Неорганические материалы, 2020, T. 56, № 12, стр. 1336-1341
Формирование состава и структуры в процессе СВС-металлургии композиционных материалов на основе Mo, легированных Nb, Si и B
Д. Е. Андреев 1, Ю. С. Вдовин 1, В. И. Юхвид 1, *, Н. В. Сачкова 1, Т. И. Игнатьева 1, И. Д. Ковалев 1
1 Институт структурной макрокинетики и проблем материаловедения им. А.Г. Мержанова
Российской академии наук
142432 Московская обл., Черноголовка, ул. Академика Осипьяна, 8, Россия
* E-mail: yukh@ism.ac.ru
Поступила в редакцию 26.11.2019
После доработки 13.07.2020
Принята к публикации 17.07.2020
Аннотация
Впервые изучена возможность синтеза литых композиционных материалов на основе Mo, легированных Nb, Si и B, методом центробежной СВС-металлургии и получены новые результаты по управлению их составом и структурой. Для синтеза использовали комбинации высокоэкзотермического (MoO3/Nb2O5/Al/Si/B) и низкоэкзотермического (Mo/Nb/Si/B) составов. Определено влияние соотношения высокоэкзотермического и низкоэкзотермического составов (α) и величины перегрузки (a) на состав и структуру литых композиционных материалов. Установлено, что смеси сохраняют способность к горению при содержании низкоэкзотермического состава до 80%. Продукты горения имеют литой вид при 0 ≤ α ≤ 65%. В интервале α от 0 до 40% и центробежном воздействии от 40g до 400g продукты горения формируются в виде двухслойного слитка: нижний слой Mo–Nb–Si–B (целевой продукт) и верхний слой Al2O3 (шлаковый продукт). Оптимальными параметрами для получения литых образцов Mo–Nb–Si–B являются: α = 20–30% и а > 100g.
ВВЕДЕНИЕ
Большой потенциал для реализации в промышленности имеют композиционные материалы (КМ) на основе Nb–Si и Mo–Si [1, 2]. Температуры плавления этих КМ превышают 1750 и 1950°C соответственно. Эти жаропрочные материалы могут иметь более высокую рабочую температуру, чем у промышленных суперсплавов. В настоящее время материалы на основе Nb–Si и Mo–Si разрабатываются для горячего сечения турбин как для авиационных двигателей, так и для наземных турбин. Эти материалы имеют перспективу увеличить рабочую температуру более чем на 150°C по сравнению с никелевыми суперсплавами. Силициды молибдена имеют высокую стойкость к окислению на воздухе при температурах 1000–1650°C, но они подвержены катастрофическому окислению при 600–800°C. Добавление бора в КМ на основе Mo–Si позволяет сформировать плотное боросиликатное стекло и защитить КМ от окисления [3, 4].
Была разработана методика получения КМ [4, 5], согласно которой при нагреве смеси Mo, Si и B и последующем быстром охлаждении формируется микроструктура, состоящая из матрицы твердого раствора на основе Mo, в которой распределены включения Mo3Si и/или Mo5SiB2. Полученная микроструктура обеспечивает повышение сопротивления ползучести и окислению [6–8]. При добавлении Nb в смесь на основе Mo, Si и B и последующем горячем изостатическим прессовании были получены высокоплотные КM состава (ат. %) Mo–3Nb–9Si–8B с температурой плавления, превышающей 1950°C.
В настоящее время для получения жаропрочных материалов и изделий из них используют метод направленной кристаллизации, порошковую металлургию и аддитивные технологии. Перспективу использования имеет СВС-металлургия [9, 10].
Цель настоящей работы состоит в разработке процесса, основанного на горении смесей термитного типа, позволяющего получать литые КМ Mo–Nb–Si–B. Большое внимание уделено исследованию влияния состава смеси и величины перегрузки на горение термитной смеси, гравитационную сепарацию двухфазного расплава продуктов горения, состав и структуру целевого продукта (Mo–Nb–Si–B).
