Нефтехимия, 2020, T. 60, № 5, стр. 686-692
Синтез модифицированного катализатора для процесса жидкофазного алкилирования бензола этиленом
Д. А. Шавалеев 1, М. Л. Павлов 2, Р. А. Басимова 2, А. А. Садовников 3, В. В. Судьин 4, Е. М. Смирнова 5, Н. Р. Демихова 5, Ю. В. Григорьев 6, А. Л. Максимов 3, Е. Р. Наранов 3, *
1 ООО “SNHGroup”
453261 Башкортостан, Салават, Россия
2 Научно-технический центр “Газпром нефтехим Салават”
453256 Башкортостан, Салават, Россия
3 Институт нефтехимического синтеза им. А.В. Топчиева РАН
119991 Москва, Россия
4 Институт металлургии и материаловедения им. А.А. Байкова РАН
119334 Москва, Россия
5 Российский государственный университет нефти и газа имени И.М. Губкина
119991 Москва, Россия
6 Институт кристаллографии им. А.В. Шубникова РАН
119333 Москва, Россия
* E-mail: naranov@ips.ac.ru
Поступила в редакцию 25.04.2020
После доработки 05.05.2020
Принята к публикации 12.05.2020
Аннотация
Синтезированы высокоэффективные катализаторы процесса жидкофазного алкилирования бензола этиленом на основе цеолита Y без связующих веществ. Модифицирование осуществляли обработкой водными растворами соляной и лимонной кислот для удаления из его состава внерешеточного алюминия, образующегося при частичном деалюминировании цеолита Y. Синтезированные катализаторы были испытаны в алкилировании бензола этиленом при температуре 200°С, давлении 2.5 МПа, мольном соотношении бензол : этилен 5 : 1, объемной скорости подачи бензола 5 ч–1. При использовании модифицированного катализатора содержание этилбензола (ЭБ) в алкилате увеличивается на 27%, а селективность по ЭБ – на 5%, по сравнению с исходным цеолитом Y.
В настоящее время среди процессов алкилирования производство ЭБ занимает одно из ведущих мест, поскольку бόльшая часть получаемого продукта используется в производстве стирола [1]. Около 40% ЭБ все еще получают с помощью устаревшего процесса алкилирования по Фриделю–Крафтсу с использованием хлорида алюминия [2]. Использование последнего создает серьезные экологические и эксплуатационные проблемы (высокая коррозионность среды и значительное количество химически загрязненных стоков). Поэтому, в последние 40 лет большое внимание уделяется получению ЭБ с использованием гетерогенных цеолитсодержащих катализаторов [3–6].
С 1990 г., благодаря успехам в области гетерогенного катализа, появились благоприятные условия (в т.ч. из-за лоббирования экологических активистов) для создания процесса получения алкилароматических углеводородов (УВ) по малоотходной, исключающей загрязнение окружающей среды, технологии. Катализаторы алкилирования ароматических УВ этиленом должны обладать определенным набором свойств, позволяющих получать ЭБ с высокими выходами и с наименьшим коксообразованием [7–9]. В настоящее время изучение цеолитсодержащих компонентов твердокислотных катализаторов ведется достаточно активно [10–18]. Поэтому разработка гетерогенных катализаторов и создание на их основе непрерывного, безотходного процесса алкилирования имеет большое практическое и экологическое значение, а также представляет несомненный научный интерес [6, 12, 18–20]. Известны технологии получения ЭБ компаний “Mobil-Badger”, “Lummus-UOP”, “CDTech”, “DowChemical” [5]. В России созданием цеолитсодержащих катализаторов и технологий процессов алкилирования бензола этиленом и трансалкилирования бензола диэтилбензолами ранее занимались в ГрозНИИ, а сейчас – в ИНХС РАН и НТЦ ООО “Газпром нефтехим Салават” [6]. В последние годы наблюдается тенденция к переходу от газофазного к жидкофазному алкилированию бензола этиленом [6]. Данный процесс характеризуется бόльшим выходом ЭБ, меньшим расходом и продолжительным межрегенерационным периодом эксплуатации катализатора.
