Нефтехимия, 2019, T. 59, № 5, стр. 560-568
Гидроформилирование этилена на родиевых катализаторах в обогащенных углеводородами средах: стадия комбинированного процесса переработки нефтезаводских газов в оксигенаты
Д. Н. Горбунов 1, *, М. В. Ненашева 1, Р. П. Мацукевич 1, М. В. Теренина 1, Ф. Н. Путилин 1, Ю. С. Кардашева 1, А. Л. Максимов 2, Э. А. Караханов 1
1 Московский государственный университет имени М.В. Ломоносова,
Химический факультет
119234 Москва, Россия
2 Институт нефтехимического синтеза им. А.В. Топчиева РАН
119991 Москва, Россия
* E-mail: suskab_91@mail.ru
Поступила в редакцию 14.03.2019
После доработки 10.05.2019
Принята к публикации 13.05.2019
Аннотация
В работе изучены закономерности гидроформилирования модельных газовых смесей с различным содержанием этилена, водорода и метана на родиевых катализаторах. Оценено влияние начального давления в реакторе и температуры реакции на скорость и селективность реакции. Показано, что гидроформилирование этилена протекает с высокой селективностью по пропаналю (до 99%), а частота оборотов реакции достигает 9500 ч–1. Предложено использование различных фосфиновых лигандов для осуществления альтернативных способов отделения каталитической системы от продуктов реакции.
ВВЕДЕНИЕ
Вопросы глубокой переработки ископаемого углеводородного сырья на сегодняшний день не теряют своей актуальности. На нефтеперерабатывающих предприятиях, располагающих установками крекинга углеводородов (УВ), помимо целевых товарных продуктов, образуется значительное количество этилена и насыщенных газов С2+, которые чаще всего сжигаются с целью выработки тепла [1–5]. Учитывая, что исходное сырье для крекинга прошло большое количество стадий очистки и подготовки (осушка, обессеривание), а также низкую теплоотдачу при сгорании смесей данного состава, такое использование нельзя считать рациональным [6]. В настоящее время ведется активный поиск способов переработки легких УВ в продукты с высокой добавленной стоимостью, например оксигенаты. Интегрирование процессов переработки газов с существующими производственными процессами позволит повысить глубину переработки сырья и экономические показатели производств, а также расширить ассортимент продукции, выпускаемой предприятиями.
Газы каталитического крекинга могут содержать некоторое количество этилена, но его гидроформилирование требует подачи в реактор синтез-газа (рис. 1, поток I). Реализация процессов переработки с использованием технологий мембранного концентрирования этилена, оксикрекинга и матричной конверсии приводит к получению обогащенных этиленом газовых смесей, содержащих также достаточное количество водорода и монооксида углерода (рис. 1, потоки II–IV), что позволяет проводить синтез кислородсодержащих соединений непосредственно из образующихся газовых смесей без создания отдельной установки производства синтез-газа [7–11]. Выбор способа переработки в значительной степени зависит от состава исходного нефтезаводского газа.
Следует отметить, что в каждом из представленных процессов образуются также насыщенные УВ. В литературе описаны процессы гидроформилирования в средах, обогащенных диоксидом углерода или низшими УВ (GasExpandedLiquids, GXLs) [12–17]. Отмечено, что повышение общего давления в реакторе гидроформилирования за счет подачи газа способствует лучшему насыщению растворителя реагирующими компонентами – олефином, монооксидом углерода и водородом, что положительно сказывается на скорости протекания реакции. Физико-химические константы газов, такие как критическая температура Tк и давление Pк, определяют параметр степени расширения жидкой фазы. При условиях протекания реакции (повышенные давления и температуры) расширение объема жидкой фазы за счет конденсации газов может составлять 40–80% от исходного объема, что позволяет снизить расход используемого растворителя. На примере гидроформилирования пропилена пропан-пропиленовой фракции показано, что реакции в GXLs (в качестве растворителей использовались толуол, бутанол-1 и NX-795 – смесь олигомеров бутаналя) протекают с более высокой селективностью по линейному альдегиду [12]. Проведение гидроформилирования пропилена в смеси с пропаном без стадии разделения компонентов является более экономичным процессом с точки зрения расхода энергии; при этом поток из реактора гидроформилирования, обогащенный пропаном, может быть направлен на дополнительное получение пропилена. Отсутствие необходимости сжатия газов до высокого давления определяет преимущества использования GXLs относительно сверхкритических жидкостей в качестве альтернативных реакционных сред [12].
