Неорганические материалы, 2019, T. 55, № 11, стр. 1241-1247
Моделирование глубокой очистки пентакарбонила железа в дистилляционной установке вертикального типа
В. А. Шапошников 1, Ю. С. Белозеров 1, Ю. П. Кириллов 1, *, А. Д. Буланов 1, А. М. Потапов 1, М. О. Стешин 1
1 Институт химии высокочистых веществ им. Г.Г. Девятых Российской академии наук
603950 Нижний Новгород, ул. Тропинина, 49, Россия
* E-mail: kirillov@ihps.nnov.ru
Поступила в редакцию 01.04.2019
После доработки 15.05.2019
Принята к публикации 22.05.2019
Аннотация
Представлена математическая модель глубокой очистки веществ дистилляцией в закрытой испарительно-конденсационной системе, в которой конденсация пара осуществляется на вертикально стекающей пленке жидкости. Механизмы испарения, переноса пара, конденсации, движения сконденсированной жидкости, диффузии примеси в испаряемой жидкости рассмотрены совместно. На примере очистки пентакарбонила железа от примеси кобальта установлены зависимости глубины очистки от температур испарения и конденсации, площади испарения, доли испарившейся жидкости, радиуса и высоты конденсационной трубки. По экспериментальным зависимостям эффективного коэффициента разделения от температуры с применением математической модели определены величины коэффициентов диффузии и равновесных коэффициентов разделения примесей кобальта, вольфрама и хрома в пентакарбониле железа.
ВВЕДЕНИЕ
Пентакарбонил железа используется в качестве исходного соединения для получения высокодисперсных порошков железа с низким содержанием примесей, получения оксидов железа в виде порошков, пленок, покрытий, нитевидных металлических монокристаллов, железосодержащих органических комплексов, изотопного разделения [1–6]. В железе, получаемом из карбонила железа, присутствуют примеси углерода, азота и кислорода в составе соответственно карбида Fe3C, нитрида Fe4N и оксидов Fe3O4 и Fe2O3 и примеси элементов, способных к образованию карбонилов, таких как никель, хром, кобальт, молибден, вольфрам [7]. Для снижения содержания примесей пентакарбонил железа очищается методами простой перегонки и ректификации при пониженном давлении или в атмосфере инертного газа [8, 9]. Метод простой перегонки является простейшим, но достаточно эффективным методом очистки пентакарбонила железа от большинства углеводородных примесей, а также от ряда карбонилов металлов. При простой перегонке жидкость испаряется, образовавшийся пар отводится из зоны испарения и далее конденсируется на охлаждаемой поверхности в зоне конденсации. В предельных случаях конденсация пара может осуществляться преимущественно на свободной поверхности жидкости [10, 11] или преимущественно на поверхности вертикально стекающей пленки жидкости [12]. Первый предельный случай реализуется в дистилляционных установках горизонтального типа [13], второй – вертикального типа [7]. В закрытых дистилляционных установках процессы испарения, отвода пара и конденсации взаимосвязаны. Поэтому скорость испарения в замкнутой испарительно-конденсационной системе может быть рассчитана только при совместном рассмотрении этих процессов. В дистилляционных установках вертикального типа в отличие от установок горизонтального типа скорость испарения зависит еще от подвижности стекающего конденсата. Процессы конденсации пара на поверхности жидкости, стекающей вниз по вертикальной трубе, рассматривались в работах [12, 14–16]. Предложена [12] простая приближенная математическая модель конденсационного процесса, которая в совокупности с уравнениями испарения и отвода пара позволила рассчитать скорость испарения в дистилляционной установке вертикального типа. Следующим шагом в изучении дистилляционных процессов является моделирование непосредственно процесса очистки в установках этого типа.
Цель настоящей работы – развить математическую модель процесса дистилляционной очистки веществ в закрытых испарительно-конденсационных установках с учетом механизма конденсации пара на вертикально стекающей пленке жидкости и на конкретном примере очистки пентакарбонила железа от примеси кобальта установить зависимости глубины очистки от температур испарения, конденсации и основных конструкционных параметров дистилляционного аппарата вертикального типа.
