Неорганические материалы, 2020, T. 56, № 12, стр. 1285-1293
Десилицирование МАХ-фазы Ti3SiC2 в атмосфере CO и SiO
Е. И. Истомина 1, *, П. В. Истомин 1, А. В. Надуткин 1, В. Э. Грасс 1
1 Институт химии ФИЦ Коми НЦ УрО Российской академии наук
167982 Сыктывкар, Первомайская, 48, Россия
* E-mail: istomina-ei@yandex.ru
Поступила в редакцию 27.05.2020
После доработки 25.07.2020
Принята к публикации 29.07.2020
Аннотация
Исследовано десилицирование порошка МАХ-фазы Ti3SiC2 при 1600°С в газовой атмосфере CO + + xSiO (где x = 0, 1, 1.5, 2, 3). Для создания требуемой газовой атмосферы использовались гранулированные порошковые смеси, содержащие технический углерод, TiO2, SiO2 и SiC, которые при нагревании в результате протекания реакций восстановления оксидов выделяли газы CO и SiO. Установлено, что десилицирование Ti3SiC2 чувствительно к составу газовой фазы и протекает только тогда, когда соотношение CO : SiO превышает 1 : 3 (x < 3). Показано, что процесс десилицирования Ti3SiC2 является обратным процессу силицирования TiC газом SiO и описывается следующей химической реакцией: Ti3SiC2 + COгаз = 3TiC + SiOгаз.
ВВЕДЕНИЕ
Карбосилицид титана (Ti3SiC2) является одним из наиболее известных и детально изученных соединений семейства MAX-фаз. Накопленные на сегодняшний день экспериментальные данные, касающиеся синтеза, структуры и свойств Ti3SiC2, подробно изложены и систематизированы в ряде обзоров по данной тематике [1–5]. Главной особенностью Ti3SiC2, как и МАХ-фаз в целом, является слоистость кристаллической структуры и связанное с этим выраженное наноламинатное строение частиц. Благодаря слоистости материалы на основе Ti3SiC2 проявляют не типичный для керамики характер разрушения, который выражается в множественном расслаивании, изгибании и сминании наноламинатных частиц Ti3SiC2 под действием механических нагрузок. Такое поведение эффективно препятствует макроскопическому разрушению материала и обеспечивает керамике на основе Ti3SiC2 высокие прочностные характеристики, в частности, высокую трещиностойкость и нечувствительность к термоударам. Наряду с этим Ti3SiC2 проявляет термодинамическую стабильность по крайней мере до температуры 1600°С [6]. В целом, по комплексу прочностных и теплофизических свойств керамика на основе Ti3SiC2 хорошо подходит для работы в жестких условиях, предполагающих комбинированное действие высоких температур и ударных механических и термических воздействий.
Во многих технических приложениях в дополнение к указанным разрушающим факторам необходимо также учитывать действие агрессивных газовых сред. В этой связи необходимо иметь представление о химической устойчивости Ti3SiC2 в атмосфере различных газов при высоких температурах. В ряде исследований была изучена высокотемпературная химическая устойчивость Ti3SiC2 в кислороде [7], азоте [8], на воздухе [9–12], а также в атмосфере водяного пара [13–15], аргона [16, 17] и в условиях вакуума [18]. Еще одним технически важным газом, химическое воздействие которого на Ti3SiC2 необходимо изучить, является монооксид углерода (CO), поскольку этот газ в том или ином виде встречается в различных высокотемпературных процессах, таких как сжигание жидких и твердых топлив, карботермическая восстановительная переработка оксидного сырья, риформинг углеводородов и др.
В работе [18] высказано предположение, что газ CO может взаимодействовать с Ti3SiC2, приводя к образованию карбида титана (TiC) и удалению кремния из материала в виде газообразного монооксида кремния (SiO). По сути, была предложена реакция десилицирования Ti3SiC2, однако авторы не представили прямых экспериментальных доказательств возможности ее протекания. В работе [19] при изучении коррозии плотноспеченной керамики Ti3SiC2 в газовой атмосфере CO при температурах 1300–1500°С мы экспериментально подтвердили реакцию десилицирования. При этом осталось невыясненным влияние на данный процесс газа SiO, который является основным продуктом десилицирования.
