Неорганические материалы, 2019, T. 55, № 3, стр. 322-329
Механохимическая активация порошков-прекурсоров в технологии получения плотной нанокерамики в системе Al2O3–ZrO2〈Y2O3〉
Л. В. Морозова *
Институт химии силикатов им. И.В. Гребенщикова Российской академии наук
199034 Санкт-Петербург, наб. Макарова, 2, Россия
* E-mail: morozova_l_v@mail.ru
Поступила в редакцию 20.04.2018
После доработки 15.10.2018
Принята к публикации 14.09.2018
Аннотация
Разработана технология получения порошков-прекурсоров и нанокристаллической керамики (60−90 нм) на основе оксида алюминия в системе Al2O3–ZrO2〈Y2O3〉. Изучено влияние механохимической активации (МА) на структуру и дисперсность порошков-прекурсоров, определен наиболее эффективный временной интервал МА. Установлено, что использование МА снижает температуру образования фазы α-Al2O3 и интенсифицирует процесс спекания керамики. Подобран оптимальный режим консолидации порошков для получения плотной нанокерамики, определены ее физико-химические и механические свойства.
ВВЕДЕНИЕ
Среди большого разнообразия керамических материалов особый интерес у материаловедов вызывает керамика на основе оксида алюминия (Al2O3), которая благодаря высоким показателям износостойкости, плотности, твердости, прочности при изгибе, стойкости к химически агрессивным средам и коррозии используется для производства самых различных изделий, начиная от абразивных инструментов и заканчивая бронежилетами и биоматериалами.
В настоящее время широкое распространение получили композиционные материалы в системе Al2O3−ZrO2〈Y2O3〉 [1–5]. Введение в алюмооксидную матрицу тетрагонального твердого раствора диоксида циркония (t-ZrO2) способствует повышению термостабильности и трещиностойкости керамических композиций, одновременно t-ZrO2 выступает и как ингибитор роста кристаллитов фаз оксида алюминия, что дает возможность получать керамику с достаточно высокой плотностью [6, 7].
Общеизвестно, что способ синтеза порошка оказывает значительное влияние на протекание процессов консолидации порошковой массы при спекании и в итоге определяет свойства конечного продукта. Современные технологические разработки новых материалов делают акцент на использование низкотемпературных (200−800°C) методов синтеза оксидных порошков-прекурсоров в нанокристаллическом состоянии, применение которых позволит не только снизить энергозатраты, но и обеспечить условия формирования из них плотной керамики, которая будет иметь размер кристаллитов <100 нм [8].
Для получения керамики в системе Al2O3− ZrO2〈Y2O3〉 часто используют метод химического осаждения гидроксидов [9–11], который не требует дорогостоящего оборудования в отличие от технологически сложных плазмохимического или гидротермального методов. Единственным недостатком данного метода является возможное образование крупных агломератов (≥5 мкм), которые препятствуют формированию наноразмерных кристаллитов, что в дальнейшем затрудняет получение высокоплотной керамики. Для решения этой проблемы целесообразно использовать механическое диспергирование, позволяющее увеличить не только дисперсность синтезированных порошков-прекурсоров, но и их реакционную активность за счет образования точечных дефектов и дислокаций [12, 13].
Цель настоящего исследования – разработать эффективную технологию получения плотной нанокристаллической керамики на основе оксида алюминия в системе Al2O3−ZrO2〈Y2O3〉 с использованием механохимической активации (МА) порошков-прекурсоров, подобрать оптимальные режимы консолидации МА-порошков и изучить физико-химические и механические свойства спеченной керамики.
ЭКСПЕРИМЕНТАЛЬНАЯ ЧАСТЬ
Методы исследования. Рентгенофазовый анализ (РФА, дифрактометр Дрон-3) использовали для идентификации фаз. Расшифровку дифрактограмм осуществляли с помощью картотеки PDF-2. По формуле Селякова–Шерера: dhkl = kλ/(β cos θ) [14] рассчитан средний размер кристаллитов, где k – коэффициент, зависящий от формы области когерентного рассеяния кристаллита, λ – длина волны падающего излучения (CuKα), β – полуширина дифракционной линии, θ – угол дифракционного рассеяния Брэгга.