ТЕОРЕТИЧЕСКАЯ ЧАСТЬ
Рассмотрим процесс глубокой очистки пентакарбонила железа в дистилляционном аппарате, схема которого приведена на рис. 1.
Рис. 1.
Схема дистилляционного аппарата: 1 – куб, 2 – отборочная камера, 3 – холодильник, 4 – термостат, 5 – загрузочная трубка.
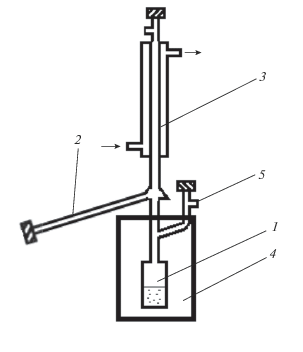
Исходный пентакарбонил железа помещают через загрузочную трубку 5 в камеру 1 с заданной температурой испарения Т1. Из камеры вертикально вверх выходит теплоизолированная трубка, по которой пар поступает в зону охлаждения 3. Зона охлаждения представляет собой вертикально расположенную трубку, обтекаемую проточной водой заданной температуры Т2 < T1. Поступивший в зону охлаждения пар конденсируется на верхнем торце цилиндрической трубки и на ее боковой поверхности. С закрытого торца трубки при малом его уклоне образовавшийся конденсат поступает на боковую поверхность трубки и далее по ней стекает вниз. По мере стекания толщина пленки жидкости увеличивается за счет дополнительной конденсации пара. Образующийся на стенках охлаждаемой трубки конденсат стекает в отборочную камеру 2. Объединенный испарительно-конденсационный процесс, включающий в себя испарение со свободной поверхности жидкости в камере 1, массоперенос пара по вертикальной трубке из камеры 1 в зону охлаждения 3, конденсацию пара на поверхности жидкости, стекающей вниз по охлаждаемой трубке, рассмотрен в [12]. Уравнения стационарного массопереноса имеют следующий вид:
(2)
${\rho }\left[ {v{\text{grad}}(v)} \right] = - {\text{grad}}p + {\eta }\Delta v + \frac{{\eta }}{3}{\text{grad}}\,{\text{div}}v,$(5)
$\begin{gathered} {{\left. v \right|}_{{{{{\sigma }}_{{\text{1}}}}}}} = \frac{M}{{{{{\rho }}_{{\text{1}}}}}}{{L}_{{{\text{исп}}}}} = \frac{{R{{T}_{1}}}}{{{{p}_{1}}}}{{L}_{{{\text{исп}}}}} = \\ = R{{T}_{1}}{{L}_{{{\text{исп}}}}}{{\left( {p_{1}^{0} - \frac{1}{k}\sqrt {2{\pi }MR{{T}_{1}}} {{L}_{{{\text{исп}}}}}} \right)}^{{ - 1}}}, \\ \end{gathered} $(6)
${{\left. p \right|}_{{{{{\sigma }}_{{\text{1}}}}}}} = {{p}_{1}} = p_{1}^{0} - \frac{1}{k}\sqrt {2{\pi }MR{{T}_{1}}} {{L}_{{{\text{исп}}}}},$(7)
${{\left. p \right|}_{{{{{\sigma }}_{{\text{2}}}}}}} = {{p}_{2}} = p_{2}^{0} + \frac{1}{k}\sqrt {2{\pi }MR{{T}_{2}}} {{L}_{{{\text{конд}}}}},$(8)
${{L}_{{{\text{исп}}}}}{{S}_{{{\text{исп}}}}} = {{L}_{{{\text{конд}}}}}\left( {{\pi }R_{n}^{2} + \sum\limits_{i = 1}^n {2{\pi }{{R}_{i}}dz} } \right),$(9)
${{Q}_{i}} = \frac{{{\pi }{{{\rho }}^{2}}gR_{0}^{4}}}{{2{\eta }}}\left( {\frac{1}{4} - {{{\left( {\frac{{{{R}_{i}}}}{{{{R}_{0}}}}} \right)}}^{2}} + \left( {\frac{3}{4} - \ln \left( {\frac{{{{R}_{i}}}}{{{{R}_{0}}}}} \right)} \right){{{\left( {\frac{{{{R}_{i}}}}{{{{R}_{0}}}}} \right)}}^{4}}} \right).$При переходе от i-й к (i – 1)-й ячейке к расходу (9) добавляется поток жидкости
сконденсировавшейся на боковой поверхности i‑го кольца. В n-й ячейке к боковому потоку добавляется поток жидкости, сконденсировавшейся на верхнем основании цилиндра при z = H0 и равный ${{L}_{{{\text{конд}}}}}{\pi }R_{n}^{2}.$ В результате имеем уравнения
Из условия полного обращения паровой фазы в жидкую в зоне конденсации для первой ячейки получаем
Система разностных уравнений (8)–(13) позволяет рассчитать внутренние радиусы колец Ri и скорость конденсации пара Lконд, если задана скорость испарения Lисп. Для того чтобы определить ее величину, необходимо решить совместно систему уравнений (1)–(13). Решение может быть найдено, например, по методике, изложенной в работе [10].
