Нефтехимия, 2020, T. 60, № 3, стр. 270-282
Использование СКФ-технологий в химической и нефтехимической отраслях (обзор)
И. А. Макарян 1, *, А. Ю. Костин 1, И. В. Седов 1
1 Институт проблем химической физики РАН
142432 Московская обл., Черноголовка, Россия
* E-mail: irenmak@icp.ac.ru
Поступила в редакцию 01.11.2019
После доработки 06.11.2019
Принята к публикации 18.11.2019
Аннотация
Обзор посвящен исследованию возможностей применения сверхкритических флюидов в качестве реакционной среды в химической и нефтехимической промышленности, что позволит решить актуальную задачу по замене традиционных токсичных, взрыво- и пожароопасных органических растворителей на экологически безопасные “зеленые” растворители. Проведен сравнительный анализ научных и технологических достижений по использованию сверхкритических флюидных технологий (СКФ-технологий) в широко применяемых нефтехимических процессах, таких как окисление, гидрирование, гидроформилирование, полимеризация, метатезис и др. СКФ-технологии имеют коммерческую направленность, обладают рядом потенциальных конкурентных преимуществ и уже внедрены или планируются к промышленной реализации в ближайшем будущем.
В наши дни воздействие любого химического или нефтехимического производства на окружающую среду приобретает особо важное значение [1]. В мире такое воздействие принято условно оценивать по так называемому экологическому фактору технологии (E-factor), который рассчитывается по количеству образующихся отходов, приходящихся на единицу массы получаемого целевого продукта. Как следует из этого определения, величина E-factor обратно пропорциональна его экологической привлекательности и исключает возможность потери растворителя в ходе проведения процесса. Кроме того, хорошо известно, что многие органические растворители, применяемые в промышленных масштабах, не только вредны, токсичны, взрыво- и пожароопасны, но и их регенерация и повторное использование часто бывают затруднительны и экономически невыгодны.
В свете решения этих проблем большой интерес со стороны фундаментальной и прикладной науки проявляется к сверхкритическим флюидам (СКФ), в частности к наиболее популярному среди них сверхкритическому диоксиду углерода (СК-СО2), в среде которых появляется возможность осуществлять экологически безопасные для окружающей среды так называемые “зеленые” технологии. С момента открытия СКФ в 1822 г. [2] прошло около 150 лет, прежде чем в 1970 г. оригинальная СКФ-технология была впервые применена для экстракции кофеина из кофейных зерен с использованием СК-СО2 в качестве растворителя [3].
Таблица 1.
Физические свойства газов, СКФ и жидкостей [4]
Физическое свойство | Газы | СКФ | Жидкости |
---|---|---|---|
Плотность, кг/м3 | 0.6 –2.0 | 200–500 | 600–1600 |
Динамическая вязкость, 103 кг/м с | 0.01–0.3 | 0.01–0.03 | 0.2–3.0 |
Кинематическая вязкость, 106 м2/с | 5–500 | 0.02–0.1 | 0.1–5.0 |
Коэффициент диффузии, 106 м2/с | 10–40 | 0.07 | 0.0002–0.002 |
Основное значение для “зеленых” СКФ-технологий имеют такие характеристики используемых растворителей, как плотность, вязкость и диффузионная способность. Сравнение физических характеристик обычных газов, жидкостей и СКФ приводятся в табл. 1 [4].
За последние годы технологии на базе СКФ успешно реализовались во многих отраслях народного хозяйства. В частности, СКФ-технологии практически поровну (на одну треть) используются в таких отраслях мировой экономики, как: а) фармацевтика, б) пищевая/сельскохозяйственная промышленность, в) химия/нефтехимия. В частности, особый интерес со стороны нефтехимии (нефтедобыча, нефтепереработка) проявляется к процессам экстрагирования в среде СКФ. С помощью СК-СО2 можно улучшить отдачу нефтяных пластов, добиться полного извлечения битумов, в также решить многие задачи полимерной химии и лакокрасочной промышленности [5].
Помимо этого, повторное использование отработанного диоксида углерода СО2, являющегося побочным продуктом ряда промышленных производств, в экологически более эффективных процессах, направленных на получение многих востребованных химических и нефтехимических продуктов, позволяет решить злободневную проблему по утилизации СО2 и снижению его выбросов в окружающую среду. В наши дни известно много материалов, свойствами которых можно управлять с помощью воздействия обычного углекислого газа: это растворители, поверхностно-активные вещества, растворенные вещества, катализаторы, частицы, полимеры и гели [6]. Под влиянием СО2 они способны изменять практически любое свое свойство: полярность, ионную силу, гидрофильность, заряд поверхности, химическую активность и т.д. Однако особые и более привлекательные возможности предоставляет использование не традиционного диоксида углерода, а сверхкритического диоксида углерода СК-СО2, который является типичным “зеленым” неполярным СКФ-растворителем и по сравнению с традиционными органическими растворителями нетоксичен, негорюч и к тому же относительно дешев [7].
Исследованию возможностей применения СК-СО2 в химической и нефтехимической промышленности посвящено большое число работ [8–14]. Поскольку СК-СО2 часто применяется в технологиях разделения, то при разработке и оптимизации процессов экстракции, фракционирования и очистки с его участием необходимы знания о растворимости твердых веществ в СК-СО2 в присутствии или в отсутствие сорастворителей. В работе [15] были точно определены растворимости твердых веществ в СК-СО2 в трехкомпонентных и/или четырехкомпонентных системах (средние логарифмические расхождения между экспериментальными и рассчитанными данными составили 0.47).
Справедливости ради отметим, что, как установлено более двадцати лет назад, СК-СО2 обладает меньшей растворяющей способностью по отношению ко многим тяжелым составляющим нефтей, в связи с чем требуется его модификация сорастворителем, а применение СК-СО2 в качестве реакционной среды нередко ограничивается процессами, проводимыми при сравнительно низких температурах [16–18].
Большинство процессов нефтехимии осуществляется в газовой или жидкой реакционной среде, что напрямую связано с проблемами массопереноса, который, например, для реакций в жидкой фазе осложняется молекулярной диффузией (она в 104 раз ниже этого показателя для газовой среды). Эти проблемы также можно успешно решить при проведении процессов в среде СКФ. В частности, значительное число исследований в этой области посвящено использованию сверхкритической воды (СК-Н2О), поскольку она является хорошим растворителем для углеводородов, а также имеет достаточно высокую критическую температуру, что позволяет осуществлять в ее среде ряд промышленно важных процессов [19–24].
Со спецификой использования СКФ при осуществлении многих реакционных процессов с одновременным рассмотрением вопросов кинетики, механизмов, проблем диффузионного и массопереноса, вариантов отделения использованных катализаторов от продуктов реакции, работой пилотных установок и многим другим можно ознакомиться в работах [25–28].
