Нефтехимия, 2020, T. 60, № 1, стр. 76-82
Влияние цеолита на синтез Фишера–Тропша в присутствии катализатора на основе скелетного кобальта
Е. Ю. Асалиева 1, *, Е. В. Кульчаковская 1, Л. В. Синева 1, 2, В. З. Мордкович 1, 2
1 Технологический институт сверхтвердых и новых углеродных материалов
108840 Троицк –, Москва, Россия
2 ИНФРА Технологии
125009 Москва, Россия
* E-mail: e.asalieva@tisnum.ru
Поступила в редакцию 02.08.2018
После доработки 25.06.2019
Принята к публикации 06.09.2019
Аннотация
В работе исследовано совместное влияние скелетного кобальта и цеолита на основные каталитические показатели композитного гранулированного катализатора. Все содержали 50 мас. % высокодисперсного порошка металлического алюминия. Содержание остальных компонентов составляло: 20–30 мас. % — связующего (бемит), 5–20 мас. % – цеолита Beta в H-форме (SiO2/Al2O3 = 38) и 10–20 мас. % – высокодисперсного скелетного кобальта. Катализатор сравнения не содержал цеолит. Все катализаторы проявили активность в синтезе Фишера–Тропша, а также во вторичных превращениях, интенсивность протекания которых зависела от соотношения цеолит/кобальт. Состав образующихся углеводородов (УВ) изменялся в широком диапазоне, в частности, 39–88% – н-парафинов, 3–38% – олефинов и т.д. Вероятность роста цепи составляла от 0.65 до 0.83 в зависимости от соотношения цеолит/кобальт и условий проведения синтеза. Показано преимущество катализаторов, исследованных в данной работе, по сравнению с другими кобальт-цеолитными катализаторами, а именно высокие конверсия СО, удельная активность, производительность и стабильность.
Синтез Фишера–Тропша (СФТ) является ключевой стадией технологии получения синтетической нефти и компонентов топлив высокого качества из углеродсодержащего сырья. В последние годы технология привлекает все большее внимание как альтернатива использованию истощающихся запасов нефти. Актуальности добавляет решение экологических проблем, например, таких как утилизация попутного газа [1–3].
Перспективными катализаторами СФТ являются кобальтовые катализаторы, в присутствии которых практически не образуются кислородсодержащие и ароматические углеводороды [4–6]. В настоящее время в промышленности и лабораторной практике используют преимущественно нанесенные кобальтовые системы. Однако для СФТ можно использовать катализаторы на основе скелетного кобальта (кобальта Ренея), свойства которых отличаются от нанесенных систем.
Катализаторы на основе кобальта Ренея были исследованы в синтезе УВ из СО и Н2 практически сразу после их открытия на начальном этапе развития СФТ в 1934 г. Было установлено, что такие катализаторы проявляют активность в этом процессе, однако существенно более низкую, чем активность применявшихся в то время в промышленности железных катализаторов [7]. В то же время они характеризовались рядом недостатков: высоким содержанием активного компонента, низкой удельной активностью (рассчитанной на единицу веса металла), высоким удельным весом, низкой производительностью, а также пирофорностью. В связи с этим скелетные катализаторы были надолго забыты.
В конце 60-х гг. русские ученые вернулись к изучению скелетных катализаторов СФТ. Однако по итогам исследований был сделан вывод, что нанесенный катализатор является все же более предпочтительным [8]. Следующая попытка использовать системы на основе скелетного кобальта была сделана в начале 90-х гг., однако эти исследования также не выявили преимуществ таких катализаторов [9].
Скелетный кобальт обладает относительно высокой теплопроводностью, что особенно важно для СФТ ввиду сильной экзотермичности процесса [4, 10] – эффективный теплоотвод критически важен и влияет на такие показатели, как скорость деактивации, селективность образования целевого продукта и производительность. Перегревы нанесенных катализаторов в процессе синтеза могут приводить к укрупнению кристаллитов кобальта и снижению активности и селективности системы.
В наших прошлых работах [11–13] были исследованы гранулированные катализаторы СФТ, отличающиеся высокой теплопроводностью. Было показано, что высокая теплопроводность гранул может быть обеспечена введением порошка металлического алюминия в больших количествах (вплоть до 50 мас. %) и дополнительно увеличена введением скелетного кобальта. Также было установлено, что гранулы с высокой теплопроводностью могут обеспечить более высокую производительность каталитического слоя по сравнению с классическими нанесенными катализаторами. В работе [14] были исследованы композитные катализаторы, содержащие активный кобальт разных типов. Катализаторы характеризовались близкими значениями конверсии и производительности, но при этом фракционный и групповой составы образующихся УВ значительно различались.
