Нефтехимия, 2020, T. 60, № 4, стр. 456-463
Превращение продуктов гидроконверсии горючего сланца в присутствии нанесенных сульфидных NiMo-катализаторов
П. П. Дик 1, *, М. О. Казаков 1, А. В. Сайко 1, О. В. Климов 1, В. Ю. Перейма 1, И. С. Голубев 1, Е. Ю. Герасимов 1, С. А. Селищева 1, Т. П. Сорокина 1, В. П. Доронин 1, А. С. Носков 1
1 Институт катализа им. Г.К. Борескова СО РАН
630090 Новосибирск, Россия
* E-mail: dik@catalysis.ru
Поступила в редакцию 27.08.2018
После доработки 21.01.2019
Принята к публикации 11.03.2020
Аннотация
В работе изучено превращение горючего сланца (ГС) в среде водорода при давлении 6.0 МПа и температуре 400°С с последующим облагораживанием получающихся продуктов в присутствии сульфидных NiMo-катализаторов, нанесенных на носители, обладающие различной кислотностью. Обнаружено, что использование катализаторов приводит к существенному снижению содержания серы, азота, ароматических углеводородов и олефинов в получаемых из ГС жидких продуктах. Показано, что облагораживание продуктов гидроконверсии ГС с использованием катализаторов приводит к облегчению фракционного состава синтетической нефти и увеличению соотношения H/C. Использование катализаторов приводит к снижению выхода синтетической нефти за счет образования углеводородного газа и отложений кокса на катализаторах, причем выход синтетической нефти изменяется в следующем порядке: без катализатора (25.7 мас. %) > NiMo/ASA-Al2O3 (22.0 мас. %) > NiMo/Al2O3 (20.7 мас. %) > NiMo/USY-Al2O3 (15.8 мас. %).
ВВЕДЕНИЕ
Истощение запасов традиционной нефти и наличие альтернативных источников углеводородного сырья, превосходящих по своим запасам нефть, таких как ГС ставят перед исследователями задачу поиска перспективных способов их переработки в ценные продукты [1, 2]. В литературе представлены различные подходы к переработке ГС. Наиболее широко распространенным способом является пиролиз [3–5], которому присущи следующие недостатки: низкий выход жидких продуктов за счет образования углеводородного газа и отложений кокса, низкое качество получаемых продуктов (высокое содержание гетероатомных и ароматических соединений, олефинов). Известен подход к переработке ГС, заключающийся в термоэкстракции жидких продуктов из ГС органическими растворителями (толуолом, бензолом) в сверхкритических условиях при температурах около 500°С [6, 7]. Недостатки данного метода – низкий выход и низкое качество получаемых жидких продуктов. В работе [8] предложен способ получения жидких углеводородов (УВ) путем прессования ГС при давлении 8–10 атм и температуре 270°С. Минусы данного метода – невысокий выход жидких продуктов и его тяжелый фракционный состав. Повышенный выход жидких продуктов более высокого качества, чем при описанных выше методах, достигается при гидрогенизационном превращении чистых ГС в присутствии различных катализаторов, что обуславливает перспективность данного подхода к переработке ГС [7, 9–11].
Условия проведения процесса гидроконверсии ГС и свойства получаемого жидкого продукта – синтетической нефти, позволяют предположить, что, для улучшения ее свойств можно эффективно вести процесс гидроконверсии в одном реакторе в две стадии: 1 стадия – непосредственно гидроконверсия ГС с образованием синтетической нефти; 2 стадия – превращение получившейся нефти на катализаторах, используемых для процессов гидропереработки тяжелых нефтяных фракций. Однако, насколько известно, в литературе такие работы не представлены. В гидрогенизационных процессах переработки тяжелых нефтяных фракций, например вакуумного газойля, используются нанесенные сульфидные NiMo- или NiW-катализаторы. При этом тип процесса и желаемая глубина облегчения фракционного состава получаемых продуктов определяет природу используемого носителя, его кислотные свойства и крекирующую активность [12]:
• для процесса гидроочистки используется оксид алюминия, при этом фракционный состав претерпевает минимальные изменения; слабые кислотные свойства, низкая крекирующая активность;
• для мягкого гидрокрекинга и получения дизельных фракций с высоким выходом используется аморфный алюмосиликат в качестве кислотного компонента и оксид алюминия в качестве связующего; средние кислотные свойства, умеренная крекирующая активность;
• для глубокого гидрокрекинга и получения бензиновых фракций используется цеолит Y в качестве кислотного компонента и оксид алюминия в качестве связующего; сильные кислотные свойства, высокая крекирующая активность.
