Нефтехимия, 2019, T. 59, № 6-1, стр. 710-718
Углекислотная конверсия метана на наноразмерных порошках карбида вольфрама, полученных механохимическим и плазмо-механохимическим методами
Р. Р. Григорян 1, С. Г. Алоян 2, В. Р. Арутюнян 2, С. Д. Арсентьев 1, *, Л. А. Тавадян 1
1 Институт химической физики им. А.Б. Налбандяна НАН Республики Армения
0014 Ереван, Республика Армения
2 Институт общей и неорганической химии им. Г. Манвеляна НАН Республики Армения
0051 Ереван, Республика Армения
* E-mail: arsentiev53@mail.ru
Поступила в редакцию 07.04.2019
После доработки 10.07.2019
Принята к публикации 11.07.2019
Аннотация
Исследована каталитическая активность карбида вольфрама WC и смеси карбидов вольфрама (WC + W2C), полученных механохимическим и плазмо-механохимическим способами в реакции углекислотной конверсии метана при давлении 650 торр, соотношении CH4 : CO2 = 1 : 1 в интервале температур 400–960°С. Показано, что нано-порошок карбида вольфрама, со средним размером частиц 40 нм, полученный плазмо-механохимическим способом, имеет более высокую каталитическую активность в реакции углекислотной конверсии метана, чем катализатор, полученный механохимическим способом. Установлено также, что при уменьшении среднего размера частиц от 40 до 18 нм активность катализатора, полученного плазмо-механохимическим способом, возрастает и при 950°C конверсия метана достигает 55%.
Синтез-газ широко используется для промышленного производства химических продуктов, таких как оксигенаты (метанол, диметиловый эфир, синтетические моторные топлива и другие ценные кислородсодержащие соединения), в оксо-синтезе (синтез альдегидов, спиртов, кислот), в синтезе Фишера–Тропша [1].
Существуют различные методы превращения метана в синтез-газ. Наиболее распространeнным в промышленности является процесс паровой конверсии метана [2], который может быть представлен следующими балансовыми уравнениями:
(1)
$\begin{gathered} {\text{C}}{{{\text{H}}}_{{\text{4}}}} + {{{\text{H}}}_{{\text{2}}}}{\text{O}} \leftrightarrow {\text{CO}} + {\text{3}}{{{\text{H}}}_{{\text{2}}}} \\ {\Delta }{{H}^{{\text{0}}}}{\text{ = 206 кДж/моль,}} \\ \end{gathered} $(2)
$\begin{gathered} {\text{C}}{{{\text{H}}}_{{\text{4}}}} + {\text{2}}{{{\text{H}}}_{{\text{2}}}}{\text{O}} \leftrightarrow {\text{C}}{{{\text{O}}}_{{\text{2}}}} + {\text{4}}{{{\text{H}}}_{{\text{2}}}} \\ {\Delta }{{H}^{{\text{0}}}}{\text{ = 165 кДж/моль,}} \\ \end{gathered} $(3)
$\begin{gathered} {\text{CO}} + {{{\text{H}}}_{{\text{2}}}}{\text{O}} \leftrightarrow {\text{C}}{{{\text{O}}}_{{\text{2}}}} + {{{\text{H}}}_{{\text{2}}}} \\ {\Delta }{{H}^{0}} = {\text{ --41 кДж/моль}}{\text{.}} \\ \end{gathered} $В результате этого процесса получается синтез-газ с соотношением H2/CO = 1 : 3, которое не всегда оптимально для дальнейшего использования. В частности, для производства метанола требуется соотношение H2/CO = 1 : 2. Прямое получение синтез-газа с использованием каменного угля в качестве дешевого сырья не всегда приемлемо из-за низкого соотношения H2/CO в получаемом продукте.
Учитывая сказанное, становится очевидным растущий интерес к разработке альтернативных технологий получения синтез-газа. Одним из перспективных путей получения синтез-газа является углекислотная конверсия метана (УКМ). Она основана на каталитическом взаимодействии метана с диоксидом углерода [3–17]:
(4)
$\begin{gathered} {\text{C}}{{{\text{H}}}_{{\text{4}}}} + {\text{C}}{{{\text{O}}}_{{\text{2}}}} = {\text{2}}{{{\text{H}}}_{{\text{2}}}} + {\text{2CO}} \\ {\Delta }{{H}^{{\text{0}}}}{\text{ = 247}}{\text{.8}}\,\,{\text{кДж/моль}}{\text{.}} \\ \end{gathered} $Этот процесс позволяет превращать парниковые газы (CH4 и CO2) в промышленно важный продукт – смесь водорода с оксидом углерода. Использование этого процесса возможно также и для переработки биогаза [18, 19], причем в [18] в качестве катализатора использовался продукт, содержащий карбиды вольфрама (WC и W2C).
