Нефтехимия, 2020, T. 60, № 1, стр. 114-124
Селективное раскрытие углеводородного кольца в этилбензоле на бифункциональном Pt–Ir-катализаторе с использованием иерархического цеолита USY в качестве носителя
Elena Pérez-Guevara 1, 2, 3, *, Jose M. G. Molinillo 2, **, Enrique J. Martínez de la Ossa 3, ***, Juana Frontela 1, ****, Jesús Lázaro 1, *****, María José Franco 1, ******
1 Cepsa Research Center, Compañía Española de Petróleos S.A.U.
Alcalá de Henares Madrid, Av. Punto Com 1, 28850 Spain
2 Department of Organic Chemistry, School of Sciences, Institute of Biomolecules (INBIO), University of Cadiz
Puerto Real Cádiz,
C/República Saharaui, 7, 11510 Spain
3 Department of Chemical Engineering and Food Technology, School of Sciences, University of Cadiz
Puerto Real Cádiz, C/República Saharaui 7, Spain
* E-mail: elena.perez@cepsa.com
** E-mail: chema.gonzalez@uca.es
*** E-mail: enrique.martinezdelaossa@uca.es
**** E-mail: juana.frontela@cepsa.com
***** E-mail: jesusjavier.lazaro@cepsa.com
****** E-mail: mariajose.franco@cepsa.com
Поступила в редакцию 08.05.2019
После доработки 20.06.2019
Принята к публикации 06.09.2019
Аннотация
Разработан бифункциональный катализатор для реакции селективного раскрытия углеводородного кольца с использованием иерархического цеолита в качестве носителя. Катализатор приготовлен с введением дополнительной мезопористости в микропористую структуру цеолита USY путем постсинтетического мезоструктурирования с использованием поверхностно-активного вещества. Также синтезированы монометаллические и биметаллические катализаторы Pt(x)–Ir(y) с различными концентрациями металлов и мольными отношениями Pt/Ir. Для оптимизации кислотно-металлического баланса кислотность носителя модулировалась с помощью ионного обмена с Na+. Каталитическую активность полученных катализаторов испытывали в реакции превращения этилбензола в проточном реакторе со стационарным слоем катализатора при 275°С и 3 МПа. Наилучшие показатели достигнуты на катализаторе со следующими металлическими характеристиками: Pt(2)–Ir(1). Ir проявляет высокую активность в реакциях гидрогенолиза и гидрирования, в то время как Pt проявляет низкую активностью по реакции крекинга. Каталитические свойства также были улучшены посредством изменения количества кислотных центров в носителе. Таким образом на катализаторе Pt(2)–Ir(1)/Na–FAU–CTAB получены наилучшие показатели по выходу парафинов, которые увеличивают значение цетанового числа топлив.
На сегодняшний день нефть по-прежнему остается основным ресурсом для получения углеводородов и энергии. В связи с постепенным истощением мировых запасов нефти возникает потребность в переработке тяжелого и низкокачественного нефтяного сырья, которое содержит полиароматические соединения, асфальтены и соединения серы. Также ужесточаются экологические стандарты на углеводородные продукты, из-за чего перед нефтеперерабатывающими предприятиями возникает проблема по переработке нетрадиционных нефтяных продуктов в углеводороды с высокой добавленной стоимостью, которые соответствуют современным экологическим стандартам [1–4]. В дизельном топливе из-за присутствия полиароматических и нафтеновых углеводородов увеличивается объем выхлопных газов автомобилей и ухудшаются характеристики по воспламеняемости топлива, снижается значение цетанового числа (ЦЧ) [5, 6]. Процессы по переработке тяжелых органических соединений до легких углеводородов с низким содержанием аренов и высоким значением ЦЧ актуальны и интересны. Для увеличения показателя ЦЧ используют реакцию селективного раскрытия углеводородного кольца [7–9]. Реакция гидрирования полиароматических соединений – возможный маршрут для увеличения ЦЧ, например, при гидрировании декалина ЦЧ топлива увеличивается с 1 до 36 по отношению к нафталину. Однако, этого недостаточно для достижения требуемых значений ЦЧ дизельного топлива, минимальный порог по ЦЧ равен 51. Для достижения необходимого значения ЦЧ осуществляют последующее раскрытие нафтенового кольца. К примеру, значение ЦЧ для н-декана соответствует 77. Также разветвленные парафины имеют значение ЦЧ меньше, чем продукты гидрирования полиароматических соединений. Из-за чего для увеличения ЦЧ необходимо осуществить полное гидрирование ароматических колец и селективное раскрытие колец нафтенов с образованием неразветвленных парафинов. Кроме того, в процессе реакции следует сохранять среднее число атомов углерода в продуктах посредством блокировки реакции крекинга [2, 10].