Цель данного исследования заключается в изучении закономерностей превращения продуктов гидроконверсии ГС на нанесенных сульфидных NiMo-катализаторах с различными крекирующими свойствами.
ЭКСПЕРИМЕНТАЛЬНАЯ ЧАСТЬ
Порошок аморфного алюмосиликата (ASA) готовили методом соосаждения по методике, описанной в работе [13], атомное соотношение Si/Al в полученном ASA составляло 0.9. Для приготовления цеолитсодержащего носителя использовали ультрастабильный цеолит Y (USY) с атомным соотношением Si/Al = 9.1 (по данным рентгенофазового анализа), дополнительно содержащий 3.3 мас. % оксидов редкоземельных элементов. В качестве связующего, для композитных носителей, а также для приготовления носителя, содержащего только гамма оксид алюминия, использовали псевдобемит производства Ишимбайского специализированого химического завода катализаторов.
Порошки ASA и псевдобемита, либо USY и псевдобемита помещали в смеситель с Z-образными лопастями и смешивали в течение 30 мин. В случае приготовления носителя Al2O3 смешения псевдобемита не производили. Затем смесь порошков (либо исходный псевдобемит в случае Al2O3) пептизировали азотной кислотой (мольное отношение HNO3/Al2O3 = 0.03–0.05) при перемешивании, в течение 30 мин. Полученную пасту экструдировали на плунжерном экструдере VINCI через тефлоновую фильеру с отверстиями в форме трилистника при давлении 3.5–4.0 МПа и скорости движения поршня 1.2 мм/с. Экструдаты сушили в течение 4 ч при температуре 120°C в токе воздуха, затем нагревали до 550°C в течение 2 ч, а затем прокаливали при 550°C в течение 4 ч. Диаметр описанной окружности готовых экструдатов составлял 1.5 мм. Массовое содержание ASA в готовом носителе ASA-Al2O3 составляло 50 мас. %. Массовое содержание USY в готовом носителе USY-Al2O3 составляло 30 мас. %.
Катализаторы готовили по методике, описанной в работе [12]. Носители пропитывали по влагоемкости водным раствором, приготовленным из основного карбоната никеля, лимонной кислоты и парамолибдата аммония. Полученные влажные катализаторы сушили при 120°C и прокаливали при 550°C в токе воздуха. Обозначения катализаторов и содержание активных металлов приведено в табл. 1.
Таблица 1.
Состав и текстурные характеристики образцов катализаторов
Образец | Содержание*, мас.% | Текстурные характеристики** | |||||||
---|---|---|---|---|---|---|---|---|---|
Ni | Mo | C | H | N | S | Sуд, м2/г | Vпор, см3/г | Vмикропор, см3/г | |
NiMo/Al2O3 | 3.7 | 12.5 | 4.0 | 1.6 | 0.25 | 9.50 | 148 | 0.36 | – |
NiMo/ASA-Al2O3 | 2.1 | 8.1 | 5.1 | 2.0 | 0.56 | 4.60 | 204 | 0.55 | – |
NiMo/USY-Al2O3 | 2.8 | 9.8 | 4.5 | 1.8 | 0.39 | 7.00 | 231 | 0.39 | 0.04 |
Текстурные характеристики катализаторов определяли методом физической адсорбции азота с использованием прибора ASAP 2400 (США). Перед анализом образцы нагревали в токе азота при 200°C в течение 2 ч. Удельную поверхность по методу БЭТ рассчитывали из количества азота, адсорбированного в области относительных давлений 0.05–0.30. Общий объем пор рассчитывали из количества азота, адсорбированного при относительном давлении, близком к единице (P/P0 = 0.995), предполагая, что все доступные поры заполнены конденсированным азотом в нормальном жидком состоянии. Объем микропор рассчитывали по t-методу.
