Неорганические материалы, 2019, T. 55, № 1, стр. 11-15
Высокотемпературное окисление материалов на основе MAX-фазы Ti3SiC2, синтезированных методом искрового плазменного спеканияН. В. Севостьянов, О. В. Басаргин, В. Г. Максимов, Н. П. Бурковская
Н. В. Севостьянов 1, *, О. В. Басаргин 1, В. Г. Максимов 1, Н. П. Бурковская 1
1 Всероссийский научно-исследовательский институт авиационных материалов
105005 Москва, ул. Радио, 17, Россия
* E-mail: kolia-phone@mail.ru
Поступила в редакцию 22.02.2018
Аннотация
Проведены высокотемпературные испытания материалов на основе MAX-фазы карбосилицида титана Ti3SiC2, синтезированных методом искрового плазменного спекания (SPS). Установлены закономерности высокотемпературного окисления для образцов как содержащих, так и не содержащих фазу карбосилицида. Показано, что наличие MAX-фазы в составе повышает жаростойкость материала, препятствуя процессу окисления. Показано, что продуктами реакции окисления материалов на основе карбосилицида титана являются оксид титана, монооксид кремния и диоксид углерода.
ВВЕДЕНИЕ
Достижения современной техники обеспечиваются прогрессом в разработке материалов, способных качественно повысить характеристики изделий, улучшив их физико-механические и энергосберегающие свойства, повысив их надежность и снизив стоимость [1–3].
Материалы на основе MAX-фаз представляют большой интерес в связи с сочетанием лучших свойств как металлов, так и керамики. Это высокая электро- и теплопроводность, низкий коэффициент теплового линейного расширения, механическая обрабатываемость [4, 5], стойкость к тепловым ударам, высокий модуль упругости, стойкость к повреждениям [6–8]. Среди них материалы на основе карбосилицида титана Ti3SiC2 считаются наиболее изученными и перспективными и предполагаются для использования в качестве триботехнических материалов, покрытий для защиты от окисления, функциональных элементов конструкций.
Вместе с тем, многие характеристики новых материалов на основе карбосилицида титана Ti3SiC2 являются неизученными, например, влияние их состава (в том числе, допирующих элементов и пассивирующих добавок) на стойкость к высокотемпературному окислению и предельную рабочую температуру [9–12]. Этот вопрос актуален в связи с перспективой эксплуатации в условиях высоких температур и окислительной среды [9].
Синтез карбосилицида титана неизбежно является многостадийным процессом, протекающим с образованием промежуточных и побочных продуктов [13]. В ходе синтеза реакции образования Ti3SiC2 и TiC являются конкурирующими по причине близкого кристаллического строения этих продуктов. Последующие высокотемпературные испытания синтезированных материалов на основе Ti3SiC2 со сложным фазовым составом также предполагают многостадийную реакцию окисления. В работах многих авторов предложены химические реакции таких процессов окисления:
Интересно, что в этих работах наличие среди продуктов реакций соединения SiO2 никакими методами не установлено.
Методов получения карбосилицида титана в настоящее время много: горячее изостатическое прессование [15], вакуумное напыление (PVD) [16–19], химическое осаждение из газовой фазы (CVD) [20], самораспространяющийся высокотемпературный синтез [21]. Одним из оптимальных и перспективных по технологии является метод искрового плазменного спекания (spark plasma synthesis SPS) [13, 22, 23], применяемый в настоящей работе.
Целью работы является установление кинетических закономерностей высокотемпературного окисления на воздухе образцов состава Ti : Si : C = = 3 : 1 : 2 в зависимости от наличия карбосилицида и продуктов окисления.
ЭКСПЕРИМЕНТАЛЬНАЯ ЧАСТЬ
Образцы на основе MAX-фазы карбосилицида титана Ti3SiC2 получали методом порошковой металлургии. Шихта представляла собой смесь порошков титана, кремния и графита молярного состава 3 : 1 : 2 соответственно, подготавливаемую на V-образном смесителе C2K/6.