Цель настоящего обзора – сравнительный анализ литературных данных по научным исследованиям и технологическим решениям, связанным с использованием СКФ-технологий в ряде химических и нефтехимических процессов (окисление, гидрирование, гидроформилирование, полимеризация, метатезис и др.), которые имеют коммерческую направленность и уже внедрены или планируются к промышленной реализации в ближайшем будущем.
Каталитическое гидрирование в среде СК-СО2
Реакции каталитического гидрирования различных соединений давно и широко реализуются в нефтехимической промышленности, по большей части в присутствии гетерогенных катализаторов в газо-жидкостных реакторах. А поскольку обычно такие реакции протекают довольно быстро, лимитирующим скорость фактором, как правило, является сопротивление массопереносу газообразного водорода сквозь жидкую фазу к поверхности твердого катализатора [29]. Одним из главных компонентов реакции гидрирования является взрывоопасный водород, что крайне нежелательно при проведении процесса в среде летучих органических растворителей, поэтому в этой реакции стараются по возможности заменять традиционные органические растворители на сверхкритический СО2.
Так, начиная с 1995 г. ученые The University of Nottingham совместно с компанией Thomas Swan and Co Ltd. активно занимаются изучением гидрирования ряда органических соединений с использованием СК-СО2 в непрерывном режиме. Большинство работ было выполнено в реакторах объемом 5 мл с фиксированным слоем катализатора с производительностью до 1200 мл продукта в ч (т.е. 7.5 т/год) [17, 18, 30]. Важные научные исследования, на которые ушло семь лет, завершилась масштабированием технологии от 5 мл реактора до действующей установки мощностью 1000 т/г, реализованной на практике компанией Thomas Swan and Co Ltd. [31]. На этой установке осуществлено гидрирование изофорона с получением продукта высокой чистоты, не требующего дальнейшей очистки. Этой же группой исследователей был разработан и коммерциализирован процесс гидрирования, направленный на получение таких специфичных продуктов, как α,β-дигидрокоричный альдегид из коричного альдегида, триметилциклогексан из сфорона (sphorone), циклогексиламин из анилина в непрерывном режиме [32].
Помимо этого, поскольку реакции непрерывного гидрирования с фиксированным слоем катализатора являются перспективными для проведения в сверхкритических условиях, то специально для их реализации в небольших масштабах специалисты The University of Nottingham и компании HEL Ltd. совместно разработали специальный реактор и вспомогательное оборудование по его обслуживанию [33]. Газы под высоким давлением, необходимые для достижения сверхкритического состояния, поставлялись в реактор не в газообразном или жидком виде, а получались in situ за счет селективного разложения муравьиной кислоты на СО2 и Н2, которые далее можно было использовать в качестве как сверхкритического растворителя, так и реагента (рис. 1).
Контроль за концентрацией Н2 в ходе реакции можно осуществлять параллельным разложением других жидких прекурсоров, а именно этилформиата, который разлагается с образованием С2Н6 + СО2. Для демонстрации своего подхода, названного технологией “без газов”, авторы приводят результаты гидрирования нескольких органических субстратов (алкенов, кетонов, альдегидов) и примеры практического использования предложенного метода, основанного на разложении жидких реагентов (муравьиной кислоты и этилформиата) с прямым образованием смесей СКФ без использования специального оборудования и компрессоров высокого давления [34]. Эксперименты показали, что образование небольших количеств СО в отходящих газах не оказывает заметного влияния на активность катализатора, однако, скорее всего, в дальнейшем это влияние будет зависеть от достигнутого уровня концентраций образуемого СО. Коммерческая инженерная версия СКФ-реактора “без газов”, разработанная компанией HEL Ltd. в начале 2000-х гг., была по тем временам самой малоразмерной реакторной системой СКФ в мире.
Также был проявлен большой интерес к комбинированной микро-реакторной технологии с СКФ [35]. Первое гидрирование соединений в микроканальном реакторе в среде скСО2 удалось осуществить и изучить авторам работы [36] с использованием специальной реакционной системы в присутствии иммобилизированного палладиевого катализатора (рис. 2). Гидрирование в такой микроканальной реакторной конструкции протекало очень быстро (в пределах 1 с) благодаря образованию большой удельной поверхности между фазами в микроканальном реакторе в целом и высокой производительности реакции в каждом отдельном взятом микроканале.
Начиная с середины 1970-х гг. активно разрабатываются гомогенные катализаторы для реакции присоединения водорода к СО2 с образованием муравьиной кислоты. Однако, все известные на сегодняшний день каталитические системы в основном направлены на производство солей, аддуктов или производных муравьиной кислоты, а не на получение муравьиной кислоты в чистом виде. Это объясняется тем, что реакция ее образования в чистом виде из СО2 и Н2 лимитируется термодинамическим равновесием, которое сдвинуто в сторону исходных газов [37]. А так как в большинстве случаев на практике требуется именно свободная муравьиная кислота, то в последние годы стали разрабатываться многоступенчатые поточные процессы, способные отводить исходные сырьевые газы от катализатора для предотвращения обратной реакции [38–41]. Например, была выдвинута новая концепция, позволяющая проводить непрерывное гидрирование СК-СО2 в свободную муравьиную кислоту на единой установке с одновременным отделением образующейся в чистом виде муравьиной кислоты от иммобилизированного катализатора и стабилизирующего основания [42, 43]. В этом процессе иммобилизированный металлоорганический рутениевый катализатор и нелетучее основание в ионной жидкости смешиваются с СК-СО2, служащим и в качестве реагента и в качестве экстрагирующей фазы, что позволяет непрерывно удалять продукт из реактора, тем самым смещая равновесие реакции (рис. 3).
Рис. 3.
Схема непрерывного гидрирования СО2 с получением свободной уксусной кислоты в системе, состоящей из СК-СО2 (экстрагирующая мобильная фаза) и ионной жидкости (стационарная фаза), катализатора и стабилизирующего основания [43].
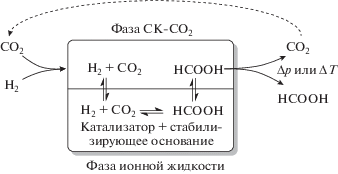
Другая важная задача нефтехимической отрасли, которую также можно решить с помощью СКФ-технологий, связана с составом дизельных фракций продукции нефтеперегонных заводов, которые часто содержат большое число нежелательных ароматических углеводородов. Для уменьшения содержания последних можно применять гидрирование дизельных фракций, что позволяет повысить содержание в них парафинов. Так, в работе [44] в качестве модельной реакции для изучения процесса гидрирования ароматических соединений изучалось гидрирование часто присутствующего в составе дизельных фракций нефти ароматического соединения – тетралина. Авторы изучили и сравнили показатели традиционного гетерогенно-каталитического процесса газ–жидкость–твердая фаза с показателями процесса, осуществленного в среде СК-СО2 в аналогичных условиях. С целью оптимизации рабочих условий и улучшения полученных результатов была рассчитана диаграмма равновесной конверсии реакции гидрирования при различных температурах и скоростях подачи реагентов. При гидрировании в среде СКФ при 493 К наблюдалось увеличение скорости реакции по сравнению с показателями традиционного гидрирования. Выдвинуто предположение, что гидрирование тетралина в СК-СО2 в качестве растворителя может стать перспективной моделью при создании эффективного коммерческого процесса гидрообработки нефтяных фракций.