В настоящей работеизучены особенности протекания реакции гидроформилирования этилена в газовых смесях, обогащенных предельными УВ (метаном). Исследовано влияние состава исходной газовой смеси, начального давления газов в реакторе и температуры на скорость и селективность реакции. В качестве компонентов каталитической системы использованы комплексы родия с фосфиновыми лигандами, позволяющими проводить отделение катализатора от продуктов реакции различными способами.
ЭКСПЕРИМЕНТАЛЬНАЯ ЧАСТЬ
Трифенилфосфин, TPPTS (натриевая соль 3,3',3''-трисульфированного трифенилфосфина), полиэтиленгликоль (М = 3000 г/моль), 4-дифенилфосфинбензойная кислота, 1,3-дициклогексилкарбодиимид (фирма “Sigma-Aldrich”) были использованы без предварительной подготовки. Комплекс Rh(acac)(CO)2 синтезирован по известной методике [18]. Подготовка растворителей (толуол, ацетилацетон) выполнена по стандартным методикам. Этилен, водород, метан и монооксид углерода, использованные в работе, приобретены в компании “Voessen”.
Анализ жидких продуктов методом ГЖХ проводили на хроматографе “Хромос” c пламенно-ионизационным детектором, капиллярной колонкой 50 м, заполненной фазой SE-30, при программировании температуры от 60 до 230°С, газ-носитель – гелий, с использованием внутреннего стандарта – н-гептана. Анализ методом ЯМР 1H и 31P проводили на приборе “VarianXL-400” с рабочей частотой 400 МГц. Спектры MALDI зарегистрированы на времяпролетном масс-спектрометре с матрично-активированной лазерной десорбцией/ионизацией “BrukerDaltonics AutoflexII”, с азотным лазером с рабочей длиной волны 337 нм. В качестве матрицы использована 2,5-дигидроксибензойная кислота.
Методика синтеза фосфинового лиганда PEG-PPh3
В круглодонную колбу, снабженную магнитной мешалкой, в атмосфере аргона помещали 0.5 г (1.62 ммоль) 4-(дифенилфосфино)-бензойной кислоты и 5 мл дихлорметана. При перемешивании к раствору добавляли 20 мг (0.16 ммоль) 4-диметиламинопиридина и 2 г (0.67 ммоль) полиэтиленгликоля (М = 3000 г/моль). Затем смесь охлаждали до 0°С и добавляли 0.34 г (1.65 ммоль) 1,3-дициклогексилкарбодиимида. Раствор перемешивали 5 мин при 0°С, затем 3 ч при комнатной температуре. По окончании реакции осадок отфильтровывали на бумажном фильтре и промывали дихлорметаном. К фильтрату добавляли 10-ти кратный избыток охлажденного диэтилового эфира и отфильтровывали выпавший осадок на воронке со стеклянным фильтром в атмосфере аргона, промывали 3 раза диэтиловым эфиром и сушили в атмосфере аргона. Полученное вещество – порошок светло-желтого цвета. Выход продукта – 1.9 г (85% от теор.):
Спектр ЯМР 1Н (400 МГц, CDCl3) δ, м.д.: 3.40–3.90 (м, 310H, –(CH2–CH2–O)n–), 4.45 (м, 4H, Ha), 7.27 – 7.38 (м, 24H, Hb), 7.94 – 7.99 (м, 4H, Hc). Спектр ЯМР 31P (162 МГц, CDCl3) δ, м.д.: –4.95. Масс-спектр (MALDI): максимум молекулярно-массового распределения m/z = = 3560.