ТЕРМОДИНАМИЧЕСКИЙ РАСЧЕТ
Термодинамические расчеты в программе “Термо” [11] показали, что адиабатическая температура горения стехиометрической смеси MoO3 + + 2Al равна 3808 К. При этой температуре конденсированные продукты горения, Mo и Al2O3, находятся в жидкофазном состоянии. Высокая температура горения (Тг) позволяет вводить в смесь MoO3 + Al различные легирующие и технологические добавки и получать материалы на основе молибдена в литом виде. Так, при вариации соотношения масс (α) высокоэкзотермического “термитного” (MoO3/Nb2O5/Al/Si/B) и низкоэкзотермического (Mo/Nb/Si/B) составов (табл. 1, составы 1 и 2) от 0 до ~35% сохраняется возможность реализации Тг > > 3000 К и получения литых КМ на основе молибдена, легированных Nb, Si и B (рис. 1). Величину α рассчитывали по формуле: α = M2/(M1 + M2) × × 100%, где M1 – масса высокоэкзотермического состава (MoO3/Nb2O5/Al/Si/B), M2 – масса низкоэкзотермического состава (Mo/Nb/Si/B) в исходной смеси.
Таблица 1.
Содержание компонентов в составах 1 и 2
Исходные составы | C, мас. % | ||||||
---|---|---|---|---|---|---|---|
Mo | Si | Nb | B | MoO3 | Nb2O5 | Al | |
1 | – | 1.5 | – | 0.5 | 68.9 | 2.4 | 26.7 |
2 | 92.5 | 3.0 | 3.4 | 1.1 | – | – | – |
Рис. 1.
Влияние соотношения смесей 1 и 2 (α) на расчетную адиабатическую температуру (Тг), состав конденсированной (Cc) и газовой (Cg) фаз продуктов горения: α = M2/(M1 + M2) × 100%, где M1 и M2 – массы составов 1 и 2.
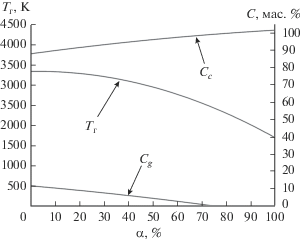
В расчетном составе продуктов горения присутствует значительное количество газов (паров металлов Al и Mo, Al2O, AlO2, Al2O2, MoO, MoO2, NbO, NbO2, BO, SiO и др.). С ростом α Тг и суммарное содержание газообразных продуктов Cg уменьшаются (рис. 1).
ЭКПЕРИМЕНТАЛЬНАЯ ЧАСТЬ
В экспериментах, так же как и в термодинамических расчетах, использовали комбинацию высокоэкзотермического (MoO3/Nb2O5/Al/Si/B) и низкоэкзотермического (Mo/Nb/Si/B) составов (табл. 1). Содержание целевых элементов (Mo, Nb, Si и B) в обоих составах было одинаковым (мас. %): Mo – 92.5, Nb – 3.4, Si – 3.0, B – 1.1. Как правило, горение смесей термитного типа с высоким уровнем газообразования сопровождается интенсивным разбросом смеси из-за использования кислороднасыщенных исходных реагентов (оксидов) и реализации высоких температур, приводящих к испарению продуктов горения. Поэтому с целью подавления разброса эксперименты по синтезу литых КМ на основе Mo, легированных Nb, Si и B, проводили на центробежных установках под воздействием перегрузки, варьируя ее от 1g до 400g, позволяющей разделить продукты горения (расплавы литых КМ и оксидной фазы) за счет разности удельных весов. Смеси массой m = = 40 г сжигали в кварцевых стаканчиках диаметром d = 25 мм, высотой h = 70 мм. Определяли линейную скорость горения (u), относительную потерю массы при горении (η1) и полноту выхода целевых элементов в слиток (η2). Характеристики рассчитывали по формулам: u = h/τг, η1 = = [(m1–m2)/m1] × 100%, η2 = = (m/mр) × 100%, где h – высота слоя исходной смеси, τг – время горения слоя, m1 и m2 – массы исходной смеси и продуктов горения, m и mр – экспериментальная и расчетная массы слитка.