Бифункциональные катализаторы, которые обладают кислотными свойствами и имеют металлические промоторы, лучше всего подходят для реакции селективного раскрытия углеводородного кольца. Кислотные центры катализируют реакцию крекинга и изомеризацию, в то время как металлический промотор способствует протеканию реакций гидрогенолиза, гидрирования и дегидрирования [1, 2, 5, 11]. Механизм реакции селективного раскрытия углеводородного кольца протекает через общее взаимодействие кислотных и металлических функций катализатора. На первом этапе происходит гидрирование ароматических соединений до нафтенов, после чего в ходе реакции дегидрирования образуются циклические олефины. Протекание двух последовательных реакций осуществляется на металлических центрах катализатора. Кислотные центры отвечают за образование ионов карбена в реакции протонирования олефинов. Кислотные центры также отвечают за скелетную изомеризацию углеводородов, а именно сокращение кольца С6 до С5, данная стадия является лимитирующей в реакции расщепления углеводородного кольца. Раскрытие углеводородного кольца может осуществляться через β-расщепление связи углерод–углерод при взаимодействии с кислотными центрами или из-за гидролитических свойств металлических центров. Для создания оптимальной каталитической системы необходимо сбалансировать кислотные и металлические свойства катализатора. Также расщепление связи С–С может осуществляться на металлических центрах в соответствии с двумя механизмами. По мультиплетному механизму гидрогенолиз во вторично-третичной или третично-третичной эндоциклической связи С–С, в замещенном положении, способствует образованию линейного соединения. По дикарбеновому механизму происходит расщепление С–С связей в незамещенном положении (вторично-вторичные атомы углерода) с образованием разветвленных продуктов [2, 5, 9, 12].
Катализаторы, в состав которых входят благородные металлы, проявляют хорошие каталитические свойства в реакции селективного раскрытия углеводородного кольца. Активность металлов в реакции гидрогенолиза снижается в следующем порядке: Ir > Rh > Ru > Pd > Pt [1, 2, 5, 9, 13]. Платина проявляет высокую активность в реакции гидрирования, что является ключевым фактором при получении ароматических соединений по реакции селективного раскрытия углеводородного кольца [14–16]. Ряд авторов пришли к выводу о том, что в реакции селективного раскрытия углеводородного кольца биметаллические Pt–Ir катализаторы демонстрируют лучшие показатели по выходу целевых продуктов, чем монометаллические катализаторы [9, 17, 18]. За счет введения металлов Pt и Ir в катализаторе создается наилучший баланс по активностям в реакциях гидрирования и гидрогенолиза [19].
В качестве носителей активных частиц для реакции селективного раскрытия углеводородного кольца используют цеолиты [2, 13, 17, 19], однако они имеют диффузионные ограничения из-за размера каналов и пор [20]. Для более легкого доступа крупных молекул к полостям катализатора используют мезопористые цеолиты, в которых лучше осуществляется массоперенос и диффузия веществ, вследствие чего исходные продукты легче взаимодействуют с наиболее активными центрами в катализаторе. Также образовавшиеся продукты не разрушаются и легко десорбируются с каталитической поверхности [21]. Один из возможных методов синтеза мезопористых цеолитов – это введение дополнительной пористости в микропористые кристаллы. Данный метод позволяет синтезировать иерархические цеолиты, которые имеют вторичную систему структурированных пор [22].
Цеолитные катализаторы, из-за сильной кислотности носителя в реакции селективного раскрытия углеводородного кольца, имеют низкую селективность по продуктам с открытой цепью (парафины) и высокий выход легких соединений, так как кислотные центры способствуют протеканию реакций изомеризации и крекинга [2, 11]. Бифункциональные катализаторы, которые сочетают в себе активность в реакции гидрогенолиза и умеренное количество кислотных центров в носителе, демонстрируют высокую селективность по парафинам без потери числа атомов углерода [11, 23, 24]. При введении в цеолит щелочного металла снижается количество кислотных центров в катализаторе [13, 25, 26]. Таким образом, существует возможность синтезировать катализаторы с умеренным количеством кислотных центров, в которых кислотность будет регулироваться посредством ионного обмена.
В работе предложен бифункциональный катализатор для реакции селективного раскрытия углеводородного кольца, который улучшает значение ЦЧ топлива. Для изучения влияния концентрации металлов и мольного отношения Pt/Ir были синтезированы монометаллические и биметаллические катализаторы с различными показателями по металлам. Как носитель использовали иерархический цеолит USY, для введения дополнительной пористости, синтезированный мезоструктурированием с использованием поверхностно-активного вещества в качестве матрицы. Также цеолит обрабатывали натрием, посредством ионного обмена, для изучения влияния кислотности носителя. В качестве модельной молекулы использовали этилбензол для изучения реакций гидрирования и селективного раскрытия углеводородного кольца.
ЭКСПЕРИМЕНТАЛЬНАЯ ЧАСТЬ
Синтез катализаторов. В качестве исходного материала использовали коммерческий цеолит USY, приобретенный у Zeolyst International, CVB-720 с мольным отношением Si/Al равным 15, далее по тексту FAU. Пост-синтетический процесс мезоструктурирования с использованием поверхностно-активного вещества осуществляли по методике [27]. Сначала приготовили раствор 0.188 г NaOH (>98%, Scharlau) в 12.5 мл дистиллированной воды. Затем в раствор добавили 1.0 г гексадецилтриметиламмония бромида (CTAB > 99%, Sigma) и 2.0 г цеолита, после чего перемешивали при помощи магнитной мешалки в течение 5 мин. Полученную реакционную смесь нагревали до 80°С в течение 12 часов. Далее раствор промывали дистиллированной водой при помощи фильтрации под давлением и сушили в течение ночи. В конечном итоге, образцы прокаливали при 550°C в течение 5 ч, сначала в атмосфере N2, а затем на воздухе, для удаления матриц поверхностно-активного вещества. Полученный текстурно-модифицированный цеолит далее по тексту обозначается как FAU–CTAB.
