Неорганические материалы, 2020, T. 56, № 10, стр. 1145-1150
Закономерности формирования структуры градиентных композиционных материалов на основе МАХ-фазы Ti3AlC2 на титане
А. Д. Прокопец 1, *, А. С. Константинов 1, А. П. Чижиков 1, П. М. Бажин 1, А. М. Столин 1
1 Институт структурной макрокинетики и проблем материаловедения им. А.Г. Мержанова
Российской академии наук
142432 Московская обл., Черноголовка, ул. Академика Осипьяна, 8, Россия
* E-mail: arina@ism.ac.ru
Поступила в редакцию 04.02.2020
После доработки 04.06.2020
Принята к публикации 08.06.2020
Аннотация
Рассмотрены основные закономерности формирования структуры градиентных композиционных материалов на основе МАХ-фазы Ti3AlC2 на титане в условиях горения и высокотемпературного деформирования, реализуемых при свободном СВС-сжатии. Подтверждена возможность образования компактного градиентного композиционного материала за десятки секунд в одну технологическую стадию при относительно низких давлениях (50 МПа). Показано, что, изменяя время задержки перед приложением давления, можно регулировать структуру и механические свойства получаемого материала. Установлено, что наибольшее количество карбидных зерен образуется в верхней части материала, а по мере приближения к титану их количество снижается с повышением количества пластинчатых зерен МАХ-фазы. Изучены механические характеристики полученных материалов: изменение микротвердости по высоте композиционного материала, модуль упругости, предел прочности на изгиб.
ВВЕДЕНИЕ
В авиационной промышленности и судостроении широко используются сплавы на основе титана [1–4]. Однако невысокие значения модулей упругости титановых сплавов ограничивают их применимость в достаточно жестких конструкциях [5]. В этой связи целесообразно получение градиентных композиционных материалов на титане, которые позволят повысить его физико-механические характеристики [6–10].
В этом отношении перспективными являются металлокерамические материалы на основе МАХ-фаз. Эти материалы обладают высокой электро-, теплопроводностью и низкими коэффициентами трения по сравнению с известными твердыми материалами, высокой жесткостью в сочетании с низкой плотностью и стойкостью к повреждениям, проявляют высокую стойкость к окислению и тепловому удару [11, 12]. Установлено, что кристаллическая решетка МАХ-фаз допускает скольжение дислокаций только в плоскостях базиса, что наряду со слабыми связями между атомными слоями приводит к сильной анизотропии механических свойств МАХ-фаз и образованию полос изгиба [13, 14]. Важной особенностью материалов на основе МАХ-фаз является легкость их механической обработки, которая делает возможным изготовление различных сложных элементов.
К основным методам получения материалов на основе МАХ-фаз относятся горячее изостатическое прессование и искровое плазменное спекание [15]. Однако для этих методов характерны значительные энергетические затраты, сложность и многостадийность технологических циклов, малая производительность, они не всегда обеспечивают требуемое качество материалов по структуре, свойствам и чистоте.
В представленной работе для получения градиентных композиционных материалов был применен метод свободного СВС-сжатия, который основан на сочетании процессов горения исходных порошковых реагентов и последующего сдвигового высокотемпературного деформирования продуктов синтеза в условиях одноосного сжатия [16]. В результате за десятки секунд, в одну технологическую стадию при относительно низких давлениях (менее 100 МПа) происходит образование компактного материала с заданными структурой и свойствами.
Целью настоящей работы являлось получение методом свободного СВС-сжатия градиентных композиционных материалов на основе МАХ-фазы Ti3AlC2 на титане, изучение особенностей их строения и измерение механических характеристик.
ЭКСПЕРИМЕНТАЛЬНАЯ ЧАСТЬ
В качестве объектов исследования были выбраны порошки титана (45 мкм, 99.1%), алюминия (5 мкм, 99.5%) и углерода (1 мкм, 99.1%) в следующем соотношении (мас. %): 64.2 (Ti), 27.1 (Al), 8.7 (С). Порошки были предварительно просушены в сушильных шкафах в течение 5–6 ч и смешаны в шаровых мельницах. Холодным односторонним прессованием под давлением 5 МПа получали цилиндрические шихтовые заготовки диаметром 30 и высотой 12 мм с относительной плотностью 0.6. Нагретую до 500°С исходную шихтовую заготовку размещали в середине титановой подложки (99.7%) диаметром 50 и толщиной 3 мм. После инициации горения в режиме СВС и заданного времени задержки (1.2 и 2 с) осуществляли сжатие материала плунжером пресса под давлением 50 МПа.