Спектроскопическим методом ATR-IR при высоком давлении в ячейках (12−15 МПа) изучались образцы поверхностей катализаторов после взаимодействия СО2 и Н2 в непрерывном и периодическом режиме [45]. В качестве модельных каталитических систем использовались катализаторы платиновой группы (Pt, Pd, Rh и Ru), нанесенные на Al2O3. Полученные результаты показали, что образование СО из СК-СО2 в присутствии водорода наблюдается в присутствии всех катализаторов на основе металлов Pt-группы, которые обычно используются при проведении гетерогенно-каталитического гидрирования в среде СК-СО2. При этом образование СО на поверхности катализатора Pt/Al2O3 в ячейке непрерывного действия было менее заметно по сравнению с проведением реакции в периодическом режиме. Показания прибора ATR-IR in situ выявили, что образование СО в смесях СО2–Н2 во время гидрирования на катализаторах Pt-группы протекает в результате незначительной побочной реакции, а это указывает на то, что СК-СО2 можно рассматривать в качестве эффективного инертного растворителя для практического использования. Однако следует учитывать тот факт, что блокировка активных центров на поверхности катализатора молекулами СО и продуктов, которые образуются в результате превращений после основной реакции, может оказывать влияние на протекание реакции гидрирования и стать причиной возникновения непредвиденных сдвигов равновесия реакции по части распределения конечных продуктов гидрирования.
Изучена реакция гидрирования нитробензола в среде двух растворителей (СК-СО2 и этанола) в присутствии катализаторов платиновой группы (Pd, Pt, Ru и Rh), нанесенных на различные подложки (активированный уголь С, оксид алюминия Al2O3 и оксид кремния SiO2). Скорость гидрирования возрастала в ряду катализаторов Pt > > Pd > Ru, Rh при использовании в качестве растворителя этанола, а эффективность подложек составила C > Al2O3 > SiO2 для Pt и Pd при проведении гидрирования в среде СК-СО2. Для всех исследованных катализаторов селективность по анилину, полученному при гидрировании в среде СК-СО2, оказалась выше этого показателя в случае проведения реакции в этаноле. Гидрирование нитробензола на катализаторах Pd/C и Pt/C успешно осуществлялось в среде СК-СО2 при низкой температуре 35°С, а полученный анилин (органическая фаза) можно было легко отделять от побочно образуемой воды (жидкая фаза), растворителя СК-СО2 (СКФ) и катализатора (твердая фаза) простым фазовым разделением. В целом гидрирование нитробензола как в этаноле, так и в среде СК-СО2 зависело от структуры используемого катализатора. Исключение составили лишь несколько образцов катализаторов Pt/C, степень дисперсии металла в которых была мала и находилась на уровне <0.08.
В промышленности очень распространены процессы жидкофазного каталитического гидрирования алкенов с целью получения многих химических и нефтехимических продуктов, пользующихся повышенным спросом на рынке. В химии этих процессов доминируют гетерогенные палладиевые катализаторы, в частности, наночастицы палладия, нанесенные на твердый носитель. Подробные сведения об используемых каталитических системах, конструкциях реакторов и технологических таких процессах представлены в обзоре [47]. Поскольку крайне важно создание новых высокоэффективных и экологически чистых каталитических систем для парциального окисления алкенов в алканы, то в этой связи замена традиционных органических растворителей на альтернативные сверхкритические флюиды, в частности, СК-СО2, выглядит весьма привлекательной.
Так, работа [48] посвящена изучению гетерогенно-каталитического гидрирования алкенов в среде СК-СО2 в присутствии нового иммобилизированного палладиевого комплекса на оксиде кремния, содержащего S,O-хелатирующий лиганд. В качестве исходных объектов гидрирования использовали стирол, октен-1 и циклогексен. Иммобилизированный катализатор SiO2-ThiophPd(II) оказался в восемь раз более активным в гидрировании стирола, чем неиммобилизированный комплекс ThiophPd(II), и кроме того его можно было повторно использовать еще не менее десяти раз без заметной потери каталитической активности. Эффективность иммобилизированного палладиевого катализатора Pd(II) при гидрировании всех трех использованных алкенов оказалась выше показателей, полученных в присутствии катализатора Rh(I), при этом наибольшая каталитическая активность наблюдалась при гидрировании циклогексена.
Реакции гидроформилирования
Реакции гидроформилирования широко распространены в нефтехимии. Они являются одним из интересных маршрутов проведения химического синтеза в растворителях, позволяющих присоединять атом углерода к длинным углеводородным цепям [49]. В наши дни на основе гидроформилирования на промышленных химических и нефтехимических производствах нарабатывается большой объем пользующейся высоким спросом продукции. Специфика проведения и практическое применение этой реакции подробно освящены в обзоре [50].
Например, каталитическое гидроформилирование алкенов представляет собой наиболее эффективный и экологически привлекательный способ получения альдегидов. Принципиальная схема гидроформилирования алкенов представлена на рис. 4.
В свою очередь, образуемые по реакции гидроформилирования линейные и разветвленные альдегиды являются ценными конечными и промежуточными продуктами в синтезе широко востребованных на рынке спиртов, эфиров и аминов (рис. 5).
Немаловажную роль в научно-исследовательском и практическом продвижении каталитического гидроформилирования сыграло использование в качестве реакционной среды для ее осуществления сверхкритического диоксида углерода СК-СО2. Поскольку применяемые катализаторы гидроформилирования по большей части были и остаются гомогенными, то при проведении реакции остро стоит проблема отделения катализатора от получаемых продуктов. Главное преимущество использования СК-СО2 – отсутствие фазовой границы газ-жидкость и способность СК-СО2 поддерживать высокие концентрации растворенных газов с возможностью легкого разделения продукта и катализатора. Однако для повышения растворимости гомогенных катализаторов в СК-СО2 часто требуется их модификация, при этом применение иммобилизованных гомогенных катализаторов позволяет преодолевать трудности, связанные как с растворимостью катализатора, так и с его отделением от продуктов реакции.