Целью настоящей работы являлось исследование реакции десилицирования МАХ-фазы Ti3SiC2 в условиях газовой атмосферы, содержащей CO и SiO.
ЭКСПЕРИМЕНТАЛЬНАЯ ЧАСТЬ
В качестве исходных реагентов использовались порошки металлического титана марки ТПП-7 (содержание титана более 99%), технического карбида кремния (6H-политип, содержание SiC более 99%), диоксида титана TiO2 квалификации “ос. ч.”, оксида кремния SiO2 квалификации “ос. ч.”, технического углерод марки П-701 (содержание углерода в минеральной части более 99.5%); а также активированный уголь марки БАУ-А (содержание углерода в минеральной части более 99%) в виде крупки размером 1.6–2.5 мм. Порошок МАХ-фазы Ti3SiC2 получали по методике твердофазного синтеза, описанной в работе [20]. Вкратце, компактированную порошковую смесь, содержащую металлический титан, технический карбид кремния и активированный уголь в мольном отношении 3 : 1.3 : 0.7 спекали при 1420°С в течение 4 ч в условиях вакуума. Полученный в результате термообработки продукт измельчали путем перетирания в ступке до дисперсности менее 150 мкм. По данным рентгенофазового анализа (РФА), полученный образец Ti3SiC2 содержал 3 об. % TiC в качестве основной примеси.
Для создания газовой атмосферы CO + xSiO, где x = 0, 1, 1.5, 2 и 3, использовали гранулированные порошковые смеси, содержащие технический углерод, TiO2, SiO2 и SiC, которые при нагревании в результате протекания реакций восстановления оксидов выделяли газы CO и SiO. Исходные составы использованных в работе реакционных источников газа представлены в табл. 1 (эксперименты 2–6). Процедура приготовления гранул включала компактирование реакционных смесей с добавлением дистиллированной воды в качестве временной технологической связки, гранулирование методом перетирания через сито и далее сушку гранул при 100°С в течение нескольких часов. В экспериментах использовали гранулы размером 1.5–2.5 мм.
Таблица 1.
Исходные составы и полнота расходования (α) реакционных источников газовой атмосферы, наблюдаемые температуры начала газообразовательных реакций (tнач), относительное уменьшение массы (δm) и фазовый состав образцов Ti3SiC2 после термообработки
№ | Реакционный источник газовой смеси (CO + xSiO) | x | tнач, °C | α, % | δm, % | Фазовый состав, об. % | |
---|---|---|---|---|---|---|---|
TiC | Ti3SiC2 | ||||||
1 | − | – | – | − | 0.2 | − | 100 |
2 | 2SiO2 + SiC = 3SiOгаз + COгаз | 3 | 1450 | 98 | 0.8 | − | 100 |
3 | 3SiO2 + SiC + C = 4SiOгаз + 2COгаз | 2 | 1380 | 98 | 0.9 | 7 | 93 |
4 | 5SiO2 + SiC + 3C = 6SiOгаз + 4COгаз | 1.5 | 1330 | 90 | 1.6 | 20 | 80 |
5 | SiO2 + C = SiOгаз + COгаз | 1 | 1310 | 90 | 3.2 | 30 | 70 |
6 | TiO2 + 3C = TiC + 2COгаз | 0 | 1030 | 83 | 6.0 | 100 | − |
Эксперименты по десилицированию Ti3SiC2 в газовой атмосфере CO + xSiO, где x = 0, 1, 1.5, 2 и 3, проводились в собранном из стеклоуглеродных тиглей четырехсекционном реакторе, который помещали в рабочую камеру вакуумной печи СШВЭ-1-2.5/25. Схема реактора представлена на рис. 1. Три нижних секции реактора были последовательно соединены между собой газопроводящими каналами, а четвертая секция отделялась от третьей с помощью перфорированной графитовой перегородки. Гранулированный реакционный источник газа в количестве 5 г загружали в нижнюю секцию реактора. Во вторую секцию помещали порошок Ti3SiC2 в количестве 5 г. Две верхние секции реактора заполняли активированным углем марки БАУ-А так, чтобы суммарная масса угля составляла 6 г. Активированный уголь выполнял функцию химического поглотителя газа SiO. Его использование позволяло предотвратить выход газа SiO за пределы реактора и таким образом защитить печное оборудование от негативного воздействия SiO.
Рис. 1.
