Неорганические материалы, 2019, T. 55, № 1, стр. 101-108
Электроимпульсное плазменное спекание мелкозернистой композиционной керамики Y2.5Nd0.5Al5O12 + MgO для инертных топливных матрицЛ. С. Головкина, А. В. Нохрин, М. С. Болдин, Е. А. Ланцев, А. И. Орлова, В. Н. Чувильдеев, А. А. Мурашов, Н. В. Сахаров
Л. С. Головкина 1, *, А. В. Нохрин 1, М. С. Болдин 1, Е. А. Ланцев 1, А. И. Орлова 1, В. Н. Чувильдеев 1, А. А. Мурашов 1, Н. В. Сахаров 1
1 Национальный исследовательский Нижегородский государственный университет им. Н.И. Лобачевского
603950 Нижний, Новгород, пр. Гагарина, 23/3, Россия
* E-mail: golovkina_lyudmila@mail.ru
Поступила в редакцию 14.04.2018
Аннотация
Исследована возможность получения методом электроимпульсного плазменного спекания высокоплотной (98.6–99.5%) композиционной керамики Y2.5Nd0.5Al5O12 (YAG)–x MgO (x = 5, 10, 20 об. %). Порошковые композиции YAG-MgO получены путем осаждения из водного раствора нитрата магния Mg(NO3)2 фазы MgO на поверхность частиц граната. Показано, что интенсивность спекания композитов YAG–MgO при низких температурах контролируется процессом объемной диффузии, а при повышенных температурах – процессом зернограничной диффузии.
ВВЕДЕНИЕ
Соединения на основе иттрий-алюминиевого граната (YAG) являются перспективными материалами для трансмутации минор-актинидов (МА) [1–4] благодаря возможности широкого изоморфизма (структура граната может включать катионы актинидов (в том числе Pu (IV)) и редкоземельных элементов (РЗЭ) [5, 6]). Важно также отметить, что керамики на основе YAG обладают высокой гидролитической и радиационной стабильностью [7, 8], что в перспективе позволяет решить одну из основных задач атомной энергетики, связанную с разработкой эффективных технологий обращения с запасами плутония и МА для создания инертных топливных матриц (ИТМ), за счет использования кристаллических минералоподобных соединений [1–3, 9–11].
Главными недостатками керамик на основе YAG (с точки зрения их применения для создания ИТМ) являются низкая теплопроводность (λYAG (300 K) = 8 Вт/(м K) [12]), твердость и трещиностойкость. Это вызывает появление микротрещин из-за неравномерного нагрева материала за счет радиогенного тепла, увеличение реакционной поверхности и, как следствие, снижение гидролитической стойкости керамик против выщелачивания Pu и РЗЭ. Все это приводит к ускорению процесса разрушения ИТМ и сокращению времени их эффективной работы. Для устранения этих недостатков в состав керамик вводят частицы второй фазы, обладающие высокой теплопроводностью и низким сечением захвата нейтронов.
Перспективным методом получения высокоплотных керамик является технология электроимпульсного плазменного спекания (ЭИПС) [4, 5, 13–16], которая позволяет получать керамики с высокой плотностью, что открывает новые возможности создания материалов различного назначения [4–6, 17], в том числе для получения высокоустойчивых минералоподобных керамик для иммобилизации высокоактивных компонентов радиоактивных отходов и трансмутации МА [6, 9–11, 17–19]. Основная идея метода ЭИПС состоит в высокоскоростном нагреве (до 2500°С/мин) порошковых материалов путем пропускания через оснастку и образец постоянного импульсного тока большой мощности с одновременным приложением давления.
Целью работы является получение методом ЭИПС композиционной керамики на основе YAG с добавлением оксида магния MgO, обладающего высоким коэффициентом теплопроводности (λMgO (300 K) = 59 Вт/(м K) [20]), а также исследование закономерностей ЭИПС керамики YAG-MgO, использование которой представляет интерес для ядерной энергетики.
ЭКСПЕРИМЕНТАЛЬНАЯ ЧАСТЬ
В качестве объекта исследования выступали порошки Y2.5Nd0.5Al5O12 (YAG) и порошковые композиции YAG–(5, 10 и 20 об. %)MgO.