Было предпринято несколько попыток использования сверхкритического диоксида углерода в качестве реакционной среды для реакции гидроформилирования. Кислотные свойства СО2 в растворе обеспечивают его преимущества в плане отделения гомогенных катализаторов с основными свойствами от нейтральных реакционных органических продуктов. В частности, компания BASF еще в середине 1980-х гг. применила СК-СО2 для экстракции так называемых “тяжелых остатков” из низкокипящих продуктов гидроформилирования и применяемого катализатора (родиевого) [51]. В начале 2000-х гг. для осуществления реакций гидроформилирования в среде СК-СО2 было рекомендовано использовать не проточные реакторы, а реакторы периодического действия под большим давлением, поскольку это необходимо для формирования монофазной системы по всему процессу гидроформилирования [52].
Проведение гидроформилирования в среде СК-СО2 представляет собой интересный метод разделения продукта и катализатора путем простого изменения плотности реакционной среды после проведения реакции. Для достижения высоких скоростей реакции химическая структура разрабатываемых катализаторов гидроформилирования (лиганды, противоионы) должна быть адаптирована к растворяющим свойствам СК-СО2. Была также разработана и многофазная версия использования СК-СО2 в реакции гидроформилирования [53], однако такой переход от монофазного к многофазному варианту увеличивает сложность процесса гидроформилирования и требует обязательной модификации каталитической системы, что затруднительно при реализации процесса в промышленных масштабах. В работе [54] описан способ управления селективностью процесса гидроформилирования октена-1 в смеси олефинов, состоящей из октена-1 и октадецена-1, в присутствии родиевого катализатора с помощью изменения их растворимости в СК-СО2.
Знакомство с литературными данными указывает на частое использование в процессах гидроформилирования родиевых катализаторов, однако к этим катализаторам ученые пришли не сразу. Первое применение СКФ в качестве реакционной среды для реакций каталитического гидроформилирования осуществилось с использованием кобальтовых катализаторов [55]. Будучи неполярными и обладая относительно низкой молекулярной массой, кобальтовые катализаторы легко растворялись в СК-СО2, однако при этом сами исходные соединения проявляли слабую растворимость и низкую активность в этой реакции. Позже, в результате многочисленных исследований было установлено, что наиболее успешными каталитическими системами для реакции гидроформилирования как в плане селективности, так и с точки зрения мягких условий проведения процесса, являются родиевые комплексы различных модификаций. Последние достижения в области дизайна катализаторов для проведения гидроформилирования в среде СK-СО2 и использования этих катализаторов для гидроформилирования α-олефинов с образованием линейных альдегидов и асимметричного гидроформилирования стирола подробно освещены в обзоре [56].
В модифицировании каталитических систем на основе родия в реакции гидроформилирования весьма эффективно проявили себя длинные перфторированные цепи, которые вводились в состав арилфосфинов и арилфосфитов. В частности, была предложена новая каталитическая система на основе родия, содержащая легко синтезируемые арилфосфиновые лиганды с CF3-группами. Эту систему применили в реакции гидроформилирования октена-1 в альдегиды в среде СK-СО2, при этом были получены соответствующие альдегиды с высокой конверсией (до 93–99%) и селективностью до 94% [57]. С использованием ИК-спектроскопии под высоким давлением и ЯМР изучена реакционная способность родиевых прекурсоров Rh(I) с синтезированными лигандами по отношению к СО и Н2. Было получено семейство фосфитов, содержащих лиганды с различными донорными и стерическими характеристиками, координационные свойства которых в составе родиевых каталитических комплексов были подробно изучены.
Для проведения реакции гидроформилирования в среде СK-СО2 использовали также родиевые комплексы, модифицированные простыми триалкилфосфинами [49]. Ниже критической точки смеси основными продуктами реакции были спирты, однако выше критической точки образовывались исключительно альдегиды. Сделано предположение, что изменения в соотношении количеств образующихся спиртов и альдегидов в зависимости от давления и свойств фазы связаны с тем, что альдегиды образуются исключительно в сверхкритической фазе, однако последующее гидрирование протекает уже в жидкой фазе (если таковая имеется). В присутствии родиевых катализаторов, модифицированных различными лигандами, с помощью ИК-спектроскопии изучена реакция гидроформилирования в среде СK-СО2 под высоким давлением. Этот процесс с использованием иммобилизованного катализатора представил большой практический интерес и был успешно коммерциализирован учеными при совместной работе с рядом заинтересованных компаний [58].
Реакция гидроформилирования октена-1 в присутствии родиевых каталитических систем детально изучена с использованием метода газовой хроматографии с on line мониторингом [59]. Результаты исследования показали, что влияние температуры, давления и соотношения фосфин/Rh в составе катализатора на скорость реакции и ее селективность аналогичны показателям, полученным в среде традиционных органических растворителей. Было определено максимальное значение TOF для катализаторов на уровне 1375, 500 и 115 ч–1 в качестве низкой каталитической активности для немодифицированной, фосфин-модифицированной и фосфит-модифицированной каталитических систем, соответственно. Для немодифицированных катализаторов скорости гидроформилирования в CК-СО2 оказались выше, чем в органических растворителях или жидком СО2, при этом модифицированные каталитические системы, сформированные с помощью различных фосфиновых и фосфитовых лигандов, проявили более высокую селективность.
Разработан процесс гидроформилирования в сверхкритических условиях относительно устойчивых алкенов (додецен-1) в непрерывном режиме [60]. Катализатор растворялся в ионной жидкости, тогда как субстрат и газообразные реагенты подавались в реактор растворенными в СК-СО2, что сопровождалось образованием альдегида. Сброс давления в жидкой смеси позволял получать чистые продукты, свободные от катализатора и растворителя. Использование родиевых комплексов триарилфосфитов при взаимодействии ионной жидкости с водой приводило к разрушению лигандов. Природа ионной жидкости играла важную роль в достижении высоких скоростей реакции, а вымывание родия в поток образуемых продуктов было низким и составило всего 0.012 ppm (за исключением низкого парциального давления СО/Н2, когда этот показатель был значительно выше). Установлено, что при определенных условиях процесса, сверхкритическая система с ионной жидкостью может работать непрерывно в течение нескольких недель без потери активности катализатора.
В качестве альтернативы гомогенному катализу изучено гетерогенно-катализируемое гидроформилирование гексена-1 [61]. Реакцию вели в среде СК-СО2 в присутствии гетерогенного родиевого катализатора, нанесенного на подложку из двуокиси кремния, а также использовали гомогенный родий-фосфиновый катализатор. Полученные результаты гидроформилирования сравнивались с показателями проведения реакции в толуоле в жидкой фазе и в толуоле в среде СК-СО2 в одних и тех же условиях. Скорости реакции в присутствии гетерогенного катализатора в СК-СО2 и толуолa в среде СК-СО2 оказались сравнимыми, тогда как обе эти скорости были выше скорости реакции в среде жидкого толуола. Начальные селективности по альдегиду в присутствии гетерогенного и гомогенного катализатора также оказались сравнимыми, однако по мере протекания процесса с использованием гетерогенного катализатора селективность реакции падала. Показана важная роль природы используемой фазы при разработке систем растворитель/катализатор для эффективной реализации реакции гидроформилирования.
