Неорганические материалы, 2020, T. 56, № 4, стр. 371-377
Влияние прекурсора на получение и текстурные свойства мезопористых порошков γ-Al2O3
Л. В. Морозова 1, *, Т. В. Хамова 1, И. Г. Полякова 1
1 Институт химии силикатов им. И.В. Гребенщикова Российской академии наук
199034 Санкт-Петербург, наб. Макарова, 2, Россия
* E-mail: morozova_l_v@mail.ru
Поступила в редакцию 20.06.2019
После доработки 07.09.2019
Принята к публикации 17.09.2019
Аннотация
Исследованы процессы формирования нанокристаллического γ-Al2О3 из различных прекурсоров (гидроксида алюминия, изопропилатa алюминия, нитрата алюминия). Синтезированы мезопористые порошки γ-Al2О3 при температурах 500 и 600°С. Методами низкотемпературной адсорбции азота и рентгенофазового анализа исследованы текстурные свойства порошков (площадь удельной поверхности, средний размер кристаллитов, объем и форма пор, распределение пор по размерам). Установлено влияние прекурсора на текстурные свойства γ-Al2О3. Показана возможность получения γ-Al2О3 с мономодальным распределением пор по размерам (2.5–4.5 и 4.5–8.0 нм в зависимости от прекурсора) и объемом пор ~0.550 см3/г. На основании полученных экспериментальных результатов можно констатировать, что полученные порошки γ-Al2О3 по текстурным характеристикам как носители катализаторов не уступают зарубежным аналогам.
ВВЕДЕНИЕ
Стратегия развития российских нефтеперерабатывающих предприятий направлена на политику импортозамещения, в частности на замену дорогостоящих импортных катализаторов продукцией отечественного производства. На сегодняшний день актуальны исследования в области создания каталитических систем для каталитического риформинга, который является основным процессом нефтепереработки при получении высококачественных бензинов и легких ароматических углеводородов [1, 2].
Катализаторы риформинга – это сложные системы, состоящие из активного вещества (металлы Pt, Re) и носителя, который является базовым компонентом всей каталитической системы. Важным критерием при выборе материала для носителя катализатора является возможность сформировать в нем пористую структуру с заданными параметрами (площадь удельной поверхности >100 м2/г, наличие мезопор, объем которых более 0.30 см3/г, и мономодальное распределение пор по размерам), которая будет оказывать существенное влияние на дисперсность и распределение активного вещества на поверхности и в объеме носителя. Наиболее часто в качестве носителя катализатора для процесса риформинга нефтепродуктов используют нанодисперсный мезопористый γ-Al2O3 [3–5]. Поскольку условия существования и текстурные свойства метастабильных структур оксида алюминия закладываются в процессе синтеза, разработка эффективных методик получения γ-Al2O3 с регулируемой мезопористой структурой (размер пор 2–50 нм) является актуальной задачей [6, 7].
В настоящее время современные технологические разработки делают акцент на использование низкотемпературных (200–800°С) методов синтеза порошков в наноразмерном диапазоне частиц (~10–30 нм). Для получения нанокристаллического γ-Al2O3 часто используют метод химического осаждения гидроксида алюминия, из которого при термическом разложении образуется γ-Al2O3 [7, 8]; метод жидкофазного гидролиза солей и алкоголятов алюминия с последующей термообработкой прекурсоров [9]; а также гидротермальный синтез [10, 11]. Первый и второй методы синтеза не требуют дорогостоящего оборудования, высоких энергетических затрат и позволяют получать конечный продукт в достаточно больших количествах. Метод гидротермального синтеза достаточно эффективен при получении различных модификаций оксида алюминия в высокодисперсном состоянии, но для его осуществления необходимо сложное печное оборудование, а количество синтезируемого вещества незначительно.
Цель работы – исследование влияния прекурсоров оксида алюминия на синтез и текстурные свойства порошков γ-Al2O3.
ЭКСПЕРИМЕНТАЛЬНАЯ ЧАСТЬ
Методы исследования. Седиментационный анализ (лазерный анализатор Horiba LB-550) применяли для измерения размеров агломератов частиц в порошках (D). Погрешность измерения D составляла от 10 до 30 нм в зависимости от дисперсности порошков.