В последнее время в этой сфере большое внимание уделяется разработке перспективных катализаторов, основанных на использовании наноразмерных порошков. Благодаря своим малым размерам нанопорошки обладают рядом уникальных свойств, которые представляют интерес в различных областях науки [20, 21], в частности при создании активных и, в то же время, стабильных наноразмерных катализаторов углекислотной конверсии метана [22–27].
Следует отметить, что процесс углекислотной конверсии метана может служить эффективным путем утилизации газов, в частности углекислого газа, ответственного за парниковый эффект в атмосфере [5, 28].
Среди систем, используемых для УКМ, преобладают нанесенные гетерогенные катализаторы [3, 4, 23–25], активными компонентами которых являются химические элементы подгруппы железа (чаще всего кобальт и никель) или благородные металлы (менее предпочтительные из-за высокой стоимости) [25], а также карбиды вольфрама и молибдена [6–8, 25, 26].
В литературе имеется ряд работ, посвященных катализаторам УКМ. Так, в обзоре [27] для катализатора Pt/α-Al2O3 при 800°C приводятся конверсии метана и CO2, составляющие 25.6 и 31.1% соответственно. Для катализатора Rh/α-Al2O3 приводятся конверсии метана и CO2, составляющие 57.2 и 64.4% соответственно. Более высокие конверсии можно получить на сложных и доро-гих катализаторах. Например, катализатор Ni–Co/CaO–ZrO2 при 750°C за 1 ч обеспечивает конверсию метана и CO2 86.1 и 89.1%, соответственно [28]. В то же время, использование более дешевой подложки для катализатора Ni–Co/SiO2 резко снижает конверсию исходных реагентов до 16 и 30% [29]. В работе [30], при использовании катализаторов, полученных с использованием гидроталцидоподобных соединений, конверсии метана составляли 10.5–66.4, а CO2 – 14.4–70.3%. Соотношение H2/CO при этом колеблется в пределах 0.87–1.1.
Основным недостатком никелевых катализаторов является их быстрое закоксовывание углеродом, образующимся в ходе реакции при разложении метана и диспропорционировании СО, что приводит к снижению каталитической активности [18, 31, 32]. Уменьшить скорость закоксовывания никелевых катализаторов можно добавками благородных металлов, в частности рутения [27], однако это повышает их стоимость. В случае использования карбидов углерод практически не образуется и закоксовывание поверхности не происходит. Однако катализатор может деактивироваться из-за его окисления [3, 6–8, 33].
В настоящее время усилия исследователей направлены на преодоление указанных недостатков. Имеется возможность повысить активность катализаторов путем их перевода в ультрадисперсное состояние, что сопровождается увеличением удельной поверхности и способствует образованию каталитически активных дефектов структуры. Последнее может стать причиной изменения как количества, так и свойств активных центров поверхности.
Перспективными методами получения наноразмерных карбидов, металлов и их сплавов являются механохимический (МХ) и плазмо-механохимический (ПМХ) методы [21, 35–37]. Механическая обработка твердых смесей в вибромельницах приводит к дроблению и пластической деформации материала, ускоряет массообмен и перемешивание компонентов смеси на квазимолекулярном уровне, активирует химическое взаимодействие между твердыми реагентами [38].
В последнее время особое внимание уделяется методу плазмо-механохимического синтеза катализаторов, который сочетает механическое измельчение исходных твердых реагентов с непрерывным воздействием электрического разряда [37]. При использовании этого метода, электрический разряд проходит между частицами порошка и вибрирующими сферами, что создает особые условия для образования целевого наноразмерного продукта. Нанопорошки металлов и их сплавов, полученные этим методом, обладают уникальными свойствами.
Цель настоящего исследования – изучение процесса углекислотной конверсии метана на катализаторах, полученных на основе нанопорошков карбида вольфрама WC и смеси карбидов вольфрама WC + W2C, синтезированных механохимическим и плазмо-механохимическим методами.
ЭКСПЕРИМЕНТАЛЬНАЯ ЧАСТЬ
Синтез карбида вольфрама производился в специальном реакционном модуле, схематически представленном на рис. 1.
Рис. 1.
