Нефтехимия, 2019, T. 59, № 5, стр. 516-523
Оценка активности дисперсных катализаторов в реакциях гидрокрекинга углеводородного сырья
А. Л. Максимов 1, Л. А. Зекель 1, *, М. Х. Кадиева 1, А. М. Гюльмалиев 1, А. У. Дандаев 1, А. Е. Батов 1, М. Я. Висалиев 1, Х. М. Кадиев 1
1 Институт нефтехимического синтеза им. А.В. Топчиева РАН
119991 Москва, Россия
* E-mail: zekel@ips.ac.ru
Поступила в редакцию 05.04.2019
После доработки 27.04.2019
Принята к публикации 13.05.2019
Аннотация
Из обратных эмульсий водных растворов солей молибдена, никеля, железа и вольфрама в присутствии сульфидирующего агента и водорода в вакуумном остатке дистилляции нефти синтезированы концентрированные суспензии наноразмерных частиц – сульфидов молибдена, никеля, железа и вольфрама, которые испытаны в реакциях гидрокрекинга смеси твердого парафина и тяжелого газойля каталитического крекинга (ТГКК). Гидроконверсию проводили в автоклаве при 445°С, давлении водорода 7 МПа. Результаты исследования показали, что каталитическая активность синтезированных катализаторов в реакциях крекинга возрастает в ряду: МоS2, (МоS2 + Ni7S6), Ni7S6, Fe1 – xS, (NH4)0.25 ⋅ WO3.
При переработке тяжелого нефтяного сырья (остатков дистилляции нефти, тяжелых нефтей, природных битумов) все более востребованы процессы полной конверсии сырья в дистилляты без образования остаточного топлива, асфальто-смолистых остатков и кокса. В настоящее время ни одна из промышленных технологий не обеспечивает полную конверсию без образования нежелательных низколиквидных продуктов, таких как мазут и кокс. Присутствие в тяжелом нефтяном сырье (ТНС) термически неустойчивых реакционноспособных компонентов – асфальтенов и смол при термокаталитической переработке приводит к образованию продуктов уплотнения – кокса на поверхности традиционных катализаторов на носителе и их быстрой дезактивации, что обусловливает жесткие ограничения к свойствам исходного сырья. Применение высокодисперсных катализаторов с наноразмерными и субмикронными частицами позволяет достичь значительного прогресса в гидрогенизационной переработке ТНС с высоким содержанием металлов, асфальто-смолистых веществ с получением легких и средних дистиллятов [1–3]. Как наиболее активный катализатор в большинстве исследований для гидроконверсии ТНС использовали суспензии наноразмерных частиц MoS2, формируемые из вводимых в сырье масло- или водорастворимых прекурсоров в процессе гидроконверсии (in situ) [4, 5].
Синтезированный молибденовый катализатор проявляет высокую активность в реакциях гидрирования радикальных фрагментов термической деструкции молекул смол, асфальтенов и, тем самым, предотвращает реакции полимеризации и формирования продуктов уплотнения [6, 7]. Отмечается, что образование дистиллятных продуктов происходит преимущественно в результате термической деструкции молекул сырья, а используемый катализатор участвует в реакции насыщения радикальных фрагментов, образующихся при разрыве связей С–С [8, 9]. В другом исследовании сделан вывод, что МоS2 также активно участвует в разрыве связей С–С [10].
В ряде работ изучали каталитические свойства дисперсных катализаторов на основе соединений никеля, кобальта, железа ванадия, рутения [3, 9, 11–16]. В экспериментах также использовали ТНС (остатки дистилляции нефти, тяжелые нефти) с низким атомным отношением Н/С (1.4–1.5). В большинстве исследований эффективность катализатора в реакциях гидрирования оценивали по количеству поглощенного водорода.
Основная цель применения суспензий высокодисперсных катализаторов при гидрогенизационной переработке ТНС – получение максимального количества дистиллятных фракций при минимальном коксообразовании. Практически не исследована активность дисперсных катализаторов в реакциях гидрокрекинга нефтяного сырья с характерным для парафинов с высоким отношением Н/С. Поэтому целью данной работы стало изучение активности некоторых дисперсных катализаторов в реакциях гидрокрекинга углеводородного сырья.
ЭКСПЕРИМЕНТАЛЬНАЯ ЧАСТЬ
Для оценки крекирующих свойств синтезированных катализаторов целесообразно использовать сырье с высоким содержанием насыщенных углеводородов (УВ) (алканов и циклоалканов). Поскольку гидроконверсия в присутствии дисперсных катализаторов проводится в жидкой фазе, сырье должно иметь высокую температуру кипения. Исходя из рассмотренных условий в качестве сырья использовали очищенный твердый нефтяной парафин марки П2 (табл. 1).