Цель настоящей работы – изучение модифицирования катализатора HY-BF, представляющего собой цеолит Y, не содержащий связующих веществ, в кислотной форме для процесса жидкофазного алкилирования бензола этиленом.
ЭКСПЕРИМЕНТАЛЬНАЯ ЧАСТЬ
Для синтеза цеолита НY использовали методику, описанную в [22]; степень кристалличности полученного цеолита с силикатным модулем SiO2/Al2O3, равным 5.5, составляла ~100%. Натриевую форму переводили в протонную Н+-форму путем ионного обмена раствором нитрата аммония (1 М).
Модифицирование цеолита НY осуществляли обработкой водными растворами соляной или лимонной кислот для удаления внерешеточного алюминия, образующегося при частичном деалюминировании цеолита. Обработку проводили растворами кислот с концентрацией 0.1; 0.3; 0.5 и 0.9 н при температуре 90°C, в течение 1 ч и соотношении гранулы/раствор = 1 : 7 (по объему). После обработки образцы промывали деионизированной водой, сушили при температуре 140°C в течение 4 ч и прокаливали в воздушной среде при температуре 600°С в течение 3 ч. Условия получения и свойства цеолита НY приведены в табл. 1. Образцы, полученные с помощью кислотной обработки без связующих компонентов, были маркированы как HY-BF (binder-free).
Таблица 1.
Условия получения и свойства катализатора НY
Показатели | НY-BF |
---|---|
Количество ионообменных обработок | Три |
Температура прокаливания после обработки, °С | 600 |
Степень обмена катионов Na+ на Н+ | 0.96 |
Содержание Na2O в цеолите, мас. % | 0.46 |
Равновесная адсорбционная емкость, см3/г, по парам: | |
воды | 0.26 |
бензола | 0.32 |
Степень кристалличности цеолита, % | 0.98 |
Модуль цеолита по данным РФА, моль/моль | 7.1 |
Содержание натрия в образцах определяли путем перевода оксида натрия из цеолита или катализатора в раствор воздействием на образцы плавиковой кислотой, с дальнейшим исследованием полученного раствора методом пламенной фотометрии с помощью анализатора ПФА-311
Фазовый состав, модуль цеолита и катализаторов определяли методом рентгенофазового анализа (РФА) на рентгеновском дифрактометре PHILIPS PW1800. Модуль цеолита рассчитывали согласно методике, описанной в [23].
Для определения равновесной адсорбционной емкости цеолитов использовали эксикаторный метод, основанный на определении величины полного насыщения цеолита парами адсорбата (воды, бензола или н-гептана), в стандартных условиях испытания (температура 25°C, P/Ps = 0.8).
Кислотные свойства катализаторов исследовали методом термопрограммированнной десорбции аммиака ТПД NH3.
Текстурные характеристики образцов определяли методом низкотемпературной адсорбции азота (77 К) с использованием прибора ASAP 2020 (“Micromeritics”). Перед анализом образцы вакуумировали 6 ч при 350°С. Удельная поверхность была рассчитана по БЭТ при относительном парциальном давлении Р/Р0 =0.2; общий объем пор определен по BJH при относительном парциальном давлении Р/Р0 = 0.95 по ветви адсорбции.
Регистрацию спектров ЯМР 27Al производили на спектрометре Brucker AVANCE II 400 с магнитным полем 9.4 Тл, что соответствует рабочим частотам ν27Al = 104.23 МГц. Спектры записывали для воздушно сухих образцов при вращении под магическим углом (54.7°) с частотой 12 кГц (ротор 4 мм ZrO2). В качестве внешнего стандарта (0 м.д.) использовался 1 М-ный водный раствор Al(NO3)3. Для регистрации спектров применялась одноимпульсная последовательность (15° импульс). Период повторения импульсной последовательности составлял 0.5 с. Количество повторов – 2048.
Просвечивающие электронные микрофотографии (ПЭМ) образцов цеолитов выполнены на приборе FEI Tecnai Osiris, ускоряющее напряжение 200 кВ.
