Нефтехимия, 2020, T. 60, № 1, стр. 83-88
Влияние промоторов ультрадисперсных катализаторов на образование диоксида углерода в условиях синтеза Фишера–Тропша в трехфазной системе
М. В. Куликова 1, *, О. С. Дементьева 1, С. И. Норко 1, 2
1 Институт нефтехимического синтеза им. А.В. Топчиева РАН
119991 Москва, Россия
2 Московский государственный университет имени М.В. Ломоносова
119991 Москва, Россия
* E-mail: m_krylova@ips.ac.ru
Поступила в редакцию 20.08.2019
После доработки 29.08.2019
Принята к публикации 09.09.2019
Аннотация
Проведено исследование влияния свойств модифицирующих добавок (Mg и Ca) к наноразмерным каталитическим дисперсиям на протекание трехфазного синтеза Фишера–Тропша. Установлено, что введение в состав каталитической дисперсии Mg и Ca способствует перераспределению кислородсодержащих продуктов: позволяет снизить выход основного побочного соединения – СО2 и повысить выход спиртов, растворенных в воде.
ВВЕДЕНИЕ
Постоянно ужесточающиеся экологические требования способствуют развитию процессов производства топлив с низким содержанием серы и ароматических соединений [1]. В настоящее время появился и устойчиво растет спрос на углеводородные топлива с ультранизким содержанием гетероатомов (менее 10 ppm серы и азота [2, 3]). Особое внимание уделяется разработке так называемых СО2-нейтральных процессов в целях сокращения антропогенного влияния и его последствий на окружающую среду. В этой связи, а также с учетом истощения запасов легко перерабатываемой нефти закономерно возникает интерес к процессам класса XTL, которые позволяют получать экологически чистые синтетические углеводороды (УВ) из малоценного сырья. В частности, синтез Фишера–Тропша является перспективным путем производства широкого спектра УВ из угля, природного газа и биомассы.
При реализации процесса Фишера–Тропша с применением реакторов со стационарным слоем катализатора, его активность непрерывно снижается из-за локальных перегревов неподвижного каталитического слоя ввиду экзотермичности реакции. В сларри-реакторах данный недостаток устраняется присутствием дисперсионной среды, эффективно отводящей тепло, однако возникает необходимость в высоких линейных скоростях потока сырьевого газа для поддержания микросферического катализатора во взвешенном состоянии. Перспективным подходом для осуществления реакции в системе газ–жидкость–твердое тело является применение наноразмерных дисперсий, не накладывающих ограничений на гидродинамический режим эксплуатации реактора, и, как следствие, позволяющих увеличить степень превращения сырья за проход и повысить производительность катализатора в сравнении с традиционными системами [4, 5].
Железосодержащие контакты наиболее предпочтительны для синтеза Фишера–Тропша, поскольку обладают низкой стоимостью и позволяют конвертировать в УВ синтез-газ с низким соотношением Н2/СО, которое характерно для газа, полученного из биомассы или угля [6, 7]. Применение наноразмерных катализаторов в сларри-реакторах приводит к значительному увеличению производительности системы по целевым продуктам синтеза до 300–500 ${{{{{{{\text{г}}}_{{{{{\text{C}}}_{{5 + }}}}}}} \mathord{\left/ {\vphantom {{{{{\text{г}}}_{{{{{\text{C}}}_{{5 + }}}}}}} {{\text{к}}{{{\text{г}}}_{{{\text{Me}}}}}}}} \right. \kern-0em} {{\text{к}}{{{\text{г}}}_{{{\text{Me}}}}}}}} \mathord{\left/ {\vphantom {{{{{{{\text{г}}}_{{{{{\text{C}}}_{{5 + }}}}}}} \mathord{\left/ {\vphantom {{{{{\text{г}}}_{{{{{\text{C}}}_{{5 + }}}}}}} {{\text{к}}{{{\text{г}}}_{{{\text{Me}}}}}}}} \right. \kern-0em} {{\text{к}}{{{\text{г}}}_{{{\text{Me}}}}}}}} {\text{ч}}}} \right. \kern-0em} {\text{ч}}}$ [5], что в несколько раз превышает значения, получаемые в присутствии традиционных систем [8]. Несмотря на указанные преимущества, нанодисперсии обладают недостатками нанесенных и микрометрических Fe-катализаторов: склонностью к дезактивации кислородсодержащими продуктами реакциии, образованию большого количества СО2 по реакции водяного газа, в результате чего часть углерода необратимо конвертируется в побочный продукт процесса [9, 10].