Методика проведения каталитических экспериментов по гидроформилированию этилена
Реакции проводили в стальном автоклаве ParrInstrument емкостью 25 мл, снабженном устройством для перемешивания с механическим приводом (магнитная муфта) и газозахватной мешалкой, а также устройством для термостатирования при температурах до 350°С. В автоклав загружали: растворитель – толуол (4.0 мл), компоненты каталитической системы – Rh(acac)(CO)2 – 0.015 ммоль и фосфиновый лиганд – 0.045 ммоль (по фосфору), и 0.6 мл внутреннего стандарта – н-гептана. Автоклав дважды продували монооксидом углерода, затем последовательно заполняли метаном до заданного давления, затем до заданных давлений последовательно закачивали монооксид углерода, водород и этилен. Контроль общего давления осуществляли с помощью датчика шприцевого насоса “Teledyne”. После этого включали перемешивание (1000 об/мин) и нагревали автоклав со скоростью 3°С/мин с последующим выдерживанием при заданной температуре. Вели реакцию при постоянном перемешивании до заданного значения времени, фиксируя зависимость давления и температуры от времени реакции. После завершения реакции автоклав охлаждали до комнатной температуры и фиксировали показания манометра (погрешность – 2 атм), затем осуществляли разгерметизацию автоклава и отбор пробы.
РЕЗУЛЬТАТЫ И ИХ ОБСУЖДЕНИЕ
В табл. 1 представлены примеры газовых смесей с комбинированных установок переработки нефтезаводских газов. Состав продуктовой газовой смеси зависит от состава исходного НЗГ (содержание метана, жирных газов, олефинов), выбранного пути комбинированной переработки, а также от условий проведения процессов парциального окисления, таких как длительность пребывания сырья в реакторе, температура, давление и скорость расхода сырья [7, 19].
Таблица 1.
Возможный состав газовых смесей, направляемых на стадию гидроформилирования при комбинированной переработке нефтезаводских газов
Компонент | Содержание, об. % | Поток 1 | Поток 2 | Поток 3 |
H2 | 20.3 | 40.6 | 4.1 | |
O2 | 0.0 | 0.4 | 0.0 | |
N2 | 0.0 | 1.1 | 0.0 | |
CO | 10.4 | 12.6 | 6.6 | |
CO2 | 1.7 | 0.8 | 0.1 | |
CH4 | 43.3 | 25.1 | 41.2 | |
C2H6 | 0.2 | 4.7 | 13.4 | |
C2H4 | 5.9 | 12.0 | 25.5 | |
C2H2 | 0.0 | 1.5 | 0.0 | |
C3H8 | 0.0 | 0.5 | 1.7 | |
C3H6 | 0.3 | 0.6 | 2.8 | |
$\sum {{{{\text{C}}}_{{{\text{4 + }}}}}} $ | 0.0 | 0.1 | 0.5 |
Организация режима работы комбинированных установок (рис. 1) позволяет регулировать состав газовых смесей, поступающих на стадию оксо-синтеза. В связи с этим, исследована реакция гидроформилирования модельных смесей, представленных в табл. 2. В качестве инертного компонента использовался метан. В табл. 3 приведены физико-химические константы газов, в среде которых ранее было изучено гидроформилирование олефинов.
Таблица 2.
Состав модельных газовых смесей
Номер модельной смеси | Компонентный состав, об. % | |||
---|---|---|---|---|
C2H4 | CO | H2 | CH4 | |
1 | 20 | 20 | 40 | 20 |
2 | 20 | 20 | 20 | 40 |
3 | 40 | 20 | 20 | 20 |
В зависимости от Тк и Рк газов жидкость (растворитель) может расширяться вследствие поглощения газов, причем величина относительного расширения жидкости (V/V0) зависит от давления газа и температуры. Предпочтительно для генерирования GXLs использовать такие газы, критическая температура которых лежит несколько ниже температуры, при которой протекает исследуемая реакция [12, 13]. Из данных табл. 3 следует, что значительное насыщение и расширение жидкости для случая с метаном маловероятно. Однако вследствие повышения общего давления из-за присутствия метана в системе, растворение газообразных реагентов (C2H4, CO и H2) в толуоле более эффективно, как и их контакт с гомогенным каталитическим комплексом.