Метод низкотемпературной адсорбции азота использовали для определения удельной поверхности порошков (БЭТ, анализатор сорбции газов Quantachrom NOVA 1200e), седиментационный анализ – для определения размера частиц порошков (лазерный анализатор Horiba LB-550).
Термическую обработку в диапазоне температур 100–1500°C проводили для изучения последовательности образования фаз и динамики спекания образцов (электрическая печь фирмы Naberterm, силитовая печь с SiC-нагревателями). Методом гидростатического взвешивания определяли открытую пористость и плотность керамических образцов (ГОСТ 2409-2014), методом индентирования – твердость по Виккерсу и трещиностойкость (микротвердомер ПМТ-3М, ГОСТ Р 8.777-2011). Метод трехточечного изгиба использовали для определения механической прочности на изгиб (ГОСТ Р 50526-93).
РЕЗУЛЬТАТЫ И ОБСУЖДЕНИЕ
Синтез порошков-прекурсоров − бемита (AlOOH) и метастабильного твердого раствора на основе диоксида циркония (с'-ZrO2). Порошки-прекурсоры в системе Al2O3−ZrO2〈Y2O3〉 синтезировали методом химического осаждения гидроксидов, условная схема установки приведена на рис. 1. В качестве исходных реагентов использовали азотнокислые соли Al(NО3)3 · 9Н2О, ZrО(NОЗ)2 · 2Н2О и Y(NО3)3 · 6Н2O (все реактивы квалификации “х. ч.”), из которых готовили разбавленные водные растворы (~0.1 М), и одномолярный раствор гидроксида аммония (NH4OH). Предварительно было установлено, что осаждение Al(OH)3 следует проводит в интервале рН 9.0−9.5, т.к. при более высоких значениях рН начинается процесс растворения гидроксида алюминия; осадок, состоящий из гидроксидов циркония и иттрия, получали при рН 8−8.5 [8, 9].
Рис. 1.
Схематическое изображение установки для проведения химического осаждения гидроксидов: 1 − бюретка с раствором соли (солей), 2 – раствор осадителя, 3 – многолопостная мешалка, 4 – водно-ледяная баня.
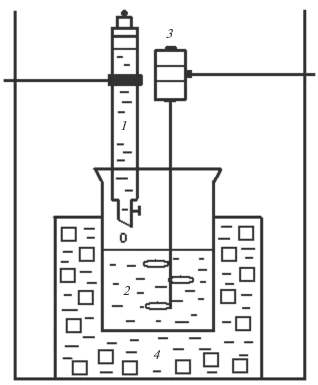
Водные растворы солей Al(NО3)3, ZrО(NОЗ)2 и Y(NО3)3 приливали к NH4OH со скоростью 1–2 мл/мин при непрерывном перемешивании образующегося осадка механической многолопастной мешалкой, чтобы добиться гомогенности продукта осаждения и снизить коагуляцию осаждаемых частиц. Температура в реакторе поддерживалась на уровне 0–2°С с помощью водно-ледяной бани, это способствовало уменьшению подвижности осаждаемых частиц, в результате чего их взаимодействие друг с другом становилось менее эффективным, т.е. система приобретала устойчивость к образованию агломератов [15]. Гелеобразные осадки промывали дистиллированной водой и фильтровали с помощью водоструйного насоса.
Осадок гидроксида алюминия нагревали до температуры 200°C [16] и выдерживали в течение 1 ч для формирования фазы бемита: Al(OH)3 → → AlOOH + H2O (рис. 2а). Осадок, состоящий из гидроксидов циркония и иттрия, обжигали при 400°C (1 ч) и получали метастабильный твердый раствор диоксида циркония (с'-ZrО2) с псевдокубической структурой [17] (рис. 2б).
Рис. 2.
Дифрактограммы синтезированных порошков-прекурсоров AlOOH (a) и c'-ZrO2 (б): 1 − AlOOH (200°C), 2 − c'-ZrO2 (400°C).