Синтез образцов карбосилицида титана из подготовленной шихты проводили на установке искрового плазменного спекания KCE®FCTH-HPD 25 при фиксированной температуре. Графитовую пресс-форму с шихтой загружали в вакуумную камеру пресса. Разогрев пресс-формы с шихтой осуществлялся за счет пропускания электрического тока через пресс-форму, одновременно к заготовке прикладывалось постоянное давление. Синтез заготовок осуществлялся при трех температурах: 1300 (образец 1), 1500 (образец 2), 1600°C (образец 3). Заготовку, спеченную искровым плазменным методом при фиксированной температуре, делили на 3 образца с равными значениями суммарной площади поверхности (15 см2), которые проходили испытания на жаростойкость при температурах 1000, 1100, 1200°C. Необходимо отметить, что в случае спекания SPS-методом при температурах 1300 и 1500°C фазовый состав образцов – Ti3SiC2, TiC и Ti5Si3, а при температуре 1600°C – TiC и SiC [13].
Испытания на жаростойкость проводили термогравиметрическим методом по ГОСТ 6130-71 “Металлы. Методы определения жаростойкости” при фиксированных температурах 1000, 1100, 1200°C в муфельной электропечи Nabertherm LT 9/13 суммарно в течение 20 ч с периодическим взвешиванием на аналитических весах VIBRA HT224RCE с точностью до 0.0001 г через каждые 2 ч выдержки.
Для рентгенофазового анализа поверхностного слоя образцов после температурных испытаний использовали дифрактометр ДРОН-3 с медным анодом, сканирование проводили в диапазоне углов от 15° до 70° с шагом 0.05° и выдержкой 2 с. Морфологию поверхности окалины изучали на оптическом микроскопе Olympus BX-51, исследование структуры поперечного среза проводили на электронном растровом микроскопе Hitachi SU 8010, оснащенном энергодисперсионным детектором Oxford Instruments X-Max N.
РЕЗУЛЬТАТЫ И ОБСУЖДЕНИЕ
Зависимости удельного прироста массы (на единицу площади образца) от времени в процессе испытаний на стойкость к окислению, представленные на рис. 1, показывают сильное влияние на процесс окисления как температур синтеза образцов, так и самих температур испытаний.
Рис. 1.
Зависимости прироста удельной массы образцов (на единицу площади) от времени испытаний Δm/S (τ) для температур испытаний: а –1000, б – 1100, в – 1200°C для образцов 1, 2 и 3 и для различных температур испытаний для образца 2 (г).
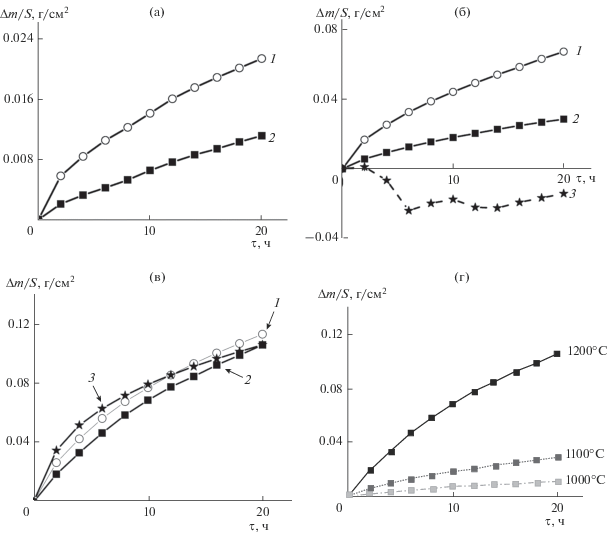
Хорошую стойкость к окислению при температуре 1000°C показывают образцы 1 и 2 (синтез при 1300 и 1500°C, рис. 1а), после выдержки в течение 20 ч они сохраняют свою целостность. Образец 3 (спекание при 1600°C) при этой температуре окисляется с образованием рыхлой окалины, не сцепленной с основой, которая осыпается с поверхности, не защищая образец от дальнейшего окисления. Этот процесс характеризуется линейной зависимостью потери массы от времени, в результате чего образец полностью разрушился за 6 ч испытаний.
