Нефтехимия, 2020, T. 60, № 5, стр. 654-662
Никельсодержащие катализаторы разложения метана на основе структурированных носителей
М. А. Губанов 1, *, М. И. Иванцов 1, М. В. Куликова 1, В. А. Крючков 2, Н. В. Никитченко 3, М. И. Князева 1, А. Б. Куликов 1, А. А. Пименов 3, А. Л. Максимов 1
1 Институт нефтехимического синтеза им. А.В. Топчиева РАН
119991 Москва, Россия
2 Институт проблем нефти и газа РАН
119333 Москва, Россия
3 Самарский государственный технический университет
443100 Самара, Россия
* E-mail: gubanov@ips.ac.ru
Поступила в редакцию 10.05.2020
После доработки 11.05.2020
Принята к публикации 12.05.2020
Аннотация
Синтезированы новые никельсодержащие катализаторы деструкции метана на основе исходного и модифицированного слоистого двойного гидроксида, а также на основе многослойных углеродных нанотрубок. Синтезированные системы охарактеризованы комплексом физико-химических методов – рентгенофазовым анализом (РФА), сканирующей электронной микроскопией (СЭМ), спектроскопией комбинационного рассеяния (СКР) и термическим методом (ТМ). Исследована каталитическая активность синтезированных катализаторов в области температур 550–850°С. Показано, что в реакции разложения метана для образца с модифицированным Ni-содержащим слоем наблюдается два участка каталитической активности (550–650°С и 700–850°С), тогда как для образца на основе углеродных нанотрубок только один (700–850°С), а система на основе двойного слоистого гидроксида не проявила активности во всем диапазоне температур.
Изменение климата, происходящее в мире, в значительной степени зависит от выбросов парниковых газов, образующихся в процессе хозяйственной деятельности человека. Основным по влиянию на процессы изменения средней глобальной температуры, в силу большого объема эмиссии, является углекислый газ [1, 2]. Поэтому разработка технологий, направленных на снижение выбросов, или даже на полное исключение выделений оксидов углерода актуальна и востребована. К одному из возможных направлений можно отнести так называемую водородную энергетику [3]. Водород считается одним из самых экологически чистых энергоносителей и может применяться в топливных элементах при полном отсутствии выбросов СО2. Однако, основным процессом получения водорода в настоящее время является паровая конверсия метана – процесс осуществляемый в промышленности при достаточно жестких условиях (температура выше 800°, давление 20–30 атм) [4], а в ходе синтеза основными отходами являются оксиды углерода. Таким образом, с учетом полного цикла, включая стадии получения, выделения и очистки водорода, водородная энергетика практических эквивалентна прямому сжиганию метана по экологическому воздействию. К тому же, при отделении оксидов углерода возникает другая очень серьезная проблема, связанная с хранением и возможной дальнейшей их утилизацией [5].
Возможным путем к решению проблемы получения чистого водорода может стать прямое каталитическое разложение углеводородов (УВ) [6], главным образом метана, по реакции: СН4 = С + 2Н2.
С точки зрения водородной энергетики процесс позволяет получать продукт без примесей СО и СО2, являющихся ядами для топливных элементов; для экологии отсутствие выбросов также является преимуществом. Углерод может образовываться в виде углеродных нанотрубок, либо углеродных нановолокон [7–9]. Углеродные материалы обладают уникальными физико-химическими (механическими, электрическими и термическими) свойствами [10], которые способствуют широкому применению в современной электронике и технике, например в качестве сепараторов для Li-батарей.
В настоящее время существуют два альтернативных метода разложения метана: гомогенный (некаталитический) и каталитический. Некаталитический процесс основан на разложении метана в объеме при высоких температурах в отсутствие катализаторов [11–13]. Гомогенные процессы развиваются в направлении интенсификации теплообмена, в частности, интенсивно разрабатываются технологии с разложением метана непосредственно в расплавах металлов [11, 12].