С использованием модифицированных родий-фосфиновых комплексов в настоящее время проводят около половины всех промышленных процессов оксо-синтеза, и отделение продуктов реакции (альдегидов) от катализаторного раствора осуществляют способом дистилляции. В качестве альтернативных способов отделения и рециркуляции каталитических систем применяют способы с использованием водорастворимых лигандов в двухфазных системах, терморегулируемых лигандов, ионных жидкостей, осуществляется отделение каталитического комплекса в процессах экстракции и мембранной нанофильтрации [20–23]. В данной работе использованы каталитические системы, включающие каталитический прекурсор – комплекс родия Rh(acac)(CO)2 и фосфиновые лиганды, позволяющие реализовать различные способы выделения каталитических систем из реакционных смесей.
Общая схема, описывающая возможные химические превращения при гидроформилировании, представлена ниже:
Схема. Гидроформилирование этилена.
В результате реакции происходит образование пропаналя (А), диэтилкетона (B) а также альдоля (C).
На примере гидроформилирования модельных смесей 1–3 в присутствии классической каталитической системы Rh/PPh3 было исследовано влияние таких параметров, как общее начальное давление и температура реакции. В работе оценивалась скорость поглощения газообразных компонентов – этилена (субстрат, S), СО и H2 по падению давления в стационарном реакторе при равномерном нагреве от комнатной температуры до заданной. Кинетика реакций гидроформилирования этилена и пропилена на родиевых катализаторах подробно изучалась в [24, 25], в связи с этим в качестве целей работы определено получение данных по влиянию инертных компонентов и состава модельных газовых смесей на конверсию этилена. На рис. 2 представлен профиль реакции гидроформилирования модельной смеси 1 (зависимость давления газов в реакторе от времени реакции), начальное давление газов – 100 атм, режим нагрева– от 25 до 80°С со скоростью 3°С/мин.Приведена также кривая термического расширения метана (пунктир), характеризующая значение давления в реакторе, если не протекает реакция и не происходит поглощения газов.
Рис. 2.
Профиль реакции гидроформилирования модельной смеси 1. Условия реакции: Rh(acac)(CO)2 – 4 мг, PPh3 – 12 мг, S/Rh = 1600, толуол – 4 мл, гептан – 0.6 мл, Pнач = 100 атм, скорость нагрева 3°С/мин, Tк = 80°С.
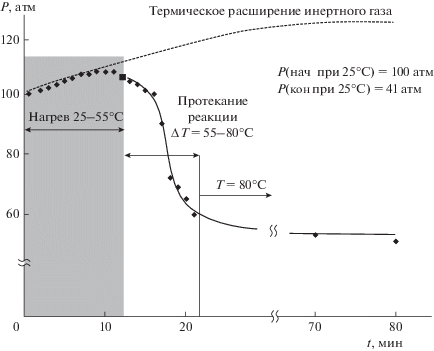
Началу реакции соответствует температура 55°С, а практически полное поглощение газообразных компонентов достигается к моменту разогрева реакционной смеси до 80°С. Производительности каталитической системы (TOF, частота оборотов реакции, ч–1) для участка кривой, отражающего наиболее быстрое протекание реакции, определена согласно формуле (1) и ее значение составило 9500 ч–1:
(1)
${\text{TOF}} = \frac{{n\,\,{\text{(прореагировавшего}}\,\,{\text{этилена)}}}}{{n({\text{Rh)}}{{t}_{{{\text{реакции}}}}}}}.$Количество прореагировавшего этилена (в моль) определяли по уравнению состояния газов, исходя из значений остаточного давления. Зафиксировано образование единственного продукта – пропаналя (А), и его количество соответствует стехиометрическому протеканию реакции. Образование продукта гидрирования – этана – в данном случае незначительно и маловероятно из-за более высокого порога энергии активации реакции гидрирования по отношению к реакции гидроформилирования [25]. По мере расходования газообразных реагентов и при их низких остаточных концентрациях скорость реакции значительно снижается, однако, она протекает практически до полного превращения газообразных реагентов, а наличие метана в системе способствует лучшему растворению газов и их трансферу к активным центрам катализатора.