Предел прочности при изгибе определяли на испытательном оборудовании Instron 1195 при скорости нагружения vн = 2 мм/мин и нагрузке P = 50 кН. Пять образцов размерами 5 × 5 × 35 мм вырезались от края пластины к центру, далее стороны доводились на шлифовальном станке до плоскопараллельного состояния. Показатели микротвердости и модуль Юнга измеряли на микротвердомере марки MHTX S/N: 01-2476 при максимальной нагрузке 3 Н, скорости приложения нагрузки 4000 нм/мин с выдержкой при максимальной нагрузке 15 с. Микроструктуру образцов изучали с помощью автоэмиссионного сканирующего электронного микроскопа сверхвысокого разрешения Carl Zeiss Ultraplus, рентгенофазовый анализ проводили на порошковом рентгеновском дифрактометре ARL X’TRA.
РЕЗУЛЬТАТЫ И ОБСУЖДЕНИЕ
Методом свободного СВС-сжатия были получены два типа образцов из градиентных композиционных материалов на основе МАХ-фазы Ti3AlC2 на титане, соответствующих времени задержки перед приложением давления 1.2 и 2 с (рис. 1). Как показали результаты РФА, полученные образцы состоят из МАХ-фазы Ti3AlC2 (до 80 мас. %), небольшого количества Ti2AlC (до 5 мас. %), интерметаллидов TiAl3 и TiAl и TiC. Как показано ранее [16], при большем времени задержки перед приложением давления (5–6 с) формируется слоистый композиционный материал, в поперечном сечении которого верхний слой состоит из металлокермического материала на основе МАХ-фаз Ti3AlC2 и Ti2AlC, TiC и Ti5Al11 и TiAl3; переходный слой состоит из интерметаллидов TiAl2 и TiAl3; нижний слой – из титана. При малых временах задержки (1.2–2 с) расплавленным продуктам синтеза под действием силы гравитации недостаточно времени, чтобы переместиться к титановому слою и образовать переходный интерметаллидный слой. В результате при времени задержки 1.2 с на расстоянии до 1 мм от титана наблюдаются области, обогащенные интерметаллидными фазами (рис. 1а), при времени задержки 2 с – на расстоянии до 0.8 мм (рис. 1б). Таким образом, изменяя время задержки перед приложением давления, можно регулировать структуру получаемого композиционного материала.
Наибольшее количество карбидных зерен образовалось в верхней части материала, а по мере приближения к подложке их количество снижается с повышением количества пластинчатых зерен МАХ-фазы. При этом в верхней части материала при приложении давления после 1.2 с образуются округлые карбидные зерна размерами до 10–12 мкм (рис. 2а), а при более длительной задержке (2 с) зерна вырастают до 20–25 мкм (рис. 2б). Как известно, образование МАХ-фаз происходит в температурном интервале 1350–1500°С [11], поэтому более длительное нахождение синтезированного материала в данном температурном интервале способствует увеличению содержания МАХ-фазы и снижению количества побочных продуктов в виде интерметаллидов и карбидов титана. Как показали результаты СЭМ, в синтезированном материале при времени задержки 1.2 с в центральной части образовалось большее количество карбидных зерен (рис. 2в) по сравнению с временем задержки 2 с (рис. 2г).
Рис. 2.
Результаты СЭМ полученных образцов: а, б – верхняя область, в, г – средняя область, д, е – переходная область; а, в, д – время задержки 1.2 с; б, г, е – 2 с.
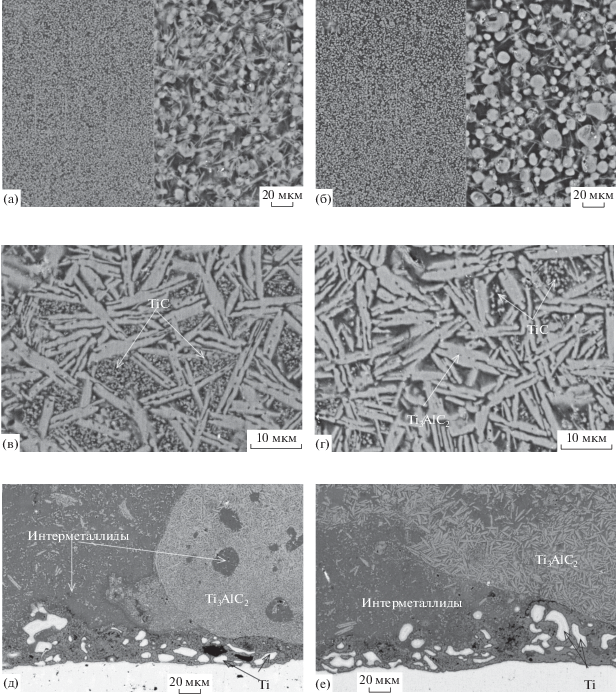
Повышение количества карбида титана в сочетании с уникальными свойствами МАХ-фазы позволяет увеличить механические характеристики полученных материалов. При этом толщина пластинчатых зерен МАХ-фазы при времени задержки 1.2 с составила до 2.8 мкм, а при 2 с – до 3.6 мкм. Переходный слой представляет собой смесь расплавленного титанового слоя, интерметаллидов и МАХ-фаз. Граница титанового слоя толщиной 2–5 мкм обогащена расплавленным алюминием и титаном, которые образовали между собой интерметаллиды TiAl2 и TiAl3. По мере приближения к титановому слою количество алюминия сокращается. За счет повышенного давления в зоне синтезированный материал–титановый слой возрастает кондуктивный отвод тепла, образовавшиеся частицы при кристаллизации не успевают вырасти и их размер составляет не более 100 нм.