Каталитическое разложение реализуют, в основном, с применением d-элементов семейства железа (Fe, Co, Ni), из которых наиболее активен, как сообщается, никель, представленный в смешанных оксидных системах [14–17]. К основной проблеме в практической реализации каталитического процесса относят быструю дезактивацию системы, связанную, во-первых, с агломерацией частиц активного металла, и, во-вторых, с зауглероживанием поверхности образующимися углеродными структурами [18, 19]. К одному из решений первой проблемы можно отнести применение термостабильных каталитических систем, структурированных на нано-уровне – например, предложены системы на основе Ni-содержащих шпинелей, полученных разложением соответствующих двойных слоистых гидроксидов [20]. Имеющиеся в литературе данные о каталитической активности углеродных систем, позволяют предположить возможное решение второй проблемы путем селективного формирования каталитически активного углерода и металлсодержащих катализаторов на его основе [21, 22].
Ранее было произведено исследование поведения модифицированных двойных слоистых систем и обнаружена их активность в синтезе водорода [23]. Также обнаружено формирование углеродных нанотрубок, как основного продукта разложения метана.
В данной работе реакцию разложения метана изучали с использованием двух типов структурированных каталитических систем: никельсодержащих катализаторов на основе гидроталькитоподобных структур и никельсодержащих, нанесенных на углеродные наноматериалы, контаков.
ЭКСПЕРИМЕНТАЛЬНАЯ ЧАСТЬ
Приготовление образцов. Синтез образца Ni-гидроталькит проводили методом pH-контролируемого соосаждения из растворов нитратов металлов с общей концентрацией катионов Mg, Al, Ni 1.0 моль/л. В качестве осадителя использовали раствор NaOH и Na2CO3 с концентрациями 2.0 и 0.20 моль/л соответственно. По окончании соосаждения проводили старение осадка в течение 24 ч. Затем осадок промывали и фильтровали под вакуумом до отрицательной реакции промывных вод на нитрат-ионы. Промытый осадок высушивали при 100–120°C до постоянной массы.
Синтез образца Ni-ЭДТА проводили в две стадии. На первой стадии синтезировали Mg,Al-гидроталькит, аналогично Ni-гидроталькиту. Затем проводили термолиз полученного гидроталькита при температуре 550°С. На второй стадии в раствор Na2[Ni-ЭДТА] помещали продукты термолиза и выдерживали в течение 10 ч. Полученный осадок Ni-ЭДТА промывали и фильтровали под вакуумом до обесцвечивания промывных вод. Промытый осадок высушивали при 100–120°С до постоянной массы.
Синтез Ni/углеродных нанотрубок (УНТ) проводили методом пропитки УНТ из водного раствора нитрата никеля. Сами УНТ синтезировали методом каталитического пиролиза пропан-бутановой фракции (содержание пропана 80%) при температуре 500°C и атмосферном давлении с использованием никелевых катализаторов [24]. Полученные УНТ в смеси с катализатором обрабатывали раствором соляной кислоты для извлечения металлов, далее подвергали функционализации кипячением в концентрированной азотной кислоте. Далее УНТ после промывки дистиллированной водой и ацетоном подвергали помолу в ацетоне с последующей сушкой и грануляцией. Полученные УНТ пропитывали по влагоемкости водным раствором нитрата никеля, высушивали на воздухе. Затем высушивали при 100–120°C и прокаливали при 400°С для разложения нитрата никеля до оксида NiO.
Характеристика образцов. Рентгенофазовый анализ (РФА) проводили с использованием дифрактометраRotaflex RU-200 (“Rigaku”, Япония), излучение CuKα. Размер кристаллитов оксида никеля NiO оценивали по уширению пика по формуле Шеррера. Термогравиметрический анализ проводили на приборе ТGA/DSC1 фирмы MettlerToledo. Навески исследуемых образцов (20–26 мг) помещали в тигли из оксида алюминия объемом 70 мкл. Нагрев образцов осуществляли в среде аргона, пропуская его со скоростью 10 мл/мин. Программа нагрева: выдержка при 30°С в течение 15 мин; нагрев с 30 до 1000°С со скоростью 10°С/мин. Обработку результатов измерения проводил и с помощью сервисной программы STARe, поставляемой в комплекте с прибором. Точность измерения составляла для определения температуры ±0.3°С, а для определения массы – 0.1 мкг.