Реакционный модуль: 1, 2 – механореакторы, 3 – система подачи и отвода газов, 4 – вибромельница, 5 – тефлоновые торцы с электродами, 6 –генератор высоковольтных импульсов (конвертор).
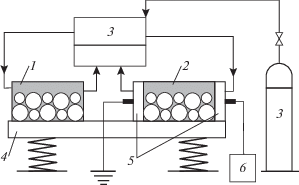
Модуль состоит из двух реакторов, которые представляют собой вибромельницы (4), механореакторы цилиндрической формы (1, 2), с внутренним диаметром 50 мм и длиной 100 мм, изготовленные из нержавеющей стали AISI310S и снабженные системой подачи и отвода газов (3). В качестве мелющих тел использовали металлические шары (сталь P6M5) диаметром 8 мм, заполняющие 3/4 объема реактора. Измельчение проводили в атмосфере аргона при частоте вибрации 25 Гц и амплитуде 4 мм в двух режимах: МХ (реактор 1) и ПМХ (реактор 2). Реактор 2 был снабжен двумя фторопластовыми торцами с полыми электродами (5) для непрерывной подачи газов и создания высоковольтных импульсов. Импульсы (30 кВ, 50 Гц, ток ~200 мкА) генерировались конвертором (6).
Синтез карбида вольфрама осуществляли с использованием оксида вольфрама (WO3) в присутствии восстановителей – магния и углерода. Применяли оксид вольфрама марки “х. ч.”, магний с чистотой 99.95% и размером частиц 50–80 нм и беззольный графит марки “о. ч.” в качестве углеродсодержащего реагента. Реагенты, взятые в стехиометрическом соотношении, предварительно, в течение трех часов, выдерживали в вакуумной печи (P = 10 Па, T = 120°C) с целью десорбции воздуха и влаги. Затем 20 г реакционной смеси помещали в каждый реактор реакционного модуля.
Механохимический (МХ) синтез проводили в течение 5–9 ч, в зависимости от требуемой степени измельчения. В частности, для получения нанопорошка WС (~40 нм) процесс измельчения длился ~8 ч.
Плазмо-механохимический (ПМХ) синтез состоял из двух последовательных стадий: первая стадия длительностью ~45 мин, обеспечивала активацию компонентов и протекание реакции; вторая стадия длительностью ~30–60 мин, с подачей высоковольтных импульсов, обеспечивала формирование нанокристаллитной структуры и полноту реакции.
Во всех случаях образование карбида фиксировали по резкому скачку температуры, измеряемой закрепленной в реакторе термопарой.
Получаемый продукт отмывали соляной кислотой (плотность 1.15 г/см3) и в растворе хлорной кислоты при кипячении, для удаления непрореагировавшего углерода. Данный метод позволяет получать нанопорошки, размер которых, в зависимости от длительности синтеза и других параметров, может изменяться в широком диапазоне.
Из нанопорошков WС, полученных методами МХ, ПМХ, а также смеси (WС + W2С) прессованием готовили таблетки диаметром 2 см и толщиной 0.15 см, которые дробили и отбирали фракцию размером 1–2 мм для изготовления образцов катализаторов.
Рентгенофазовый анализ полученных нанопорошков проводили на дифрактометре URD 63 (VEB “Carl Zeiss Jena”, DDR) с использованием излучения CuKα. Линии дифрактограмм идентифицировали по базе данных JCPDS-ICDD 2004. Морфологию карбидов вольфрама, полученных методами МХ и ПМХ, исследовали на просвечивающем электронном микроскопе TESLA-BS-500 (разрешение 3–5 Å, ускоряющее напряжение 90 кВ). Средний размер наночастиц определяли с использованием полученных TEM-изображений. Удельную поверхность определяли методом БЭТ с использованием прибора Accusorb 2300A (Micrometrics, USA). Элементный анализ образцов выполняли на энерго-дисперсионном микроанализаторе INCA Energy 300 (“OxfordInstruments”, England).
Каталитическую активность порошков в процессе углекислотной конверсии метана исследовали в проточных условиях при давлении 650 Торр. Навеску катализатора в 1.2 г смешивали с кварцевым боем (2–2.5 мм) и 1 см3 порошка помещали в U-образный реактор с внутренним диаметром 0.8 см, нагретый до 400–960°C. Затем смесь реагирующих газов при мольном соотношении CH4 : CO2 = 1 : 1 подавали в реактор с объемной скоростью 50 см3. Чистота метана и диоксида углерода составляла не менее 99%.
