Нефтехимия, 2020, T. 60, № 4, стр. 483-487
Жидкофазное окисление н-пропилмеркаптана молекулярным кислородом в присутствии аммиачного раствора фталоцианина кобальта
О. М. Корнетова 1, *, А. М. Мазгаров 1, А. Ф. Вильданов 1, И. К. Хрущева 1
1 АО “Волжский научно-исследовательский институт углеводородного сырья”
420061 Республика Татарстан, Казань, Россия
* E-mail: vniius.4lab@mail.ru
Поступила в редакцию 13.01.2020
После доработки 10.03.2020
Принята к публикации 11.03.2020
Аннотация
Исследованы основные кинетические закономерности окисления н-пропилмеркаптана молекулярным кислородом в модельной смеси с дизельным топливом в присутствии аммиачного раствора фталоцианина кобальта. На основе экспериментальных данных получено кинетическое уравнение реакции и подобраны оптимальные условия безотходного процесса очистки нефтей от сероводорода и меркаптанов.
Технический Регламент Евразийского Экономического Союза ТР ЕАЭС 045/2017 “О безопасности нефти, подготовленной к транспортировке и (или) использованию” накладывает ограничение на содержание сероводорода (не более 20 ppm) и суммарное содержание метил- и этилмеркаптанов (не более 40 ppm) в транспортируемой нефти.
В настоящее время очистка нефти от сернистых соединений на промыслах производится отдувкой бессернистым углеводородным газом, нейтрализацией химическими реагентами и окислением кислородом воздуха в присутствии катализаторов [1, 2]. Отдув сероводорода и легких меркаптанов углеводородным газом требует наличия на установке подготовки нефти блока очистки сероводородсодержащего углеводородного газа. Данная технология менее эффективна для очистки нефти от легких меркаптанов, поэтому возникает необходимость комбинировать данную технологию с одним из химических методов для доочистки нефти от метил- и этилмеркаптанов до требуемых норм.
Другим распространенным способом промысловой очистки нефти от сероводорода и легких меркаптанов является технология нейтрализации указанных соединений химическими реагентами. В качестве нейтрализаторов широко используются аминоформальдегидные смеси. С одной стороны, технология эффективная, простая и не требует больших капитальных затрат. С другой стороны, имеется ряд серьезных недостатков: высокая токсичность формальдегида, большой расход и, соответственно, высокая удельная стоимость очистки сырья. Кроме того, на некоторых НПЗ обнаружены негативные последствия от применения формальдегидсодержащих нейтрализаторов для очистки нефти от сероводорода и легких меркаптанов. Как выяснилось, свободный и связанный с сероводородом формальдегид, который приходит вместе с потоком нефти на НПЗ, является причиной коррозии и забивки аппаратуры на установках первичной переработки нефти. Забивка оборудования происходит полиметиленсульфидами, представляющими собой труднорастворимый полимер, являющийся продуктом взаимодействия сероводорода и формальдегида [3].
Этих недостатков не имеют окислительно-каталитические технологии промысловой очистки нефти от сероводорода и легких меркаптанов [4, 5].
В России первая окислительно-каталитическая технология удаления сероводорода и низкомолекулярных меркаптанов из сырой нефти и газоконденсатов (процесс ДМС) была разработана в АО “ВНИИУС”. Суть технологии ДМС заключается в экстракции сероводорода и нафтеновых кислот слабощелочным раствором на первой стадии процесса, и на второй стадии – в прямом окислении содержащихся в нефти низкомолекулярных меркаптанов кислородом воздуха в щелочной среде в присутствии катализатора ИВКАЗ (дихлордисульфофталоцианина кобальта). Технологии из серии ДМС внедрены на предприятиях Республики Казахстан (СП “Тенгизшевройл”, CNPC “Актобемунайгаз”, АО “КазахойлАктобе”), России (ЗАО “Южно-Уральская промышленная компания”), Литвы (АО “МажейкюНафта”) и др.
Однако широкое использование щелочных растворов в процессах окислительной очистки нефти от сероводорода и легких меркаптанов ограничивается следующими факторами: многие нефти образуют со щелочными растворами трудноразделяющиеся эмульсии; безвозвратная потеря части щелочного раствора за счет взаимодействия с сероводородом, углекислым газом и нафтеновыми кислотами, которые могут присутствовать в нефти в значительных количествах. Регенерации подвергается только та часть щелочного раствора, которая связана с меркаптанами. Отсюда следует, что данная технология характеризуется высоким расходом щелочи.
