Нефтехимия, 2020, T. 60, № 4, стр. 556-574
Получение нефтехимического сырья из резиновых отходов методом термического сольволиза
А. И. Юсевич 1, *, Н. Н. Малевич 2, Т. Н. Генарова 3
1 Белорусский государственный технологический университет
220006 Минск, Беларусь
2 ИПУП “Союзнефтехимпроект”
220116 Минск, Беларусь
3 Институт тепло- и массообмена им. А.В. Лыкова НАН Беларуси
220072 Минск, Беларусь
* E-mail: usevich@mail.ru
Поступила в редакцию 25.09.2019
После доработки 27.01.2020
Принята к публикации 11.03.2020
Аннотация
Изучали термическое разложение шинной крошки на основе изопренового каучука в автоклаве в различных средах: толуоле, изопропиловом спирте, воде. В среде толуола достигается наибольшая степень конверсии каучука, а в среде воды – наименьшая. Образование газа минимально в среде воды, максимально – в среде изопропилового спирта, однако выход газообразных продуктов намного меньше, чем в процессах высокотемпературного пиролиза резины. Фракционный состав жидких продуктов варьируется в широких пределах: в среде толуола образуется больше бензиновых фракций, в воде – масляных фракций, в продуктах, полученных в среде изопропилового спирта, преобладают средние дистилляты. В дистиллятных фракциях содержание дипентена и п-цимола, которые могут представлять интерес в качестве исходных веществ для промышленного органического синтеза, доходит до 10–16 мас. %. В масляных фракциях, полученных в среде воды или изопропилового спирта, преобладают ненасыщенные алифатические структуры, в “толуольных” маслах – алкилбензолы. Масляные фракции могут представлять интерес как сырье для получения смазочных и технологических масел. Твердый углеродистый остаток термического сольволиза резины содержит непревращенный технический углерод, а также оксид и сульфид цинка, поэтому может направляться на получение цинка, либо использоваться повторно как наполнитель резины. Для этой статьи приводится также дополнительная информация, рисунки и таблицы в которой, обозначены как Д1, Д2 и т.д.
В мире ежегодно образуется около 12 млн т изношенных автомобильных шин [1]. Их повторное использование позволяет экономить первичное нефтехимическое сырье и имеет важное природоохранное значение. С точки зрения концепции устойчивого развития наиболее целесообразен возврат резиновых отходов в производственный цикл. Однако из-за сложного состава и сшитой структуры резины ее рециклинг представляет собой непростую задачу, эффективное решение которой до сих пор не найдено. Не случайно в Европейском Союзе, где с 2003 г. запрещено складировать отработавшие автомобильные покрышки на полигонах [2], из общего количества ежегодно образующихся утильных шинв среднем сжигается с рекуперацией энергии 48.9%, направляется на измельчение 39.0%, применяется в различных инженерных сооружениях 6.1%, подвергается пиролизу 0.8%, используется в металлургии 0.2% [3].
По причине дорогой переработки резиновые отходы наиболее привлекательны как вторичный энергетический ресурс [3, 4]. Покрышки выгодно сжигать в цементных печах для экономии первичного ископаемого топлива [5]. При этом шинный корд служит источником железа для цементного клинкера. Однако, как было показано в [6], альтернативным топливом, полученным из отходов, включая автомобильные шины, может быть заменено не более 35–40% традиционного топлива без ущерба для качества клинкера. Не следует рассматривать сжигание как перспективный метод утилизации автомобильных покрышек еще и потому, что на их производство тратится 87–115 МДж/кг энергии, в то время как теплотворная способность резины составляет всего около 32 МДж/кг [7].
Как правило, первой стадией переработки изношенных шин является их измельчение [3, 4]. При этом в зависимости от технологии получают либо крошку (гранулят), либо тонкодисперсные порошки (<0.8 мм). Крошку, более дешевую и поэтому более массовую, используют для модификации дорожных битумов и асфальта [8–12], из нее также изготавливают покрытия для спортивных площадок [13, 14]. Резиновые порошки вводят в полимеры [15–17] и бетоны [18, 19]. Однако все эти композиты, как правило, имеют недостатки по сравнению с традиционными материалами, изготовленными из первичных сырьевых компонентов:
– высокую стоимость производства и/или применения;
– худшие или компромиссные свойства;
– спорные санитарно-гигиенические и экологические характеристики. Последнее обстоятельство особенно тормозит развитие рынка шинного гранулята [20].
Следует отметить, что применение дробленых автопокрышек в новых материалах, по существу, не решает задачи рециклинга резины, которая в составе этих материалов рано или поздно попадет в категорию отходов и переработать их будет гораздо сложнее. Только химическая переработка позволит максимально использовать сырьевой потенциал резиновых отходов. Тем не менее, из девяти крупных научных проектов, выполнявшихся за последние годы под эгидой Европейской ассоциации по вторичной переработке шин (ETRA) [21], восемь направлены на создание материалов с применением резиновой крошки или шинного текстиля и лишь один проект посвящен газификации резины с последующим получением новых веществ с высокой добавленной стоимостью [22, 23]. Такая диспропорция, на наш взгляд, свидетельствует о кризисе научных разработок в данной области.
Если говорить о глубокой химической переработке резиновых отходов, то в этом направлении преобладают работы, посвященные высокотемпературному (>400°С) пиролизу шин [24–29]. В большинстве случаев цель пиролиза – получение газообразного и жидкого топлива, т.е., по сути, то же сжигание покрышек, только с промежуточной эндотермической стадией. При этом жидкие продукты пиролиза, как правило, существенно отличаются по составу и свойствам от традиционных нефтяных топлив, имеют высокое содержание полиароматических углеводородов (ПАУ) и гетероциклических соединений, таких как бензотиазол [30, 31]. Как следствие, пирогаз и пирокондесат, полученные из автомобильных шин, можно использовать в качестве энергетического топлива лишь на оптимизированных для их сжигания установках, оборудованных специальной системой очистки отходящих газов от соединений серы и азота, высокодисперсного углерода. О применении продуктов пиролиза резины в качестве транспортного топлива без дополнительной дорогостоящей обработки говорить не приходится [32–35]. Поэтому коммерческая эксплуатация установок пиролиза часто не рентабельна.
Интересным направлением является каталитическая гидроконверсия отработавших автомобильных шин в среде тяжелых нефтяных остатков [36]. Показано, что при совместном гидрокрекинге гудрона и шинной резины в присутствии ультрадисперсных катализаторов на основе Mo, Ni и Co можно получать с достаточно высоким выходом дистиллятные жидкие продукты, характеризующиеся относительно низким содержанием непредельных углеводородов (УВ) и соединений серы. По-видимому, перспективы практического применения этого метода будут зависеть от успехов в разработке высокоэффективных катализаторов, позволяющих существенно снизить выход нерастворимого углеродистого остатка.