На рис. 3а и 3б изображены профили реакции гидроформилирования модельной смеси 1 при температуре 60°С, при начальном давлении 100 атм (а), а также при 80°С со стартовым значением давления 50 атм (б).
Рис. 3.
Профиль реакции гидроформилирования модельной смеси 1: (а) при температуре 60°С и начальном давле-нии 100 атм, S/Rh = 1600; (б) при температуре 80°С и давлении 50 атм, S/Rh = 800. Условия реакции: Rh(acac)(CO)2 – 4 мг, PPh3 – 12 мг, толуол – 4 мл, гептан – 0.6 мл, скорость нагрева 3°С/мин.

Снижение конечной температуры проведения реакции с 80 до 60°С приводит к некоторому увеличению времени полной конверсии этилена (TOF = 6000 ч–1) и образованию смеси диэтилкетона и пропаналя в соотношении 1 : 10. Проведение аналогичной реакции с выдерживанием реакционной среды при конечной температуре 120°С способствует протеканию альдольной конденсации с образованием альдоля (С); его содержание в конечной смеси достигает 48%. При снижении стартового давления смеси 1, подаваемой в реактор, до 50 атм, профиль реакции и ее селективность меняются незначительно.
Гидроформилирование модельных смесей 1 и 2 позволило оценить влияние избытка водорода на скорость и селективность реакции (рис. 4).
Рис. 4.
Профиль реакции гидроформилирования модельных смесей 1 и 2. Условия реакции: Rh(acac)(CO)2 – 4 мг, PPh3 – 12 мг, S/Rh = 800, толуол – 4 мл, гептан – 0.6 мл, Pнач = 50 атм, скорость нагрева 3°С/мин, Tк = 80°С.
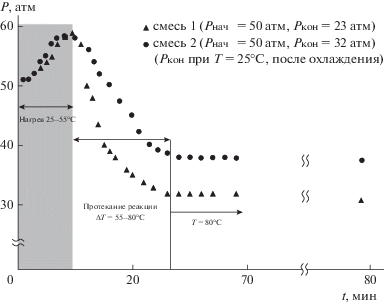
Избыток водорода способствует более глубокому протеканию реакции и увеличению селективности по пропаналю (до 99%). Остаточное давление газов смеси 2 (обогащенной метаном) составило 32 атм, из которых 20 атм – давление метана, а остальные 12 атм – давление газовой смеси этилена с монооксидом углерода и водорода, причем среди продуктов идентифицировано 20% диэтилкетона и 80% пропаналя. Более пологий наклон кривой изменения давления газов при гидроформилировании газовой смеси 2 также свидетельствует о более низкой скорости реакции для смеси, не обогащенной водородом, хотя для начала реакции требуется в обоих случаях одинаковая температура.
Модельная смесь 3 отражает примерный состав промышленных газовых смесей, обогащенных этиленом, причем этилен в таких смесях содержится в избытке относительно количества как монооксида углерода, так и водорода. В работе проведено гидроформилирование модельной смеси 3 на родий-фосфиновом катализаторе (Rh(acac)(CO)2 + PPh3) в среде толуола при температурах 60 и 80°С (табл. 4). В данном случае, наряду с пропаналем, образовывался диэтилкетон (15 и 20%, соответственно).
Таблица 4.