В 2006 г. в АО “ВНИИУС” был разработан новый окислительно-каталитический процесс очистки нефти от сероводорода ДМС-1МА в присутствии каталитического комплекса – аммиачного раствора катализатора ИВКАЗ [5–7]. В 2007 г. технология внедрена на УПВСН “Кутема” НГДУ “Нурлатнефть” ПАО “Татнефть” для очистки тяжелой карбоновой нефти от сероводорода. Технология заключается в прямом окислении сероводорода в нефти кислородом воздуха в присутствии каталитического комплекса. Процесс проводится при давлении 0.4–1.0 МПа и температуре 50–60°С. В присутствии аммиачного раствора катализатора ИВКАЗ сероводород окисляется до элементной серы.
В ходе исследований было обнаружено, что при окислении сероводорода окисляются и низкомолекулярные меркаптаны, присутствующие в нефти. По аналогии с реакцией окисления меркаптанов в водно-щелочном растворе [8] реакция окисления меркаптанов в аммиачном растворе катализатора ИВКАЗ можно представить следующими двумя уравнениями, где конечным продуктом окисления меркаптанов являются дисульфиды:
(1)
${\text{N}}{{{\text{H}}}_{4}}{\text{OH}} + {\text{RSH}} \to {\text{N}}{{{\text{H}}}_{4}}{\text{RS}} + {{{\text{H}}}_{2}}{\text{O}},$(2)
$\begin{gathered} 2{\text{N}}{{{\text{H}}}_{4}}{\text{RS}} + 0.5{\kern 1pt} {{{\text{O}}}_{2}} + {{{\text{H}}}_{2}}{\text{O}}\xrightarrow{{{\text{Kt}}}} \\ \to {\text{RSSR}} + 2{\text{N}}{{{\text{H}}}_{4}}{\text{OH}}.{\text{\;}} \\ \end{gathered} $В данной работе исследованы кинетические закономерности окисления н-пропилмеркаптана молекулярным кислородом в присутствии аммиачного раствора катализатора ИВКАЗ в среде углеводородов.
ЭКСПЕРИМЕНТАЛЬНАЯ ЧАСТЬ
Для проведения исследований был выбран н-пропилмеркаптан, который имеет достаточно высокую температуру кипения (Ткип = 67.6°С), что позволяет избежать испарения окисляемого компонента в газовую фазу и исключить ошибку эксперимента. Все эксперименты по окислению проводились при температуре 30–50°С.
Кинетику окисления н-пропилмеркаптана исследовали на модельной смеси с гидроочищенным дизельным топливом. Для приготовления модельной смеси использовали н-пропилмеркаптан фирмы “Aldrich” с чистотой 97%. Катализаторный комплекс (КТК) готовили путем растворения порошковой формы катализатора ИВКАЗ в 25%-ном водном растворе аммиака. Окисление проводили при атмосферном давлении техническим кислородом (О2 = 99.5 об. %) в стеклянном реакторе периодического действия объемом 250 мл при постоянном перемешивании магнитной мешалкой. Реактор был снабжен отражательной перегородкой, обратным холодильником и контактным термометром, соединенным с электронным реле. Обогрев реактора производили с помощью нихромовой спирали, напряжение на которой регулировали ЛАТРом. Постоянство температуры поддерживали с точностью до ±0.5°С контактным термометром, управляющим электронным реле. За начало реакции принимали момент достижения заданной температуры в реакторе. Окисление проводили в течение 60 мин. Скорость реакции окисления н-пропилмеркаптана определяли по скорости его расходования в реакционной смеси. Анализ на содержание н-пропилмеркаптана в реакционной смеси проводили через равные промежутки времени методом потенциометрического титрования раствором азотнокислого аммиаката серебра по ГОСТ 17323-71 (СТ СЭВ 756-77) “Топливо для двигателей. Метод определения меркаптановой и сероводородной серы потенциометрическим титрованием” на приборе рН-метр-иономер “Эксперт-001”.