Рентгенофазовый анализ (РФА, дифрактометр ДРОН-3, CuKα-излучение) использовали для определения кристаллической структуры порошков. Расшифровку дифрактограмм осуществляли с помощью международной базы данных PDF-2. По формуле Селякова–Шеррера рассчитан средний размер кристаллитов [12, 13]. При расчете величины погрешности размеров кристаллитов учитывалась точность юстировки дифрактометра, точность определения интенсивности и полуширины дифракционных линий. Погрешность вычисления составляла ±1.5–3.0 нм в зависимости от величины среднего размера кристаллитов.
Метод электронной микроскопии (электронный микроскоп ЭМ-125 с Uуск = 75 кВ) использовали для исследования степени агломерации прекурсоров. Исследуемые порошки перед просмотром фиксировали на опорной сетке с помощью коллоидной пленки.
Метод низкотемпературной адсорбции азота (анализаторы сорбции газа Quanta Chrome Nova 1200В и QuantaChrome Nova 4200е) применяли для исследования текстурных свойств порошков. Перед измерениями образцы дегазировали в сушильном отделении при 40°C в течение 5 ч. На основании полученных данных была рассчитана площадь удельной поверхности (Sуд) образцов с использованием многоточечного метода БЭТ. Относительная погрешность определения Sуд составляла 4%. Удельный объем пор определяли по предельному заполнению (р/р0 = 0.99), относительная погрешность при этом составляла 6%. Расчет порометрического объема и распределения пор по размерам в порошках осуществляли по десорбционной ветви изотермы по методу Баррета–Джойнера–Халенды (BJH). Тип поровой структуры и форма пор порошков были определены путем анализа вида полученных для них изотерм адсорбции–десорбции и формы петель капиллярно-конденсационного гистерезиса согласно международной классификации ИЮПАК [14].
Термогравиметрический анализ (ТГА, дериватограф Q-1000 фирмы МОМ) проводили в политермическом режиме (нагрев на воздухе до 900°С со скоростью 10°C/мин) для изучения процессов термолиза порошков-прекурсоров.
Термическую обработку для получения порошков с заданной кристаллической структурой выполняли на воздухе в интервале температур 100–800°C (электрическая печь фирмы Naberterm).
Синтез прекурсоров оксида алюминия. В качестве прекурсоров для синтеза порошков γ-Al2O3 были выбраны гидроксид алюминия (Al(OH)3), изопропилат алюминия (Al[(CH3)2CHO]3) и азотнокислый алюминий (Al(NO3)3 ∙ 6H2O), которые готовили следующим образом:
1. Гидроксид алюминия – Al(OH)3. Из соли Al(NO3)3 ∙ 9H2O (квалификация “ч. д. а.”) был приготовлен разбавленный раствор азотнокислого алюминия с концентрацией 0.1 М, из которого путем вливания раствора NH4OH (~1 М) со скоростью 1–2 мл/мин осуществляли осаждение гидроксида алюминия. Значение pH в реакционном сосуде поддерживалось на уровне 9.0–9.5 с помощью раствора NH4Cl, чтобы избежать растворения уже образовавшегося Al(OH)3. Процесс осаждения проводили при температуре 0–2°С для уменьшения степени агломерации осаждаемого гидроксида. Гелеобразный осадок, полученный после вакуумной фильтрации, высушивали при 100оС и получали Al(OH)3, который был идентифицирован методом РФА.
2. Изопропилат алюминия – Al[(CH3)2CHO]3. Жидкофазный гидролиз изопропилата алюминия (“ч. д. а.”) проводили на установке, состоявшей из стеклянного сосуда, снабженного механической мешалкой, и системы обогрева. Al[(CH3)2CHO]3 загружали в реактор и разогревали его до температуры 100–110°С, затем при интенсивном перемешивании добавляли раствор изопропилового спирта в Н2Одист с концентрацией 50 мас. %. Выделившуюся твердую фазу сушили при 120°С.
3. Нитрат алюминия – Al(NO3)3 · 6H2O. Готовили насыщенный раствор нитрата алюминия из Al(NO3)3 ∙ 9H2O (“ч. д. а.”) с учетом предельной растворимости данной соли в 100 г дистиллированной воды при 60°С [15], который нагревали на водяной бане при 100°С в течение ~1.5 ч до достижения гелеобразной консистенции раствора. Полученный гидрогель охлаждали при 0–2°С (на льду), в результате чего происходило образование кристаллогидрата Al(NO3) ∙ nH2O, который затем термообрабатывали при 75°С, что способствовало его частичной дегидратации и получению A1(NО3)3 ∙ 6Н2О [9, 15]. Перекристаллизация нитрата алюминия является наиболее простым методом очистки 6-водного нитрата алюминия, что экспериментально установлено автором работы [9].