Регистрацию спектров комбинационного рассеяния света (КР) осуществляли с помощью прибора HoribaJobinYvonLabRAM HR 800 UV. Для возбуждения спектров использовали излучение ионного аргонового лазера с длиной волны 514.53 нм; мощность на образце не превышала 7 мВт. Накопление сигнала проводили в течение 200 с.
Микрофотографии получали с применением растрового электронного микроскопа в комплекте с рентгеновским спектрометром, JSM-6390A, JEOL, Япония.
Каталитические испытания проводили в проточной лабораторной установке с кварцевым реактором (рис. 1).
Рис. 1.
Схема каталитической установки: 1–3 – баллоны с газами, 4–6 – регуляторы давления, 7–9 – вентили, 10 – РРГ Элточприбор-10М, 11 – реактор, 12 – печь, 13 – горячий спай термопары, 14 –ТРМ251 ОВЕН.
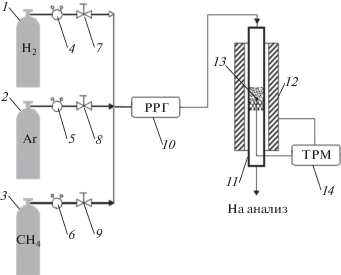
В реактор загружали 2 см3 кварца в качестве подложки, затем сверху загружали 2 см3 катализатора, горячий спай термопары располагали непосредственно в слое катализатора. Перед проведением эксперимента катализаторы активировали в течение 2 ч: Ni-гидроталькит в токе Н2 при 800°С, Ni-ЭДТА – в токе Ar при 420°С, Ni/УНТ – в токе Н2 при 400°С. После активации в реакторе устанавливали температуру начала реакции (550°С) и подключали метан. Эксперимент проводили в одинаковом режиме для всех катализаторов. Относительная объемная скорость 2000 ч–1. Изменение температуры осуществлялось автоматически по следующей программе: выдержка в течение 30 мин, нагрев в течение 3 мин с шагом 50°С. Отбор газа на анализ проводили трижды для каждого режима через 10, 20 и 30 мин от начала.
РЕЗУЛЬТАТЫ И ИХ ОБСУЖДЕНИЕ
Образец на основе исходного гидроталькита практически не проявляет активности, и конверсия метана в исследованном интервале температур не превышает 3%. Зависимости степени превращения метана от температуры процесса при установившемся режиме для образцов Ni-ЭДТА и Ni/УНТ приведены на рис. 2 и табл. 1.
Рис. 2.
Зависимость степени превращения метана от температуры для исследованных образцов: а – Ni-ЭДТА, б – Ni/УНТ.
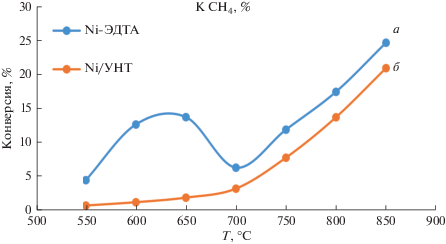
Таблица 1.