Альтернативой пиролизу может служить термический сольволиз резиновых отходов при умеренных температурах (250–400°С) [37–43]. Термодеструкция резины в среде растворителя происходит при меньших температурных градиентах, что исключает перегревы и снижает газообразование. Кроме того, разбавитель подавляет вторичные реакции конденсации, приводящие к твердым продуктам.
Жидкие продукты термолиза характеризуются широким диапазоном температур кипения и могут быть разделены на фракции, аналогичные нефтяным, методом перегонки. Полученные таким образом дистилляты – бензиновые и дизельные фракции – изучались, например, в работе [44] с точки зрения возможности их применения в качестве топлива. Однако, до настоящего времени не уделялось должного внимания термическому сольволизу резины как источнику нефтехимического сырья, потенциал которого, по нашему мнению, достаточно велик. Для того,чтобы отчасти восполнить пробелы в этой теме, мы изучили состав и свойства дистиллятных и остаточных продуктов, полученных в результате термического ожижения резиновых отходов в различных средах.
ЭКСПЕРИМЕНТАЛЬНАЯ ЧАСТЬ
В качестве объекта исследования была выбрана частично девулканизованная резиновая крошка с размером частиц до 1.2 мм, полученная механическим измельчением изношенных автомобильных шин. Природу каучука идентифицировали по ГОСТ 28665 методом ИК-спектрометрии пиролизата на приборе Инфраспек ФСМ 1202. Наличие в спектре продуктов пиролиза диагностических полос поглощения при 1640, 1370, 909, 885, 813 и 800 см–1 позволило установить, что исследуемая резина была изготовлена на основе изопренового каучука.
Термический сольволиз резины проводили в качающемся автоклаве Parr 4923 объемом 250 мл, оснащенном ПИД-регулятором температуры Parr 4843 и пружинным манометром. В качестве растворителей были выбраны вещества различной природы: толуол, изопропиловый спирт (ИПС) и вода. Толуол, являясь ароматическим УВ, способствует набуханию резины, в нем хорошо растворяются жидкие продукты ее термолиза. ИПС не оказывает такого же сильного сольватирующего действия на резину, однако может вступать в химическое взаимодействие с продуктами ее разложения. Вода в отсутствие катализаторов химически инертна по отношению к резине и образующимся продуктам и участвует в процессе скорее как теплоноситель-разбавитель.
В автоклав помещали 60 г резиновой крошки и добавляли равное по массе количество растворителя. Нагрев осуществляли со скоростью 9°С/мин при установке регулятора 340°С. Время термолиза составляло 30 мин; отсчет времени начинали и заканчивали при достижении 300°С в процессе нагрева и охлаждения соответственно. Средняя температура термолиза с учетом неизотермических участков составляла 330°С. Общее давление в автоклаве зависело от давления насыщенных паров растворителя и при достижении заданной температуры составляло 16 МПа для воды, 14 МПа для изопропилового спирта и 5 МПа для толуола. Каждый опыт как минимум дублировался для проверки воспроизводимости условий и результатов.
Образующиеся газообразные продукты пропускали через газовый счетчик барабанного типа ГСБ 400 и анализировали на хроматографе Цвет-800, оснащенном детектором по теплопроводности и стальной насадочной колонкой (3 м × × 4 мм), заполненной цеолитом NaX. Конденсированные продукты экстрагировали толуолом в аппарате Сокслета. От экстракта отгоняли растворитель под вакуумом и получали таким образом жидкие продукты. Их фракционный состав определяли методом имитированной дистилляции по ASTMD 2887 на хроматографе Хроматэк Кристалл 5000.2 (пламенно-ионизационный детектор, капиллярная колонка RestekRtx 2887, газ-носитель – водород). Далее жидкие продукты подвергали перегонке сначала при атмосферном давлении, затем при остаточном давлении 0.5 кПа, отбирая фракции НК–350 и 350–460°C соответственно.
Групповой углеводородный состав фракции ≤350°C (атмосферного дистиллята) изучали методом двумерной хроматографии на приборе AgilentTechnologies 7890A с пламенно-ионизационным детектором и модулятором. Использовали две колонки: неполярная AgilentDB-5MS (30 м × × 0.25 мм × 0.25 мкм) и полярная AgilentINNOWAX (5 м × 0.25 мм × 0.25 мкм). Обработку двумерных хроматограмм осуществляли по программе GCImage. Условия хроматографирования: температура термостата с момента ввода пробы повышали от 50 до 250°C со скоростью 10°C/мин, затем выдерживали в течение 20 мин.
Индивидуальные вещества идентифицировали методом газовой хромато-масс-спектрометрии (ГХ-МС) на приборе Agilent 7890A/5975С, оснащенном капиллярной колонкой HP-5MS (30 м × × 0.25 мм × 0.25 мкм), в режиме ионизации электронным ударом 70 эВ. Условия хроматографирования: температура термостата с момента ввода пробы повышалась от 80 до 300°C со скоростью 10°C/мин, затем выдерживалась в течение 20 мин. Оценочное содержание компонентов получали методом внутренней нормализации без учета эффективности ионизации. Базовые линии при интегрировании хроматографических пиков проводили методом “от впадины к впадине”.
Количественное содержание отдельных компонентов фракции ≤350°C (лимонена, п-цимола, ПАУ) определяли методом газовой хроматографии (ГХ) на приборе AgilentTechnologies 7890A, оснащенном капиллярной колонкой DB-5MS (30 м × 0.25 мм × 0.25 мкм) и пламенно-ионизационным детектором (ПИД). Условия хроматографирования: температура термостата с момента ввода пробы повышали от 50 до 250°C со скоростью 10°C/мин, затем выдерживали в течение 20 мин. Количественный анализ проводили с использованием метода абсолютной калибровки по эталонным растворам.
Плотность (ρ) жидких фракций измеряли по ГОСТ 3900, среднюю молярную массу (M) – методом криоскопии в нафталине.
Для фракции 350–460°C (масляной фракции) определяли элементный состав методом сжигания образцов в автоматическом CHNS-анализаторе VarioEL V2.9; иодное число (ИЧ) – по ГОСТ 2070; показатель преломления $\left( {n_{D}^{{20}}} \right)$ – на рефрактометре ИРФ‑454Б. Спектры ЯМР 1H (400 МГц) и 13C (100 МГц) записывали на приборе Bruker Avance-400, растворитель – дейтерированный хлороформ, внутренний эталон – тетраметилсилан. ИК-спектры дистиллятных и остаточных фракций регистрировали на ИК-Фурье-спектрометре Инфраспек ФСМ 1202 в KBr.
Удельную поверхность (Sуд) твердого углеродистого остатка из аппарата Сокслета измеряли методом низкотемпературной адсорбции азота на приборе NOVA 2200 (Quantachrome Corp.). Элементный анализ осуществляли на волновом рентгенофлуоресцентном спектрометре Axios (PANalytical). Зольность определяли по ГОСТ 11022. Морфологию мелкодисперсных частиц изучали на сканирующем электронном микроскопе JEOL JSM-5610 LV.