Катализаторы готовили пропиткой носителя растворами солей-прекурсоров металлов H2PtCl6 (99.995% Aldrich) и H2IrCl6 (99.99% Aldrich). Концентрации водных растворов солей подбирались так, чтобы концентрация металлов в образцах соответствовала: 1% Pt, 1% Ir, 1% Pt–0.5% Ir, 1% Pt–1% Ir, 2% Pt–0.5% Ir и 2% Pt–1% Ir. Затем образцы выдерживали при перемешивании в термостатирующей бане при 60°C и 200 мбар, давление в системе постепенно увеличивали до 10 мбар для удаления воды. По истечении двух часов полученное твердое вещество высушивали при 110°C в течение ночи. Далее катализаторы прокаливали в потоке воздуха при 300°C в течение 4 ч и охлаждали до комнатной температуры в атмосфере азота. Бифункциональные катализаторы обозначены как Pt(x)–Ir(y)/FAU–CTAB, где “x” – номинальное содержание Pt в мас. %, “y” – номинальное содержание Ir в мас. %.
Катализатор с модулированной кислотностью перед процедурой введения металлов подвергали ионному обмену с водным раствором NaNO3 (>99.5% Scharlau). На первом этапе 20 г цеолита перемешивали при помощи магнитной мешалки в 1 литре 1 М раствора NaNO3 в течение 5 мин, после чего нагревали до 80°C в течение 2 ч. Полученную смесь тщательно промывали дистиллированной водой при помощи вакуумной фильтрации и сушили в течение ночи. Далее образец прокаливали при 450°C в течение 2 ч в потоке воздуха. Полученный цеолит далее по тексту носит название Na–FAU–CTAB.
Характеристики катализаторов. Содержание металла и содержание натрия определяли с помощью индуктивно-связанной плазменно-оптической эмиссионной спектроскопии (ICP-OES, Optima 8300 PerkinElmer) после расщепления образцов в кислотном растворе. Дифракцию рентгеновских лучей (XRD) проводили на дифрактометре X’PertPRO от PANanytical, используя CuKα-излучение в диапазоне 0°–50°, работая при 40 кВ и 45 мА. XRD применяли для оценки кристалличности образцов, как описано в методе ASTM D-5357-03. Изотермы адсорбции/десорбции азота, при 77 К, измеряли на приборе Micromeritics ASAP 2010. Перед измерениями образцы дегазировали в вакууме при 300°C в течение 4 ч. Площадь поверхности по БЭТ (SБЭТ) была рассчитана путем применения модели БЭТ к данным по адсорбции азота. Объем пор и “внешнюю” площадь поверхности (Sвнш) определяли методом t-plot. Хемосорбция СО измерялась на приборе Micrometrics AutoChem 2910 и выражалась в нормальных миллилитрах СО на грамм катализатора. Перед анализом катализаторы восстанавливали в потоке H2 при 350°C, затем продували в токе He при 350°C, после чего охлаждали до 35°C. Последовательные импульсы CO посылались на образцы до тех пор, пока катализатор не становился насыщен, выход газа контролировался детектором TCD. Температурно-программированные профили восстановления катализаторов (ТПВ), получали на приборе AutoChem 2910 от Micromeritics. 60 мг каждого катализатора обрабатывали газом (10% Н2 в токе Ar) со скоростью 50 см3/мин, параллельно повышая температуру на 10°С/мин от комнатной до 500°С.
Количественные характеристики по кислотным центрам катализаторов определяли с помощью температурно-программированной десорбции аммиака (NH3-ТПД). Анализ проводили на приборе Micromeritics ТПВ/ТПД 2910. Приблизительно 60 мг катализатора нагревали до 450°С со скоростью 10°С/мин в токе Ar в течение 1 ч. Затем в потоке аргона образцы охлаждали до 100°С. При устоявшейся температуре 1.3% NH3 в Ar пропускали через образцы в течение 1 ч. После чего газ NH3/Ar переключали на Ar и охлаждали до 100°C. Анализ ТПД проводили в диапазоне температур от 100 до 600°C со скоростью нагрева 10°C/мин в токе Ar (50 мл/мин).
Испытание каталитической активности и анализ продуктов. Каталитические характеристики образцов в реакции селективного раскрытия углеводородного кольца этилбензола (99.8% Sigma-Aldrich) оценивали в реакторе проточного типа из нержавеющей стали со стационарным слоем катализатора при 275°C, давлении 3 МПа и LHSV 0.5 ч–1. В каждом эксперименте в реактор загружали 5 мл свежего катализатора. Предварительно порошок катализаторов прессовали, затем измельчали и просеивали до размера частиц 0.25–0.5 мм. Перед началом реакции катализаторы предварительно обрабатывали in situ при атмосферном давлении. На первом этапе осуществляли сушку образца в атмосфере N2 при 160°C в течение 6 ч, затем катализатор восстанавливали водородом при 325°C в течение 12 ч. После чего реактор охлаждали до температуры реакции. Далее повышали давление в системе до 3 МПа и шприцевым насосом подавали этилбензол в реакционную зону со скоростью 0.042 мл/мин совместно с потоком Н2, равным 14.72 л/ч (соотношение Н2/этилбензол = 30). После шести часов стабильной работы продукты реакции отправляли на анализ.