Каталитические характеристики образцов Ni-ЭДТА и Ni/УНТ
Катализатор | T, °C | Содержание Н2 в прод. газе, % | Содержание СН4 в прод. газе,% | Выход H2, г/м3 СН4 | Выход С, г/м3 СН4 | Активность, моль CH4/г Ni ч |
---|---|---|---|---|---|---|
Ni-ЭДТА | 550 | 8.47 | 91.53 | 7.89 | 23.68 | 64.59 |
600 | 22.39 | 77.61 | 22.51 | 67.52 | 184.14 | |
650 | 24.08 | 75.92 | 24.45 | 73.34 | 200.01 | |
700 | 11.77 | 88.23 | 11.17 | 33.50 | 91.36 | |
750 | 21.18 | 78.82 | 21.15 | 63.45 | 173.05 | |
800 | 29.65 | 70.35 | 31.08 | 93.25 | 254.32 | |
850 | 39.53 | 60.47 | 43.98 | 131.95 | 359.86 | |
900 | 40.33 | 59.67 | 45.11 | 135.33 | 369.09 | |
Ni/УНТ | 550 | 1.37 | 98.63 | 1.23 | 3.68 | 13.21 |
600 | 2.32 | 97.68 | 2.10 | 6.29 | 22.57 | |
650 | 3.63 | 96.37 | 3.30 | 9.89 | 35.50 | |
700 | 6.15 | 93.85 | 5.66 | 16.98 | 60.96 | |
750 | 14.34 | 85.66 | 13.79 | 41.36 | 148.45 | |
800 | 24.05 | 75.95 | 24.41 | 73.22 | 262.79 | |
850 | 34.56 | 65.44 | 37.31 | 111.92 | 401.69 |
На кривой конверсии метана в присутствии Ni-ЭДТА наблюдается максимум в области 600–650°С, что является типичным диапазоном для Ni-содержащих катализаторов разложения метана [25, 26]. В тоже время, в этой области происходит наиболее интенсивное снижение активности в ходе эксперимента, например, при температуре 650°С активность снижается в более чем два раза в течение 30 мин (рис. 3).
Рис. 3.
Изменение активности Ni-ЭДТА во времени в ходе эксперимента.За начальную точку (100%) взято значение активности в табл. 1 при соответствующих условиях.
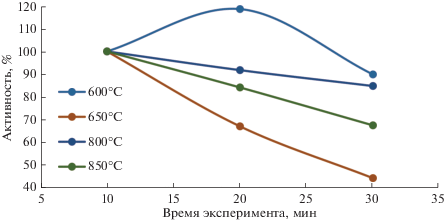
Вероятнее всего, в области температур ниже 700°С никель, расположенный в межслоевом пространстве гидроталькита, стабилизируется в высокодисперсном активном состоянии. Однако, отложения углерода частично блокируют доступ метана в межслоевое пространство. Системы, содержащие Ni, при определенных условиях подвержены дезактивации в результате инкапсуляции углеродом, что наблюдается если скорость осаждения углерода превышает скорость его диффузии в карбиде никеля [22, 23].
Фазовый состав полученных систем исследовали методом рентгенофазового анализа.
На рентгенограмме образца Mg0.78Al0.22(OH)2(Ni-edta)0.11 · zH2O (рис. 4) идентифицированы характерные рефлексы, соответствующие рефлексам слоистого двойного гидроксида (2θ = 11.3°, 22.9°, 34.7°, 39.3°, 46.6°, 60.1°), т.е. синтезированное соединение изоструктурны минералу гидроталькиту Mg6Al2(OH)16CO3 · 4H2O.
Рис. 4.
Рентгенограмма образца Mg1 –хAlx(OH)2(Ni-edta)х/2 · zH2O: ⚫ – рефлексы слоистого двойного гидроксида.
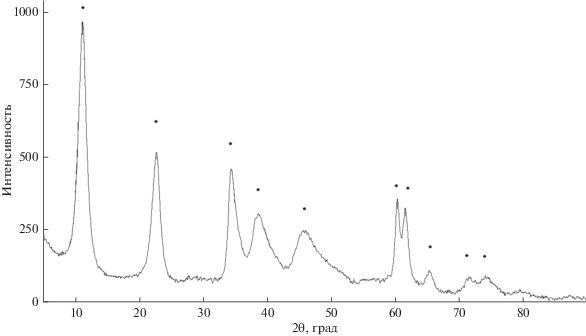
Согласно данным ТГА-ДСК для образца Ni-ЭДТА (рис. 5) деструкция образца протекает ступенчато. До 220°С происходит удаление кристаллизационной воды и части гидроксогрупп. Разложение комплексона наиболее интенсивно протекает в интервале 380–440°С с образованием слоистой структуры интеркалированной металлическим никелем. При дальнейшем повышении температуры вплоть до 1050°С происходит постепенное разрушение слоистой структуры гидроталькита с образованием никель-алюминиевой шпинели.
