Неорганические материалы, 2019, T. 55, № 3, стр. 271-282
Получение высокочистого оксида алюминия путем механохимического окисления алюминия в 0.1 М растворе KOH с последующими химической и термической обработками
Г. Н. Амбарян 1, *, М. С. Власкин 1, А. З. Жук 1, Е. И. Школьников 1
1 Объединенный институт высоких температур Российской академии наук
125412 Москва, Ижорская ул., 13, стр. 2, Россия
* E-mail: ambaryan1991@gmail.com
Поступила в редакцию 18.07.2017
После доработки 15.10.2018
Принята к публикации 19.09.2018
Аннотация
Исследована возможность получения высокочистого оксида алюминия путем окисления гранулированного алюминия в 0.1 М растворе гидроксида калия с последующими термической и кислотной обработками продуктов окисления. Продукт окисления алюминия, представленный двумя модификациями Al(OH)3 (байеритом и гиббситом), был предварительно прокален при температурах 300, 600, 900 или 1200°С, затем обработан соляной кислотой и отожжен при температуре 1450°С. Установлено, что с увеличением температуры предварительной термообработки суммарная концентрация примесей, включая примесь железа, увеличивается, а концентрация щелочных металлов (K, Na, Li), наоборот, уменьшается. Из алюминия с чистотой 99.7% был получен оксид алюминия с чистотой на уровне 99.886%. Из алюминия с чистотой 99.98% был получен оксид алюминия с чистотой на уровне 99.993%.
ВВЕДЕНИЕ
Одним из продуктов, востребованных на рынке особо чистых неорганических веществ, является высокочистый оксид алюминия. Он применяется для получения высококачественной оптической керамики [1, 2], монокристаллического алюмо-иттриевого граната [3], синтетического сапфира, огнеупорных изделий, используемых в производстве особо чистых материалов, а также носителей катализаторов и сорбентов.
Промышленный способ получения оксида алюминия, известный как процесс Байера, обеспечивает химическую чистоту оксида алюминия, как правило, не выше 99.7% и не удовлетворяет требованиям ряда современных неметаллургических производств, где суммарное содержание примесей не должно превышать единиц и десятков ppm. Именно это обстоятельство обусловило ряд работ, посвященных разработке способов получения оксида алюминия высокой чистоты (ОАВЧ).
Основным промышленным способом получения ОАВЧ (с чистотой 99.99–99.999 мас. %) является алкоголятная технология [4–6], в которой промежуточным веществом служит изопропилат алюминия, получаемый в результате взаимодействия алюминия с изопропиловым спиртом в присутствии катализатора [7, 8]. В качестве альтернативных способов можно отметить получение и термическое разложение нитрата алюминия [9], электрохимическое растворение алюминия с последующей термообработкой [10, 11] и гидротермальный метод [12–14]. Во всех перечисленных случаях в качестве исходного химического сырья для получения ОАВЧ используется алюминий. Это связано, в том числе, с тем, что алюминий является химически активным металлом, промышленное производство которого исчисляется десятками миллионов тонн в год.
В качестве варианта, в котором исходным сырьем служит оксид алюминия, отметим способ [15], в котором различные фазы гидроксида алюминия растворяются в концентрированной соляной кислоте с образованием растворимого хлорида алюминия, после чего раствор отделяется от нерастворенных твердых примесей и осуществляется кристаллизация хлорида алюминия и его термическая обработка. Данный способ был разработан для прямой переработки минерального сырья, однако достигнутая максимальная химическая чистота не удовлетворяет современным требованиям. Основной причиной является то, что вместе с хлоридом алюминия в процессе его растворения образуются также растворимые хлориды примесных атомов, которые остаются в продукте после кристаллизации.
Алюминий в качестве исходного сырья для получения ОАВЧ более предпочтителен, чем его оксид, в том числе потому, что его чистота может быть дополнительно повышена с 99.7 до 99.99% в ходе промышленного процесса трехслойного электролиза. Энергозатратность электролитического рафинирования (процесса Хупса) не превышает энергозатратность процесса получения первичного алюминия (процесса Холла–Эру) [16]. При добавлении кислорода к алюминию с чистотой 99.99% (суммарным содержанием примесей 100 ppm) теоретически можно получить оксид с чистотой ~99.995% (суммарным содержанием примесей 50 ppm), так как из 1 кг алюминия получается около 2 кг оксида и, соответственно, количество примесей в единицах ppm уменьшается вдвое. Однако на практике осуществить реакцию прямого окисления в чистом кислороде или воде без каких-либо добавок или катализаторов оказывается не так просто [17].
Относительно недавно был предложен способ окисления гранулированного алюминия в низкопроцентных растворах щелочей при интенсивном перемешивании, в котором щелочь выступала в качестве катализатора процесса окисления [18, 19]. Образующийся алюминат в конкретных экспериментальных условиях быстро распадался на гидроксид алюминия и щелочь, которая затем участвовала в окислении следующей порции алюминия. На примере калиевой щелочи были определены оптимальные скорость перемешивания, начальная концентрация щелочи в растворе (0.1 М) и массовое отношение водного раствора к алюминию (α = 4), обеспечивающие высокую степень превращения алюминия (более 80%).
Также относительно недавно была показана возможность очистки оксида алюминия в ходе высокотемпературного вакуумного прокаливания [20, 21]. Данный процесс основан на диффузии примесей к поверхности кристалла (поверхностной сегрегации) и их последующим испарении [22]. В качестве исходного сырья использовался микронный порошок алюминия, окисление которого осуществлялось в гидротермальных условиях при температуре около 300°С и давлении 10 МПа.