Газообразные продукты анализировали в GC Varian 450-GC, оборудованном капиллярной колонкой (Agilent Technologies GASPRO) и двумя детекторами, ТПД (детектор по теплопроводности) и ПИД (пламенно-ионизационный детектор). Анализ состава жидких продуктов проводили в автономном режиме на GC Agilent Technologies 7890A с капиллярной колонкой (колонка AC-Analytical Controls BP) и детектором ПИД; прибор подключали к преобразователю переменного тока M3 (ACI Series 3) и использовали стандартный режим анализа PIONA (парафины, изопарафины, олефины, нафтены и ароматические углеводороды). Для распознавания разветвленных парафинов в диапазоне С5–С8 жидкие образцы анализировали в масс-спектрометре Agilent Technologies 5975 VLMSD, соединенном с системой GC Agilent Technologies 7890A, с капиллярной колонкой (Agilent Technologies HP-1).
Степень превращения этилбензола (XЭБ), выход продуктов реакции (YПр), выход для различных типов парафинов в диапазоне C5–C8 (YП) рассчитывали по следующим формулам:
РЕЗУЛЬТАТЫ И ОБСУЖДЕНИЯ
Физико-химические характеристики катализаторов. Данные о характеристиках образцов катализаторов: SБЭТ, Sвнш, объем микропор и мезопор, кристалличность, представлены в табл. 1. Согласно авторам [21, 27], процесс мезоструктурирования цеолита FAU приводит к увеличению мезопористости и снижению кристалличности цеолита. В следствии чего, у иерархического цеолита FAU–CTAB приблизительно на 80% больше внешняя поверхность и объем мезопор по сравнению с исходным цеолитом FAU. Также кристалличность и объем микропор образцов катализаторов уменьшились вдвое. Текстурные свойства цеолита FAU–CTAB после введения металлов практически не изменялись, в то время как кристалличность немного уменьшилась.
Таблица 1.
Текстурные свойства, кристалличность, содержание металлов и объемная характеристика CO для носителей и бифункциональных катализаторов
Катализаторы | SБЭТ, м2/г |
Sвнш, м2/г |
Vмикропор, см3/г |
Vмезопор, см3/г |
Кристалличность, % |
Pt, мас. % |
Ir, мас. % |
Объем СО, Н мл/г кат. |
---|---|---|---|---|---|---|---|---|
FAU | 930 | 305 | 0.25 | 0.28 | 100 | – | – | – |
FAU−CTAB | 903 | 577 | 0.14 | 0.52 | 42 | – | – | – |
Pt(1)/FAU−CTAB | 899 | 566 | 0.15 | 0.51 | 38 | 1.10 | – | 0.53 |
Ir(1)/FAU−CTAB | 912 | 589 | 0.14 | 0.54 | 33 | – | 1.07 | 0.48 |
Pt(1)−Ir(0.5)/FAU−CTAB | 857 | 540 | 0.14 | 0.50 | 28 | 1.04 | 0.48 | 1.03 |
Pt(1)−Ir(1)/FAU−CTAB | 865 | 539 | 0.14 | 0.47 | 26 | 1.04 | 1.05 | 1.70 |
Pt(2)−Ir(0.5)/FAU−CTAB | 826 | 514 | 0.14 | 0.51 | 35 | 1.83 | 0.43 | 1.72 |
Pt(2)−Ir(1)/FAU−CTAB | 886 | 560 | 0.14 | 0.51 | 30 | 1.95 | 1.02 | 2.24 |
Na−FAU−CTAB | 826 | 562 | 0.12 | 0.52 | 37 | – | – | – |
Pt(2)−Ir(1)/Na−FAU−CTAB | 811 | 509 | 0.13 | 0.45 | 21 | 1.93 | 1.16 | 2.25 |
Концентрация натрия в исходном материале FAU–CTAB соответствовала 0.4 мас. %, после проведения ионного обмена концентрация натрия в цеолите увеличилась до 1.06 мас. % (Na–FAU–CTAB). Концентрации металлов Pt и Ir в образцах катализаторов очень близки к номинальным значениям. Информацию о дисперсности металла получали из значений объема адсорбированного СО в каталитической поверхности [28]. Из значений, представленных в табл. 1, видно, что объем адсорбированного СО увеличивается с общим содержанием металла независимо от природы металла. Следовательно, дисперсность частиц Pt и Ir одинаковая. Так как объем адсорбированного СО увеличивается пропорционально процентному содержанию металла, то концентрация введенного металлического компонента не влияет на дисперсность.
Профили температурно-программируемого восстановления (ТПВ) позволяют оценить степень взаимодействия металла с носителем в бифункциональных катализаторах, а также взаимодействие металла с металлом в биметаллических материалах [25, 29]. Как видно на рис. 1 (слева), монометаллический Ir проявляется в количестве четырех пиков восстановления с центрами при 120, 190, 270 и 325°C. Это может быть связано с неоднородным распределением различных видов металлов на носителе [18, 29]. Монометаллическая Pt проявляется в виде двух пиков при 310 и 460°C. Pt образует только два вида соединений с различными окислительно-восстановительными свойствами и показывает более высокую температуру восстановления, чем оксиды Ir, из-за чего Pt вступает в более интенсивное взаимодействие с цеолитом, по сравнению с Ir [17, 30]. В биметаллических катализаторах существует сильное взаимодействие между металлом и оксидом металла. Оксид металла может восстанавливаться при более низкой температуре а также катализировать восстановление другого металла, тем самым уменьшать его температуру восстановления [31]. Второй пик Pt при 460°C исчезает в биметаллических профилях, что указывает на сильное взаимодействие между Pt и Ir. Одиночный пик на ТПВ в биметаллическом катализаторе характеризует совместное восстановление двух монометаллических систем [17, 18, 30, 31]. На профилях ТПВ биметаллических катализаторов в диапазоне 250–400°С, кроме Pt(1)–Ir(1), присутствуют пики, которые соответствуют различным видам Pt и Ir. Pt(1)–Ir(1) катализатор имеет только один пик в этом диапазоне температур, что свидетельствует о сильном взаимодействии между двумя металлами. Из-за изолированных монометаллических частиц Ir в биметаллических катализаторах пик восстановления при 120°C, который относится к оксиду Ir, сохраняется во всех Pt–Ir ТПВ [29]. Второй пик монометалла Ir (190°C) уменьшается и сдвигается в биметаллических профилях, фактически он не наблюдается в Pt(2)–Ir(0.5) ТПВ, поскольку происходит взаимодействие между Pt и Ir.