РЕЗУЛЬТАТЫ И ИХ ОБСУЖДЕНИЕ
В ходе проведения кинетических исследований была изучена зависимость скорости окисления н-пропилмеркаптана от концентрации меркаптана в исходной модельной смеси, концентрации катализаторного комплекса в реакционной смеси и от температуры проведения процесса окисления. Предварительными опытами было установлено, что число оборотов мешалки N = 2500 об./мин соответствует кинетической области для окисления н-пропилмеркаптана.
Зависимость скорости окисления н-пропилмеркаптана от концентрации катализаторного комплекса изучалась при температуре 50°С и исходной концентрации меркаптана в модельной смеси, равной 0.0095 моль/л. На рис. 1 изображены графики изменения концентрации н-пропилмеркаптана по времени в зависимости от концентрации катализаторного комплекса в реакционной массе.
Рис. 1.
Графики изменения концентрации н-пропилмеркаптана по времени в зависимости от концентрации катализаторного комплекса: 1 – [КТК] = 0.026 моль/л; 2 – [КТК] = 0.130 моль/л; 3 – [КТК] = 0.181 моль/л; 4 – [КТК] = 0.260 моль/л.
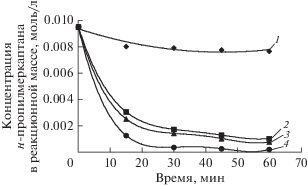
Анализ экспериментальных данных, приведенных на рис. 1, позволил наглядно представить влияние концентрации катализаторного комплекса в реакционной массе на степень превращения н-пропилмеркаптана (рис. 2).
Рис. 2.
Влияние концентрации КТК в реакционной массе на степень превращения н-пропилмеркаптана за 60 мин при температуре 50°С.
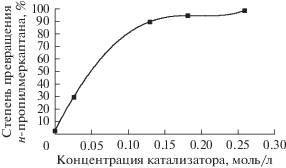
Как видно из рис. 2, скорость реакции сильно зависит от концентрации КТК в интервале 0.00–0.15 моль/л. В диапазоне концентраций КТК 0.12–0.16 моль/л в реакционной массе происходит превращение более 90% н-пропилмеркаптана. Следовательно, диапазон концентраций КТК 0.12–0.16 моль/л можно считать оптимальным для окисления н-пропилмеркаптана и дальнейшее увеличение концентрации КТК в реакционной массе нецелесообразно.
Исследование кинетики окисления н-пропилмеркаптана в зависимости от исходной концентрации меркаптана в модельной смеси проводили при температуре 50°С, концентрации КТК, рав-ной 0.13 моль/л и при различных концентрациях н-пропилмеркаптана. На рис. 3 приведены графики изменения концентрации н-пропилмеркаптана в процессе его окисления по времени в зависимости от исходной концентрации меркаптана.
Рис. 3.
Графики изменения концентрации н-пропилмеркаптана по времени в зависимости от исходной концентрации меркаптана в модельной смеси: 1 – [RSH]исх= 0.0064 моль/л; 2 – [RSH]исх= 0.0095 моль/л; 3 – [RSH]исх= 0.0116 моль/л.
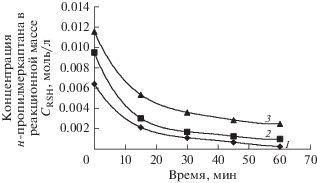
На рис. 4 изображены полулогарифмические анаморфозы кинетических кривых окисления н‑пропилмеркаптана по времени в зависимости от исходной его концентрации в модельной смеси. Графики зависимости логарифма концентрации lgCRSH от времени имеют вид прямых линий, что свидетельствует о первом порядке реакции по концентрации н-пропилмеркаптана в реакционной массе. Непараллельный характер этих прямых говорит о присутствии явления торможения процесса окисления продуктами реакции.
Рис. 4.
Графики изменения логарифма концентрации н-пропилмеркаптана в реакционной массе по времени при различных его исходных концентрациях в модельной смеси: 1 – [RSH]исх = 0.0064 моль/л; 2 – [RSH]исх = = 0.0095 моль/л; 3 – [RSH]исх = 0.0116 моль/л.