Для определения химического состава и структуры продуктов синтеза использовали методы аналитической химии и автоэмиссионный сканирующий электронный микроскоп Carl Zeiss Ultra plus на базе Ultra 55. Фазовый состав конечных продуктов горения определяли на рентгеновском дифрактометре ДРОН-3М, в качестве источника излучения использовалась рентгеновская трубка типа БСВ–27 с медным анодом (λ = 1.54178 Å). Содержание бора определяли методом потенциометрического титрования маннитборной кислотой.
РЕЗУЛЬТАТЫ И ОБСУЖДЕНИЕ
Установлено, что горение высокоэкзотермического состава (MoO3/Nb2O5/Al/Si/B) в атмосферных условиях без перегрузки протекает с полным выбросом продуктов горения из кварцевой формы. Для подавления разброса при горении использовали комбинацию высокоэкзотермического (MoO3/Nb2O5/Al/Si/B) и низкоэкзотермического (Mo/Nb/Si/B) составов (табл. 1), а также воздействие перегрузки.
В первой серии экспериментов для получения литых КМ на основе Mo при заданной величине перегрузки варьировали α. Во второй серии экспериментов для состава, выбранного по результатам первой серии, изучено влияние перегрузки (a). Показано, что смеси сохраняют способность к горению в интервале 0 ≤ α ≤ 80%, а продукты горения имеют литой вид при 0 ≤ α ≤ 65. В интервале α от 0 до 40% и перегрузки от 40g до 400g продукты горения формируются в виде двухслойного слитка: нижний слой (Mo–Nb–Si–B) – целевой продукт и верхний слой (Al2O3) – шлаковый продукт.
Оптимальными параметрами для получения литых КМ являются α = 20–30% и а > 100g. В этих диапазонах формируются малопористая структура литых КМ и четкая граница между металлическим и шлаковым слоями.
Формирование химического и фазового составов литых КМ. На рис. 2 и 3 показано влияние содержания низкоэкзотермического состава Mo/Nb/Si/B в смеси (α) и перегрузки (a) на содержание целевых (Nb, Si и B) и примесных (Al и O) элементов в литых КМ. Содержание базового элемента (Mo) на рис. 2 и 3 не приводится, определяется как остальное.
Рис. 2.
Влияние соотношения составов 1 и 2 (α) в смеси на химический состав литых КМ, a = 40g: a – базовые элементы, б – примесные элементы.

В первой серии экспериментов с увеличением α от 0 до 40 мас. % содержание молибдена, ниобия и бора в литых КМ практически не изменяется и составляет для Mo ~ 90, Nb 3.5, B ~ 1.0 мас. %. Содержание Si уменьшается, а примесей Al и O возрастает (рис. 2). Для второй серии экспериментов была выбрана смесь с α = 20 мас. %. Показано, что увеличение a от 40g до 400g слабо влияет на содержание целевых и примесных элементов в литых КМ (рис. 3). По данным рентгенофазового анализа, все образцы, полученные при α = = 20 мас. % и a от 40g до 400g, содержат три фазы: твердый раствор на основе Mo, фазу с решеткой Mo3Si и фазу с решеткой Mo5SiB2 (рис. 4). Расчетное соотношение (мас. %) элементов в фазе Mo3Si составляет 91.1/8.9, а в Mo5SiB2 – 90.6/5.3/4.1.