Данная работа посвящена исследованию возможности получения высокочистого оксида алюминия путем механохимического окисления алюминия в 0.1 М растворе гидроксида калия с последующими химической и термической обработками гидроксида алюминия и других его соединений. Выбор КОН обусловлен относительно низкими температурами испарения оксида и алюминатов калия. Промежуточная термическая обработка проводилась с целью понижения концентрации примесей в объеме кристалла и повышения их концентрации у поверхности. Кислотная обработка (HCl) применялась для растворения и отделения предположительно более загрязненного примесями поверхностного слоя гидроксида или оксида. Предположение основывается, в том числе, на результатах работы [23], в которой на примере гидроксида алюминия, полученного с использованием процесса Байера, показано, что примеси щелочных металлов в виде алюминатов сконцентрированы у поверхности.
ЭКСПЕРИМЕНТАЛЬНАЯ ЧАСТЬ
Химические реактивы. Для наработки гидроксида алюминия путем окисления алюминия в 0.1 М растворе гидроксида калия использовался алюминий гранулированный двух марок: А7 с содержанием алюминия 99.7% и А98 с содержанием алюминия 99.98% (Русал), содержание примесей в исходном алюминии представлены в табл. 1 . Внешний вид алюминия разных марок был одинаков (рис. 1). Окисление проводилось в водном 0.1 М растворе KOH. Для приготовления раствора использовался особо чистый 30%-ный водный раствор KOH (Компонент-реактив). Массовое отношение водного раствора к алюминию составляло α = 4. Для промывки полученного гидроксида алюминия использовали соляную кислоту квалификации “ос. ч.” (Компонент-реактив) с концентрацией 5%. В экспериментах использовалась дистиллированная вода.
Таблица 1.
Содержание примесей (мас. %) в исходном алюминии марок А7 и А98 (ГОСТ 11069-2001 алюминий первичный)
Марка алюминия | А7 | А98 |
---|---|---|
Al, % (не менее) | 99.7 | 99.98 |
Si, % (не более) | 0.15 | 0.0035 |
Fe, % (не более) | 0.16 | 0.0056 |
Cu, % (не более) | 0.01 | 0.0016 |
Мn, % (не более) | 0.03 | 0.002 |
Mg, % (не более) | 0.02 | 0.002 |
Zn, % (не более) | 0.04 | 0.003 |
Gа, % (не более) | 0.03 | 0.003 |
Тi, % (не более) | 0.01 | 0.002 |
Прочие примеси (каждой в отдельности), % (не более) | 0.02 | 0.001 |
Наработка гидроксида алюминия проводилась на установке, схема которой представлена на рис. 2. Установка состоит из стеклянного реактора Lenz объемом 1 л с термостатирующей рубашкой, вход и выход которой соединены с термостатом Huber CC 308В силиконовыми шлангами для поддержки постоянной температуры в реакторе; верхнеприводной мешалки IKA Eurostar 60digital с перемешивающим элементом якорного типа; холодильника для возврата сконденсировавшегося водяного пара в реакционную среду; барботера в виде склянки Дрекселя.
Рис. 2.
Схема установки для наработки гидроксида алюминия: 1 – термостат, 2 – верхнеприводная мешалка, 3 – обратный холодильник, 4 – реактор, 5 – барботер.
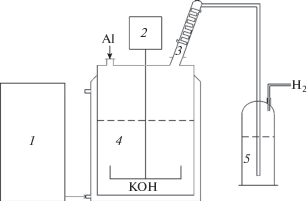
Перед непосредственно окислением алюминиевые гранулы проходили обработку в ультразвуковой ванне. Ультразвуковое воздействие использовалось для очистки поверхности гранул от органических и механических загрязнений. Затем приготавливался водный раствор гидроксида калия с заданной концентрацией щелочи и с помощью мерной стеклянной емкости в объеме 600 мл заливался в реактор. В реактор после его нагрева и термостатирования загружалась навеска алюминия массой 150 г. Реактор был утеплен теплоизолирующим материалом для поддержания постоянной температуры. После герметизации реактора включалась верхнеприводная мешалка со скоростью вращения 400 об./мин, в результате чего запускалась реакция окисления алюминия. Образующийся в ходе окисления алюминия водород наблюдался по пузырькам в барботере. Эксперимент проводился в изотермическом режиме при температуре 90°C и атмосферном давлении. Продолжительность процесса окисления составляла 5 ч. Важной особенностью эксперимента по окислению алюминия являлось то, что реакция осуществлялась при интенсивном перемешивании, что способствовало механическому трению гранул алюминия друг о друга и, соответственно, дополнительной активации реакции за счет снятия оксидной пленки с поверхности алюминия. Полученная в ходе эксперимента суспензия отделялась от непрореагировавшего алюминия с помощью лабораторного сита (ячейка 500 мкм) с последующей стадией вакуумной фильтрации. После фильтрации гидроксид алюминия промывался дистиллированной водой до нейтральной среды pH ~ 7 и помещался в вакуумный сушильный шкаф Binder серии VD. Степень превращения алюминия определялась, как в работе [18].
После сушки образца осуществлялась либо его термообработка, либо кислотная обработка. Обобщенная блок-схема проведения экспериментов представлена на рис. 3.
Термическая обработка. Для термической обработки образец оксида или гидроксида алюминия массой 25 г помещался в корундовый тигель, который устанавливался в муфельной печи. Время выдержки при максимальной температуре во всех экспериментах с промежуточной термообработкой было одинаковым и составляло 1 ч. Время выдержки при температуре 1450°С составляло 3 ч.
Для термообработки использовались муфельная печь LHT 08/16 (Nabertherm) с дисилицидмолибденовыми нагревателями и корундовый тигель объемом 80 см3. Масса образцов в ходе исследования измерялась с помощью аналитических весов Sartorius Cubis MSA324S.
Кислотная обработка. Полученный гидроксид алюминия после стадии окисления и сушки, а также продукты промежуточной термообработки были обработаны в 5%-ном растворе соляной кислоты в стеклянной колбе объемом 500 мл с перемешиванием на магнитном перемешивающем устройстве IKA C-MAG HS 7 в течение 2.5 ч. После этого образцы фильтровались при пониженном давлении. После фильтрации осадок промывался дистиллированной водой до нейтральной среды pH ~ 7 и помещался в вакуумный сушильный шкаф Binder.