Идея совмещения в единой каталитической системе функций металла, активного в СФТ, и кислотных центров, активных в превращениях образующихся УВ, для того, чтобы уйти от широкого распределения продуктов, подчиняющихся модели Шульца–Флори–Андерсона, возникла еще в середине 1970 гг., а в последние 10 лет вызывает большой интерес [15–20]. Такие катализаторы, называемые бифункциональными (или гибридными), способны производить УВ, типичные для бензиновой фракции, из синтез-газа в одну стадию [17–23].
Кислотная функция носителя может оказывать влияние на распределение образующихся УВ и таким образом вызывать отклонения от классического молекулярно-массового распределения. УВ, образующиеся на активных центрах СФТ, могут подвергаться различным превращениям в присутствии твердых кислот, к которым относятся смешанные оксиды, в том числе цеолиты. Кислотные центры цеолита проявляют селективность в образовании более легких и разветвленных УВ благодаря протеканию реакций крекинга, алкилирования и изомеризации. Нанесение на твердую кислоту, например, цеолит солей металлов приводит к формированию катализаторов, в которых совмещены преимущества металлических и кислотных центров [24]. Состав продуктов синтеза при этом будет определяться относительными скоростями реакций на кислотных и металлических центрах. Согласно литературным данным [25–27], наиболее часто в СФТ для повышения селективности катализатора в образовании более легких и разветвленных углеводородов применяют цеолиты H-Y, H-ZSM-5, H-Beta или H-Mordenite. В работе [28] показано, что в отличие от кобальтовых катализаторов на основе цеолитов другого типа, катализаторы на основе цеолита H-Beta были активны в изомеризации углеводородов уже при 220°С.
Для оптимизации расположения активных центров СФТ и превращений УВ можно использовать различные способы: физически смешивать катализаторы СФТ с цеолитами, капсулировать их в цеолитную оболочку или наносить на цеолит активный в СФТ металл. Менее популярным способом получения цеолитсодержащих катализаторов СФТ является формование цеолита и активного металла со связующим в композиты. Однако именно в последнем варианте реализуется такое взаимное расположение металлических и кислотных активных центров, которое обеспечивает образование углеводородов и их участие во вторичных превращениях без снижения интенсивности массообмена, а, следовательно, и теплопередачи.
Целью данной работой явилось изучение влияния соотношения кобальта Ренея и цеолита в составе гранулированного композитного катализатора. Сочетание кобальта Ренея и цеолита в катализаторе открывает широкие возможности для создания высокоэффективного теплопроводного катализатора, который позволит получать УВ заданного состава с высокой производительностью и селективностью.
ЭКСПЕРИМЕНТАЛЬНАЯ ЧАСТЬ
Катализаторы, исследованные в данной работе, были приготовлены согласно методикам, защищенным патентами [29–31]. Содержание сухих компонентов пасты до экструзии и прокаливания составляет (мас. %): порошка металлического алюминия – 50, связуюшего (бемит) – 20–30, цеолита Beta в H-форме (SiO2/Al2O3 = 38) – 5–20 и высокодисперсного скелетного кобальта – 10–20. Один из катализаторов (катализатор сравнения) не содержит цеолит (табл. 1).
Таблица 1.
Состав сухой части пасты до экструзии и прокаливания
Состав пасты, мас. % | Соотношение НВ/Со | |||
---|---|---|---|---|
алюминий | бемит | цеолит НВ | скелетный кобальт | |
50 | 30 | 0 | 20 | 0 |
50 | 25 | 5 | 20 | 0.25 |
50 | 20 | 10 | 20 | 0.5 |
50 | 20 | 15 | 15 | 1 |
50 | 20 | 20 | 10 | 2 |
Все компоненты тщательно смешивали с жидкой фазой, содержащей пептизатор (HNO3) и пластификатор (триэтиленгликоль), до образования однородной пасты. Пасту выдавливали поршневым экструдером через фильеру диаметром 2.5 мм. Экструдат выдерживали на воздухе, сушили и прокаливали, затем измельчали до гранул длиной 2.5–3.0) мм. Выдерживание на воздухе, высушивание и прокаливание приводили к постепенному превращению бемита в оксид алюминия, который связывал остальные компоненты в единый композит. В результате металлический алюминий и скелетный кобальт образовывали непрерывную теплопроводящую сеть. На рис. 1 приведены микрофотографии образца катализатора. Заметно, что все компоненты равномерно распределены в композите, видны транспортные поры, а также блестящие чешуйки металлического алюминия. Рис. 1б демонстрирует крупную частицу скелетного кобальта (Co), которая окружена чешуйками металлического алюминия (Al) и мелкими сферическими частицами цеолита Beta (HB).