Метатезис олефинов
Реакция метатезиса олефинов представляет собой оригинальный экологически чистый и экономически привлекательный способ создания сложных углеродных структур. Метатезис был открыт в 1950-х гг. и с тех пор прошел огромный путь развития (в 2005 г. разработчики реакции метатезиса Chauvin, Grubbs и Schrock стали лауреатами Нобелевской премии в области химии).
Как образец “зеленой” химии, реакция метатезиса получила широкое распространение в самых различных областях от нефтехимии (синтез высших линейных олефинов и пропилена) и полимерной химии (метатезис-полимеризация с раскрытием цикла) до общей химии в целом. Это позволило создать новые гомогенные катализаторы, способные работать в мягких условиях, улучшить селективность реакции метатезиса и расширить в целом объем синтезов на ее основе. Поскольку в последние годы наметилась четкая тенденция к использованию альтернативных реакционных сред взамен традиционных органических растворителей, то в этом плане идеально подошел СК-СО2, особенно в сочетании с гетерогенными катализаторами на основе Ru- и Mo-карбеновых комплексов или солей ряда переходных металлов. Отметим следующие преимущества использования СК-СО2 в метатезисе олефинов: а) высокая растворимость в нем алкенов; б) высокая эффективность по проникновению в мезо- и микропористую структуру подложек гетерогенных катализаторов благодаря низкой вязкости и высокой диффузионной способности; в) как в жидком, так и в сверхкритическом состоянии СО2 улучшает массоперенос (и скорость реакции) во многих гетерогенных процессах.
Жидкий/сверхкритический СО2 является также гибкой реакционной средой для проведения реакций метатезиса олефинов с раскрытием цикла (циклополимеризации) (ring-opening metathesis polymerization) и метатезиса олефинов с закрытием цикла (ring-closing olefin metathesis) в присутствии хорошо структурированных металлических катализаторов. В качестве последних в метатезисе могут применяться алкилиденовый комплекс 1, рутениевые карбены 2 и N-гетероциклические карбеновые лиганды. Как установлено, эффективность этих катализаторов при проведении реакции метатезиса в среде СK-СО2 схожа с каталитической эффективностью в среде традиционных хлорированных органических растворителей. Перечисленные выше катализаторы были успешно использованы в [62] для осуществления метатезиса олефинов с раскрытием и закрытием цикла в сжатом (сверхкритическом или жидком) диоксиде углерода. Проведенные детальные исследования позволили вникнуть в суть представлений о механизме реакции в нетрадиционной сверхкритической среде на молекулярном уровне. Метатезис удобно применять как для полимерных, так и для низкомолекулярных продуктов, для иммобилизации катализаторов, для настройки реакции с помощью контролирования плотности среды и т.д.
В работе [63] сообщается об осуществлении оригинального самометатезиса олефинов с использованием нанесенных рениевых катализаторов в среде СК-СО2. Установлено, что при 35°С в присутствии СК-СО2 в качестве растворителя (80–150 бар) исходные α-олефины (RCH=CH2, где R = C4–C6) подвергаются высокоселективному самометатезису, который катализируется оксидом Re (7%). Известно, что такая трансформация служит первой ступенькой для метатезиса алкенов, при котором гетерогенные катализаторы комбинируются с использованием СО2. Внутренняя эко-совместимость и уникальные физико-химические свойства такой среды в сверхкритическом состоянии обеспечивают как экологические, так и реакционно-синтетические преимущества, поскольку здесь не только устраняются традиционные токсичные растворители (например, н-гептан и толуол), но и изменяется скорость протекания реакции. Например, по прошествии двух часов с начала реакции средняя конверсия октена-1 в среде СК-СО2 достигает 67%, тогда как в н-гептане она составляет всего 40%, а продуктом такого самомететезиса является тетрадецен-7, который можно получать с выходом до 68%. При давлении 90 бар реакция становится чувствительной к мольным концентрациям олефина в СК-СО2, хотя увеличение давления (и плотности) сверхкритической среды не оказывает существенного влияния ни на скорость процесса, ни на его селективность. При этом установлено, что на показатели реакции сильно влияет природа используемой каталитической подложки: исследования показали, что оксиды рения приобретают хорошую активность при нанесении на γ-Al2O3, тогда как системы на SiO2 в качестве подложки оказались неэффективными.
Изучены реакции метатезиса с закрытием цикла в присутствии гетерогенного катализатора типа Hoveyda, иммобилизированного на подложках из различных материалов, при этом также установлена сильная зависимость каталитической активности системы от природы используемой подложки-носителя [64]. В некоторых случаях была достигнута высокая конверсия, что позволяло запускать повторные циклы превращений. Помимо этого, наблюдался очень низкий уровень экстрагирования металлического рутения из катализатора в продукт (20 ppm). Такой процесс имеет хорошие перспективы промышленной реализации в режиме непрерывной работы.
Синтез полимеров в среде СКФ
В наши дни мировое производство пластмасс превышает 340 млн т и увеличивается со средней скоростью около 2.5–3.0% в год. После энергетики и транспорта пластмассы относятся к крупнейшему сектору практического использования на рынке сырой нефти, при этом индустрия пластиков находится в сильнейшей зависимости от конъюнктуры мирового рынка нефти и рост цен на нефть отрицательно сказывается на цене изделий из пластиков.
Роль СКФ в синтезе полимеров была и остается предметом обсуждения многих научных обзоров. В частности, в [65] приводится ссылка на исторический обзор-эссе [66], где упомянуты многие мировые ученые, внесшие значительный вклад в исследования в области СКФ, в том числе М. Фарадей и Д.И. Менделеев. Автор обзора также отмечает и большой вклад советских ученых, подчеркивая, что пионерская работа по применению СКФ в процессах переработки полимеров была осуществлена В.Н. Ипатьевым, который еще в начале 20 в обнаружил, что этилен при критической температуре и высоком давлении в автоклаве способен некаталитическим путем олигомеризоваться в продукты с более высокой молекулярной массой.
В обзоре [67] описаны методики синтеза полимеров, включая гомогенную полимеризацию в растворе, дисперсионную и эмульсионную полимеризацию и поликонденсацию в массе, образование пористых полимеров и полимерных смесей, а также преимущества каждого из рассматриваемых методов. Анализируется вклад пластификации в процессы вкрапления и гетерогенно-химической модификации полимерных материалов, а также в процесс формирования микропористых полимерных пен с помощью давления. Отмечаются большие возможности использования сверхкритического диоксида углерода в самых различных областях, не только в полимерной химии, но и в органическом синтезе, гетерогенном и гомогенном катализе, неорганической и металлорганической химии.