Промывка гидроксида алюминия в водном растворе соляной кислоты обеспечивает частичный перевод железа и щелочных металлов, а также их оксидов, содержащихся в гидроксиде алюминия, в соответствующие хлориды, некоторые из которых растворяются в воде. Отделение гидроксида алюминия от раствора соляной кислоты после такой промывки способствует дополнительной очистке целевого продукта от примесей, поскольку хлориды некоторых металлов (например, железа) имеют, как правило, более низкую температуру кипения (сублимации) при атмосферном давлении, чем их оксиды, и при дальнейшем прокаливании в муфельной печи температура кипения (сублимации) хлоридов будет ниже, чем оксидов соответствующих металлов, следовательно, и очистка от примесей будет наиболее полной при термообработке.
Рентгенофазовый анализ. Фазовый состав образцов изучался методом рентгеновской дифракции на дифрактометре Thermo ARL XTRA с использованием CuKα-излучения (λ = 0.15418 нм). Спектры рентгеновской дифракции снимались в интервале углов 2θ = 10°–100° с шагом сканирования 0.75 град/мин. Идентификация фазового состава образцов осуществлялась с помощью программного комплекса Maud. Область когерентного рассеяния вычислялась с помощью уравнения Шеррера.
Масс-спектрометрический анализ. Методика определения примесных элементов в порошках бемита и оксидов алюминия основана на использовании масс-спектрометрии с индуктивно связанной плазмой (ИСП-МС, X-Series II Thermo Scientific, США) с предварительным растворением вещества. Анализируемый оксид алюминия в количестве 25 мг смачивали 0.03%-ным раствором изовинилового спирта и прессовали (давление ~500 МПа) в течение 30 мин. Полученный компактный образец α-Al2O3 помещали на предметный столик в ячейку лазерной приставки. В качестве внутреннего стандарта при масс-спектральных измерениях использовали 27Al. Концентрации элементов получали усреднением по всем определяемым изотопам с учетом их распространенности. Для каждого образца проводили по пять измерений, результаты усредняли и вычисляли стандартное отклонение. Для контроля и проверки правильности разработанной методики использовали независимый метод, основанный на растворении образцов α-Al2O3 массой 100 мг в смеси 1 мл H2SO4 и 1 мл H3PO4 в течение 6 ч при давлении 140 МПа и температуре 320°C в кварцевых закрытых пробирках. Растворы переносили в пластиковые пробирки, объем каждого раствора доводили до 10 мл. Результаты трех параллельных измерений усредняли. Погрешность определения для элементов составляла не более 30% [24].
Сканирующая электронная микроскопия. Морфология поверхности образцов изучалась на сканирующем электронном микроскопе JEOL JSM-7401F. Образцы в микроскопе размещались на углеродной подложке. Съемка образцов проводилась при ускоряющем напряжении 1 кВ.
РЕЗУЛЬТАТЫ И ОБСУЖДЕНИЕ
Алюминий марки А7 (99.7%). Алюминий гранулированный марки А7 был окислен при температуре 90°C в водном растворе гидроксида калия с концентрацией 0.1 М. Степень превращения алюминия составила 82%. После отделения полученного гидроксида алюминия от неокисленного алюминия, а также фильтрации и сушки, проводили термообработку и кислотную обработку.
Полученный в результате окисления гидроксид алюминия вначале проходил промежуточную термическую обработку при температурах 300, 600, 900 или 1200°С. После этого продукт подвергался кислотной обработке, а затем прокалке при температуре 1450°С для образования α-Al2O3. Полученный гидроксид алюминия также подвергался кислотной обработке без предварительной термической обработки с последующей прокалкой при температуре 1450°С. Кроме того, был получен образец α-Al2O3 путем прямого прокаливания продукта окисления при температуре 1450°С. Блок-схема процессов термообработки и кислотной обработки для продукта окисления алюминия марки А7 показана на рис. 4.
Рис. 4.
Блок-схема процессов термообработки и кислотной обработки продукта окисления алюминия марки А7 (образцы оксида алюминия 1.1–1.6 отправлялись на масс-спектрометрический анализ).
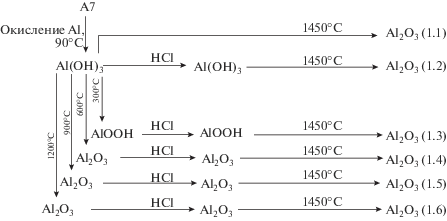
При температуре 300°С, согласно [25], гидроксид алюминия должен переходить преимущественно в оксигидроксид алюминия (AlOOH):
При температуре обжига выше 600°С гидроксид переходит в одну из кристаллических фаз оксида (γ-, δ-, θ- или α-Al2O3):
В результате рентгенофазового анализа продукта окисления алюминия было установлено, что доминирующей кристаллической фазой в нем является Al(OH)3, представленный двумя модификациями: байеритом и гиббситом. Небольшая часть Al(OH)3 находится в рентгеноаморфном состоянии (размер областей когерентного рассеяния не превышает 1 нм). После термообработки при 300°С к уже перечисленным кристаллическим фазам добавляется бемит (AlOOH). После термообработки при температурах 600 и 900°С доминирующими кристаллическими фазами в образцах являются γ-, δ- и θ-Al2O3. После термообработки при температурах 1200 и 1450°С доминирует α-Al2O3.
В ходе кислотной обработки соляная кислота взаимодействовала с поверхностью оксида (гидроксида) алюминия с образованием хлоридов:
В табл. 2 представлены массы соединений, полученных в результате окисления алюминия с последовательными химической и термической обработками. Перед взвешиванием все образцы высушивались до достижения постоянного значения массы при температуре 120°С. Во всех сериях экспериментов исходная масса продукта окисления Al(OH)3 составляла 25 г, конечным продуктом являлся оксид алюминия, прошедший термическую обработку при температуре 1450°С.
