Нефтехимия, 2020, T. 60, № 2, стр. 206-213
Эпоксидирование этилена под воздействием продуктов реакции термического газофазного окисления н-бутана
Р. Р. Григорян 1, С. Д. Арсентьев 1, *
1 Институт химической физики им. А.Б. Налбандяна НАН Республики Армения
Ереван, 378433 Республика Армения
* E-mail: arsentiev53@mail.ru
Поступила в редакцию 31.07.2019
После доработки 29.09.2019
Принята к публикации 14.10.2019
Аннотация
В проточных условиях осуществлено эпоксидирование этилена активными продуктами, образующимися при термическом газофазном окислении н-бутана с разделением зон генерации радикалов и их взаимодействия с этиленом. Бутан окислялся в первой секции двухсекционного реактора, а этилен подавался во вторую секцию. Установлено, что увеличение времени пребывания бутан–кислородной смеси в 1-ой секции реактора от 7 до 13 с повышает скорость накопления оксида этилена. Дальнейшее увеличение времени контакта приводит к ее уменьшению. Аналогичным образом, увеличение соотношения С4Н10/О2 в интервале 0.05–0.25 приводит к увеличению скорости накопления оксида этилена. Дальнейшее увеличение этого соотношения уменьшает скорость эпоксидирования. Установлено также, что зависимости скорости накопления оксида этилена от температуры, как в первой, так и во второй секциях реактора проходят через максимум. Полученные данные свидетельствуют о протекании реакции эпоксидирования этилена, инициированной продуктами окисления н-бутана в условиях, когда этилен сам по себе практически не окисляется.
Оксиды олефинов являются базовыми нефтехимическими продуктами с быстрорастущим объемом потребления [1–3]. Это объясняется непрерывным ростом промышленного производства их производных [4, 5]. Например, этиленгликоль, являющийся основным производным оксида этилена, используется в качестве исходного реагента в производстве полиэтилентерефталата, растворителя, пластификатора, а также в производстве антифризов и мономеров для изготовления синтетических волокон [6]. Другое производное – диэтиленгликоль – является исходным сырьем в производстве полиэфирных смол и пенопластов, а динитроэтиленгликоль применяется как заменитель нитроглицерина для получения низкозамерзающего и ударостойкого динамита. Получаемые на основе оксида этилена неионогенные поверхностно-активные вещества (ПАВ) весьма эффективно используются в нефтедобывающей и нефтеперерабатывающей промышленности [7–9]. Полимеризацией оксида этилена получают жидкие и воскообразные полимеры, используемые в качестве пластификаторов, смазок. Непосредственно оксид этилена, а также композиции на его основе, могут использоваться как топливо [10], в качестве бактерицидного и стерилизующего агента [11].
Для получения оксида этилена в промышленных масштабах возможно использование, в основном, трех методов: каталитическое окисление этилена; некаталитическое окисление этилена; получение из этиленхлоргидрина [12]. До настоящего времени промышленное применение нашли только два способа – окисление этилена на серебряных катализаторах и действие щелочей на этиленхлоргидрин [13]. Из них наиболее экономичным является хлоргидринный метод. Однако, получение оксида этилена этим способом требует использования хлора, хлоростойких материалов для реакторов и сопровождается образованием значительного количества хлорсодержащих отходов, загрязняющих окружающую среду.
Значительно более чистым, с экологической точки зрения, является каталитическое окисление этилена [14–17]. В настоящее время в промышленных масштабах практически весь оксид этилена получают именно каталитически. Наиболее эффективными катализаторами окисления этилена в его оксид являются серебро и его соединения [1, 5, 18–20], которые позволяют получать целевой продукт с селективностью, превышающей 70% [13, 19, 21]. В то же время, использование серебра в каталитических процессах связано с рядом сложных проблем. Технологии изготовления катализатора сложны и многостадийны. В процессе эксплуатации катализаторы вследствие старения и отравления ядами, теряют активность [22] и подлежат периодической регенерации. Осложняющие факторы – особые требования к чистоте исходного углеводородного сырья. Наибольшую опасность для серебряных катализаторов представляют соединения серы, являющиеся естественным спутником природного углеводородного сырья, мышьяк и ацетилен. Нежелательно присутствие других углеводородов, а также водорода и оксидов углерода.