Морфологию синтезированных материалов и катализаторов изучали методом растровой электронной микроскопии (РЭМ) на приборе Carl Zeiss NVision 40 со встроенными детекторами: InstrumentsX-Maxdetector и EsB – детектор обратно рассеянных электронов. Увеличение до 500 000×, пространственное разрешение 4 нм при 30 кВ.
Реакцию алкилирования бензола этиленом (чистота 99.9 об. %) изучали на лабораторной установке, оборудованной реактором проточного типа, при следующих условиях проведения испытаний: температура 200°С; давление 2.5 МПа; объемная скорость по бензолу 5 ч–1; мольное соотношение бензол/этилен 5/1. Пробу отбирали через 1 ч после выхода установки на режим.
Продукты реакции анализировали на хроматографе “Кристаллюкс 4000” с пламенно-ионизационным детектором, кварцевой капиллярной колонкой размером 60 м × 0.32 мм × 1.0 мкм с неподвижной фазой ZB-1. Обработку результатов проводили на программно-аппаратном комплексе по методу “внутренней нормализации”.
Для оценки работы катализаторов в реакции жидкофазного алкилирования бензола этиленом использовали следующие показатели: конверсия бензола (Б), выход ЭБ от теоретического, селективность по ЭБ.
1. Конверсия бензола (степень превращения бензола), КБ, %, рассчитывали по формуле:
2. Выход ЭБ – показатель, характеризующий полноту использования сырья в процессе алкилирования, (ХЭБ), %, рассчитывается по формуле:
3. Теоретический выход этилбензола, %, рассчитывается по формуле:
4. Селективность по ЭБ – относительная концентрация ЭБ в расчете на продукты реакции, %, рассчитывается по формуле:
РЕЗУЛЬТАТЫ И ИХ ОБСУЖДЕНИЕ
Изучение морфологии и кристалличности исходного образца HY проводили методом РЭМ, ПЭМ и РФА (рис. 1). Результаты показали, что синтезированный образец обладал высокой степенью кристалличности, средний размер кристаллитов составлял ~ 300 нм, что соответствовало значению, полученному с помощью уравнения Шеррера: D(Å) ~ 0.94λ/∆(2θ)cos(θ) (0.94 – постоянная Шеррера, ∆(2θ) – ширина рефлекса на полувысоте, θ – угол дифракции).
С помощью ПЭМ было установлено, что кислотная обработка (как соляной, так и лимонной кислотой) существенно не оказывает влияние на размер кристаллитов. Тем не менее, морфология цеолита претерпела изменения: грани кристаллитов аморфизовались в результате частичного растворения в кислотах (рис. 2). Полученные результаты согласуются с предыдущими исследованиями в данной области [21].
Влияние кислотной обработки на изменения цеолитного модуля оценивали с помощью элементного и рентгенофазового анализа. В табл. 2 приведены текстурные характеристики и данные о химическом составе и модуле образцов катализаторов до и после кислотной обработки.
Таблица 2.
Физико-химические характеристики материалов
Образец | SБЭТ, м2/г | Vпор, см3/г | Модуль по элементному анализу | Модуль по данным РФА |
---|---|---|---|---|
HY-BF | 650 | 0.35 | 7.1 | 7.1 |
HY-BF-1 | 630 | 0.33 | 7.2 | 7.1 |
HY-BF-2 | 605 | 0.33 | 7.7 | 7.1 |
HY-BF-3 | 570 | 0.30 | 8.1 | 7.7 |
HY-BF-4 | 510 | 0.30 | 8.6 | 8.6 |
HY-BF-5 | 705 | 0.37 | 7.7 | 7.1 |
HY-BF-6 | 670 | 0.34 | 8.6 | 7.7 |
HY-BF-7 | 650 | 0.34 | 9.2 | 8.0 |
HY-BF-8 | 610 | 0.36 | 10.9 | 9.2 |
Силикатный модуль материалов после обработки НY растворами кислот, как и ожидалось, возрастает. Рост модуля напрямую связан с деалюминированием цеолитов, причем обработка лимонной кислотой приводит к более высокой степени деалюминирования по сравнению с соляной кислотой, что вероятно связано с бóльшей комплексообразующей способностью. Значения удельной поверхности и объема пор также существенно зависят от способа модифицирования. Так, при повышении концентрации соляной кислоты удельная поверхность заметно снижается с 650 до 510 м2/г, в то время как при использовании лимонной кислоты наблюдался максимум значений при использовании 0.1 н лимонной кислоты (705 м2/г и 0.37 см3/г).