РЕЗУЛЬТАТЫ И ИХ ОБСУЖДЕНИЕ
Материальные балансы термического сольволиза шиной крошки в разных средах приведены в табл. 1.
Таблица 1.
Материальный баланс термического сольволиза шинной крошки
Среда | Выход продуктов, мас. % | Состав газообразных продуктов, об. % | Потенциальное содержание фракций в жидких продуктах*, мас. % | ||||||||||||||||
---|---|---|---|---|---|---|---|---|---|---|---|---|---|---|---|---|---|---|---|
газообразных | жидких | твердых | сумма | H2 | CH4 | C2H4 | C2H6 | C3H6 | C3H8 | C4H8 | C4H10 | C5H12 | CO | CO2 | I | II | III | IV | |
Толуол | 1.5 | 50.7 | 37.7 | 89.9 | 5.9 | 41.2 | 8.6 | 19.3 | 3.7 | 6.3 | 1.8 | 1.9 | 0.4 | 4.5 | 6.4 | 11.0 | 51.2 | 33.9 | 3.9 |
ИПС | 5.1 | 63.0 | 36.6 | 104.7 | 4.3 | 10.6 | 11.9 | 11.6 | 43.6 | 8.9 | 1.5 | 2.6 | 0.7 | 0.6 | 3.7 | 8.2 | 43.3 | 40.2 | 8.3 |
Вода | 0.5 | 58.2 | 40.7 | 99.4 | 17.7 | 32.6 | 1.9 | 2.7 | 1.0 | 3.0 | 0.8 | 1.4 | 0.2 | 8.8 | 29.9 | 5.2 | 31.2 | 52.7 | 10.9 |
Среда – толуол. Выход газообразных продуктов составил 13.4 мл (н. у.) на 1 г резины. В газе преобладали УВ, причем метана было примерно столько же, сколько остальных углеводородных компонентов, вместе взятых. Суммарное содержание алканов – 69.1 об. %, алкенов – 14.1 об. %. Помимо УВ были обнаружены также водород и оксиды углерода. Наиболее вероятным путем образования УВ С1–С3 является деалкилирование замещенных аренов, идентифицированных в жидких фракциях (см. ниже). Углеводороды С4+ могут образовываться непосредственно в результате расщепления макромолекул каучука. Молекулярный водород, очевидно, выделяется при протекании реакций дегидрирования. Наиболее легко дегидрируются частично ненасыщенные циклические структуры, которые формируются в результате замыкания цепей макрорадикалов – первичных продуктов деструкции полиизопрена. Оксиды углерода, по-видимому, образуются при деоксигенации компонентов резины, содержащих карбоксильные группы: стеариновой кислоты, канифоли, фталевого ангидрида, которые могут входить в рецептуру резины в количествах до 2.0, 1.1 и 0.25 мас. % соответственно [45].
Жидкие продукты удобно представить совокупностью следующих фракций: бензина, легкого и тяжелого газойлей, остатка (табл. 1). При определении количества этих фракций следует учесть, что наиболее летучие продукты могут отгоняться вместе с растворителем от экстрактного раствора, полученного в аппарате Сокслета. Этим, в частности, объясняются 10.1 мас. % потерь в материальном балансе термолиза шинной крошки в толуоле. По-видимому, их следует добавить к бензиновой фракции и увеличить выход жидких продуктов, приведенный в табл. 1, до 60.8 мас. %. Тогда скорректированное содержание целевых фракций составит: I – 25.8, II – 42.7, III – 28.3, IV – 3.2 мас. %. Таким образом, 68.5 мас. % жидких продуктов, полученных из резины в среде толуола, выкипают до 350°С и относятся к так называемым атмосферным дистиллятам, которые в нефтепереработке служат основой моторных топлив и источником нефтехимического сырья.
Выходы атмосферных дистиллятов, полученные при перегонке жидких продуктов в лабораторных условиях, показаны в табл. 2. Там же представлены их физико-химические свойства и групповой состав, определенный по двумерным хроматограммам. Сами хроматограммы приведены в приложении к статье (рис. Д1).
Таблица 2.
Выход, свойства и групповой состав фракций НК–350°С жидких продуктов термолиза резиновой крошки
Среда термолиза | Выход фракции (в расчете на жидкие продукты), мас. % | ρ, кг/м3 | M, г/моль | Содержание, мас. % | ||
---|---|---|---|---|---|---|
алифатических углеводородов | ароматических углеводородов | гетероорганических соединений | ||||
Толуол | 53.0 | 894.7 | 186.3 | 43.7 | 55.2 | 1.1 |
ИПС | 39.1 | 886.2 | 194.0 | 77.5 | 21.0 | 1.5 |
Вода | 24.6 | 882.5 | 205.6 | 66.5 | 32.3 | 1.2 |
Как следует из данных табл. 2, фактический выход атмосферного дистиллята в опыте с толуолом составил 85.2% от потенциального содержания фракции ≤350°С в жидких продуктах. Его плотность оказалась максимальной, а средняя молярная масса – минимальной среди сравниваемых образцов. Также дистиллят “толуольного” опыта характеризуется наибольшим содержанием аренов и наименьшим содержанием алифатических УВ. Концентрация гетеросоединений невелика. Очевидно, это продукты химических превращений неуглеводородных ингредиентов: ускорителей вулканизации, стабилизаторов, пластификаторов и пр., – суммарная концентрация которых в резиновой смеси может варьироваться от 1.5 до 4 мас. % [45].
Ряд веществ в составе атмосферных дистиллятов был идентифицирован методом газовой хромато-масс-спектрометрии (табл. Д1).
На основании данных, представленных в табл. Д1, можно сделать вывод, что в среде толуола основным продуктом термохимических превращений изопренового каучука является п-цимол, который, по-видимому, образуется через стадию лимонена (рис. 1):
Кроме цимолов были обнаружены другие алкилбензолы (5.22 хромат. %) с числом заместителей от 1 до 3 и длиной алкильных радикалов от 1 до 4 атомов углерода. Полициклические УВ представлены производными индена (7.02 хромат. %), нафталина (8.35 хромат. %), флуорена (0.94 хромат. %), фенантрена (1.76 хромат. %) преимущественно с метильными заместителями в ядре. Были найдены также насыщенные (3,7,7-триметилбицикло[4.1.0]гептан) и неконденсированные (2-метилбифенил) полициклические структуры. Все это – продукты деструкции полиизопрена.