Схема реактора для проведения экспериментов по десилицированию Ti3SiC2 в газовой атмосфере CO + xSiO: 1 – газопроводящий канал, 2 – стеклоуглеродный тигель, 3 – перфорированная графитовая перегородка, 4 – реакционный источник газовой смеси CO + xSiO, 5 – образец Ti3SiC2, 6 – активированный уголь.
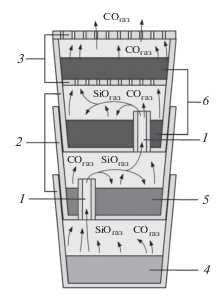
Термическую обработку образцов проводили в условиях непрерывной вакуумной откачки рабочей камеры вакуумной печи. На начальном этапе термообработки скорость нагрева составляла 2000°С/ч. В период стадии интенсивного газообразования скорость подъема температуры резко снижалась и далее регулировалась автоматически так, чтобы поддерживать давление газов в рабочей камере вакуумной печи в интервале 10–20 Па (режим стабилизации давления). Это обеспечивало равномерность выделения газов реакционными источниками газовой атмосферы в ходе термической обработки. При достижении 1600°С подъем температуры прекращался; продолжительность изотермической выдержки при 1600°С составляла 15 мин; затем следовало охлаждение со скоростью 4000°С/ч. Для оценки термической устойчивости Ti3SiC2 был проведен холостой эксперимент, в котором реакционный источник газовой атмосферы в реактор не загружался (эксперимент 1 в табл. 1). В этом случае режим термической обработки включал нагрев до 1600°С с постоянной скоростью 2000°С/ч, изотермическую выдержку в течение 15 мин и охлаждение со скоростью 4000°С/ч.
Для всех использованных в работе реакционных источников газовой атмосферы оценивали полноту расходования (α), которую рассчитывали по уменьшению массы после термообработки в соответствии с формулой
где ∆mэксп – наблюдаемое в эксперименте уменьшение массы реакционного источника газа после термообработки; ∆mтеор – уменьшение массы реакционного источника газа, достигаемое при условии, что соответствующая газообразовательная реакция прошла полностью (см. табл. 1).Фазовый состав продуктов термообработки исследовали методом порошковой рентгеновской дифрактометрии (РФА) на дифрактометре SHIMADZU XRD 6000 (CuKα-излучение, Ni-фильтр). Количественное содержание кристаллических фаз в образцах оценивали по рентгеновским данным методом Ритвельда с помощью программы PowderCell 2.4 [21]. Микроструктуру образцов изучали методом сканирующей электронной микроскопии (СЭМ) на микроскопе TESCAN VEGA 3SBU в режиме вторичных электронов. Локальный элементный состав образцов определялся методом рентгеноспектрального микроанализа (РСМА) с помощью энергодисперсионного микроанализатора X-ACT, совмещенного с электронным микроскопом.
РЕЗУЛЬТАТЫ И ОБСУЖДЕНИЕ
В экспериментах 2–6 (табл. 1) в ходе термической обработки наблюдалось интенсивное газообразование в области высоких температур, которое приводило к резкому росту давления в вакуумной камере. В качестве иллюстрации на рис. 2 представлены барограмма и термограмма эксперимента, в котором в качестве реакционного источника газа была использована гранулированная смесь состава 5SiO2 + SiC + 3C (эксперимент 4). В представленном на рис. 2 случае газообразование началось при ∼1330°С и продолжалось вплоть до достижения температуры изотермической выдержки. Общая продолжительность процессa газообразования составила около 40 мин, при этом полнота расходования реакционного источника газа, согласно данным по потере массы, составила 90%. В остальных случаях, за исключением холостого эксперимента (эксперимент 1), наблюдалась похожая динамика газообразования. Температуры начала газообразования, зафиксированные в экспериментах 2–6, а также полнота расходования использованных реакционных источников газовой атмосферы приведены в табл. 1.
Рис. 2.
Температурный режим (1) и барограмма (2) эксперимента, в котором в качестве источника газа была использована реакционная смесь 5SiO2 + SiC + + 3C (эксперимент 4).