Порошок YAG был получен методом соосаждения. Водный раствор, содержащий Y(NO3)3, Nd(NO3)3 и Al(NO3)3, смешивали с 5%-ным раствором аммиака. Полученную смесь нагревали для дегидратации при 90°C. Сухой остаток выдерживали при 300, 500, 800 и 1000°C в течение 10 ч на каждой стадии и механически диспергировали после каждого этапа термостатирования. Для получения композитов порошок YAG помещали в водный раствор нитрата магния Mg(NO3)2. Полученную суспензию выдерживали при постоянном перемешивании при температуре 100°C до полного удаления воды. Сухой остаток нагревали при 500°C на воздухе в течение 2 ч до полного завершения образования фазы MgO. Полученную смесь диспергировали с использованием лабораторной планетарной шаровой мономельницы Pulverisette 6 в течение 2 ч. Сушка порошков после размола проводилась в течение 8 ч при температуре 70°C.
Керамику получали на установке Dr.Sinter model SPS-625. Порошки помещали в графитовую пресс-форму диаметром 12 мм и нагревали за счет пропускания миллисекундных импульсов постоянного электрического тока большой мощности (до 3 кА). Режимы спекания представлены в табл. 1.
Таблица 1.
Режимы спекания, плотность и характерные температуры спекания композиционных керамик на основе граната
Материал | Режимы ЭИПС | Плотность | Характерные температуры ЭИПС, °С* | Lmax, мм | Smax × 102, мм/с | ||||||
---|---|---|---|---|---|---|---|---|---|---|---|
vh, °C/мин |
p, МПа |
tЭИПС, °C |
τЭИПС, мин |
г/см3 | % | t0 | t1 | t2 | |||
YAG | 100 | 85 | 1400 | 7 | 4.60 | 98.6 | 1010 | 1335 | 1390 | 2.04 | 1.50 |
YAG–5% MgO | 100 | 85 | 1360 | 7 | 4.85 | 99.1 | 960 | 1240 | 1345 | 1.96 | 0.90 |
YAG–10% MgO | 100 | 85 | 1400 | 7 | 4.82 | 99.5 | 940 | 1240 | 1325 | 2.95 | 1.31 |
YAG–20% MgO | 100 | 85 | 1380 | 7 | 4.67 | 99.2 | 910 | 1235 | 1320 | 2.45 | 1.29 |
Для измерения эффективной усадки при спекании (Leff) использовался дилатометр, входящий в состав установки Dr. Sinter model SPS-625. Истинная усадка (L) рассчитывалась путем вычитания вклада теплового расширения системы машина–образец (ΔL) из величины эффективной усадки Leff. По полученным данным рассчитывалась зависимость скорости усадки от температуры нагрева S(t), по которой определялись температура начала стадии активного спекания (t0); температура t1, соответствующая максимальному значению скорости усадки Smax = S(t = t1); и температура t2, соответствующая окончанию стадии активной усадки.
Фазовый состав керамик изучали методом рентгенофазового анализа (РФА) с использованием дифрактометра Shimadzu LabX XRD-6000. Для изучения микроструктуры образцов использовали растровый электронный микроскоп JEOL JSM-6495 с EDS-микроанализатором Oxford Instruments INCA 350. Плотность полученных керамик измеряли методом гидростатического взвешивания на весах Sartorius CPA.
РЕЗУЛЬТАТЫ И ОБСУЖДЕНИЕ
Полученные порошки представляли собой легко разрушающиеся конгломераты размером от ~1 до ~10 мкм (см. рис. 1). Результаты электронно-микроскопического анализа свидетельствуют о том, что субмикронные частицы MgO синтезировались на поверхности частиц YAG (рис. 2).
Рис. 1.
Изображения микроструктуры конгломератов порошков граната Y2.5Nd0.5Al5O12 (a) и композиций Y2.5Nd0.5Al5O12, содержащих 5 (б), 10 (в) и 20 об. % MgO (г): растровая электронная микроскопия; состояние после синтеза (до механического диспергирования (помола в планетарной мельнице)).