Наличие парафиновых УВ – гептадекана и нонадекана – объясняется декарбоксилированием высших жирных кислот, входящих в состав стеарина. Другими продуктами превращения вспомогательных компонентов резины являются бензотиазол, N-фенил-2-нафтиламин, нитрилы пальмитиновой и стеариновой кислот. Бензотиазол, очевидно, образовался в результате разложения сульфенамидного ускорителя вулканизации, фенилнафтиламин – из фенилендиаминного антиоксиданта. Карбоновые кислоты в процессе вулканизации резины вступают во взаимодействие с бензотиазолсульфенамидами и могут давать амиды кислот, которые в условиях термолиза способны дегидратироваться до нитрилов.
Следует отметить, что данные ГХ-МС, представленные в табл. Д1, позволяют сравнить состав продуктов термолиза, проведенного в различных средах, однако не являются точной оценкой содержания отдельных веществ в дистиллятных фракциях. Поэтому дополнительно были количественно определены основные компоненты атмосферных дистиллятов – лимонен и п-цимол – по данным ГХ с ПИД методом абсолютной калибровки. Таким же образом было установлено содержание 10 незамещенных полициклических ароматических УВ (ПАУ). Идентификацию веществ осуществляли по совпадению времен удерживания со стандартными образцами. Результаты количественного анализа представлены в табл. 3.
Из табл. 3 можно видеть, что соотношения концентраций лимонена и п-цимола, как внутри исследуемых образцов, так и между образцами, хорошо согласуются с данными табл. Д1.
Таблица 3.
Содержание (в мг/г) лимонена, п-цимола и ПАУ во фракциях ≤350°С жидких продуктов термического сольволиза шинной крошки
Вещество | Среда термолиза | ||
---|---|---|---|
толуол | ИПС | вода | |
Лимонен | 0.0 | 146.7 | 21.5 |
п-Цимол | 103.9 | 2.1 | 82.7 |
Нафталин | 1.10 | 0.23 | 0.94 |
Аценафтилен | 0.13 | 0.02 | 0.11 |
Аценафтен | 0.79 | 0.34 | 0.03 |
Флуорен | 0.11 | 0.07 | 0.10 |
Фенантрен | 0.02 | 0.19 | 0.01 |
Антрацен | 0.57 | 0.12 | 0.65 |
Флуорантен | 0.04 | 0.04 | 0.02 |
Пирен | 0.01 | 0.07 | 0.06 |
Бензо[a]антрацен | 0.03 | 0.007 | 0.03 |
Хризен | 0.02 | 0.007 | 0.03 |
Сумма ПАУ без нафталина | 1.72 | 0.864 | 1.04 |
В атмосферном дистилляте, отогнанном из продуктов термолиза в среде толуола, содержание п-цимола превышает 10 мас. %, что делает целесообразным его выделение. Содержание голоядерных конденсированных полиароматических УВ в этом образце наибольшее среди образцов сравнения, но не превышает 0.3 мас. %. При этом по числу колец ПАУ распределились следующим образом (мас. %): бициклических (нафталина) – 39.0; трициклических – 57.4; тетрациклических – 3.6.
При перегонке жидких продуктов под вакуумом удалось выделить без термической деструкции фракцию 350–460°С тяжелого газойля, названную нами масляной фракцией. Она также представляет интерес как нефтехимическое сырье. В табл. 4 приведены свойства масляных фракций, полученных при термолизе в разных средах: образец 1 – в толуоле; образец 2 – в ИПС; образец 3 – в воде. Их плотности, показатели преломления и йодные числа имеют высокие значения, что наводит на мысль о большом содержании ненасыщенных полициклических структур. При этом у “толуольного” масла плотность и показатель преломления наибольшие, а иодное число наименьшее среди сравниваемых образцов. Кроме того, продукт, полученный в среде толуола, характеризуется наибольшим отношением углерода к водороду. Для более детального изучения строения веществ масляных фракций был проведен их структурно-групповой анализ, результаты которого представлены ниже.
Таблица 4.
Свойства масляных фракций, выделенных из жидких продуктов термического сольволиза шинной крошки в среде толуола (образец 1), ИПС (образец 2) и воды (образец 3)
Образец | Выход (в расчете на жидкие продукты), мас. % | Физико-химические свойства | Элементный состав, мас. % | |||||||
---|---|---|---|---|---|---|---|---|---|---|
ρ, кг/м3 | M, г/моль | $n_{D}^{{20}}$ | ИЧ, г I2/100 г | C | H | S | N | O | ||
1 | 16.5 | 973.1 | 301.0 | 1.5458 | 19.2 | 87.01 | 11.51 | 0.59 | 0.50 | 0.39 |
2 | 22.5 | 959.1 | 296.2 | 1.5325 | 39.9 | 86.40 | 11.79 | 0.71 | 0.32 | 0.78 |
3 | 19.8 | 936.9 | 314.9 | 1.5163 | 44.8 | 85.55 | 11.68 | 0.62 | 0.09 | 2.06 |
И-20А* | – | 879.3 | 316.2 | 1.4850 | – | 86.66 | 12.81 | 0.46 | 0.00 | 0.07 |
В табл. 5 приведена характеристика нерастворимых в толуоле твердых продуктов термического сольволиза шинной крошки. Их основу составляет непревращенный компонент резины – технический углерод. Содержание технического углерода в резиновых смесях может достигать 35 мас. % [45], что, в совокупности с прочими нерастворимыми ингредиентами (оксид цинка, минеральные наполнители), дает значение, близкое к выходам твердого остатка, приведенным в табл. 1, и дает основание полагать, что основная масса каучука в процессе термического сольволиза переходит в жидкие продукты. Доля углеродистой части в твердых образцах варьируется от 84.5 до 87.1 мас. %. Помимо сажи в ее состав могут входить высокомолекулярные продукты термических превращений каучука и углеводородные радикалы солей карбоновых кислот.
Таблица 5.
Характеристика твердых продуктов термического сольволиза шинной крошки
Среда | Sуд, м2/г | Зольность, мас. % | Содержание элементов, мас. % | |||||||||||
---|---|---|---|---|---|---|---|---|---|---|---|---|---|---|
O | Mg | Al | Si | S | Cl | K | Ca | Ti | Fe | Zn | ∑ | |||
Толуол | 38 | 15.3 | 1.16 | 0.13 | 0.44 | 0.88 | 3.02 | 0.49 | 0.09 | 1.93 | 0.10 | 0.22 | 7.30 | 15.77 |
ИПС | 42 | 15.5 | 1.11 | 0.14 | 0.45 | 0.85 | 2.91 | 0.23 | 0.08 | 1.82 | 0.11 | 0.21 | 7.60 | 15.53 |
Вода | 14 | 13.3 | 0.90 | 0.13 | 0.42 | 0.79 | 2.27 | 0.08 | 0.06 | 1.28 | 0.08 | 0.18 | 6.71 | 12.90 |
Среди прочих обнаруженных в твердых продуктах элементов преобладают цинк, кальций, сера и кислород. Судя по соотношению элементов, металлы присутствуют главным образом в виде сульфидов и оксидов. Оксид цинка как активатор вулканизации вводится в резиновые смеси в количестве от 2 до 3.5 мас. % [45], что соответствует зафиксированным нами концентрациям цинка в углеродистых остатках (табл. 5). Кальций, по-видимому, попал в твердые продукты термического сольволиза в составе мела, который наряду с техуглеродом вводится в резиновые смеси в качестве наполнителя в количестве от 5 до 20 мас. ч. на 100 мас. ч. каучука [45].
