Нефтехимия, 2019, T. 59, № 5, стр. 552-559
СИНТЕЗ НОВЫХ АЛИФАТИЧЕСКИХ УГЛЕВОДОРОДНЫХ СМОЛ НА ОСНОВЕ ИЗОПРЕНА
В. А. Розенцвет 1, *, В. Г. Козлов 1, Н. А. Саблина 1, Д. М. Ульянова 1, А. А. Стыценков 2
1 Институт экологии Волжского бассейна РАН
445003 Тольятти, Россия
2 ООО “Биком”
446026 Сызрань, Россия
* E-mail: rozentsvet@mail.ru
Поступила в редакцию 20.12.2018
После доработки 10.04.2019
Принята к публикации 13.05.2019
Аннотация
В работе исследована катионная олигомеризация изопрена под действием широкого круга каталитических систем на основе различных кислот Льюиса. Установлена возможность синтеза на каталитической системе TiCl4–трет-бутилхлорид полностью растворимых олигомеров изопрена во всем интервале конверсий мономера. Определены условия получения олигомеров изопрена с температурой размягчения 100–120°С, характерной для алифатических углеводородных смол. Разработанный метод получения алифатических смол на основе изопрена характеризуется простой технологией и возможностью регулирования температуры размягчения смол в ходе процесса.
Алифатические углеводородные смолы – низкомолекулярные термопластичные полимеры с температурой размягчения на уровне от 80 до 120°С [1–3]. В ряде публикаций алифатические углеводородные смолы (АУС) называют “нефтеполимерными” [3]. На наш взгляд, этот термин используется не корректно, так как исторически термином “нефтеполимерные смолы” обозначали продукты химической модификации гудронного остатка переработки нефти [4]. АУС находят широкое применение в производстве адгезивных полимерных композиций, клеевых слоев липких лент и этикеток, пластификаторов резиновых смесей, термопластичных красок для разметки дорог и т.д. [1–3]. Важным преимуществом АУС является высокая стойкость к атмосферному старению [1].
Традиционный метод получения АУС основан на катионной олигомеризации пиролизной С5-фракции, которая является побочным продуктом процесса пиролиза углеводородов (УВ) и представляет собой смесь диеновых, олефиновых и алифатических С5-УВ различного состава [1–3, 5]. Процесс получения АУС из пиролизной С5-фракции является технологически сложным, многостадийным и энергоемким [1–3, 5–9]. Например, для предотвращения гелеобразования на стадии олигомеризации необходимо удаление из С5-фракции циклопентадиена, а также строгое регулирование соотношения диеновых и олефиновых УВ. В этой связи выход АУС, как правило, не превышает 35–40% в расчете на исходную С5-фракцию [7–9]. Это приводит к значительному увеличению стоимости АУС, которая в 2–3 раза превышает цену на каучуки общего назначения, например на синтетический полизопреновый каучук марки СКИ-3.
Характерной особенностью пиролизных С5-фракций российских нефтехимических предприятий является относительно высокое содержание диеновых УВ, составляющее в ряде случаев 50 мас. % и более от общего количества УВ [10]. Использование пиролизных фракций, обогащенных диеновыми УВ, требует при получении АУС разработки специальных методов подготовки мономерной смеси. Это одна из причин того, что производство АУС в России отсутствует, и значительное количество этих полимеров импортируется из-за рубежа.
В литературе описан также и иной подход к получению углеводородных смол. Например, производство ароматических углеводородных смол методом катионной олигомеризации с использованием “чистых” мономеров, такие как стирол или α-метилстирол [1, 11]. Преимущества такого подхода – высокий выход и возможность контролирования молекулярных и физико-химических характеристик ароматических смол. Кроме того, в литературе имеется значительное количество публикаций, посвященных исследованию процесса катионной олигомеризации изопрена [2, 12–17]. Анализ данных публикаций показывает, что во всех случаях, независимо от природы каталитических систем и условий полимеризации, были получены жидкие олигомерные продукты, не находящие практического применения. Кроме того, при глубоких конверсиях изопрена, как правило, наблюдалось формирование в составе олигомера сшитой нерастворимой фракции.