При проведении полимеризации по процессу RAFT (Reversible Addition Fragmentation Chain Transfer Polymerization Process) были образованы полимерные цепи полиметилметакрилата на сферических поверхностях нано-оксида титана (n-TiO2) с использованием “зеленого” растворителя СК-СО2 [68]. Сначала n-TiO2 был функциализирован агентом RAFT, а затем проводилась живая полимеризация в среде СК-СО2, в результате чего были синтезированы высокомолекулярные гибридные материалы n-TiO2/PMMA. Агентом и для процесса функционализации и для процесса полимеризации служила валерьяновaя кислота с различными карбоксильными группами. Морфология полученных нанокомпозитов изучалась с помощью термогравитометрического анализа, сканирующей электронной микроскопии и динамического рассеяния света. Сравнивались скорости полимеризации и молекулярные веса получаемых продуктов при различных давлениях в среде СK-СО2 с показателями, полученными при проведении процесса в среде сжатых и несжатых органических растворителей и показано, что повышенные давления сверхкритического диоксида углерода обеспечивают более высокие скорости полимеризации и формирование более длинных цепей. Изучена также кинетика полимеризации ММА на поверхности n-TiO2 в среде СК-СО2 и установлен первый порядок реакции по концентрации мономера.
В обзоре [69] анализируются работы по использованию сверхкритических флюидных технологий для микронизации полимерных частиц и формирования эффективных порошковых полимерных покрытий. Рассмотрены потенциальные преимущества комбинированных СКФ-процессов, позволяющих объединить в единой технологической цепочке различные стадии формирования порошкового покрытия; определены возможные направления дальнейших научных и инжиниринговых исследований в этой области.
Хорошо известно, что пластиковые отходы трудно утилизировать, так как они очень долго разлагаются, поэтому не случайно ученые во всем мире работают над созданием биоразлагаемых пластиков. В таких пластиках в качестве биополимера сейчас широко используется крахмал, однако его непосредственно прямое применение приводит к снижению механических свойств образуемых пластмасс, в частности, к низкой прочности на разрыв, что затрудняет дальнейшую переработку соответствующих полимерных материалов.
Решением этих проблем стало смешивание крахмала с синтетическим полимером поликарболактоном. Установлено, что образуемые в этом случае смеси обладают хорошими механическими свойствами, сохраняя при этом свойственную крахмалу биоразлагаемость. Однако при простом смешивании исходных веществ наблюдается расслоение фаз и плохо регулируемая морфология, для устранения чего подошел бы эффективный межфазовый агент, который смог бы улучшить адгезию на поверхности раздела фаз между двумя полимерами. Как правило, для этих целей используются межфазные агенты на основе химически модифицированного поликапролактона PCL. Другой возможный вариант – прививание PCL к крахмалу за счет in situ полимеризации капролактама в присутствии частиц крахмала и катализатора. В качестве среды для прививания хорошо бы подошел СК-СО2. Так, в работе [70] была синтезирована серия реактивных межфазных агентов на основе поликапролактон-g-глицидилметакрилата (PCL-g-GMA) для образования трехкомпонентных смесей PCL/PCL-g-GMA/крахмал, что привело к большей функционализации образцов (PCL-g-GMA). Описать корреляцию между скоростями расходования мономера и инициатора удалось с помощью разработанной для этой цели математической модели. Она продемонстрировала хорошую сходимость с экспериментальными данными (на уровне 0.978), а сравнение этой модели с моделью для реакции, проводимой в расплаве, подтвердило увеличение эффективности реакции при ее проведении в среде СК-СО2. Кроме того, образцы, полученные в СК-СО2, обладали лучшими механическими свойствами и меньше подвергались разрушению.
С практической точки зрения очень важна эффективная пост-обработка полученных полимеров и в этом деле большую помощь может оказать все тот же СК-СО2. Хотя большинство полимеров действительно нерастворимы в СК-СО2, однако в свою очередь сам СК-СО2 демонстрирует хорошую растворимость во многих полимерных расплавах. Это снижает температуру стеклования полимеров и сопровождается значительным пластифицирующим эффектом. Сама пластификация очень важна для многих процессов последующей обработки полимеров, таких как пропитка, экстракция, химическая модификация и вспенивание. Вспенивание полимеров – это отдельная область интенсивных исследований, например, известно о создании непрерывной технологии вспенивания с использованием микро- и супермикроячеек [71].
Реакции окисления
Поскольку растворимость кислорода в сверхкритическом диоксиде углерода приблизительно в десять раз выше, чем в среде традиционных органических растворителей, то большое внимание уделяется также возможности проведения и реакций окисления различных субстратов в присутствии кислорода и СК-СО2 [72, 73]. При определенных условиях кислород с СО2 может образовывать пероксикарбонат, который в качестве агента по переносу кислорода действует даже эффективнее, чем сам кислород. Вот почему пероксикарбонат можно использовать для повышения эффективности многих окислительных процессов.
Изучено селективное гетерогенно-каталитическое окисление различных органических субстратов в СК-СО2 [74]. Для парциального окисления использовались три типа катализаторов: а) сложный оксо-комплекс на основе Fe; б) 0.5% Pt на γ-Al203 и в) 0.5% Pd на γ-Al203. Оксо-металлический катализатор показал конверсию циклогексана на уровне 3.9% по отношению к его окислам и эпоксидам, а главными продуктами реакции были кетон и спирт. Окисление циклогексана оказалось в сильнейшей зависимости от концентрации кислорода, тогда как продолжительность реакции (3–18 ч) и значения температур (60–150°С) оказали менее заметное влияние на конверсию и селективность реакции. При окислении циклогексана в присутствии катализаторов Pd/γ-Al203 и Pt/γ-Al203 образовывались смеси продуктов гидрирования и окисления.
Одним из ярких примеров окисления в среде СКФ является получение терефталевой кислоты, которая, как известно, служит одним из мономеров для получения полиэфиров. Обычно терефталевая кислота синтезируется окислением п-ксилола (≤200°С, ~3 МПа О2) в уксусной кислоте с использованием солей кобальта и марганца в качестве катализаторов и HBr в качестве промотора. Одновременно с этим происходит образование крайне нежелательного побочного продукта в виде 4-карбоксибензальдегида. Если же в качестве реакционной среды вместо уксусной кислоты использовать сверхкритическую воду СК-Н2О, то образование побочного продукта полностью исключается [75]. Эта технология вызвала большой интерес у таких известных мировых производителей терефталевой кислоты и полиэфиров, как компании Dupont, Invista, Artiva и Mitsubishi. С учетом коммерческой важности терефталевой кислоты используются и альтернативные способы ее производства, например, устраняющие использование п-ксилола. В качестве сырьевого материала вместо п-ксилола можно использовать толуол, который в присутствии СК-СО2 карбоксилируется в п-толуоловую кислоту, которая затем окисляется в терефталевую кислоту. Помимо получения терефталевой кислоты, сверхкритическую воду СК-Н2О можно успешно применять при обработке сточных вод, содержащих органические загрязнения, а также при выделении драгметаллов из отработанных катализаторов [76].