С разрушением слоев, блокирующих активные центры, связано возрастание каталитической активности при дальнейшем повышении температуры катализа выше 700°С. При этом, разрушение структуры при более низких температурах, чем определено методом ТГА-ДСК, может быть объяснено частичным восстановлением шпинели в среде метана [29]; кроме того, углеродные отложения также способствуют разрушению слоев. Суммарная производительность по углероду в ходе эксперимента составила 0.87 г С/г Ni в интервале до 700°С и 2.06 г С/г Ni– до 850°С.
Катализатор Ni/УНТ в области температур, характерной для никелевых систем, проявляет незначительную активность, и максимальная конверсия составляет 3% при 700°С (рис. 2). В случае образца, содержащего углеродные нанотрубки, методом рентгенофазового анализа показано, что до нанесения нитрата никеля (рис. 6а) для него характерны рефлексы (2θ = 25°, 43°, 52°, 78°), которые соответствуют рефлексам многостенных углеродных нанотрубок [30]. А после введения в систему соединения никеля (рис. 6б) на дифрактограмме проявляются рефлексы, соответствующие NiO (2θ = 37.3°, 62.9° и 75.4°). На основе данных об уширении пиков, методом Дебая–Шеррера, можно оценить размер кристаллитов оксида никеля. Так, величина области когерентного рассеяния составляет приблизительно 2 нм. Вероятнее всего, что уже на стадии восстановления происходит агломерация частиц никеля ввиду их слабой связи с углеродным носителем.
Известно, что при повышенных температурах деструкция метана в отсутствие активных металлов возможна непосредственно на углеродных носителях; при этом более структурированные углеродные системы, такие как, например, однослойные УНТ и фуллерены, обладают наименьшей активностью [31, 32]. За каталитические свойства ответственны поверхностные дефекты, наличие которых в образце Ni/УНТ подтверждается методами КР-спектроскопии и электронной микроскопии.
При анализе спектра комбинационного рассеяния (рис. 7) можно заключить, что УНТ представляют собой многослойные системы, так как в спектре отсутствуют характерные полосы в низкочастотной области спектра, так называемая радиальная дыхательная мода, наличие которой характерно для одностенныхна нотрубок. Отношение интенсивности полосы D (1375 см–1), соответствующей колебательной моде и “ответственной” за нарушение структуры нанотрубки, к полосе G (1616 см–1), отвечающей за сигнал от sp2-гибридизованного углерода, показывает качество нанотрубок. В нашем случае, I(D)/I(G) равно 1.429, что может свидетельствовать о высокой концентрации аморфной фазы, большом содержании дефектных нанотрубок или значительном числе коротких углеродных нанотрубок, в которых наибольшее влияние оказывают краевые эффекты.
Эволюция морфологии УНТ на стадиях приготовления катализатора исследована методами электронной микроскопии (рис. 8). На каждом этапе приготовления происходит частичное разрушение исходных УНТ.
Рис. 8.
Микрофотoграфия УНТ: а – СЭМ до процесса функционализации и помола; б – ПЭМ до процесса функционализации и помола, в – СЭМ после функционализации и помола, г, д – прокаленные после пропитки.