Твердый остаток, полученный в среде толуола, имеет достаточно высокую удельную поверхность, на уровне технического углерода марки N683 по ASTMD1765. Он может быть пригоден для повторного использования в резине в качестве наполнителя. Для этого надо изучить влияние зольных компонентов остатка на процесс вулканизации и физико-механические свойства резиновых вулканизатов.
Среда – изопропиловый спирт. При термолизе шинной крошки в ИПС выходы газообразных и жидких продуктов были наибольшими, а количество твердого остатка – наименьшим среди всех опытов (табл. 1).
Выход газа составил 32.0 мл/г (н. у.). Основным его компонентом был пропилен, который может образовываться не только при деструкции каучука, но и в результате дегидратации ИПС. Всего в газе содержалось 57.0 об. % алкенов и 34.4 об. % алканов. Алканы на 90% состояли из трех гомологов: метана, этана и пропана, концентрации которых были близки между собой. Следует также отметить низкое содержание монооксида углерода. Его было в 6 раз меньше, чем диоксида углерода. Концентрация водорода в газе была не намного меньше, чем в опыте с толуолом.
Суммарное количество собранных продуктов термолиза превысило100 мас. % от загрузки сырья. Это говорит о вкладе растворителя в расходную часть материального баланса. Если предположить, что весь пропилен образовался из ИПС, и вычесть его долю (2.6 мас. %) из выхода продуктов, их количество все равно будет превышать массу взятого сырья. На основании этого можно заключить, что изопропиловый спирт не только дает газообразные продукты, но и участвует в синтезе веществ, входящих в жидкие фракции. Например, он выступает как алкилирующий агент для ароматических структур.
Сравним жидкие продукты, полученные в среде ИПС и толуола. В опыте с изопропиловым спиртом они содержат меньше бензина и легкого газойля (табл. 1). Атмосферные дистилляты имеют меньшую плотность, бóльшую молярную массу (табл. 2) и более простой состав по числу веществ, как можно видеть из двумерных хроматограмм, приведенных в дополнительной информации на рис. Д1. Судя по данным хромато-масс-спектрометрии (табл. Д1), во фракции, выкипающей до 350°С, преобладают алифатические УВ. Основным компонентом является лимонен. Присутствует также его бициклический изомер – карен. В совокупности они занимают 39.57% площади хроматограммы. В то же время содержание продуктов дегидрирования лимонена – п-цимола и 1-метил-4-(1-метилвинил)бензола – составляет всего 2.15 хромат. %. Очевидно, ИПС как донор водорода препятствует ароматизации первично образующихся циклических структур. Среди прочих ароматических УВ были идентифицированы три гомолога бензола (2.18 хромат. %), один гомолог индена (2.59 хромат. %), два гомолога нафталина (1.78 хромат. %) и четыре производных фенантрена (1.77 хромат. %), приведенные в табл. Д1. Видно, что количество моно- и бициклических аренов меньше, чем в аналогичной фракции, полученной в среде толуола, однако содержание веществ с фенантреновой структурой практически одинаковое. Еще одной особенностью является большое количество продуктов превращения карбоновых кислот: были обнаружены парафины от ундекана до нонадекана (3.92 хромат. %), октадеканнитрил, а также не встречавшиеся в других опытах изопропиловые эфиры пальмитиновой и стеариновой кислот (2.28 хромат. %). Очевидно, что в образовании эфиров участвовал изопропиловый спирт.
Согласно данным табл. 3, концентрация лимонена во фракции ≤350°С продуктов термолиза, проведенного в среде ИПС, составляет 14.7 мас. %, что дает его выход в размере 3.6 мас. % в расчете на загруженную резину и находится на уровне лучших результатов, достигнутых при термохимической переработке шин [25]. Содержание незамещенных ПАУ в атмосферном дистилляте наименьшее среди сопоставляемых образцов (0.11 мас. %), причем 21.0 мас. % от этого количества приходится на нафталин, 67.7 мас. % – на трициклические и 11.3 мас. % – на тетрациклические конденсированные арены.
Масляная фракция, выделенная из продуктов термоожижения резины в среде ИПС (образец 2, табл. 4), имеет меньшие значения средней молекулярной массы, плотности и показателя преломления, но гораздо большее йодное число по сравнению с “толуольным” маслом (образец 1). Отношение углерода к водороду у “изопропанольного” масла ниже, чем у аналогичного продукта, полученного в среде толуола.
Твердые продукты опытов с ИПС и толуолом близки по содержанию золы и элементному составу (табл. 5). При этом углеродистый остаток термического сольволиза шинной крошки изопропиловым спиртом имеет самую большую удельную поверхность, что говорит о его высокой дисперсности. Это может обеспечить хорошие усиливающие свойства материала при использовании его в качестве наполнителя полимеров.
Среда – вода. Термолиз шинной крошки в водной среде сопровождался весьма небольшим газообразованием: 3.9 мл/г (н. у.). При этом суммарный выход продуктов был близок к 100 мас. % (табл. 1). Основными компонентами газа были оксиды углерода, метан и водород. Высокое содержание водорода и оксидов углерода говорит о протекании реакций окислительной конверсии углеводородов с участием воды.
Жидких продуктов получилось меньше, чем в других опытах (табл. 1). Однако в процессе их выделения потери были не так велики, как в опыте с толуолом, а сам растворитель не расходовался при термолизе, как в случае с изопропиловым спиртом. Содержание бензина и легкого газойля в жидких продуктах также оказалось наименьшим. Отбор атмосферного дистиллята при перегонке жидких продуктов составил 67% от потенциала, его плотность была минимальной, а молярная масса – максимальной среди сопоставляемых образцов (табл. 2). Из двумерных хроматограмм, представленных в дополнительной информации (рис. Д1), следует, что состав фракции НК–350°С, полученной в среде воды, несколько проще, чем у соответствующей фракции, образовавшейся в среде толуола, но сложнее, чем у продуктов, полученных с применением ИПС. Среди групповых компонентов преобладают алифатические углеводороды, но их массовая доля меньше, чем в продукте “изопропанольного” опыта (табл. 2). Среди индивидуальных компонентов, идентифицированных методом хромато-масс-спектрометрии (табл. Д1), основным является п-цимол (21.07 хромат. %), хотя великоостаточное содержание первичных продуктов деструкции полиизопрена – лимонена и 2‑карена (6.74 хромат. %). В качестве особенности следует отметить большое количество алкенильных производных бензола, а также наличие частично ненасыщенных полициклических структур: дигидроиндена, тетралина и 10,18-биснорабиета-8,11,13-триена. Конденсированные арены представлены метильными и изопропильными производными нафталина (3.69 хромат. %), в то время как три и тетрациклические структуры методом ГХ-МС идентифицировать не удалось. Отсутствовали также нитрилы карбоновых кислот. Очевидно, их образованию из амидов препятствовал избыток воды, а сами амиды гидролизовались до карбоновых кислот, одна из которых, пальмитиновая, была идентифицирована. Продуктами разложения ускорителей вулканизации и антиоксидантов могут быть циклогексанон и анилин. Обнаружена также бензойная кислота.