Величина модуля, определенная по данным химического анализа, постоянно возрастает с увеличением концентрации растворов соляной и лимонной кислот, в то время как после обработки цеолита растворами соляной кислоты с концентрацией 0.1 и 0.3 н, а также 0.1 н раствором лимонной кислоты модуль катализаторов (по данным РФА) не изменяется. Это свидетельствует об удалении исключительно внерешеточного алюминия, а деалюминирование кристаллическойструктуры цеолита не происходит.
Для установления окружения атомов алюминия в материалах использовали метод ЯМР-спектроскопии твердого тела на ядрах 27Al (рис. 3).
Как видно из данных, приведенных на рис. 3, в спектре ЯМР 27Al исходного образца HY присутствуют два сигнала, из которых основной сигнал при δ = 56 ppm соответствует атомам алюминия, имеющим тетраэдрическое окружение в кристаллической структуре, в то время как доля внерешеточного шестикоординационного алюминия сравнительно мала. В спектрах ЯМР 27Al образцов HY-BF-4, полученного в результате кислотной обработки HCl (0.9 н), и HY-BF-8, полученного кислотной обработкой 0.9 н лимонной кислотой, отсутствуют сигналы внерешеточного алюминия. Стоит отметить тот факт, что основной сигнал в образцах после обработки концентрированными кислотами стал более уширен, что свидетельствует о частичном деалюминировании кристаллической структуры цеолита.
Равновесные адсорбционные емкости материалов по парам воды, бензола и гептана приведены в табл. 3.
Таблица 3.
Условия обработки НY-BF, равновесная адсорбционная емкость по парам различных адсорбатов
ОбразецН2ОС6Н6С7Н16 | Концентрация обрабатывающего раствора | Равновесная адсорбционная емкость, см3/г, по парам | ||
---|---|---|---|---|
HY | – | 0.26 | 0.32 | 0.34 |
HY-BF-1 | 0.1 н HCl | 0.26 | 0.32 | 0.34 |
HY-BF-2 | 0.3 н HCl | 0.26 | 0.32 | 0.34 |
HY-BF-3 | 0.5 н HCl | 0.25 | 0.31 | 0.33 |
HY-BF-4 | 0.9 н HCl | 0.24 | 0.30 | 0.32 |
HY-BF-5 | 0.1 н лимонная кислота | 0.26 | 0.32 | 0.34 |
HY-BF-6 | 0.3 н лимонная кислота | 0.25 | 0.32 | 0.34 |
HY-BF-7 | 0.5 н лимонная кислота | 0.24 | 0.0 | 0.32 |
HY-BF-8 | 0.9 н лимонная кислота | 0.22 | 0.28 | 0.30 |
Результаты показали, что после обработки цеолита растворами кислот с концентрацией 0.1 и 0.3 н, величина адсорбционной емкости катализаторов практически не изменялась. С увеличением концентрации наблюдалось снижение адсорбционной емкости вследствие частичной аморфизации кристаллической решетки цеолита.
Анализ образцов методом ТПД аммиака показал, что наибольшей концентрацией сильных кислотных центров обладает исходный цеолит HY. Снижение концентрации сильных кислотных центров при обработке соляной и лимонной кислотами коррелирует со степенью кристалличности материалов (рис. 4). Стоит отметить, что для материалов, полученных с помощью лимонной кислоты, снижение концентрации сильных кислотных центров с уменьшением pH раствора происходит постепенно, в то время как для материалов, полученных с помощью соляной кислоты не наблюдается явной закономерности. Данное наблюдение может служить косвенным подтверждением предположения о селективной экстракции внерешеточного алюминия лимонной кислотой. При увеличении концентрации растворов этих кислот концентрация слабых кислотных центров практически не изменяется в случае использования лимонной кислоты.
Рис. 4.
Зависимость степени кристалличности и кислотности образцов катализаторов до и после обработки соляной (а) и лимонной (б) кислотами от концентрации обрабатывающих растворов.