Таблица 1.
Физико-химические свойства сырья гидроконверсии
Свойство | Парафин | ТГКК |
---|---|---|
Плотность, кг/м3 при 20°С | 789 | 1065 |
Коксовое число по Конрадсону, мас. % | – | 2.3 |
Начало кипения, °С | 359 | 175 |
Выкипает (мас. %) при температуре, °С: | ||
5 | 376 | 230 |
10 | 391 | 252 |
20 | 407 | 294 |
30 | 423 | 334 |
50 | 439 | 406 |
90 | 477 | 488 |
Элементный состав, % | ||
С | 86.4 | 86.16 |
Н | 13.6 | 10.1 |
S | – | 3.29 |
N | – | 0.45 |
Н/С, атомное | 1.89 | 1.41 |
Групповой состав, мас. % | ||
Парафино-нафтеновые углеводороды (ПНУВ) | 98 | 14.1 |
Ароматические углеводороды (АУВ), в том числе: | 2 | 76.4 |
легкая ароматика | – | 10.3 |
средняя ароматика | – | 65.0 |
тяжелая ароматика | – | 1.1 |
Смолы (СМ) | – | 7.3 |
Асфальтены (АСФ) | – | 2.2 |
ПНУВ/(СМ + АСФ) | – | 1.48 |
(ПНУВ + АУВ)/(СМ + АСФ) | – | 9.53 |
Для синтеза суспензий наноразмерных катализаторов использовали эмульсионный метод, при котором водные растворы солей металлов эмульгируют в сырье с получением микроэмульсий. Последующие процессы формирования суспензии наноразмерных частиц катализатора – обезвоживание эмульсии, формирование твердой фазы и сульфидирование – протекают при нагревании эмульсии и рассмотрены в работе [17]. Обязательным условием для использования этого метода является присутствие в сырье компонентов, стабилизирующих эмульсии водных растворов прекурсоров. В ТНС эту роль выполняют асфальтены [18]. В нефтяных парафинах такие компоненты отсутствуют. Поэтому суспензии частиц катализаторов синтезировали предварительно (ex situ) в ТНС, содержащем асфальтены. В качестве углеводородной среды для синтеза катализаторов использовали вакуумный остаток дистилляции нефти, характеризующийся плотностью 1011 кг/м3, содержанием смол и асфальтенов 40 мас. %, серы 3.3 мас. %. Синтез проводили на установке, включающей обогреваемый автоклав с перемешивающим устройством и кавитационный диспергатор. К нагретому в автоклаве до 150°С гудрону добавляли сульфидирующий агент – элементную серу в количестве 5 мас. %. После полного растворения серы смесь в автоклаве охлаждали до 80°С. В гудроне, содержащем сульфидирующий агент, эмульгировали водные растворы прекурсоров катализаторов – парамолибдата аммония, вольфрамата аммония, нитрата железа и сульфата никеля с концентрациями солей (%): 23, 9, 43 и 31, соответственно. Соли эмульгировали с использованием кавитационного диспергатора при 80°С, числе оборотов ротора – 10 000 мин–1, длительности – 40 мин. Концентрация водной фазы в эмульсиях составляла 28 мас. %. Дисперсный состав эмульсии определяли микроскопическим методом. Максимумы на кривых распределения капель эмульсии по диаметрам лежали в интервале 1.5–1.9 мкм. Приготовленные эмульсии подвергали ступенчатой термической обработке при постоянном токе водорода, давлении 7 МПа с выдержкой при температуре 360°С 3 ч. В результате термической обработки получали концентрированные суспензии наноразмерных частиц катализаторов, содержащие 1.1–5.4% активных металлов.
Из суспензий экстракцией толуолом выделяли нерастворимую твердую фазу, которую исследовали методами лазерной корреляционной спектроскопии (ЛКС, DLS), рентгеноспектрального флуоресцентного анализа (РСФА, RSFA) , рентгено-дифракционнного анализа (РДА, XRD). Характеристики катализаторов приведены в табл. 2. Как видно из данных таблицы, средние диаметры частиц катализаторов находятся в пределах 273–364 нм. Катализаторы, синтезированные из соединений молибдена, никеля и железа присутствуют преимущественно в форме сульфидов MoS2, Ni7S6 и Fe(1 – x)S. Вольфрамат аммония в условиях синтеза частично разлагался с потерей части аммиака и образованием (NH4)0.25WO3. Для получения сульфида вольфрама из оксидный формы необходима температура выше 600°С [19]. В катализаторе, синтезированном из смеси солей молибдена и никеля, обнаружены фазы индивидуальных сульфидов MoS2 и Ni7S6. Фаз, содержащих оба элемента, не обнаружено.