Указанных выше недостатков лишены некаталитические способы получения оксида этилена. В отличие от каталитических процессов, при гомогенном окислении этилена кислородом образуется ряд ценных продуктов: оксид этилена, формальдегид, органические кислоты. В настоящее время разрабатываются методы синтеза оксида этилена гомогенным окислением этилена в газовой фазе [23, 24], так как для этого процесса не требуется ни дорогого катализатора, ни хлора. Кроме того, при этом способе получения оксида этилена не требуются газы такой высокой степени очистки, как при каталитическом процессе. Недостаток метода – многообразие образующихся продуктов и низкая селективность, что объясняется цепной природой происходящих превращений и высокой температурой. Однако развитие теории цепных процессов открывает новые пути совершенствования реакций газофазного окисления этилена.
В предыдущих работах [25–29] было показано, что эпоксидирование этилена и пропилена в процессах их термического газофазного окисления происходит при взаимодействии пероксидных радикалов с двойной связью олефина по реакции:
Ранее эпоксидирование этилена изучалось также при сопряженном окислении этилена и бутана. Было показано, что в этом случае эпоксидирование этилена протекает при низких температурах, при которых этилен сам по себе не окисляется [33]. В то же время, введение этилена в реагирующую смесь с самого начала процесса, приводит к его нерациональному расходованию на нецелевые продукты. Поэтому было решено отделить зону генерации активных частиц, образующихся при окислении парафинового углеводорода, от зоны эпоксидирования. Выбор углеводорода, генерирующего пероксидные радикалы, обусловлен тем, что при окислении бутана в двухсекционном реакторе во второй секции накапливаются алкилпероксидные радикалы в концентрациях, превышающих 10–9 моль/см3 [33, 34].
Цель данной работы – изучение процесса эпоксидирования этилена активными соединениями, генерируемыми в реакции термического газофазногоокисления бутана при сопряженном окислении этилена и н-бутана с разделением зон генерации радикалов и их взаимодействия с этиленом.
ЭКСПЕРИМЕНТАЛЬНАЯ ЧАСТЬ
Схема реакционного узла для проведения процессов сопряженного эпоксидирования этилена приведенана рис. 1. Использовался двухсекционный реактор, представляющий собой кварцевую трубку длиной 20 см и диаметром 2 см. Разделение реактора на секции производилось с помощью перегородки, состоящей из пакета кварцевых трубок. Реактор обогревался двумя независимыми электрическими печами, что позволяло устанавливать разные температуры в секциях реактора. Смесь н-бутана с кислородом подавали через уплотнительный штуцер в первую секцию реактора, где происходило окисление бутана с образованием активной среды. Этилен подавали во вторую секцию реактора через капилляр.
Рис. 1.
Схема реактора: 1 – штуцер для подачи бутан-кислородной смеси; 2 – первая секция реактора; 3 – капилляр для подачи этилена; 4 – пакет кварцевых трубок; 5 – печь первой секции реактора; 6 – печь второй секции реактора; 7 – штуцер для отбора пробы на анализ.
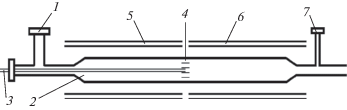
Разделение и определение концентраций газообразных продуктов осуществляли хроматографически на хроматографе ЛХМ-8МД. На колонке, заполненной полимерным орбентом полисорб-1 (l = 3 м, d = 3 мм, Ткол = 378 К, Q = 30 см3/мин, газ-носитель гелий) разделяли метанол, этанол, ацетальдегид, оксид этилена. Углеводороды С1–С4 разделяли на колонке, заполненной силипором-600 (l = 3 м, d = 3 мм, Ткол = 363 К, Q = 24 см3/мин, газ-носитель елий). Водород, кислород, метан и СО разделяли на колонке, заполненной молекулярными ситами 5 Å (l = 2 м, d = 3 мм, Ткол = 363 К, Q = 24 см3/мин, газ-носитель аргон). Во всех случаях детектором служил катарометр.
Измерение концентрации формальдегида проводили с использованием хромотроповой кислоты на фотоэлектроколориметре КФК-2. Для анализа формальдегида отходящие реакционные газы в течение определенного времени барботировали через дистиллированную воду. Для увеличения поверхности контакта газов с растворителем барботер заполняли мелким стеклянным боем. Концентрацию формальдегида в реакторе рассчитывали по формуле C = CбVTк/QtбTр, где C – концентрация в реакторе (моль/см3), Cб – концентрация в растворе из барботера (моль/см3), V – объем воды в барботере (см3), Q – объемная скорость подачи реагентов в реактор (см3/с), tб – длительность барботирования (с), Tк и Tр – температура в комнате и в реакторе соответственно.