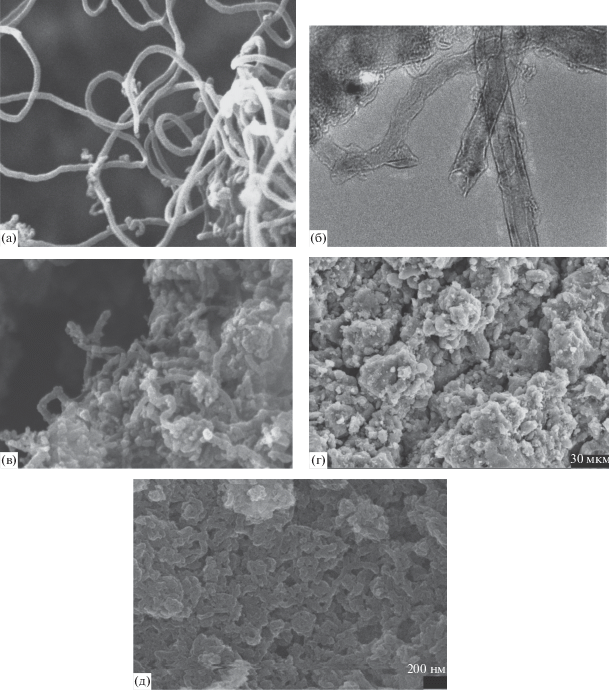
Отмытые от катализатора УНТ представляли из себя гранулы из агломератов нанотрубок (рис. 8а). Размеры отдельных исходных нанотрубок варьировались по внешнему диаметру от 60 до 90 нм (рис. 8б). В ходе функционализации происходит укорочение и значительное уплотнение УНТ (рис. 8в). После пропитки и прокалки УНТ только частично сохраняют структуру и преимущественно представляют собой агломераты мелких фрагментов с высоким содержанием аморфного углерода (рис. 8г, д). Средний диаметр УНТ в представленном образце оценен шириной порядка 80 нм.
Активность образцов Ni/УНТ и Ni-ЭДТА в реакции разложения метана при повышенной температуре практически совпадает. Вероятно, после разрушения матрицы гидроталькита катализ протекает непосредственно на дефектных углеродных отложениях, сходных с образцом Ni/УНТ, что также объясняет крайне низкую активность исходного гидроталькита ввиду отсутствия стадии образования дефектных УНТ при низких температурах.
ЗАКЛЮЧЕНИЕ
В работе синтезировано и исследовано два типа каталитических систем: на основе двойных слоистых гидроксидов и на основе углеродных нанотрубок. Показано, что при введении молекул ЭДТА в структуру неорганического композита сохраняется слоистая структура, что, вероятно, обеспечивает в дальнейшем стабилизацию активного Ni-содержащего компонента. Данный факт способствует проявлению двух температурных диапазонов каталитической активности. Образец, содержащий нанотрубки, несмотря на высокую дисперсию и малый размер (примерно 2 нм) наночастиц оксида никеля, не проявляет активности в области низких температур (550–650°С), что может быть связано с агломерацией частиц в виду слабого взаимодействия с углеродным носителем, а каталитическая активность соответствует протеканию реакции на дефектах самих УНТ (дефектная структура подтверждается результатами КР-спектроскопии) при высокой температуре.
Список литературы
MacDougall A.H. // Curr. Clim. Change Rep. 2016. V. 2. P. 39.
Kweku D.W., Bismark, O., Maxwell, A., Desmond, K.A., Danso, K.B., Oti-Mensah, E.A., Quachie, A.T., Adormaa, B.B. // J. of Scientific Research and Reports. 2017. V. 17. I. 6. P. 1.
Dawood F., Anda M., Shafiullah G.M. // Intern. J. of Hydrogen Energy. 2020. V. 45. № 7. P. 3847.
Vozniuk O., Tanchoux N., Millet J.-M., Albonett S., Di Renzo F., Cavani F. // Studies in Surface Science and Catalysis. 2019. V. 178. P. 281.
Lin H., Biddinger E.J. // Energy Technology. Generation, Conversion, Storage, Distribution. 2017. V. 5. I. 6. P. 771.
Ahmeda A., Aitani F., Rahman A., Al-Dawood F., Al-Muhaish // Applied Catalysis A: General. 2009. V. 359. P. 1.
Torres D., Pinilla J.L., Suelves I. // Applied Catalysis A: General. 2018. V. 559. P. 10.
Allaedini G., Aminayi P., Tasirin S.M. // Chem. Engineering Research and Design. 2016. V. 112. P. 163.