Таблица 2.
Состав и свойства синтезированных суспензий катализаторов
Активный металл катализатора | Мо | Ni | Fe | W | Мо + Ni* |
---|---|---|---|---|---|
Характеристики суспензии | |||||
Содержание катализатора, в пересчете на металлы, % | 5.4 | 2.7 | 2.2 | 2.2 | 1.1 |
Характеристики твердой фазы | |||||
Средний диаметр частиц, нм | 364 | 274 | 273 | 349 | 302 |
S/Me (атомное) | 3.2 | 1.3 | 2.7 | 0.1 | – |
C/Me (атомное) | 11.6 | 2.5 | 1.5 | 2.4 | – |
Фазовый состав катализаторов | |||||
Неорганическая фаза | MoS2 | Ni7S6 | Fe(1 – x)S | (NH4)0.25 ⋅ WO3 | MoS2 |
Во всех катализаторах присутствует органическое вещество, которое по данным рентгено-фазового анализа (РФА) идентифицировано как твердый парафин. Присутствие парафина в катализаторах может быть связано его низкой растворимостью в толуоле и соосаждением при выделении твердой фазы из гудрона.
В суспензиях катализаторов в гудроне присутствуют асфальтены. При добавлении таких суспензий в расплавленный парафин из-за низких значений параметра растворимости парафина (16–16.5 МПа0.5) будет происходить коагуляция и осаждение асфальтенов. Поэтому для стабилизации суспензий катализатора в парафин был добавлен ТГКК, содержащий около 80% ароматических УВ (значение параметра растворимости – 19.3 МПа0.5). Соотношение парафина и ТГКК составляло 1 : 1 (по массе). Состав ТГКК приведен в табл. 1. Во всех экспериментах добавку катализатора вводили в разогретую до 80°С смесь ТГКК и парафина из расчета 0.1% металла на сырьевую смесь.
Опыты гидроконверсии проводили в автоклавной установке [20] при постоянном давлении с непрерывной подачей водорода. Сырьевую смесь в количестве 300 г помещали в автоклав, герметизировали, продували азотом, затем открывали ток водорода с постоянной скоростью 18–20 нл/ч и давлении 7 МПа. В предварительной серии экспериментов были установлены оптимальные значения температуры (445°С) и длительности выдержки автоклава на режиме при заданных условиях 2 ч.
В процессе эксперимента выходящие из реактора водород и продукты реакции охлаждали и разделяли в сепараторе на газовую и жидкую фазы. Газовая фаза, состоящая из газообразных продуктов реакции, водяных паров и водорода, поступала в газовый счетчик и после щелочного абсорбера подвергалась хроматографическому анализу. По окончании эксперимента рассчитывали выход газа, определяли массу жидких продуктов в сепараторе и остатка в автоклаве. Затем продукты, уловленные в сепараторе и оставшиеся в автоклаве, объединяли и определяли массу, состав и свойства гидрогенизата. В гидрогенизате определяли плотность, содержание серы и нерастворимых в толуоле твердых частиц (НРТ). Из гидрогенизата выделяли соединения, нерастворимые в толуоле, и исследовали их состав методами ЛКС (DLS), РСФА (RSFA) и РДА (XRD). Гидрогенизат подвергали атмосферно-вакуумной разгонке и определяли выход отдельных фракций. Групповой состав гидрогенизата и его фракций определяли на хромато-масс-спектрометре Thermo Focus DSQ II (капиллярная колонка Varian VF-5ms) и жидкостном хроматографе “Градиент-М”.
Конверсию сырья (Q) рассчитывали по уравнению:
Селективность процесса гидрокрекинга (F) рассчитывали по уравнению:
РЕЗУЛЬТАТЫ И ИХ ОБСУЖДЕНИЕ
Характеристики синтезированных катализаторов приведены в табл. 2. Как видно из данных таблицы, средние диаметры частиц катализаторов находятся в пределах 273–364 нм. Катализаторы, синтезированные из соединений молибдена, никеля и железа, присутствуют преимущественно в форме сульфидов MoS2 , Ni7S6 и Fe(1 – x)S. Вольфрамат аммония в условиях синтеза частично разлагается с потерей части аммиака и образованием (NH4)0.25 ⋅ WO3. Для получения сульфида вольфрама из оксидный формы необходима температура выше 600°С [19]. В катализаторе, синтезированном из смеси солей молибдена и никеля обнаружены фазы индивидуальных сульфидов MoS2 и Ni7S6. Фаз, содержащих оба элемента, не обнаружено.
