Нефтехимия, 2019, T. 59, № 6-2, стр. 781-787
Обессеривание светлых дистиллятов путем окисления и ректификации газового конденсата
А. В. Акопян 1, *, П. Д. Поликарпова 1, Д. А. Плотников 1, Е. А. Есева 1, А. В. Тараканова 1, А. В. Анисимов 1, Э. А. Караханов 1
1 Московский государственный университет им. М.В. Ломоносова, Химический факультет
119991 Москва, Россия
* E-mail: arvchem@yandex.ru
Поступила в редакцию 11.11.2018
После доработки 10.02.2019
Принята к публикации 12.02.2019
Аннотация
Исследована возможность использования метода, сочетающего в себе окисление сернистых соединений, присутствующих в газовом конденсате, с последующей его ректификацией, для обессеривания светлых нефтяных фракций. Окисление газового конденсата пероксидом водорода в присутствии солей переходных металлов с последующей его ректификацией позволяет снизить содержание сернистых соединений в бензиновой фракции на 95% и на 75% в дизельной, при этом содержание сернистых соединений в остаточной фракции (350°С – КК) остается практически неизменным.
В настоящее время нефтеперерабатывающая промышленность перешла к производству топлив, соответствующих требованиям стандарта качества Евро-5, в соответствии с которым содержание серы в бензиновой и дизельной фракциях не должно превышать 10 ppm [1]. Необходимость снижения содержания общей серы в продуктах нефтеперерабатывающей промышленности связана с тем, что широкое применение различных видов углеводородного топлива в транспорте и на энергетических объектах приводит к загрязнению атмосферы продуктами горения сернистых соединений. Также сера, присутствующая в топливах в виде различных серосодержащих соединений, является нежелательным компонентом, вызывающим коррозию аппаратуры и отравляющим катализаторы в процессах вторичной переработки нефти [2–4].
В связи с тем, что наиболее распространенный в мире способ очистки топлив от серы – гидроочистка требует существенных энерго- и капиталовложений [5–7], которые являются недоступными для небольших нефтеперерабатывающих заводов (НПЗ), большое развитие получают альтернативные безводородные способы сероочистки: окислительное обессеривание, адсорбция, экстракция и биодесульфуризация [8–14].
Преимущества окислительного обессеривания перед гидроочисткой – отсутствие необходимости использования водорода, а также небольшие капитало- и энергозатраты, т.к. метод не требует высоких температур и давлений [15]. В качестве окислителей могут быть использованы различные реагенты, такие как пероксид водорода, органические алкилгидропероксиды, неорганические окислители, кислород и озон [16, 17].
Традиционно процесс окислительного обессеривания проводят, окисляя сернистые соединения углеводородных фракций, с последующей экстракцией или адсорбцией продуктов окисления [18, 19]. Однако при обессеривании сырой нефти и газового конденсата использование адсорбции нецелесообразно из-за большого количества асфальтенов и смол, присутствующих в данном сырье и затрудняющих адсорбционное удаление сульфоксидов и сульфонов [8]. Использование метода экстракции сопряжено с большими потерями экстрагента и самого сырья [20].
В предлагаемой работе для извлечения серосодержащих соединений применена двухступенчатая схема обессеривания, первой стадией которой является окисление газового конденсата, а второй его последующая разгонка. Метод основан на том, что температуры кипения окисленных серосодержащих соединений – сульфоксидов и сульфонов, существенно выше неокисленных сернистых соединений, следовательно, продукты окисления после ректификации будут концентрироваться в остаточных фракциях (мазуте, гудроне и т.д.), в которых существенно менее строгие требования по содержанию общей серы; при этом часть продуктов окисления (преимущественно сульфоны и сульфоксиды, образовавшиеся при окислении сернистых соединений легких фракций) будет удаляться после водной промывки газового конденсата.
Основное преимущество выбранного подхода – возможность упрощения способа окислительного обессеривания за счет отсутствия стадии извлечения сернистых соединений, а также отсутствия потерь экстрагента/адсорбента при экстракционной/адсорбционной очистке.
ЭКСПЕРИМЕНТАЛЬНАЯ ЧАСТЬ
Реактивы и оборудование. В качестве сырья был использован конденсат газовый стабильный У-930 Карачаганакского газоконденсатного месторождения с содержанием общей серы 5700 ppm.