Rastegarpanah A., Meshkani F., Rezaei M. // Fuel Processing Technology. 2017. V. 167. P. 250.
Saito R., Dresselhaus M. S., Dresselhaus G. Physical Properties of Carbon Nanotubes. Imperial College Press, 1999. 251 p.
Парфенов В.Е., Никитченко Н.В., Пименов А.А., Кузьмин А.Е., Куликова М.В., Чупичев О.Б., Максимов А.Л. // Журнал прикладной химии. 2020. Т. 93. Вып. 5. С. 611.
Catalan L.J.J., Rezaei E. // Intern. J. of Hydrogen Energy. 2020. V. 45. № 4. P. 2486.
Javad M., Farjad A., Larry F., Kostiuk W., Olfert J.S. // J. of Aerosol Science. 2019. V. 131. P. 13.
Al-Fatesh A.S., Kasim S.O., Ibrahim A.A., Al-Awadi A.S., Abasaeed A.E., Fakeeha A.H., Awadallah A.E. // Renewable Energy. 2020. V. 155. P. 969.
Wang D., Zhang J., Sun J., Gao W., Cui Y. // Intern. J. of Hydrogen Energy. 2019. V. 44. № 14. P. 7205.
Awadallah A.E., Mostaf M.S., Aboul-Enein A.A., Hanafi S.A. // Fuel. 2014. V. 129. P. 68.
Hornés A., Bera P., Fernández-García M., Guerrero-Ruiz A., Martínez-Arias A. // Applied Catalysis B: Environmental. 2012. V. 111–112. P. 96.
de la Cruz-Flores V.G., Martinez-Hernandez A., Gracia-Pinilla M.A. // Applied Catalysis A: General. 2020. V. 594. P. 117455.
Suelves I., Lázaro M.J., Moliner R., Corbell B.M., Palacios J.M. // Intern. J. of Hydrogen Energy. 2005. V. 30. № 15. P. 1555.
García-Sancho C., Guil-López R., Pascual L., Maireles-Torres P., Navarro R.M., Fierro J.L.G. // Applied Catalysis A: General. 2017. V. 548. P. 71.
Zhang J., Qi M., Zhang G., Hu H., Xie L., Ma X. // Intern. J. of Hydrogen Energy. 2017. V. 42. № 16. P. 11 047.
Nishii H., Miyamoto D., Umed Y., Hamaguchi H., Suzuki M., Tanimoto T., Harigai T., Takikawa H., Suda Y. // Applied Surface Science. 2019. V. 473. P. 291.
Крылова М.В., Куликов А.Б., Маслов И.А., Мордкович В.З. // Газохимия. 2009. № 8. С. 50.
Крючков В.А., Крючков М.В., Выморков Н.В., Портнова Я.М., Бушанский Н.В., Бушанский С.Н. // Композиты и наноструктуры. 2014. Т. 6. № 4. С. 223.
García-Sancho C.,Guil-López R., Sebastián-López A., Navarro R.M., Fierro J.L.G. // Intern. J. of Hydrogen Energy. 2018. V. 43. № 20. P. 9607.
Ashraf M.A., Croiset E., Epling W. // Intern. J. of Hydrogen Energy. 2011. V. 36. № 4. P. 2904.
Ermakova M.A., Ermakov D.Y., Kuvshinov G.G. // Appl. Catal. A. 2000. V. 201. № 1. P. 61.
Буранова Ю.С. // Труды МФТИ. 2011. Т. 3. № 3. С. 30.
Zardin L., Perez-Lopez O.W. // Intern. J. of Hydrogen Energy. 2017. V. 42. № 12. P. 7895.
Das R., Bee S., Hamid A., Ali E. Md., Ramakrishna S., Yongzhi W. // Current Nanoscience. 2015. V. 11. № 1. P. 1.
Muradov N., Smith F., T-Raissi A. // Catalysis Today. 2005. V. 102–103. P. 225.
Muradov N. // Catalysis Communications. 2001. V. 2. № 3–4. P. 89.
Дополнительные материалы отсутствуют.