Снимки просвечивающей электронной микроскопии высокого разрешения (ПЭМВР) были получены на электронном микроскопе JEM-2010 (JEOL, Япония) с разрешением по решетке 0.14 нм при ускоряющем напряжении 200 кВ. Образцы катализаторов в сульфидной форме закрепляли на стандартные медные сетки, которые помещали в держатель и вводили в камеру образцов электронного микроскопа. Среднюю длину частиц сульфидного активного компонента и среднее количество слоев сульфидного активного компонента в пакете рассчитывали на основе данных более чем 500 частиц для каждого образца катализатора.
Характеристики исходного образца ГС представлены в табл. 2. Содержание органического вещества в образце составляет около 33 мас. %.
Таблица 2.
Характеристики исходного горючего сланца
Влажность, мас. % | Зольность, мас. % | Элементный состав, мас. % | ||||
---|---|---|---|---|---|---|
C (общий) | C (орг.) | H | N | S | ||
7.2 | 54.9 | 31.4 | 28.8 | 3.1 | 0.6 | 5.4 |
Исходный образец ГС предварительно подвергали измельчению с отбором фракции с размером частиц менее 0.5 мм. Влажность образца определяли по ГОСТ Р 52917-2008. Содержание неорганических соединений (зольность) определяли по ГОСТ Р 55661-2013; для этого образец прокаливали в муфеле при температуре 815°C в течение 1 ч (с выдержкой 1 ч при 500°C в ходе нагрева).
Содержание углерода, водорода, азота и серы в исходном образце ГС, в получаемых жидких УВ, в отработанных катализаторах и переработанных сланцах определяли на CHNOS-элементном анализаторе Vario EL Cube (Elementar Analysensysteme GmbH). Для определения содержания органического углерода (C(орг)) исходный ГС промывали соляной кислотой в соответствии с методикой, описанной в ГОСТ 13455-91. Промывка HCl приводит к удалению карбонатов. Содержание органического углерода рассчитывали из данных элементного анализа исходного ГС и сланца, промытого соляной кислотой, с учетом потери массы при кислотной обработке.
Перед испытаниями катализаторы сульфидировали. Для этого 35 см3 катализатора помещали в стеклянный проточный реактор и при атмосферном давлении подавали H2S со скоростью 40 см3/мин. Катализатор нагревали до 220°C, выдерживали при 220°C 2 ч, затем нагревали до 400°C и выдерживали при этой температуре 2 ч, после чего охлаждали в токе азота.
С целью исследования возможности использования сульфидных NiMo-катализаторов для облагораживания продуктов гидроконверсии ГС, были проведены следующие эксперименты: 1) гидроконверсия ГС, эксперимент обозначен “Без катализатора”; 2) гидроконверсия ГС с последующим превращением в том же реакторе полученных продуктов на катализаторе; эксперименты обозначены соответственно используемому катализатору NiMo/Al2O3, NiMo/ASA-Al2O3, NiMo/USY-Al2O3.
Холостой опыт “Без катализатора” проводили в проточном реакторе со стационарным слоем ГС при температуре 400°C, давлении 6.0 МПа в потоке водорода 350 см3/мин. Исходный ГС с размером частиц менее 0.5 мм в количестве 90 см3 загружали в реактор. Для размещения ГС в изотермической зоне реактора выше и ниже слоя ГС размещали инертный материал – карбид кремния (размер частиц 1.0–2.3 мм). Водород подавали в верхнюю часть реактора, а продукты выводили из нижней части.
Превращение продуктов гидроконверсии ГС в присутствии катализаторов проводили в проточном реакторе при давлении, температуре и потоке водорода таких же, как и в холостом опыте. Катализатор (30 см3) загружали в нижнюю часть реактора, поверх загружали исходный ГС с размером частиц менее 0.5 мм (90 см3), разделяя два слоя стекловолокном. Для размещения ГС и катализатора в изотермической зоне реактора выше и ниже слоя ГС и катализатора размещали инертный материал – карбид кремния (размер частиц 1.0–2.3 мм).