Гидроформилирование модельной смеси 3 при температурах 60 и 80°С*
T, °C | Pнач, атм | Pкoн, атм | Конверсия этилена, % | Селективность реакции, % | TOF, ч–1 | |
---|---|---|---|---|---|---|
пропаналь (А) | диэтилкетон (B) | |||||
60 | 75 | 40 | 78 | 85 | 15 | 3700 |
80 | 75 | 35 | 90 | 80 | 20 | 6500 |
Полученные экспериментальные данные по гидроформилированию модельных смесей 1–3 позволяют сделать вывод, что промышленные газовые смеси, обогащенные инертными УВ (в частности, метаном), могут быть переработаны в различные оксигенаты гидроформилированием на родий-фосфиновом катализаторе; при этом приемлемые показатели по скорости реакции и ее селективности по пропаналю достигаются при проведении реакции при температурах 60–80°С и стартовых давлениях газовой смеси 50–100 атм. Участкам кривых поглощения газов с наибольшим углом наклона соответствует производительность каталитической системы с показателями TOF, равными 3500–9500 ч–1. Гомогенный катализатор в приведенных примерах может быть отделен от продуктов реакции только способом дистилляции, который имеет известные недостатки, в связи с этим в работе исследовано гидроформилирование модельной смеси 1 с использованием представленных ниже фосфиновых лигандов, позволяющих выделить каталитическую систему из гомогенных сред альтернативными способами:
PEG-PPh3 – макромолекулярный лиганд, синтезированный путем модификации полиэтиленгликоля со средней молекулярной массой 3000 г/моль, TPPTS – натриевая соль трисульфированного трифенилфосфина. Макромолекулярный лиганд PEG-PPh3, как было установлено ранее [26], может быть выделен из реакционной среды нанофильтрацией на мембранах, размер пор которых не превышает 2 нм. TPPTS является известным водорастворимым лигандом; с его использованием гидроформилирование проводят в двухфазной системе вода – органический растворитель [27].
На рис. 5 представлено сравнение профилей протекания реакции с различными каталитическими системами. Начало реакции для случая с TPPTS несколько смещено в область более высоких температур (начало реакции при Т ≈ 70°C), и при низких концентрациях реагентов замедление скорости более существенно, чем в случаях с PPh3 и PEG-PPh3. Это может быть объяснено наличием воды в системе, и тем, что катализатор находится в водной фазе. Растворимость реагентов в такой системе ниже, чем в чистом толуоле, и лимитирующей скорость стадией может быть трансфер реагентов на поверхность раздела фаз, где протекает каталитическая реакция. Варьирование лиганда не влияет на селективность реакции, и в качестве основного продукта в жидкой фазе в каждом случае был идентифицирован пропаналь (98–99%).
ВЫВОДЫ И ДАЛЬНЕЙШИЕ ИССЛЕДОВАНИЯ
В ходе работы определены оптимальные условия проведения гидроформилирования этиленсодержащих газовых смесей, обогащенных инертными газами. Рассмотренным в статье каталитическим системам может быть сопоставлен процесс (табл. 5), который позволит осуществлять данную стадию комбинированной переработки нефтезаводских газов в оксигенаты с наибольшей производительностью и наименьшими затратами. Установлено, что при гидроформилировании на родий-фосфиновых катализаторах смесей, обогащенных водородом, в качестве основного продукта образуется пропаналь (до 99%), а образование диэтилкетона (до 20%) происходит при наличии мольного избытка этилена к СО в смеси.
Работа выполнена при финансовой поддержке Минобрнауки России (Соглашение о предоставлении субсидии № 14.607.21.0171, идентификатор RFMEFI60717X0171).
Список литературы
Melero J. A., Iglesias J., Garcia A. // EnergyEnviron. Sci. 2012. V. 5. P. 7393.
Luo X.B., Wang M.H., Li X.G., Li Y., Chen C., Sui H. // Fuel. 2015. V. 158. P. 424.
Li X.G., Li Y., Zhang L.H., Li H. // Chem. Eng. Res. Des. 2016. V. 109. P. 258.
Горбунов Д.Н., Теренина М.В., Кардашева Ю.С., Максимов А.Л., Караханов Э.А. // Нефтехимия. 2017. Т. 57. № 6. С. 759 [Petrol. Chemistry. 2017. V. 57. № 12. P. 1137].
Wang D.L., Feng X. // Int. J. Hydrogen Energy. 2013. V. 38. P. 12 968.
Никитин А.В., Седов И.В., Озерский А.В., Афаунов А.А., Артамонова Н.Е., Арутюнов В.С. // В сб. тезисов. XII Международной конференции молодых ученых по нефтехимии. г. Звенигород. 17–21 сентября 2018 г. С. 531.
Магомедов Р.Н., Никитин А.В., Савченко В.И., Арутюнов В.С. // Кинетика и катализ. 2014. Т. 55. № 5. С. 584.