РЕЗУЛЬТАТЫ И ОБСУЖДЕНИЕ
Методом электронной микроскопии проведена оценка размеров агломератов частиц в полученных прекурсорах. Установлено, что агломераты в Al(OH)3, Al[(CH3)2CHO]3 и A1(NО3)3 ∙ 6Н2О имеют размер от 0.3 до 2 мкм. Для снижения степени агломерации свежеприготовленные прекурсоры были подвергнуты ультразвуковой (УЗ) обработке в течение 30 мин (УЗ-ванна “Сапфир”, частота 35 кГц) в дистиллированной воде [16]. При увеличении времени воздействия ультразвука на прекурсоры до 45 мин зафиксировано очень незначительное уменьшение степени их агломерации по сравнению с 30-минутной УЗ-обработкой, поэтому в данном случае 30 мин – оптимальное время УЗ-воздействия на прекурсоры.
Дисперсность порошков–прекурсоров Al2O3 после УЗ-обработки определяли методом седиментационного анализа (рис. 1). Для Al(OH)3 характерно достаточно узкое мономодальное распределение агломерированных частиц по размерам (60–130 нм), тогда как в Al[(CH3)2CHO]3 зафиксировано бимодальное распределение агломератов (50–140 и 140–260 нм). В A1(NО3)3 ∙ 6Н2О так же как и в гидроксиде алюминия, установлено мономодальное распределение агломерированных частиц по размерам (100–230 нм), но более широкое, чем в Al(OH)3. Различие в дисперсности прекурсоров, вероятно, связано с количественным содержанием в них водного компонента, что согласуется с результатами исследования термического разложения Al(OH)3, Al[(CH3)2CHO]3 и A1(NО3)3 ∙ 6Н2О методом ТГА (рис. 2). На кривой ТГА гидроксида алюминия (рис. 2а) фиксируется меньшая потеря массы образца, чем в случае изопропилата алюминия и нитрата алюминия, а эндотермический эффект на кривой ДТА Al(OH)3, соответствующий процессу дегидратации (удаление адсорбционной и химически связанной Н2О), менее глубокий, чем для Al[(CH3)2CHO]3 и A1(NО3)3 ∙ 6Н2О (рис. 2б, 2в). На кривой ДТА на рис. 2в не регистрируется экзотермический эффект, соответствующий выделению оксидов азота при разложении нитрата алюминия, поскольку процессы дегидратации и разложения A1(NО3)3 ∙ · 6Н2О протекают одновременно в интервале температур 100–320°С [15]. Экзотермические эффекты на кривых ДТА (450, 590 и 475°С) соответствуют процессу кристаллизации γ-Al2O3. Следует отметить, что при нагревании изопропилата алюминия на кривой ДТА (рис. 2б) при температуре 535°С первоначально фиксируется экзотермический эффект, характеризующий выделение оксидов углерода (СО и СО2) в результате термического разложения Al[(CH3)2CHO]3 [17], что вызывает дополнительное диспергирование γ-Al2O3, который образуется при температуре 590°С.
Рис. 1.
Распределение агломерированных частиц по размерам в прекурсорах оксида алюминия после УЗ-обработки: а – Al(OH)3, б – Al[(CH3)2CHO]3, в – Al(NO3)3 ∙ 6H2O.
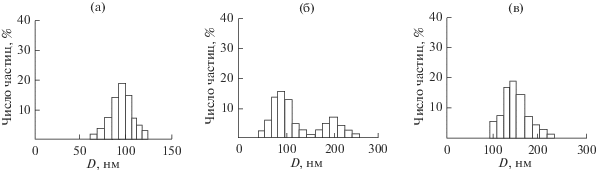
Рис. 2.
Результаты термического анализа прекурсоров оксида алюминия: а – Al(OH)3, б – Al[(CH3)2CHO]3, в – Al(NO3)3 ∙ 6H2O.