Методика проведения экспериментов подробно описана ранее [9]. Конверсию органического углерода ГС рассчитывали по формуле:
(1)
${{X}_{{{\text{C(орг}})}}} = \frac{{{{m}_{{{\text{ГС}}}}}{{W}_{{{\text{C(орг)ГС}}}}} - {{m}_{{{\text{ПС}}}}}{{W}_{{{\text{C(орг)ПС}}}}}}}{{{{m}_{{{\text{ГС}}}}}{{W}_{{{\text{C(орг)Г}}С}}}}} \times 100,$Жидкие продукты подвергали фракционной разгонке при атмосферном давлении по методу ASTM D86, с отбором бензиновой фракции НК–180°C и дизельной фракции 180–360°C. Содержание серы в жидких продуктах определяли рентгенофлуоресцентным методом ASTM D4294 на анализаторе Horiba SLFA-2100. Фракционный состав жидких углеводородов определяли на газовом хроматографе Agilent 7890B, оснащенном испарителем, капиллярной колонкой и пламенно-ионизационным детектором, методом имитированной дистилляции ASTM D7169. Содержание ароматических соединений в дизельных фракциях определяли методом ВЭЖХ на хроматографе Agilent 1260 Infinity с рефрактометрическим детектором согласно ASTM D6591. Групповой состав бензиновых фракций определяли на газовом хроматографе Clarus 580 GC (Perkin Elmer), оснащенном испарителем, капиллярной колонкой и пламенно-ионизационным детектором, по ГОСТ Р 52714-2007 метод Б.
РЕЗУЛЬТАТЫ И ИХ ОБСУЖДЕНИЕ
Текстурные характеристики катализаторов, определенные с помощью низкотемпературной адсорбции азота, также приведены в табл. 1. Удельная поверхность катализаторов закономерно увеличивается в ряду: NiMo/Al2O3 < NiMo/ ASA-Al2O3 < NiMo/USY-Al2O3 из-за высокой удельной поверхности порошков ASA и USY. Объ-ем пор катализаторов увеличивается в ряду: N-iMo/Al2O3 < NiMo/ USY-Al2O3 < NiMo/ASA-Al2O3, что связано как с разным объемом пор в исходных носителях, так и с разным содержанием нанесенных оксидов активных металлов. При этом катализатор NiMo/ USY-Al2O3, из-за наличия в своем составе микропористого материала – цеолита, в отличие от других катализаторов имеет микропоры с удельным объемом 0.04 см3/г.
Образцы катализаторов в сульфидной форме были исследованы методом ПЭМВР. На микрофотографиях частицы MoS2, ориентированные параллельно направлению электронного пучка, представлены в виде темных полос. Для всех катализаторов было обнаружено, что частицы MoS2 расположены преимущественно на поверхности Al2O3, а не на цеолите или аморфном алюмосиликате. Для катализаторов были рассчитаны средняя длина частиц и среднее количество слоев сульфида молибдена в пакете (рис. 1). Расчет производился на основе более чем 500 частиц сульфида молибдена для каждого катализатора. Количество слоев в частице сульфида молибдена уменьшается в ряду: NiMo/Al2O3 > NiMo/USY-Al2O3 > NiMo/ASA-Al2O3 и равняется 2.1, 2.0 и 1.7 соответственно. Из рис. 1 видно, что для NiMo/ Al2O3 и NiMo/ASA-Al2O3-катализаторов преобладают однослойные сульфидные частицы. Для цеолитсодержащего катализатора преобладающими являются одно- и двухслойные частицы. Наибольшее среднее количество слоев в частице MoS2 наблюдается для NiMo/Al2O3-катализатора, что может быть связно с большей концентрацией активных металлов и меньшей удельной поверхностью исходного носителя. Средняя длина слоя сульфида молибдена уменьшается в ряду: NiMo/Al2O3 > > NiMo/USY-Al2O3 > NiMo/ASA-Al2O3 и равняется 2.3, 2.1 и 1.9 нм соответственно. Размер сульфидных слоев и количество слоев в частицах сульфидного компонента согласуются с данными, приведенными в литературе для NiMo-катализаторов гидропроцессов.
