Неорганические материалы, 2019, T. 55, № 3, стр. 330-335
Влияние степени деформации на формирование МАХ-фазы в материалах на основе Ti–Al–C при СВС-экструзии
П. М. Бажин 1, *, Л. С. Стельмах 1, А. М. Столин 1
1 Институт структурной макрокинетики и проблем материаловедения им. А.Г. Мержанова
Российской академии наук
142432 Московская обл, Черноголовка, ул. Академика Осипьяна, 8, Россия
* E-mail: olimp@ism.ac.ru
Поступила в редакцию 09.04.2018
После доработки 15.10.2018
Принята к публикации 12.09.2018
Аннотация
Приведены численные и экспериментальные результаты исследования температурных условий при СВС-экструзии в материалах на основе МАХ-фазы состава Ti–Al–C. На основе математической модели тепловых режимов СВС-экструзии, позволяющей анализировать температурные поля по длине и по радиусу экструдированного образца модельного состава (мас. %): 64.2Ti + 27.1Al + 8.7С, даны рекомендации и прогноз для реализации благоприятных условий образования МАХ-фазы в зависимости от степени деформации. Проведено качественное сопоставление теоретических и экспериментальных результатов. Выявлено влияние времени задержки перед приложением давления прессования на дефектность поверхности полученных образцов, а также степени деформации на структуру и качество поверхности экструдированных материалов. Показано, что образцы диаметром 10 мм не содержат карбида титана, а для образцов диаметром 5 и 8 мм его содержание находится на уровне 6–8 мас. %.
ВВЕДЕНИЕ
Материалы на основе МАХ-фазы на сегодняшний день перспективны в различных отраслях промышленности благодаря совокупности свойств керамики и металлов [1–3]. Эти материалы показывают высокую тепловую и электрическую проводимость, а также достаточно высокую стойкость к тепловым ударам, что характерно для металлов. Как керамика они обладают высоким модулем упругости, низким тепловым коэффициентом расширения, высокой теплостойкостью и превосходной жаростойкостью [4–6].
Среди них нужными свойствами обладают материалы на основе МАХ-фазы состава Ti–Al–C [7–9]. Синтез таких материалов из исходных компонентов (титана, алюминия и сажи) проходит поэтапно. В первую очередь образуются алюминиды и карбиды титана, а затем происходит образование МАХ-фаз (Ti2AlC, Ti3AlC2) в результате взаимодействия карбида и алюминида [10–12]. При этом продукт синтеза представляет собой смесь из МАХ-фаз, интерметаллида Ti–Al различного стехиометрического состава и TiC. Для изделий, работающих при циклических температурных нагрузках, содержание карбида титана в синтезированном материале должно быть минимальным [13].
В работе [14] показана возможность получения методом СВС материалов на основе МАХ-фазы состава Ti2AlC с чистотой около 95%, изучена эволюция фазового состава во время протекания постпроцессов, установлено, что тепловые условия оказывают существенное влияние на фазовый состав конечного продукта синтеза.
В работах [1, 15] исследовано влияние технологических и конструктивных параметров СВС-экструзии, состава исходной смеси и внешних условий на состав и структуру получаемых длинномерных материалов на основе МАХ-фазы Ti–Al–C.
В настоящей работе представлены численные и экспериментальные результаты исследования температурных условий для реализации образования МАХ-фазы из материалов на основе Ti3AlC2, полученных методом СВС-экструзии.
ЭКСПЕРИМЕНТАЛЬНАЯ ЧАСТЬ
Ранее были разработаны математические модели тепловых режимов процесса СВС-экструзии [16]. Эти модели позволяют исследовать температурные поля в материале образца, находящемся в цилиндрической пресс-форме, и в экструдированном стержне в зависимости от различных технологических параметров процесса (температуры горения, времени задержки, скорости плунжера пресса, температуры подогрева различных зон оборудования и т.п.). Решается система дифференциальных уравнений теплопроводности [16] для материала в пресс-форме и экструдированного стержня.