Основные способы подавления образования диоксида углерода в присутствии Fe-контактов – подбор условий осуществления реакции (температуры, давления, отношения H2/CO, парциального давления воды) и модификация катализатора компонентами, образующими поверхность, не склонную к повторной адсорбции воды, вступающей в реакцию с адсорбированным монооксидом углерода с образованием СО2 [11–18]. В частности, в работе [12] была проведена химическая модификация железосодержащих контактов путем нанесения на их поверхность SiO2-пленки, полученной разложением тетраэтоксисилана. Авторы показали, что модификация поверхности не приводила к снижению адсорбционной способности катализаторов по отношению к СО – ингибирование реадсорбции воды и, таким образом, реакции водяного газа являлось результатом формирования гидрофобной оболочки на активных центрах, в результате чего образование CO2 снижалось с 40 до 5% в пересчете на углерод.
Введение в состав Fe-катализаторов добавок щелочных и щелочно-земельных металлов приводит к подавлению процесса окисления карбидных фаз железа, на которых происходит полимеризация углеродсодержащих фрагментов с образованием УВ, до магнетита, являющегося наиболее активной фазой для протекания реакции водяного газа [13–15]. Авторами [13] установлено уменьшение содержания магнетита в составе железосодержащей фазы контактовот 43.8 до 37.9% при промотировании их Mg; именно с этим они связывали снижение селективности в отношении образования СО2 от 50 до 40.8%. В работе [14] показано, что под действием Са и Mg увеличивается доля обогащенных углеродом карбидов железа, наличие которых способствует усилению адсорбции СО, повышая количество углерода, участвующего в росте цепи. Изучение серии Fe-катализаторов с добавками К, Ве, Mg, Ca и Ba позволило установить ингибирующее действие Сa и Mg в составе контакта на его активность в реакции водяного газа, тогда как остальные добавки способствовали увеличению скорости образования диоксида углерода [15]. Подобный эффект наблюдали в работе [16]: максимальное содержание карбидных форм железа на каталитической поверхности достигали при повышении отношения Mg/Fe до 0.07, при этом доля СО, конвертирующегося в УВ, возрастала с одновременным снижением количества образующегося диоксида углерода.
Промотирование каталитических систем Mg, Ca и La наряду с подавлением образования диоксида углерода способствует изменению производительности контактов по непредельным УВ и кислородсодержащим соединениям за счет увеличения основности поверхности при образовании твердых растворов оксидов железа и промоторов, и, как следствие, усиления диссоциативной адсорбции СО [17, 18].
В силу особенностей формирования активной фазы наноразмерных суспензий в сравнении с пропиточными и соосажденными катализаторами [19, 20], невозможно напрямую применить традиционные методы промотирования и модификации каталитических систем к дисперсиям для осуществления синтеза Фишера–Тропша в сларри-реакторе.
Для изучения проблемы направленного изменения свойств таких систем в настоящей работе исследованы суспендированные в углеводородной среде Fe-содержащие наноразмерные каталитические системы, модифицированные добавками щелочно-земельных металлов (Ca и Mg).
В ходе работы установлено влияние содержания модифицирующих добавок на селективность каталитической суспензии в отношении образования диоксида углерода и целевых продуктов синтеза.
ЭКСПЕРИМЕНТАЛЬНАЯ ЧАСТЬ
Железосодержащие дисперсные системы для осуществления синтеза УВ по методу Фишера–Тропша готовили с применением методов термического разложения растворов прекурсоров железа (термолиз).