Массовые доли п-цимола и лимонена в атмосферном дистилляте составили, соответственно, 8.3 и 2.2% (табл. 3), что в сумме равно содержанию п-цимола в дистилляте “толуольного” опыта. По-видимому, варьируя температуру и продолжительность термолиза полиизопреновой резины в водной среде, можно регулировать соотношение этих двух компонентов в продуктах.
Три- и тетрациклические конденсированные арены наряду с нафталином были обнаружены в атмосферном дистилляте опыта с водой методом ГХ с ПИД путем сопоставления с хроматограммами стандартных образцов. Суммарное содержание полициклоаренов составило 0.2 мас. %, что больше, чем в опыте с ИПС, но меньше, чем в опыте с водой (табл. 3). Среди ПАУ нафталин и трициклические арены представлены практически поровну – 47.5 и 45.4 мас. % соответственно; на долю тетрациклических структур приходится 7.1 мас. %.
Масляная фракция (образец 3, табл. 4) характеризуется наибольшими значениями средней молекулярной массы и иодного числа среди сравниваемых продуктов, но имеет самую низкую плотность и показатель преломления. Отношение углерода к водороду в ней почти такое же, как в масляной фракции, полученной в среде ИПС, однако велико содержание кислорода.
При термолизе шинной крошки в воде образовалось больше твердого продукта, чем в остальных случаях (табл. 1). Это означает, что больше непревращенного вещества резины осталось на поверхности технического углерода. Следствием явилась меньшая зольность углеродистого остатка и малая удельная поверхность его частиц (табл. 5), которые оказались склеенными в агрегаты (рис. 2). Последнее обстоятельство делает продукт непригодным для повторного использования в качестве наполнителя полимеров. С другой стороны, высокое содержание соединений цинка и других металлов, распределенных в углеродной матрице, может обусловить каталитические свойства материала по отношению к органическим реакциям. По-видимому, это вопрос требует отдельного изучения.
Рис. 2.
Микрофотографии углеродистого остатка термического сольволиза резиновой крошки в среде толуола (слева) и воды (справа).
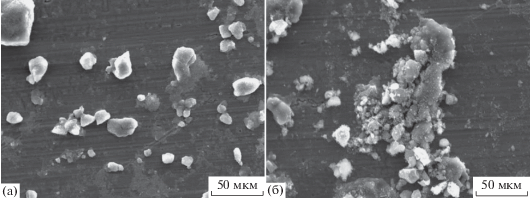
Структурно-групповой анализ масляных фракций. Высококипящие фракции жидких продуктов термического сольволиза резины состоят из “гибридных” молекул, содержащих в соизмеримых долях фрагменты УВ разных классов. Поэтому для характеристики состава масляных фракций (вакуумных дистиллятов) был применен метод структурно-группового анализа. Параметры “средних” молекул оценивали на основании данных 1H и 13C ЯМР-спектроскопии (табл. Д2) по модифицированной нами методике, первоначально опубликованной в [46].
Согласно результатам структурно-группового анализа (табл. Д2) в масляных фракциях преобладают парафино-нафтеновые структуры (CPN). Доля олефиновых фрагментов (COL) невелика, причем в молекулах образца 3 она наибольшая, а в молекулах образца 1 – наименьшая. Это хорошо согласуется с результатами измерения иодных чисел (табл. 4).
Содержание ароматических структур (CAr) в образце 1 выше, чем в образцах 2 и 3. При этом, судя по числу атомов ароматического углерода в “средней” молекуле (#CAr), вероятность существования в масляных фракциях соединений с конденсированными ароматическими фрагментами низка. Так, молекулы “толуольного” масла имеют в основном одно бензольное кольцо (RAr) с двумя-тремя алифатическими заместителями (#S/ring), каждый из которых может включать от 6 до 8 атомов углерода (n).
Среднее число бензольных колец в молекулах образцов 2 и 3 меньше единицы. Это значит, что в маслах, полученных в среде ИПС или воды, присутствуют и полностью алифатические соединения. Их доля может быть оценена как (1 – RAr) × 100%, т.е. 37% в образце 2 и 30% в образце 3. Производные бензола, в свою очередь, имеют в среднем по 3–4 заместителя с 4–5 атомами углерода в каждом.
Таким образом, данные структурно-группового анализа не подтверждают высказанное выше предположение о том, что высокие показатели преломления масляных фракций обусловлены большим содержанием в них полиароматических соединений. По-видимому, основной причиной является значительное присутствие в продуктах изопреноидных структур, показатель преломления которых превышает 1.5.
Для уточнения химического строения молекул дистиллятных масляных фракций и остатков вакуумной перегонки снимали их ИК-спектры (рис. 3). Отнесение полос колебаний проводили по [47]. Интенсивности полос и спектральные коэффициенты, рассчитанные на их основе, приведены в дополнительной информации в табл. Д3.
Рис. 3.
Фрагменты ИК-спектров фракций жидких продуктов термического сольволиза резиновой крошки: а – образец 1; б – образец 2; в – образец 3; г – образец 4; д – образец 5; е – образец 6.
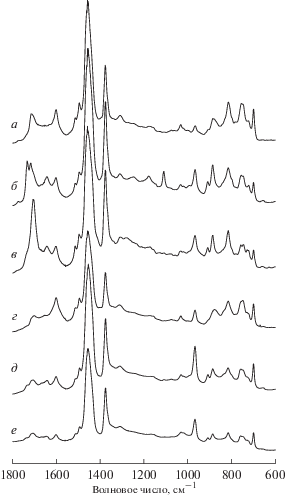
По высоте пика при 1600 см–1 можно судить об общем содержании ароматических структур в образце. Из данных табл. Д3 следует, что образец 1 имеет наибольшую ароматичность, а образец 2 – наименьшую, хотя и близок по этому показателю к образцу 3. Это хорошо согласуется с данными ЯМР. Примечательно, что в случае опыта с толуолом остаток от перегонки (образец 4) характеризуется большей ароматичностью, чем соответствующий масляный дистиллят. В то же время остаточные фракции, полученные в среде ИПС (образец 5) и воды (образец 6), содержат меньше ароматических углеводородов, чем отогнанные от них масла.