Повышение температуры испытаний до 1100°C (рис. 1б) образцов 1 и 2 приводит к увеличению скорости окисления относительно температуры 1000°C примерно в два раза (для образца 2 см. также рис. 1г).
Поведение образца 3 в испытаниях на жаростойкость при температуре 1100°C качественно отличается от поведения образцов 1 и 2. Первые 14 ч на поверхности образца образовывается рыхлая, осыпающаяся окалина, не защищающая от дальнейшего окисления (рис. 1б), что приводит к уменьшению массы образца. После 14 ч испытаний на поверхности образца формируется плотная, хорошо сцепленная с основой оксидная пленка и масса образца постепенно увеличивается.
Отличие поведения образцов 1, 2 от 3 в одинаковых высокотемпературных испытаниях объясняется различным фазовым составом этих образцов, синтезированных при разных температурах. В образцах 1 и 2 (спекание при 1300 и 1500°С) MAX-фаза Ti3SiC2 присутствует, в образце 3 ее нет. Таким образом, испытания на жаростойкость при температурах 1000 и 1100°C позволяют предположить защитные свойства Ti3SiC2 в составе исследуемых материалов.
Поведение всех образцов при температуре испытания 1200°C практически совпало (рис. 1в). На их поверхности образовалась плотная оксидная пленка крупнокристаллического строения с высокой адгезией к основе. Одинаковый характер процесса окисления при 1200°C для всех образцов свидетельствует об изменении устойчивости Ti3SiC2 (присутствующего в образцах 1 и 2) к окислению при этой температуре. Скорость окисления образца 2, содержащего эту фазу, возрастает в 5 раз при изменении температуры испытаний с 1100 до 1200°C (рис. 1г).
Исследование морфологии поверхности образцов 2 после испытаний при различных температурах показали формирование оксидных пленок крупнокристаллического строения, различимых невооруженным глазом. На микрофотографиях поверхности оксидных слоев (рис. 2) видна зависимость размеров кристаллов от температуры испытания: для более высоких температур характерны кристаллы большего размера. Также на микрофотографиях видно, что особенностью строения кристаллов оксидной пленки является срез в двух непараллельных плоскостях, что может быть следствием двойникования, типичного для природы рутила [24].
Рис. 2.
Морфология окисленной поверхности образцов 2 после испытаний при 1000 (а), 1100 (б), 1200°C (в) (съемка проводилась в скрещенных поляризаторах).
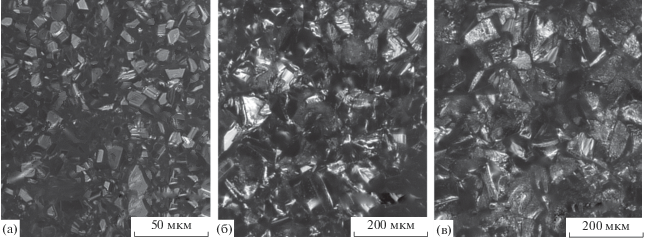
РФА самой оксидной пленки показал наличие в ней только рутила (рис. 3). Слой материала, расположенный непосредственно под оксидной пленкой, содержал титан, кремний и углерод, как в материале до окисления [13]. Таким образом, весь слой, подвергшийся окислению, превратился в оксид титана и летучий монооксид кремния [5, 14].
Рис. 3.
Дифрактограммa оксидного слоя материала на основе Ti3SiC2 (1) и штрих-рентгенограмма рутила TiO2 [26] (2).
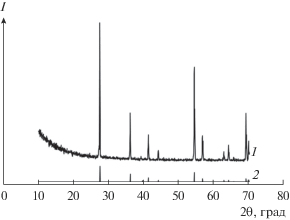
Известно, что при высокотемпературном окислении силицидов в восстановительных условиях (титан и углерод – сильнейшие восстановители) образуется летучее соединение кремния SiO (низший оксид) [25]. Результирующие уравнения окисления можно представить в виде:
СЭМ-изображения профилей окисленных слоев (рис. 4) образцов 1 и 3 после выдержки при температуре 1000°C в течение 2 ч демонстрируют различные механизмы высокотемпературного окисления в зависимости от фазового состава образцов. Характерна значительная разница в толщине оксидных слоев. Материал, синтезированный при 1300°C, покрыт тонкой оксидной пленкой, при этом видны участки с глубоким проникновением TiO2 вглубь (рис. 4а). Микрорентгеноспектральный анализ показал, что на границе раздела исходного и окисленного материала концентрируется карбосилицид титана Ti3SiC2, затрудняющий диффузию кислорода и дальнейшее окисление. Остальные фазы, имеющиеся в структуре материала (TiC и Ti5Si3), подвергаются окислению, в результате чего наблюдается прорастание оксида титана в глубь материала в виде лучей.