Выделенные из гидрогенизатов нерастворимые в толуоле продукты состоят по данным РФА из фазы катализатора и графитизированных продуктов уплотнения (кокса). Содержание продуктов уплотнения возрастает в ряду: Мо, Ni, Fe, W. Эта закономерность соответствует установленной нами активности катализаторов в реакциях крекинга (табл. 3–5). Вольфрамовый катализатор в условиях эксперимента не сульфидируется и не восстанавливается, а превращается в WO3.
Таблица 3.
Выход продуктов при гидроконверсии смеси парафина и ТГКК (массовое отношение 1 : 1) в присутствии суспензий наноразмерных катализаторов. Условия опытов: 445°С, 7 МПа, расход водорода 18–20 нл/ч, длительность опыта при рабочих условиях – 2 ч, количество катализатора – 0.1 мас. % на сырье (в пересчете на активные металлы). Н.К. - начало кипения
Выход продуктов, мас. % | Сырье | Катализатор | |||||
---|---|---|---|---|---|---|---|
без катализатора | МоS2 | Ni7S6 | Fe1 – xS | (NH4)0.25 ⋅ WO3 | МоS2 + Ni7S6 | ||
Газ | – | 6.2 | 2.9 | 5.62 | 7.6 | 6.59 | 4.15 |
Состав газа, мас. % | |||||||
С1 | – | 66.7 | 80.9 | 72.2 | 69.2 | 74.3 | 75.8 |
$\sum {{{{\text{C}}}_{{\text{2}}}}} $ | – | 16.3 | 15.3 | 14.1 | 16 | 20.9 | 14.6 |
$\sum {{{{\text{C}}}_{{\text{3}}}}} $ | – | 10.6 | 2.98 | 7.86 | 8.71 | 0.91 | 7.24 |
$\sum {{{{\text{C}}}_{{\text{4}}}}} $ | – | 5.94 | 0.82 | 5.42 | 5.77 | 3.33 | 2.09 |
$\sum {{{{\text{C}}}_{{\text{5}}}}} $ | – | 0.46 | 0 | 0.42 | 0.32 | 0.56 | 0.27 |
Гидрогенизат, в т. ч.: | 100.0 | 93.03 | 96.88 | 94.12 | 90.8 | 92.81 | 95.53 |
фр. Н.К.–180°C | 0.6 | 7.63 | 6.69 | 5.3 | 8.68 | 12.2 | 6.3 |
фр. 180–350°C | 17.6 | 27.9 | 32.4 | 34.3 | 31.6 | 40.7 | 34.2 |
фр. 350–500°C | 76.0 | 47.1 | 51.5 | 47.4 | 41.7 | 31.1 | 48.9 |
Остаток выше 500°C | 5.8 | 10.4 | 6.29 | 7.12 | 8.82 | 8.81 | 6.13 |
НРТ | – | 0.77 | 0.22 | 0.26 | 1.6 | 1.2 | 0.32 |
Конверсия фр. 350°С+ | – | 34.6 | 31.6 | 37.3 | 43.9 | 54.7 | 35.7 |
Селективность по дистиллятной фракции Н.К.–350°С | – | 52.5 | 76.2 | 62.6 | 51.1 | 69.0 | 70.1 |
Гидрокрекинг – один из основных процессов переработки высококипящих нефтяных фракций (вакуумного газойля, газойля каталитического крекинга и т.п. ) с получением легких и средних дистиллятов. Процесс проводят в присутствии бифункциональных катализаторов, содержащих как гидрирующий компонент (обычно MoS2, промотированный кобальтом или никелем), так и крекирующий компонент с высокой концентрацией активных кислотных центров на носителе (оксиды алюминия, кремния, титана, алюмосиликаты, цеолиты). Оценку эффективности катализаторов проводят, исходя из глубины превращения фракции вакуумного дистиллята “350°С–К.К. (конец кипения)” в бензиновую и дизельную фракции и степени удаления гетероатомов.
Для сравнения эффективности суспензии наноразмерных частиц разных катализаторов без носителя проведена серия экспериментов.