В работе были использованы следующие реактивы: молибдат натрия (Na2MoO4 ⋅ H2O, ч. д. а., “Sigma Aldrich”), пероксид водорода (Н2О2, 50%-ный, “ПраймКемикалсГрупп”), метилфенилсульфид (МФС, 97%, “Sigma Aldrich”), бензотиофен (БТ, 98%, “Sigma Aldrich”), дибензотиофен (ДБТ, 98%, “Sigma Aldrich”), серная кислота (H2SO4, 95.6%, “Сигма Тек”); фосфорная кислота (H3PO4, 85%, “РусХим”), бензол (ч. д. а., “Экос-1”), муравьиная кислота (НСООН, 90%, “Компонент-реактив”), уксусная кислота (СН3СООН, 99.8%, “Компонент-реактив”), н-гептан (98%, “Компонент-реактив”), ацетон (99.5% “Компонент-Реактив”), серебро азотнокислое (AgNO3, ХЧ, “Реахим” по ГОСТ 1277), вода дистиллированная по ГОСТ 6709.
Состав продуктов реакции и контроль чистоты исходных веществ осуществляли методом газовой хроматографии на хроматографе “Кристалл-2000М” с пламенно-ионизационным детектором, колонка Zebron L = 30 м, d = 0.32 мм, жидкая фаза ZB-1, при программировании температуры от 100 до 250°С. Хроматограммы анализировали с использованием программы Хроматэк Аналитик 1.5.
Условия проведения анализа реакционной смеси до и после окисления:
–газ-носитель: азот (p = 200 кПа), объемная скорость потока 30 мл/мин;
− начальная температура колонки 100°С;
− температура инжектора 150°С;
− температура детектора 250°С;
− скорость нагрева колонки 20°С/мин.
Определение содержания общей серы в углеводородных фракциях осуществляли с помощью анализатора серы в нефтепродуктах СПЕКТРОСКАН SL по ASTM D 4294-10 [21]. Принцип действия прибора основан на методе рентгенофлуоресцентной энергодисперсионной спектрометрии, являющимся арбитражным методом определения массовой доли серы в дизельном топливе и допустимым методом определения массовой доли серы в неэтилированном бензине. Прибор позволяет определять содержание серы в диапазоне от 7 до 50 000 ppm с относительной погрешностью 3%.
Приготовление каталитической окислительной смеси. К 0.75–2.3 мл 50%-ного раствора пероксида водорода добавляли при постоянном перемешивании 0.0045–0.0180 г Na2MoO4 ⋅ H2O. Перемешивание продолжали в течение 5 мин, далее добавляли 0.2–0.6 мл кислоты (серной, ортофосфорной, муравьиной или уксусной в зависимости от условий опыта) и перемешивали еще 3 мин.
Окисление модельных смесей сероорганических соединений. Модельные смеси готовили, растворяя метилфенилсульфид, бензотиофен и дибензотиофен, являющиеся компонентами бензиновой, дизельной и тяжелой фракций, в смеси растворителей бензол–н-гептан (20 : 80 по объему).
Реакции окисления модельных смесей проводили по следующей методике: к 5 мл раствора сульфидов (содержание метилфенилсульфида 500 ppm, бензотиофена 500 ppm и дибензотиофена 500 ppm) добавляли 0.05–0.1 мл каталитической окислительной смеси, состоящей из пероксида водорода, кислоты и молибдата натрия. Реакцию проводили при постоянном перемешивании на магнитной мешалке при температуре 20–80°С в течение 0.5–6 ч.
После проведения окисления реакционную смесь анализировали методом газовой хроматографии.
Обессеривание светлых фракций. В реактор, снабженный магнитной мешалкой, добавляли 50 мл газового конденсата и 0.95–2.9 мл каталитической окислительной смеси, состоящей из пероксида водорода, кислоты и молибдата натрия. Смесь перемешивали в течение 2–6 ч. После окончания реакции к реакционной смеси добавляли 5 мл воды для удаления остатков каталитической окислительной системы, водную фазу отделяли от углеводородной фракции, которую далее подвергали ректификации. Выделяли бензиновую фракцию с температурой конца кипения (КК) равной 165°С и керосино-газойлевую фракцию в температурном интервале 165–310°С. Полученные фракции анализировали на содержание общей серы с помощью анализатора серы в нефтепродуктах СПЕКТРОСКАН SL.
РЕЗУЛЬТАТЫ И ИХ ОБСУЖДЕНИЕ
Окисление модельной смеси серосодержащих соединений. Окисление модельной смеси проводили действием окислительной системы, содержащей пероксид водорода, с использованием в качестве катализатора молибдата натрия, обладающего способностью образовывать пероксокомплексы в присутствии пероксида водорода [22–24]. Для повышения конверсии в окислительную систему вводили дополнительно органические и минеральные кислоты, поскольку их присутствие существенно повышает окислительную активность пероксида водорода [25].