В настоящем исследовании впервые описана катионная олигомеризация изопрена с получением смол, характеризующихся высокой температурой размягчения и соответствующих требованиям, предъявляемым к АУС. Цель работы – разработка нового, технологически простого способа синтеза АУС, основанного на катионной олигомеризации изопрена. В рамках поставленной цели задачами исследования являлись поиск способов получения полностью растворимых олигомеров изопрена с контролируемыми температурами размягчения, а также выбор оптимальных параметров процесса катионной олигомеризации, обеспечивающих полную конверсию изопрена за технологически удобное время.
ЭКСПЕРИМЕНТАЛЬНАЯ ЧАСТЬ
В работе в качестве мономеров использовали изопрен и 1,3-пентадиен производства ОАО “Синтез каучук” (г. Стерлитамак) с содержанием основного вещества 97.0 мас. % и бутадиен производства ООО “СИБУР ТОЛЬЯТТИ” (г. Тольятти) с содержанием основного вещества 99.6 мас. %. Кислоты Льюиса: AlCl3 (Sigma-Aldrich, >99.0%), VOCl3 (Aldrich, >99.8%), ZnBr2 (Merck, >98.0%), ZnCl2 (Merck, >98.0%), BF3·O(C2H5)2 (Fluka, >99.0%), TiCl4 (Merck, >99.9%), а также трифторуксусная кислота (CF3COOH, Aldrich, >99.5%) были использованы без дополнительной очистки. Комплекс Густавсона (AlCl3 ⋅ м-ксилол ⋅ 0.5HCl) получали по методике, описанной в работе [10]. Хлористый метилен (CH2Cl2, Biosolve, >99.0%), и трет-бутилхлорид (ТБХ, Fluka, >99.5%) перегоняли над CaH2 в токе аргона. Приготовление каталитических систем и олигомеризацию изопрена проводили в атмосфере аргона в предварительно прогретых в вакууме стеклянных ампулах по методикам наших работ [18, 19]. Выход олигомера определяли гравиметрически.
Нерастворимую фракцию (НФ) в олигомере отделяли от растворимой фракции центрифугированием раствора олигомера в толуоле. Содержание НФ в олигомере определяли дополнительной экстракцией толуолом осадка после центрифугирования в аппарате Сокслетта в течение 24 ч. Перед проведением анализов по определению молекулярных характеристик и микроструктуры олигомеры очищали от остатков катализатора методом колоночной хроматографии на силикагеле марки Silica gel 60 (Fluka). Молекулярные характеристики олигомера (Mn – среднечисленная, Mw – среднемассовая молекулярные массы, Mw/Mn – полидисперсность) определяли методом гель-проникающей хроматографии на жидкостном хроматографе “Alliance GPCV-2000” фирмы “Waters”, снабженным рефрактометрическим и вискозиметрическим детекторами и набором из четырех стирогелевых колонок “Waters” с размером пор 500 (HR-2), 103 (HR-3), 104 (HR-4) и 105 (HR-5) Å. Элюент – толуол, температура 30°С, скорость элюирования 0.5 мл/мин. Расчет молекулярных характеристик проводили на основе универсальной калибровки по полистирольным стандартам фирмы “Waters” [20, 21].
13С ЯМР-спектры олигомеров изопрена регистрировали на спектрометре “Bruker Avance-600” с числом накоплений сигналов не менее 8000 и задержкой между импульсами 12 с. Образцы готовили в виде 10–12 мас. % растворов в CDCl3. Ненасыщенность (Н) и содержание структурных звеньев в олигомерах изопрена определяли по данным 13С ЯМР-спектров по методикам, описанным ранее в нашей работе [22]. Температуру размягчения (Тр) олигомеров определяли методом “кольца и шара” (КИШ) по ГОСТ 11506-73, термомеханические характеристики олигомеров определяли на приборе ТМ-2 при нагрузке 2.7 г/мм2, плотность, пенетрацию и водопоглащение полимерных композиций с использованием АУС – по ГОСТ 25945-98, прочность связи полимера с бетоном и металлом – по ГОСТ 209-75.
РЕЗУЛЬТАТЫ И ИХ ОБСУЖДЕНИЕ
Систематическое исследование катионной полимеризации сопряженных диенов позволило авторам разработать ряд эффективных способов получения полностью растворимого поли-1,3-пентадиена, полибутадиена и полиизопрена [18–20, 22–26]. В ходе исследований было установлено, что из всех синтезированных авторами “катионных” олигодиенов только олигоизопрен, полученный методом катионной олигомеризации, характеризуется высокой температурой размягчения. В этой связи основное внимание в данной работе было уделено изучению процесса катионной олигомеризации изопрена. В настоящей работе была исследована олигомеризация изопрена на каталитических системах, представленных в табл. 1.