Рис. 1.
Морфология частиц MoS2: (а) распределение слоев MoS2 по длине; (б) распределение количества слоев MoS2 в сульфидных частицах. L – средняя длина слоя MoS2, N – среднее количество слоев MoS2 в сульфидной частице.
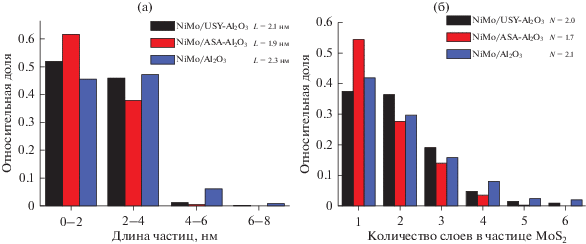
Выход жидких углеводородов (синтетической нефти) при гидроконверсии ГС “Без катализатора” составляет 25.7 мас. % в расчете на исходный ГС (табл. 3). Последующее превращение полученных продуктов гидроконверсии ГС на катализаторах приводит к снижению выхода синтетической нефти за счет образования углеводородного газа и отложений кокса на катализаторах. При использовании NiMo/Al2O3 и NiMo/ASA-Al2O3 выход синтетической нефти, несмотря на возможные различия в крекирующей активности катализаторов, близок и составляет: 20.5 и 22.0 мас. % соответственно. При использовании цеолитсодержащего катализатора NiMo/USY-Al2O3, обладающего сильными кислотными центрами и, соответственно, высокой крекирующей активностью, выход синтетической нефти (15.8 мас. %) существенно ниже из-за образования газообразных продуктов. Степень извлечения органического углерода при гидроконверсии ГС “Без катализатора” составляет 90.2%. В экспериментах с катализаторами исходный ГС превращается в таких же условиях, независимо от того загруженного вторым слоем образца катализатора, поэтому степень извлечения также составляет 90.2–90.3% (табл. 3).
Таблица 3.
Конверсия органического углерода и выход продуктов, при гидроконверсии ГС и при последующем превращении продуктов в присутствии катализаторов
Показатель | Без катализатора | NiMo/Al2O3 | NiMo/ASA-Al2O3 | NiMo/USY-Al2O3 |
---|---|---|---|---|
Конверсия C(орг), % | 90.2 | 90.3 | 90.2 | 90.3 |
Выход продуктов, мас. % | ||||
Синтетическая нефть, в том числе: | 25.7 | 20.5 | 22.0 | 15.8 |
бензиновая фракция (<180°C) | 3.2 | 4.4 | 4.7 | 5.3 |
дизельная фракция (180–360°C) | 9.0 | 8.8 | 9.5 | 2.0 |
вакуумный газойль (360–550°C) | 8.1 | 4.0 | 4.3 | 3.3 |
Остаток (>550°C) | 5.4 | 3.3 | 3.5 | 5.1 |
Отработанный сланец | 61.4 | 61.0 | 61.3 | 61.2 |
Кокс* | – | 2.1 | 1.3 | 1.9 |
Газ | 5.3 | 8.5 | 8.0 | 14.0 |
Вода | 7.5 | 7.9 | 7.4 | 7.1 |
Каталитическое превращение продуктов гидроконверсии ГС приводит к значительному изменению фракционного состава жидких продуктов (табл. 4). В случае применения NiMo/Al2O3 и NiMo/ ASA-Al2O3 происходит увеличение доли светлых нефтепродуктов, т.е. суммы бензиновой и дизельной фракций в получаемой синтетической нефти за счет превращения вакуумно-газойлевой фракции (360–550°C) и остатка (>550°C). В случае использования NiMo/USY-Al2O3 перераспределение фракций в синтетической нефти происходит таким образом, что увеличивается содержание бензиновой фракции и остатка (>550°C), а содержание дизельной фракции и вакуумно-газойлевой фракции (360–550°C) снижается.