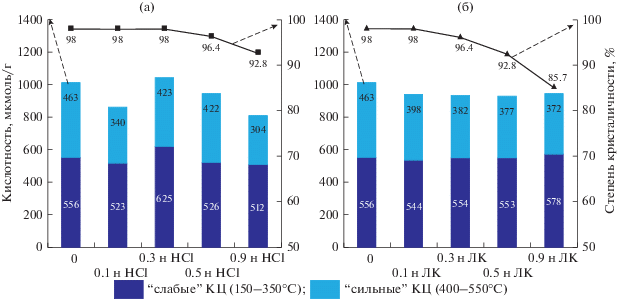
Степень кристалличности катализаторов начинает уменьшаться после обработки 0.3 н раствором лимонной кислоты и 0.5 н раствором НCl. При этом, по данным РФА, наблюдается увеличение модуля кристаллической решетки цеолита. Следовательно, удаляется не только внерешеточный алюминий, но и алюминий в кристаллической структуре цеолита. Повышение концентрации кислот приводит к дальнейшему деалюминированию катализаторов.
Катализаторы HY-BF-2 и HY-BF-5, обладающие оптимальной кислотностью и текстурными характеристиками, были выбраны для дальнейших исследований каталитических свойств. В табл. 4 приведены результаты каталитических экспериментов по жидкофазному алкилированию бензола этиленом с использованием исходного цеолита HY и модифицированных катализаторов HY-BF-2 и HY-BF-5.
Таблица 4.
Результаты твердокислотного алкилирования бензола этиленом на разработанных катализаторах (200°С; 2.5 МПа; ОСПС = 5 ч–1 по бензолу, бензол : этилен = 5 : 1 моль/моль)
Показатели | Наименование катализатора | ||
---|---|---|---|
HY | HY-BF-2 | HY-BF-5 | |
1. Углеводородный состав, мас. % | Алкилат | ||
неароматические углеводороды | 0.46 | 0.44 | 0.37 |
бензол | 82.16 | 78.39 | 80.20 |
толуол | 0.032 | 0.035 | 0.030 |
этилбензол | 12.77 | 16.29 | 14.67 |
изо-пропилбензол | 0.077 | 0.051 | 0.081 |
ксилолы | 0.000 | 0.000 | 0.001 |
н-пропилбензол | 0.002 | 0.004 | 0.004 |
этилтолуол | 0.192 | 0.132 | 0.204 |
м-диэтилбензол | 1.061 | 1.417 | 1.205 |
п-диэтилбензол | 0.788 | 0.866 | 0.822 |
о-диэтилбезол | 0.775 | 0.696 | 0.721 |
С11 и выше (ПАБ) | 1.685 | 1.676 | 1.705 |
Сумма | 100.0 | 100.0 | 100.0 |
2. Конверсия бензола, % | 17.67 | 21.46 | 19.4 |
3. Выход ЭБ от теоретического, % | 50.37 | 64.27 | 57.40 |
4. Селективность по ЭБ, % | 72.27 | 75.92 | 74.65 |
При использовании катализаторов HY-BF-2 и HY-BF-5 основные показатели процесса – конверсия бензола, концентрация ЭБ в алкилате, выход ЭБ и селективность по ЭБ оказались выше по сравнению с исходным цеолитом HY.
Полученные результаты, прежде всего свидетельствуют о том, что в данном процессе концентрация сильных кислотных центров катализатора не является ключевой характеристикой. Суммарная кислотность вкупе с развитой поверхностью определяет высокую каталитическую активность. Так, образец HY-BF-2 обладает высокой общей кислотностью и примерно схожими текстурными характеристиками с исходным HY; при этом концентрация ЭБ в алкилате выше на 27.6%, а селективность по ЭБ – на 5.1%.
Таким образом, разработан эффективный способ модифицирования цеолита HY с помощью кислотной обработки. Полученные материалы обладают оптимальными текстурными характеристиками и кислотностью. Данные свойства материалов позволяют достаточно селективно проводить процесс алкилирования бензола этиленом.