Использование гранулированного катализатора позволяет обеспечить достаточную прочность для промышленного применения без разрушения гранул и уплотнения каталитического слоя. При этом могут возникать некоторые диффузионные ограничения массообмена в каталитическом слое. Несмотря на это, структура и объем пор композитного катализатора позволяет создать эффективную и высокопроизводительную систему.
Структурные параметры пористой системы приготовленных образцов были охарактеризованы по данным физической сорбции азота и гелиевой пикнометрии. Установлено, что удельная поверхность по БЭТ определяется содержанием цеолита, увеличиваясь в ряду: НВ/Со = 0 (65 м2/г) < < НВ/Со = 0.5 (114 м2/г) < НВ/Со = 1 (131 м2/г) < < НВ/Со = 2 (173 м2/г). Удельная поверхность цеолита Beta составляет 710 м2/г, а скелетного кобальта — 24–26 м2/г. Пористость бесцеолитного катализатора (НВ/Со = 0) составляет 0.72 см3/г. Введение цеолита в состав катализатора предсказуемо снижает пористость системы, которая при этом, однако, не зависит от количества цеолита и составляет 0.67–0.69 см3/г.
Сканирующая электронная микроскопия была выполнена на приборе VEGA 3 TESCAN.
Синтез проводили в проточном стальном реакторе с внутренним диаметром 10 мм. В реактор загружали 2.5 см3 катализатора без разбавления гранул инертным материалом. Перед синтезом катализатор активировали в токе водорода, подаваемого с объемной скоростью 3000 ч–1 при 400°С и 0.1 МПа в течение 1 ч. После активации катализатор разрабатывали в токе синтез-газа, поднимая температуру от 170 до 228–234°С на 3–10°С каждые 6 ч. Давление синтез-газа составляло 2 МПа. Синтез-газ (мольное соотношение Н2 : CO = 2, в состав смеси вводили 5 мол. % N2 в качестве внутреннего стандарта) подавали с объемной скоростью 1000 ч–1 (в режиме разработки – подъема и оптимизации температуры) и увеличивали до 5000 ч–1 (в режиме оптимизации производительности). В процессе оптимизации производительности при подъеме скорости синтез-газа на 1000 ч–1 повышали температуру синтеза на 3–6°С.
Катализаторы были испытаны в течение 110 ч в режиме пуск–остановка, при этом заметная деактивация не была зафиксирована.
Состав газообразных и жидких продуктов определяли хроматографически [17].
Основные показатели процесса рассчитывали следующим образом. Конверсия СО, % — доля прореагировавшего СО от пропущенного. Удельная активность (А), мкмоль СО/(г Со · с) — количество (мкмоль) прореагировавшего СО на 1г Со в 1 секунду. Селективность образования углеводородов С5+, мол. % — доля углерода в прореагировавшем CO, пошедшая на образование углеводородов С5+. Производительность катализатора по углеводородам С5+ — количество (г) жидких углеводородов, образовавшихся из пропущенного газа в единицу времени (ч) на единице массы катализатора (кг).
РЕЗУЛЬТАТЫ И ИХ ОБСУЖДЕНИЕ
Все исследованные катализаторы были активны в синтезе Фишера–Тропша и характеризовались высокой стабильностью и отсутствием деактивации в течение 100 часов синтеза. В синтезе при 1000 ч–1 конверсия СО уменьшалась с 78–80 до 70% при увеличении соотношения HB/Co с 0–0.5 до 2 (рис. 2). Для сравнения, гибридный гранулированный катализатор от компании Chevron, предлагаемый для промышленного применения [21], способен обеспечить конверсию СО не выше 40% при сопоставимых условиях синтеза.