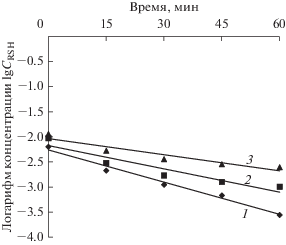
На рис. 5 представлены графики изменения концентрации н-пропилмеркаптана в реакционной массе по времени в зависимости от температуры.
Рис. 5.
Графики изменения концентрации н-пропилмеркаптана по времени в зависимости от температуры: 1 – 30°С; 2 – 40°С; 3 – 50°С. Исходная концентрация н-пропилмеркаптана в модельной смеси составляет 0.0095 моль/л. Концентрация КТК имеет значение 0.13 моль/л.
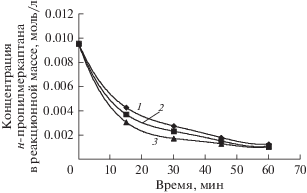
Согласно рис. 5, реакция окисления н-пропилмеркаптана имеет слабую температурную зависимость. Хотя теоретически, по правилу Вант-Гоффа, скорость реакции при повышении температуры на 10°С возрастает вдвое. Первые 30 мин скорость окисления при различных температурах значительно отличается, затем эта разница стремится к нулю, что объясняется явлением торможения реакции окисления продуктами, образующимися в реакционной массе.
На основе экспериментальных данных, полученных при исследовании кинетики окисления н-пропилмеркаптана в модельной смеси в присутствии аммиачных растворов фталоцианиновых катализаторов, создана математическая модель для описания этого процесса с использованием программы DosBox и получено кинетическое уравнение для скорости реакции окисления н-пропилмеркаптана молекулярным кислородом:
В программе DosBox методом дифференцирования были рассчитаны константы скорости k для различных концентраций КТК в реакционной массе. На рис. 6 приведена зависимость константы скорости k от квадрата концентрации КТК, которая описывается прямой и свидетельствует о втором порядке реакции по концентрации КТК.
Анализ кинетического уравнения показывает, что для увеличения скорости реакции необходимо повышать концентрацию КТК в реакционной массе и температуру проведения процесса. При концентрации КТК, равной 0.5 мас. %, достигается высокая степень превращения н-пропилмеркаптана и это значение концентрации принято за константу для разработки основ процесса совместного окисления сероводорода и легких меркаптанов.
Повышение температуры выше 50°С не приводит к значительному увеличению скорости реакции окисления. Кроме того, фталоцианиновый катализатор обладает высокой активностью уже при температуре 40°С. Следовательно, температура 50°С является оптимальной для процесса окисления н-пропилмеркаптана молекулярным кислородом в присутствии аммиачного раствора фталоцианина кобальта.
Список литературы
Мазгаров А.М., Вильданов А.Ф., Коробков Ф.А., Комлева Т.И., Хрущева И.К., Набиев А.И. // Экспозиция Нефть Газ. 2015. № 5 (44). С. 71.
Сахабутдинов Р.З., Шаталов А.Н., Гарифуллин Р.М., Шипилов Д.Д., Мухаметгалеев Р.Р. // Нефтяное хозяйство. 2008. № 7. С. 82.
Тыщенко В.А., Федоров И.И., Чернова М.М., Чернова В.М., Беркович К.В., Овчинников К.А., Долганов Р.А., Спиридонова И.В., Занозина И.И. // Технологии нефти и газа. 2017. № 2. С. 14.
Мазгаров А.М., Вильданов А.Ф. // Нефтехимия. 1990. Т. 39. № 5. С. 371.
Аслямов И.Р., Копылов А.Ю., Мазгаров А.М., Вильданов А.Ф., Хрущева И.К., Аюпова Н.Р. // Нефтяное хозяйство. 2008. № 12. С. 93.
Вильданов А.Ф., Аслямов И.Р., Хрущева И.К., Аюпова Н.Р., Мазгаров А.М., Сафиуллина А.К. // Нефтяное хозяйство. 2012. № 11. С. 138.
Мазгаров А.М., Гарифуллин Р.Г., Шакиров Ф.Г., Хрущева И.К., Вильданов А.Ф., Аюпова Н.Р. // Патент РФ № 2272065. Дата публ. 20.03.2006. Б.И. 2006. № 8.
Мазгаров А.М., Фомин В.А. // Нефтехимия. 1979. Т. 19. № 2. С. 244.
Дополнительные материалы отсутствуют.