Таблица 2.
Результаты измерения масс образцов, полученных в ходе термической и кислотной обработок продукта окисления алюминия марки А7 (исходная масса продукта окисления Al(OH)3 в каждой серии экспериментов составляла 25 г)
Серия | Процесс | Масса, г | Отношение масс | |
---|---|---|---|---|
до | после | |||
1.1 | Термообработка продукта окисления Al(OH)3 при 1450°C | 25 | 15.98 | 0.64 |
1.2 | Кислотная обработка продукта окисления Al(OH)3 | 25 | 20.25 | 0.81 |
Термообработка Al(OH)3 при 1450°C | 20.25 | 13.16 | 0.65 | |
1.3 | Термообработка продукта окисления Al(OH)3 при 300°C | 25 | 19.04 | 0.76 |
Кислотная обработка AlOOH | 19.04 | 16.49 | 0.87 | |
Термообработка AlOOH при 1450°C | 16.49 | 14.01 | 0.85 | |
1.4 | Термообработка продукта окисления Al(OH)3 при 600°C | 25 | 16.19 | 0.65 |
Кислотная обработка Al2O3 | 16.19 | 15.80 | 0.98 | |
Термообработка Al2O3 при 1450°C | 15.80 | 15.05 | 0.95 | |
1.5 | Термообработка продукта окисления Al(OH)3 при 900°C | 25 | 16.21 | 0.65 |
Кислотная обработка Al2O3 | 16.21 | 15.70 | 0.97 | |
Термообработка Al2O3 при 1450°C | 15.70 | 15.18 | 0.97 | |
1.6 | Термообработка продукта окисления Al(OH)3 при 1200°C | 25 | 16.08 | 0.64 |
Кислотная обработка Al2O3 | 16.08 | 15.75 | 0.98 | |
Термообработка Al2O3 при 1450°C | 15.75 | 15.61 | 0.99 |
Из результатов измерения масс образцов можно видеть, что с увеличением температуры предварительной термической обработки масса конечного продукта увеличивается. Это объясняется тем, что с увеличением температуры продукт меньше растворяется в соляной кислоте. Промывка в кислоте гидроксида Al(OH)3 и оксигидроксида алюминия AlOOH приводит к наибольшему уменьшению массы, отношение масс после и до кислотной обработки составляeт 0.81 и 0.87 соответственно. Для экспериментов с кислотной обработкой оксида алюминия, полученного при 600–1200°С, отношение масс после и до кислотной обработки составляет 0.97–0.98. Из результатов измерения масс образцов также следует, что в случае кислотной обработки непосредственно продукта окисления Al(OH)3 или оксигидроксида алюминия AlOOH теряется значительная часть массы конечного продукта – до 17.6 или 12.3% соответственно (в сравнении с массой образца 1.1). В случае кислотной обработки оксида алюминия, полученного при 600–1200°С, в итоге теряется от 2.3% (для 1200°С) до 5.8% (для 600°С).
Результаты масс-спектрометрического анализа образцов оксида алюминия, полученных из алюминия марки А7, представлены в табл. 3 . Наибольшая суммарная концентрация примесей наблюдается в образце 1.1, полученном из продукта окисления алюминия напрямую путем обжига при температуре 1450°С. Наименьшая суммарная концентрация примесей представлена в образце 1.2, полученном в результате последовательных кислотной обработки и прокаливания при температуре 1450°С (без предварительной термообработки). Уменьшение суммарной концентрации примесей достигнуто за счет уменьшения содержания железа в образце. Снижение концентрации железа может объясняться тем, что примесь, находящаяся на границе зерен гидроксида алюминия, распределенного по всему объему, в результате кислотной обработки растворяется в водном растворе соляной кислоты.
Предварительная термообработка привела к увеличению содержания железа в конечном продукте по сравнению с образцом 1.2. Причем с увеличением температуры предварительной термообработки концентрация примеси железа увеличивалась. Возможно, с повышением температуры железо переходит в более стабильную форму оксида железа и во время взаимодействия с соляной кислотой не растворяется и не переходит в хлорид железа. Также это может быть связано с диффузией железа в объем кристалла в результате предварительной термообработки, о чем свидетельствуют результаты работ [26, 27].
Концентрация таких примесей, как титан и ванадий, с увеличением температуры предварительной обработки практически не изменяется. Небольшое снижение примесного состава после кислотных промывок связано с пропорциональным растворением гидроксида алюминия и равномерно распределенных в нем примесей [25, 26]. Примеси Ti, V, Cr являются наиболее проблемными с точки зрения очистки оксида алюминия методом высокотемпературного прокаливания [20].
Концентрация щелочных металлов (K, Na, Li), как видно из результатов исследования, с увеличением температуры предварительной термообработки уменьшается. Это связано с диффузией этих примесей к поверхности кристалла, что также показано в работе [21]. С увеличением температуры скорость диффузии увеличивается. Поэтому повышение температуры предварительной термообработки приводит к уменьшению содержания примесей K, Na и Li в объеме кристалла и увеличению их концентрации у поверхности. Кислотная промывка после предварительной термообработки способствует удалению данных примесей из продукта, о чем и свидетельствуют результаты, представленные в табл. 3 . Можно отметить, что для примеси Na практически полное удаление (менее 1 ppm) достигается при температуре предварительной термообработки 900°С. Концентрация примеси калия была уменьшена по сравнению с образцом 1.1 более чем в два раза при температуре предварительной термообработки 900°С и более чем в 4 раза при 1200°С.
Таблица 3.