Таблица 1.
Влияние природы кислоты Льюиса (КЛ) и инициатора полимеризации (ИП) на конверсию изопрена (К), содержание нерастворимой фракции (НФ), молекулярные характеристики и температуру размягчения (Тр) олигомеров изопрена. Условия: [С5Н8] = 2.0 моль/л, [КЛ] = 1.5 × 10–2 моль/л, 20°С, хлористый метилен
Каталитическая система | Время, ч | К, мас. % | НФ, мас. % | Молекулярные характеристики |
Тр, °C | |||
---|---|---|---|---|---|---|---|---|
КЛ | ИП | ИП/КЛ, моль/моль | ||||||
Mn × 10–3, г/моль | Mw/Mn | |||||||
AlCl3 | – | – | 0.5 | 29.4 | 11.7 | – | – | – |
(CH3)3CCl | 20 | 0.5 | 75.8 | 52.3 | – | – | – | |
1КГ | – | – | 0.5 | 69.0 | 41.0 | – | – | – |
(CH3)3CCl | 50 | 0.5 | 96.7 | 59.6 | – | – | – | |
– | – | 0.5 | 37.3 | 0 | 4.5 | 16.9 | <20 | |
VOCl3 | – | – | 2.0 | 70.4 | 12.7 | – | – | – |
CF3COOH | 2 | 0.5 | 25.3 | 0 | 3.6 | 8.2 | <20 | |
(CH3)3CCl | 10 | 0.5 | 56.1 | 0 | 3.9 | 12.7 | <20 | |
50 | 0.5 | 84.9 | 6.2 | – | – | – | ||
2ZnBr2 | HCl | 10 | 1.0 | 85.2 | 0 | 0.6 | 2.8 | <20 |
(CH3)3CCl | 50 | 1.0 | 59.5 | 0 | 0.6 | 3.7 | <20 | |
100 | 1.0 | 92.5 | 0 | 0.6 | 4.0 | <20 | ||
BF3 ⋅ O(C2H5)2 | – | – | 1.0 | 29.1 | 0 | 1.0 | 2.9 | <20 |
– | – | 48.0 | 89.3 | 0 | 2.5 | 10.6 | 94 | |
CF3COOH | 5 | 1.0 | 54.3 | 0 | 0.8 | 2.8 | 32 | |
12.0 | 82.1 | 0 | 1.0 | 4.0 | 91 | |||
24.0 | 99.7 | 0 | 2.3 | 9.7 | 106 |
Катионные каталитические системы состояли из кислоты Льюиса и инициаторов полимеризации, однако в ряде случаев инициатор не вводился в систему (табл. 1). В этом случае роль инициатора процесса выполняли микропримеси воды и других кислородсодержащих соединений, которые невозможно удалить из исходных реагентов в процессе их очистки [11]. Из табл. 1 видно, что олигомеризация изопрена в присутствии AlCl3 приводит к получению олигомера, содержащего нерастворимую фракцию даже при невысоких конверсиях мономера. Введение в реакционную массу в качестве инициатора трет-бутилхлорида (ТБХ) увеличивает выход олигомера, но одновременно возрастает и содержание НФ в олигомере. Сходные результаты по содержанию НФ в олигомере получены и при олигомеризации изопрена на комплексе Густавсона. Олигомеризация изопрена в присутствии окситрихлорида ванадия без введения инициатора в систему позволяет синтезировать полностью растворимый олигомер только при конверсиях изопрена менее 70%. Добавление в ванадиевую каталитическую систему в качестве инициатора трифторуксусной кислоты снижает выход олигомера, а введение ТБХ, хотя и активирует процесс олигомеризации, но не позволяет получить полностью растворимый олигомер при высоких конверсиях мономера.