В области 699–868 см–1 проявляются колебания связей C–H в ароматических кольцах с разной степенью замещения. Наиболее интенсивной на спектрах масляных фракций является полоса пара-дизамещенных бензолов (814 см–1). орто-Дизамещенные арены обнаруживаются в виде расщепленного пика с вершинами при 746 и 756 см–1. Расщепление, вероятно, обусловлено наличием в смеси энергетически неэквивалентных структур: 1,2-диалкилбензолов и производных тетралина – в сопоставимых количествах. Следует также отметить достаточно интенсивную узкую полосу моноалкилбензолов при 699 см–1. В то же время три-, тетра- и пентазамещенные арены, имея невысокие коэффициенты удельного поглощения, проявляются в виде плеч по обе стороны пика при 814 см–1. Полоса колебаний трех соседних атомов водорода (780 см–1) имеет наименьшую интенсивность, указывая на низкое содержание мета-диалкилбензолов.
Спектральные коэффициенты A1 и A2 (табл. Д3) позволяют сопоставить образцы по степени замещенности ароматических структур. Так, образец масел, полученный в водной среде, имеет наибольшую долю дизамещенных ядер (A1), а по относительному содержанию полизамещенных ароматических фрагментов (A2) близок к маслам, полученным в среде ИПС. Молекулы масляной фракции, выделенной из продуктов термолиза резины в среде толуола, напротив, имеют наименьшее число заместителей в бензольном кольце. Интересно, что при сопоставлении остаточных фракций наблюдается противоположная закономерность. При этом спектральный коэффициент B, пропорциональный степени разветвленности алкилов, для продуктов “толуольного” опыта, как дистиллятных так и остаточных, значительно меньше, чем для продуктов двух других опытов.
Олефиновые структуры представлены в молекулах исследуемых фракций транс-алкениленовыми (966 см–1), концевыми винилиденовыми (886 см–1) и незамещенными винильными (909 см–1) группами. Термодинамически более устойчивые транс-алкениленовые группировки формируются, вероятно, в результате изомеризации цис-1,4-полиизопреновых фрагментов при термодеструкции макромолекул каучука. Винилиденовые группы могут получаться в результате разложения третичных радикалов по схеме, аналогичной представленной на рис. 1. Винильные группы, по-видимому, являются продуктом диспропорционирования концевых радикалов, образующихся при разрыве полимерной цепи.
ИК-спектр дистиллятного образца 1 характеризуется меньшей интенсивностью олефиновых пиков по сравнению со спектрами образцов 2 и 3 (табл. Д3), что вполне соответствует данным иодометрии и ЯМР-спектроскопии. Вместе с тем новую информацию можно получить, анализируя значения спектрального коэффициента C. Исходя из сделанных выше предположений о механизме образования олефиновых фрагментов в процессе термодеструкции каучука, этот коэффициент можно рассматривать как характеристику степени развития вторичных процессов превращения первичных продуктов разложения полиизопрена, в том числе их циклизации. Значение коэффициента C наиболее велико для образца 1, и в целом для дистиллятных фракций оно выше, чем для остаточных, хотя остаточный образец 4 (“толуольный”) весьма близок по этому показателю к дистиллятному образцу 3 (“водяному”). Наименьшее значение коэффициента C наблюдается у образцов 5 и 6. Таким образом, можно сделать вывод, что при термообработке шинной крошки в среде толуола вторичные превращения протекают наиболее глубоко, не только определяя структуру низкомолекулярных продуктов, но и оказывая существенное влияние на строение высокомолекулярных остаточных фракций. В то же время высококипящие остатки от перегонки жидких продуктов термолиза, полученных в среде ИПС или воды, содержат главным образом фрагменты исходных полимерных цепей, сохранившие в большой степени первоначальную структуру молекул каучука.
Следует также обратить внимание на полосы карбоксильных групп (1702–1733 см–1). В “толуольных” и “водяных” продуктах они принадлежат свободным карбоновым кислотам, тогда как в образцах, полученных в среде ИПС, наряду с кислотами присутствуют сложные эфиры, подтверждая выводы о химическом взаимодействии изопропилового спирта с компонентами резины в процессе термолиза. Также из приведенных ИК-спектров видно, что по сравнению с остаточными фракциями дистиллятные масла содержат больше карбоксильных соединений. Вместе с тем, сигналы углерода, связанного с кислородом, на спектрах 13C ЯМР малы (табл. Д2), свидетельствуя о низкой концентрации карбоновых кислот и их производных в маслах. Вероятно, большая часть стеариновой кислоты остается в твердом продукте термолиза в виде солей.
ЗАКЛЮЧЕНИЕ
Термический сольволиз резиновых отходов позволяет получать с высоким выходом вещества, которые могут представлять интерес в качестве сырья для нефтехимического синтеза. При этом, регулируя сольватирующую способность, окислительно-восстановительные свойства среды и термобарические условия процесса путем подбора растворителя, можно варьировать в широких пределах состав продуктов. Так, при термолизе резины на основе изопренового каучука в среде изопропилового спирта образуется в больших количествах лимонен (дипентен), который можно использовать непосредственно в качестве мономера при синтезе новых полимеров, превратить в изопрен (рециклинг), направить на получение душистых веществ, флотореагентов либо использовать как растворитель для лаков и смол. При термолизе этой же резины в среде толуола образуется значительное количество п-цимола, который является исходным веществом для синтеза п-крезола и ацетона, а также мономера – гомолога α-метилстирола. Масляные фракции жидких продуктов термического сольволиза резины в ИПС, воде или толуоле имеют разное соотношение алифатических соединений и алкилбензолов, но характеризуются низким содержанием полициклических ароматических УВ и после гидрооблагораживания могут найти применение в качестве компонентов смазочных масел либо технологических масел различного назначения. Остатки от вакуумной перегонки жидких продуктов термического сольволиза резины можно использовать в качестве заменителей нефтеполимерных и каменноугольных инден-кумароновых смол. Твердый углеродистый остаток термического сольволиза в зависимости от того, в какой среде он был получен, можно использовать в качестве наполнителя полимерных композиционных материалов либо направлять на выделение цинка и получение углеродных адсорбентов.
Список литературы
Bureau of International Recycling (BIR) Annual Report 2014. Режим доступа http://www.bir.org/assets/Documents/publications/Annual-Reports/BIR-Annual-Report-revised-062015-UK.pdf. Дата доступа 26.08.2019.
Council Directive 1999/31/EC of 26 April 1999 on the landfill of waste. Режим доступа http://eur-lex.europa.eu/legal-content/EN/TXT/?uri=CELEX:31999L0031. Дата доступа 26.08.2019.
The 2015 edition of ETRMA’s End-of-life Tyres Management report. Режим доступа http://www.etrma.org/uploads/Modules/Documentsmanager/elt-report-v9a—final.pdf. Дата доступа 26.08.2019.