При необходимости концентрацию формальдегида пересчитывали в парциальное давление по формуле P = PаCNATр/TнNL, где P – парциальное давление (кПа), Tн – нормальная температура (298 K), Pа – нормальное давление (101.308 кПа), NA – число Авoгадро, NL – число Лошмидта.
РЕЗУЛЬТАТЫ И ИХ ОБСУЖДЕНИЕ
Эксперименты показали, что основными продуктами процесса являются оксид углерода, оксид этилена, ацетальдегид, метанол, формальдегид. В незначительных количествах обнаруживаются также этанол, метан, диоксид углерода.
В табл. 1 приводятся концентрации основных продуктов реакции, измеренные при различных скоростях подачи бутан-кислородной смеси в первую секцию реактора.
Таблица 1.
Концентрации основных продуктов реакции, полученные для различных времен контакта в 1 и 2 секциях реактора. T1 = 673 K, T2 = 613 K, н-C4H10 : O2 = 0.117, Р = 86.7 кПа
№ | Q1, см3/с | Q2, см3/с | Парциальное давление продуктов реакции, кПа | ||||
---|---|---|---|---|---|---|---|
СН3ОН | СН3СНО | С2Н4О | НСНО | СО | |||
1 | 0.51 | 0.92 | 0.459 | 0.526 | 1.396 | 0.502 | 2.14 |
2 | 0.63 | 1.14 | 0.441 | 0.542 | 1.449 | 0.509 | 2.13 |
3 | 0.76 | 1.37 | 0.433 | 0.561 | 1.437 | 0.521 | 2.12 |
4 | 0.83 | 1.49 | 0.412 | 0.583 | 1.354 | 0.532 | 2.03 |
5 | 1.03 | 1.85 | 0.354 | 0.592 | 1.318 | 0.532 | 1.95 |
6 | 1.28 | 2.30 | 0.305 | 0.588 | 1.211 | 0.518 | 1.63 |
7 | 1.34 | 2.41 | 0.281 | 0.467 | 1.234 | 0.474 | 1.23 |
8 | 1.45 | 2.61 | 0.134 | 0.372 | 1.103 | 0.368 | 0.91 |
9 | 1.52 | 2.73 | 0.106 | 0.296 | 0.982 | 0.271 | 0.45 |
10 | 1.59 | 2.86 | 0.096 | 0.254 | 0.723 | 0.218 | 0.23 |
11 | 1.92 | 3.45 | 0.083 | 0.186 | 0.292 | 0.153 | 0.09 |
Поскольку наблюдаемая на выходе из реактора концентрация оксида этилена определяется разницей между ее образованием и расходом, а также зависит от градиентов концентрации эпоксидирующих активных частиц, то мы можем с уверенностью говорить только об экспериментально измеряемой средней скорости накопления оксида этилена во второй секции реактора. Расчет этой величины, проводился на основании данных табл. 1 по формуле:
Рис. 2.
Зависимость средней скорости накопления оксида этилена от времени контакта в 1 секции реактора. T1 = 673 K, T2 = 613 K, C4H10 : O2 = 0.117, Р = = 86.7 кПа. Пунктиром представлены результаты, полученные при замене бутана на аргон.
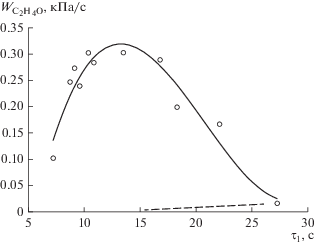
Как видно из рис. 2, средняя скорость накопления оксида этилена максимальна при времени пребывания бутан-кислородной смеси в первой секции реактора ~13 с. При уменьшении или увеличении времени контакта происходит резкое уменьшение скорости накопления оксида этилена. Очевидно, это связано с тем, что окисление бутана является вырожденно-разветвленным цепным процессом, вследствие чего скорость процесса и концентрации активных частиц зависят от времени контакта. Поскольку скорость накопления оксида этилена связана с концентрацией активных частиц, поступающих из первой секции, а концентрация этилена во всех опытах (см. табл. 1) поддерживалась одной и той же, то экстремальная зависимость скорости процесса и концентрации активных частиц, поступающих из первой секции реактора, от времени контакта приводит к появлению максимума на зависимости ${{W}_{{{{{\text{C}}}_{{\text{2}}}}{{{\text{H}}}_{{\text{4}}}}{\text{O}}}}}$ от времени пребывания бутан-кислородной смеси (/1) в 1 секции.