Продуктами окисления в условиях окислительного обессеривания используемой модельной смеси являются соответствующие сульфоны, что подтверждено методом газовой хроматографии. Реакции окисления модельных сульфидов приведены ниже:
В результате проведенных опытов (табл. 1) были подобраны оптимальные условия для селективного окисления различных сульфидов в бензиновой фракции: время реакции – 2 ч, температура реакции – 80°С, мольное соотношение компонентов окислительной смеси: Na2MoO4 : S : H3PO4 : H2O2 = 1 : 200 : 200 : 800.
Таблица 1.
Результаты опытов по окислению модельных сульфидов в различных условиях
Варьируемый параметр | Конверсия, % | Условия окисления | |||
---|---|---|---|---|---|
МФС | БТ | ДБТ | |||
Н3РО4 | 22 | 0 | 0 | H2O2 : S : кисл : Mo = 800 : 200 : 200 : 1 (мольн.), 2 ч, комнатная температура | |
Н2SО4 | 100 | 2 | 12 | ||
CH3COOH | 24 | 0 | 0 | ||
HCOOH | 100 | 3 | 41 | ||
Без кислоты | 10 | 0 | 0 | ||
Время окисления, ч | 0.5 | 2 | 0 | 0 | H2O2 : S : H3PO4 : Mo = 800 : 200 : 200 : 1 (мольн.), комнатная температура |
1 | 4 | 0 | 0 | ||
2 | 22 | 0 | 0 | ||
4 | 26 | 2 | 0 | ||
6 | 28 | 4 | 6 | ||
Количество пероксида водорода, H2O2 : S, мольн. | 1 : 4 | 18 | 0 | 0 | S : H3PO4 : Mo = 200 : 200 : 1 (мольн.), 2 ч, температура окисления = 40°С |
1 : 2 | 19 | 0 | 0 | ||
2 : 1 | 28 | 1 | 0 | ||
4 : 1 | 38 | 1 | 3 | ||
6 : 1 | 42 | 1 | 9 | ||
Количество молибдата натрия, Mo : S, мольн. | 1 : 500 | 8 | 0 | 0 | H2O2 : S : H3PO4 = 4 : 1 : 1 (мольн.), 2 ч, комнатная температура |
1 : 200 | 22 | 0 | 0 | ||
1 : 100 | 26 | 0 | 4 | ||
Температура, °С | 20 | 22 | 0 | 0 | H2O2 : S : H3PO4 : Mo = 800 : 200 : 200 : 1 (мольн.), 2 ч |
40 | 33 | 0 | 3 | ||
60 | 52 | 1 | 4 | ||
80 | 98 | 7 | 8 | ||
Количество H3PO4, H3PO4 : S, мольн. | 1 : 2 | 78 | 0 | 0 | H2O2 : S : Mo = 800 : 200 : 1 (мольн.), 2 ч, температура окисления = 40°С |
1 : 1 | 98 | 7 | 8 | ||
2 : 1 | 100 | 0 | 31 |
Для подбора условий окисления сернистых соединений в светлых нефтяных фракциях (бензиновой и дизельной) были проведены опыты с той же модельной смесью, целью которых было достижение максимального окисления сернистых компонентов светлых нефтяных фракций –МФС и БТФ (рис. 1). В качестве кислотной добавки использовали муравьиную кислоту, зарекомендовавшую себя в качестве наиболее эффективной добавки для полного окисления модельных смесей сероорганических соединений (табл. 1).
Рис. 1.
Зависимость остаточного содержания сульфидов в модельной смеси от температуры реакции (Na2MoO4 : S : НСООН : H2O2 = 1 : 200 : 200 : 800 (мольн.), 2 ч).
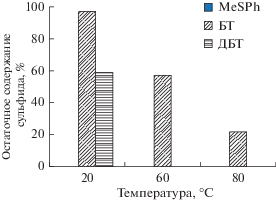
Как видно из рис. 1, при 60°C МФС и ДБТ окисляются полностью. Дальнейшее увеличение температуры реакции до 80°С позволяет снизить остаточное содержание серы; однако это сопряжено с увеличением скорости разложения пероксида водорода и повышением его расхода, поэтому в дальнейших экспериментах использовали температуру 60°С.