Предлагается также синтез терефталевой кислоты парциальным каталитическим окислением п-ксилола с использованием в качестве реакционной среды не СК-Н2О, а сверхкритического СК-СО2 [77]. Изучено влияния условий на протекание процесса в присутствии катализатора CoBr2, включая температуру, время пребывания и загрузку катализатора. Большинство из исследованных условий проведения процесса не способствовали синтезу кислоты (максимально достигнутый выход терефталевой кислоты не превысил 35%), что по всей вероятности было связано с плохой растворимостью в среде СК-СО2 использованного при окислении катализатора CoBr2. При этом добавки в реакционную смесь небольших количеств уксусной кислоты или воды приводили к увеличению конверсии п-ксилола и повышению выхода терефталевой кислоты. Кроме того, авторами было установлено, что заметно улучшить выход этой кислоты можно, применив катализатор на основе органического кобальта в качестве альтернативы катализатору CoBr2.
ЗАКЛЮЧЕНИЕ
СКФ, в том числе СК-СО2, обладают рядом неоспоримых конкурентных преимуществ и способны выступить в качестве достойной альтернативы летучим органическим растворителям, традиционно используемым в промышленности. Они экологически безопасны; благодаря низкой вязкости СКФ-среды в сочетании с высоким коэффициентом диффузии в их присутствии осуществляется хороший массо- и теплоперенос; катализатор меньше подвергается дезактивации; здесь легче контролировать кинетику процесса с помощью давления и температуры; почти полное отсутствие поверхностного натяжения обеспечиваeт высокую проникающую способность в СКФ (микроинкапсуляция, импрегнация и пр.).
В наши дни СКФ-технологии успешно работают на производствах ряда отраслей народного хозяйства. Однако, несмотря на явные технологические преимущества, они так и не нашли пока достойного применения в промышленных масштабах. Этому мешает ряд факторов, ограничивающих их использование: плохая растворимость полярных и высокомолекулярных соединений в СКФ; в некоторых случаях (например, когда отсутствуют ограничения по массопереносу) не наблюдается улучшения в проведении химической реакции; характерны высокие капиталовложения из-за необходимости применять специальное оборудование для работы при высоких давлениях.
Все это говорит о том, что научные и инжиниринговые исследования для преодоления существующих ограничений по широкому промышленному использованию СКФ следует продолжать. Воодушевляет тот факт, что благодаря инновационным разработкам по некоторым химическим и нефтехимическим процессам уже удалось решить одну из серьезных проблем – создать реально действующие в промышленных масштабах непрерывные СКФ-технологии, хотя до этого достижения СКФ-процессы могли реализовываться только в периодическом режиме.
Список литературы
Capello C., Fischer U., Hungerbuhler K. // Green Chem. 2007. V. 9. P. 927.
Charles Cagniard de la Tour. // Ann. Chim. Phys. 1822. V. 21. P. 127.
Zosel K. // Angew. Chem. Int. Ed. Engl. 1978. V. 17. P. 702.
Munshi P., Bhaduri S. // Curr. Sci. 2009. V. 97. № 1. P. 63.
Гумеров Ф., Яруллин Р. // The Chemical J. 2008. № 10. Р. 26.
Jessor P.G., Mercer S.M., Heldebrant D.J. // Energy Environ. Sci. 2012. V. 5. P. 7240.
Bell S. Supercritical CO2: a Green Solvent. Process Economics Program Report № 269. August 2009. 223 p.
Al Ghafri S.Z., Maitland G.C., Trusler J.P.M. // Fluid Phase Equilib. 2014. V. 365. P. 20.
Burant A., Lowry G.V., Karamalidis A.K. // Environ. Sci. Technol. 2013. V. 47. № 1. P. 37.
Tran T.Q.M.D., Neogi P., Bai B. // SPE J. 2017. V. 22. № 2. P. 539.
Im S.I., Shin S., Park J.W., Yoon H.J., Go K.S., Nho N.S., Lee K.B. // Chem. Eng. J. 2018. V. 31. P. 389.
Seyyedsar S.M., Farzaneh S.A., Sohrabi M. // J. Nat. Gas Sci. Eng. 2016. V. 34. P. 1205.
Marufuzzaman M., Henni A. // Can. J. Chem. Eng. 2015. V. 93. № 3. P. 553.
Rudyk S. // Energy Fuels. 2014. V. 28. № 7. P. 4714.
Bitencourt R.G., Palma A.M., Coutinho J.A.P., Cabral F.A., Meirellese A.J.A. // Fluid Phase Equilib. 2018. V. 482. P. 1.
Devetta L., Giovanzana A., Canu P., Bertucco A., Minder B.J. // Catal. Today. 1999. V. 48. № 1–4. P. 337.
Hitzler M.G., Smail F.R., Ross S.K., Poliakoff M. // Org. Process Res. Dev. 1998. V. 2. P. 137.
Hitzler M.G., Poliakoff M. // Chem. Commun. 1997. № 17. P. 1667.
Caniaz R.O., Simsek S., Arca S., Sarayloo E., Kavakli I.H., Erkey C. // J. Supercrit. Fluids. 2018. V. 133. Part 2. P. 674.
Zhao Q.Y., Guo L.J., Huang Z.J., Chen L, Jin H., Wang Y.C. // Energy Fuels. 2018. V. 32. № 2. P. 1685.
Liu J., Xing Y., Chen Y.X., Yuan P.Q., Cheng Z.M., Yuan W.K. // Ind. Eng. Chem. Res. 2018. V. 57. № 3. P. 867.
Campanario F.J., Ortiz F.J.G. // Energy Convers. Manage. 2017. V. 154. P. 591.
Wang K., Bao L.Y., Xing Y, Yuan P.Q., Cheng Z.M., Yuan W.K. // Ind. Eng. Chem. Res. 2017. V. 56. № 45. P. 12920.
Fedyaeva O.N., Antipenko V.R., Vostrikov A.A. // J. Supercrit. Fluids. 2017. V. 126. P. 55.
Bruno Miguel da Silva Pinho. Specific Properties of Supercritical Fluids for Fast and Exothermic Reactive Systems. Université de Bordeaux, 2015.
Franciò G., Hintermair U., Leitner W. // Philos. Trans. R. Soc. A. 2015. V. 28. P. 373.
Gandhi K., Arora S, Kumar A. // Int. J. Chem. Stud. 2017. V. 5. № 3. P. 336.
Manjare S.D., Dhingra K. // Materials Science for Energy Technologies. 2019. V. 2. № 3. P. 463.
Ya-Ping Sun. Supercritical Fluid technology in Materials Science and Engineering: Syntheses, Properties and Applications. CRC Press, 2002. 600 p.