Для сравнения, на этом же рисунке, пунктирной линией приводится аналогичная зависимость, полученная при тех же условиях проведения процесса, но с заменой бутана на аргон в смеси, подаваемой в 1 секцию реактора. Эксперименты показали, что при этом происходит значительное уменьшение скорости накопления оксида этилена. Например, для τ1 ~ 12–14 с ${{W}_{{{{{\text{C}}}_{{\text{2}}}}{{{\text{H}}}_{{\text{4}}}}{\text{O}}}}}$ уменьшается более чем в 30 раз. Этот результат говорит о том, что этилен в этих условиях окисляется очень медленно, а присутствие бутана резко повышает генерацию эпоксидирующих его частиц.
При скорости подачи бутан-кислородной смеси в 1 секцию реактора Q1 = 1.92 см3/c (табл. 1, п. 11) селективность превращения этилена в оксид этиленасоставила ~96%. Расчет селективности проводился по формуле:
Согласно [27] максимальная селективность образования оксида этилена при окислении этилена в обычных условиях не может превышать 67%. Такой предел селективности связан с тем, что часть этилена расходуется на образование пероксидных радикалов. В условиях наших экспериментов в двухсекционном реакторе генерация активных частиц происходит в процессе окисления бутана в первой секции, а этилен во второй секции расходуется, в основном, в реакции эпоксидирования. В результате селективность превращения этилена в его оксид возрастает.
Очевидно, что скорость окисления углеводородов и концентрации радикалов в ходе процесса зависят от состава реагирующей смеси. В связи с этим проводилось исследование влияния состава смеси в первой секции реактора на процесс эпоксидирования. В табл. 2 приводятся концентрации основных продуктов реакции, полученные при изменении соотношения бутан/кислород в смеси, подаваемой в первую секцию реактора.
Таблица 2.
Концентрации основных продуктов реакции, полученные для различных составов бутан-кислородной смеси, подаваемой в первую секцию реактора. T1 = 673 K, T2 = 613 K, Q1 = 1.30 см3/с, Q2 = 2.30 см3/с, Р = 86.7 кПа
№ | C4H10 : O2 | Парциальное давление продуктов реакции, кПа | ||||
---|---|---|---|---|---|---|
CH3OH | CH3CHO | C2H4O | HCHO | CO | ||
1 | 0.05 | 0.475 | 0.227 | 1.055 | 0.231 | 2.10 |
2 | 0.07 | 0.509 | 0.365 | 1.907 | 0.284 | 1.95 |
3 | 0.13 | 0.563 | 0.485 | 1.722 | 0.424 | 1.82 |
4 | 0.21 | 0.562 | 0.531 | 1.818 | 0.448 | 1.79 |
5 | 0.25 | 0.527 | 0.493 | 1.901 | 0.465 | 1.78 |
6 | 0.35 | 0.512 | 0.434 | 1.556 | 0.432 | 1.81 |
7 | 0.50 | 0.504 | 0.421 | 1.436 | 0.396 | 1.81 |
8 | 0.79 | 0.499 | 0.393 | 0.870 | 0.372 | 1.79 |
9 | 0.85 | 0.483 | 0.348 | 0.888 | 0.353 | 1.77 |
Зависимость средней скорости накопления оксида этилена от соотношения бутан/кислород в смеси, подаваемой в первую секцию реактора, построенная с использованием данных табл. 2 приведена на рис. 3.
Рис. 3.
Зависимость средней скорости накопления оксида этилена от соотношения бутан/кислород в первой секции реактора. T1 = 673 K, T2 = 683 K, Q1 = = 1.30 см3/с, Q2 = 2.30 см3/с, Р = 86.7 кПа.
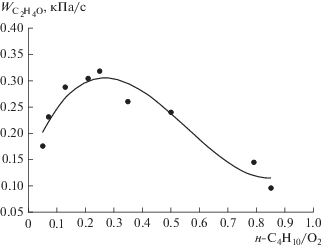
Как видно из рис. 3, увеличение соотношения н-С4Н10/О2 в интервале от 0.05 до 0.25 приводит к увеличению средней скорости накопления оксида этилена в 1.8 раза. Дальнейшее увеличение этого соотношения приводит к уменьшению ${{W}_{{{{{\text{C}}}_{{\text{2}}}}{{{\text{H}}}_{{\text{4}}}}{\text{O}}}}}$ более, чем в два раза.