На рис. 3 приведены усредненные результаты измерений модуля Юнга и микротвердости по высоте градиентного комозиционного материала для образцов, полученных при времени задержки перед приложением нагрузки 1.2 и 2 с. Измерения проводились на шлифах, изготовленных вдоль прикладываемой нагрузки на синтезированный материал при свободном СВС-сжатии от поверхности и до титана с шагом 0.4 мм. Места индентирования выбирались идентичные по высоте для двух типов образцов. Как показали измерения, значения микротвердости и модуля Юнга на поверхности материала наибольшие, что объясняется максимальным содержанием карбидной фазы. По сравнению с титаном (модуль Юнга до 120 ГПа, микротвердость до 4 ГПа) значения этих характеристик на поверхности полученного композиционного материала существенно повысились: модуль Юнга более чем в 2 раза, микротвердость более чем в 5 раз. По мере приближения к титановому слою эти параметры снижаются, а после переходной зоны (2 мм от поверхности рис. 3) снижение более резкое. Также установлено, что для образцов, полученных при времени задержки 1.2 с, значения механических характеристик выше, что также подтверждает наличие большего количества карбидной фазы.
Рис. 3.
Изменение микротвердости (разброс значений ±0.3 ГПа) (1, 2) и модуля Юнга (разброс значений ±10 ГПа) (3, 4) по высоте градиентного композиционного материала, полученного при времени задержки 1.2 с (1, 3); 2 с (2, 4).
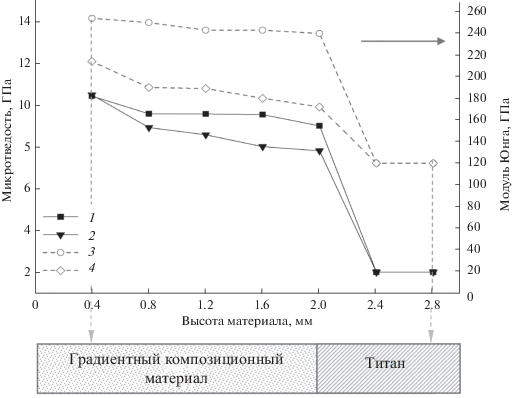
Испытания на изгиб показали, что керамический материал после деформирования частично разрушился, при этом бóльшая его часть осталась на титане. Данные результаты характеризуют наличие хорошей адгезии керамического материала с титаном. На основе проведенных измерений установлено, что среднее значение предела прочности при изгибе образцов, полученых при времени задержки 1.2 с, равно 481 МПа, при 2 с – 470 МПа. Отметим, что у материалов на основе МАХ-фазы Ti3AlC2 предел прочности на изгиб равен 169 МПа для крупнозернистой структуры и 340 МПа для мелкозернистой. Таким образом предел прочности полученного композиционного материала повысился в 1.4–2.8 раза.
Полученные экспериментальные результаты показали, что в условиях свободного СВС-сжатия возможно получение градиентных композиционных материалов на основе МАХ-фазы состава Ti3AlC2 за десятки секунд в одну технологическую стадию при относительно низком давлении (50 МПа).
ЗАКЛЮЧЕНИЕ
Методом свободного СВС-сжатия на титане получен градиентный композиционный материал, в поперечном сечении которого верхний слой состоит из металлокермического материала на основе МАХ-фазы Ti3AlC2, упрочненного карбидными зернами. За счет особенностей процесса синтеза наибольшее количество карбидных зерен образовалось на поверхности материала, по мере приближения к титановому слою их содержание снижается.