Окислительное обессеривание светлых нефтяных фракций газового конденсата. Данные, полученные при проведении опытов на модельных смесях, были проверены на реальном углеводородном сырье. В качестве объекта исследования использовали газовый конденсат с исходным содержанием серы 5700 ppm (3220 ppm в бензиновой фракции, 4130 ppm в дизельной фракции и 12980 ppm в остаточной фракции).
К исходному сырью добавляли рассчитанное количество окислительной смеси, содержащей пероксид водорода, молибдат натрия и кислоту. После окончания реакции окисления сырье отделяли от катализатора, промывали водой и подвергали ректификации. Полученные фракции анализировали на остаточное содержание серы. Результаты опытов степени обессеривания в зависимости от времени окисления приведены на рис. 2.
Рис. 2.
Результаты опытов степени обессеривания газового конденсата от времени окисления (Na2MoO4 : : S : Н3РО4 : H2O2 = 1 : 200 : 200 : 800 (мольн.), 20°С).
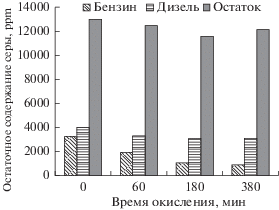
Как уже было показано для модельных смесей (табл. 1), основное снижение содержания серы происходит за два часа, однако для достижения более высокой степени обессеривания исследование реальных углеводородных фракций проводили при шестичасовом окислении. Количество пероксида водорода варьировали в интервале соотношений H2O2 : S от 2 : 1 до 6 : 1. Избыток добавляемого окислителя необходим в связи с тем, что возможно частичное разложение пероксида водорода в ходе реакции. Полученные результаты приведены на табл. 2.
Таблица 2.
Результаты опытов по обессериванию газового конденсата в зависимости от количества пероксида водорода (Na2MoO4 : S : Н3РО4 = 1 : 200 : 200 (мольн.), 6 ч, 20°С)
Н2О2 : S (мольн.) | Остаточное содержание серы, ppm | ||
---|---|---|---|
в бензиновой фракции | в дизельной фракции | в остаточной фракции | |
Исходное топливо | 3220 | 4130 | 12 980 |
2 : 1 | 2010 | 3220 | 11 720 |
4 : 1 | 840 | 2970 | 12 100 |
6 : 1 | 155 | 3000 | 12 010 |
Как видно из табл. 2 наилучшие результаты показывает шестикратный избыток пероксида водорода. При этом с целью минимизации расхода окислителя в дальнейших опытах использовали четырехкратный избыток.
На рис. 3 представлено исследование влияния природы кислотной добавки на степень удаления сернистых соединений из прямогонной бензиновой фракции. В качестве кислот были выбраны те же кислоты, что и в опытах с модельными смесями. Результаты, полученные при обессеривании светлых фракций, коррелируют с результатами окисления модельных смесей – наилучшие результаты достигаются в присутствии серной и муравьиной кислот (табл. 1, рис. 3). Для повышения селективности процесса и окисления преимущественно сульфидов и меркаптанов, содержащихся в бензиновой фракции, не затрагивая более тяжелые фракции, в дальнейших экспериментах использовали фосфорную кислоту.
Рис. 3.
Зависимость остаточного содержания сернистых соединений в различных фракциях от природы кислотной добавки (Na2MoO4 : S : кислота : H2O2 = = 1 : 200 : 200 : 800 (мольн.), 6 ч, 20°С).
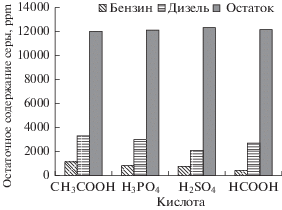
Как видно из приведенных данных (табл. 3) при добавлении в окислительную систему кислоты существенно увеличивается степень окисления сероорганических соединений из бензиновой фракции; при этом увеличение концентрации кислоты в два раза практически не сказывается на остаточном содержании серы в бензиновой фракции. На модельной смеси ранее было показано, что уменьшение концентрации кислоты негативно сказывается на степени окисления сернистых соединений. Исходя из полученных данных, оптимальным соотношением общей серы к кислоте является соотношение 1 : 1.
Таблица 3.