Каталитические системы ZnBr2–HCl и ZnBr2–(CH3)3CCl обеспечивают получение полностью растворимого олигомера изопрена во всем интервале конверсий мономера, но полученные олигомеры характеризуются наиболее низкими значениями Mn, а температура размягчения не достигает и 20°C. Аналогичные результаты были получены на каталитических системах на основе ZnCl2. Полностью растворимые олигомеры были также синтезированы при олигомеризации изопрена под действием каталитических систем на основе эфирата трифторида бора, как при отсутствии специально вводимого инициатора, так и при добавлении трифторуксусной кислоты. Важно отметить, что каталитические системы на основе BF3 ⋅ O(C2H5)2 при высоких конверсиях мономера обеспечивают получение растворимого олигомера с высокой температурой размягчения, достигающей 106°С. Недостаток данного типа каталитических систем – неудовлетворительная скорость олигомеризации изопрена. Хотя добавка в каталитическую систему трифторуксусной кислоты заметно активирует олигомеризацию изопрена, продолжительность процесса до полной конверсии мономера составляет 24 ч, что технологически не приемлемо для производства.
В табл. 2 представлены результаты по олигомеризации изопрена на каталитической системе TiCl4–CF3COOH. При исходной концентрации мономера 2.0 моль/л во всем интервале конверсий изопрена был получен полностью растворимый олигомер. С ростом конверсии мономера наблюдается увеличение полидисперсности, уменьшение ненасыщенности и возрастание температуры размягчения олигомера.
Таблица 2.
Результаты олигомеризации изопрена под действием TiCl4–CF3COOH. Условия: 20°С, [TiCl4] = 1.5 × × 10–2 моль/л, CF3COOH/TiCl4 = 2.0, хлористый метилен. Н – мол. % двойных связей в олигоизопрене от теоретического содержания (ненасыщенность)
[С5Н8], моль/л | Время, мин | Конверсия изопрена, К, мас. % | Нераствор. фракция, НФ, мас. % | Молекулярные характеристики |
Н, мол. % | Тр, °C | |
---|---|---|---|---|---|---|---|
Mn × 10–3, г/моль | Mw/Mn | ||||||
2.0 | 0.5 | 48.4 | 0 | 2.2 | 3.5 | 58 | <20 |
5.0 | 60.0 | 0 | 2.5 | 4.6 | 56 | <20 | |
30.0 | 73.5 | 0 | 2.8 | 6.5 | 53 | 64 | |
240.0 | 94.5 | 0 | 3.0 | 17.2 | 50 | 92 | |
1440.0 | 99.7 | 0 | 3.0 | 20.6 | 47 | 112 | |
4.0 | 0.5 | 39.8 | 0 | 4.6 | 3.6 | 61 | <20 |
5.0 | 55.9 | 41.3 | – | – | – | – |
При конверсиях мономера, близких к 100%, был получен олигоизопрен с необходимой температурой размягчения 112°C. Недостатком данной каталитической системы, как и в случае систем на основе BF3 ⋅ O(C2H5)2, является большая продолжительность процесса (24 ч), обеспечивающая достижение количественного выхода олигомера с необходимой температурой размягчения. Кроме того, при повышении исходной концентрации изопрена до 4.0 моль/л наблюдалось образование сшитого олигомера (табл. 2).
Установлено, что замена инициатора полимеризации – трифторуксусной кислоты на трет-бутилхлорид (ТБХ) позволяет синтезировать на “титановой” каталитической системе полностью растворимый олигомер во всем интервале конверсий изопрена даже при исходной концентрации мономера 4.0 моль/л. Для этого в ходе синтеза олигомера необходимо поддерживать соотношение ТБХ к TiCl4 в реакционной массе не менее 50 (табл. 3). Повышение концентрации ТБХ в системе значительно увеличивает скорость олигомеризации изопрена и при мольном соотношении (CH3)3CCl к TiCl4, равном 360, полная конверсия мономера достигается за 2 ч процесса. Как видно из табл. 3, олигомер изопрена, синтезированный при глубоких степенях превращения мономера, характеризуется температурой размягчения на уровне 100–120°С, что и требуется для алифатических смол. Обнаруженная закономерность повышения значений Тр олигомеров с ростом конверсии изопрена подтверждается исследованием термомеханических свойств полученных олигомеров изопрена.
Таблица 3.