Что касается поведения примеси в очищаемой жидкости, то заметим, что эффект очистки обусловлен различием в составах разделяемой жидкой смеси и образующегося из нее пара. При испарении находящаяся в жидкости примесь перераспределяется с течением времени в результате диффузии, оттока через поверхность испарения и уменьшения объема жидкости. Для расчета глубины очистки можно применить диффузионную модель [19]
(14)
$\frac{{\partial C}}{{\partial {\tau }}} = D\frac{{{{\partial }^{2}}C}}{{\partial {{x}^{2}}}} + w\frac{{\partial C}}{{\partial x}},$(15)
${{\left. {D\frac{{\partial C}}{{\partial x}}} \right|}_{{x = 0}}} + {{\left. {w(1 - {\alpha })C} \right|}_{{x = 0}}} = 0,$Уравнение (14) характеризует изменение концентрации примеси С(τ, x) внутри исходной жидкости, (15) – на верхней ее границе (поверхность испарения), (16) – на нижней границе (дно кубовой емкости), (17) – начальное распределение примеси в жидкости. Кроме того, в уравнениях (14)–(17) τ – время, с; x – координата, направленная по нормали от поверхности испарения в глубь жидкости, м; D – коэффициент диффузии примеси, м2/с; α = Сп/Сж – равновесный коэффициент разделения; w – скорость перемещения границы раздела фаз, м/с; С0– начальная концентрация, моль/м3; Сп и Сж – концентрация примеси вблизи границы раздела фаз в паре и кубовой жидкости соответственно, моль/м3; X0 = V0/Sисп, V0 – начальный объем жидкости, м3; Sисп – площадь испарения, м2.
Скорость перемещения границы w связана со скоростью испарения Lисп следующим соотношением:
где ρж – плотность кубовой жидкости.Глубину очистки веществ удобно количественно характеризовать фактором разделения F = С0/Спрод, где С0 и Спрод – концентрация примеси в исходной смеси и конечном продукте соответственно [8, 11, 19]. Продуктом является дистиллят, если примесь труднолетучая, или кубовый остаток, если примесь легколетучая.
ЭКСПЕРИМЕНТАЛЬНАЯ ЧАСТЬ
В [7] представлены общая схема и описание дистилляционной установки для фракционной разгонки пентакарбонила железа. Показанная на рис. 1 схема испарительно-конденсационной системы является частью этой общей схемы. Целью экспериментов было определение температурных зависимостей эффективного коэффициента разделения труднолетучих примесей кобальта, вольфрама, хрома в пентакарбониле железа и сопоставление экспериментальных данных с результатами теоретических расчетов. Для экспериментов использовался пентакарбонил железа производства ООО “Синтез-ПКЖ” (г. Дзержинск), полученный в соответствии с ТУ 2436-051-05807977-99 и содержащий не менее 93 мас. % основного вещества. Эксперименты проводили следующим образом.