Рис. 2.
Показатели синтеза Фишера–Тропша при 1000 ч–1: К – конверсия СО, %; S – селективность С5+, %; А – активность катализатора, мкмоль СО/(г Со с); Р – производительность С5+ г/кг/ч.
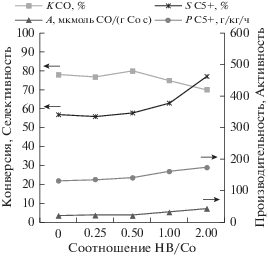
Во введении говорилось о том, что высокая общая активность кобальта Ренея в синтезе Фишера–Тропша известна давно, однако эти катализаторы не нашли промышленного применения из-за низкой удельной активности массивного металла. В данной работе нам удалось добиться высокой активности катализатора, содержащего скелетный кобальт. Введение цеолита в состав катализатора в количестве до 10% включительно (катализаторы с соотношением HB/Co 0.25 и 0.5) не привело к заметному увеличению удельной активности (рис. 2). Дальнейшее увеличение доли цеолита приводило к увеличению удельной активности до 45 мкмоль СО/(г Со · с), что объясняется одновременным снижением содержания скелетного кобальта (табл. 1).
На рис. 2 представлены данные, из которых следует, что производительность катализаторов по углеводородам С5+ равномерно возрастала с 132 до 174 г/кг/ч при увеличении доли цеолита, даже в случае снижения доли активного металла (катализаторы с соотношением HB/Co 1 и 2). Наибольшая производительность была получена в присутствии катализатора с соотношением HB/Co = 2, содержание кобальта в котором было минимальным, удельная активность — наибольшей, а конверсия СО — наименьшей. Таким образом, в синтезе при 1000 ч—1 введение цеолита в состав катализатора благоприятно влияет на его производительность даже в случае снижения содержания активного металла за счет появления синергетического эффекта между кислотными и металлическими активными центрами. Кислотные центры цеолита позволяют крекировать образующиеся тяжелые углеводороды и тем самым освобождают заблокированные кобальтовые центры для доступа исходных компонентов и продолжения реакции синтеза углеводородов.
Все катализаторы характеризовались высокой селективностью образования УВ С5+ (не ниже 56% при скорости подачи синтез-газа 1000 ч–1). При этом этот показатель возрастал до 77% при увеличении соотношения HB/Co (рис. 2). В работе [32] исследовали гибридный катализатор, который был получен при капсулировании катализатора Со/SiO2 в оболочку из композитного цеолита MOR/ZSM-5. Он был наиболее селективен в образовании углеводородов С5–С11 (72.3%) в СФТ при 260°С, 1 МПа и соотношении Н2/СО = 2. Однако конверсия СО при этом составляла всего 33.4%.
При увеличении скорости подачи синтез-газа с 1000 до 5000 ч–1 характер зависимости основных показателей процесса от соотношения HB/Co в основном не изменялся (рис. 3). Однако удельная активность возрастала в 2.8–4.2 раза, не смотря на снижение конверсии СО в 1.1–1.8 раза. Наибольшая конверсия СО (68–69%) была получена в присутствии катализаторов с соотношением HB/Co = 0.25–0.5.
Рис. 3.
Показатели синтеза Фишера–Тропша при 5000 ч–1. Обозначения аналогичны обозначениям на рис. 2.
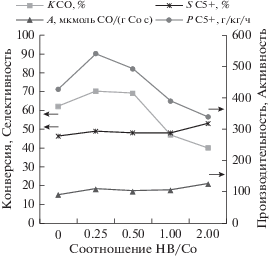
При повышении нагрузки по синтез-газу характер зависимости производительности катализаторов по УВ С5+ от соотношения HB/Co существенным образом изменялся (рис. 3). Введение 5% цеолита в состав катализатора приводило к резкому увеличению производительности до 540 г/(кг · ч) (HB/Co = 0.25). Увеличение его содержания до 10% приводило к некоторому снижению показателя до 500 г/(кг · ч) (HB/Co = 0.5). Дальнейшее увеличение соотношения HB/Co сопровождалось снижением содержания кобальта (табл. 1) и приводило к резкому снижению производительности по целевому продукту до 339 г/(кг · ч). Мы полагаем, что при объемной скорости 5000 ч−1 пятикратное увеличение скорости обтекания гранулы по сравнению с экспериментами при 1000 ч−1 приводит к существенному облегчению массообмена на поверхности гранулы, в результате чего высокая производительность обеспечивается оптимальным соотношением кислотных и кобальтовых активных центров (HB/Co 0.25 и 0.5).