Результаты олигомеризации изопрена под действием TiCl4 – (CH3)3CCl. Условия: 20°С, [TiCl4] = 1.5 × × 10–2 моль/л, [С5Н8] = 4.0 моль/л, хлористый метилен
(CH3)3CCl/TiCl4, моль/моль | Время, мин | Конверсия изопрена, К, мас. % | Нераствор. фракциия, НФ, мас. % | Молекулярные характеристики | Н, мол. % | Тр, °C | |
---|---|---|---|---|---|---|---|
Mn × 10–3, г/моль | Mw/Mn | ||||||
10.0 | 30.0 120.0 240.0 |
18.7 52.2 77.8 |
0 0 0 |
1.7 1.8 2.4 |
3.2 4.9 7.4 |
72 61 55 |
<20 <20 32 |
1440.0 | 92.6 | 36.9 | – | – | – | – | |
50.0 | 30.0 120.0 240.0 1440.0 |
40.5 89.1 94.5 99.8 |
0 0 0 0 |
1.7 1.9 2.3 2.5 |
4.1 5.3 7.8 8.7 |
70 53 51 49 |
<20 96 108 112 |
360.0 | 5.0 30.0 60.0 120.0 240.0 |
19.5 70.1 91.1 99.9 100.0 |
0 0 0 0 0 |
1.3 1.6 1.7 1.8 1.8 |
3.5 4.7 4.8 4.9 5.1 |
72 54 52 50 47 |
<20 75 99 112 120 |
На рис. 1 приведены зависимости величины деформации олигомеров, синтезированных при различных конверсиях изопрена, от температуры. С ростом конверсии мономера наблюдается возрастание температуры текучести (Тт) олигомеров изопрена, что соответствует увеличению температур размягчения данных олигомеров, измеренных методом “кольца и шара” (табл. 3). Так, при конверсии мономера 19.5 мас. % значения Тт составляет минус 22°С, а значения Тр – ниже 20°С, для конверсии мономера 70.1 мас. % значения Тт и Тр составляют 32 и 75°С соответственно и для конверсии изопрена 99.9 мас. % значения Тт и Тр составляют 78 и 112°С соответственно. Следует отметить, что для последнего полимера на термомеханической кривой наблюдается слабо выраженная область высокоэластического состояния в интервале температур от 48 до 78°С (рис. 1, кривая 3). Сопоставление значений ненасыщенности олигомера и его температуры размягчения позволяет сделать вывод, что высокая Тр олигомера достигается только при уровне ненасыщенности 50 мол. % и ниже (табл. 2 и 3).
Рис. 1.
Зависимость деформация олигомеров изопрена, синтезированных на каталитической системе Ti-Cl4–трет-бутилхлорид, от температуры при различной конверсии мономера: 1 – 19.5, 2 – 70.1 и 3 – 99.9 мас. %. Условия олигомеризации: 20°С, [TiCl4] = = 1.5 × 10–2 моль/л, ТБХ/TiCl4 = 360 моль/л, [С5Н8] = 4.0 моль/л.
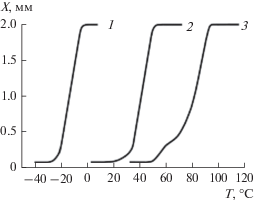
Для “цинковых” систем ненасыщенность синтезированного олигомера даже при глубоких степенях превращения мономера не снижалась ниже уровня 60 мол. %, видимо именно поэтому Тр олигоизопрена находится на низком уровне (табл. 1). Для олигомера изопрена, полученного на основе эфирата трифторида бора, высокие значения Тр также наблюдались для олигомеров с уровнем ненасыщенности 50 мол. % и менее (конверсия мономера более 80 мас. %, табл. 1). Для “катионных” олигомеров 1,3-пентадиена и бутадиена, синтезированных на изученных каталитических системах (табл. 1–3), такой низкий уровень ненасыщенности не наблюдался даже при высоких конверсиях мономера, поэтому значения Тр для этих олигомеров всегда оставались на неудовлетворительном уровне.
При мольном соотношении (CH3)3CCl к TiCl4 в системе, равном 360 (табл. 3) ТБХ фактически является единственным растворителем в реакционной массе, т.е. процесс олигомеризации изопрена протекает в среде трет-бутилхлорида. Так как ТБХ имеет относительно низкую температуру кипения (51°С), то получаемый олигомер изопрена может быть легко дегазирован на стадии выделения, а отогнанный ТБХ возвращен на стадию олигомеризации. Таким образом, трет-бутилхлорид в предлагаемом процессе получения АУС на основе изопрена выполняет двоякую роль – инициатора реакции олигомеризации и растворителя процесса.