В предварительно промытый (последовательно фтористоводородной кислотой марки ОСЧ 27-5, бидистиллированной водой, ацетоном квалификации “ос. ч.”) и вакуумированный испаритель (куб цилиндрической формы высотой 115 и внутренним диаметром 43 мм) загружали пентакарбонил железа массой 73.580 г. Испаритель помещали в термостат с регулируемой температурой. Температуру в ходе серии экспериментов изменяли в диапазоне 50–68°С. Давление в системе составляло 20 мм рт. ст. и контролировалось при помощи образцового мановакуумметра с классом точности 0.25. Пары пентакарбонила железа конденсировались в цилиндрической трубке высотой 163 и диаметром 14 мм, охлаждаемой проточной водой с температурой 20°С. Конденсат стекал по поверхности трубки в отборочную камеру с предварительно нанесенной меткой для отбора фиксированного объема дистиллята. После первого его заполнения в приемнике конденсата открывали кран и сливали дистиллят в предварительно вакуумированную приемную ампулу. Ампула взвешивалась на аналитических весах класса точности 4 с пределом погрешности ±20 мг до и после заполнения. Разность масс составила 4.640 г. Эта величина в дальнейшем использовалась для фиксации доли испарившейся жидкости и расчета скорости испарения. Далее пентакарбонил железа выдерживали в испарителе в течение 1.5 ч для установления стационарного режима испарения. Скопившуюся за это время в приемнике конденсата жидкость сливали в ампулу. Далее продолжали процесс испарения и при помощи секундомера определяли время заполнения фиксированного объема приемника. Для каждой температуры время заполнения измерялось 3 раза. По измеренным временам заполнения и фиксированной массе 4.640 г рассчитывалась средняя скорость испарения. Процесс дистилляции продолжали до момента, когда доля отобранной жидкости достигала величины 0.85.
Далее брались пробы на анализ на содержание примесей кобальта, вольфрама, хрома. Анализ проводился методом масс-спектрометрии высокого разрешения с индуктивно-связанной плазмой. Полученные данные для различных температур использовались для расчета эффективного коэффициента разделения αэф = Ск/Сср, где Ск – средняя концентрация примеси в конденсате, Сср – средняя концентрация примеси в кубовой жидкости.
Вычислительные эксперименты проводились с применением математической модели (1)–(18). Вычисления проводились в следующей последовательности. Сначала методом доверительных областей (Trust-Region Dogleg Method) [20] решались уравнения (8)–(13) при некотором заданном значении Lисп. Затем методом конечных объемов [21] решалась краевая задача (1)–(7) по методике, предложенной в [10]. В результате определялись соответствующие заданным температурам испарения и конденсации величины скорости испарения Lисп для закрытой испарительно-конденсационной установки (рис. 1). Найденные значения Lисп далее использовались при решении уравнений (14)–(18) методом “ловли фронта в узел сетки” [22]. Необходимые для расчета физико-химические характеристики, температурная зависимость давления насыщенного пара пентакарбонила железа
Уравнения математической модели (1)–(18) использованы для расчета процесса очистки пентакарбонила железа от примесей кобальта, вольфрама и хрома. Коэффициент испарения k = 5.5 × 10–4 пентакарбонила железа в дистилляционной установке, схема которой приведена на рис. 1, был определен ранее [12]. Значение равновесного коэффициента разделения α = Сп/Сж = 0.042 системы пентакарбонил железа – примесь кобальта приведено в [24]. Для примесей вольфрама и хрома в литературе нет данных о величинах равновесных коэффициентов разделения в пентакарбониле железа.
РЕЗУЛЬТАТЫ И ОБСУЖДЕНИЕ
В табл. 1 приведены значения величины, обратной эффективному коэффициенту разделения, рассчитанные по экспериментально измеренным значениям концентраций примесей кобальта, вольфрама и хрома при различных температурах. При Т1 = 291.6 К для кобальта значение эффективного коэффициента разделения равно значению равновесного коэффициента α = 0.042, которое измерено отдельно при равновесных условиях и приведено в работе [24].