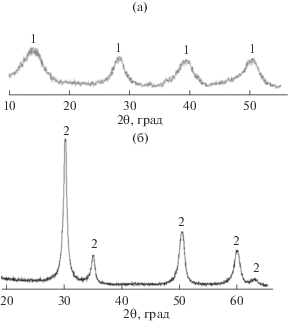
Механохимическая активация смесей порошков AlOOH и с'-ZrО2. МА при синтезе оксидных композиций в системе Al2O3−ZrO2〈Y2O3〉 использовали для гомогенизации смесей порошков-прекурсоров, увеличения их дисперсности и создания дополнительных структурных дефектов, что в дальнейшем позволит интенсифицировать процесс спекания и получать керамику c высокой плотностью [18].
AlOOH и с'-ZrО2 смешивали в заданном соотношении (табл. 1) и подвергали МА в планетарной мельнице фирмы Fritch (рис. 3) с мелющими шарами из высокоплотной алюмооксидной керамики в режиме сухого помола, продолжительность МА составляла 5, 10, 15, 20, 25, 30, 35 и 40 мин. Составы образцов системы Al2O3−ZrO2〈Y2O3〉 выбраны с учетом результатов работы [4], где установлено, что при количестве компонента на основе ZrО2 в алюмооксидной матрице более 20 мол. % происходит снижение относительной плотности и твердости спеченной керамики, что отрицательно влияет на качество керамики в целом.
Таблица 1.
Химический и фазовый составы порошков в системе Al2O3−ZrO2〈Y2O3〉 до и после механохимической активации
Химический состав (мол. %) порошка | Условное обозначение | Фазовый состав порошка до МА | Удельная поверхность порошка (м2/г) после МА (30 мин) | Фазовый состав порошка после МА (30 мин) |
---|---|---|---|---|
90Al2O3−10ZrO2〈Y2O3〉 | AlZr-1 | AlOOH + c′-ZrO2 | 132 | Аморфная фаза AlOOH + + c'-ZrO2 |
80Al2O3−20ZrO2〈Y2O3〉 | AlZr-2 | AlOOH + c′-ZrO2 | 124 | Аморфная фаза AlOOH + + c'-ZrO2 |
Рис. 3.
Планетарная мельница фирмы Fritch: 1 – размольный стакан, 2 – вращающийся опорный диск, 3 – крепление для фиксации стакана на опорном диске, 4 – панель управления процессом, 5 – крышка мельницы.
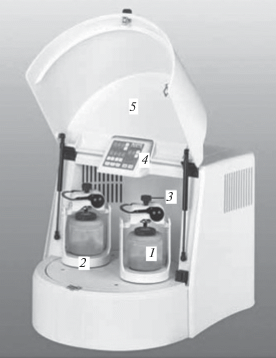
МА смесей AlOOH + с'-ZrО2 в планетарной мельнице приводит к частичной аморфизации порошков и увеличению их дисперсности. Методом БЭТ исследована зависимость удельной поверхности (Sуд) смеси порошков AlOOH + c'-ZrO2 от времени МА (рис. 4). Наиболее активный рост Sуд наблюдается при продолжительности механохимической активации от 10 до 20 мин. Тридцатиминутная МА порошков составов AlZr-1 и AlZr-2 способствует двукратному увеличению их удельной поверхности (58 → 124 м2/г и 63 → 132 м2/г), при этом распределение частиц по размерам, по данным седиментационного анализа, носит унимодальный характер (260−530 нм) (рис. 5а). После 40 мин МА зафиксировано уменьшение удельной поверхности порошков составов AlZr-1 и AlZr-2 на 7−9%.
Рис. 5.
Распределение частиц по размерам в порошке состава AlZr-2: а – МА AlOOH и c'-ZrO2 в течение 30 мин, б − старение МА-порошка на воздухе в течение 3 ч.