Результаты масс-спектрометрического анализа образцов оксида алюминия 1.1–1.6
Элемент | ПО, ppm | С, ppm | |||||
---|---|---|---|---|---|---|---|
1.1 | 1.2 | 1.3 | 1.4 | 1.5 | 1.6 | ||
Li | 0.03 | 0.27 ± 0.1 | 0.74 ± 0.2 | 2.6 ± 0.7 | 2.1 ± 0.5 | 1.0 ± 0.3 | 0.8 ± 0.2 |
Be | 0.02 | 0.028 | <ПО | <ПО | <ПО | <ПО | <ПО |
B | 1.0 | <ПО | <ПО | <ПО | <ПО | <ПО | <ПО |
Na | 1.0 | 20.5 ± 5.8 | 13.8 ± 3.6 | 21.1 ± 6.2 | 14.8 ± 4.0 | <ПО | <ПО |
Mg | 1.0 | 61.6 ± 9.1 | 44.8 ± 6.3 | 25.6 ± 4.0 | 24.1 ± 3.5 | 41.9 ± 6.3 | 40.9 ± 6.7 |
Al | Основа | Основа | Основа | Основа | Основа | Основа | Основа |
K | 1.0 | 225 ± 27.3 | 231 ± 27.4 | 86.8 ± 9.8 | 72.7 ± 8.8 | 97.9 ± 11.9 | 49.3 ± 6.3 |
Ca | 3.0 | <ПО | <ПО | <ПО | <ПО | <ПО | <ПО |
Sc | 0.3 | <ПО | <ПО | <ПО | <ПО | <ПО | <ПО |
Ti | 1.0 | 18.9 ± 2.5 | 13.8 ± 1.8 | 13.6 ± 1.8 | 12.6 ± 1.7 | 12.1 ± 1.6 | 13.9 ± 1.8 |
V | 1.0 | 3.8 ± 0.8 | 3.5 ± 0.8 | 3.4 ± 0.9 | 3.5 ± 0.8 | 3.2 ± 0.7 | 3.1 ± 0.7 |
Cr | 0.1 | 5.6 ± 1.5 | 5.0 ± 1.4 | 6.7 ± 1.8 | 7.1 ± 2.0 | 7.2 ± 2.1 | 8.2 ± 2.3 |
Mn | 0.1 | 16.6 | 14.0 | 9.1 | 8.6 | 10.2 | 13.9 |
Fe | 2.0 | 1555 ± 268 | 717 ± 130 | 959 ± 169 | 1058 ± 184 | 1263 ± 225 | 1332 ± 224 |
Co | 0.2 | 0.31 | <ПО | 0.30 | 0.29 | 0.34 | 0.31 |
Ni | 1.0 | 5.5 | 1.4 | 5.6 | 5.8 | 6.7 | 6.3 |
Cu | 0.5 | 28.6 | <ПО | 9.7 | 9.5 | 9.2 | 12.8 |
Zn | 0.2 | 59.4 ± 7.4 | 42.5 ± 5.5 | 54.1 ± 6.7 | 50.6 ± 6.3 | 47.0 ± 5.9 | 37.6 ± 4.7 |
Ga | 0.2 | 40.0 | 37.6 | 46.2 | 47.2 | 47.0 | 46.6 |
As | 0.1 | <ПО | <ПО | <ПО | <ПО | <ПО | <ПО |
Se | 0.4 | <ПО | <ПО | <ПО | <ПО | <ПО | <ПО |
Rb | 0.02 | <ПО | <ПО | <ПО | <ПО | <ПО | <ПО |
Sr | 0.07 | <ПО | <ПО | <ПО | <ПО | <ПО | <ПО |
Y | 0.02 | <ПО | <ПО | 0.028 | 0.024 | 0.036 | 0.043 |
Zr | 0.06 | 1.5 | 1.4 | 1.4 | 1.5 | 1.5 | 1.5 |
Nb | 0.1 | <ПО | <ПО | <ПО | <ПО | <ПО | <ПО |
Mo | 0.07 | 5.3 | 12.9 | 49.5 | 49.6 | 40.7 | 15.5 |
Rh | 0.01 | <ПО | <ПО | <ПО | <ПО | <ПО | <ПО |
Pd | 0.04 | <ПО | <ПО | <ПО | <ПО | <ПО | <ПО |
Ag | 0.05 | <ПО | <ПО | <ПО | <ПО | <ПО | <ПО |
Cd | 0.04 | <ПО | <ПО | <ПО | <ПО | <ПО | <ПО |
Sn | 0.1 | 2.2 | 2.1 | 2.6 | 2.3 | 2.0 | 2.1 |
Ta | 0.09 | <ПО | <ПО | <ПО | <ПО | <ПО | <ПО |
W | 0.03 | 0.13 | 0.22 | 0.19 | 0.20 | 0.20 | 0.25 |
Сумма | 2050.24 | 1141.76 | 1297.52 | 1370.51 | 1591.18 | 1585.10 |
Концентрации Cu и Co минимальны в случае кислотной обработки продукта окисления, а предварительная термообработка приводит к увеличению их концентраций. Концентрация Mg и Mn минимальна при температурах предварительной термообработки 300–600°C. Концентрация Zn, Ga, Zr, Sn, W практически не меняется. Концентрация B, Ca, Sc, As, Se, Rb, Sr, Y, Nb, Rh, Pd, Ag, Cd, Ta находится ниже предела определения масс-спектрометрического метода.
Из результатов масс-спектрометрического анализа следует, что, несмотря на то что суммарная концентрация примесей минимальна в случае, когда кислотная промывка применяется непосредственно после окисления, для удаления Na и K нужна дополнительная термообработка до промывки кислотой. Дополнительная термообработка может применяться при окислении алюминия высокой чистоты, т.е. с заведомо низкой концентрацией железа, растворами щелочей (калия или натрия), в такой ситуации наиболее важным становится вопрос об удалении щелочных металлов.
На рис. 5 представлены микрофотографии гидроксида алюминия, полученного в результате окисления гранулированного алюминия, а также продуктов предварительной термической обработки при температурах 600 и 1200°С. Видно, что в результате выхода кристаллизационной воды в ходе термообработки поверхность кристаллов становится более шероховатой (при температуре 600°С), а при температуре 1200°С в результате спекания оксида образуются поры с размером в несколько десятков нм.