В процессе гидрокрекинга происходит восстановление неорганических компонентов исходных катализаторов, в результате чего доли основных фаз (гексагонального дисульфида молибдена, Ni7S6 и пирротина) возрастают. Вольфрамовый катализатор в условиях эксперимента не сульфидируется и не восстанавливается, теряет часть аммиака и переходит в WO3. В отсутствие катализаторов превращение сырья сопровождается образованием газообразных продуктов, легких дистиллятных фракции “Н.К.–180°С”, “180–350°C” и нерастворимых в толуоле продуктов (табл. 3). Увеличение выхода легких фракций гидрогенизата происходит в результате крекинга фракции “350–500°C”. По сравнению с исходным сырьем в гидрогенизате опыта без катализатора растут содержания ароматических УВ, смол и асфальтенов, в то время как снижается содержание парафино-нафтеновых УВ (табл. 4). Аналогичная закономерность установлена и для отдельных фракций гидрогенизата (табл. 5). Результаты, приведенные в табл. 3–5 позволяют сделать вывод, что в отсутствиe катализаторов сырье превращается по механизму термического крекинга.
Таблица 4.
Состав и свойства гидрогенизата, полученного при гидроконверсии смеси парафина и ТГКК в присутствии суспензий наноразмерных катализаторов
Свойства продуктов | Сырье | Катализатор | |||||
---|---|---|---|---|---|---|---|
без катализатора | МоS2 | Ni7S6 | Fe1 – xS | (NH4)0.25 ⋅ WO3 | МоS2 + Ni7S6 | ||
Средний диаметр частиц катализатора (DLS), нм | – | – | 564 | 667 | 751 | 632 | 681 |
Плотность гидрогенизата (20°С), кг/м3 | 890 | 895 | 883 | 887 | 894 | 898 | 880 |
Сера, мас. % | 1.75 | 1.72 | 1.44 | 1.40 | 1.7 | 1.69 | 1.35 |
Групповой состав, мас. %: | |||||||
ПНУВ | 56.1 | 46.1 | 78.2 | 74.1 | 62.3 | 64.9 | 74.7 |
АУВ | 39.7 | 48.3 | 19.5 | 22.8 | 34.5 | 30.9 | 22.7 |
СМ | 2.9 | 3.19 | 1.28 | 1.56 | 1.89 | 2.3 | 1.43 |
АСФ | 1.3 | 2.41 | 1.02 | 1.54 | 1.31 | 1.9 | 1.17 |
ПНУВ/АУВ | 1.41 | 0.95 | 4.01 | 3.25 | 1.80 | 2.10 | 3.29 |
ПНУВ/(СМ + АСФ) | 13.3 | 8.23 | 34 | 23.9 | 19.5 | 15.4 | 28.7 |
(ПНУВ + АУВ)/(СМ + АСФ) | 22.8 | 16.9 | 42.5 | 31.3 | 30.2 | 22.8 | 37.5 |
Таблица 5.
Состав фракций гидрогенизата, полученных при гидроконверсии смеси парафина и ТГКК в присутствии суспензий наноразмерных катализаторов
Свойства продуктов | Катализатор | |||||
---|---|---|---|---|---|---|
без катализатора | МоS2 | Ni7S6 | Fe1 – xS | (NH4)0.25 ⋅ WO3 | МоS2 + Ni7S6 | |
Фракция Н.К.–180°C | ||||||
Содержание серы, % | 0.23 | 0.1 | 0.19 | 0.31 | 0.23 | 0.1 |
Групповой состав, мас. %: | – | – | – | – | – | – |
парафино-нафтеновые УВ | 89.3 | 90.05 | 90.82 | 87.2 | 89.8 | 87.8 |
ароматические УВ | 10.7 | 9.95 | 9.18 | 12.8 | 10.2 | 12.2 |
Фракция 180–350°С | ||||||
Групповой состав, мас. %: | ||||||
парафино-нафтеновые УВ | 74.7 | 83.9 | 77.2 | 60.1 | 67.6 | 82.0 |
ароматические УВ | 25.3 | 16.1 | 22.8 | 39.9 | 32.4 | 18.0 |
ПНУВ/АУВ | 2.95 | 5.21 | 3.89 | 1.51 | 2.07 | 4.56 |
Фракция 350–500°C | ||||||
Групповой состав, мас. %: | ||||||
ПНУВ | 29.5 | 88.9 | 80.2 | 54.8 | 60.7 | 83.2 |
АУВ | 66.9 | 10.1 | 18.6 | 44.6 | 37.9 | 15.3 |
СМ | 3.6 | 1 | 1.2 | 0.6 | 1.4 | 1.3 |
ПНУВ/АУВ | 0.44 | 8.80 | 4.31 | 1.23 | 1,60 | 5.44 |