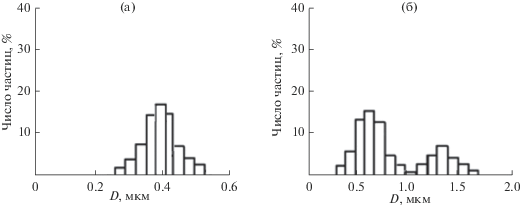
В работах [19, 20] показано, при МА поверхностные слои порошков переходят в крайне неустойчивое термодинамическое состояние, поэтому по истечении определенного интервала времени происходят релаксационные процессы, в результате которых осуществляется замыкание разорванных в процессе МА связей и уменьшение дисперсности порошков. Вероятно, с точки зрения термодинамики, активация порошков AlZr-1 и AlZr-2 в течение 30 мин оптимальна для получения смесей в системе Al2O3−ZrO2〈Y2O3〉 с максимальной дисперсностью. Авторы работы [21] предлагают проводить МА алюмооксидных порошков в присутствии поверхностно-активного вещества (ПАВ), которое, адсорбируясь на поверхности частиц, будет предотвращать релаксацию с выделением тепла образующихся под действием механических нагрузок микродеформаций, что позволит сохранить как дефектность кристаллитов, так и дисперсность МА-порошков. Но следует отметить, в этом случае возможно загрязнение материала продуктами разложения ПАВ, что может отрицательно повлиять на свойства керамики.
По результатам РФА, в МА-порошках наблюдается практически полное разрушение кристаллической структуры бемита (рис. 6), об этом свидетельствует отсутствие на дифрактограммах порошковых смесей четких пиков, соответствующих AlOOH, на их месте регистрируются размытые дифракционные максимумы, что можно трактовать как переход кристаллической фазы AlOOH в рентгеноаморфное состояние. Интенсивности пиков фазы c'-ZrO2 значительно уменьшились по сравнению с дифрактограммой, приведенной на рис. 2б, что, вероятно, также связано с частичным переходом фазы c'-ZrO2 в рентгеноаморфное состояние.
Рис. 6.
Дифрактограммы порошков составов AlZr-1 (а) и AlZr-2 (б) после МА в течение 30 мин: 1 − AlOOH, 2 − с'-ZrО2.

Следует отметить, что при использовании МА очень важным является вопрос сохранения дисперсности порошков после завершения процесса. В результате упругопластических деформаций поверхностные слои порошков приходят в термодинамически неравновесное состояние, характеризующееся резким повышением их химической активности [19], поэтому при взаимодействие МА-порошков с окружающей средой происходит формирование вторичных структур, которые изменяют первоначальную кристаллическую структуру порошков. Так, в случае системы Al2O3−ZrO2〈Y2O3〉 после 3 ч старения на воздухе механоактивированных в течение 30 мин порошков AlZr-1 и AlZr-2 наблюдается взаимодействие Н2Огаз с компонентами МА-смесей, приводящее к формированию на поверхности порошков некоторого количества Al(OH)3, а также моноклинного твердого раствора на основе диоксида циркония (m-ZrO2), который образуется в результате фазового перехода c'-ZrO2 → m-ZrO2 [22] (рис. 7). Присутствие фазы m-ZrO2 в составе МА-порошков может вызвать проблемы при их спекании, а также снизить механические параметры спеченной керамики системы Al2O3−ZrO2〈Y2O3〉 [8].
Рис. 7.
Дифрактограммы МА-порошка состава AlZr-2 до (а) и после старения на воздухе в течение 3 ч (б): 1 − AlOOH, 2 − c'-ZrO2, 3 − Al(OH)3, 4 – m-ZrO2 (для МА-порошка состава AlZr-1 дифрактограмма анaлогичная).
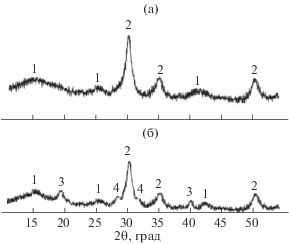
После нахождения МА-порошков AlZr-1 и AlZr-2 в течение 3 ч на воздухе зафиксировано уменьшение их дисперсности, при этом распределение частиц по размерам становится бимодальным (250−1000 и 1000−1700 нм) (рис. 5б).
Получение керамики в системе Al2O3−ZrO2〈Y2O3〉. Из смесей МА-порошков, подвергнутых МА в течение 30 мин, методом холодного одноосного прессования при давлениях 100, 150 и 200 МПа формовали компакты, которые последовательно обжигали в интервале температур 800–1500°C. Скорость нагрева составляла ~350–400°С/ч, продолжительность изотермической выдержки при каждой температуре − 2 ч. Достаточно высокая скорость нагрева была выбрана для уменьшения скорости роста кристаллитов. Спеченные образцы после обжига сразу вынимали из печи, т.к. закалка оксидной керамики приводит к достижению более высокой плотности, чем охлаждение вместе печью, поскольку при быстром охлаждении керамики возникает обжимающее действие наружных слоев материала [23].