Известно, что интенсивность окисления углеводородов зависит от соотношения углеводород/кислород и проходит через максимум [35, 36]. Очевидно, что зависимость концентрации активных промежуточных продуктов, способствующих эпоксидированию этилена, от соотношения н-С4Н10/О2 также проходит через максимум, что и объясняет наличие максимума на рис. 3.
Поскольку скорость химического процесса, и, следовательно, концентрации активных промежуточных продуктов (в том числе и радикалов) зависят от температуры, то очевидно, что температура в первой секции реактора должна влиять на скорость образования оксида этилена во второй секции. Данные, полученные при различных температурах в первой секции реактора, приведены в табл. 3.
Таблица 3.
Влияние температуры в первой секции реактора (T1) на выход продуктов реакции.С4H10 : O2 = 0.21, T2 = 683 K, Q1 = 1.30 см3/с, Q2 = 2.30 см3/с, P = 86.7 кПа
№ | T1, K | Парциальное давление продуктов реакции, кПа | ||||
---|---|---|---|---|---|---|
CH3OH | CH3CHO | C2H4O | HCHO | CO | ||
1 | 610 | 0.581 | 0.549 | 1.186 | 0.418 | 1.72 |
2 | 623 | 0.563 | 0.544 | 1.654 | 0.443 | 1.75 |
3 | 638 | 0.558 | 0.536 | 1.783 | 0.451 | 1.78 |
4 | 657 | 0.552 | 0.533 | 1.773 | 0.450 | 1.78 |
5 | 673 | 0.562 | 0.531 | 1.868 | 0.448 | 1.83 |
6 | 683 | 0.536 | 0.512 | 1.705 | 0.453 | 1.91 |
7 | 700 | 0.492 | 0.486 | 1.668 | 0.472 | 2.16 |
8 | 723 | 0.465 | 0.434 | 1.329 | 0.479 | 2.31 |
На рис. 4 приводится зависимость средней скорости накопления оксида этилена от температуры в первой секции реактора. Скорость накопления рассчитывалась на основании данных табл. 3.
Рис. 4.
Зависимость средней скорости накопления оксида этилена от температуры в первой секции реактора. C4H10 : O2 = 0.21, T2 = 683 K, Q1 = 1.30 см3/с, Q2 = 2.30 см3/с, P = 86.7 кПа.
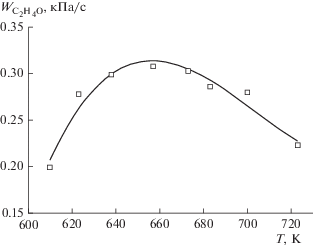
Как видно из рис. 4, средняя скорость накопления оксида этилена максимальна при температуре в первой секции T1 = 650–660 K. При уменьшении или увеличении температуры происходит уменьшение скорости накопления оксида этилена. Очевидно, это связано с тем, что окисление бутана является вырожденно-разветвленным процессом, вследствие чего время достижения максимальной концентрации активных промежуточных продуктов, включая пероксидные радикалы, в первой секции реактора меняется с изменением температуры. При низких температурах (T1 < 640 K) концентрация активных частиц за установленное время контакта не успевает достичь максимума и поэтому скорость накопления оксида этилена во второй секции меньше максимальной. При температурах T1 > 670 K процесс окисления при заданном времени контакта начинает тормозиться из-за расхода реагентов, вследствие чего концентрация активных частиц, выходящих во вторую секцию, уменьшается. В результате, скорость накопления оксида этилена также начинает уменьшаться, что приводит к появлению максимума на зависимости ${{W}_{{{{{\text{C}}}_{{\text{2}}}}{{{\text{H}}}_{{\text{4}}}}{\text{O}}}}}$ от температуры в первой секции.
Ранее в [26] была измерена константа скорости эпоксидирования этилена алкилпероксидными радикалами •RO2. Было установлено, что энергия активации этой реакции составляет E = = 57.7 кДж/моль. Очевидно, что при такой энергии активации, повышение температуры должно увеличивать скорость эпоксидирования. В связи с этим проводились эксперименты при различных температурах во второй секции реактора, т.е. в зоне эпоксидирования. Концентрации основных продуктов реакции, экспериментально измеренные при изменении температуры во второй секции реактора, приводятся в табл. 4.