Очевидно, что введение 5–10 мас. % цеолита в состав катализатора благоприятно влияло на конверсию СО и особенно на производительность по УВ С5+ при высоких нагрузках по синтез-газу (рис 3). Тогда как дальнейшее увеличение доли цеолита до 15–20% (которое сопровождалось снижением содержания кобальта) приводило к снижению конверсии СО при всех скоростях подачи синтез газа и производительности — при 5000 ч−1. Селективность образования УВ C5+ снижалась в 1.2–1.5 раза при повышении нагрузки по синтез-газу до 5000 ч–1.
Состав УВ С5+, образующихся в присутствии исследованных катализаторов, зависел и от соотношения HB/Co, и от условий синтеза (рис. 4). Состав продукта, полученного в синтезе при 1000 ч–1 в присутствии катализатора, который не содержал цеолит (НВ/Со = 0), характеризовался самым высоким содержанием н-парафинов (88%). Введение в состав катализатора цеолита приводило к снижению доли н-парафинов, причем, чем больше доля цеолита, тем заметнее это снижение. Минимальное количество н-парафинов получено в присутствии катализатора с соотношением НВ/Со = 2 (39%). Содержание олефинов равномерно возрастало при введении цеолита и увеличении его доли и составляло 3% в присутствии катализатора с соотношением НВ/Со = 0 и 36% — при соотношении НВ/Со = 2. Содержание изопарафинов было наименьшим в УВ, полученных в присутствии катализатора, не содержащего цеолит, и составляло 9%. При введении цеолита доля изопарафинов возрастала до 32% при НВ/Со = 0.5, снижаясь до 25% при НВ/Со = 2.
Сделанные наблюдения хорошо согласуются с данными работы [20]: похожие закономерности были замечены в присутствии нанесенного порошкового кобальт-цеолитного катализатора (соотношение цеолит/кобальт варьировалось от 4 до 9, условия синтеза — 200°C, 0.1 МПа, ~1700 ч–1, H2/CO = 2). Содержание изопарафинов и н-парафинов уменьшалось, а олефинов — увеличивалось при увеличении соотношения цеолит/кобальт.
Наибольшая вероятность роста цепи (0.83) характеризовала продукты, полученные в присутствии катализатора, не содержащего цеолит (рис. 4). Введение цеолита приводило к резкому снижению вероятности роста цепи до 0.75 при НВ/Со = 0.5, тогда как при увеличении доли цеолита вероятность роста цепи возрастала до 0.81 при НВ/Со = 2. Очевидно, что активность бифункционального катализатора определяется в первую очередь количеством металлических центров, доступных для образования УВ. Однако в присутствии кислотных центров образовавшиеся УВ могут претерпевать вторичные превращения, такие как крекинг, изомеризация и алкилирование. В результате комбинирования активных центров двух типов состав продукта будет определяться относительными скоростями реакций на кислотных и металлических центрах. Благодаря этому мы можем наблюдать нелинейную зависимость вероятности роста цепи от соотношения кобальт/цеолит.
Зависимость состава УВ С5+ от содержания цеолита при 5000 ч–1 существенно отличалась от полученной при 1000 ч–1 (рис. 5). Так, введение цеолита в состав катализатора приводило к значимым изменениям в составе продукта, а увеличение его содержания мало влияло на состав продукта.
При увеличении скорости синтез-газа до 5000 ч–1 содержание н-парафинов в УВ С5+ снижалось с 73%, полученных в присутствии катализатора, не содержащего цеолит, до 42–44% при НВ/Со = 0.5–2. В то же время, содержание олефинов увеличивалось с минимальных 17%, полученных в присутствии катализатора с соотношением НВ/Со = 0, до 37–38% при НВ/Со = 0.5–2. Наименьшее содержание изопарафинов (10%) было получено в присутствии катализатора, не содержащего цеолит, а введение и увеличение его доли приводило к повышению содержания изопарафинов до 18–20%. В условиях интенсивного массообмена на поверхности гранул время контакта снижается, поэтому образующиеся углеводороды, в частности, олефины, не успевают вступать в реакции олигомеризации, о чем также свидетельствует снижение количества высокомолекулярных продуктов.