В результате решения двумерной тепловой задачи [17] с двумя подвижными границами и соответствующими граничными условиями в настоящей работе определяли температурное поле T = T(r, z, τ), являющееся функцией двух координат – r, z – и времени τ (относительно угловой координаты ϕ существует симметрия) в образце, экструдированной части материала и прогнозировали длину изделия (L).
Когда часть материала, находящаяся в профилирующей матрице и расположенная непосредственно над ее отверстием, теряла “живучесть”, т.е. способность к пластическому деформированию (температура в отверстии профилирующей матрицы становилась ниже температуры “живучести”-формования), и закупоривала выходное отверстие, выдавливание прекращалось. Полученная длина – ордината нижней границы образца – являлась искомой длиной изделия. В результате численного исследования строились графики полей температур в сгоревшем образце и экструдированном стержне, а также зависимости его длины от времени экструзии.
Моделируя тепловые режимы СВС-экструзии, изучали температурные поля и зависимость длины экструдированной части образца модельного состава (мас. %) 64.2Ti + 27.1Al + 8.7С для получения МАХ-фазы из материалов на основе Ti3AlC2.
В расчетах использовались следующие данные: давление на плунжере пресса p = 108 Па, плотность несжимаемой основы материала ρ1 = 4 × 103 кг/м3, теплоемкость C = 854 Дж/(кг К), коэффициент теплопроводности λ = 13–16.7 Вт/(м К), начальная высота заготовки Н0 = 30 × 10–3 м, диаметр заготовки d1 = 27 × 10–3 м, угол конуса матрицы 2α = 180°, температура горения Tг = 2373 K, температура формования Тж = 1337–1470 K ((0.7–0.9)Tm – температуры плавления связки, 1600 К), скорость плунжера пресса Un = 20 × 10–3 м/с, скорость горения Uг = 10 × 10–3 м/с, диаметры отверстий профилирующей матрицы d3 = 5 × 10–3, 8 × 10–3, 10 × × 10–3 м, толщина теплоизолятора на матрице и в отверстии δ = (0–3) × 10–3 м.
Методом СВС-экструзии, который сочетает процессы горения исходных компонентов и их последующее высокотемпературное деформирование, были получены стержни диаметрами 5, 8 и 10 мм из материалов на основе МАХ-фазы Ti–Al–C.
В качестве объекта исследования был выбран следующий состав (мас. %): 64.2 титан (ПТС, ТУ 14-22-57-92), 27.1 алюминий (АСД-4, ТУ 1791-99-019-98) и 8.7 сажа (ОСТ-38-1531-73). Порошки предварительно перемешивали, формовали из них цилиндрические заготовки массой 50 г, диаметром 27 мм, высотой 30 мм, после чего инициировали реакцию горения и через заданное время задержки экструдировали через формующую матрицу.
Степень деформации полученных образцов рассчитывали по формуле
Важной характеристикой для материалов, полученных методом СВС-экструзии, является дефектность поверхности. Для подобных изделий характерна дефектность типа “елочка”. Критерием состояния дефектного слоя выбирается величина дефектного слоя δ, равная двойной глубине трещин и макродефектов на поверхности экструдированного образца [14]. Критерий дефектности поверхности определяли по формуле
где d – диаметр экструдированного образца, Kδ выражает соотношение между дефектной и бездефектной частями поперечного сечения образца. Чем меньше дефектность поверхности, тем меньше потребность в дополнительных механических операциях.Для выполнения материаловедческих исследований было привлечено оборудование Распределенного центра коллективного пользования ИСМАН: автоэмиссионный сканирующий электронный микроскоп сверхвысокого разрешения Carl Zeiss Ultraplus (Германия), порошковый рентгеновский дифрактометр ARL X’TRA и др.