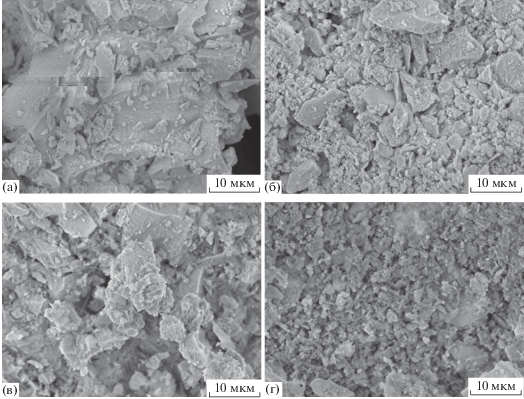
По данным РФА (рис. 3), порошки YAG кристаллизуются в структурном типе граната (пр. гр. Ia3d (ICDD DataBase card no. 79-1891)). Результаты РФА показывают, что композиции YAG–MgO представлены фазами граната и оксида магния (ICDD DataBase card no. 75-0447, пр. гр. Fm$\bar {3}m$).
Рис. 3.
Данные РФА порошков граната Y2.5Nd0.5Al5O12 (1), композиций YAG–5 об. % MgO (2), YAG–10 об. % MgO (3), YAG–20 об. % MgO (4).
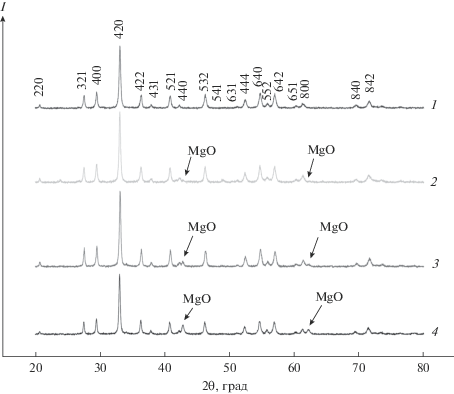
На рис. 4 представлены зависимости усадки и скорости усадки для исследуемых керамик. Из диаграммы спекания порошков YAG следует, что зависимости скорости усадки имеют четырехстадийный характер: стадия I (t ≤ t0), на которой усадка и скорость усадки практически не изменяются при повышении температуры нагрева; стадия II (t0 < t ≤ t1), на которой наблюдается быстрое увеличение усадки и скорости усадки порошков YAG и YAG–MgO; стадия III (t1 < t ≤ t2), на которой наблюдается быстрое уменьшение скорости нагрева; стадия IV (t ≥ t2), когда скорость усадки вновь перестает изменяться. Аналогичный характер L(t) и S(t) наблюдается при спекании композиционных керамик на основе граната с добавками MgO.
Рис. 4.
Зависимости усадки и скорости усадки от температуры спекания керамики Y2.5Nd0.5Al5O12 (a) и композитов с содержанием 5 (б), 10 (в) и 20 об. % MgO (г).
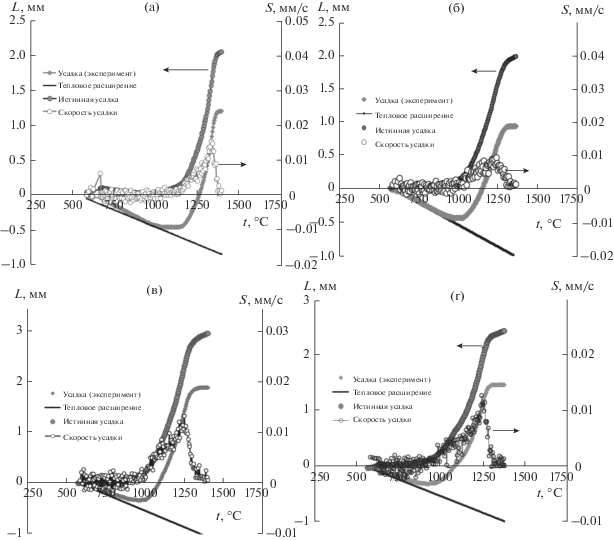
Из диаграмм спекания видно, что температура начала усадки t0 для граната YAG составляет 1010 ± ± 10°С, температура, соответствующая максимуму скорости усадки, составляет t1 = 1335 ± 10°С, а температура, соответствующая окончанию стадии активной усадки, t2 = 1390 ± 15°С (см. табл. 1). При спекании композита YAG + 5% MgO наблюдается незначительное t0 до 960 ± 10°С, а характерные температуры уменьшаются до t1 = 1240 ± ± 10°С и до t2 = 1345 ± 15°С, соответственно. При дальнейшем увеличении содержания оксида магния до 20 об. % значения t0, t1 и t2 уменьшаются до 910 ± 10, 1235 ± 10 и 1320 ± 15°С соответственно.