В МА-порошках после обжига при 800°C, по данным РФА, происходит фазовый переход метастабильного кубического твердого раствора на основе диоксида циркония в тетрагональную модификацию (c'-ZrO2 → t-ZrO2). Образование фазы α-Al2O3 фиксируется начиная с температуры 1000°C, а при 1200°C образцы AlZr-1 и AlZr-2 состоят из двух индивидуальных фаз: α-Al2O3 и t-ZrO2 (рис. 8), соотношение которых сохраняется до 1500°C. Изменение среднего размера кристаллитов (d) фаз α-Al2O3 и t-ZrO2 в интервале температур 1000−1500°C приведено на рис. 9. Видно, что кристаллиты t-ZrO2 растут быстрее, чем α-Al2O3, поэтому можно предположить, что фаза на основе диоксида циркония выступает в качестве ингибитора роста кристаллитов оксида алюминия.
Рис. 8.
Дифрактограммы керамических образцов AlZr-1 (а) и AlZr-2 (б) после обжига при 1200°C (2 ч): 1 – α-Al2О3, 2 – t-ZrO2.
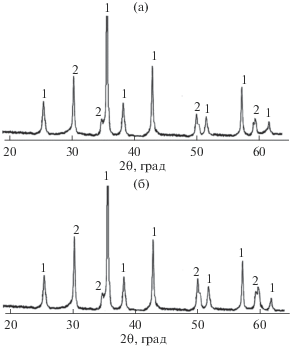
Рис. 9.
Изменение среднего размера кристаллитов фаз α-Al2О3 (1, 2) и t-ZrO2 (1', 2 ') в керамических образцах AlZr-1(1, 1') и AlZr-2 (2, 2') в интервале температур 1000−1500°C.
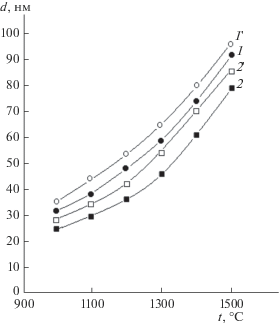
Результаты исследования процесса спекания керамики в зависимости от температуры и давления прессования компактов представлены на рис. 10. Прессование образцов при 100 МПа неэффективно для получения плотной керамики даже при использовании МА-порошков. Спекание образцов AlZr-1 и AlZr-2, спрессованных при 150 МПа, происходит более активно, но оптимальным давлением прессования для получения плотной керамики на основе α-Al2O3 из смесей МА-порошков AlOOH и с'-ZrО2 является давление 200 МПа (рис. 10, кривая 3), величина относительной плотности образцов в этом случае составляет 98−99%. На кривых 2 и 3 (рис. 10), характеризующих зависимость ρотн от температуры спекания, можно выделить три участка: 800−900, 900−1300 и 1300−1500°C. До 900°C образцы практически не спекаются, относительная плотность керамики начинает возрастать после 900°C. Наиболее интенсивно процесс спекания происходит в интервале 900−1300°C, о чем свидетельствует значительный рост ρотн. Увеличение относительной плотности образцов в диапазоне температур 1300−1500°C замедляется и практически достигает единицы.
Рис. 10.
Изменение относительной плотности керамических образцов AlZr-1 (а) и AlZr-2 (б) при спекании МА-порошков в интервале температур 800−1500°C в течение 30 мин. pпрес = 100 (1), 150 (2, 4), 200 МПа (3), 4 − порошки, не подвергнутые МА (для сравнения).