Микроструктура и состав структурных составляющих литых КМ. На микрофотографиях шлифов можно выделить три структурных составляющих, отличающихся как по цветовому контрасту, так и по составу: светлая основа (1), разделенная на крупные блоки границами; границы, на которых чередуются светло-серые участки (2), и темно-серые участки (3) (рис. 5). Элементный состав структурных составляющих приведен в табл. 2 и 3. Из сопоставления микроструктуры, состава структурных составляющих и результатов рентгенофазового анализа литых КМ следует, что светлая основа (1) сформирована из раствора ниобия, кремния и алюминия в молибдене, светло-серая фаза (2) сформирована из раствора ниобия и алюминия в Mo3Si, темно-серая фаза сформирована из раствора ниобия и алюминия в Mo5SiB2 (табл. 2 и 3).
Таблица 3.
Состав структурных составляющих литого КМ, a = 400g
Фаза | C, мас. % | Фазовый состав | |||
---|---|---|---|---|---|
Nb | Si | B | Al | ||
Светлая | 0.3–0.6 | 0.7 | – | 0.9 –1.0 | Tв. р-р на основе Mo |
Серая | 1.0–1.1 | 8.9 | – | 1.0 –1.2 | (Mo,Nb, Al)3Si |
Темная | 3.7 | 5.3 | 4.1 | 0.3–0.4 | (Mo, Nb, Al)5SiB2 |
Примечание. Остальное – Mo. |
Обсуждение результатов. Проведенные исследования выявили следующую последовательность процессов, протекающих после воспламенения смеси высокоэкзотермического (MoO3/Nb2O5/Al/ Si/B) и низкоэкзотермического (Mo/Nb/Si/B) составов. Формируется фронт горения, который распространяется по смеси. Во фронте горения протекает химическое превращение смеси в конечные продукты. Высокая температура горения смеси приводит к плавлению исходных реагентов и продуктов горения.
Анализ процессов, протекающих на стадии горения, с учетом представлений, полученных при моделировании горения систем термитного типа, позволяет представить следующую модель горения смеси (MoO3/Nb2O5/Al/Si/B) + (Mo/Nb/Si/B). Согласно термодинамическим расчeтам и полученным экспериментальным результатам, в достаточно широком интервале соотношений MoO3/Nb2O5/ Al/Si/B и Mo/Nb/Si/B температура горения превышает 3000 К. В этом случае в зоне прогрева волны горения компоненты смеси претерпевают следующие превращения:
– плавление MoO3 при 1070 К и последующее кипение (без разложения) при 1480 К;
– пары MoO3 движутся по исходной смеси в зону химического превращения;
– при температуре 2300 К после плавления защитной пленки (Al2O3) на поверхности частиц Al происходит воспламенение и последующее горение Al в парах MoO3;
– высокотемпературные продукты горения вступают в тепло- и массообмен с другими, “холодными”, компонентами смеси, между которыми после разогрева происходит химическое взаимодействие.
Схему превращений в реакционных ячейках можно представить в виде:
(1)
${\text{Mo}}{{{\text{O}}}_{3}} + 2{\text{Al}} \to {\text{Mo}} + {\text{A}}{{{\text{l}}}_{{\text{2}}}}{{{\text{O}}}_{3}},$(2)
${\text{Mo}} + x{\text{Nb}} + у{\text{Si}} + z{\text{B}} \to {\text{MoN}}{{{\text{b}}}_{x}}{\text{S}}{{{\text{i}}}_{y}}{{{\text{B}}}_{z}}.$После завершения химических превращений и теплообмена устанавливается тепловое и химическое равновесие (квазиравновесие) в расплаве конечных продуктов. Под действием гравитации происходит сепарация расплавов металлической и оксидной фаз продуктов горения. На завершающей стадии происходит охлаждение двухфазного расплава, формирование фазового состава, структуры литых КМ и шлакового слоя.