Таблица 4.
Влияние температуры во второй секции реактора (T2) на выход продуктов реакции. C4H10 : O2 = 0.21, T1 = 673 K, Q1 = 1.30 cм3/c, Q2 = 2.30 см3/c, P = 86.7 кПа
№ | T2, K | Парциальное давление продуктов реакции, кПа | ||||
---|---|---|---|---|---|---|
CH3OH | CH3CHO | C2H4O | HCHO | CO | ||
1 | 603 | 0.5.29 | 0.537 | 0.770 | 0.412 | 1.65 |
2 | 630 | 0.532 | 0.536 | 1.370 | 0.441 | 1.72 |
3 | 663 | 0.543 | 0.532 | 1.602 | 0.449 | 1.77 |
4 | 683 | 0.562 | 0.531 | 1.818 | 0.448 | 1.79 |
5 | 694 | 0.558 | 0.512 | 1.887 | 0.470 | 1.83 |
6 | 710 | 0.553 | 0.485 | 1.702 | 0.465 | 1.92 |
7 | 728 | 0.541 | 0.473 | 1.720 | 0.467 | 2.14 |
На рис. 5 приводится зависимость средней скорости накопления оксида этилена от температуры во второй секции реактора, построенная на основе данных табл. 4.
Рис. 5.
Зависимость средней скорости накопления оксида этилена от температуры во второй секции реактора. C4H10 : O2 = 0.21, T1 = 673 K, Q1 = 1.30 см3/с, Q2 = 2.30 см3/с, P = 86.7 кПа.
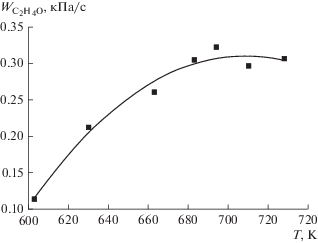
Как видно из рис. 5, повышение температуры в интервале 600–695 K приводит к увеличению скорости накопления оксида этилена в 2.8 раза. Поскольку условия окисления бутана в первой секции не меняются, т.е. концентрация активных компонентов, поступающих во вторую секцию реактора, остается постоянной, то рост ${{W}_{{{{{\text{C}}}_{{\text{2}}}}{{{\text{H}}}_{{\text{4}}}}{\text{O}}}}},$ очевидно, связан с увеличением константы скорости эпоксидирования при росте температуры. При дальнейшем увеличении температуры скорость накопления оксида этилена меняется мало. По-видимому, увеличение константы скорости эпоксидирования компенсируется ускоряющимся расходом оксида этилена при высоких (>700 K) температурах. Об этом свидетельствует также уменьшение концентраций других кислородсодержащих продуктов реакции (табл. 4) и увеличение концентрации продукта глубокого окисления – монооксида углерода. При температуре во второй секции T2 = 683 K селективность превращения этилена в оксид этилена составляет S ~ 87% при конверсии этилена ~6%.
ЗАКЛЮЧЕНИЕ
Характер зависимости скорости накопления оксида этилена от соотношения бутан/кислород в первой секции реактора и от температуры в обеих секциях свидетельствует об инициировании процесса эпоксидирования этилена продуктами окисления н-бутана в условиях, когда сам этилен окисляется очень медленно.
Список литературы
The Global Ethylene Oxide Market. 2019. Williams & Marshall Strategy. 200 p. (https://www.researchandmarkets.com/reports/4665297/the-global-ethylene-oxide-market#rela3-3150666).
Propylene oxide. Chemical Economics Handbook. IHS Markit. 2019. P. 6 (https://ihsmarkit.com/products/propylene-oxide-chemical-economics-handbook.html).
Rebsdat S., Mayer D. “Ethylene oxide” in Ullman’s Encyclopedia of industrial Chemistry, 2012. V. 13. P. 548. Wiley-VCH Verlag GmbH & Co. KGaA, Weinheim
Mono-Ethylene Glycol (MEG): Production, Market, Price and Its Properties. Plastics insight. 2016. (https://www.plasticsinsight.com/resin-intelligence/ resin-prices/mono-ethylene-glycol-meg/).
Ethylene Glycols. HS Markit. Chemical Economics Handbook. 2018. (https://ihsmarkit.com/products/ethylene-glycols-chemical-economics-handbook.html).