Исходные реагенты и продукты реакции анализировали методами ГЖХ. Анализ СН4, СО2, CH2O, Н2О и CH3OH проводили с использованием колонки, заполненной полимерным сорбентом Porapak N (длина 3 м, T = 118°C, Q = = 60 см3/мин, газ-носитель гелий). Метанол, этанол и ацетальдегид определяли на колонке, заполненной 20% ПЭГА, нанесенном на Хромосорб W (длина 3 м, T = 118°C, Q = 40 см3/мин, газ-носитель гелий). Анализ Н2, СО и СН4 проводили на колонке, заполненной молекулярным ситом 5 Å (длина 10 м, T = 50°C, Q = 10 см3/мин, газ-носитель аргон). В качестве детектора во всех случаях использовали катарометр.
РЕЗУЛЬТАТЫ И ИХ ОБСУЖДЕНИЕ
Эксперименты показали, что концентрации таких продуктов реакции, как формальдегид, метанол, этанол и ацетальдегид находятся ниже предела чувствительности хроматографического анализа, т.е. практически не образуются.
На рис. 2 приведены дифрактограммы нанопорошков WС и смеси (WС + W2С), полученные методами МХ и ПМХ. Можно видеть, что на рентгенограммах 2 и 4 присутствуют рефлексы, соответствующие рефлексам WС производства фирмы Alldyne Powder Technologies. Отметим, что коммерческий карбид вольфрама не предназначен производителем для каталитических процессов. Он приводится для того, чтобы показать, что без специальной обработки WC в качестве катализатора непригоден.
Рис. 2.
Дифрактограммы нанопорошков: 1 – WС(Alldyne Powder Technologies), 2 – WС(МХ) до УКМ, 3 – WС(МХ) после УКМ, 4 – WС(ПМХ) до УКМ, 5 – WС(ПМХ) после УКМ, 6 – 40%WС + 60%W2С (ПМХ) до УКМ, 7 – 40%WС + 60%W2С(ПМХ) после УКМ.
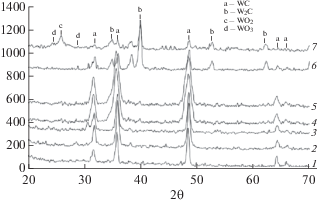
На дифрактограмме видно, что катализатор 40%WС + 60%W2С(ПМХ) после реакции содержит незначительное количество оксидов вольфрама (образец 7). Поскольку образование WO2 и WO3 из-за окисления в присутствии образующегося в ходе реакции водорода представляется сомнительным, можно предположить, что этот катализатор окисляется кислородом воздуха при его выгрузке.
Элементный анализ образца, изготовленного методом ПМХ, показал, что в продукте синтеза присутствуют 93 мас. % вольфрама, 6.7 мас. % С и 0.3 мас. % О2. Поскольку чистый WC состоит из 93.9% вольфрама и 6.1% углерода, то очевидно, что в получаемом образце содержится незначительное (менее 1%) количество свободного углерода.
Электронно-микроскопическая фотография порошка WC, полученного методом ПМХ, представлена на рис. 3.
Рис. 3.
Электронно-микроскопическая фотографияпорошка WC, полученного плазмо-механохимическим методом.
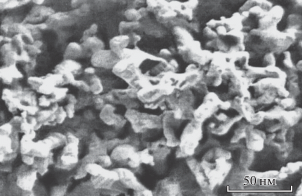
Как видно из снимка, в образце присутствует большое количество наноразмерных частиц. Для определения размеров кристаллов WC использовали формулу Дебая–Шеррера [39] .
Обработку данных проводили с помощью программы Origin Pro7.0. На основе дифракционных кривых, представленных на рис. 2, используя формулу Дебая–Шеррера, были рассчитаны размеры кристаллитов для θ = 17.88 (межплоскостное расстояние d = 2.52 Å) и θ = 24.215 (межплоскостное расстояние d = 1.88 Å). Размеры кристаллитов нанопорошков WC до и после реакции углекислотной конверсии метана приведены в табл. 1.
Таблица 1.