Анализ результатов РФА показывает, что снижение характерных температур спекания для композиций YAG–MgO обусловлено образованием шпинели: согласно данным РФА (рис. 5), при ЭИПС происходит взаимодействие частиц YAG и MgO, в результате которого образуется шпинель состава MgAl2O4 (ICDD DataBase card no. 70-5187, пр. гр. Fd$\bar {3}m$), а также преобразование граната в форму с тетраэдрической кристаллической структурой (ICDD DataBase card no. 09-0310). Следует отметить, что это неожиданный результат, поскольку предполагается, что в условиях нагрева, близких к равновесным, образование шпинели в тройной системе Al2O3–Y2O3–MgO происходит при температурах более 1700°С [21, 22]. Анализ возможных причин снижения температуры фазового перехода в условиях нестационарного высокоскоростного нагрева выходит за рамки настоящей работы.
Рис. 5.
Данные РФА композитов Y2.5Nd0.5Al5O12–5% MgO (1), Y2.5Nd0.5Al5O12–10% MgO (2), Y2.5Nd0.5Al5O12–20% MgO (3).
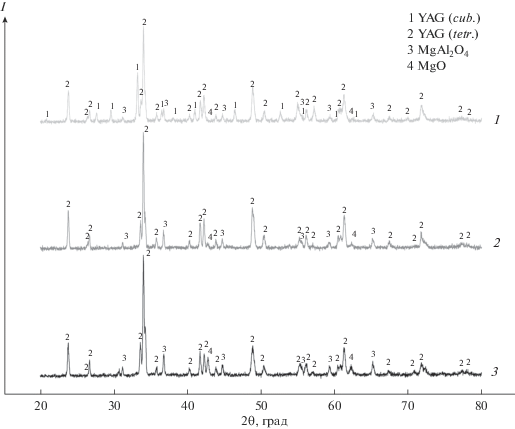
Обобщение представленных в табл. 1 данных показывает, что при введении в гранат добавки MgO наблюдается незначительное повышение плотности – от 98.6 до 99.2–99.5%, а также повышение максимальной усадки Lmax = L(t = tЭИПС) и максимальной скорости усадки Smax = S(t = t2).
Для сравнительного анализа кинетики спекания порошков граната и композитов YAG–MgO зависимости L(t) были преобразованы в графики уплотнения ρ/ρtht, где ρth – теоретическая плотность керамики. Процедура пересчета подробно описана в [13, 23].
Зависимости ρ/ρth(t) имеют трехстадийный характер, типичный для кривых уплотнения при спекании порошковых материалов. Ограничим дальнейший анализ зависимостей ρ/ρth(t) рассмотрением стадии интенсивного уплотнения (область температур t1 < tЭИПС < t2). Величину энергии активации ЭИПС (Qs) можно определить по углу наклона зависимости ρ/ρth(T), представленной в двойных логарифмических координатах: ln(ln[(ρ/ρth)/(1 – ρ/ρth)])–Tm/T, где Tm = = 2243 K – температура плавления граната [24]. (Более подробно процедура расчета энергии спекания описана в работах [13, 23].
Анализ полученных результатов показывает, что температурная зависимость усадки порошков YAG в координатах ln(ln[(ρ/ρth)/(1 – ρ/ρth)])–Tm/T может быть интерполирована прямой линией, угол наклона которой составляет ~35.5 ± 2.5 kTm (~630 ± ± 40 кДж/моль) (см. рис. 6а). Полученные значения Qs близки к энергии активации самодиффузии кислорода в кристаллической решетке граната, величина которой лежит в интервале от 325 до 567 кДж/моль по данным [25, 26]).
Рис. 6.
Зависимости усадки в двойных логарифмических координатах ln(ln[(ρ/ρth)/(1 – ρ/ρth)])–Tm/T для чистого граната (а), композитов YAG–5% MgO (б) и YAG–20% MgO (в).