2017 U.S. Scrap Tire Management Summary. Режим доступа https://www.ustires.org/system/files/USTMA_scraptire_summ_2017_072018.pdf. Дата доступа 26.08.2019.
Morton A. Barlaz, William E. Eleazer II, Daniel J. Whittle // Waste Management & Research. 1993. Vol. 11. № 6. P. 463.
Бернадинер И.М., Александрова Е.Ю. // Вестник Пермского национального исследовательского политехнического университета. Прикладная экология. Урбанистика. 2018. № 2. С. 47.
Sienkiewicz M., Kucinska-Lipka J., Janik H., Balas A. // Waste Management. 2012. V. 32. P. 1742.
Sienkiewicz M., Borzędowska-Labuda K., Wojtkiewicz A., Janik H. // Fuel Processing Technology. 2017. V. 159. P. 272.
Vega-ZamanilloÁ., Lastra-González P., Calzada-Pérez M. A., Castro-Fresno D., Teijón-López-Zuazo E. // Transportation Research Procedia. 2018. V. 33. P. 91.
Liu G., Liang Y., Chen H., Wang H., Komacka J., Gu X. // Construction and Building Materials. 2019. V. 210. P. 555.
Pszczoła M., Jaczewski M., Szydłowski C., Judycki J., Dołżycki B. // Procedia Engineering. 2017. V. 172. P. 897.
Agudelo G., Cifuentes S., Colorado H. A. // J. of Cleaner Production. 2019. V. 228. P. 1048.
Bocca B., Forte G., Petrucci F., Costantini S., Izzo P. // Science of тhe Total Environment. 2009. V. 407. № 7. P. 2183.
Li X., Berger W., Musante C., Incorvia Mattina M.J. // Chemosphere. 2010. V. 80. № 3. P. 279.
Sienkiewicz M., Janik H., Borzędowska-Labuda K., Kucińska-Lipka J. // J. of Cleaner Production. 2017. V. 147. P. 560.
Ramarad S., Khalid M., Ratnam C.T., LuqmanChuah A., Rashmi W. // Progress in Materials Science. 2015. V. 72. P. 100.
Aoudia K., Azem S., AïtHocine N., Gratton M., Pettarin V., Seghar S. // Waste Management. 2017. V. 60. P. 471.
Li Y., Zhang Sh., Wang R., Dang F. // Construction and Building Materials. 2019. V. 225. P. 1183.
Strukar K., Kalman Šipoš T., Miličević I., Bušić R. // Engineering Structures. 2019. V. 188. P. 452.
Bureau of International Recycling (BIR) Annual Report 2016. Режим доступа http://www.bir.org/assets/Documents/publications/Annual-Reports/BIR-Annual-Report-2016-UK-WEB.pdf. Дата доступа 26.08.2019.
European Tyre Recycling Association. Режим доступа https://www.etra-eu.org/projects. Дата доступа 26.08.2019.
Karatas H., Olgun H., Engin B., Akgun F. // Fuel. 2013. V. 105. P. 566.
Károly Z., Mohai I., Klébert Sz., Keszler A., Sajó I.E., Szépvölgyi J. // Powder Technology. 2011. V. 214. P. 300.
Martínez J.D., Puy N., Murillo R., García T., Navarro M.V., Mastral A.M. // Renewable and Sustainable Energy Reviews. 2013. V. 23. P. 179.
Ульянов В.В., Кошелев М.М., Харчук С.Е., Гулевский В.А., Тимочкин А.В. // Нефтехимия. 2018. Т. 58. № 1. С. 72 [Petrol. Chemistry. 2018. V. 58. № 1. P. 68].
Ding K., Zhong Zh.,Zhang Bo, Wang Jia, Min A., Rua R. // J. of Analytical and Applied Pyrolysis. 2016. V. 122. P. 55.
Lopez G., Alvarez J., Amutio M., Mkhize N.M., Danon B., van der Gryp P., Görgens J.F., Bilbao J., Olazar M. // Energy Conversion and Management. 2017. V. 142. P. 523.
Lewandowski W.M., Januszewicz K., Kosakowski W. // J. of Analytical and Applied Pyrolysis. 2019. V. 140. P. 25.
Okoro E.E., Sanni S.E., Emetere M.E., Orodu D.O. // Procedia Manufacturing. 2019. V. 35. P. 847.
Wang W., Chang J., Cai L., Shi Sh.Q. // Waste Management. 2014. V. 34. № 12. P. 2603.
Mkhize N.M., Danon B., van der Gryp P., Görgens J.F. // J. of Analytical and Applied Pyrolysis. 2017. V. 124. P. 180.
Pilusa T.J. // Waste Management. 2017. V. 60. P. 451.
Han Yi., Stankovikj F., Garcia-Perez M. // Fuel Processing Technology. 2017. V. 159. P. 328.
Ryoiti Umeki E., Fernandes de Oliveira C., Belchior Torres R., Gonçalves dos Santos R. // Fuel. 2016. V. 185. P. 236.
Mohan A., Dutta S., Madav V. // Fuel. 2019. V. 250. P. 339.
Кадиев Х.М., Батов А.Е., Дандаев А.У., Зекель Л.А. // Журнал прикладной химии. 2018. Т. 91. № 6. С. 905.
Money D.M., Harrison G. // Fuel. 1999. V. 78. P. 1729.
Conesa J.A., Martin-Gullón I., Font R. // J. of Analytical and Applied Pyrolysis. 2005. V. 74. № 1–2. P. 265.
Uçar S., Karagöz S., Yanik J., Saglam M., Yuksel M. // Fuel Processing Technology. 2005. V. 87. P. 53.
Андрейков Е.И., Амосова И.С. // Каучук и резина. 2008. № 2. С. 4.
Малевич Н.Н, Юсевич А.И., Шашок Ж.С. // Каучук и резина. 2013. № 6. С. 26.
Quek A., Balasubramanian R. // J. of Analytical and Applied Pyrolysis. 2013. V. 101. P. 1.
Ahmad N., Abnisa F., Wan Mohd Ashri Wan Daud // Fuel. 2018. V. 218. P. 227.
Ляхевич Г.Д, Ляхевич А.Г. Технология и экономика переработки вторичных резиновых материалов, включая шины с металлокордом [монография]. Минск: БГПА, 1999. 244 с.
Шашок Ж.С., Вишневский К.В. Основы рецептуростроения эластомерных композиций. Минск: БГТУ, 2015. 73 с.
Pyase L. Gupta, Prem V. Dogra, Rakesh K. Kuchhal, Pradeep Kumar // Fuel. 1986. V. 65. P. 515.
Наканиси К. Инфракрасные спектры и строение органических соединений: Пер. с англ. М.: Мир, 1965. 217 с.
Дополнительные материалы отсутствуют.
Инструменты
Нефтехимия