Увеличение скорости подачи синтез-газа приводило к снижению вероятности роста цепи (рис. 4, 5). Так, в синтезе при 5000 ч–1 этот показатель снижался в 1.1 раз по сравнению с данными, полученными при 1000 ч–1. Характер зависимости вероятности роста цепи от соотношения НВ/Со при этом мало изменился, т.е. вероятность роста цепи снижалась при введении цеолита и увеличивалась при повышении его доли.
Таким образом, сочетание скелетного кобальта и цеолита в составе композитного катализатора позволяет получать легкую синтетическую нефть напрямую из СО и Н2, а изменение соотношения цеолит/кобальт — контролировать ее состав. Сравнение исследованных катализаторов с другими кобальт-цеолитными системами, например, описанными в [21, 22], подчеркивает преимущества предложенных катализаторов, таких как высокие конверсия СО, удельная активность, производительность и стабильность.
Исследовано влияние соотношения содержания скелетного кобальта и цеолита в составе гранулированного композитного катализатора. Установлено, что все катализаторы были активны в СФТ. Показано, что введение цеолита в состав катализатора благоприятно влияет на конверсию СО и производительность по углеводородам С5+, особенно при высоких нагрузках по синтез-газу. Введение цеолита в состав катализатора интенсифицирует массообмен на поверхности гранулы за счет крекирования восков и освобождения заблокированных ими активных кобальтовых центров для доступа исходных компонентов. Наибольшая производительность при скорости подачи синтез-газа 1000 ч–1 была достигнута в присутствии катализатора с соотношением НВ/Со = 2, который при этом характеризовался наибольшей удельной активностью и наименьшей конверсией СО. Однако при повышении скорости подачи синтез-газа до 5000 ч–1 наиболее производительным был катализатор с соотношением НВ/Со = 0.25, характеризующийся средней удельной активностью и максимальной конверсией. Таким образом, для достижения высокой производительности композитный кобальтовый катализатор СФТ не должен отличаться слишком высокой удельной активностью.
Состав углеводородов С5+, образующихся в присутствии исследованных катализаторов, зависит и от соотношения цеолит/скелетный кобальт, и от условий синтеза, поскольку определяется скоростями конкурирующих реакций на металлических и кислотных центрах. Показаны возможности контролирования состава образующихся углеводородов путем введения цеолита в состав катализатора. В синтезе при 1000 ч–1 введение и увеличение доли цеолита приводит к снижению доли н-парафинов, снижению доли олефинов и снижению вероятности роста цепи. Повышение нагрузки по синтез-газу приводит к тому, что введение цеолита способствует уменьшению содержания н-парафинов, увеличению содержания олефинов и изопарафинов, а увеличение его доли уже не оказывает столь заметного влияния.
Следует отметить, что наиболее чувствительным к увеличению скорости синтез-газа был катализатор, не содержащий цеолит, что подтверждает предложенное положительное влияние цеолита на массообмен в гранулах композитного катализатора. Таким образом, можно заключить, что введение цеолита в состав гранулированного композитного катализатора способствует интенсификации массообмена, особенно в условиях высокой нагрузки по синтез-газу, что является критичным для СФТ [33].
Список литературы
Dry M., Steynberg A. Fischer–Tropsch Technology (Studies in surface science and catalysis). Amsterdam: Elsevier, 2004.
Baliban R.C., Elia J.A., Floudas C.A. // AIChE J. 2013. V. 59. P. 505.
Song D., Li J. // J. Mol Catal A: Chem. 2006. V. 247. P. 206.
Maitlis P.M., de Klerk A. (eds.) Greener Fischer–Tropsch Processes. Weinheim: Wiley–VCH, 2013.
de Klerk A., Furimsky E. Catalysis in the refining of Fischer–Tropsch syncrude. Cambridge: RSC Publishing, 2010.
van Steen E., Claeys M. // Chem. Eng. Technol. 2008. V. 31. P. 655.
Fischer F., Meyer H. // Ber. 1934. V. 67. P. 253.
Ejdus Ya.T. // Russ. Chem. Bull. 1971. V. 20. P. 589.
Mikhailenko S.D., Khodareva T.A., Leongardt E.V., Lyashenko A.I., Fasman A. // J. Catal. 1993. V. 141. P. 688.