Таблица 1.
Значения величины, обратной эффективному коэффициенту разделения для примесей кобальта, вольфрама, хрома при различных температурах
Температура, К | 1/αэф | ||
---|---|---|---|
Co | W | Cr | |
291.6 | 23.8 [25 ] | – | – |
323 | 3.55 | 4.34 | 2.96 |
328 | 3.49 | 1.93 | 1.36 |
338 | 1.31 | 1.96 | 1.54 |
341 | 1.26 | 1.10 | 1.01 |
На рис. 2 приведена зависимость величины, обратной эффективному коэффициенту разделения αэф, от температуры испарения Т1. Сравнивая теоретические кривые с экспериментальными точками, отметим, что теоретические расчеты согласуются с экспериментальными данными. Путем решения обратной задачи из условия минимума среднеквадратичного отклонения теоретической кривой от экспериментальных данных (рис. 2) для примеси кобальта получено значение коэффициента диффузии D = 3.1 × 10–9 м2/с. Найденное значение далее использовалось как начальное приближение для определения коэффициентов диффузии, а также равновесных коэффициентов разделения примесей вольфрама и хрома (табл. 2).
Рис. 2.
Зависимости величины, обратной эффективному коэффициенту разделения 1/αэф, от температуры испарения Т1 для кобальта, вольфрама и хрома: сплошные линии – расчет по уравнениям (1)–(19); T2 = 293 К; D = 3.1 × 10–9 м2/с.
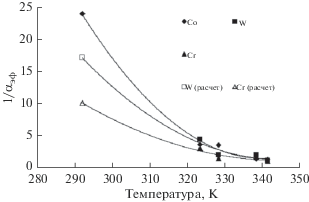
Таблица 2.
Значения равновесного коэффициента разделения и коэффициента диффузии для примесей кобальта, вольфрама, хрома
Примесь | Co | W | Cr |
α | 0.042[25 ] | 0.059 | 0.1 |
D × 109, м2/с | 3.1 | 3.0 | 2.0 |
Труднолетучие примеси кобальта, вольфрама, хрома концентрируются в жидкой фазе. В этом случае продуктом очистки является дистиллят, для которого Спрод = Сд. Тогда для фактора разделения F = С0/Спрод получаем [11]
(20)
$F = \frac{V}{{{{V}_{0}}}}{{\left( {1 - \int\limits_0^{{{1\, - \,V} \mathord{\left/ {\vphantom {{1\, - \,V} {{{V}_{0}}}}} \right. \kern-0em} {{{V}_{0}}}}} {\frac{{C(V,u)}}{{{{C}_{0}}}}{\text{d}}u} } \right)}^{{ - 1}}},$(21)
$F = \frac{{{V \mathord{\left/ {\vphantom {V {{{V}_{0}}}}} \right. \kern-0em} {{{V}_{0}}}}}}{{1 - {{{(1 - {V \mathord{\left/ {\vphantom {V {{{V}_{0}}}}} \right. \kern-0em} {{{V}_{0}}}})}}^{{\alpha }}}}}.$Для примеси кобальта на рис. 3–6 показаны зависимости фактора разделения от доли отбора, площади испарения, радиуса и высоты конденсационной трубки при различных температурах испарения. Из рисунков следует, что фактор разделения увеличивается при уменьшении доли отбора, сближении температур испарения и конденсации, увеличении площади испарения, уменьшении радиуса и высоты конденсационной трубки. Фактор разделения принимает предельные значения, если для жидкости выполняются условия полного перемешивания. В этом случае фактор разделения зависит только от доли отбора и равновесного коэффициента разделения. Максимальное значение фактора разделения не превышает величины, равной обратному равновесному коэффициенту разделения.
Рис. 3.
Зависимости фактора разделения F от доли отбора v = V/V0 при различных температурах испарения T1, K: 1 – 293.5, 2 – 297, 3 – 301, 4 – 323, 5 – 341; пунктирная линия 6 – расчет по уравнению (21); T2 = 293 K.