По сравнению с опытом без катализатора в присутствии суспензии наноразмерных частиц MoS2 существенно снижаются выходы газа, смол, асфальтенов и НРТ (табл. 3, 4). Выходы фракций “Н.К.–180°С” и “180–350°C” близки к выходу этих фракций в опыте без катализатора (табл. 3), но отношение парафино-нафтеновых УВ к ароматическим УВ (ПНУВ/АУВ) в гидрогенизате и фракциях гидрогенизата существенно выше, чем в опыте без катализатора (табл. 4, 5). Полученные результаты по изменению углеводородного состава дистиллятных фракций продуктов реакции показывают существенное влияние суспензий наноразмерных частиц катализатора на механизм реакций и конверсии сырья. Первой стадией процесса является термический крекинг компонентов сырьевой смеси. Частицы MoS2, равномерно распределенные в реакционном объеме и находящиеся на небольшом расстоянии друг от друга, обеспечивают доставку активного водорода к радикальным фрагментам молекул, образовавшимся в результате термической деструкции молекул смол и асфальтенов, тем самым снижая выход газа и НРТ. Одновременно, MoS2 активно участвует в реакции гидрирования присутствующих в сырье ароматических УВ с образованием нафтеновых УВ, а также образовавшихся при термическом крекинге ненасыщенных ПНУВ. В результате этих процессов в гидрогенизате содержание ПНУВ достигает 78.2% (табл. 4). Высокая активность наноразмерного MoS2 проявляется и в реакциях гидрообессеривания и гидрирования непредельных УВ. В его присутствии наблюдаются наименьшие содержания непредельных УВ и серы во фракциях гидрогенизата (рис. 1 и 2). Полученные результаты свидетельствуют о том, что наноразмерные суспензии MoS2 проявляют высокую активность в реакциях гидрирования ароматических УВ, сопровождающуюся снижением количества ароматических и ростом парафино-нафтеновых УВ практически во всех дистиллятных фракциях. Образующиеся при разрыве С–С-связи радикальные фрагменты эффективно гидрируются и стабилизируются в присутствии МоS2, на что указывает высокая селективность по выходу фракции Н.К.–350°С 76.2% при низкой глубине конверсии 31.6% (табл. 3). Снижение показателя иодных чисел в опытах с катализатором свидетельствует о высокой активности МоS2, в гидрировании олефинов. Снижение более чем в 3 раза содержания НРТ в гидрогенизате и выхода газа указывает на эффективное прерывание в опытах с МоS2 реакций, протекающих с образование конечных продуктов термической деструкции кокса и газа.
Рис. 1.
Содержание серы во фракциях гидрогенизата. Катализаторы: 1 – МоS2; 2 – Ni7S6; 3 – Fe1 – xS; 4 – (NH4)0.25 ⋅ WO3 ; 5 – МоS2 + Ni7S6.
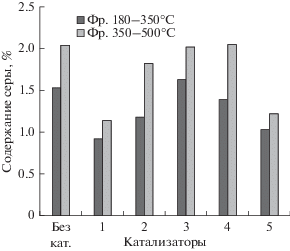
Рис. 2.
Содержание олефинов во фракциях гидрогенизата. Катализаторы: 1 – МоS2; 2 – Ni7S6; 3 – Fe1 – xS; 4 – (NH4)0.25 ⋅ WO3; 5 – МоS2 + Ni7S6.
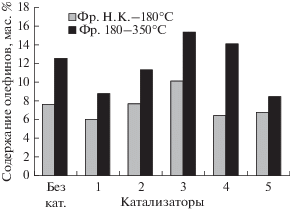
Наноразмерный сульфид никеля Ni7S6 по сравнению с МоS2 в меньшей степени, проявляет каталитические свойства в реакциях с присоединением водорода. Исходя из оценки конверсии сырья, можно предположить, что этот катализатор обладает небольшой каталитической активностью в реакциях крекинга сырья (табл. 3).
Близкие к индивидуальному MoS2 каталитические свойства проявляет смесь MoS2 и Ni7S6. По-видимому, из-за отсутствия совместных сульфидных фаз эффект промотирования молибдена никелем в реакциях гидродесульфуризации и гидрирования не наблюдается (рис. 1, 2).