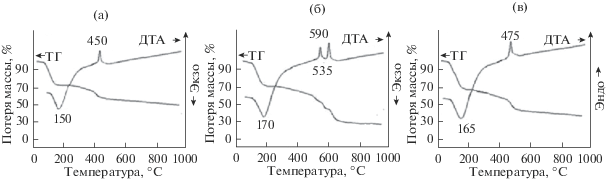
По данным РФА, на дифрактограммах порошков, полученных из различных прекурсоров оксида алюминия, регистрируется одинаковая совокупность максимумов, соответствующих γ-Al2O3 (рис. 3). Температуры образования γ-Al2O3 из Al(OH)3, Al[(CH3)2CHO]3 и Al(NO3)3 ∙ 6H2O приведены в табл. 1. Средний размер кристаллитов порошков γ-Al2O3 не превышает 9 нм (см. табл. 2).
Таблица 1.
Параметры элементарной ячейки γ-Al2O3, синтезированного из различных прекурсоров
Прекурсор | Температура образования γ-Al2O3, °C | d400, Å | а, Å | V, Å3 |
---|---|---|---|---|
Al(OH)3 | 450 | 1.9791 | 7.9164 | 496.1 |
Al[(CH3)2CHO]3 | 590 | 1.9785 | 7.9140 | 495.7 |
A1(NО3)3 ∙ 6Н2О | 475 | 1.9793 | 7.9192 | 496.3 |
Таблица 2.
Текстурные свойства порошков γ-Al2O3, полученных из различных прекурсоров
Прекурсор | Температура обжига прекурсора*, °С | Площадь удельной поверхности, м2/г | Средний размер кристаллитов, нм | Объем пор, см3/г | Размер пор, нм | Форма пор |
---|---|---|---|---|---|---|
Al(OH)3 | 500 | 302 | 7.5 | 0.568 | 2.5–4.5 | Щелевидные |
Al[(CH3)2CHO]3 | 600 | 284 | 7.5 | 0.532 | 4.5–8.0 | Цилиндрические |
Al(NO3)3 ∙ 6Н2О | 500 | 201 | 9 | 0.432 | 7.0–9.8 9.8–32.5 |
Бутылкообразные |
* Температура обжига выбрана с учетом результатов ДТА (рис. 2).
Параметр элементарной ячейки а синтезированных порошков γ-Al2O3 вычисляли по наиболее интенсивному дифракционному максимуму 400 и соответствующему значению межплоскостного расстояния d400 (табл. 1). Значения а и d для всех порошков γ-Al2O3 соответствуют данным, приведенным в базе PDF-2.
Текстурные свойства синтезированных порошков оценивали с помощью метода низкотемпературной адсорбции азота, проведен сравнительный анализ изотерм адсорбции–десорбции γ-Al2O3, а также распределения пор по размерам. О характере пористой структуры γ-Al2O3, синтезированного из прекурсоров Al(OH)3, Al[(CH3)2CHO]3 и A1(NО3)3 ∙ 6Н2О, можно судить по типу петли гистерезиса на изотермах низкотемпературной адсорбции–десорбции азота, представленных на рис. 4. Форма изотерм для всех порошков γ-Al2O3 соответствует IV типу (по классификации ИЮПАК) – изотермы с четко выраженной капиллярной конденсацией, что характерно для мезопористых материалов с размером пор от 2 до 50 нм [18]. Взаимосвязь профиля гистерезиса и вида пористой структуры мезопористых веществ описана в работе [14] (рис. 5). Текстурные свойства порошков приведены в табл. 2.
Рис. 4.
Изотермы низкотемпературной адсорбции–десорбции азота порошков γ-Al2O3, полученных из различных прекурсоров: а – Al(OH)3, б – Al[(CH3)2CHO]3, в – Al(NO3)3 ∙ 6H2O.
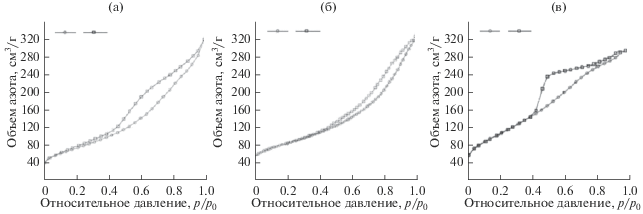
Порошок γ-Al2O3, полученный из гидроксида алюминия, обладает площадью удельной поверхности 302 м2/г, объемом пор 0.568 см3/г. Профиль гистерезиса изотерм низкотемпературной адсорбции–десорбции азота для γ-Al2O3 (рис. 4а) совпадает с классическим типом Н3 (рис. 5), который соответствует наличию щелевидных пор, сформированных параллельными пластинчатыми кристаллитами оксида алюминия и открытых со всех сторон [18]. Пористая структура γ-Al2O3 характеризуется узким и мономодальным распределением пор по размерам с единственным узким максимумом в диапазоне 2.5–4.5 нм, что свидетельствует об однородности мезопор данного порошка (рис. 6а).