Таблица 4.
Фракционный и элементный состав синтетической нефти, полученной при гидроконверсии ГС, а также облагороженной в присутствии катализаторов синтетической нефти
Показатель | Без катализатора | NiMo/Al2O3 | NiMo/ASA-Al2O3 | NiMo/USY-Al2O3 |
---|---|---|---|---|
Фракционный состав, мас. % | ||||
бензиновая фракция (<180°C) | 12.5 | 21.5 | 21.2 | 33.5 |
дизельная фракция (180–360°C) | 34.9 | 42.9 | 43.4 | 12.9 |
вакуумный газойль (360–550°C) | 31.5 | 19.4 | 19.4 | 21.0 |
остаток (>550°C) | 21.1 | 16.2 | 16.0 | 32.6 |
Элементный состав, мас. % | ||||
C | 83.1 | 86.7 | 86.9 | 86.2 |
H | 9.5 | 10.6 | 10.3 | 10.4 |
N | 2.1 | 1.1 | 1.1 | 1.3 |
S* | 3.9 | 1.0 | 0.8 | 1.6 |
S** | 3.7 | 0.8 | 0.7 | 1.4 |
H/C (ат.) | 1.37 | 1.47 | 1.42 | 1.45 |
При этом содержание остатка (>550°C) в синтетической нефти увеличивается за счет снижения выхода синтетической нефти, выход же остатка в мас. % по сравнению с экспериментом “Без катализатора” незначительно снижается.
На катализаторе NiMo/ASA-Al2O3 происходит образование дополнительных количеств бензиновой и дизельной фракций (табл. 3). На катализаторе NiMo/Al2O3 также происходит образование дополнительного количества бензиновой фракции, выход же дизельной фракции несколько ниже для опыта “Без катализатора”. На катализаторе NiMo/ USY-Al2O3 происходит образование дополнительного количества бензиновой фракции, однако выход дизельной фракции существенно ниже, чем на других катализаторах и в случае “Без катализатора”. При этом в отличие от катализаторов NiMo/ Al2O3 и NiMo/ASA-Al2O3 практически не наблюдается уменьшения выхода остатка (>550°C). Это, по-видимому, связанно с недоступностью сильных кислотных центров внутри каналов цеолита Y для крупных молекул, содержащихся во фракции с температурой кипения выше 550°С. В свою очередь, в катализаторах NiMo/Al2O3 и NiMo/ASA-Al2O3 кислотные центры доступны для таких молекул. Таким образом, на катализаторе NiMo/USY-Al2O3 преимущественно наблюдается превращение дизельной и вакуумно-газойлевой фракций в углеводородный газ и бензиновую фракцию, что вероятно обусловлено как локализацией кислотных центров в каналах цеолита, так и их силой.
По данным CHNS-анализа полученной синтетической нефти (табл. 4) использование NiMo-катализаторов приводит к существенному снижению содержания серы и азота в синтетической нефти. Гидрообессеривающая активность катализаторов увеличивается в ряду: NiMo/USY-Al2O3 < < NiMo/Al2O3 < NiMo/ASA-Al2O3. Гидродеазотирующая активность катализаторов увеличивается в ряду: NiMo/USY-Al2O3 < NiMo/Al2O3 = NiMo/ ASA-Al2O3. Наибольшая активность катализатора NiMo/ASA-Al2O3 в гидрообессеривании, может быть обусловлена наименьшим размером частиц сульфидного активного компонента. Стоит отметить, что содержание активных металлов в катализаторе NiMo/Al2O3 выше, чем в катализаторе NiMo/ASA-Al2O3 и является характерным для катализаторов гидроочистки вакуумного газойля. Однако гидрообессеривающая активность NiMo/ Al2O3 оказалась ниже, чем катализатора NiMo/ ASA-Al2O3, что вероятно связано с отличием состава синтетической нефти от вакуумного газойля. Катализатор NiMo/USY-Al2O3, несмотря на промежуточное содержание активных металлов, обладает наименьшей гидрообессеривающей и гидродеазотирующей активностью. По-видимому, для переработки синтетической нефти оптимальный состав катализаторов гидроочистки и гидрокрекинга может отличаться от такового для переработки вакуумного газойля.