Зависимость остаточного содержания общей серы от количества ортофосфорной кислоты (Na2MoO4 : S : H2O2 = 1 : 200 : 800 (мольн.), 2 ч, 20°С)
Н3РО4 : S (мольн.) | Остаточное содержание серы, ppm | ||
---|---|---|---|
в бензиновой фракции | в дизельной фракции | в остаточной фракции | |
Исходное топливо | 3220 | 4130 | 12980 |
– | 2000 | 3400 | 11780 |
1 : 1 | 840 | 2970 | 12100 |
2 : 1 | 514 | 2620 | 11530 |
Для изучения влияния концентрации металла на остаточное содержание серы были проведены опыты с газовым конденсатом при разных дозировках молибдата натрия. Полученные результаты приведены в рис. 4.
Рис. 4.
Зависимость остаточного содержания сернистых соединений в различных фракциях от количества молибдата натрия (S : Н3РО4 : H2O2 = 1 : 1 : 4 (мольн.), 6 ч, 20°С).
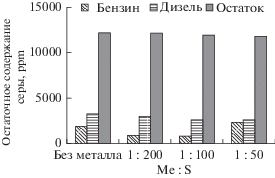
Увеличение концентрации металла в окислительной системе в два раза не влияет на эффективность обессеривания (рис. 4). При этом значительное увеличение концентрации металла от 1 : 100 до 1 : 50 (мольн. по отношению к общей сере) ведет к интенсификации разложения пероксида водорода и уменьшению степени обессеривания бензиновой фракции. Уменьшение концентрации молибдата натрия ведет к уменьшению степени обессеривания, что было показано на модельных смесях. Важно отметить, что использование комбинированной каталитической системы, содержащей как соль металла, так и кислоту, позволяет достигать лучших результатов по сравнению с использованием только металла или только кислоты в качестве катализаторов окисления.
В результате проделанной работы были подобраны оптимальные условия селективного окисления сероорганических соединений, присутствующих в бензиновой фракции – Na2MoO4 : S : Н3РО4 : H2O2 = 1 : 200 : 200 : 1200 (мольн.), температура реакции – 20°С, время реакции – 6 ч, и оптимальные условия окисления сернистых соединений в светлых нефтяных фракциях (бензиновой и дизельной): Na2MoO4 : S : НСООН : : H2O2 = 1 : 200 : 200 : 1200 (мольн.), температура реакции − 40°С. Полученные результаты приведены на рис. 5.
Для сравнения эффективности метода окислительного обессеривания с последующей ректификацией с традиционным методом окислительного обессеривания с извлечением продуктов окисления методом экстракции были проведены опыты по окислению бензиновой, дизельной и остаточной фракциях в условиях селективного окисления бензиновой фракции с последующей экстракцией продуктов окисления ДМФА. Полученные данные приведены в табл. 4.
Таблица 4.
Сравнение методов окислительного обессеривание с последующей ректификацией и экстракцией
Остаточное содержание серы, ppm | ||
---|---|---|
Фракция | окисление газового конденсата с последующей его ректификацией | окисление нефтяных фракций с последующей экстракцией ДМФА |
Бензиновая | 840 | 812 |
Дизельная | 2970 | 1156 |
Остаточная | 12 100 | 3120 |
Из данных табл. 4 можно сделать вывод, что использование предложенного метода обессеривания позволяет снижать содержание общей серы в бензиновой фракции также, как и методом окислительного обессеривание с последующей экстракцией, при этом сокращается количество стадий и количество необходимых реактивов, что существенно удешевляет процесс обессеривания. Большее количество серосодержащих веществ в дизельной и остаточной фракции объясняется тем, что в процессе ректификации окисленные серосодержащие соединения, ранее присутствующие в бензиновой фракции, переходят в более тяжелые фракции.
Для оценки влияния процесса окислительного обессеривания на качество получаемого газового конденсата было проведено сравнение фракционного состава до и после его окисления с помощью метода имитированной дистилляции. Результаты приведены в табл. 5.
ВЫВОДЫ
В результате работы были подобраны оптимальные условия для селективного окисления соединений серы, присутствующих в бензиновой фракции и легких сульфидных соединениях. Показано, что эти выбранные условия практически не влияют на физические свойства газового конденсата, а также его фракционный состав. Содержание общей серы в бензиновой и дизельной фракциях было снижено на 95 и 75% соответственно.
ФИНАНСИРОВАНИЕ РАБОТЫ
Работа выполнена при финансовой поддержке Министерства образования и науки РФ в рамках ФЦП “Исследования и разработки по приоритетным направлениям развития научно-технологического комплекса России на 2014–2020 гг.” мероприятие 1.3, Соглашение о предоставлении субсидии № 14.607.21.0173 от 26.09.2017. Уникальный идентификатор прикладных научных исследований RFMEFI60717X0173.