РЕЗУЛЬТАТЫ И ОБСУЖДЕНИЕ
По расчетным данным для скорости плунжера пресса 20 мм/с и исходной высоте шихтовой заготовки 30 мм время экструзии синтезированного материала составляет τэ = 0.7 с. Температура горения образца выбранного состава с предварительным нагревом исходной заготовки до 300°С составила 2100°С. За счет того что скорость плунжера пресса постоянна, количество экструдированного материала для матриц с различными диаметрами выходного отверстия одинаково, а длина стержня, соответственно, изменяется. При этом распределение температуры в сгоревшем образце постоянно за счет практически равных условий теплоотвода. В его центре температура соответствует температуре горения выбранного состава, а периферия остывает за счет контакта со стенками пресс-формы. Распределение температуры в экструдированной части изменяется в зависимости от радиуса стержня для фиксированного времени экструзии. При малых степенях деформации (для диаметра образца 5 мм) теплоотвод более интенсивен: в центре температура составляет 1421°С, на периферии – уже 1323°С (рис. 1, кривая 1). Для стержней с большим диаметром за счет менее выраженного теплообмена температура выше на 200–270°С, а ее перепад по радиусу меньше (рис 1, кривые 2, 3). Поскольку температура образования МАХ-фазы составляет 1300–1500°С, увеличение времени нахождения экструдированного материала в этом температурном интервале способствует ее образованию. При времени τ1 = 0.1τэ = 0.07 с температура стержней диаметром 5 мм составляет 882–951°С и образования МАХ-фазы уже не происходит. При этом времени для стержней с бóльшим диаметром температура в пресс-форме выше 1350°С. Таким образом, на основе приведенных численных результатов можно сделать вывод, что за счет менее выраженного теплоотвода при экструзии стержней с бóльшими диаметрами температурные и временные условия образования МАХ-фазы более благоприятны, чем для стержней малого диаметра.
Рис. 1.
Распределение температуры по радиусам экструдированных стержней диаметром 5 (1), 8 (2), 10 мм (3).
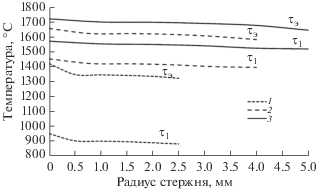
Рентгенофазовый анализ подтверждает, что степень деформации при СВС-экструзии влияет на фазовый состав полученных материалов. Как показало математическое моделирование СВС-экструзии, приведенное выше, это происходит вследствие различной скорости охлаждения образца после экструзии при нахождении его в прессовой оснастке. Для стержней диаметром 5 мм наблюдаются рефлексы МАХ-фазы Ti3AlC2, алюминида титана TiAl3 и карбида титана TiC, при этом пики фазы Ti2AlC находятся на уровне фона (рис. 2, дифрактограмма 1). Для образца диаметром 8 мм также обнаружены фазы Ti3AlC2, TiAl3 и TiC со следами Ti2AlC, однако при этом интенсивность пиков карбида титана оказалась значительно меньше и находилась на уровне фона (рис. 2, дифрактограмма 2). Увеличение диаметра формующей матрицы до 10 мм привело к образованию в материале МАХ-фазы Ti3AlC2 со следами интерметаллида TiAl3 (рис.2, дифрактограмма 3). В соответствии с расчетами при больших диаметрах экструдированных стержней теплоотвод менее выражен, чем для стержней меньшего диаметра, что и обеспечивает более полное образование МАХ-фазы. Таким образом, с целью снижения содержания карбидных включений, характерных для данного класса соединений, необходимо увеличивать габариты экструдированных стержней. В данном случае в экструдированном стержне были обнаружены фазы Ti3AlC2, TiAl3 и следы Ti2AlC, при этом карбид титана не обнаружен.
В табл. 1 представлены результаты количественного анализа структурных составляющих в экструдированных образцах различных диаметров на основе корундовых чисел. Как видно из табл. 1, доля МАХ-фазы во всех образцах составляет 76–90 мас. %, остальное – интерметаллиды и карбиды. При этом стержни диаметром 10 мм состоят из МАХ-фазы и интерметаллида, карбид титана отсутствует.
На рис. 3 продемонстрировано влияние степени деформации на дефектность поверхности экструдируемых стержней при различных временах задержки перед приложением давления. Как видно из полученных зависимостей, с увеличением степени деформации дефектность поверхности снижается, качество улучшается. Оптимальным временем задержки является 3 с, т.к. при этом качество поверхности выше при выбранных степенях деформации. При временах задержки менее 2 с материал не успевает консолидироваться при экструзии, что приводит к повышению дефектности поверхности. При времени задержки 4 с синтезированный материал частично остывает, что приводит к потере его пластичности при экструзии и повышает дефектность. При временах задержки более 4 с материал остывает в большей степени и в итоге перестает формоваться и экструдироваться.