Показано, что время задержки перед приложением давления оказывает влияние на макро- и микроструктуру. С уменьшением времени задержки размер структурных составляющих снижается до 2 раз, а содержание карбидных зерен увеличивается, что приводит к повышению механических характеристик материала. По сравнению с материалами на основе МАХ-фазы Ti3AlC2 предел прочности полученного градиентного композиционного материала повысился в 1.4–2.8 раза, а по сравнению с титаном модуль Юнга увеличился более чем в 2 раза, микротвердость – более чем в 5 раз.
Список литературы
Ширяев А.А., Ночовная Н.А., Анташев В.Г., Алексеев Е.Б. Перспективы и особенности применения современных экономнолегированных высокопрочных титановых сплавов // Технология легких сплавов. 2013. № 2. С. 29–35.
Каблов Е.Н. Стратегические направления развития материалов и технологий их переработки на период до 2030 года // Авиационные материалы и технологии. М.: ВИАМ, 2012. С. 7–17.
Орыщенко А.С., Леонов В.П., Михайлов В.И. Титанический труд: к 60-летию развития титановых технологий в России // Инновации. 2017. № 7(225). С. 7–10.
Головкин П.А., Валиахметов С.А., Фесенко С.А. Перспективы повышения надежности изделий из титановых сплавов в летательных аппаратах // Технология металлов. 2011. № 9. С. 16–21.
Орыщенко А.С., Леонов В.П., Ртищева Л.П., Копылов В.Н., Мартынов К.Г. Современное состояние производства и применение труб из титановых сплавов в атомной энергетике и судостроении // Титан. 2018. № 3(61). С. 21–32.
Rahmani R., Antonov M., Kollo L. Wear Resistance of (Diamond-Ni)-Ti6Al4V Gradient Materials Prepared by Combined Selective Laser Melting and Spark Plasma Sintering Techniques // Adv. Tribology. 2019. № 5415897.
Bai H., Zhong L., Shang Z. et al. Microstructure and Mechanical Properties of TiC-Fe Surface Gradient Coating on a Pure Titanium Substrate Prepared in situ // J. Alloys Compd. 2019. V. 771. P. 406–417.
Насакина Е.О., Сударчикова М.А., Спрыгин Г.С., Баскакова М.И., Федюк И.М., Беспамятнова А., Борисов Н.И., Данилова Е.А., Севостьянов М.А., Григорович К.В., Колмаков А.Г. Исследование формирования защитного титанового поверхностного слоя при магнетронном распылении в зависимости от геометрии потока // Актуальные вопросы машиноведения. 2018. Т. 7. С. 294–296.
Agzamov R.D., Tagirov A.F., Ramazanov K.N. Influence of Ion Nitriding Regimes on Diffusion Processes in Titanium Alloy TI–6AL–4V // Diffus. Defect Data, Pt. A. 2018. V. 383. P. 161–166.
Wu F., Zhou W., Han Y. et al. Effect of Alloying Elements Gradient on Solid-State Diffusion Bonding between Aerospace Aluminum Alloys // Materials. 2018. V. 11. № 8. № 1446.
Magnus C., Cooper D., Sharp J. et al. Microstructural Evolution and Wear Mechanism of Ti3AlC2–Ti2AlC Dual MAX Phase Composite Consolidated by Spark Plasma Sintering (SPS) // Wear. 2019. V. 438. № 203013.
Xu L., Zhu D., Grasso S. et al. Effect of Texture Microstructure on Tribological Properties of Tailored Ti3AlC2 Ceramic // J. Adv. Ceram. 2017. V. 6. № 2. P. 120–128.
Drouelle E., Joulain A., Cormier J. et al. Deformation Mechanisms during High Temperature Tensile Creep of Ti3AlC2 MAX Phase // J. Alloys Compd. 2017. V. 693. P. 622–630.
Zhang Z., Duan X., Qiu B. et al. Preparation and Anisotropic Properties of Textured Structural Ceramics: A Review // J. Adv. Ceram. 2019. V. 8. № 3. P. 289–332.
Benamor A., Hadji Y., Chiker N. et al. Spark Plasma Sintering and Tribological Behavior of Ti3SiC2–Ti5Si3–TiC Composites // Ceram. Int. 2019. V. 45. № 17. P. 21781–21792.
Аверичев О.А., Прокопец А.Д., Столин П.А. Структурообразование слоистых керамических материалов Ti/Ti–Al–C, полученных методом свободного CВC-сжатия // Новые огнеупоры. 2019. № 4. С. 57–60.
Дополнительные материалы отсутствуют.
Инструменты
Неорганические материалы