Hydrogenation in supercritical CO2. The University of Nottingham. Clean Technology Group. URL: https://www.nottingham.ac.uk/supercritical/beta/hydrogenation.html.
Licence P., Ke J., Sokolova M., Ross S.K., Poliakoff M. // Green Chem. 2003. V. 5. Issue 2. P. 99.
Ross S.K., Meehan N.J., Poliakoff M., Cater DD.N. // Patetn EP № 1373166. 2004.
Hyde J.R, Walsh B., Singh J., Poliakoff M. // Green Chem. May, 2005. V. 7. № 5.
Hyde J.R., Poliakoff M. // Chem. Commun. 2004. № 13. P. 1482.
Ehrfeld W., Hessel V., Loewe H. Microreactors: New Technology for Modern Chemistry. Weinheim: Wiley-VCH, 2000.
Kobayashi J., Mori Y., Kobayashi S. // Chem. Commun. 2005. V. 28. № 20. P. 2567.
Jessop P.G. The Handbook of Homogeneous Hydrogenation. Weinheim: Wiley-VCH, 2007. P. 489.
Preti D., Resta C., Squarcialupi S., Fachinetti G. // Angew. Chem. Int. Ed. 2011. V. 50. № 52. P. 12551.
Schaub T., Paciello R., Mohl K.-D., Schneider D., Schfer M., Rittinger S. // Patent WO № 2010149507. 2010.
Zhang Z., Hu S., Song J., Li W., Yang G., Han B. // Chem. Sus. Chem. 2009. V. 2. № 3. P. 234.
Yasaka Y., Wakai C., Matubayasi N., Nakahar M. // J. Phys. Chem. A. 2010. V. 114. P. 3510.
Hintermair U., Wesselbaum S., Leitner W. // Patent WO № 2012095345. 2012.
Wesselbaum S., Dr. Hintermair U., Leitner W. // Angew. Chem. Int. Ed. 2012. V. 51. P. 8585.
Martins E.P., Aranda D.A.G., Pessoa F.L.P, Zotin J.L. // Braz. J. Chem. Eng. 2000. V.17. № 3. P. 361.
Burgener M., Ferri D., Grunwaldt J.D., Mallat T., Baiker A.S. // J. Phys. Chem. B. 2005. V. 109. № 35. P. 16794.
Zhao F., Zhang R., Chatterjee M., Ikushima Y. // Adv. Synth. Catal. 2004. V. 346. № 6. P. 661.
Moreno-Marrodan C., Liguori F., Barbaro P. // Beilstein J. Org. Chem. 2017. V. 20. № 13. P. 734.
Yilmaz F. // Anadolu University J. of Science and Technology A − Applied Sciences and Engineering. 2018. V. 19. № 2. P. 546.
Sellin M.F., Bach I., Webster J.M., Montilla F., Rosa V., Avilés T., Poliakoff M., Cole-Hamilton D.J. // J. Chem. Soc. Dalton Trans. 2002. P. 4569.
Franke R., Selent D., Börner A. // Chem. Rev. 2012. V. 112. P. 5675.
Schwirten K., Kummer R., Richter W. // Patent USA № 4568653. 1986.
Ke J., Han B., George M.W., Yan H., Poliakoff M. // J. Am. Chem. Soc. 2001. V. 123. № 16. P. 3661.
Gordon C.M., Leitner W. Catalyst Separation and Recycling. Springer: Dordrecht, 2006. P. 215.
Koch T.J., Desset S.L., Leitner W. // Green Chem. 2010. V. 12. № 10. P. 1719.
Rathke J.W., Klingler R.J., Krause T.R. // Organometallics. 1991. V. 10. № 5. P. 1350.
Borner A., Franke R. Hydroformylation: Fundamentals, Processes, and Applications in Organic Synthesis, First Edition. Wiley-VCH Verlag GmbH & Co. KGaA, 2016. 736 p.
Estorach C.T., Orejon A., Masdeu-Bulto A.M. // Green Chem. 2008. V. 10. P. 545.
Meehan N.J., Sandee A.J., Reek J.N.H., Kamer P.C.J., van Leeuwen P.W.N.M., Poliakoff M. // Chem. Commun. 2000. P. 1497.
Koch D., Leitner W. // J. Am. Chem. Soc. 1998. V. 120. P. 13398.
Webb P.B., Sellin M.F., Kunene T.E., Williamson S., Slawin A.M.Z., Cole-Hamilton D.J. // J. Am. Chem. Soc. 2003. V. 125. № 50. P. 15577.
Hemminger O., Marteel A., Mason M.R., Davies J.A. // Green Chem. 2002. V. 5. № 5. P. 507.
Fürstner A., Ackermann L., Beck K., Hori H., Koch D., Langemann K., Liebl M., Six Ch., Leitner W. // J. Am. Chem. Soc. 2001. V. 123. № 37. P. 9000.
Selva M., Perosa A., Fabris M., Canton P. // Green Chem. 2009. V. 11. № 2. P. 229.
Michalek F., Madge D., Rühe J., Bannwarth W. // Eur. J. Org. Chem. 2006. № 3. P. 577.
Kazarian S.G. // Polym. Sci. Ser. C. 2000. V. 42. № 1. P. 78.
Jessop P.G., Leitner W. Chemical Synthesis Using Supercritical Fluids. Weinheim: Wiley-VCH, 1999.
Cooper A.I. // J. Mater. Chem. 2000. V. 10. № 2. P. 207.
Hojjati B., Charpentier P.A. // Polymer. 2010. V. 51. № 23. P. 5345.
Макарян И.А, Костин А.Ю., Седов И.В. // Сверхкритические флюиды: Теория и Практика. 2017. Т. 12. № 3. С. 50.
Igbal M., Vensen Ch, Qian X., Picchion F. // Polymers. 2018. V. 10. P. 1285.
Park C.B., Suh N.P., Baldwin D.F. // Patent USA № 6051174. 2000.
Beckman E.J. // Environ. Sci. Technol. 2003. V. 37. P. 5289.
Lopez-Castillo Z.K., Aki S.N.V.K., Stadtherr M.A., Brennecke J.F. // Ind. Eng. Chem. Res. 2006. V. 45. P. 5351.
Sahle-Demessie E., Gonzalez M.A., Enriquez J., Zhao Q. // Ind. Eng. Chem. Res. 2000. V. 39. № 12. P. 4858.
Dunn J.B., Urquhart D.I., Savage P.E. // Adv. Synth. Catal. 2002. V. 344. № 3–4. P. 385.
Grumett P. // Platinum Met. Rev. 2003. V. 47. № 4. P. 163.
Kim D.S., Shin Y.H., Lee Y-W. // Chem. Eng. Commun. 2015. V. 202. № 1. P. 78.
Дополнительные материалы отсутствуют.