Суспензия наноразмерных частиц пирротина – Fe(1 – x)S – проявляет в большей степени крекирующие свойства, чем гидрирующие. Сопоставление составов исходного сырья и гидрогенизата, полученного в присутствии Fe(1 – x)S, свидетельствует о том, что он катализирует реакции крекинга всех компонентов сырья с образованием дистиллятных фракций, газа и кокса. В результате этих процессов конверсия сырья возрастает до 43.9%. Из-за образования значительных количеств газа и кокса процесс характеризуется низким значением селективности – 51.1% (табл. 3). При этом выход кокса более чем в 2 раза превышает выход кокса в опыте без катализатора. Поскольку образование кокса в термических процессах переработки тяжелого нефтяного сырья преимущественно происходит в результате крекинга асфальтенов и смол [21–23], можно полагать, что пирротин катализирует реакции последовательного превращения компонентов сырья по схеме: АУВ → смолы → асфальтены → кокс (НРТ). Эта схема подтверждается результатами экспериментов, которые показывают, что в присутствии пирротина наблюдаются максимальные выход НРТ (табл. 3). Превращения компонентов сырья на каждом этапе сопровождаются образованием легких УВ. Каталитический эффект суспензий наноразмерных частиц Fe(1 – x)S в реакциях крекинга подтверждается результатами экспериментов гидроконверсии гудронов при температуре 435°С и давлении водорода 7 МПа [24].
В условиях эксперимента пирротин обладает слабыми гидрирующими свойствами. Выход парафино-нафтеновых УВ выше, а ароматических УВ ниже, чем в эксперименте без катализатора (табл. 4). Следует отметить, что при более высоком давлении водорода (18–30 МПа) пирротин проявляет каталитическую активность в реакциях гидрирования смол и асфальтенов, что позволило использовать такой катализатор в промышленно освоенных процессах гидрогенизации углей [25], а также в разработанных процессах гидропереработки битума и тяжелых нефтей: CANMET, Veba Oel’s Combi-Cracking (VCC), Pet-roCanada’s SRC Uniflex [26–28]
Из испытанных дисперсных катализаторов минимальной гидрирующей активностью обладает суспензия (NH4)0.25 ⋅ WO3 (табл. 3). В присутствии этого катализатора превращение сырья характеризуется максимальными значениями выхода легких дистиллятных фракций “Н.К – 180°С” и “180–350°C” и конверсии 54.3%. Селективность суспензии (NH4)0.25 ⋅ WO3 лишь не намного уступает селективности гидрокрекинга в присутствии MoS2. В отличие от пирротина (NH4)0.25 ⋅ WO3 в меньшей степени катализирует крекинг асфальто-смолистых компонентов (табл. 5). Гидрирующие функции катализатора можно оценить по изменению соотношения ПНУВ/АУВ, которое в гидрогенизате существенно выше, чем в сырье (табл. 4). Однако в реакциях гидрообессеривания и гидрирования (NH4)0.25 ⋅ WO3 практически не активен, как и пирротин (рис. 1 и 2). Следует отметить, что в опыте с (NH4)0.25 ⋅ WO3 наблюдается высокая степень превращения фракции 350–500°С с образование легких и средних дистиллятов. Полученные результаты согласуются с приведенным в литературе данным о высокой каталитической активности оксида вольфрама в реакциях крекинга дистиллятного углеводородного сырья [29, 30].
Проведенные исследования показали, что активность синтезированных ex situ дисперсных катализаторов в реакциях крекинга растет в ряду: МоS2, (МоS2 + Ni7S6 ), Ni7S6, Fe1 – xS, (NH4)0.25 ⋅ WO3. При этом МоS2 проявляет высокую каталитическую активность как в реакциях разрыва С–С-связей, так и в реакциях гидрогенолиза. Fe1 – xS и (NH4)0.25 ⋅ WO3 в условиях эксперимента в большей степени проявили крекирующие функции и низкую активность в реакциях гидрирования.
Исследование выполнено на базе ИНХС РАН за счет гранта Российского научного фонда (проект № 17-73-30046).
Список литературы
Хаджиев С.Н. // Наногетерогенный катализ. 2016. Т. 1. № 1. С. 3. [Petrol. Chemistry. 2016. V. 56. № 6. P. 4651].
Zhang S., Liu D., Deng W., Que G. // Energy & Fuels. 2007. V. 21. № 6. P. 3057.
Bellussi G., Rispoli G., Landoni A., Millini L., Molinare D., Montanari E., Pollesel P. // J. Catal. 2013. V. 308. P. 189.
Nguyen M.T., Nguyen N.T., Cho J., Park C., Park S., Jung J., Lee C.W. // J. of Industrial and Engineering Chemistry. 2016. V. 43. № 11. P. 1.