Рис. 5.
Микрофотографии гидроксида алюминия, полученного в результате окисления гранулированного алюминия (а, б), а также продуктов предварительной термической обработки при температурах 600 (в, г) и 1200°С (д, е).
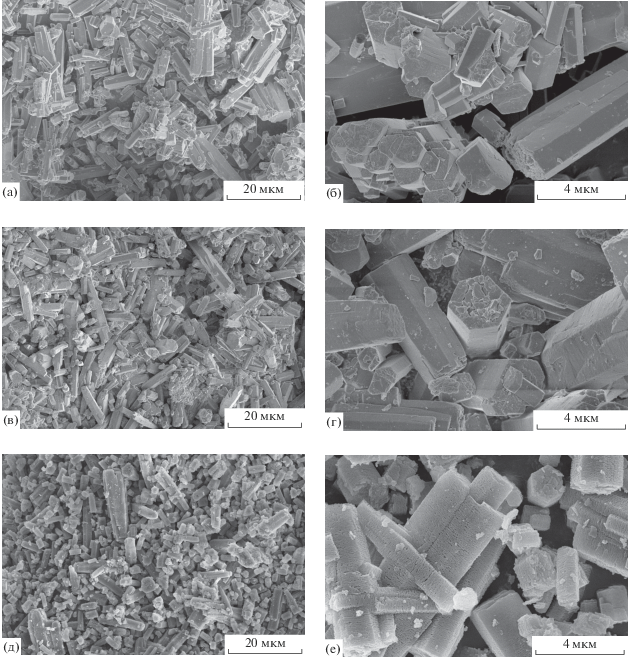
На рис. 6 представлены образцы до и после кислотной промывки. Видно, что в целом морфология продукта не изменяется, однако в результате кислотной обработки поверхность частиц становится менее гладкой, образуются агломераты частиц меньшего размера.
Рис. 6.
Микрофотографии оксида алюминия, полученного в результате предварительной термической обработки при 600°С, до (а) и после (б) кислотной обработки.
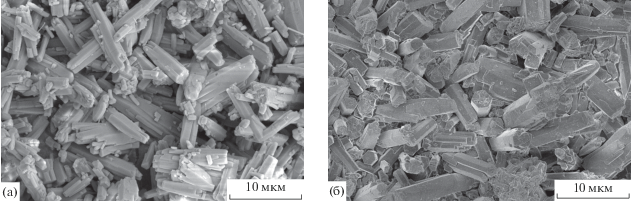
На рис. 7 представлены микрофотографии образцов оксида алюминия, полученных при температурах 900, 1200 и 1450°С. Из анализа микрофотографий следует, что увеличение температуры термообработки приводит к образованию макропор по границам дефектов кристаллов. С увеличением температуры происходит спекание, увеличивается путь выхода примеси из объема кристалла на его поверхность. Несмотря на увеличение коэффициента диффузии примеси с увеличением температуры, это может затруднять выход примесей, о чем косвенно свидетельствуют результаты исследования, в частности сравнение результатов масс-спектрометрического анализа образцов 1.5 и 1.6, полученных при температурах предварительной термообработки 900 и 1200°С соответственно.
Рис. 7.
Микрофотографии образцов оксида алюминия, полученного при температурах 900 (а), 1200 (б) и 1450°С (в).
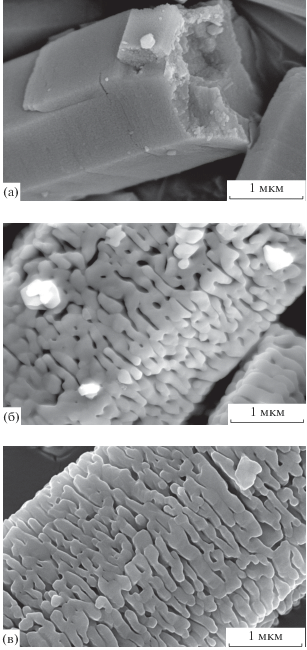
Алюминий марки А98 (99.98%). Алюминий гранулированный марки А98 был окислен при температуре 90°C в 0.1 М водном растворе гидроксида калия. Степень превращения алюминия составила 79%. После отделения полученного гидроксида алюминия от неокисленного алюминия, а также фильтрации и сушки были проведены термообработка и кислотная обработка (рис. 8).
Рис. 8.
Блок-схема процессов термообработки и кислотной обработки продукта окисления алюминия марки А98 (образцы оксида алюминия 2.1–2.3 отправлялись на масс-спектрометрический анализ).
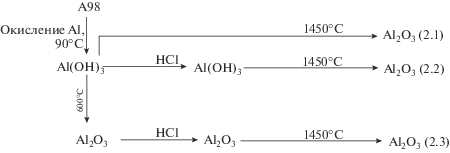
Из результатов масс-спектрометрического анализа образцов (табл. 4 ) видно, что при использовании алюминия высокой чистоты можно относительно легко получить оксид алюминия с химической чистотой на уровне 99.99%. Стоит отметить, что в данном случае удается значительно понизить содержание железа в конечном продукте, причем как в образце с предварительной термообработкой, так и без нее. За счет низкого содержания в исходном алюминии примесей Ti, V и Cr их содержание в конечном продукте минимально и удовлетворяет современным требованиям потребителей высокочистого оксида алюминия.
Таблица 4.