Hairong Yue, Yujun Zhao, Xinbin Ma, Jinlong Gong // Chem. Soc. Rev. 2012. V. 41. № 11. P. 4218.
Поверхностно-активные вещества в нефтегазовой отрасли. Состав, свойства, применение. Под ред. Шрамм Л.Л. С.-Петербург: ЦОП “Профессия”, 2018. 592 с.
Саутина Н.В. Дис. … канд. хим. наук. ВАК РФ 02.00.11. 2009. Казань. Казанский гос. технологический ун-тет. 178 с.
Фахрутдинов Б.Р. Дис. … канд. хим. наук. ВАК РФ 02.00.13. 2001. Казань. Казанский гос. технологический ун-тет. 176 с.
Glassman I., Yetter R.A. Combustion. 4-th ed. Elsevier Inc. 2008. 800 p.
Shintani H. // Biocontrol Sci. 2017. V. 22. № 1. P. 1.
Смит В., Бочков А., Кейпл Р. Органический синтез. М.: Мир. 2001. 345 с.
Слинько М.Г. // Вестник РАН. 2001. Т. 71. № 7. С. 635.
Пак С., Рокицки А., Кавабата С. // Патент РФ № 2495715. Б.И. 2013. № 29.
Рекерс Д.М., Смардейк А.А. // Патент РФ № 2462461. Б.И. 2012. № 27.
Rizkalla N., Klein R., Milne S.B. // Patent US № 5945551. 1999.
ВанКрюхтен Э.М.Г.А., Рекерс Д.М., Слапак М.Й.П. // Патент РФ № 2466123. Б.И. № 31. 2012.
Yusuff A.S., Adeyi A.A., Jeffrey O.O. // Int. J. of Scientific and Engineering Research. 2015. V. 6. Issue 6. P. 1626.
Локмейер Дж.Р., Рейналда Д., Йетс Р.К. // Патент РФ. № 2314156 C2. Б.И. № 1. 2008.
Othmer K. Encyclopedia of Chemical Technology. V. 9. 4-th ed. New-York: JohnWiley&Sons, 1994. P. 1112.
Рубанк М.Я., Гороховатский Я.Б. Неполное каталитическое окисление олефинов. Киев: Техника, 1964. 196 с.
Montrasi G.L., Tauszik G.R., Solari M., Leofanti G. // Applied Catalysis 1983. V. 5. Issue 3. P. 359.
Сафин Д.Х., Ашихмин Г.П., Мустафин Х.В., Чебарева А.И. // Химическая промышленность сегодня. 2003. № 4. С. 25.
Сафин Д.Х., Петухов А.А. // Химическая промышленность сегодня. 2005. № 8. С. 45.
Arsentev S.D., Mantashyan A.A. // Catal. Letters. 1980. V. 13. № 2. P. 125.
Mantashyan A.A., Arsentev S.D., Khachatryan L.A. Niazyan O.M. // Combustion and Flame. 1981. V. 43. P. 221.
Манташян А.А., Арсентьев С.Д. // Кинетика и катализ. 1981. Т. 22. № 6. С. 1389.
Mantashyan A.A., Arsentev S.D., Grigoryan R.R. // React. Kinet. Catal. Letters. 1982. V. 21. № 3. P. 347.
Манташян А.А., Арсентьев С.Д., Григорян Р.Р. // Кинетика и катализ. 1986. Т. 27. № 4. С. 782.
Арсентьев С.Д. Дис. … докт. хим. наук. ВАК РА 02.00.15. 1996. Ереван. Институт химической физики. 313 с.
Grigoryan R.R., Arsentev S.D., Mantashyan A. A. // Petrol. Chemistry. 2011. V. 51. № 6. P. 448.
Арсентьев С.Д., Манташян А.А. // Арм. хим. журнал. 1980. Т. 33. № 9. С. 778.
Симонян Т.Р., Манташян А.А. // Арм. хим. журн. 1979. Т. 32. № 9. С. 691.
Симонян Т.Р., Манташян А.А. // Арм. хим. журн. 1979. Т. 32. № 10. С. 757.
Технологическое горение. Коллективная монография. Под ред. Алдошина С.М. и Алымова М.И. РАН: Москва, 2018. Гл. 5. С. 114.
Arutyunov V., Pogosyan N., Pogosyan M., Tavadyan L., Shapovalova O., Strekova L. // Chemical Engineering J. 2017. V. 329. P. 231.
Дополнительные материалы отсутствуют.