Результаты ТПВ на рис. 1 (справа) показывают, как процесс ионного обмена цеолита с Na+ модифицирует пики восстановления для биметаллического катализатора Pt(2)–Ir(1). На профилях ТПВ для катализатора Pt(2)–Ir(1)/Na–FAU–CTAB наблюдаются три пика при более низкой температуре, чем у того же катализатора без Na+. Снижение кислотности цеолита, вызванное ионным обменом с Na+, привело к снижению взаимодействия металла с носителем, что способствует восстановлению частиц Pt–Ir при более низких температурах. Авторы [25] описывают аналогичную тенденцию для катализатора Pt–Ir/Al2O3 при ионном обмене катализатора с Na+.
В табл. 2 представлены данные об общей кислотности и количестве кислотных центров, определенные с помощью анализа ТПД аммиака. Текстурная модификация с обработкой CTAB на 40% снизила общую кислотность цеолита. По мнению авторов [21], текстурная модификация в основном способствует снижению количества сильных кислотных центров. Кислотность носителя после ионного обмена с Na+ снижается на 25% по отношению к FAU–CTAB. Как и предполагалось, после проведения процедуры ионного обмена с Na+, в катализаторе уменьшается общее количество кислотных центров [25, 26].
Таблица 2.
Результаты по определению кислотности носителей и бифункциональных катализаторов
Катализаторы | Распределение кислотных центров (ммоль NH3/г кат.) |
||
---|---|---|---|
общее количество кислотных центров (ммоль NH3/г кат.) | слабые кислотные центры (T < 300°C) | сильные кислотные центры (300 > T < 550°C) | |
FAU | 0.626 | 0.196 | 0.468 |
FAU−CTAB | 0.369 | 0.129 | 0.253 |
Pt(1)/FAU−CTAB | 0.355 | 0.121 | 0.244 |
Pt(2)−Ir(0.5)/FAU−CTAB | 0.296 | 0.168 | 0.134 |
Pt(1)−Ir(0.5)/FAU−CTAB | 0.288 | 0.098 | 0.196 |
Pt(2)−Ir(1)/FAU−CTAB | 0.261 | 0.200 | 0.064 |
Pt(1)−Ir(1)/FAU−CTAB | 0.234 | 0.195 | 0.042 |
Ir(1)/FAU−CTAB | 0.239 | 0.215 | 0.027 |
Na−FAU−CTAB | 0.278 | 0.175 | 0.113 |
Pt(2)−Ir(1)/Na−FAU−CTAB | 0.184 | 0.184 | 0 |
При введении Pt и/или Ir уменьшается общая кислотность и изменяется распределение силы кислотных центров в случае с обоими носителями, аналогичная тенденция наблюдается и в других исследованиях [20, 32, 33]. Некоторые авторы предполагают, что благородные металлы снижают кислотность носителя из-за прямого закрепления на протонных центрах и/или блокировки пор с активными кислотными центрами [11, 33]. Моно- и биметаллические катализаторы FAU–CTAB представлены в табл. 2 в соответствии с содержанием Ir. Общая кислотность и концентрация сильных кислотных центров уменьшается с увеличением Ir в катализаторе. В случае с Na–FAU–CTAB концентрация сильных кислотных центров снижается после введения металлов Pt–Ir. Это может быть связано с тем, что сила кислотных центров в Na–FAU–CTAB слабее, чем у других носителей.
Испытание каталитической активности. В процессе реакции селективного раскрытия углеводородного кольца этибензола на бифункциональных катализаторах получены соединения двух типов: нафтены и парафины. Изначально при гидрировании ароматического кольца образуется этилциклогексан (нафтены С8). Далее, в нафтенах разрывается связь С–С с образованием парафинов (парафины С8). Последовательное расщепление связей С–С приводит к образованию продуктов крекинга (нафтены или парафины <C8, включая парафины в газовой фазе). Схема реакции представлена на рис. 2. Степень превращения этилбензола на всех испытанных катализаторах была выше 99% (результаты не представлены). Таким образом, введение металлов, мольное отношение Pt/Ir, модификация носителя Na+ не повлияли на конверсию этилбензола. Все испытанные образцы катализаторов продемонстрировали стабильную работу в течениe 6 ч.
Значения выходов по продуктам реакции представлены на рис. 3. Основными продуктами, полученными на монометаллическом Pt катализаторе, были нафтены С8, а также небольшое количество парафинов С8. Pt продемонстрировала низкую активность по реакции крекинга. На Ir монометаллических катализаторах в основном образуются парафины и большое количество низкомолекулярных парафинов в газовой фазе. Данная тенденция обусловлена высокой гидрирующей активностью Pt и высокой активностью Ir по реакции гидрогенолиза, что согласуется с литерными данными [9, 16, 18, 32].