Рис. 4.
СЭМ-изображения профиля материала после высокотемпературных испытаний: а – образец 1, б – образец 3; стрелкой показана граница раздела окисленной и неокисленной частей.

Оксидный слой на образце 3 (синтезирован при температуре 1600°C) толще и более равномерен по толщине (рис. 4б). По данным микрорентгеноспектрального и рентгенофазового анализов, в материале отсутствует карбосилицид титана, а содержащиеся фазы TiC и SiC не препятствуют высокотемпературному окислению. Слой на поверхности состоит из оксида титана, а в глубине имеет включения карбида кремния. При более длительной высокотемпературной выдержке конечный продукт окисления состоит только из оксида титана.
ЗАКЛЮЧЕНИЕ
Наличие MAX-фазы Ti3SiC2 в составе материала улучшает его жаростойкость до температуры 1200°C. Фаза Ti3SiC2 служит преградой для диффузии кислорода вглубь, предотвращая процесс окисления. Установлено, что рабочая температура 1200°C для материалов на основе MAX-фазы Ti3SiC2 является предельной. При этой температуре наличие карбосилицида титана не дает преимуществ в стойкости к окислению материала.
Показано, что при температуре испытаний 1200°C процесс окисления одинаков для материалов Ti : Si : C = 3 : 1 : 2 независимо от фазового состава. Карбосилицид титана также выступает модификатором роста оксида титана, формируя плотную, хорошо сцепленную с основой пленку.
Высокотемпературное окисление материалов состава Ti : Si : C = 3 : 1 : 2 приводит к образованию летучего SiO из-за присутствия сильных восстановителей (Ti, C). Одновременно на их поверхности образуется слой оксида титана.
БЛАГОДАРНОСТЬ
Работа выполнена в рамках реализации комплексного научного направления № 12 “Металломатричные и полиматричные композиционные материалы” [1].
Список литературы
Каблов Е.Н. Инновационные разработки ФГУП “ВИАМ” ГНЦ РФ по реализации “Стратегических направлений развития материалов и технологий их переработки на период до 2030 года” // Авиационные материалы и технологии. 2015. № 1. С. 3–33.
Каблов Е.Н. Современные материалы – основа инновационной модернизации России // Материалы Евразии. 2012. № 3. С. 10–15.
Каблов Е.Н., Гращенков Д.В., Исаева Н.В., Солнцев С.С., Севастьянов В.Г. Перспективные высокотемпературные керамические композиционные материалы // Рос. хим. журн. 2010. Т. 54. № 1. С. 20–24.
Barsoum M.W. The M(N+1)AX(N) Phases: a New Class of Solids; Thermodynamically Stable Nanolaminates // Prog. Solid State Chem. 2000. V. 28. P. 201–281.
Barsoum M.W., El-Raghy T. Synthesis and Characterization of a Remarkable Ceramic: Ti3SiC2 // J. Am. Ceram. Soc. 1996. V. 79. P. 1953–1956.
Zhou Y.C., Sun Z.M. Microstructure and Mechanism of Damage Tolerance for Ti3SiC2 Bulk Ceramics // Mater. Res. Innov. 1999. V. 2. P. 360–363.
Low I.M., Lee S.K., Lawn B.R. Contact Damage Accumulation in Ti3SiC2 // J. Am. Ceram. Soc. 1998. V. 81. P. 225–228.
Bao Y.W., Zhou Y.C., Zhang H.B. Investigation on Reliability of Nanolayer-Grained Ti3SiC2 via Weibull Statistics // J. Mater. Sci. 2007. V. 42. P. 4470–4475.