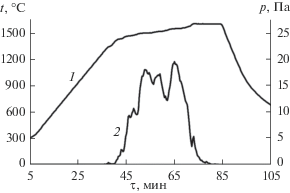
Во всех случаях, за исключением холостого эксперимента, в активированном угле, взятом после термического обработки из двух верхних секций реактора, обнаружено присутствие достаточно большого количества β-SiC. Типичная рентгенограмма образца активированного угля, содержащего β-SiC, представлена на рис. 3. Как показано ранее [22–24], образование β-SiC в активированном угле с определенностью указывает на присутствие в атмосфере газа SiO. Очевидно, что SiO, попадая через газоотводящие каналы в верхние секции реактора, взаимодействовал с активированным углем, образуя β-SiC и CO по реакции
(1)
$2{\text{C}} + {\text{Si}}{{{\text{O}}}_{{{\text{газ}}}}} = {\text{SiC}} + {\text{C}}{{{\text{O}}}_{{{\text{газ}}}}}.$Рис. 3.
Рентгенограмма активированного угля, взятого из двух верхних секций реактора после термической обработки.
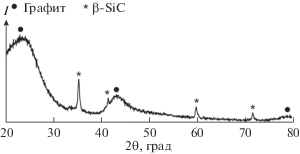
Важно отметить, что β-SiC обнаружен не только в тех экспериментах, где использовались твердотельные реакционные источники, генерирующие смесь газов CO + xSiO (эксперименты 2–5), но также и в эксперименте 6, где использовался реакционный источник, генерирующий только газ CO. Этот факт однозначно свидетельствует о том, что SiO являлся одним из продуктов взаимодействия Ti3SiC2 с газом CO.
Рентгенограммы образцов Ti3SiC2 после термической обработки в газовой атмосфере CO + + xSiO (где x = 0, 1, 2, 3) и в холостом эксперименте представлены на рис. 4. Фазовый состав полученных образцов, оцененный по данным РФА, приведен в табл. 1 вместе с данными по уменьшению массы образцов после термообработки. СЭМ-изображения и энергетические спектры характеристического рентгеновского излучения представительных участков полученных образцов показаны на рис. 5. Элементный состав этих участков, рассчитанный по данным РСМА, приведен в табл. 2.
Рис. 4.
Рентгенограммы порошка Ti3SiC2 после термообработки в различных газовых средах: а – холостой эксперимент (эксперимент 1), б – в атмосфере CO + 3SiO (эксперимент 2), в – в атмосфере CO + 2SiO (эксперимент 3), г – в атмосфере CO + SiO (эксперимент 5), д – в атмосфере CO (эксперимент 6).
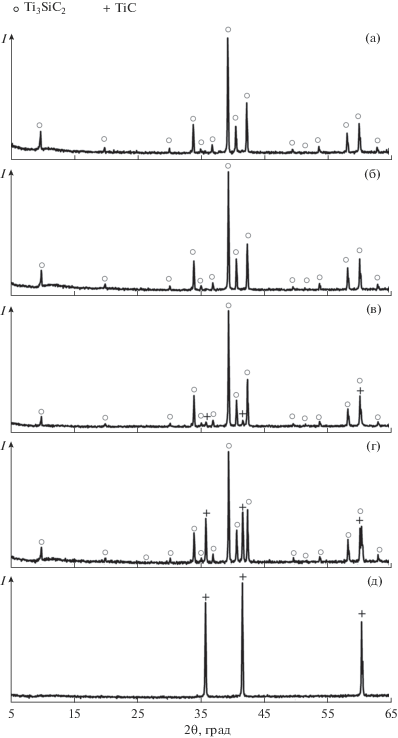
Рис. 5.
СЭМ-изображения и энергетические спектры характеристического рентгеновского излучения представительных участков образцов порошка Ti3SiC2 после термообработки в различных газовых средах: а – холостой эксперимент (эксперимент 1), б – в атмосфере CO + 3SiO (эксперимент 2), в – в атмосфере CO + SiO (эксперимент 5), г – в атмосфере CO (эксперимент 6).