Селективность образования тех или иных продуктов не зависит от концентрации введенного металла в диапазоне от 1.5 до 3 мас. %. Селективность зависит от пропорции каждого металлического промотора и мольного отношения Pt/Ir (рис. 3). В случае с катализаторами, содержащими Ir в количестве 0.5 мас. %, преобладает гидрирующая функция, что приводит к образованию нафтенов С8 в качестве основных продуктов. При уменьшении мольного отношения Pt/Ir снижается селективность по нафтенам, при этом увеличивается селективность по парафинам и продуктам крекинга. Напротив, биметаллические катализаторы с 1 мас. % Ir демонстрируют более высокий выход парафинов и нафтенов. Парафины представляют собой углеводороды С8 и углеводороды с менее, чем восемью атомами углерода, включая газы. Таким образом, при уменьшении мольного отношения Pt/Ir в катализаторе увеличивается активность раскрытия кольца, но в то же время активно протекают реакции крекинга. Катализатор Pt(1)–Ir(1)/FAU–CTAB демонстрирует самую высокую селективность по углеводородам в газовой фазе.
Рис. 1.
Профили ТПВ носителя FAU–CTAB для моно- и биметаллических катализаторов (слева) и Pt (2)–Ir(1)-катализаторы с обработкой Na+ и без (справа).
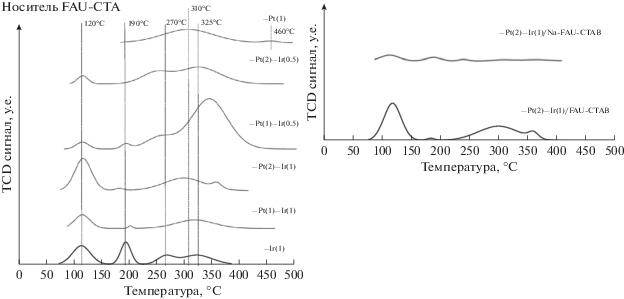
Рис. 2.
Упрощенная схема селективного раскрытия кольца этилбензола через бифункциональный механизм металл (М)/кислота (К), катализаторы и возможные продукты реакции.
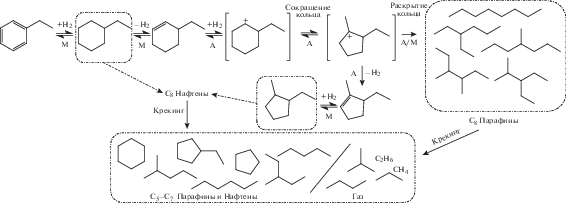
Рис. 3.
Выходы продуктов реакции на катализаторах с различным содержанием Pt–Ir. Условия реакции: 275°C, 3 МПа, LHSV = 0.5 ч–1, H2/этилбензол = 30, время реакционного цикла 6 ч.
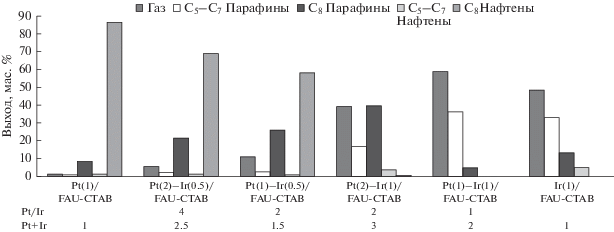
На рис. 4 представлены выходы парафинов (диапазон C5–C8), а именно нормальных парафинов (н-) и различных разветвленных изопарафинов (моно-, ди- и три-). На графике парафины подразделяются на две группы: “н- и моно-парафины”, которые улучшают ЦЧ, и “ди- и три-парафины”, которые оказывают негативное влияние на показатель ЦЧ. [10]. При увеличении концентрации Ir растет выход н- и моно-парафинов. На катализаторах с высокой концентрацией Pt наблюдается высокий выход по ди- и три-парафинам. Такое явление противоречит литературным данным. На катализаторах, содержащих Pt, реакция протекает по мультиплетному механизму расщепления C–C-кольца, что приводит к образованию менее разветвленных углеводородных продуктов. На катализаторах с промотором Ir реакция протекает по дикарбеновому механизму, в результате которой образуются разветвленные углеводороды [19, 34]. С другой стороны, реакции на Pt катализаторах могут протекать по мультиплетному или дикарбеновому механизму, в зависимости от дисперсности Pt [9, 28]. Реакции на Ir катализаторах протекают по дикарбеновому механизму независимо от дисперсности частиц металла. В данной работе на Ir катализаторах образовывались в основном моно-парафины и небольшое количество линейных углеводородов (результаты не представлены). Поэтому на катализаторах с загрузкой 1 мас. % Ir реакции протекали по дикарбеновому механизму с образованием моно-парафинов, результаты согласуются с литературными данными. Авторы [16] привели данные, по которым значение ЦЧ увеличивается при использовании монометаллического Ir катализатора. Образование разветвленных ди- и три-парафинов объясняется протеканием реакции изомеризации на кислотных центрах носителя [35]. На катализаторах с высокой концентрацией Pt реакции могут протекать по обоим механизмам. Также из-за повышенной кислотности носителя образуется большое количество разветвленных соединений.
Рис. 4.
Выход парафинов C5–C8 на катализаторах с различным содержанием Pt–Ir. Условия реакции: 275°C, 3 МПа, LHSV = 0.5 ч–1, H2/этилбензол = 30, время реакционного цикла 6 ч.