Zhang H.B., Wang X., Berthold C., Nickel K.G., Zhou Y.C. Effect of Al Dopant on the Hydrothermal Oxidation Behavior of Ti3SiC2 Powders // J. Eur. Ceram. Soc. 2009. V. 29. P. 2097–2103.
Barsoum M.W., Brodkin D., El-Raghy T. Layeredmachinable Ceramics for High Temperature Applications // Scr. Mater. 1997. V. 36. № 5. P. 535–541.
Pang W.K., Low I.M., Prince K.E., Atanacio A.J. Mapping of Elemental Composition in Air-Oxidized Ti3SiC2 // J. Austr. Ceram. Soc. 2008. V. 44. № 2. P. 52–55.
Надуткин А.В., Истомин П.В., Рябков Ю.И. Окисление на воздухе материалов на основе Ti3SiC2 // Керамика и композиционные материалы: докл. VI Всерос. науч. конф. Сыктывкар, 2007. С. 53.
Гращенков Д.В., Севостьянов Н.В., Ефимочкин И.Ю., Бурковская Н.П. Синтез карбосилицида титана Ti3SiC2 методом искрового плазменного спекания // Конструкции из композиционных материалов. 2016. № 4. С. 23–26.
Stumpf K.M., Fey T., Greil P. Thermochemical Calculations of the Stability of Ti2AlC in Various Atmospheres // J. Ceram. Sci. Technol. 2016. V. 3. № 7. P 223–228.
Raghy T.El., Barsoum M.W. Processing and Mechanical Properties of Ti3SiC2. Reaction Path and Microstructure Evolution // J. Am. Ceram. Soc. 1999. V. 82. P. 2849–2053.
Лучанинов А.А., Стрельницкий В.Е. Покрытия системы Ti–Al–N, нанесенные PVD методами // ФИП. 2012. Т. 10. № 1. С. 5–24.
Мубояджян С.А., Будиновский С.А., Гаямов А.М., Матвеев П.В. Высокотемпературные жаростойкие покрытия и жаростойкие слои для теплозащитных покрытий // Авиационные материалы и технологии. 2013. № 1. С. 17–20.
Мубояджян С.А., Будиновский С.А., Гаямов А.М., Смирнов А.А. Получение керамических теплозащитных покрытий для рабочих лопаток турбин авиационных ГТД магнетронным методом // Авиационные материалы и технологии. 2012. № 4. С. 3–8.
Каблов Е.Н., Мубояджян С.А. Теплозащитные покрытия для лопаток турбины высокого давления перспективных ГТД // Металлы. 2012. № 1. С. 5–13.
Истомина Е.И. Силицирование карбидов титана и оксикарбидов титана газообразным монооксидом кремния: Автореф. дис. … канд. хим. наук. Сыктывкар: Институт химии Коми научного центра УрО РАН, 2013. 20 с.
Hendaoui A., Andasmas M., Amara A., Benaldjia A., Langlois P., Vrel D. SHS of High-Purity MAX Compounds in the Ti–Al–C System // Int. J. Self-Propagating High-Temp. Synthesis. 2008. V. 17. № 2. P. 129–134.
Ghosh N.Ch. Synthesis and Tribological Characterization of in situ Spark Plasma Sintered Ti3SiC2 and Ti3SiC2–TiC Composites // Degree of Master of Science. Dhaka, 2009. P. 105.
Сорокин О.Ю., Солнцев С.Ст., Евдокимов С.А., Осин И.В. Метод гибридного искрового плазменного спекания: принцип, возможности, перспективы применения // Авиационные материалы и технологии. 2014. № S6. С. 11–16.
Минералогическая энциклопедия / Под ред. Фрея К.: Пер. с англ. Л.: Недра, 1985. 512 с.
Техника высоких температур / Под общ. ред. Кемпбелла И.Э.; Пер. с англ. Маураха М.А.; Под. ред. Елютина В.П. М.: Иностранная лит., 1959. 596 с.
CardInformation: PDFNumber: 21-1276.
Дополнительные материалы отсутствуют.
Инструменты
Неорганические материалы