ЗАКЛЮЧЕНИЕ
Разработан метод центробежной СВС-металлургии, позволяющий получать литые КМ Mo/Nb/Si/B из смесей, включающих высокоэкзотермический (MoO3/Nb2O5/Al/Si/B) и низкоэкзотермический (Mo/Nb/Si/B) составы. Определены оптимальные составы смеси и величины перегрузки для проведения процесса с минимальными потерями при горении, высокой полнотой химического превращения и гравитационной сепарации, формированием литого Mo/Nb/Si/B. Литые КМ содержат три фазы: твердый раствор на основе Mo, Mo3Si и Mo5SiB2. Полученные результаты перспективны для создания новых жаростойких материалов.
Список литературы
Zhao J.C., Westbrook J.H. Ultrahigh-Temperature Materials for Jet Engines // MRS Bull. 2003. V. 28. № 9. P. 622–627. https://doi.org/10.1557/mrs2003.189
Drawin S., Justin J.F. Advanced Lightweight Silicide and Nitride Based Materials for Turbo-Engine Applications // AerospaceLab. 2011. P. 1–13.
Martinz H.P., Nigg B., Matej J., Sulik M., Larcher H., Hoffmann A. Properties of the Sibor® Oxidation Protective Coating on Refractory Metal Alloys // Int. J. Refract. Met. Hard Mater. 2006. V. 24. P. 283–291.
Drawin S., Heilmaier M., Jéhanno P., Hu D., Belaygue P., Tsakiropoulos P., Vilasi M. Creep and Oxidation Resistance of Refractory Silicide Based Materials // 17-th Plansee Seminar, Int. Conf. on High Performance PM Materials. Reutte: Plansee, 2009. V. 4. RM 33. P. 1–10.
Jéhanno P., Kestler H., Venskutonis A., Böning M., Heilmaier M., Bewlay B., Jackson M. Assessment of a Powder Metallurgical Processing Route for Refractory Metal Silicide Alloys // Metall. Mater. Trans. 2005. V. 36. № 3. P. 515–523. https://doi.org/10.1007/s11661-005-0165-5
Jéhanno P., Heilmaier M., Saage H., Böning M., Kestler H., Freudenberger J., Drawin S. Assessment of the High Temperature Deformation Behavior of Molybdenum Silicide Alloys // Mater. Sci. Eng. A. 2007. V. 463. № 1. P. 216–223. https://doi.org/10.1016/j.msea.2006.08.125
Jéhanno P., Heilmaier M., Saage H., Heyse H., Böning M., Kestler H., Schneibel J. Superplasticity of a Multiphase Refractory Mo–Si–B Alloy // Scr. Mater. 2006. V. 55. № 6. P. 525–528. https://doi.org/10.1016/j.scriptamat.2006.05.033
Byuna Jong Min, Bangb Su-Ryong, Kim Se Hoon, Choib Won June, Do Young. Mechanical properties of Mo–Nb–Si–B Quaternary Alloy Fabricated by Powder Metallurgical Method // Int. J. Refract. Met. Hard Mater. 2017. V. 65. P. 14–18. https://doi.org/10.1016/j.ijrmhm.2016.10.008
Yukhvid V.I., Andreev D.E., Sanin V.N., Gorshkov V.A., Alymov M.I. Synthesis of Cast Composite Materials by SHS Metallurgy Methods // Key Eng. Mater. 2017. V. 746. P. 219–232. https://doi.org/10.4028/www.scientific.net/KEM.746.219
Юхвид В.И., Алымов М.И., Санин В.Н., Андреев Д.Е., Сачкова Н.В. Синтез композиционных материалов на основе силицидов ниобия методами СВС-металлургии // Неорган. материалы. 2015. Т. 51. № 12. С. 1347–1354. https://doi.org/10.7868/S0002337X15110159
Shiryaev A. Thermodynamics of SHS Processes: An Advanced Approach // Int. J. SHS. 1995. V. 4. № 4. P. 351–362.
Дополнительные материалы отсутствуют.
Инструменты
Неорганические материалы