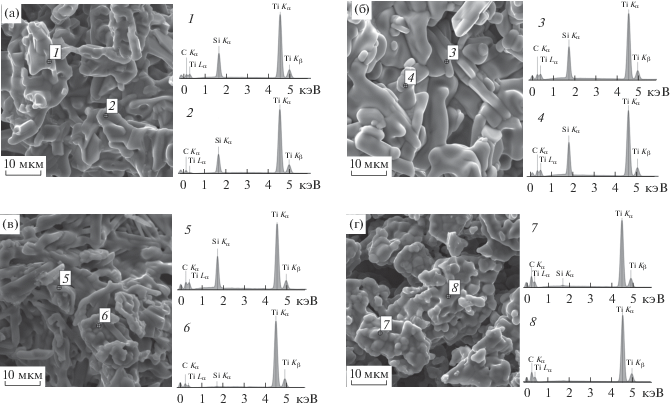
Таблица 2.
Элементный состав представительных участков образцов Ti3SiC2 после термической обработки в газовой атмосфере CO + xSiO и в холостом эксперименте по данным РСМА
Номер эксперимента | Номер участка | Элементный состав, ат. % | Идентифицированная фаза | ||
---|---|---|---|---|---|
C | Si | Ti | |||
1 | 1 | 41.8 | 12.9 | 45.3 | Ti3SiC2 |
2 | 35.6 | 11.8 | 52.6 | Ti3SiC2 | |
2 | 3 | 46.4 | 13.9 | 39.7 | Ti3SiC2 |
4 | 50.1 | 13.4 | 36.5 | Ti3SiC2 | |
5 | 5 | 53.9 | 12.0 | 34.1 | Ti3SiC2 |
6 | 56.4 | 0.7 | 42.9 | TiC | |
6 | 7 | 59.0 | 0.3 | 40.7 | TiC |
8 | 57.4 | – | 42.6 | TiC |
Данные РФА, СЭМ и РСМА по холостому эксперименту (эксперимент 1) показали, что по крайней мере до температуры 1600°С в условиях отсутствия сколько-нибудь значимой газовой атмосферы исследуемый образец Ti3SiC2 термически устойчив и сохраняет свою кристаллическую структуру. На соответствующей холостому эксперименту рентгенограмме (рис. 4а) присутствовали только пики, относящиеся к фазе Ti3SiC2. Микроструктура образца образована частицами преимущественно пластинчатой формы, что характерно для кристаллов Ti3SiC2 (рис. 5а). В спектрах характеристического рентгеновского излучения, снятых в представительных точках образца, присутствовали аналитические линии атомов титана, кремния и углерода, при этом элементный состав исследованных участков достаточно близко соответствовал фазе Ti3SiC2 (табл. 2, точки 1 и 2).
Похожие результаты были получены при термической обработке порошка Ti3SiC2 в газовой атмосфере состава CO + 3SiO (эксперимент 2), т.е. в условиях, когда концентрация SiO в газовой фазе существенно превышала концентрацию CO. В этом случае на рентгенограмме образца, так же как и в холостом эксперименте, отчетливо проявлялась только одна кристаллическая фаза – Ti3SiC2 (рис. 4б). Микроструктура образца представлена частицами характерной пластинчатой формы (рис. 5б), элементный состав которых близок к составу фазы Ti3SiC2 (табл. 2, точки 3 и 4). Основываясь на представленных результатах, можно констатировать отсутствие заметного химического взаимодействия между Ti3SiC2 и газовой средой, содержащей одновременно CO и SiO, в случаях, когда соотношение указанных газов не превышает 1 : 3.
При более высокой концентрации газа CO в атмосфере происходило десилицирование образцов, которое сопровождалось разрушением фазы Ti3SiC2 и одновременно с этим образованием TiC. Так, для образца Ti3SiC2, прошедшего термообработку в газовой атмосфере состава CO + 2SiO (эксперимент 3), содержание TiC в конечном продукте, согласно данным РФА, составило 7 об. %. Соответствующая рентгенограмма приведена на рис. 4в. При дальнейшем увеличении концентрации CO в газовой фазе доля TiC в продуктах термообработки росла, составив 20 об. % для газовой атмосферы состава CO + 1.5SiO (эксперимент 4) и 30 об. % для газовой атмосферы состава CO + SiO (эксперимент 5). В случае, когда газовая среда содержала только CO (эксперимент 6), фаза Ti3SiC2 в результате реакции десилицирования оказалась целиком трансформирована в TiC. На соответствующей этому случаю рентгенограмме пики Ti3SiC2 отсутствовали полностью (рис. 4д).