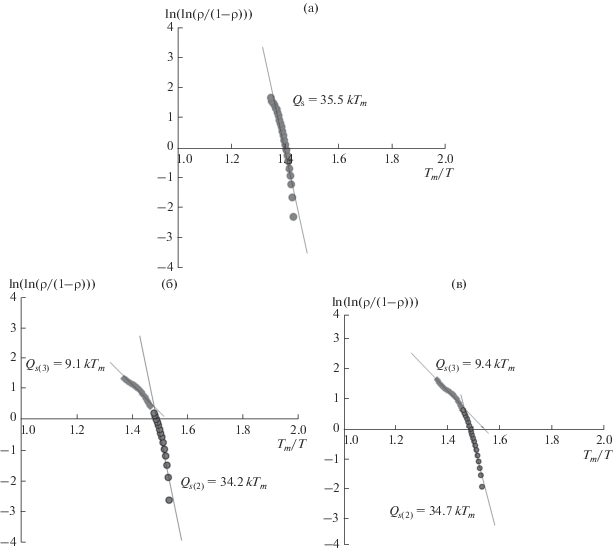
Зависимости для композитов YAG–MgO в координатах ln(ln[(ρ/ρth)/(1 – ρ/ρth)])–Tm/T могут быть интерполированы двумя линиями с различными углами наклона (см. рис. 6б, 6в). В области “низких” температур величина энергии активации спекания композитов YAG–MgO составляет 31.0–34.7 kTm и оказывается близка к энергии активации спекания чистого граната. Энергия активации в области “высоких” температур спекания оказывается существенно ниже и составляет 8.3–9.4 kTm (~147–167 кДж/моль).
Сопоставление полученных значений с литературными данными показывает, что рассчитанные значения энергии активации уплотнения порошков YAG–MgO при повышенных температурах ЭИПС заметно меньше энергии активации ионов магния (360–384 кДж/моль [26, 27]) и кислорода O18 (404–439 кДж/моль [26–28]) в кристаллической решетке шпинели MgAl2O4, но близки к энергии активации зернограничной диффузии ионов магния (139.4–230.5 кДж/моль [26]) и кислорода (262.3 кДж/моль [26]) в оксиде магния MgO, а также близки к энергии активации зернограничной диффузии ионов кислорода O18 в шпинели MgAl2O4 (Qb = 264 кДж/моль [29]).
Причиной снижения энергии активации спекания (Qs) по сравнению с табличными значениями энергии активации зернограничной диффузии может быть рост зерен, приводящий к повышению плотности дефектов на мигрирующих границах зерен мелкозернистых материалов [30]. Ранее данный эффект был подробно исследован при высокоскоростном ЭИПС нанопорошков карбида вольфрама [23].
Дополнительной причиной ускорения спекания могут быть внутренние напряжения, возникающие в композитах YAG-MgO вследствие различий в коэффициентах теплового расширения граната (αYAG = 6.9 × 10–6 °С–1 [31]) и шпинели MgAl2O4 (αMgAl) = 8.5 × 10–6 °С–1 [32]). При охлаждении спеченного композита YAG–MgAl2O4 средний размер частиц шпинели уменьшается на ~20% больше, чем размер частиц YAG. Это приводит к формированию внутренних полей напряжений, величина которых зависит от размера и формы частиц шпинели, а также их объемной доли. Положительное влияние внутренних напряжений на ускорение спекания керамик описано в работе [33].
Следует отметить, что энергия активации ЭИПС мелкозернистых композитов YAG–MgO оказывается меньше энергии обычного спекания крупнозернистых порошков шпинели: при температурах 1300–1500°С Qs составляет 485–494 кДж/моль и близка к энергии активации диффузии кислорода в решетке MgAl2O4 [34, 35].
Таким образом, кинетика ЭИПС мелкозернистого граната и композитов YAG-MgO в области низких температур лимитируется интенсивностью диффузии кислорода в решетке граната, а кинетика ЭИПС мелкозернистых композитов YAG–MgO при повышенных температурах – интенсивностью процесса зернограничной диффузии.
ЗАКЛЮЧЕНИЕ
Исследованы композиционные порошки состава Y2.5Nd0.5Al5O12–(5, 10, 20 об. %) MgO, полученные методом соосаждения и последующего осаждения MgO из водного раствора нитрата магния Mg(NO3)2.
Показано, что ЭИПС позволяет получить керамики YAG–MgO с плотностью 98–99%. Кинетика ЭИПС керамик и композитов при “низких” температурах лимитируется энергией активации диффузии атомов кислорода в решетке граната, а при “высоких” температурах – энергией активации зернограничной диффузии.