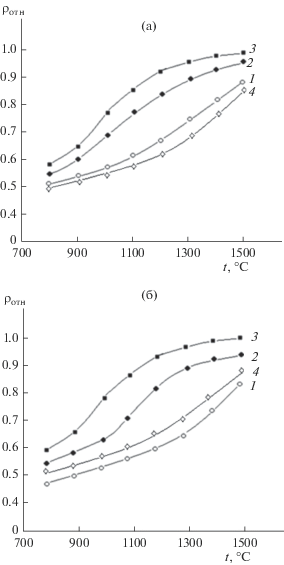
Физико-химические и механические свойства керамических образцов составов AlZr-1 и AlZr-2, спеченных при 1400°C, приведены в табл. 2. Фазы (α-Al2O3 и t-ZrO2), являющиеся компонентами композиций системы Al2O3–ZrO2〈Y2O3〉, находятся в наноразмерном состоянии (<100 нм). Присутствие в алюмооксидной матрице фазы t-ZrO2 позволяет почти в два раза увеличить трещиностойкость (К1С) керамики по сравнению с чистым оксидом алюминия. Зафиксировано некоторое уменьшение (~ на 10%) твердости (HV), но ее значения остались на достаточно высоком уровне.
Таблица 2.
Физико-химические и механические свойства керамики в системе Al2O3−ZrO2〈Y2O3〉, спеченной при 1400°C (2 ч)
Условное обозначение | AlZr-1 | AlZr-2 |
---|---|---|
Фазовый состав керамики | α-Al2O3 + t-ZrO2 | α-Al2O3 + t-ZrO2 |
Кажущаяся плотность (ρк), г/см3 | 4.08 | 4.32 |
Открытая пористость (Поткр), % | 2.5 | 1.8 |
Средний размер кристаллитов фазы α-Al2O3, нм | 73 | 61 |
Средний размер кристаллитов фазы t-ZrO2, нм | 87 | 70 |
Микротвердость по Виккерсу (HV), ГПа | 18.9 | 17.8 |
Прочность на изгиб (σизг), МПа | 680 | 720 |
Трещиностойкость (К1С), МПа м1/2 | 6.1 | 6.9 |
ТКЛР × 106, °C–1 (20−1000°С) | 7.5 | 8.2 |
Химическая стойкость | HF, H2SO4, HNO3, NaOH | HF, H2SO4, HNO3, NaOH |
ЗАКЛЮЧЕНИЕ
Разработана и экспериментально реализована технология получения нанокристаллической керамики (60−90 нм) на основе оксида алюминия в системе Al2O3–ZrO2〈Y2O3〉.
Установлено эффективное влияние МА на дисперсность смеси порошков-прекурсоров AlOOH + + с'-ZrО2. Выявлено, что МА в течение 30 мин наиболее оптимальна для получения высокодисперсных (Sуд = 124 и 132 м2/г) порошков составов AlZr-1 и AlZr-2. Подобраны давление прессования и температура спекания МА-порошков в системе Al2O3–ZrO2〈Y2O3〉. Показано положительное влияние МА на процесс спекания керамических образцов, наибольший эффект уплотнения которых наблюдается в интервале температур 900−1300°C, а максимальная относительная плотность (98−99%) керамики достигается при 1400 и 1500°C соответственно.
При оптимальных условиях (pпрес = 200 МПа и t = 1400°C) получена композиционная нанокера-мика с пористостью 1.5–2.5%, микротвердостью ~18–19 ГПа и прочностью на изгиб ~680–720 МПа.
Список литературы
Лукин Е.С., Макаров Н.А., Козлов А.И. и др. Современная оксидная керамика и области ее применения // Конструкции из композиционных материалов. 2007. № 3. С. 3–13.
Кульков С.Н., Григорьев М.Н. Особенности синтеза керамики на основе порошков Al2O3 различной дисперсности // Перспективные материалы. 2010. № 6. С. 73−75.
Guimares F.A.T., Silva K.L., Trombini V. Correlation between Microctructure and Mechanical Properties of Al2O3/ZrO2 Nanocomposites // Ceram. Int. 2009. V. 35. P. 741–745.
Tuan W.H., Chen R.Z., Wang T.C. Mechanical Properties of Al2O3/ZrO2 Composites // Eur. Ceram. Soc. 2002. V. 22. P. 2827–2833.
Moraes M.C., Elias C.N., Filho J.D., Oliviera L.G. Mechanical Properties of Alumina-Zirconia Composites for Ceramic Abutments // Mater. Res. 2004. № 7(4). P. 643–649.