Микроструктурные особенности, связанные с десилицированием Ti3SiC2, показаны на рис. 5в на примере образца, прошедшего термообработку в газовой атмосфере состава CO + SiO (эксперимент 5). Видно, что микроструктура этого образца состоит из частиц двух типов, различающихся как по морфологии, так и по химическому составу. Частицы первого типа имели характерную пластинчатую форму, и, согласно данным РСМА, их элементный состав близко соответствовал фазе Ti3SiC2 (табл. 2, точка 5). Частицы второго типа имели изометричную форму, и их размер составлял в среднем 1–2 мкм. У этих частиц в спектрах характеристического рентгеновского излучения присутствовали аналитические линии атомов титана и углерода, при этом атомное отношение C/Ti составляло приблизительно 1.3 (табл. 2, точка 6). Аналитическая линия кремния в энергетических спектрах частиц второго типа была крайне слабой, а ее присутствие в спектрах, по-видимому, было связано с нахождением кремнийсодержащих объектов, а именно частиц Ti3SiC2, в непосредственной близости от анализируемого участка. Следует указать также на отсутствие в спектрах характеристического рентгеновского излучения частиц второго типа пика при 0.525 кэВ, соответствующего Kα-линии кислорода. Учитывая все вышеназванное, а также принимая во внимание, что метод РСМА, как правило, дает несколько завышенное содержание углерода в исследуемом материале, частицы второго типа можно с высокой степенью уверенности идентифицировать как TiC, т.е. как карбид титана состава, близкого к стехиометрическому. Оценочное содержание TiC в образце, исходя из приведенного СЭМ-изображения (рис. 5в), составляло 20–30 об. %, что хорошо согласуется с данными РФА (рис. 4г).
В случае, когда газовая атмосфера содержала только CO (эксперимент 6), микроструктура образца после термообработки представлена частицами только одного типа – TiC (рис. 5г), средний размер которых составлял 2–3 мкм. Отсутствие частиц Ti3SiC2 подтверждает сделанный ранее на основе данных РФА (рис. 4д) вывод о том, что в этом образце реакция десилицирования Ti3SiC2 прошла полностью.
Еще одной важной микроструктурной особенностью, связанной с десилицированием Ti3SiC2, являлось то, что частицы TiC имели тенденцию группироваться, образуя протяженные агломераты, которые по своей форме в целом повторяли пластинчатую форму кристаллов Ti3SiC2. Очевидно, что частицы TiC формировались непосредственно на месте частиц Ti3SiC2 в результате распада последних. Более того, они являлись единственным твердофазным продуктом десилицирования Ti3SiC2, поскольку, согласно данным РФА, никаких других кристаллических фаз, помимо Ti3SiC2 и TiC, в исследованных образцах не обнаружено. При этом прослеживалась прямая корреляция между содержанием TiC в продуктах десилицирования и уменьшением массы образцов после термообработки в газовой атмосфере CO + xSiO. Ясно, что уменьшение массы образцов было связано с образованием газа SiO, который, как уже было показано ранее, также являлся продуктом десилицирования Ti3SiC2.
Обобщая полученные результаты, можно предложить следующую химическую реакцию для описания процесса десилицирования Ti3SiC2 в газовой атмосфере CO + xSiO:
(2)
${\text{T}}{{{\text{i}}}_{{\text{3}}}}{\text{Si}}{{{\text{C}}}_{2}} + {\text{C}}{{{\text{O}}}_{{{\text{газ}}}}} = 3{\text{TiC}} + {\text{Si}}{{{\text{O}}}_{{{\text{газ}}}}}.$По сути, реакция (2) является обратной для реакции силицирования TiC газом SiO, которая уже была детально изучена в работах [25, 26]. Вместе две эти реакции описывают обратимый процесс силицирования–десилицирования, происходящий в карбидно-силицидной системе в условиях газовой атмосферы CO + xSiO. Очевидно, что, поскольку газовые компоненты принимали участие в реакции (2) как со стороны реагентов, так и со стороны продуктов, эта реакция была чувствительна к составу газовой атмосферы. С увеличением в газовой фазе концентрации SiO равновесие смещалось в сторону силицирования, т.е. в продуктах термической обработки присутствовала преимущественно фаза Ti3SiC2. Напротив, с увеличением концентрации CO равновесие смещалось в сторону десилицирования. В этом случае содержание Ti3SiC2 в продуктах обработки снижалось, а содержание TiС возрастало.