Хаджиев С.Н., Кадиев Х.М., Кадиева М.Х. // Нефтехимия. 2014. Т. 54. № 5. С. 327 [Petrol. Chemistry. 2014. V. 54. № 5. P. 323].
Bellussi G., Rispoli G., Molinari D. Landoni A., Pollesel P., Panariti N., Millini R., Montanari E. // Catalysis Science & Technology. 2013. № 3. P. 176.
Хаджиев С.Н., Кадиев Х.М., Зекель Л.А., Кадиева М.Х. // Наногетерогенный катализ. 2018. Т. 3. № 1. С. 18 [Petrol. Chemistry. 2018. V. 58. № 7. P. 535].
Del Bianco A., Panariti N., Di Carlo S., Beltrame P.L., Carnitii P. // Energy & Fuels. 1994. V. 8. P. 593.
Panaritia N., Del Bianco A., Del Piero G., Marchionna M. // Applied Catalysis. 2000. V. 204. P. 203.
Kun H., Shuichang Zh., Jingkui M., Jianping C., Lei Ch. // Pet. Sci. 2011. V. 8. P.134.
Jeon S.G., Na J.G., Ko Ch.H. // Energy & Fuels. 2011. V. 25. P. 4256.
Al-Marshed A., Hart A., Leeke G., Greaves M., Wood J. // Energy & Fuels. 2015. V. 29. P. 6306.
Liu D., Cui W., Zhang Sh., Que G. // Energy & Fuels. 2008. V. 22. P. 4165.
Zhang Sh., Deng W., Luo H., Liu D., Que G. // Energy & Fuels. 2008. V. 22. P. 3583.
Shi B., Que G. // Prepr. Pap.-Am. Chem. Soc. Div. Fuel Chem. 2003. V. 48. № 2. P. 722.
Кадиев Х.М., Зекель Л.А., Гюльмалиев А.М., Дандаев А.У., Кадиева М.Х. // Наногетерогенный катализ. 2019. T. 4. № 1. C. 1 [Petrol. Chemistry. 2019. V. 59. № 3. Р. 498].
Кадиев Х.М. Автореферат на соискание ученой степени доктора хим. наук. ИНХС РАН. Москва. 2018. 48 с.
Кадиев Х.М., Кадиева М.Х., Зекель Л.А., Эрман Е.С. Хаджиев С.Н. // Коллоидный журнал. 2019. Т. 81. № 2. С.153.
Van der Vlies A.J., Kishan G., Niemantsverdriet J.W., Prins R., Weber Th. // J. Phys. Chem. B. 2002. V. 106. P. 3449.
Kadiev Kh.M., Oknina N.V., Maksimov A.L., Kadieva M.Kh., Batov A.E., Dandaev A.U. // Research J. of Pharmaceutical, Biological and Chemical Sciences. 2016. V. 7. № 5. P. 704.
Сергиенко С. Р., Таимова Б.А., Талалаев Е.И. Высокомолекулярные неуглеводородные соединения нефти. Смолы и асфальтены. М.: Наука, 1979. 269 с.
Mullins O.C., Sheu E.Y., Hammami A.G. Heavy Oils and Petroleomics. New York City: Springer, 2007. 370 p.
Ancheyta J., Treiro F., Rana M.S. Asphaltenes: Chemical Transformation during Hydroprocessing of Heavy Oils. Boca Raton, London, New York: CRC Press, 2009. 419 p.
Кадиев Х.М., Зекель Л.А., Гюльмалиев А.М., Дандаев А.У., Кадиева М.Х. // Наногетерогенный катализ. 2018. Т. 3. № 2. С. 67 [Petrol. Chemistry. 2018. V. 58. № 14. P. 1165].
Vasireddy S., Morreale B., Cugini A., Song Ch., Spivey J.J. // Energy Environ. Sci. 2011. № 4. P. 311.
Graeser U, Eschet G, Holighnaus R. In: Proceedings of the Refining Department. American Pet. Institute, San Diego, CA, USA. 1986. P. 169.
Benham N.K., Pruden B.B. CANMET Residuum Hydrocracking Advances through Control of Polar Aromatics in NPRA. Annual meeting, San Antonio, USA. March 1996.
Huy N., Pham V.H. // Chem. Engineering & Technology. 2013. V. 36. № 8. P. 1365.
Barton D.G., Soled S.L., Iglesia E. // Topics Catal. 1998. V. 6. P. 87.
Kline C.H., Kollonitsch V. // II. Ind. Eng. Chem. 1965. V. 57. P. 53.
Дополнительные материалы отсутствуют.