Размеры кристаллов, полученных методами МХ и ПМХ
Соединение | L, нм | |||
---|---|---|---|---|
до УКМ | после УКМ | |||
θ = 17.88 | θ = 24.215 | θ = 17.88 | θ = 24.215 | |
WC (Alldyne Powder Technologies) | 998 | 991 | – | – |
WC(МХ) | 40 | 41.1 | 43.3 | 43.5 |
WC(ПМХ) | 18 | 18 | 34 | 34.2 |
(WC + W2C)( ПМХ) | 40 | 41.2 | 46 | 46.1 |
WC(ПМХ) | 40 | 41.1 | 45.2 | 45.6 |
WC(ПМХ) | 35.7 | 36.0 | 40 | 41.2 |
WC(ПМХ) | 17.6 | 17.6 | 34 | 34.1 |
(WC + W2C)( ПМХ) | 37.3 | 37.5 | 43.3 | 43.5 |
Как видно из табл. 1, в результате реакции происходит увеличение размеров частиц катализатора, что, возможно, связано с образованием агломератов в результате протекания химического процесса. Размеры частиц после реакции были определены не менее, чем после 60 ч работы. При этом, при тестировании при T = 580–950°C катализаторов, изготовленных на основе порошков WC 40 нм, деактивации катализатора не наблюдалось в течение 60 ч.
Изменение размеров частиц видно также из гистограмм распределения размеров частиц WC, полученного методом ПМХ, до (а) и после (б) УКМ, которыепредставлены на рис. 4. В связи с тем, что частицы по форме не изотропны, в качестве размера принимался наибольший габарит частицы, измеряемый на электронно-микроскопической фотографии. В частности, для получения данных по распределению частиц WC со средним размером 40 нм до УКМ, полученных методом ПМХ, были измерены габариты 24 частиц в диапазоне 37.6–41.4 нм.
Рис. 4.
Гистограммы распределения по размерам частиц WC, полученных методом ПМХ до (а) и после (б) УКМ.

Проведенные в аналогичных условиях опыты показали, что до температуры 960°C в реакторе, заполненном только насадкой из кварцевого стекла, углекислотная конверсия метана не протекает. При использовании в качестве катализатора карбида вольфрама, произведенного фирмой Alldyne Powder Technologies, превращение СН4 начиналось при 530°C, а при температуре 780°C его конверсия достигала 11.9%. При дальнейшем повышении температуры баланс по углероду (количество образующегося СО при определенной конверсии метана и СО2) нарушался из-за образования на поверхности карбида вольфрама, произведенного фирмой Alldyne Powder Technologies, продуктов углеродного уплотнения (кокса). Действительно, как следует из литературных данных [3, 23, 24], при высоких температурах, в ходе УКМ может происходить образование продуктов уплотнения (кокса).
Следует отметить, что на образцах, полученных методами МХ и ПМХ, дезактивации не наблюдалось.
С целью выяснения влияния на процесс метода приготовления нанопорошка WC при одинаковых условиях были проведены эксперименты по углекислотной конверсии метана с использованием нанокристаллитов WC (40 нм), полученных механохимическим и плазмо-механохимическим методами. Эксперименты показали, что в присутствии обоих катализаторов конверсия метана наблюдается, начиная с 530°C. При повышении температуры до 950°C конверсия метана на катализаторе с WC, полученном методом МХ, составляет 18.9%, а на катализаторе с WC, полученном методом ПМХ, достигает 26%. Во всех случаях основным продуктом реакции являются CO и H2 – компоненты синтез-газа. В обоих случаях в процессе углекислотной конверсии метана селективность образования CO близка к 100%, т.е. расходуемые в процессе метан и диоксид углерода полностью превращаются в монооксид углерода и водород. Анализ экспериментальных данных приводит к выводу, что метод ПМХ позволяет получать более активный катализатор, чем метод МХ.
С целью выяснения влияния размеров наночастиц на процесс УКМ, плазмо-механохимическим методом был изготовлен также порошок WC со средним размером частиц 18 нм. Эксперименты показали, что в этом случае процесс начинается при 500°C и при повышении температуры до 950°C, достигает 55%. На катализаторе, изготовленном с использованием порошка WC со средним размером частиц 35.7 нм, конверсия метана при 950°C достигает 35%. Таким образом, полученные результаты показывают, что уменьшение размера частиц катализатора приводит к увеличению конверсии метана.
Как можно видеть из рис. 2, на дифрактограмме образца WC (МХ) (кривая 2) после реакции УКМ появляются фазы W2С и WO3 (кривая 3). В случае WC (ПМХ) на дифрактограмме образца (рис. 2, кривая 4) после реакции УКМ также появляются фазы W2С и WO3 (кривая 5). Очевидно, что следовало выяснить роль этих соединений в изучаемом процессе.