Из всех полученных синтетических нефтей были выделены бензиновые и дизельные фракции и определен их групповой состав (табл. 5, 6). Дизельные фракции, выделенные из продуктов полученных облагораживанием на NiMo катализаторах, характеризуются значительно меньшим содержанием ди-, три- и полициклических ароматических УВ, по сравнению с дизельной фракцией, выделенной из жидкого продукта полученной гидроконверсией ГС “Без катализатора”. Содержание моноциклических ароматических углеводородов в дизельных фракциях, полученных на NiMo катализаторах выше, чем в дизельной фракции, полученной гидроконверсией ГС “Без катализатора”, что связанно с превращением ди-, три- и полициклических ароматических УВ в соответствующие моноциклические УВ на NiMo-катализаторах. Судя по содержанию ди-, три- и полициклических ароматических УВ дизельных фракциях гидрирующая активность исследованных катализаторов увеличивается в ряду: Ni-Mo/ASA-Al2O3 < NiMo/Al2O3 < NiMo/USY-Al2O3.
Таблица 5.
Характеристики дизельных фракций, полученных при гидроконверсии ГС в присутствии катализаторов
Показатель | Без катализатора | NiMo/Al2O3 | NiMo/ASA-Al2O3 | NiMo/USY-Al2O3 |
---|---|---|---|---|
Групповой состав, мас. % | ||||
Неароматические углеводороды | 63.9 | 67.9 | 64.2 | 70.7 |
Моноароматические углеводороды | 21.2 | 26.3 | 29.3 | 25.9 |
Диароматические углеводороды | 9.0 | 5.0 | 5.7 | 2.9 |
Три+-ароматические углеводороды | 5.9 | 0.8 | 0.8 | 0.5 |
Содержание S, мас. % | 4.4 | 0.1 | 0.2 | 0.2 |
Таблица 6.
Групповой состав бензиновых фракций, полученных при гидроконверсии ГС в присутствии катализаторов
Групповой состав, мас. % | Без катализатора | NiMo/Al2O3 | NiMo/ASA-Al2O3 | NiMo/USY-Al2O3 |
---|---|---|---|---|
н-Алканы | 13.5 | 21.6 | 21.4 | 14.4 |
Изоалканы | 25.8 | 29.9 | 30.6 | 29.3 |
Олефины | 16.2 | 3.0 | 2.8 | 4.0 |
Циклоалканы | 16.4 | 17.1 | 18.2 | 33.3 |
Арены | 24.1 | 25.6 | 24.8 | 17.8 |
Не идентифицировано | 3.9 | 2.9 | 2.3 | 1.2 |
Содержание серы в дизельной фракции (4.4 мас. %) полученной гидроконверсией ГС “Без катализатора” выше, чем в исходной синтетической нефти (3.9 мас. %), что согласуется с результатами, полученными ранее [10]. В дизельных фракциях, полученных на NiMo-катализаторах содержание серы существенно ниже, чем в исходной синтетической нефти, и составляет 0.1–0.2 мас. % что существенно меньше, чем для дизельной фракции, полученной гидроконверсией ГС “Без катализатора”.
Согласно полученным результатам, содержание олефинов (2.8–4 мас. %) в бензиновых фракциях, полученных превращением продуктов гидроконверсии ГС на NiMo-катализаторах, значительно ниже, чем в бензиновой фракции, полученной гидроконверсией ГС “Без катализатора” (16.2 мас. %). Это объясняется гидрированием олефинов в предельные углеводороды на сульфидных катализаторах. Для бензиновых фракций, полученных на NiMo/ASA-Al2O3 и NiMo/Al2O3, наблюдается близкий групповой состав, который резко отличается от группового состава бензиновой фракции, полученной на NiMo/USY-Al2O3. Групповой состав бензиновой фракции, полученной на NiMo/USY-Al2O3, характеризуется меньшим содержанием аренов, алканов и большим содержанием циклоалканов.