Результаты масс-спектрометрического анализа образцов оксида алюминия 2.1–2.3
Элемент | ПО, ppm | С, ppm | ||
---|---|---|---|---|
2.1 | 2.2 | 2.3 | ||
Li | 0.1 | 3.8 ± 0.8 | 3.4 ± 0.7 | 3.4 ± 0.7 |
Be | 0.03 | <ПО | 0.038 | <ПО |
B | 0.3 | <ПО | <ПО | <ПО |
Na | 6.0 | 15.0 ± 3.5 | 13.0 ± 3.1 | 12.0 ± 3.4 |
Mg | 2.0 | <ПО | <ПО | <ПО |
Al | Основа | Основа | Основа | Основа |
K | 1.0 | 86.7 ± 9.3 | 64.8 ± 7.2 | 46.1 ± 5.2 |
Ca | 6.0 | 6.1 | <ПО | <ПО |
Sc | 1.0 | <ПО | <ПО | <ПО |
Ti | 1.0 | <ПО | <ПО | <ПО |
V | 0.6 | 2.2 ± 0.6 | 2.4 ± 0.6 | 1.6 ± 0.4 |
Cr | 1.0 | <ПО | <ПО | <ПО |
Mn | 0.2 | 1.2 | 1.2 | <ПО |
Fe | 9.0 | 32.9 ± 5 | <ПО | <ПО |
Co | 0.1 | <ПО | <ПО | <ПО |
Ni | 1.0 | <ПО | <ПО | <ПО |
Cu | 1.0 | <ПО | <ПО | <ПО |
Zn | 1.0 | <ПО | <ПО | <ПО |
Ga | 0.3 | 3.1 | 3.2 | 2.0 |
As | 0.1 | <ПО | <ПО | <ПО |
Se | 2.0 | <ПО | <ПО | <ПО |
Rb | 0.04 | <ПО | <ПО | <ПО |
Sr | 0.09 | <ПО | <ПО | <ПО |
Y | 0.02 | <ПО | <ПО | 0.52 |
Zr | 0.6 | <ПО | <ПО | <ПО |
Nb | 0.04 | <ПО | <ПО | <ПО |
Mo | 0.07 | <ПО | <ПО | 0.26 |
Rh | 0.2 | <ПО | <ПО | <ПО |
Pd | 0.1 | <ПО | <ПО | <ПО |
Ag | 0.04 | <ПО | <ПО | <ПО |
Cd | 0.03 | <ПО | <ПО | <ПО |
Sn | 0.3 | <ПО | <ПО | <ПО |
Ta | 0.01 | <ПО | <ПО | <ПО |
W | 0.03 | <ПО | <ПО | 0.081 |
Сумма | 151.00 | 88.04 | 65.96 |
Кислотная промывка позволяет снизить содержание щелочных металлов (Li, Na и K), однако в образце без предварительной термообработки и в образце с термообработкой при 600°С содержание Na и K все еще остается достаточно высоким. Это может быть связано с наличием устойчивых форм алюминатов натрия и калия, для удаления которых требуется либо оптимизация термических и кислотных обработок, либо более высокая конечная температура обжига.
ЗАКЛЮЧЕНИЕ
Исследована возможность получения оксида алюминия с пониженным содержанием примесей путем окисления гранулированного алюминия в 0.1 М растворе гидроксида калия с последующими химической и термической обработками гидроксида алюминия и других его соединений.
Из алюминия марки А7 с чистотой 99.7% был получен оксид алюминия с суммарным содержанием примесей 1141.76 ppm, что соответствует 1141.76 × 10–6 г или 99.886%. Установлено, что с увеличением температуры предварительной обработки продукта окисления алюминия суммарная концентрация примесей, включая примесь железа, увеличивалась, концентрация щелочных металлов (K, Na, Li), наоборот, уменьшалась. Концентрация примеси калия была уменьшена по сравнению с образцом, полученным прямым обжигом продукта окисления алюминия при температуре 1450°С, более чем в два раза при температуре предварительной термообработки 900°С и более чем в 4 раза при 1200°С.
Из алюминия марки А98 с чистотой 99.98% был получен оксид алюминия с суммарным содержанием примесей 65.96 ppm, что соответствует 65.96 × 10–6 г или 99.993%. Кислотная промывка также снизила содержание щелочных металлов (Li, Na и K) в конечном продукте. В образце, полученном с применением кислотной обработки и предварительной обработки при 600°С, содержание Na и K составило 12 и 46 ppm соответственно.
Список литературы
Kim H.S., Oh S.T., Kim Y.D. Effects of the Two-Step Sintering Process on the Optical Transmittance and Mechanical Strength of Polycrystalline Alumina Ceramics // Ceram. Int. 2014. V. 40. № 9. P. 14471–14475. doi 10.1016/j.ceramint.2014.05.127
Lisitsyn A.V., Dombrovsky L.A., Mendeleyev V.Y., Grigorenko A.V., Vlaskin M.S., Zhuk A.Z. Near-Infrared Optical Properties of a Porous Alumina Ceramics Produced by Hydrothermal Oxidation of Aluminum // Infrared Phys. Technol. 2016. V. 77. P. 162–170. doi 10.1016/j.infrared.2016.05.028
Varfolomeev M.S., Moiseev V.S., Shcherbakova G.I., Krivtsova N.S., Yurkov G.Y. High-Refractory Ceramics Based on Alumina-Yttria Binders // Inorg. Mater. 2015. V. 51. № 7. P. 722–727. doi 10.1134/S0020168515070183
Grinberg E.E., Saradzhev V.V., Levin Y.I., Ryabenko E.A. Preparation of Fine Alumina Powders by Hydrolysis of Aluminum Isopropylate // Russ. J. Appl. Chem. 2002. V. 75. № 2. P. 245–247. doi 10.1023/A:1016108302641
Khishigbayar K.E., Moon Y.G., Bae E.J., Shim K.B., Kim C.J. Impurity Control with the Precise Measurement of Alumina Powders Synthesized by Hydrolysis Method // J. Ceram. Proc. Res. 2013. V. 14. № 2. P. 168–171.
Mekasuwandumrong O., Silveston P.L., Praserthdam P., Inoue M., Pavarajarn V., Tanakulrungsank W. Synthesis of Thermally Stable Micro Spherical χ-Alumina by Thermal Decomposition of Aluminum Isopropoxide in Mineral Oil // Inorg. Chem. Commun. 2003. V. 6. № 7. P. 930–934.