Pасчетное количество нитрата железа вводили из 40%-го водного раствора в расплавленную дисперсионную среду (смесь твердых парафинов фракции С19–С32) при 280°C при перемешивании в токе инертного газа. Был синтезирован ряд железосодержащих образцов с содержанием кальция и магния в диапазоне 4.5–12.0 мас. % в качестве модифицирующих агентов. Прекурсоры железа, магния и кальция представляли собой их нитраты. Расчет навески прекурсоров производили на нольвалентную форму компонента, при этом содержание железа в составе дисперсной системы во всех случаях составляло 1 мас. %, а количество модифицирующего агента рассчитывали в процентах от содержания Fe.
Размер частиц синтезированных образцов определяли методом динамического светорассеяния на приборе MalvernZetasizer Nano ZS. Пробоподготовку осуществляли растворением 0.01 г образца суспензии в 10 мл н-гексана с добавлением 5 мас. % ПАВ (диоктилсульфосукцината натрия).
РФА образцов проводили на рентгеновской установке RigakuRotaflex D/MAX-RC с вращающимся медным анодом (длина волны характеристического Kα-излучения λ = 0.1542 нм). За счет использования вторичного монохроматора – монокристалла графита – был минимизирован вклад от флуоресцентного излучения атомов железа в экспериментальные дифрактограммы. Рентгеновская съемка проводилась с помощью горизонтального широкоуглового гониометра по схеме Брэгга–Брентано в геометрии θ–2θ. Ска-нирование проводилось в угловом диапазоне 10°–70° по 2θ со скоростью 1°/мин и с шагом 0.04°.
Оценку каталитической активности образцов дисперсий проводили в проточной по газу установке со сларри-ректором. Предварительно каталитические системы активировали под давлением монооксида углерода (2 МПа) в течение 12 ч при температуре 360°С. Синтез УВ осуществляли в токе синтез-газа со скоростью подачи 10 л/ч с мольным отношением СО : Н2 = 1 : 1 под давлением 2 МПа в интервале температур 260–320°С c подъемом температуры на 20°С каждые 12 ч. Отбор проб газа и жидкости на анализ осуществляли для каждого температурного режима через 8–12 ч после подъема температуры. Исходный синтез-газ и газообразные продукты синтеза анализировали методом ГАХ на хроматографе “Кристаллюкс-4000” (детектор – катарометр, газ-носитель – гелий). Для разделения СО, СН4 и N2 применяли колонку, заполненную молекулярными ситами СаА (3 м × 3 мм), для разделения СО2 и УВ С2–С4 использовали колонку, заполненную HayeSept. Анализ жидких УВ проводили на хроматографе “Кристаллюкс-4000М”, оснащенном ПИД-детектором и капиллярной колонкой OV-351 (50 м × × 0.32 мм) при температурно-программированном режиме (подача гелия – 30 мл/мин, водорода – 25 мл/мин, воздуха – 250 мл/мин). Водную фазу анализировали методом газо-адсорбционной хроматографии на хроматографе “Кристаллюкс-4000М”. Детектор – пламенно-ионизационный. Скорость подачи газов: гелий – 20 мл/мин, водорода – 25 мл/мин, воздух – 250 мл/мин. Для анализа использовали капиллярную колонку HP-FFAP (полиэтиленгликоль, модифицированный нитротерефталевой кислотой) (50 м × × 0.32 мм × 0.50 мкм). Объем пробы – 0.3 мкл. Температурный режим – 70°С (8 мин), термопрограммируемый нагрев от 70°С до 110°С со скоростью 10°С/мин, термопрограммируемый нагрев от 110 до 220°С со скоростью 15°С/мин, и выдержка при 220°С в течении 10 мин.