ЗАКЛЮЧЕНИЕ
Полученные результаты показывают, что проведение процесса гидроконверсии ГС с последующим облагораживанием продуктов в одном реакторе в присутствии нанесенных сульфидных NiMo-катализаторов позволяет существенно улучшить качество получаемой синтетической нефти: снизить содержание серы, азота, ароматических соединений и олефинов, увеличить долю светлых фракций. Превращение продуктов гидроконверсии ГС в присутствии нанесенных сульфидных NiMo-катализаторов приводит к уменьшению выхода синтетической нефти за счет образования газообразных продуктов и кокса на катализаторах. Наибольший выход синтетической нефти – 22.0 мас.% наблюдался для катализатора на основе аморфного алюмосиликата NiMo/ASA-Al2O3, что всего на 3.7 мас. % ниже, чем для гидроконверсии ГС “Без катализатора”. Наименьший выход синтетической нефти наблюдался для цеолитсодержащего катализатора NiMo/USY-Al2O3, обладающего излишней для данного процесса крекирующей активностью и низкой селективностью по отношению к жидким продуктам. Кроме того, для данного катализатора превращение наиболее тяжелой фракции синтетической нефти – остатка (>550°C) происходит неэффективно, по-видимому, из-за локализации кислотных центров в микропорах.
По совокупности выхода продуктов и их качества, наиболее перспективным для облагораживания продуктов гидроконверсии ГС является; катализатор на основе аморфного алюмосиликата, наименее перспективным – катализатор на основе цеолита; катализатор на основе оксида алюминия занимает промежуточное положение
Список литературы
Gwyn J.E. // Fuel Process. Technol. 2001. V. 70. № 1. P. 27.
Dyni J.R. Oil Shale, in: Survey of Energy Resources. Clarke A.W., Trinnaman J.A. (Eds.). World Energy Council, 2010. P. 93.
Speight J.G. Shale Oil Production Processes. Elsevier Inc., 2012. P. 192.
Стрижакова Ю.А., Усова Т.В. // Химия твердого топлива. 2008. № 4. С. 7.
Зайденцалъ А.Л., Сооне Ю.X., Муони Р.Т. // Химия твердого топлива. 2008. № 2. С. 14.
Анисимов А.В., Кардашев С.В., Акопян А.В., Теренина М.В., Поликарпова П.Д., Винокуров В.А., Караханов Э.А. // Химия твердого топлива. 2015. № 5. С. 59.
Кардашев С.В., Максимов А.Л., Тараканова А.В., Кардашева Ю.С., Анисимов А.В., Караханов Э.А. // Химия твердого топлива. 2016. № 4. С. 28.
Ромаденкина С.Б., Решетов В.А. // Химия твердого топлива. 2016. № 2. С. 61.
Казаков М.О., Дик П.П., Климов О.В., Черепанова С.В., Чесалов Ю.А., Носков А.С. // Журн. прикладной химии. 2016. Т. 89. № 2. С. 247 [Russian J. of Applied Chemistry. 2016. V. 89. № 2. Р. 254].
Казаков М.О., Дик П.П., Климов О.В., Шаверина А.В., Перейма В.Ю., Носков А.С. // Химия твердого топлива. 2018. № 1. С. 27 [Solid Fuel Chemistry, 2018, V. 52. № 1. Р. 26].
Казаков М.О., Климов О.В., Дик П.П., Шаверина А.В., Перейма В.Ю., Носков А.С. // Нефтехимия. 2017. Т. 57. № 6. С. 792 [Petrol. Chemistry. 2017. V. 57. № 12. Р. 1169].
Dik P.P., Klimov O.V., Koryakina G.I., Leonova K.A., Pereyma V.Yu., Budukva S.V., Gerasimov E.Yu., Noskov A.S. // Catal. Today. 2014. V. 220–222. P. 124.
Chen S., Li T., Cao G., Guan M // Patent USA № 6399530. 1998.
Дополнительные материалы отсутствуют.