Жарныльская А.Л., Вольхин В.В., Щербань М.Г., Ройтер Х. Синтез прекурсора алюмооксидной керамики, упроченной диоксидом циркония, из неорганических соединений // Журн. прикл. химии. 2008. Т. 81. Вып. 7. С. 1069−1074.
Веселов С.В., Стукачева Н.С., Кузьмин Р.И. и др. Структура и механические свойства керамических материалов системы Al2O3–ZrO2 // Науч. вестн. НГТУ. 2016. Т. 65. № 4. С. 207–217.
Хасанов О.Л., Двилис Э.С., Бикбаева З.Г. Методы компактирования и консолидации наноструктурных материалов и изделий. Томск: Изд. Томского политех. ун-та, 2008. 196 с.
Panova T.I., Arsent’ev M.Yu., Morozova L.V., Drozdova I.A. Synthesis and Investigation of the Structure of Ceramic Nanopowders in the ZrO2–CeO2–Al2O3 // Glass Phys. Chem. 2010. V. 36. № 4. P. 470–477.
Морозова Л.В., Калинина М.В., Арсентьев М.Ю., Шилова О.А. Влияние криохимической и ультразвуковой обработки на текстуру, термическое разложение ксерогелей и свойства нанокерамики в системе ZrO2〈Y2O3〉–Al2O3 // Неорган. материалы. 2017. Т. 53. № 6. С. 654–661.
Волкова Г.И., Иванов В.Г., Кухоренко О.А. Влияние условий синтеза на структуру и свойства ультрадисперсных оксигидроксидов алюминия // Химия в интересах устойчивого развития. 2005. Т. 13. С. 427–4329.
Толчев А.В., Клещев Д.Г., Лопушан В.И. Влияние механохимической активации и добавки α-Fe2O3 на формирование корунда при термических превращениях γ-Al(OH)3 // Журн. прикл. химии. 2002. Т. 75. Вып. 9. С. 1417–1421.
Болдырев В.В. Механохимические методы активации неорганических веществ // Журн. ВХО им. Д.И. Менделееева. 1988. Т. 33. № 4. С. 14–23.
Гусев А.И., Курлов А.С. Аттестация нанокристаллических материалов по размеру частиц (зерен) // Металлофизика и новейшие технологии. 2008. Т. 30. № 5. С. 679–694.
Вассерман И.М. Химическое осаждение из растворов. Л.: Химия, 1980. 208 с.
Химическая энциклопедия / Под ред. Кнунянца И.Л. М.: Сов. энциклопедия, 1989. Т. 2. С. 119.
Morozova L.V., Kalinina M.V., Koval’ko N.Yu. et al. Preparation of Zirconia Based Nanoceramics with a High Degree of Tetragonality // Glass Phys. Chem. 2014. V. 40. № 3. P. 352–355.
Зырянов В.В. Механохимическая керамическая технология // Механохимический синтез в неорганической химии. Новосибирск: Наука, 1991. С. 102.
Бутягин П.Ю., Стрелецкий А.Н. Кинетика и энергетический баланс в механохимических превращениях // Физика твердого тела. 2005. Т. 45. Вып. 5. С. 830–836.
Болдырев В.В. Механохимия и механохимическая активация твердых веществ // Успехи химии. 2006. Т. 75. № 3. С. 203–216.
Ильин А.П., Широков Ю.Г., Прокофьев В.Ю. Механохимическое активирование глинозема // Неорган. материалы. 1995. Т. 31. № 7. С. 933–936.
Chevalier J., Gremillard L., Deville S. Low-Temperature Degradation of Zirconia and Implications for Biomedical Implants // Annu. Rev. Mater. Res. 2007. V. 37. № 1. P. 1–32.
Морозова Л.В., Калинина М.В., Панова Т.И., Попов В.П., Дроздова И.А., Шилова О.А. Синтез и исследование твердых растворов на основе системы ZrO2–HfO2–Y2O3 (СеО2) // Физика и химия стекла. 2017. Т. 43. № 5. С. 522−530.
Дополнительные материалы отсутствуют.
Инструменты
Неорганические материалы