Для оценки активности катализатора были выбраны следующие показатели: XСО, % – конверсия СО (процентное отношение массы прореагировавшего СО к массе СО, вошедшего в реакционную зону); выход продуктов YN, г/м3 –количество граммов продукта N, полученное при пропускании через катализатор 1 м3 синтез-газа, приведенного к нормальным условиям; селективность по продуктам SN; % – процентное отношение углерода, пошедшего на образование продукта, к общему количеству прореагировавшего углерода.
РЕЗУЛЬТАТЫ И ИХ ОБСУЖДЕНИЕ
Образцы каталитических суспензий были изучены методом РФА после предварительной активации в токе монооксида углерода и исследования в синтезе УВ по методу Фишера–Тропша в интервале температур 260–320°С для установления фазового состава активной поверхности контакта, формирующейся непосредственно в ходе реакции гидрирования СО. Показано, что введение добавок кальция и магния способствует более интенсивному формированию карбидов железа Fe5C2 и Fe7C3 (рис. 1а, 1б), наличие которых в составе каталитической поверхности приводит к подавлению реакции водяного газа за счет снижения содержания фазы магнетита, активной в реакции водяного газа [13, 14].
Установлено, что в присутствии добавки магния увеличение ее содержания свыше 7.5% от железосодержащей фазы приводит к уменьшению доли карбидной фазы железа, тогда как эффект от введения магния сохраняется во всем диапазоне его концентраций.
Каталитические дисперсии были проанализированы методом динамического светорассеяния непосредственно после формирования методом капельного термолиза. Было показано, что введение добавок магния и кальция во всех случаях приводило к увеличению диаметра частиц дисперсной фазы по сравнению с непромотированным катализатором от 0.7 до 2.1–3.3 нм (рис. 2). Однако, в присутствии модификаторов в ходе синтеза Фишера–Тропша происходило незначительное укрупнение частиц дисперсной фазы на 15–20% против с четырехкратного (до 3 нм) увеличения диаметра металлсодержащих частиц, наблюдаемого для непромотированного образца.
Рис. 2.
Среднечисловое распределение частиц дисперсной фазы по размерам для Fe-систем с модифицирующими добавками различной природы.
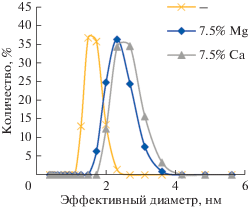
Модифицированные Fe-катализаторы проявляли пониженную активность ко вторичной реакции водяного газа. Так, селективность по диоксиду углерода в присутствии Mg и Са во всех случаях снижалась за счет утилизации кислорода в воду и оксигенаты, растворимые в водной фазе (преимущественно спирты С1−С4) (табл. 1, рис. 3).
Таблица 1.
Влияние модифицирующей добавки на активность каталитических суспензий в синтезе углеводородов по методу Фишера–Тропша (Т = 300–320°С, ХCO = 60%)
Модифицирующая добавка | Выход, г/м3 | П, г/кг Ме ч | |||||
---|---|---|---|---|---|---|---|
С1 | С2–С4 | С5+ | СО2 | Oxy | H2O | ||
– | 20 | 28 | 47 | 216 | 4 | 34 | 471 |
4.5% Mg | 13 | 18 | 42 | 128 | 6 | 40 | 415 |
4.5% Ca | 18 | 25 | 66 | 142 | 8 | 83 | 656 |
7.5% Mg | 30 | 30 | 48 | 191 | 13 | 62 | 478 |
7.5% Ca | 13 | 18 | 85 | 127 | 22 | 108 | 847 |
12% Mg | 20 | 26 | 37 | 154 | 13 | 44 | 373 |
12% Ca | 25 | 29 | 45 | 169 | 23 | 67 | 454 |
Рис. 3.
Влияние степени превращения исходного сырья на селективность в отношении образования диоксида углерода в присутствии каталитических суспензий с модифицирующими добавками различной природы.