С целью выяснения влияния роли W2C, был приготовлен катализатор с использованием смеси нанопорошков двух карбидов вольфрама – WC(40%) + W2C(60%), изготовленных методом ПМХ с размером частиц 40 нм. Конверсия метана на этом катализаторе при 650°C составила 6.9%, а при повышении температуры до 780°C достигла 8.1%, что в 1.7 раза меньше, чем конверсия метана на чистом карбиде вольфрама. Исходя из экспериментальных результатов можно заключить, что в процессе УКМ активна только фаза WС, а на W2C реакция практически не протекает.
Как показали эксперименты, при тех же условиях, на катализаторах, изготовленных на основе порошка WO3, конверсия метана, в исследованном диапазоне температур, не наблюдается.
Поскольку соотношение H2/CO в синтез-газе, при его практическом использовании в качестве сырья для производства промышленно-важных продуктов, имеет большое значение, было изучено влияние характеристик катализатора на этот параметр. Результаты исследования приведены в табл. 2.
Таблица 2.
Зависимость соотношения H2/CO от температуры для изученных катализаторов
Т, °С | Отношение H2/CO в продуктах | |||||
---|---|---|---|---|---|---|
Катализаторы | ||||||
1 | 2 | 3 | 4 | 5 | 6 | |
658 | – | – | 1.8 | – | 1.25 | – |
668 | 0.6 | – | – | – | – | – |
705 | 0.45 | 1.5 | 1.9 | 1.7 | 1.2 | 2.1 |
738 | – | – | – | – | 1.19 | – |
746 | – | 1.75 | 2.1 | – | – | – |
780 | 0.5 | – | 2.1 | 1.85 | – | 2.2 |
791 | 0.5 | – | – | – | 1.2 | – |
810 | – | – | 2.2 | 1.9 | – | 2.3 |
820 | – | 1.75 | – | – | – | – |
843 | – | 1.75 | – | – | 1.22 | 2.3 |
871 | – | 1.76 | 1.8 | 1.71 | – | – |
887 | – | – | 1.9 | 1.7 | 1.3 | – |
924 | – | 1.79 | 1.95 | 1.8 | 1.46 | – |
944 | – | – | 1.87 | 1.74 | – | – |
948 | – | – | 1.91 | 1.74 | 1.48 | – |
950 | – | 1.75 | 1.9 | 1.74 | 1.48 | – |
Сравнение результатов показывает, что наилучшими являются катализаторы, изготовленные на основе карбида вольфрама, полученного методом ПМХ с размером частиц 18 нм. Как известно, при стехиометрическом протекании реакции УКМ, соотношение H2/CO должно равняться единице. В то же время, из табл. 2 видно, что это соотношение для образцов, приготовленных методами МХ и ПМХ, меняется в интервале 1.25–1.95. Согласно термодинамическим расчетам, выполненным программой ИСМАН-ТЕРМО, это соотношение, в исследованном интервале температур, в условиях равновесия, может колебаться в пределах 1.00–1.43.
По данным табл. 3 можно определить максимально достижимую конверсию метана. Результаты расчета показывают, что после достижения равновесия, конверсия метана теоретически может составить от 91.2 до 98.7% в указанном диапазоне температур.
Таблица 3.
Равновесное содержание исходных реагентов и продуктов реакции при углекислотной конверсии метана, полученные с применением программы ИСМАН-ТЕРМО. Исходные количества реагентов: MCH4 = MCO2 = 1 моль, P = 650 торр
Соединение | Температура, °С | ||
---|---|---|---|
705 | 820 | 950 | |
CH4 | 0.0882 | 0.0350 | 0.0132 |
CO2 | 0.3188 | 0.0815 | 0.0135 |
CO | 1.0733 | 1.7519 | 1.9533 |
H2 | 1.5343 | 1.8449 | 1.9539 |
H2О | 0.2892 | 0.0851 | 0.0197 |
C | 0.5197 | 0.1316 | 0.0200 |
В работе [18] было показано, что в зависимости от условий проведения процесса, соотношение H2/CO может колебаться от 0.4 до 2.1.
