соединений, затрудняющих процесс адсорбции, окисленные сернистые соединения извлекали методом экстракции полярным растворителем. В качестве экстрагентов окисленных сернистых соединений чаще всего используют диэтиленгликоль, этанол, диметилформамид, ацетонитрил, N-метилпирролидон, фурфурол [20]. В связи с тем, что тяжелым нефтяным фракциям свойственна высокая вязкость при комнатной температуре и существует необходимость проводить экстракцию при повышенной температуре, были выбраны экстрагенты с высокой температурой кипения: ДМФА – 153°С, N-метилпирролидон – 202°С, ацетонитрил – 82°С.
Влияние природы экстрагента и температуры экстракции. Влияние природы экстрагента и температуры экстракции на степень обессеривания проводили на образце вакуумного газойля, окисленного в избытке каталитической окислительной системы. Для полного протекания реакции окисление проводили при высоком избытке пероксида водорода и муравьиной кислоты при ступенчатом нагреве (1 ч – 40°С, 5 ч – 60°С). Результаты приведены на рис. 1.
Рис. 1.
Влияние природы экстрагента и температуры экстракции на степень обессеривания вакуумного газойля. Условия: H2O2 : S = 20 : 1; HCOOH : S = 10 : 1 (мольн.); всего 6 ч, в том числе: 1 ч – 40°С, 5 ч – 60°С.
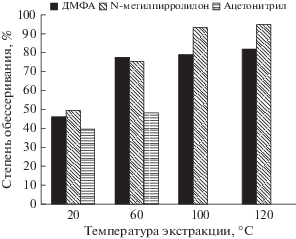
Как видно из рис. 1, максимальное извлечение сернистых соединений происходит при температуре экстракции, равной 120°С. При этом наилучшие результаты в ходе экстракции получены для N-метилпирролидона. В связи с этим в дальнейшей работе в качестве экстрагента был выбран N-метилпирролидон.
Влияние природы переходного металла и температуры реакции. Реакция окисления сероорганических соединений вакуумного газойля пероксидом водорода проходит на границе водной и углеводородной фаз, что создает диффузионные ограничения при протекании реакции. Для снижения диффузионных ограничений в реакционную смесь добавляют межфазный переносчик, для улучшения эмульгирования водной фазы – поверхностно-активные вещества (ПАВ). В предложенной работе в качестве ПАВ был использован неонол АФ 9-6 и бромид тетрабутиламмония – в качестве межфазного переносчика. Известно, что кислая среда способствует окислению сернистых соединений [14], поэтому в качестве кислотного агента была выбрана муравьиная кислота, зарекомендовавшая себя в окислении легких нефтяных фракций [13].
Исследование влияния температуры на степень обессеривания ВГ проводили с использованием в качестве катализатора солей переходных металлов, способных образовывать пероксокомплексы в присутствии пероксида водорода (молибден, вольфрам, ванадий). Температурный режим варьировали в интервале 40–80°С. При этом использовали программируемый нагрев реакции (1 ч проводили окисление при 40°С, далее нагревали до заданной температуры). Использование постепенного нагрева реакционной смеси обусловлено тем, что в присутствии переходных металлов возможно разложение пероксида водорода при высокой температуре. При 40°С происходит окисление легких сернистых соединений и частично расходуется пероксид водорода, дальнейшее поднятие температуры способствует окислению трудноокисляемых сероорганических соединений. Из полученных результатов, представленных на рис. 2, видно, что наиболее эффективным катализатором является вольфрамат аммония в температурном режиме 40–60–80°С (1 ч – 40°С, 1 ч – 60°С, 4 ч – 80°С).
Рис. 2.
Влияние природы переходного металла и температуры реакции на степень обессеривания вакуумного газойля. Условия: H2O2 : S = 4 : 1; HCOOH : S = = 1 : 1 (мольн.), 6 ч.