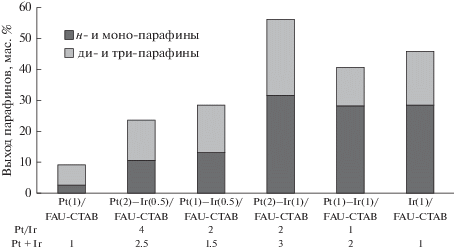
Целью проведения реакции селективного раскрытия углеводородного кольца было максимизировать выработку парафинов C8, в основном достигнуть высокие значения по выходу н- и моно-парафинов. Выход парафинов C8 на катализаторах Pt(1) и Pt(2)–Ir(0,5) был слишком низким из-за отсутствия активности по реакции гидрогенолиза, необходимой на стадии раскрытия кольца. Катализаторы Ir(1) и Pt(1)–Ir(1) проявили хорошую селективность по реакции гидрогенолиза, но с чрезмерным крекингом, который резко снижает выход парафинов C8. Катализаторы с мольным отношением Pt/Ir = 2 имеют лучшие равновесные показатели по отношению к введенным металлам, а также в реакциях на данных катализаторах наблюдается высокий выход по парафинам C8. На катализаторе Pt(1)–Ir(0.5) достигнут выход парафинов C8 равный 26%, но также в продуктах реакции присутствовали нафтены и разветвленные парафины. На катализаторе Pt(2)–Ir(1) достигнуты наилучшие показатели по реакции селективного раскрытия углеводородного кольца, выход по парафинам С8 составляет 40%. Кроме того, на данном катализаторе достигается высокий выход н- и моно-парафинов, до 31%. Также катализатор Pt(2)–Ir(1) отличается хорошими характеристиками по концентрации металлов и мольному балансу металл/металл.
Несмотря на хорошие каталитические свойства Pt(2)–Ir(1)/FAU–CTAB в продуктах реакции наблюдается значительное количество парафинов в газовой фазе, выход 56%. Это обусловлено наличием кислотных центров в носителе [2, 16]. Кислотность цеолита регулируется посредством щелочной обработки, которая модифицирует каталитические свойства [13, 25, 26]. Кислотность FAU–CTAB снижали ионообменном с Na+, после чего пропиткой вводили металлы Pt(2)–Ir(1). Каталитические характеристики катализаторов представлены на рис. 5. Профили ТПВ носителя FAU–CTAB для моно- и биметаллических катализаторов (слева) и Pt (2)–Ir(1) катализаторы с обработкой Na+ и без (справа).
Обработку цеолита Na+ проводили для снижения количества сильных кислотных центров, тем самым для снижения активности катализатора по реакции крекинга. Из результатов видно, что выход парафинов С8 увеличивается на 15 единиц, а количество нафтенов в продуктах практически не изменяется. Кроме того, эффект разветвления в парафинах снизился, подавляющее большинство парафинов, полученных на катализаторе Pt(2)–Ir(1)/Na–FAU–CTAB, представляет собой н- и моно-парафины. Полученные результаты подтверждают тот факт, что разветвленные ди- и три-парафины образуются в процессе изомеризации углеводородов на кислотных центрах носителя. Таким образом, на образце с мольным отношением Pt/Ir = 2 и концентрацией металлов 3.0 мас. % в сочетании с носителем Na–FAU–CTAB, достигается наилучший баланс между металл-кислотными функциями катализатора. На данном катализаторе выход по парафинам более 56%, и 77% составляет выход парафинов н- и моно- типа.
Таким образом, процесс получения низкоразветвленных парафинов из ароматических соединений реакцией селективного раскрытия углеводородного кольца требует тонкого баланса между соотношениями металл−металл и металл−кислота в биметаллических бифункциональных катализаторах. Процесс мезоструктурирования поверхностно-активного вещества на основе цеолита FAU увеличил на 80% внешнюю поверхность и объем мезопор, также снизил общую кислотность носителя на 40%. Таким образом, иерархический цеолит FAU–CTAB с умеренной кислотностью продемонстрировал подходящие свойства носителя для проведения реакции. Биметаллические катализаторы проявили себя лучшие, чем монометаллические, так как в их состав входит Ir, который проявляет высокую активность по реакции гидрогенолиза, и Pt, которая проявляет высокую активность в реакции гидрирования. Для достижения наилучших показателей по реакции селективного раскрытия углеводородного кольца необходимо ввести в структуру катализатора минимальное количество Ir (около 1 мас. %) и примерно в два раза большее количество Pt, для блокирования реакции крекинга. Таким образом, на катализаторе Pt(2)–Ir(1)/FAU–CTAB получен выход по парафинам 40 и 32% выход по н- и моно-парафинам, а также значительное количество продуктов реакции крекинга. Для варьирования кислотных свойств носителя в исследовании осуществили ионный обмен цеолита с Na+. В результате на катализаторе Pt(2)–Ir(1)/Na–FAU–CTAB был достигнут выход парафинов C8, равный 56%, при этом уменьшен выход легких парафинов в газовой фазе. Выход н- и моно-парафинов также увеличился до 77%, так как углеводороды не вступали в реакцию изомеризации на кислотных центрах. Подводя итог можно сказать, что биметаллический катализатор с концентрацией металлов 3 мас. %, мольным отношением Pt/Ir равным 2, полученный с использованием иерархического цеолита с низкой умеренной кислотностью, показал наилучший металл-кислотный баланс, низкий выход по разветвленным парафинам и продуктам реакции крекинга в реакции селективного раскрытия углеводородного кольца ароматических соединений.