Особенностью реакции катионной олигомеризации сопряженных диенов является выраженный нестационарный характер процесса [2, 18, 19]. Как правило, наиболее высокая скорость реакции наблюдается на начальном этапе, когда за первые секунды процесса выход олигомера достигает уровня 50 мас. % и более (табл. 2). Это ведет к сложностям при отводе тепла процесса и, в ряде случаев, перегреву реакционной массы. Важным преимуществом предлагаемой каталитической системы TiCl4–(CH3)3CCl является стационарный характер процесса олигомеризации изопрена (рис. 2, зависимости 1–3).
Рис. 2.
Зависимость конверсии изопрена (K) от продолжительности олигомеризации (t) под действием TiCl4–(CH3)3CCl (1–3) и TiCl4–CF3COOH (4) при мольном соотношении (CH3)3CCl к TiCl4, равном 10 (1), 50 (2) и 360 (3). Условия олигомеризации в табл. 2 и 3.
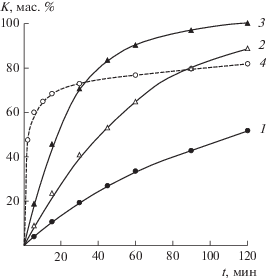
Как видно из линейного характера полулогарифмических анаморфоз конверсионных зависимостей от времени процесс олигомеризации изопрена характеризуется первым порядком по мономеру независимо от содержания трет-бутилхлорида в системе (рис. 3, зависимости 1–3). Для процесса олигомеризации изопрена на системе TiCl4–CF3COOH первый порядок реакции по мономеру не реализуется ни на одном этапе процесса (рис. 2, 3, зависимость 4).
Рис. 3.
Зависимости логарифма отношения исходной (M0) и текущей (Mt) концентраций мономера от продолжительности олигомеризации изопрена (t) под действием TiCl4–(CH3)3CCl (1–3) и TiCl4–CF3COOH (4) при мольном соотношении (CH3)3CCl к TiCl4, равном 10 (1), 50 (2) и 360 (3). Условия олигомеризации в табл. 2 и 3.
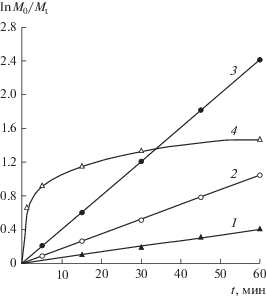
Строение макромолекулярной цепи олигомеров изопрена, синтезированных на каталитической системе TiCl4–(CH3)3CCl определялось методом 13С ЯМР-спектроскопии (рис. 4). С использованием методики расчета содержания структурных звеньев, представленной в нашей работе [22], установлено, что ненасыщенная часть цепи олигоизопрена на 94 мол. % состоит из 1,4-транс-звеньев с различным типом присоединения (“голова–хвост”, “голова–голова” и “хвост–хвост”), 3 мол. % составляют 1,2-звенья и 3 мол. % – 3,4-звенья, 1,4-цис-звенья не обнаружены.
Рис. 4.
Алифатическая область 13С ЯМР-спектра олигоизопрена, синтезированного на каталитической системе Ti-Cl4–(CH3)3CCl.
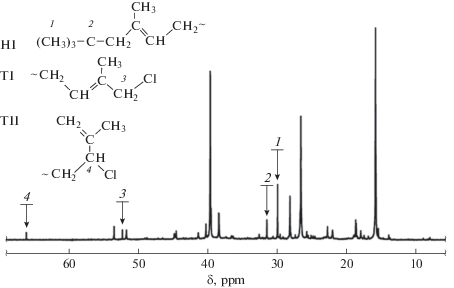
Кроме того, на 13С ЯМР спектре (рис. 4) идентифицированы сигналы начальных трет-бутильных звеньев (HI) и двух типов концевых хлорсодержащих звеньев (TI и TII), связанных с макромолекулярной цепью олигоизопрена [22].