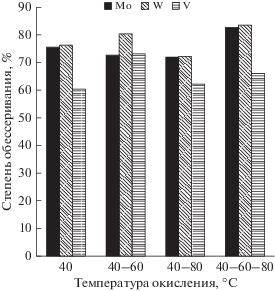
Влияние времени проведения реакции. Время окисления варьировали в интервале 2–12 ч. Полученные результаты представлены на рис. 3. Согласно полученным данным, за 6 ч проходит максимальное окисление сернистых соединений, присутствующих в вакуумном газойле. Дальнейшее окисление не приводит к увеличению степени обессеривания.
Рис. 3.
Влияние времени проведения окисления на степень обессеривания вакуумного газойля на катализаторе (NH4)2WO4. Условия: H2O2 : S = 4 : 1; HCOOH : S = 1 : 1 (мольн.), всего 6 ч, в том числе: 1 ч – 40°С, 1 ч – 60°С, 4 ч – 80°С.
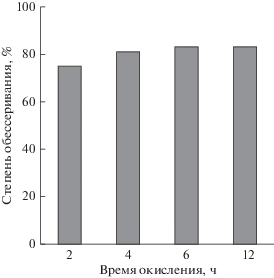
Влияние количества окислителя. Исследование влияния количества пероксида водорода на степень обессеривания проводили в интервале мольных соотношений H2O2 : S от 2 : 1 до 10 : 1. Избыток добавляемого окислителя необходим в связи с тем, что возможно частичное разложение пероксида водорода в ходе реакции.
Как видно из рис. 4, увеличение избытка пероксида водорода по отношению к сере от 6 : 1 до 10 : 1 не ведет к значительному улучшению степени обессеривания. С целью минимизации расхода пероксида водорода в дальнейшей работе был использован шестикратный избыток окислителя.
Рис. 4.
Влияние количества пероксида водорода на степень обессеривания вакуумного газойля на катализаторе (NH4)2WO4. Условия: HCOOH : S = 1 : 1 (мольн.), всего 6 ч, в том числе: 1 ч – 40°С, 1 ч – 60°С, 4 ч – 80°С.
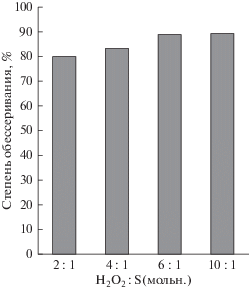
Влияние количества каталитической смеси на основе муравьиной кислоты и вольфрамата аммония. Исследование влияния количества катализатора на степень обессеривания ВГ проводили в интервале массовых соотношений катализатор : сера от 1.5 до 5.5 мас. %. Как видно из рис. 5, уменьшение количества муравьиной кислоты незначительно сказывается на степени обессеривания вакуумного газойля.
Рис. 5.
Влияние количества катализатора на степень обессеривания вакуумного газойля. Условия: H2O2 : : S = 6 : 1 (мольн.), 1 ч – 40°С, 1 ч – 60°С, 4 ч – 80°С; катализатор – (NH4)2WO4.
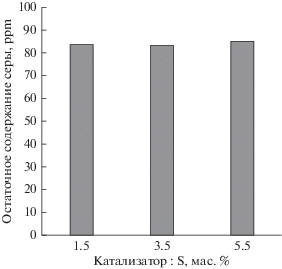
Для анализа влияния окисления на физико-химические характеристики вакуумного газойля была проведена вакуумная дистилляция и измерены такие показатели, как плотность и кинематическая вязкость. Результаты приведены в табл. 1 .
Таблица 1.
Физико-химические показатели вакуумного газойля
Вакуумный газойль | Плотность, г/см3 | Вязкость кинематическая, сСт | Содержание серы, мас. % | Фракционный состав | |||
---|---|---|---|---|---|---|---|
НК, °С | 10%, °С | 50%, °С | КК, °С | ||||
До окисления | 0.904 | 7.1 | 1.48 | 346 | 390 | 442 | 532 |
После окисления | 0.910 | 7.2 | 0.13 | 342 | 387 | 440 | 536 |
Как видно из табл. 1 , окисление вакуумного газойля не сказывается отрицательно на его физико-химических показателях, что свидетельствует о возможности применения данного метода для обессеривания тяжелых фракций.