Список литературы
Čejka J., Wichterlová B. // Catalysis Reviews – Science and Engineering. 2002. V. 44. № 3. C.375.
Galadima A. // Microporous Mesoporous Mater. 2015. V. 213. P. 169.
Arstad B., Kolboe S., Swang O. // J. of Physical Chemistry B. 2004. V. 108. № 7. P. 2300.
Christensen C.H., Johannsen K., Schmidt I., Christensen C.H. // J. Am. Chem. Soc. 2003. V. 125. № 44. P. 13 370.
Degnan T.F., Smith C.M., Venkat C.R. // Applied Catalysis. A: General. 2001. V. 221. № 1–2. P. 283.
Naranov E.R., Dement’ev K.I., Gerzeliev I.M., Kolesnichenko N. V., Roldugina E.A., Maksimov A.L. // Petrol. Chemistry. 2019. V. 59. № 3. P. 247.
Shi Y., Xing E., Xie W., Zhang F., Mu X., Shu X. // Applied Catalysis. A: General. 2015. V. 497. P. 135.
Liu K., Xie S., Liu S., Xu G., Gao N., Xu L. // J. of Catalysis. 2011. V. 283. № 1. P. 68.
Gao N., Xie S., Liu S., Xin W., Gao Y., Li X., Wei H., Liu H., Xu L. // Microporous and Mesoporous Materials. 2015. V. 212. P. 1.
Grzybek J., Kubů M., Roth W.J., Gil B., Čejka J., Kasneryk V. // Catalysis Today. 2019.
Gushchin P.A., Kolesnikov I.M., Vinokurov V.A., Ivanov E.V., Lyubimenko V.A., Borshch V.N. // J. of Catalysis. 2017. V. 352. P. 75.
Naranov E.R., Sadovnikov A.A., Maximov A.L., Karakhanov E.A. // Microporous and Mesoporous Materials. 2018. V. 263. P. 150.
Naranov E.R., Maximov A.L. // Catalysis Today. 2019. V. 329. P. 94.
Naranov E.R., Badeeva A.S., Sadovnikov A.A., Kardashev S.V., Maksimov A.L., Lysenko S. V., Vinokurov V.A., Karakhanov E.A. // Petroleum Chemistry. 2016. V. 56. № 7. P. 599.
Naranov E.R., Sadovnikov A.A., Vatsouro I.M., Maximov A.L. // Inorg. Chemistry Frontiers. 2020. V. 7. № 6. P. 1400.
Afokin M.I., Smirnova E.M., Starozhitskaya A.V., Gushchin P.A., Glotov A.P., Maksimov A.L. // Chemistry and Technology of Fuels and Oils. 2020. P. 1.
Shirokopoyas S.I., Baranova S. V., Maksimov A.L., Kardashev S.V., Kulikov A.B., Naranov E.R., Vinokurov V.A., Lysensko S.V., Karakhanov E.A. // Petrol. Chemistry. 2014. V. 54. № 2. P. 94.
Roldugina E.A., Glotov A.P., Isakov A.L., Maksimov A.L., Vinokurov V.A., Karakhanov E.A. // Russian J. of Applied Chemistry. 2019. V. 92. № 8. P. 1170.
Naranov E.R., Golubev O.V, Guseva A.I., Nikulshin P.A., Maksimov A.L., Karakhanov E.A. // Petrol. Chemistry. 2017. V. 57. № 6. P. 965.
Wang Y., Gao Y., Xie S., Liu S., Chen F., Xin W., Zhu X., Li X., Jiang N., Xu L. // Catalysis Today. 2018. V. 316. P. 71
Ristić A., Fischer F., Hauer A., Zabukovec Logar N. // J. of Materials Chemistry. A. 2018. V. 6. № 24. P. 11 521.
Шавалеев Д.А., Павлов М.Л., Басимова Р.А., Шавалеева Н.Н., Эрштейн А.С., Травкина О.С., Кутепов Б.И. // Патент РФ № 2553876. Опубл. 10.06.15. Бюл. 17.
Брек Д. // Цеолитовые молекулярные сита. М.: Мир, 1976. 782 с.
Дополнительные материалы отсутствуют.