При использовании АУС в термопластичных красках для разметки дорог в зависимости от температуры окружающей среды существует необходимость использования смол с различной температурой размягчения. В этой связи актуальной задачей является разработка надежных способов регулирования Тр олигомеров изопрена, получаемых на каталитической системе TiCl4–(CH3)3CCl. Как видно из данных табл. 3 значения Тр олигомеров зависят от конверсии мономера, однако использование степени превращения мономера как способа регулирования значений Тр не является надежным и целесообразным. Поэтому были разработаны альтернативные методы регулирования температуры размягчения синтезированных полимеров. Установлено, что введение 1,3-пентадиена или бутадиена в исходную мономерную смесь на основе изопрена позволяет снижать Тр получаемых АУС (рис. 5). При этом в случае катионной соолигомеризации изопрена с 1,3-пентадиеном заметное уменьшение Тр наблюдается только при содержании 1,3-пентадиена в исходной мономерной смеси более 10 мас. % (рис. 5, зависимость 1). При введении в мономерную смесь бутадиена температура размягчения получаемого соолигомера снижается более значительно. Например, даже при 5 мас. % содержании бутадиена в смеси с изопреном значения Тр олигомера уменьшается со 112 до 81°С (рис. 5, зависимость 2). Добавки 1,3-пентадиена обеспечивают более плавное регулирование температур размягчения получаемых АУС.
Рис. 5.
Зависимость Тр олигомера от содержания изо-прена (С1) и второго сомономера (С2) в исходной мономерной смеси. Второй сомономер: 1 – 1,3-пентадиен, 2 – бутадиен. Условия: 20°С, [TiCl4] = 1.5 × × 10–2 моль/л, ТБХ/TiCl4 = 360 моль/л, [С1 + С2] = = 4.0 моль/л.
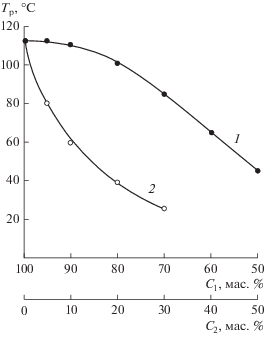
Важно отметить, что использование 1,3-пентадиена в процессе соолигомеризации с изопреном практически не оказывает влияния на скорость олигомеризации и выход полимера. Например, при соотношении изопрена к 1,3-пентадиену в мономерной смеси, равном 1 к 1, в условиях, приведенных на рис. 5, за 2 ч процесса наблюдается количественный выход соолигомера.
Образец АУС на основе изопрена, синтезированный при мольном соотношении (СH3)3CCl к TiCl4, равном 360, и продолжительности процесса 2 часа (табл. 3), был испытан в качестве компонента полимерной композиции для рулонных кровельных материалов на основе бутилкаучука. В табл. 4 приведены характеристики контрольной полимерной композиции с использованием АУС “Hikorez C-1100” (производство Южная Корея) и опытной партии композиции с применением АУС на основе изопрена.
Таблица 4.
Характеристики полимерных композиций для рулонных кровельных материалов на основе бутилкаучука с использованием различных АУС
Показатели качества | Композиция с АУС “Hikorez C-1100” | Композиция с АУС на основе изопрена |
---|---|---|
Плотность, кг/м3 | 1570 | 1500 |
Пенетрация, мм | 7.5 | 6.0 |
Водопоглощение, % | 0.1 | 0.1 |
Прочность связи с бетоном при отрыве, кг/см2 | 0.47 | 0.46 |
Прочность связи с металлом при отрыве, кг/см2 | 0.41 | 0.51 |
Результаты, представленные в табл. 4 показывают, что полимерная композиция с использованием АУС на основе изопрена по физико-механическим показателям не уступает композиции, полученной со смолой “Hikorez C-1100”, а по показателю “прочность связи с металлом при отрыве” заметно превышает показатель контрольной композиции. Наиболее вероятно, что повышенная прочность связи полимера с металлом связана с наличием в АУС на основе изопрена концевых хлорсодержащих групп (рис. 4).
Таким образом, разработан новый подход к синтезу полностью растворимых алифатических углеводородных смол с регулируемой температурой размягчения. Метод основан на катионной олигомеризации изопрена под действием каталитической системы TiCl4–трет-бутилхлорид. Преимуществами метода, по сравнению с традиционным способом получения АУС из пиролизной С5-фракции, являются использование мономера (изопрена) со стабильными показателями качества, относительно простая технология получения АУС и возможность эффективного регулирования температуры размягчения олигомера в ходе процесса. На основании проведенных испытаний показана возможность замены в полимерных композициях для получения рулонных кровельных материалов импортной АУС “Hikorez C-1100” на АУС на основе изопрена.
Работа выполнена при финансовой поддержке Российского фонда фундаментальных исследований (проект № 17-43-630945).
Список литературы
Mildenberg R., Zander M., Collin G. Hydrocarbon Resins. Weinheim: VCH, 1997. 175 p.