Установлено, что при повышении содержания MgO наблюдается уменьшение характерных температур ЭИПС: при увеличении содержания частиц MgO от 0 до 20 об. % температура начала усадки t0 уменьшается от 1010 до 910°С, температура максимума скорости усадки t1 – 1335 до 1255°С, а температура окончания стадии активной усадки t2 уменьшается от 1390 до 1320°С. Продемонстрировано, что ускорение спекания при введении в гранат добавки MgO обусловлено образованием шпинели состава MgAl2O4, а также полиморфным преобразованием кубической решетки граната в тетраэдрическую.
Список литературы
Cocuaud N. et al. Inert Matrices, Uranium-Free Plutonium Fuels and Americium Targets. Synthesis of CAPRA, SPIN and EFTTRA Studies // Proc. Conf. GLOBAL’97. Yokohama (Oct 5–10). 1997. P. 1044–1049.
Chauvin N., Konings R.J., Matzke H. Optimization of Inert Matrix Fuel Concepts for Americium Transmutation // J. Nucl. Mater. 1999. V. 274. № 1–2. P. 105–111.
Neeft E.A.C., Bakker K., Schram R.P.C. et al. The EFTTRA-T3 Irradiation Experiment on Inert Matrix Fuels // J. Nucl. Mater. 2003. V. 320. № 1–2. P. 106–116.
Golovkina L.S., Orlova A.I., Boldin M.S. et al. Development of Composite Ceramic Materials with Improved Thermal Conductivity and Plasticity Based on Garnet-Type Oxide // J. Nucl. Mater. 2017. V. 489. P. 158–163.
Potanina E., Golovkina L., Orlova A. et al. Lanthanide (Nd, Gd) Compounds with Garnet and Monazite Structures. Powders Synthesis by “Wet” Chemistry to Sintering Ceramics by Spark Plasma Sintering // J. Nucl. Mater. 2016. V. 473. P. 93–98.
Golovkina L.S., Orlova A.I., Nokhrin A.V. et al. Ceramics Based on Yttrium Aluminum Garnet Containing Nd and Sm Obtained by Spark Plasma Sintering // Adv. Ceram. Sci. Eng. 2013. V. 2. № 4. P. 161–165.
Томилин С.В., Лизин А.А., Лукиных А.Н. и др. Радиационная и химическая устойчивость алюмоиттриевого граната // Радиохимия. 2011. Т. 53. № 2. С. 162–165.
Лившиц Т.С., Лизин А.А., Джанг Д. и др. Аморфизация редкоземельных алюминатных гранатов при ионном облучении и распаде примеси 244Cm// Геология рудных месторождений. 2010. Т. 52. № 4. С. 297–309.
Gregg D.J., Karatchevtseva I., Triani G. et al. The thermophysical Properties of Calcium and Barium Zirconium Phosphate // J. Nucl. Mater. 2013. V. 441. P. 203–210.
Ryu H.J., Lee Y.W., Cha S.I. et al. Sintering Behaviour and Microstructures of Carbides and Nitrides for the Inert Matrix Fuel by Spark Plasma Sintering // J. Nucl. Mater. 2006. V. 352. P. 341–348.
Kamel N., Aϊt-Amar H., Kamel Z. et al. On the Basic Properties of an Iron-Based Simulated Cermet Inert Matrix Fuel, Synthesized by a Dry Route in Oxidizing Conditions // Progr. Nucl. Eng. 2006. V. 48. P. 590–598.
Wang B., Jiang H., Jia X. et al. Thermal Conductivity of Doped YAG and GGG Laser Crystal // Front. Opt. China. 2008. V. 1. № 1–2. P. 138–141.
Чувильдеев В.Н., Болдин М.С., Дятлова Я.Г. и др. Сравнительное исследование горячего прессования и искрового плазменного спекания порошков Al2O3–ZrO2–Ti(C,N) // Неорган. материалы. 2015. Т. 51. № 10. С. 1128–1134.
Chuvil’deev V.N., Boldin M.S., Nokhrin A.V., Popov A.A. Advanced Materials Obtained by Spark Plasma Sintering // Acta Astron. 2017. V. 135. P. 192–197.
Tokita M. Spark Plasma Sintering (SPS) Method, Systems, and Applications // Handbook of Advanced Ceramics. Academic Press, 2013. P. 1149–1177.