Рис. 6.
Кривые распределения пор по размерам в порошках γ-Al2O3, полученных из различных прекурсоров: а – Al(OH)3, б – Al[(CH3)2CHO]3, в – Al(NO3)3 ∙ 6H2O.
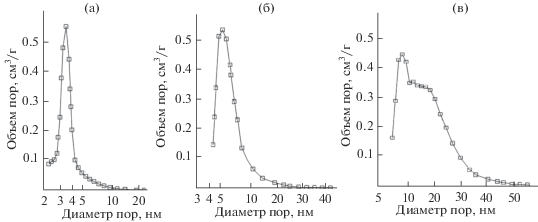
Из Al[(CH3)2CHO]3 также получен высокодисперсный мезопористый порошок γ-Al2O3 (Sуд = = 284 м2/г, Vпор = 0.532 см3/г), существенных отличий в величинах площади удельной поверхности, объема и размера пор по сравнению с γ-Al2O3, синтезированным из Al(OH)3, не наблюдается. Профиль петли гистерезиса на изотермах низкотемпературной адсорбции–десорбции азота (рис. 4б) эквивалентен цилиндрическим (или трубчатым) порам с открытыми концами (тип Н1) (рис. 5), при этом наблюдается достаточно узкое мономодальное распределение пор по размерам в диапазоне 4.5–8.0 нм (рис. 6б).
Для γ-Al2O3, синтезированного из нитрата алюминия, тип изотермы адсорбции–десорбции (рис. 4в) также соответствует мезопористому веществу. Наблюдаемое уширение петли гистерезиса в области средних и высоких относительных давлений (р/р0) указывает на образование пор большего диаметра по сравнению с предыдущими случаями. Профиль петли гистерезиса в данном случае согласуется с профилем, характерным для бутылкообразных пор (рис. 5) (тип Н2). Мезористая структура γ-Al2O3 характеризуется наличием двух совмещенных максимумов на кривой распределения пор по размерам (рис. 6в), что свидетельствует о бимодальном распределении (7.0–9.8 и 9.8–32.5 нм).
Мезопористый γ-Al2O3 с бутылкообразными порами не подходит для использования в качестве носителя катализатора из-за невозможности достижения равномерного распределения активной фазы в носителе, поскольку доступность таких пор для диффундирующих молекул катализатора будет затруднена. В связи с этим была предпринята попытка изменить размер и форму пор γ-Al2O3. Для этого синтезированный порошок подвергали УЗ-воздействию в течение 15 мин, а затем исследовали методом БЭТ (рис. 7). Зафиксирована трансформация петли гистерезиса на изотермах низкотемпературной адсорбции–десорбции азота от Н2 к Н1 (ср. рис. 7а и 4в), поэтому можно предположить, что происходит разрушение бутылкообразных пор в γ-Al2O3 и образование цилиндрических пор, при этом увеличивается площадь удельной поверхности (201 → 255 м2/г) и объем пор (0.432 → 0.510 см3/г), а распределение пор по размерам становится мономодальным, хотя и является достаточно широким (4–20 нм) (рис. 7б).
ЗАКЛЮЧЕНИЕ
Предложены способы жидкофазного синтеза нано-кристаллического γ-Al2O3 из различных прекурсоров (Al(OH)3), Al[(CH3)2CHO]3, Al(NO3)3 · · 6H2O), которые являются достаточно простыми и не требуют больших энергетических затрат. Установлено влияние природы прекурсора на размер и форму пор порошков γ-Al2O3. Получены мезопористые порошки γ-Al2O3 с площадью удельной поверхности 280–300 м2/г, объемом пор ~0.550 см3/г и узким распределением пор по размерам (2.5–4.5 и 4.5–8.0 нм). Наиболее высокими текстурными характеристиками обладает γ-Al2O3, синтезированный из гидроксида алюминия.