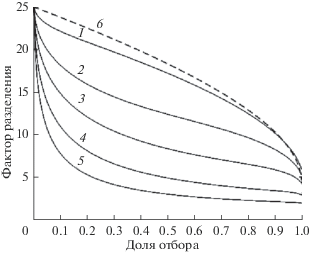
Рис. 4.
Расчетные зависимости фактора разделения F от площади испарения Sисп при различных температурах испарения Т1, K: 1 – 293.5, 2 – 297, 3 – 301, 4 – 323, 5 – 341; V/V0 = 0.85.
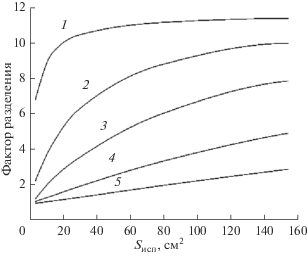
ЗАКЛЮЧЕНИЕ
Представлена математическая модель глубокой очистки веществ методом простой перегонки с учетом диффузии примеси в жидкости и конденсации пара на вертикально стекающей пленке жидкости. Верификация модели проведена по экспериментальным температурным зависимостям эффективного коэффициента разделения при очистке пентакарбонила железа от примесей кобальта, вольфрама и хрома.
Модель позволяет рассчитать распределение примеси в жидкости, распределение скоростей течения в пленке, утолщение пленки при конденсации, распределение скоростей газового потока в пространстве от поверхности испарения до поверхности конденсации, эффективный коэффициент разделения, фактор разделения при различных значениях температуры испарения, конденсации, доли отогнанной при испарении жидкости, равновесного коэффициента разделения, коэффициента диффузии примеси и конструкционных параметров дистилляционной установки вертикального типа. Кроме того, модель позволяет путем решения обратной задачи идентифицировать величины коэффициента диффузии и равновесного коэффициента разделения присутствующих в очищаемых веществах примесей.
На примере примеси кобальта продемонстрированы основные характерные закономерности дистилляционной очистки пентакарбонила железа. Для примесей кобальта, вольфрама и хрома определены значения равновесного коэффициента разделения и коэффициента диффузии.
Список литературы
Волков В.Л., Сыркин В.Г., Толмасский И.С. Карбонильное железо. М.: Металлургия, 1969. 256 с.
Maruyama T., Shinyashiki Y. Iron-Iron Oxide Composite Thin Films Prepared by Chemical Vapor Deposition from Iron Pentacarbonyl // Thin Solid Films. 1998. V. 333. № 1–2. P. 203–206. https://doi.org/10.1016/S0040-6090(98)00999-7
van Worterghem J., Mørup S., Charles S.W. et al. Formation and Chemical Stability of Metallic Glass Particles Prepared by Thermolysys of Fe(CO)5 // Hyperfine Interact.1986. V. 27 № 1. P. 333–336. https://doi.org/10.1007/BF02354774
Comprehensive Organometallic Chemistry. V. 4 / Ed. Wilkinson G. et al. Abel.: Elsevier Science Ltd., 1982. 1064 c.
Wiesli R.A., Beard B.L., Braterman P.S. et al. Iron Isotope Fractionation between Liquid and Vapor Phases of Iron Pentacarbonyl // Talanta. 2007. V. 71. № 1. P. 90–96. https://doi.org/10.1016/j.talanta.2006.03.026
Кузнецов В.И. Металлоорганические соединения в разделении стабильных изотопов. М.: Альфа-Лабл, 2001. 200 с.
Белозеров Ю.С., Буланов А.Д., Потапов А.М., Созин А.Ю., Стешин М.О., Чернова О.Ю. Глубокая очистка пентакарбонила железа дистилляционными методами // Неорган. материалы. 2017. T. 53. С. 1129–1134. № 10. https://doi.org/10.7868/S0002337X17100177
Девятых Г.Г., Еллиев Ю.Е. Введение в теорию глубокой очистки веществ. М.: Наука, 1981. 320 с.