Полученные образцы имеют микроструктуру, характерную для материалов на основе МАХ-фазы: пластинчатые вытянутые зерна Ti3AlC2 распределены в матрице алюминида титана TiAl3. В случае стержней меньших диаметров (5 и 8 мм) можно встретить округлые зерна карбида титана, количество которых, впрочем, не превышает 6–8 мас. %. Была изучена микроструктура экструдированных стержней в центральной и периферийной частях (рис. 4): в обоих образцах пластинчатые зерна МАХ-фазы расположены в матрице алюминида титана. Можно отметить некоторое укрупнение зерен в центральной части стержня, не более чем на 10%, что объясняется более медленным остыванием этой части образца после синтеза. В обоих случаях доля алюминида титана не превышает нескольких процентов, что позволяет считать достаточным количество МАХ-фазы даже при диаметре формующей матрицы 8 мм, и, что немаловажно, можно считать распределение структурных составляющих по сечению экструдированного образца равномерным.
Как видно из СЭМ-изображений, в стержнях диаметром 10 мм карбидные зерна отсутствуют, что также соответствует результатам РФА (рис. 5). Структура синтезированного материала практически однородна, что делает невозможным наведение четкого контраста. Это связано с тем, что интерметаллидная фаза и МАХ-фаза имеют схожие характеристики плотности и дисперсности, однако прослеживаются пластинчатые зерна МАХ-фазы.
Результаты измерения микротвердости образцов различных диаметров при нагрузке 0.5 H методом Виккерса по сечению (5 замеров) приведены в табл. 2. Для материалов на основе МАХ-фазы системы Ti–Al–C без посторонних примесей, особенно без твердых зерен карбида титана, микротвердость составляет 4–4.5 ГПа. Из табл. 2 видно, что полученные материалы практически не содержат карбидных примесей. Также отметим, что разброс измеренных значений микротвердости составляет не более 5–14%, что говорит о равномерном распределении составляющих в материалах после СВС-экструзии.
ЗАКЛЮЧЕНИЕ
На основе численного и экспериментального исследования установлено, что степень деформации материала при СВС-экструзии влияет на фазовый состав и структуру. Уменьшение степени деформации с 0.99 до 0.89 приводит к более полному растворению карбида в алюминиде титана за счет снижения теплопотерь при остывании и нахождения экструдированного материала в благоприятных температурных и временных условиях образования МАХ-фазы. Однако при этом дефектность поверхности за счет менее интенсивного деформирования повышается с 7 до 19%.
Полученные образцы имеют структуру, характерную для материалов на основе МАХ-фазы: пластинчатые вытянутые зерна Ti3AlC2 распределены в матрице алюминида титана TiAl3. В случае образцов меньших диаметров (5 и 8 мм) встречаются округлые зерна карбида титана, количество которых не превышает 6–8 мас. %.
Список литературы
Столин А.М., Бажин П.М., Аверичев О.А., Алы-мов М.И., Гусев А.О., Симаков Д.А. Электродные материалы на основе МАХ-фазы Ti–Al–C // Неорган. материалы. 2016. Т. 52. № 10. С. 1069–1072.
Zapata-Solvas E., Hadi M.A., Horlait D. et al. Synthesis and Physical Properties of (Zr1 – x, Tix)3AlC2 MAX Phases // J. Am. Ceram. Soc. 2017. V. 100. № 8. P. 3393–3401. doi 10.1111/jace.14870
Radovic M., Barsoum M.W., Ganguly A. et al. On the Elastic Properties and Mechanical Damping of Ti3SiC2, Ti3GeC2, Ti3Si0.5Al0.5C2 and Ti2AlC in the 300–1573 K Temperature Range // Acta Mater. 2006. V. 54. № 10. P. 2757–2767. doi 10.1016/j.actamat.2006.02.019
Barsoum M.W. The MAX Phases and Their Properties in Ceramics Science and Technology. N.Y.: Wiley–VCH, 2010. V. 2. P. 299–345.