Возможными причинами наблюдаемого в эксперименте результата является многообразие реакций, протекающих в реальном процессе. В частности, к увеличению соотношения H2/CO могут приводить рассмотренные в статье О.В. Крылова [3] реакции (1), (3), (5)–(7):
(5)
${\text{C}} + {\text{2}}{{{\text{H}}}_{{\text{2}}}} = {\text{C}}{{{\text{H}}}_{{\text{4}}}}\,\,\,\,{\Delta }{{H}^{{\text{0}}}} = {\text{ + 74 кДж/моль,}}$(6)
${\text{C}} + {\text{C}}{{{\text{O}}}_{{\text{2}}}} \leftrightarrow {\text{2CO}}\,\,\,\,\Delta {{Н}^{{\text{0}}}} = \,\,{\text{--}}{\text{172}}{\text{.5 кДж/моль,}}$(7)
${\text{С + }}{{{\text{Н}}}_{{\text{2}}}}{\text{О}} \to {\text{СО}} + {{{\text{Н}}}_{{\text{2}}}}\,\,\,\Delta {{H}^{{\text{0}}}} = {\text{ + 74}}{\text{.8 кДж/моль}}{\text{.}}$Действительно, из табл. 3 видно, что при УКМ образуется вода, взаимодействие которой с метаном, монооксидом углерода и углеродом приводит к образованию дополнительных количеств водорода.
Одним из показателей эффективности процесса является конверсия исходных реагентов. В связи с этим, для всех катализаторов была изучена зависимость конверсии метана от температуры. Экспериментальные данные представлены на рис. 5.
Рис. 5.
Зависимость конверсии метана от температуры для изученных катализаторов: 1 – WС(ПМХ 18 нм), 2 – WС(ПМХ 35.7 нм), 3 – WС(ПМХ 40 нм), 4 – WС(МХ 40 нм), ⚫ – WС + W2С, ◻ – WC (Alldyne Powder Technologies).

Как видно из данных рис. 5, конверсия метана для всех изученных катализаторов растет с повышением температуры. При этом, более эффективными оказываются катализаторы, изготовленные методом ПМХ. Кроме того, уменьшение размера частиц приводит к заметному повышению конверсии метана. В частности, при 950°C конверсия метана на катализаторе, изготовленном методом ПМХ из порошка WC с размером частиц 18 нм, в 2.1 раза выше, чем с размером 40 нм, и примерно в три раза выше, чем на WC с размером частиц 40 нм, изготовленном методом МХ.
ВЫВОДЫ
Таким образом, сравнение результатов, полученных в процессе углекислотной конверсии метана на катализаторах, изготовленных из наноразмерных порошков карбида вольфрама, полученных методами механохимии (МХ) и плазмо-механохимии (ПМХ), показывает, что нанопорошок WC, изготовленный методом ПМХ, обладает более высокой каталитической активностью и стабильностью. Установлено, что материалы, имеющие одинаковую дисперсность, но синтезированные разными методами, могут иметь разные физико-химические и, соответственно, каталитические свойства. Более высокая активность катализаторов, изготовленных методом ПМХ, вероятно обусловлена ростом избытка поверхностной энергии, запасенной в дефектах структуры, создаваемых электрическим разрядом и влияющих на каталитические свойства карбида вольфрама.
Список литературы
Sheldon R.A. Chemicals from Synthesis Gas. D. Reidel Publ. Co. Holland. 1983. 202 p.
Van Beurden P. ECN-I-04-003. 2004.
Крылов О.В. // Рос. хим. журн. 2000. Т. 46. № 1. С. 19.
Shang R., Guo X., Mu Sh., Wang YI., Jin G., Kosslick H., Schulz A., Guo X.Y. // Int. J. Hydrogen Energy. 2011. V. 36. № 8. P. 4900.
Fan M.S., Abdullah A.Z., Bhatia S. // Int. J. Hydrogen Energy. 2011. V. 36. № 8. P. 4875.
Григорян Р.Р., Вартикян Л.А., Мнацаканян Р.А., Зурначян А.Р. // Хим. журн. Армении. 2010. Т. 63. № 4. С. 535.
Claridge J.B., York A.P.E., Brungs A.J., Marquez-Alvarez C., Sloan J., Tsang S.C., Green M.L.H. // J. of Catalysis. 1998. V. 180. № 1. P. 85.
Yao Z., Jiang J., Zhao Y., Luan F., Hu J., Shi Y., Gao H., Wang H. // RSC Adv. 2016. V. 6. № 24. P. 19944.
Aldashukurova G., Mironenko A.V., Mansurov Z.A., Rudina N.A., Itshenko A.V., Ushakov V.A., Ismagilov Z.R. // Eurasian Chem.Tech. J. 2010. V. 12. № 2. P. 97.
Osazuwa O.U., Cheng C.K. // J. of Cleaner Production. 2017. V. 148. P. 202.
Bawadi A., Nur Azeanni Abd Ghani, Dai-Viet N.Vo. // J. of Cleaner Production. 2017. V. 162. P. 170.