КОНФЛИКТ ИНТЕРЕСОВ
Авторы заявляют об отсутствии конфликта интересов, требующего раскрытия в данной статье.ИНФОРМАЦИЯ ОБ АВТОРАХ
Акопян Аргам Виликович, к.х.н., с.н.с. ORCID: https://orcid.org/0000-0001-6386-0006Поликарпова Полина Димитровна, инженер, ORCID: https://orcid.org/0000-0002-0456-8248Плотников Дмитрий Андреевич, ORCID: https://orcid.org/0000-0001-5064-8989Есева Екатерина Андреевна, инженер, ORCID: https://orcid.org/0000-0001-7538-9012Тараканова Алла Васильевна, к.х.н., в.н.с., ORCID: https://orcid.org/0000-0002-5589-0253Анисимов Александр Владимирович, д.х.н., профессор, ORCID: https://orcid.org/0000-0001-9272-2913 Караханов Эдуард Аветисович, д.х.н., профессор, ORCID: https://orcid.org/0000-0003-4727-954X
Список литературы
Технический регламент № 609 “О требованиях к выбросам автомобильной техникой, выпускаемой в обращение на территории Российской Федерации, вредных (загрязняющих) веществ”.
Рудяков Е.В. // Иркутск: Изд-во Иркутского гос. техн. университета, 2013. С. 56.
Chen Y., Xie Ch., Li Y., Song Ch., Bolin T.B. // Phys. Chem. Chem. Phys. 2010. V. 12. P. 5707.
Dunleavy J.K. // Platinum Metals Review. 2006. V. 50. P. 110.
Xiaoliang M., Lu S., Chunshan S. // Catalysis Today. 2002. V. 77. P. 107.
Zhan L., Long X., Li D., Gao X. // Catalysis Communications. 2011. V. 12. № 11. P. 927.
Dai Y., Qi Y., Zhao D., Zhang H. // Fuel Processing Technology. 2008. V. 89. № 10. P. 927.
Babich I.V., Moulijn J.A. // Fuel. 2003. V. 82. P. 607.
Javadli R., de Klerk A. // Appl. Petrochem Res. 2012. № 1. P. 3.
Xueni Sun, Bruce J. Tatarchuk. // Fuel. 2016. V. 183. P. 550.
Wan Mokhtar W., Ali Kader A., Abu Bakar W. // Fuel Process Technology. 2012. V.101. P. 78.
Nie Y., Dong Y. // Fuel. 2013. V. 103. P. 997.
Bhutto A.W., Abro R. // J. of the Taiwan Institute of Chemical Engineers. 2016. V. 62. P. 84.
Campos-Martin J.M., Capel-Sanchez M.C., Perez-Presas P., Fierro J.L.G. // Chemical Technology and Biotechnology. 2010. V. 86. № 7. P. 879.
Mohammed-Dabo I.A., Abubakar A., Ahmed A.S. // Swiss J. of Applied Sciences. 2012. V. 1. № 1. P. 39.
Zeelani G.G., Ashrafi A., Dhakad A., Gupta G., Pal S.L. // Intern. Research J. of Engineering and Technology. 2015. V. 3. № 5. P. 331.
Zhao H., Baker G.A. // Frontiers of Chemical Science and Engineering. 2015. V. 9. № 3. P. 262.
Nie Y., Dong Y. // Fuel. 2013. V. 103. P. 997.
Анисимов А.В., Тараканова А.В. // Рос. хим. журн. (Журн. Рос. хим. об-ва им. Д.И. Менделеева). 2008. Т. LII. № 4. С. 32.
Kumar S., Srivastava V.C., Nanoti Sh.M. // Separation & Purification Reviews. 2017. V. 46. № 4. P. 319.
ASTM D 4294-10. Standard Test Method for Sulfur in Petroleum and Petroleum Products by Energy Dispersive X-ray Fluorescence Spectrometry.
Amini M., Bagherzadeh M., Atabaki B., Derakhshandeh P.G., Ellern A., Woo L.K. // J. of Coordin. Chemistry. 2014. V. 67. № 8. P. 1429.
Yang Ch., Zhao K., Cheng Y., Zeng G., Zhang M., J. Shao, Li Lu. // Separation and Purification Technology. 2016. V. 163. P. 153.
Jin W., Tian Y., Wang G., Zeng D., Xu Q., Cui J. // RSC Advances. 2017. V. 7. P. 48208.
Yazu K., Mitsunori M., Koji K. // Chemistry Letters. 2004. V. 33. P. 1306.
Дополнительные материалы отсутствуют.