Khosravi M.M., Andrus M.B., Burt S.R., Woodfield B.F. Generalized Preparation Method and Characterization of Aluminum Isopropoxide, Aluminum Phenoxide, and Aluminum n-Hexyloxide // Polyhedron. 2013. V. 62. P. 18–25.
Yoo S.-J., Yoon H.-S., Jang H.D., Lee J.-W., Hong S.-T., Lee M.-J., Lee S.-I., et al. Synthesis of Aluminum Isopropoxide from Aluminum Dross // Korean J. Chem. Eng. 2006. V. 23. № 4. P. 683–687.
Pacewska B., Keshr M. Thermal Transformations of Aluminium Nitrate Hydrate // Thermochim. Acta. 2002. V. 385. № 1–2. P. 73–80.
Lysenko A.P., Nalivayko A.Y. Optimization of Electrolysis During the High-Pure Aluminium Oxide Obtaining, Using Electrochemical Method of Aluminium Oxidation // Tsvetn. Met. (Moscow). 2017. № 1. doi 10.17580/tsm.2017.01.05
Balde M., Bibi F., Charlot B., Combette P., Sorli B. Growth and Characterization of Anodized Aluminum Oxide Thin Film on Paper-Based Substrate // Symposium on Design, Test, Integration and Packaging of MEMS/MOEMS (DTIP). 2013. P. 1–5.
Vlaskin M.S., Shkolnikov E.I., Lisicyn A.V., Bersh A.V., Zhuk A.Z. Computational and Experimental Investigation on Thermodynamics of the Reactor of Aluminum Oxidation in Saturated Wet Steam // Int. J. Hydrogen Energy. 2010. V. 35. № 5. P. 1888–1894.
Bersh A.V., Lisitsyn A.V., Sorokovikov A.I., Vlaskin M.S., Mazalov Y.A., Shkol’nikov E.I. Study of the Processes of Steam-Hydrogen Mixture Generation in a Reactor for Hydrothermal Aluminum Oxidation for Power Units // High Temperature. 2010. V. 48. № 6. P. 866–873.
Shkolnikov E.I., Shaitura N.S., Vlaskin M.S. Structural Properties of Boehmite Produced by Hydrothermal Oxidation of Aluminum // J. Supercrit. Fluids. 2013. V. 73. P. 10–17.
Edward L. Production of High Purity Alumina: Patent № WO1985000799 A1 US. 1984. Publicat. Date 28.02.1985.
Totten G.E., MacKenzie D.S. The Handbook of Aluminum. N.Y.: Marcel Dekker, 2003. 1296 p.
Shkolnikov E.I., Zhuk A.Z., Vlaskin M.S. Aluminum as Energy Carrier: Feasibility Analysis and Current Technologies Overview // Renewable Sustainable Energy Rev. 2011. V. 15. № 9. P. 4611–4623.
Ambaryan G.N., Vlaskin M.S., Dudoladov A.O., Meshkov E.A., Zhuk A.Z., Shkolnikov E.I. Hydrogen Generation by Oxidation of Coarse Aluminum in Low Content Alkali Aqueous Solution Under Intensive Mixing // Int. J. Hydrogen Energy. 2016. V. 41. № 39. P. 17216–17224. doi 10.1016/j.ijhydene.2016.08.005
Амбарян Г.Н., Дудоладов А.О., Мешков Е.А., Власкин М.С., Жук А.З., Школьников Е.А. Генерация водорода путем окисления алюминия в низкоконцентрированном водном растворе калиевой щелочи при интенсивном перемешивании // Альтернативная энергетика и экология (ISJAEE). 2015. № 23. С. 95–104. https://org/10.15518/isjaee.2015.23.013.
Zhuk A.Z., Vlaskin M.S., Grigorenko A.V., Kislenko S.A., Shkolnikov E.I. Synthesis of High-Purity α-Al2O3 from Boehmite by High Temperature Vacuum Treatment // J. Ceram. Proc. Res. 2016. V. 17. № 9. P. 910–918.
Vlaskin M.S., Grigorenko A.V., Zhuk A.Z., Lisitsyn A.V., Sheindlin A.E., Shkol’nikov E.I. Synthesis of High-Purity α-Al2O3 from Boehmite Obtained by Hydrothermal Oxidation of Aluminum // High Temperature. 2016. V. 54. № 3. P. 322–329. doi 10.1134/S0018151X16020231
Kislenko S.A., Vlaskin M.S., Zhuk A.Z. Diffusion of Cation Impurities by Vacancy Mechanism in α-Al2O3: Effect of Cation Size and Valence // Solid State Ionics. 2016. V. 293. P. 1–6. doi 10.1016/j.ssi.2016.05.021
Kazantseva E.L., Tolchev A.V., Larin D.D. Impurity Localization in Aluminum Oxide Compounds // Inorg. Mater. 2011. V. 47. № 11. P. 1264.
Khvostikov V.A., Karandashev V.K., Burmii Z.P. Analysis of α-Alumina Samples by Mass Spectrometry with Inductively Coupled Plasma and Laser Ablation // Inorg. Mater. 2015. V. 51. № 14. P. 1410–1415.
McLeod C.T., Kastner J.W., Carbone T.J., Starr J.P. Aluminas for Tomorrow’s Ceramics // Proceedings of the Conference on Raw Materials for Advanced and Engineered Ceramics. Ceramic Engineering and Science Proceedings. N.Y.: Wiley, 2008. P. 1233–1243.
Roy S.K., Coble R.L. Solubilities of Magnesia, Titania, and Magnesium Titanate in Aluminum Oxide // J. Am. Ceram. Soc. 1968. V. 51. № 1. P. 1–6.
Gülgün M.A., Voytovych R., Maclaren I., Rühle M., Cannon R.M. Cation Segregation in an Oxide Ceramic with Low Solubility: Yttrium Doped α-Alumina // Interface Sci. 2002. V. 10. № 1. P. 99–110.
Дополнительные материалы отсутствуют.
Инструменты
Неорганические материалы