Розенцвет В.А., Козлов В.Г., Монаков Ю.Б. Катионная полимеризация сопряженных диенов. М.: Наука, 2011. 238 с.
Думский Ю.В., Но Б.И., Бутов Г.М. Химия и технология нефтеполимерных смол. М.: Химия, 1999. 302 с.
Алиев В.С., Альтман Н.Б. Синтетические смолы из нефтяного сырья. М.: Химия, 1965. 156 с.
Zohuriaan-Mehr M.J., Omidian H. // J. Macromol. Sci. 2000. V. C40(1). P. 23.
Berahman B., Darib B., Sadeghpour S. // Petrol. Sci. Technol. 2010. V. 28. P. 1277.
Lepert A. // Patent US No . 4068062. 1978 / Режим доступа: http://www. espacenet.com.
Small A.В., Hughes V.L., Benitez F.M. // Patent US No . 4391961. 1981 / Режим доступа: http://www.espacenet.com.
Benitez F.M., English M.F. // Patent US No . 4419503. 1983 / Режим доступа: http://www. espacenet.com.
Розенцвет В.А., Козлов В.Г., Саблина Н.А., Нестеров В.Н., Федорова З.Д., Мунасыпов Д.Н., Кирюхин А.М. // Нефтехимия. 2018. Т. 58. № 4. С. 487 [Petrol. Chemistry. 2018. V. 58. № 8. P. 694].
Kennedy J.P., Marechal E. Carbocationic Polymerization. Wiley: New York, 1982. 510 p.
Kostjuk S.V., Ouardad S., Peruch F., Deffieux A., Absalon C., Puskas J.E., Ganachaud F. // Macromolecules. 2011. V. 44. P. 1372.
Ouardad S., Lebarbe T., Deffieux A., Peruch F. // Polym. Chem. 2013. V. 4. P. 407.
Siu P.W., Hazin K., Gates D.P. // Chem. Eur. J. 2013. V. 19. P. 9005.
Ouardad S., Wirotius A., Kostjuk S.V., Ganachaud F., Peruch F. // RSC Adv. 2015. V. 5. P. 59 218.
Huang Y., He J., Cai G., Liu Z., Li T., Du T., Zhang S., Yao B., Li X. // J. Polym. Sci., Part A: Polym. Chem. 2017. V. 55. P. 1250.
Radchenko A.V., Bouchekif H., Peruch F. // Europ. Polym. J. 2017. V. 89. P. 34.
Rozentsvet V.A., Kozlov V.G., Stotskaya O.A., Sablina N.A., Peruch F., Kostjuk S.V. // Europ. Polym. J. 2018. 103. № 6. P. 11.
Розенцвет В.А., Козлов В.Г., Коровина Н.А., Новаков И.А. // Кинетика и катализ. 2015. Т. 56. № 2. С. 146 [Kinet. Catal. 2015. V. 56. №. 2. P. 132].
Розенцвет В.А., Козлов В.Г. // Изв. АН. Сер. хим. 2007. № 6. С. 1310 [Russ. Chem. Bull. (Int. Ed.). 2007. V. 56. № 7. P. 1359].
Benoit H., Grubisic Z., Rempp P., Dekker D., Zilliox J.G. // J. Chim. Phys. 1966. V. 63. P. 1507.
Rozentsvet V.A., Korovina N.A., Stotskaya O.A., Kuznetsova M.G., Peruch F., Kostjuk S.V. // J. Polym. Sci. Part A: Polym. Chem. 2016. V. 54. № 15. P. 2430.
Rozentsvet V.A., Kozlov V.G., Korovina N.A., Kostjuk S.V. // Macromol. Chem. Phys. 2013. V. 214. P. 2694.
Розенцвет В.А., Козлов В.Г., Саблина Н.А., Стоцкая О.А. // Изв. АН. Сер. хим. 2018. № 8. С. 1419 [Russ. Chem. Bull. (Int. Ed.). 2018. V. 67. № 8. P. 1419].
Rozentsvet V.A., Kozlov V.G., Ziganshina E.F., Boreiko N.P., Kostjuk S.V. // Polym. Int. 2013. V. 62. № 5. P. 817.
Rozentsvet V.A., Kozlov V.G., Sablina N.A., Stotskaya O.A., Peruch F., Kostjuk S.V. // Polym. Chem. 2017. V. 8. P. 926.
Дополнительные материалы отсутствуют.