ЗАКЛЮЧЕНИЕ
Проведено исследование десилицирования порошка МАХ-фазы Ti3SiC2 при температуре 1600°С в газовой атмосфере, содержащей в различном соотношении газы SiO и CO. Дополнительно в результате проведения холостого эксперимента была подтверждена термическая и структурная устойчивость Ti3SiC2 при 1600°С в условиях отсутствия сколько-нибудь значимой газовой атмосферы.
Для создания газовой атмосферы CO + xSiO (где x = 0, 1, 1.5, 2, 3) в экспериментах по десилицированию Ti3SiC2 были использовали гранулированные порошковые смеси следующих составов: 2SiO2 + SiC, 3SiO2 + SiC + C, 5SiO2 + SiC + 3C, SiO2 + C, TiO2 + 3C, которые при нагревании в результате протекания реакций восстановления оксидов выделяли газы CO и SiO. Полученные результаты показали, что десилицирование Ti3SiC2 чувствительно к составу газовой фазы и происходит только в тех случаях, когда соотношение газов CO : SiO превышает 1 : 3 (x < 3). В результате десилицирования фаза Ti3SiC2 разрушалась, а непосредственно на месте частиц Ti3SiC2 формировались более мелкие частицы TiC. Газообразным продуктом десилицирования был SiO. Показано, что процесс десилицирования Ti3SiC2 является обратным изученному ранее процессу силицирования TiC газом SiO [25, 26] и описывается реакцией (2).
Список литературы
Barsoum M.W. The Mn+ 1AXn Phases: a New Class of Solids; Thermodynamically Stable Nanolaminates // Prog. Solid State Chem. 2000. V. 28. № 1–4. P. 201–281. https://doi.org/10.1016/S0079-6786(00)00006-6
Sun Z. Progress in Research and Development on MAX Phases: a Family of Layered Ternary Compounds // Int. Mater. Rev. 2011. V. 56. № 3. P. 143–166. https://doi.org/10.1179/1743280410Y.0000000001
Barsoum M.W., Radovic M. Elastic and Mechanical Properties of the MAX Phases // Annu. Rev. Mater. Res. 2011. V. 41. P. 195–227. https://doi.org/10.1146/annurev-matsci-062910-100448
Zhang H., Bao Y., Zhou Y. Current Status in Layered Ternary Carbide Ti3SiC2, a Review // J. Mater. Sci. Technol. 2009. V. 25. № 1. P. 1–38.
Barsoum M.W. MAX Phases: Properties of Machinable Carbides and Nitrites. Weinheim: Wiley-VCH-Verl, 2013. 437 p.
Istomin P., Istomina E., Nadutkin A., Leonov A., Kaplan M., Presniakov M. Fabrication of Ti3SiC2 and Ti4SiC3 MAX Phase Ceramics Through Reduction of TiO2 with SiC // Ceram. Int. 2017. V. 43. P. 16128–16135. https://doi.org/10.1016/j.ceramint.2017.08.180
Racault C., Langlais F., Naslain R. Solid-state Synthesis and Characterization of the Ternary Phase Ti3SiC2 // J. Mater. Sci. 1994. V. 29. P. 3384–3392.
Zhang H., Zhou Y., Bao Y., Li M. Titanium Silicon Carbide Pest Induced by Nitridation // J. Am. Ceram. Soc. 2008. V. 91. P. 494–499. https://doi.org/10.1111/j.1551-2916.2007.02018.x
Barsoum M.W., El-Raghy T. Oxidation of Ti3SiC2 in Air // J. Electrochem. Soc. 1997. V. 144. P. 2508–2516.