Storch H., Golumbic N., Anderson R. The Fischer–Tropsch and Related Synthesis. New York: John Wiley & Sons, 1951.
Sineva L.V., Mordkovich V.Z., Ermolaev V.S., Ermolaev I.S., Mitberg E.B., Solomonik I.G. // Catalysis in Industry. 2012. V. 6. P. 13.
Mordkovich V.Z., Ermolaev V.S., Ermolaev I.S., Mitberg E.B., Sineva L.V., Solomonik I.G. // Proc. AIChE Spring Meeting and 7th Global Congress on Process Safety. 2011. P. 42.
Sineva L.V., Mordkovich V.Z., Khatkova E.Yu. // Mendeleev Commun. 2012. V. 23. P. 44.
Mordkovich V.Z., Ermolaev V.S., Mitberg E.B., Sineva L.V., Solomonik I.G., Ermolaev I.S., Asalieva E.Yu. // Res. Chem. Intermed. 2015. V. 41. P. 9539.
Lapidus A.L., Krylova A.Yu. // Russian Chem. Reviews. 1998. V. 67. P. 941.
Li Y., Wang T., Wu C., Li H., Qin X., Tsubaki N. // Fuel Proc. Tech. 2010. V. 91. P. 388.
Савостьянов А.П., Яковенко Р.Е., Салиев А.Н., Нарочный Г.Б., Митченко С.А., Зубков И.Н., Соромотин В.Н., Кирсанов В.А. // Нефтехимия. 2018. Т. 58. С. 332.
Sartipi S., van Dijk J.E., Gascon J., Kapteijn F. // Appl. Catal. A: Gen. 2013. V. 456. P. 11.
Jin Yu., Yang R., Mori Y., Sun J., Taguchi A., Yoneyama Y., Abe T., Tsubaki N. // Appl. Catal. A: Gen. 2013. V. 456. P. 75.
Espinosa G., Dominguez J.M., Morales-Pacheco P., Tobon A., Aguilar M, Benitez J. // Catal. Today. 2011. V. 166. P. 47.
Kibby C., Jothimurugesan K., DasT., Lacheen H.S., Rea T., Saxton R.J. // Catal. Today. 2013. V. 215. P. 131.
Martinez A., Valencia S., Murciano R., Cerqueira H.S., Costa A.F., S.-Aguiar E.F. // Appl. Catal A: Gen. 2008. V. 346. P. 117.
Sartipi S., Parashar K., Makkee M., Gascon J., Kapte-ijn F. // Catal. Sci. Technol. 2013. V. 3. P. 572.
Rabo J.A. Zeolite Chemistry and Catalysis. Washington: American Chemical Soc., 1979.
Zola A.S., Bidart A.M.F., Fraga A.C., Hori C.E., Sousa-Aguiar E.F., Arroyo P.A. // Stud. Sur. Sci. and Cat. 2007. vol. 167. p. 129.
Subramanian V., Zholobenko V.L., Cheng K., Lancelot C., Heyte S., Thuriot J., Paul S., Ordomsky V.V., Khodakov A.Y. // ChemCatChem. 2015. vol. 8. p. 380.
Carvalho A., Marinova M., Batalha N., Marcilio N. R., Khodakov A.Y., Ordomsky V.V. // Catal. Sci. Technol. 2017. vol. 7. p. 5019.
Espinosa G., Domínguez J.M., Morales-Pacheco P., Tobon A., Aguilar M., Beníteza J. // Catal. Today. 2011. vol. 166. p. 47.
Mordkovich V.Z., Sineva L.V., Solomonik I.G., Ermolaev V.S., Mitberg E.B. // WO 2010147513. 2011.
Mordkovich V.Z., Sineva L.V., Solomonik I.G., Ermolaev V.S., Mitberg E.B. // WO 2011016759. 2011.
Mordkovich V.Z., Sineva L.V., Solomonik I.G., Ermolaev V.S., Mitberg E.B. // Rus. Patent № 2422202. 2011.
Cheng S., Mazonde B., Zhang G., Javed M., Dai P., Cao Y., Tu S., Wu J., Lu C., Xing C., Shan S. // Fuel. 2018. V. 223. P. 354.
Brosius R., Fletcher J.C.Q. // J. Catal. 2014. V. 317. P. 318.
Дополнительные материалы отсутствуют.