Chuvildeev V.N., Panov D.V., Boldin M.S. et al. Structure and Properties of Advanced Materials Obtained by Spark Plasma Sintering // Acta Astron. 2015. V. 109. P. 172–176.
Орлова А.И., Корытцева А.К., Канунов А.Е. и др. Высокоскоростное электроимпульсное спекание керамических материалов на основе фосфатов со структурой NaZr2(PO4)3 // Неорган. материалы. 2012. Т. 48. № 3. С. 372–377.
Golovkina L.S., Orlova A.I., Chuvil’deev V.N. et al. Spark Plasma Sintering of High-Density Fine-Grained Y2.5Nd0.5Al5O12 + SiC Composite Ceramics // Mater. Res. Bull. 2018. V. 103. P. 211–215.
Golovkina L.S., Orlova A.I., Nokhrin A.V. et al. Spark Plasma Sintering of Fine-Grain Ceramic-Metal Composites Based on Garnet-Structure Oxide Y2.5Nd0.5Al5O12 for Inert Matrix Fuel // Mater. Chem. Phys. 2018. V. 214. P. 516–526.
Шелудяк Ю.Е., Кашпоров Л.Я., Малинин А.А. и др. Теплофизические свойства компонентов горючих систем. М., 1992. 184 с.
Михайлов Г.Г., Макровец Л.А., Смирнов Л.А. Термодинамика процессов взаимодействия магния, алюминия, углерода и иттрия с кислородом в расплаве на основе // Вестн. ЮУрГУ. Сер. Металлургия. 2016. Т. 16. № 3. С. 5–10.
Adylov G.T., Mansurova E.P., Sigalov L.M. Phase relations in air // Dokl. Akad. Nauk USSR. 1988. № 4. P. 29–31.
Chuvil'deev V.N., Blagoveshchenskiy Yu.V., Nokhrin A.V. и дp. Spark Plasma Sintering of Tungsten Carbide Nanopowders Obtained through DC arc Plasma Synthesis // J. Alloys. Compd. 2017. V. 708. P. 547–561.
Андриевский А.Р., Спивак И.И. Прочность тугоплавких соединений и материалов на их основе. Справ. изд. Челябинск: Металлургия, 1989. 368 с.
Haneda H., Miyazawa Y., Shirasaki S. Oxygen Diffusion in Single Crystal Yttrium Aluminum Garnet // J. Cryst. Growth. 1984. V. 68. № 2. P. 581–588.
Diffusion in Non-Metallic Solids (Part 1) / Ed. Beke D.L. Landolt-Börnstein–Group III Condensed Mater. 1999. V. 33B1.
Reddy K.P.R., Cooper A.R. Oxygen Diffusion in Magnesium Aluminate Spinel // J. Am. Ceram. Soc. 1981. V. 64. № 6. P. 368–371.
Ando K., Oishi Y. Self-Diffusion Coefficients of Oxygen Ion in Single Crystals of MgO · n Al2O3 spinels // J. Chem. Phys. 1974. V. 61. № 2. P. 625–629.
Фрос Г.Дж., Эшби М.Ф. Карты механизмов деформации. Челябинск: Металлургия, 1989. 328 с.
Нохрин А.В. Эффект ускорения зернограничной диффузии при рекристаллизации в субмикрокристаллических металлах и сплавах, полученных методом интенсивного пластического деформирования // Письма в ЖТФ. 2012. Т. 38. № 13. С. 70–79.
Foster J.D., Osterink L.M. Index of Refraction and Expansion Thermal Coefficients of Nd:YAG // Appl. Opt. 1968. V. 7. P. 2428–2429.
Kaprálik I. Thermal Expansion of Spinels MgCr2O4, MgAl2O4 and MgFe2O4 // Chem. Zvesti. 1969. V. 23. P. 665–670.
Pelleg J. Diffusion in Ceramics. Series “Solid Mechanics and Its Applications”. Switzerland: Springer, 2016. V. 221. 464 p.
Bratton R.J. Initial Sintering Kinetics of MgAl2O4 // J. Am. Ceram. Soc. 1969. V. 52. № 8. P. 417–419.
Bratton R.J. Sintering and Grain-Growth Kinetics of MgAl2O4 // J. Am. Ceram. Soc. 1971. V. 54. Iss. № 3. P. 141–143.
Дополнительные материалы отсутствуют.
Инструменты
Неорганические материалы