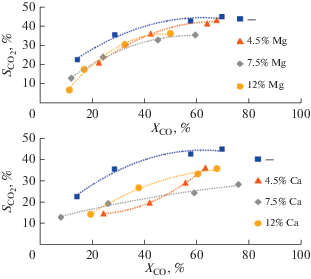
В общем случае введение модификаторов в состав каталитической системы приводило к значительному изменению молекулярно-массового распределения продуктов реакции, оказывая влияние на выход как газообразных, так и жидких продуктов реакции.
В частности, введение добавки магния в количестве 4.5 мас. % от содержания железной фазы приводило к снижению образования УВ фракции С1–С4 с одновременным увеличением выхода спиртов. Содержание олефинов в составе жидких УВ повышалось от 26.4 до 36.1 мас. %; при этом молекулярно-массовое распределение продуктов реакции смещалось в сторону образования бензиновой фракции (табл. 2). Дальнейшее увеличение содержания магния до 7.5–12% вызывало интенсификацию образования метан-бутановой фракции, однако образование диоксида углерода при этом оставалось ниже значений, зарегистрированных для немодифицированного образца. Содержание олефинов в составе продуктов для данных систем достигало 39.4%, причем 80% непредельных соединений содержалось в бензиновой фракции УВ.
Таблица 2.
Влияние модифицирующей добавки на состав жидких углеводородов, полученных по методу Фишера–Тропша (Т = 300–320°С, ХCO = 60%)
Модифицирующая добавка | Групповой состав | Фракционный состав | α | ||||
---|---|---|---|---|---|---|---|
н-парафины | изо-парафины | олефины | С5–С10 | С11–С18 | С19+ | ||
– | 30.9 | 42.8 | 26.4 | 62.9 | 32.0 | 5.2 | 0.75 |
4.5% Mg | 31.9 | 36.1 | 32.0 | 69.2 | 28.6 | 2.2 | 0.74 |
4.5% Ca | 31.1 | 35.5 | 33.4 | 68.2 | 29.5 | 2.3 | 0.73 |
7.5% Mg | 32.1 | 34.7 | 30.8 | 59.0 | 34.1 | 6.9 | 0.77 |
7.5% Ca | 29.2 | 32.4 | 38.4 | 70.0 | 27.0 | 2.9 | 0.70 |
12% Mg | 25.2 | 35.3 | 39.4 | 62.0 | 34.0 | 4.0 | 0.74 |
12% Ca | 33.7 | 34.0 | 32.2 | 71.9 | 27.3 | 0.8 | 0.71 |
Для систем, модифицированных кальцием, наблюдали более значительное изменение образования диоксида углерода: во всем диапазоне активности образцов происходило снижение селективности по данному продукту не менее, чем на 20%, достигая 45–50% в области малых конверсий (рис. 3).
В присутствии Са-содержащих катализаторов удалось повысить выход жидких УВ и спиртов в 1.8 и 5.7 раз, соответственно (в сравнении с системой без добавок), содержание ненасыщенных структур в составе УВ С5+ также возрастало, достигая 38.4 мас. % при содержании добавки Са 7.5%. (табл. 1, 2).
Относительное содержание спиртов (в % от общей массы), полученных в присутствии дисперсных железосодержащих систем с добавками модифицирующих агентов в различной концентрации, представлено на рис. 4. Введение небольших количеств модификаторов (4.5% Ca и Mg) способствовало увеличению содержания спиртов С4+, тогда как повышение концентрации добавки приводило к интенсификации образования спиртов С2+: их доля в составе кислородсодержащих продуктов возрастала от 75% для образца без добавок до 80–82%.
ВЫВОДЫ
В работе изучен ряд образцов железосодержащих наноразмерных суспензий с добавками магния и кальция, приготовленных методом капельного термолиза. Установлено, что введение модифицирующих добавок в количестве 4.5–12.0 мас. % от содержания железа приводило к уменьшению выхода СО2 на 20–40% при сохранении активности каталитической системы в отношении степени превращения исходного сырья. Содержание бензиновой фракции УВ при введении добавок магния и кальция возрастало от 63 до 70%, при этом во всех случаях доля ненасыщенных продуктов увеличивалась от 26 до 30–44 мас. %. Введение магния и кальция в качестве модификаторов позволило увеличить долю спиртов С2+ от 75 до 80–82 отн. %.