Список литературы
Galadima A., Muraza O. // Fuel. 2016. V. 181. P. 618.
Martínez A., Arribas M.A., Pergher S.B.C. // Catal. Sci. Technol. 2016. V. 6. P. 2528.
Fechete I., Jacques C.V. // Comptes Rendus Chim. 2018. V. 21. P. 408.
Lee Y.J., Kim E.S., Kim J.R., Kim J.W., Kim T.W., Chae H.J., Kim C.U., Lee C.H., Jeong S.Y. // J. Nan-osci. Nanotechnol. 2016. V. 16. P. 4335.
Du H., Fairbridge C., Yang H., Ring Z. // Appl. Catal. A Gen. 2005. V. 294. P. 1.
Lee S., Lee Y., Kim J., Jeong S. // J. Ind. Eng. Chem. 2018. V. 66. P. 279.
Lee S.-U., Lee Y.-J., Kim J.-R., Jeong S.-Y. // Appl. Catal. B Environ. 2017. V. 219. P. 1.
Catherin N., Blanco E., Piccolo L., Laurenti D., Simonet F., Lorentz C., Leclerc E. // Catal. Today. 2019. V. 323. P. 105.
Dong X., Zheng P., Zheng A.G., Li H.F., Xia G.F., Li M.F., Zheng R.Y., Xu B.Q. // Catal. Today. 2018. V. 316. P. 162.
Santana R.C., Do P.T., Santikunaporn M., Alvarez W.E., Taylor J.D., Sughrue E.L., Resasco D.E. // Fuel. 2006. V. 85. P. 643.
Ziaei-Azad H., Sayari A. // J. Catal. 2016. V. 344. P. 729.
Vicerich M.A., Sánchez M.A., Benitez V.M., Pieck C.L. // Catal. Letters. 2017. V. 147. P. 758.
Nageswara Rao R., You N., Yoon S., Upare D.P., Park Y.K., Lee C.W. // Catal. Letters. 2011. V. 141. P. 1047.
Arribas M.A., Martínez A. // Appl. Catal. A Gen. 2002. V. 230. P. 203.
Arribas M.A., Concepción P., Martínez A. // Appl. Catal. A Gen. 2004. V. 267. P. 111.
Calemma V., Giardino R., Ferrari M. // Fuel Process. Technol. 2010. V. 91. P. 770.
D’Ippolito S.A., Gutierrez L.B., Vera C.R., Pieck C.L. // Appl. Catal. A Gen. 2013. V. 452. P. 48.
D’Ippolito S.A., Gutierrez L.B., Pieck C.L. // Appl. Catal. A Gen. 2012. V. 445–446. P. 195.
Calemma V., Ferrari M., Holl T., Weitkamp J. // Oil Gas Eur. Mag. 2014. V. 2. P. 77.
Kumar N., Mäki-Arvela P., Musakka N., Kubicka D., Kangas M., Tiitta M., Österholm H., Leino A.-R., Kordás K., Heikkilä T., Salmi T., Murzin D.Y. // Catal. Ind. 2013. V. 5. P. 105.
Lee S.-U., Lee Y.-J., Kim J.-R., Kim E.-S., Kim T.-W., Kim H.J., Kim C.-U., Jeong S.-Y. // Mater. Res. Bull. 2017. V. 96. P. 149.
Li K., Valla J., Garcia-Martinez J. // ChemCatChem. 2014. V. 6. P. 46.
Upare D.P., Lee C.W. // Fuel Process. Technol. 2014. V. 126. P. 243.
Santi D., Holl T., Calemma V., Weitkamp J. // Appl. Catal. A Gen. 2013. V. 455. P. 46.
Vicerich M.A., Oportus M., Benitez V.M., Reyes P., Pieck C.L. // Appl. Catal. A Gen. 2014. V. 480. P. 42.
Rabl S., Santi D., Haas A., Ferrari M., Calemma V., Bellussi G., Weitkamp J. // Micropor. Mesopor. Mater. 2011. V. 146. P. 190.
Garcia-Martinez J., Xiao C., Cychosz K.A., Li K., Wan W., Zou X., Thommes M. // ChemCatChem. 2014. V. 6. P. 3110.
Do P.T., Alvarez W.E., Resasco D.E. // J. Catal. 2006. V. 238. P. 477.
D’Ippolito S.A., Especel C., Epron F., Pieck C.L. // Fuel Process. Technol. 2015. V. 140. P. 180.
D’Ippolito S.A., Especel C., Vivier L., Pronier S., Epron F., Pieck C.L. // J. Mol. Catal. A Chem. 2015. V. 398. P. 203.
Hérault N., Olivet L., Pirault-Roy L., Especel C., Vicerich M.A., Pieck C.L., Epron F. // Appl. Catal. A Gen. 2016. V. 517. P. 81.
Benitez V.M., de Lima S.P., do Carmo Rangel M., Ruiz D., Reyes P., Pieck C.L. // Catal. Today. 2017. V. 289. P. 53.
Monteiro C.A.A., Costa D., Zotin J.L., Cardoso D. // Fuel. 2015. V. 160. P. 71.
McVicker G. // J. Catal. 2002. V. 210. P. 137.
Blanco E., Piccolo L., Laurenti D., di Felice L., Catherin N., Lorentz C., Geantet C., Calemma V. // Appl. Catal. A Gen. 2018. V. 550. P. 274.
Дополнительные материалы отсутствуют.