Arutyunov V.S., Savchenko V.I., Sedov I.V., Fokin I.G., Nikitin A.V., Strekova L.N. // Chem. Engineering J. 2015. V. 282. P. 206.
Арутюнов В.С., Савченко В.И, Седов И.В., Шмелев В.М., Никитин А.В., Фокин И.Г., Эксанов С.А., Шаповалова О.В., Тимофеев К.А. // ЖПХ. 2016. Т. 89. № 11. С. 1450.
Никитин А.В., Озерский А.В., Тимофеев К.А., Комаров И.К., Зимин Я.С., Седов И.В., Шмелев В.М., Арутюнов В.С. // Горение и взрыв. 2018. Т. 11. № 2. С. 18.
Hu C., Wu J., Zhang H., Qin S. // AIChE J. 2007. V. 53. № 11. P. 2925.
Liu D., Chaudhari V.R., Subramaniam B. // Chem. Eng. Sc. 2018. V. 187. P. 148.
Liu D., Xie Z., Snavely W.K., Chaudhari V.R., Subramaniam B. // React. Chem. Eng. 2018. V. 3. P. 344.
Jin H., Subramaniam B. // Chem. Eng. Sc. 2004. V. 59. P. 4887.
Liu D., Chaudhari V.R., Subramaniam B. // AIChE J. 2018. V. 64. P 970.
Subramaniam B., Chaudhari V.R., Chaudhari S.A., Akien G.R., Xie Z. // Chem. Eng. Sc. 2014. V. 115. P. 3.
Caporali M., Frediani P., Piacenti F., Salvini A. // J. Mol. Cat. A: Chem. 2003. V. 204–205. P. 195.
Варшавский Ю., Черкасова Т. // Нефтехимия. 1967. Т. 12. С. 1709
Озерский А.В., Никитин А.В., Седов И.В., Фокин И.Г., Савченко В.И., Арутюнов В.С. // ЖПХ. 2018. Т. 91. № 12. С. 1790.
Hydroformylation: Fundamentals, Processes, and Applications // In Organic Synthesis, First Ed. Börner A., Franke R. Wiley-VCH Verlag GmbH & Co, 2016. P. 1.
Горбунов Д.Н., Волков А.В., Кардашева Ю.С., Максимов А.Л., Караханов Э.А. // Нефтехимия. 2015. Т. 55. № 6. С. 443.
Rosler T., Fassbach T., Schrimpf M., Vorholt A., Leitner W. // Ind. &Eng. Chem. Res. 2019. V. 58. № 7. P. 2421.
Marinkovic J., Riisager A., Franke R. // Ind. & Eng. Chem. Res. 2019. V. 58. № 7. P. 2409.
Руш С.Н., Носков Ю.Г., Крон Т.Е., Корнеева Г.А. // Кинетика и катализ. 2009. Т. 50. № 4. С. 578.
Kiss G., Mozeleski E.G., Nadler K.C., van Driessche E., DeRoover C. // J. Mol. Cat. A: Chem. P. 1999. V. 138. P. 155.
Сафронова Д.С., Горбунов Д.Н., Караханов Э.А. // В сб. тезисов. XII Международная конференция молодых ученых по нефтехимии. г. Звенигород. 18–21 октября 2016. С. 235.
Horváth I., Kastrup R.V., Oswald A., Mozeleski A.E. // J. Catal. Let. 1989. V. 2. P. 85.
Рыбаков В.А., Елькин А.Л., Тюкавин Г.Н., Лурия В.Б., Рябов В.Г. // Технология оксосинтеза и родственных процессов с участием окиси углерода. Пермь: Сибур-Химпром, 2004. 229 С.
Cornils B., Fischer R.W., Kohlpaintner C. Butanals. In Ullmann’s Encyclopedia of Industrial Chemistry. 2000.https://doi.org/10.1002/14356007.a04_447
Lejeune A., Rabiller-Baudry M., Renouard T., Balannec B., Liu Y., Augello J., Wolbert D. // Chem. Eng. Sc. 2018. V. 183. P. 240.
Дополнительные материалы отсутствуют.