Полученные мезопористые порошки γ-Al2O3 можно рекомендовать в качестве носителей катализаторов для процесса риформинга нефтепродуктов, так как их мезопористая структура способна обеспечить тонкое диспергирование частиц металлов (Pt, Re), что замедлит процесс спекания активной фазы в процессе эксплуатации и будет способствовать повышению потенциальных возможностей каталитической системы в целом.
Список литературы
Колесников И.М. Катализ и производство катализаторов. М.: Техника, 2004. 400 с.
Алиев Р.Р. Катализаторы и процессы переработки нефти. М.: Химия, 2010.
Busca G. Structural, Surface, and Catalytic Properties of Aluminas // Adv. Catal. 2014. V. 57. P. 319–404. https://doi.org/10.1016/B978-0-12-800127-1.00003-5
Трегубенко В.Ю., Удрас И.Е., Белый А.С. Исследование закономерностей синтеза носителей катализатора риформинга // Кинетика и катализ. 2009. Т. 50. № 6. С. 914–915.
Трегубенко В.Ю., Удрас И.Е., Дроздов В.А., Белый А.С. Изучение влияния условий приготовления γ-оксида алюминия в качестве носителя катализаторов риформинга на его физико-химические свойства // Журн. физ. химии. 2009. Т. 83. № 12. С. 2238–2243.
Лыгин В.И. Изменение поверхности оксида алюминия в зависимости от фазового состава, термической обработки и адсорбции молекул // Журн. физ. химии. 2004. Т. 78. № 8. С. 1469–1474.
Волкова Г.И., Иванов В.Г., Кухаренко О.А. Влияние условий синтеза на структуру и свойства ультрадисперсных оксигидроксидов алюминия // Химия в интересах устойчивого развития. 2005. Т. 13. № 3. С. 427–432.
Чукин Г.Д. Строение оксида алюминия и катализаторов гидрообессеривания. Механизмы реакций. М.: Паладин, ООО “Принта”, 2010. 288 с.
Сударикова Е.Ю. Получение прекурсоров и синтез из них порошков высокочистого оксида алюминия: Автореф. дис. … канд. хим. наук. М., 2009. 22 с.
Альмяшева О.В., Корыткова Э.Н., Маслов А.В., Гусаров В.В. Получение нанокристаллов оксида алюминия в гидротермальных условиях // Неорган. материалы. 2005. Т. 41. № 5. С. 540–547.
Panda P.K., Jaleel V.A., Usha Devi S. Hydrothermal Synthesis of Boehmite and α-Alumina from Bayer’s Alumina Trihydrate // J. Mater. Sci. 2006. V. 42. № 24. P. 8386–8389.
Гусев А.И. Аттестация нанокристаллических материалов по размеру частиц (зерен) // Металлофизика и новейшие технологии. 2008. Т. 30. № 5. С. 679–694.
Ягодкин Ю.Д., Добаткин С.В. Применение электронной микроскопии и рентгеноструктурного анализа для определения размеров структурных элементов в нанокристаллических материалах (Обзор) // Завод. лаб. Диагностика материалов. 2007. Т. 73. № 1. С. 38–49.
Sing, K.S.W., Everett D.H., Haul R.A.W. Reporting Physisorption Data for Gas/Solid Systems with Special Reference to the Determination of Surface Area and Porosity // Pure Appl. Chem. 1985. V. 57. P. 603–619.
Химическая энциклопедия / Под ред. Кнунянца И.Л. М.: Сов. энциклопедия, 1988. Т. 1. С. 118.
Хасанов О.Л., Двилис Э.С., Полисадова В.В., Зыкова А.П. Эффекты мощного ультразвукового воздействия на структуру и свойства наноматериалов // Уч. пособие. Изд-во Томского политехнического ун-та, 2008. 149 с.
Гринберг Е.Е., Сырычко В.В., Стрельникова И.Е., Потелов В.В., Баранов К.В. Технологические вопросы получения высокочистых веществ для золь-гель и пиролитических методов синтеза // Физика и химия стекла. 2008. Т. 34. № 4. С. 668–673.
Gregg S.J., Sing K.S.W. Adsorption, Surface Area and Porosity. N.Y.: Academic Press, 1982. 310 p.
Дополнительные материалы отсутствуют.
Инструменты
Неорганические материалы