Christopoulos S.-R.G., Filippatos P.P., Hadi M.A. et al. Intrinsic Defect Processes and Elastic Properties of Ti(3)AC(2) (A = Al, Si, Ga, Ge, In, Sn) MAX Phases // J. Appl. Phys. 2018. V. 123. № 2. 025103. doi 10.1063/ 1.5011374
Prikhna T.A., Starostina A.V., Lizkendorf D. et al. Studies of the Oxidation Stability, Mechanical Characteristics of Materials Based on Max Phases of the Ti–Al–(C, N) Systems, and of the Possibility of Their Use as Tool Bonds and Materials for Polishing // J. Superhard Mater. 2014. V. 36. № 1. P. 9–17. doi 10.3103/ S106345761401002X
Jeong G., Baek G., Zhang T.F. et al. MAX-Phase Ti2AlC Ceramics: Syntheses, Properties and Feasibility of Applications in Micro Electrical Discharge Machining // J. Ceram. Proc. Res. 2016. V. 17. № 10. P. 1116–1122.
Tomoshige R., Tanaka H. Thermal Properties of Various Ti–Al–C Composites Prepared by Hot Shock Compaction Utilizing Combustion Synthesis // Arch. Metall. Mater. 2014. V. 59. № 4. P. 1575–1578. doi 10.2478/amm-2014-0267
Stolin A.M., Vrel D., Galyshev S.N., Hendaoui A., Bazhin P.M., Sytschev A.E. Hot Forging of MAX Compounds SHS-Produced in the Ti–Al–C System // Int. J. Self-Propag. High-Temp. Synth. 2009. V. 18. № 3. P. 194–199.
Bazhin P.M., Kovalev D.Yu., Luginina M.A., Averichev O.A. Combustion of Ti–Al–C Compacts in Air and Helium: A TRXRD Study // Int. J. Self-Propag. High-Temp. Synth. 2016. V. 25. № 1. P. 30–34. doi 10.3103/ S1061386216010027
Khoptiar Y., Gotman I. Ti2AlC Ternary Carbide Synthesized by Thermal Explosion // Mater. Lett. 2002. V. 57. № 1. P. 72–76. № PII S0167-577X(02)00701-2. doi 10.1016/S0167-577X(02)00701-2
Hashimoto S., Nishina N., Hirao K., Zhou Y., Hyuga H., Honda S., Iwamoto Y. Formation Mechanism of Ti2AlC under the Self-Propagating High-Temperature Synthesis (SHS) Mode // Mater. Res. Bull. 2012. V. 47. № 5. P. 1164–1168. doi 10.1016/j.materresbull.2012.02.003
Новиков А.С., Пайкин А.Г., Шулов В.А. Получение, свойства и перспективы применения МАХ-материалов на основе титана // Упрочняющие технологии и покрытия. 2006. № 11. С. 24–34.
Hendaoui A., Andasmas M., Amara A., Benaldjia A., Langlois P., Vrel D. SHS of High-Purity MAX Compounds in the Ti–Al–C System // Int. J. Self-Propag. High-Temp. Synth. 2008. V. 17. № 2. P. 129–135.
Столин А.М., Бажин П.М. Получение изделий многофункционального назначения из композитных и керамических материалов в режиме горения и высокотемпературного деформирования (СВС-экструзия) // Теоретические основы химической технологии. 2014. Т. 48. № 6. С. 1–13.
Stolin A.M., Stel’makh L.S. Mathematical Modeling of SHS Compaction / Extrusion: An Autoreview // Int. J. Self-Propag. High-Temp. Synth. 2008. V. 13. № 1. P. 53–70.
Столин А.М., Стельмах Л.С. Общие принципы математического моделирования СВС-технологий // Вестн. ТГТУ. 2014. Т. 20. № 4. С. 684–692.
Дополнительные материалы отсутствуют.
Инструменты
Неорганические материалы