Aramouni N.A.K., Touma J.G.,Tarboush B.A., Zeaiter J., Ahmad M.N. // Renewable and Sustainable Energy Reviews. 2018. V. 82. № 3. P. 2570.
Leimert J.M., Karl J., Dillig M. // Processes. 2017. V. 5. № 4. P. 82.
Mondal K., Sasmal S., Badgandi S., Chowdhury D.R., Nair V. // Environmental Science and Pollution Research. 2016. V. 23. № 22. P. 22267.
Debek R., Motak M., Grzybek T., Galvez M., Da Costa P. // Catalysts. 2017. V. 7. № 1. P. 32.
Penner S. // Catalysts. 2017. V. 7. № 11. P. 334.
Дедов А.Г., Локтев А.С., Моисеев И.И., Баранчиков А.Е., Иванов В.К., Краснобаева О.Н., Носова Т.А., Данилов В.П., Тюменова С.И., Быков М.А., Мухин И.Е. // Нефтехимия. 2018. Т. 58. № 3. С. 314 [Petrol. Chemistry. 2018. V. 58. № 3. P. 203].
Qiangu Yan, Yongwu Lu, Filip To, Yebo Li, Fei Yu // Catalysis Science and Technology. 2015. V. 5(6). P. 3270.
Yuchen Gao, Jianguo Jiang, Yuan Meng, Feng Yan, Aikelaimu Aihemaiti // Energy Conversion and Management. 2018. V. 171 P. 133.
Нанотехнологии. Под ред. Третьякова Ю.А. М.: Физматлит, 2008. 368 с.
Гусев А.И. Наноматериалы, наноструктуры, нанотехнологии. М.: Физматлит, 2009. 416 с.
Алоян С.Г., Арутюнян В.Р., Вартикян Л.А., Григорян Р.Р., Тавадян Л.А. // Кинетика и катализ. 2014. Т. 55. № 2. С. 234.
Ma J., Sun N., Zhang X., Zhao N., Xiao F., Wei W., Sun Y. // Catal. Today. 2009. V. 148. № 3–4. P. 221.
Guo J., Lou H., Zhao H., Chai D., Zheng X. // Appl. Catal. A. General. 2004. V. 273. № 1–2. P. 75.
Liu D., Cheo W., Wen Y., Lim Y., Borgna A., Lau R., Yang Y. // Catal. Today. 2010. V. 154. № 3–4. P. 229.
Sehested J., Jacobsen C.J.H., Rokni S., Rostrup-Nielsen J.R. // J. of Catalysis. 2001. V. 201. № 2. P. 206.
Hou Z., Chen P., Fang H., Zheng X., Yashima T. // Int. J. Hydrogen Energy. 2006. V. 31. № 5. P. 555.
Wang C., Zhang Y., Wang Y., Zhao Y. // Chin. J. Chem. 2017. V. 35. № 1. P. 113.
Bian Z., Kawi S. // J. of CO2 Utilization. 2017. V. 18. P. 345.
Aider N., Touahra F., Bali F., Djebarri B., Lerari D., Bachari K., Halliche D. // Int. J. of Hydrogen Energy. 2018.V. 43. № 17.P. 8256.
Guojie Zhang, Jiwei Liu, Ying Xu, Yinghui Sun // Int. J. of Hydrogen Energy. 2018.V. 43. № 32. P. 15030.
Abdulrasheed A., Jalil A.A., Gambo Y., Ibrahim M., Hambali H.U., Hamid M.Y.S. // Renewable and Sustainable Energy Reviews. 2019. V. 108. P. 175.
Qiangu Yan, Yongwu Lu, Filip To, Yebo Li, Fei Yu // Catalysis Science and Technology. 2015. V. 5. P. 3270.
Арутюнов В.С. // Российский хим. журн. 2001. Т. 45. № 1. С. 55.
Calka A., Wexler D. // J. of Metastable and Nanocrystalline Materials. 2004. V. 20–21. P. 111.
Wexler D., Calka A., Dunne D. // J. of Metastable and Nanocrystalline Materials. 2005. V. 26. P. 16.
Calka A., Wexler D., Mosbah A.Y. // J. of Alloys and Compounds. 2006. V. 434–435. P. 463.
Молчанов В.В., Буянов Р.А. // Успехи химии. 2000. Т. 69. № 5. С. 476.
Лиопо В.А., Война В.В. Рентгеновская дифрактометрия. Гродно: ГрГУ, 2003. 171 с.
Дополнительные материалы отсутствуют.