Таким образом, в результате проделанной работы были подобраны оптимальные условия окислительного обессеривания вакуумного газойля: общее время реакции – 6 ч, 1 ч – 40°С, 1 ч – 60°С, 4 ч – 80°С, (NH4)2WO4, H2O2 : S = 6 : 1 (мольн.) и HCOOH : S = 1 : 2 (мольн.), экстрагент N-метилпирролидон при температуре экстракции 100°С.
Работа выполнена при финансовой поддержке Министерства высшего образования и науки РФ в рамках ФЦП “Исследования и разработки по приоритетным направлениям развития научно-технологического комплекса России на 2014–2020 гг.” мероприятие 1.3, Соглашение о предоставлении субсидии № 14.607.21.0173 от 26.09.2017. Уникальный идентификатор прикладных научных исследований RFMEFI60717X0173.
Список литературы
Технический регламент № 609 “О требованиях к выбросам автомобильной техникой, выпускаемой в обращение на территории РФ, вредных (загрязняющих) веществ”.
Рудякова Е.В. // Система оценки качества топлива, масел и специальных жидкостей. Иркутск: Изд-во Иркутского гос. техн. университета, 2013. 56 с.
Анисимов А.В., Тараканова А.В. // Журн. Рос. общ-ва им. Д.И. Менделеева. 2008. Т. LII. № 4. С. 32.
Dunleavy J.K. // Platinum Metals Review. 2006. V. 50. P. 110.
Javadli R., de Klerk A. // Appl. Petrochem. Res. 2012. № 1. P. 3.
Babich I.V., Moulijn J.A. // Fuel. 2003. V. 82. P. 607.
Campos-Martin J.M., Capel-Sanchez M.C., Perez-Presas P., Fierro J.L.G. // Chem. Technology and Biotechnology. 2010. V. 86. № 7. P. 879.
Eber J., Wasserscheid P., Jess A. // Green Chem. 2004. V. 6. P. 316.
LiY., Li Q., Wang X., Yu L., Yang J. // Petroleum Science. 2018. V. 15. P. 613.
Nadeina K.A., Klimov O.V. // Catalysis Today. 2016. V. 271. P. 4.
Rodriguez E., Felix G., Ancheyta J., Trejo F. // Fuel. 2018. V. 225. P. 118.
Xiaoliang M., Lu S., Chunshan S. // Catalysis Today. 2002. V. 77. P. 107–116.
Akopyan A.V., Ivanov E.V., Polikarpova P.D., Tarakanova A.V., Rakhmanov E.V., Polyakova O.V., Anisimov A.V., Vinokurov V.A., Karakhanov E.A. // Petrol. Chemistry. 2015. V. 55. № 7. P. 571.
Акопян А.В., Федоров Р.А., Андреев Б.В., Тараканова А.В., Анисимов А.В., Караханов Э.А. // Журн. прикладн. химии. 2018. Т. 91. № 4. С. 457.
Jiang Z., Lü H., Zhang Y., Li C. // Chinese J. of Catalysis. 2011. V. 32. № 5. P. 707.
Zeelani G.G., Ashrafi A., Dhakad A., Gupta G., Pal S.L. // International Research J. of Engineering and Technology. 2015. V. 3. № 5. P. 331.
Ismagilov Z., Yashnik S., Kerzhentsev M., Parmon V., Bourane A. // Catalysis Reviews-Science and Engineering. 2011. V. 53. № 3. P. 199.
Kadijani J.A., Narimani E. // Petroleum & Coal. 2014. V. 56. № 1. P. 116.
ASTM D 4294-10. Standard Test Method for Sulfur in Petroleum and Petroleum Products by Energy Dispersive X-ray Fluorescence Spectrometry.
Ali M.F., Al-Malki A., El-Ali B., Martinie G., Sidd iqui M.N. // Fuel. 2006. V. 85. № 85. P. 1354.
Дополнительные материалы отсутствуют.