Показано, что введение добавок во всех случаях приводило к увеличению диаметра частиц дисперсной фазы по сравнению с непромотированным катализатором от 0.7 нм до 2.1‑3.3 нм, однако в ходе синтеза УВ по методу Фишера–Тропша размер частиц дисперсной фазы с добавками модификаторов увеличивался не более, чем на 20%.
Методом рентгенофазового анализа установлено, что в присутствии модифицирующих добавок магния и кальция в ходе предварительной активации контактов монооксидом углерода (карбидизации) и обработки синтез-газом формируется железосодержащая фаза с большим содержанием углерода (Fe5C2 против Fe7C3 для немодифицированного образца).
Список литературы
Dry M.E // Catalysis Today. 2002. V. 71. P. 227.
ГOCT 32513-2013.
TPTC 013/2011.
Хаджиев С.Н. // Нефтехимия. 2011. Т. 51. № 1. С. 3.
Хаджиев С.Н., Сагитов С.А., Лядов А.С., Куликова М.В., Крылова А.Ю. // Нефтехимия. 2014. Т. 54. № 2. С. 88.
Review: Biomass for Energy // J. Sci. Food Agriculture. 2006. V. 86. P. 1755.
Mallick D. et al. // J. of the Energy Institute. https://doi.org/10.1016/j.joei.2019.04.005
Todic B, Nowicki L., Nikacevi N., Bukur D.B. // Catalysis Today. 2016. V. 261. P. 28.
Steynberg A.P., Dry M.E., Davis B.H., Breman B.B. // Stud. Surf. Sci. Catal. 2004. V. 152. P. 64.
Liu Y, Teng B.T., Guo X.H., Li Y., Chang J., Tian L., Hao X., Wang Y., Xiang H.W., Xu Y.Y., Li Y.W. // J. Mol. Catal. A Chem. 2007. V. 272. P. 182
Bukur D.B., Todic B., Elbashir N. // Catal. Today. 2016. V. 275. P. 66.
Xufei Yu., Zhang J., Wang X., Ma Q., Gao X., Hongqiang X., Xiaoyong L., Subing F., Tian-Sheng Z. // Applied Catalysis B: Environmental. 2018. V. 232. P. 420.
Yi Cheng, Jun Lin, Tijun Wu, Hao Wang, Songhai Xie, Yan Pei, Shirun Yan, Minghua Qiao, Baoning Zong // Applied Catalysis B: Environmental. 2017. V. 204. P. 475.
Pour Ali Nakhaei, Mohammad Reza Housaindokht, Jamshid Zarkesh, Sayyed Faramarz Tayyari // J. of Industrial and Engineering Chemistry. 2010. V. 16. № 6. P. 1025.
Mingsheng L., Burtron H. // Davis Applied Catalysis A: General. 2003. V. 246. No 1. P. 171.
Yang Y., Sun Y.C, Tang Y., Liu Y., Wang H.L., Tian L, Wang H., Zhang Z.X, Xiang H.W., Li Y.W. // J. Mol. Catal. A. 2006. V. 245. P. 26.
Pour A.N., Shahri S.M.K., Zamani Y., Irani M., S. Tehrani // J. Nat. Gas. Chem. 2008. № 17. P. 242.
Shiya L.I. et al. // J. of Fuel Chemistry and Technology. 2018. V. 46. № 11. P. 1342.
Khadzhiev S.N., Kadiev K.M., Kadieva M.K. // Petrol. Chemistry. V. 54. № 5. P. 323.
Guala A. Godard C., Castillon S, Curulla-Ferre D., Carmen C. // Catalysis Today. 2012. V. 183. P. 154.
Дополнительные материалы отсутствуют.