Гельперин Н.И. Основные процессы и аппараты химической технологии. М.: Химия, 1981. 812 с.
Кириллов Ю.П., Шапошников В.А., Кузнецов Л.А., Ширяев В.С., Чурбанов М.Ф. Моделирование испарения жидких веществ и конденсации их паров при дистилляции // Неорган. материалы. 2016. Т. 52. № 11. С. 1256–1261. https://doi.org/10.7868/S0002337X161100063
Кириллов Ю.П., Шапошников В.А., Чурбанов М.Ф. Моделирование глубокой очистки веществ дистилляционным методом простой перегонки // Неорган. материалы. 2017. Т. 53. № 8. С. 867–873. https://doi.org/10.7868/S0002337X17080127
Шапошников В.А., Белозеров Ю.С., Кириллов Ю.П., Буланов А.Д., Чурбанов М.Ф. Моделирование испарения пентакарбонила железа в условиях конденсации его паров на вертикально стекающей пленке жидкости // Неорган. материалы, 2018. Т. 54. № 9. С. 929–935. https://doi.org/10.1134/S0002337x18090154
Ширяев В.С., Пименов В.Г., Липатова М.М., Евдокимов И.И., Чурбанов М.Ф., Кириллов Ю.П., Корноухов В.Н. Очистка селена от примеси бария вакуумной дистилляцией // Неорган. материалы. 2010. Т. 46. № 3. С. 365–369.
Lee K.-Y., Kim M.H. Experimantal and Empirical Study of Steam Condensation Heat Transfer with a Noncondensable Gas in a Small-Diameter Vertical Tube // Nucl. Eng. Des. 2008. V. 238. № 1. P. 207–216. https://doi.org/10.1016/j.nucengdes.2007.07.001
Hammami Y.El., Feddaoui M., Mediouni T., Mir A. Numerical Study of Condensing a Small Condensation of Vapour Inside a Vertical Tube // Heat Mass Transf. 2012. V. 48. № 9. P. 1675–1685. https://doi.org/10.1007/s00231-012-1011-0
Adil Charef, M’barek Feddaoui, Monssif Najim, Hicham Meftah. Liquid Film Condensation from Water Vapour Flowing Downward along a Vertical Tube // Desalination. 2017. V. 409. P. 21–23. https://doi.org/10.1016/j.desal.2017.01.018
Кнаке О., Странский И.Н. Механизм испарения // Успехи физ. наук. 1959. Т. 68. № 6. С. 261–305.
Ивановский М.Н., Сорокин В.П., Субботин В.И. Испарение и конденсация металлов. М.: Атомиздат, 1976. 216 с.
Кириллов Ю.П., Кузнецов Л.А., Шапошников В.А., Чурбанов М.Ф. Влияние диффузии на глубину очистки веществ дистилляцией // Неорган. материалы. 2015. Т. 51. № 11. С. 1177–1182. https://doi.org/10.7868/S0002337X15100085
Powell M.J.D. A Fortran Subroutine for Solving Systems of Nonlinear Algebraic Equations. London: H.M. Stationery Office, 1968. 55 p.
Флетчер К. Вычислительные методы в динамике жидкостей. М.: Мир, 1991. 552 с.
Будак Б.М., Соловьев Е.Н., Успенский А.Б. Разностный метод со сглаживанием коэффициентов для решения задач Стефана // Журн. вычислительной математики и математической физики. 1965. Т. 5. № 5. С. 828–840.
Yaws C.L., Satyro M.A. Vapor Pressure – Inorganic Compounds // The Yaws Handbook of Vapor Pressure: Antoine Coefficients (Second Edition). Elsevier Inc., 2015. P. 315–322. https://doi.org/10.1016/C2014-0-03590-3
Шарова Т.В., Леонов М.Р. Изучение возможности выделения микропримесей никеля и кобальта из карбонила железа методами экстракции и дистилляции // Получение и анализ чистых веществ. Горький: Изд-во ГГУ, 1987. С. 53.
Дополнительные материалы отсутствуют.
Инструменты
Неорганические материалы