Sun Z., Zhou Y., Li M. High Temperature Oxidation Behavior of Ti3SiC2-Based Material in Air// Acta Mater. 2001. V. 49. P. 4347–4353. https://doi.org/10.1016/S1359-6454(01)00247-6
Zhang H., Zhou Y., Bao Y., Wang J. Oxidation Behavior of Bulk Ti3SiC2 at Intermediate Temperatures in Dry Air// J. Mater. Res. 2006. V. 21. P. 402–408. https://doi.org/10.1557/jmr.2006.0046
Zhang H., Shen S., Liu X., Wang Z., Jiang Y., He Y. Oxidation Behavior of Porous Ti3SiC2 Prepared by Reactive Synthesis // Trans. Nonferrous Met. Soc. China. 2018. V. 28. P. 1774–1783. https://doi.org/10.1016/S1003-6326(18)64821-6
Zhang H., Presser V., Berthold C., Nickel K.G., Wang X., Raisch C., Chassé T., He L., Zhou Y. Mechanisms and Kinetics of the Hydrothermal Oxidation of Bulk Titanium Silicon Carbide // J. Am. Ceram. Soc. 2010. V. 93 P. 1148–1155. https://doi.org/10.1111/j.1551-2916.2009.03570.x
Ward J., Bowden D., Prestat E., Holdsworth S., Stewart D., Barsoum M.W., Preuss M., Frankel P. Corrosion Performance of Ti3SiC2, Ti3AlC2, Ti2AlC and Cr2AlC MAX Phases in Simulated Primary Water Conditions // Corros. Sci. 2018. V. 139. P. 444–453. https://doi.org/10.1016/j.corsci.2018.04.034
Jung Y.-I., Park D.-J., Park J.-H., Park J.-Y., Kim H.-G., Koo Y.-H. Effect of TiSi2/Ti3SiC2 Matrix Phases in a Reaction-bonded SiC on Mechanical and High-temperature Oxidation Properties // J. Eur. Ceram. Soc. 2016. V. 36. P. 1343–1348. https://doi.org/10.1016/j.jeurceramsoc.2016.01.015
Radhakrishnan R., Williams J., Akinc M. Synthesis and High-temperature Stability of Ti3SiC2 // J. Alloys. Compd. 1999. V. 285. P. 85–88.
Nguyen T.D., Park S.-W., Lee D.-B. Corrosion of Ti3SiC2 in an Ar–1% SO2 Atmosphere between 800 and 1100°C// J. Ceram. Proc. Res. 2009. V. 10. P. 355–358.
Low I.M., Oo Z., Prince K.E. Effect of Vacuum Annealing on the Phase Stability of Ti3SiC2 // J. Am. Ceram. Soc. 2007. V. 90. P. 2610–2614. https://doi.org/10.1111/j.1551-2916.2007.01817.x
Istomin P., Istomina E., Nadutkin A., Grass V. Corrosion of Ti3SiC2 Ceramics in a High-temperature CO Environment // Mater. Lett. 2020. V. 259. P. 126763. https://doi.org/10.1016/j.matlet.2019.126763
Истомин П.В., Надуткин А.В., Рябков Ю.И., Голдин Б.А. Получение Тi3SiС2 // Неорган. материалы. 2006. Т. 42. № 3. С. 292–297.
Kraus W., Nolze G. Powder Cell – a Program for the Representation and Manipulation of Crystal Structures and Calculation of the X-ray Powder Patterns// J. Appl. Crystallogr. 1996. V. 29. P. 301. https://doi.org/10.1107/S0021889895014920
Истомина Е.И., Истомин П.В., Надуткин А.В. Получение биоморфного SiC // Неорган. материалы. 2013. Т. 49. № 10. С. 1060. https://doi.org/10.7868/S0002337X13090078
Istomin P., Istomina E., Nadutkin A., Grass V., Presniakov M. Synthesis of a Bulk Ti4SiC3 MAX Phase by Reduction of TiO2 with SiC// Inorg. Chem. 2016. V. 55. P. 11050–11056. https://doi.org/10.1021/acs.inorgchem.6b01601
Истомина Е.И., Истомин П.В., Надуткин А.В., Грасс В.Э., Богданова А.С. Оптимизация карбосиликотермического синтеза МАХ-фазы Ti4SiC3 // Неорган. материалы. 2018. Т. 54. № 6. С. 554–563. https://doi.org/10.7868/S0002337X18060027
Istomin P., Istomina E., Nadutkin A., Grass V. Effect of Silicidation Pretreatment with Gaseous SiO on Sinterability of TiC Powders // Int. J. Refract. Met. Hard Mater. 2016. V. 57. P. 12–18. https://doi.org/10.1016/j.ijrmhm.2016.02.004
Истомина Е.И., Истомин П.В., Надуткин А.В. Силицирование карбидов титана парами SiO // Журн. неорган. химии. 2012. Т. 57. № 8. С. 1134.
Дополнительные материалы отсутствуют.
Инструменты
Неорганические материалы