Неорганические материалы, 2020, T. 56, № 5, стр. 549-554
Влияние добавок ZrC и ZrO2 на микроструктуру и свойства керамики ZrB2–SiC
А. Ю. Гусев 1, В. Ф. Войцик 1, Е. С. Дедова 1, 2, *, С. П. Буякова 1, 2, 3
1 Институт физики прочности и материаловедения СО Российской академии наук
634055 Томск, пр. Академический, 2/4, Россия
2 Национальный исследовательский томский политехнический университет
634034 Томск, пр. Ленина, 30, Россия
3 Национальный исследовательский томский государственный университет
634034 Томск, пр. Ленина, 36, Россия
* E-mail: lsdedova@yandex.ru
Поступила в редакцию 11.03.2019
После доработки 11.10.2019
Принята к публикации 26.11.2019
Аннотация
Изучено влияние добавок ZrC и ZrO2 на микроструктуру и свойства керамических композитов на основе ZrB2–5% SiC, получаемых спеканием под давлением при температуре 1600°С механически активированных порошков. Показано, что добавка ZrO2 приводит к увеличению плотности, твердости и трещиностойкости керамических композитов на основе ZrB2–5% SiC. Так, например, KIс керамики ZrB2–5% SiC составил 4.6 ± 0.3 МПа м1/2, а композита с 20% ZrO2 – 7.3 ± 0.4 МПа м1/2.
ВВЕДЕНИЕ
Бориды циркония и гафния ZrB2 и HfB2 характеризуются высокой электро- и теплопроводностью, износостойкостью, химической инертностью, в том числе к расплавам металлов, что делает их привлекательными для использования в машинах и аппаратах, эксплуатируемых в условиях высоких температур, фрикционного контакта, контакта с металлическими расплавами [1–7]. Однако высокая ковалентность химической связи, низкие коэффициенты самодиффузии Zr, Hf и B наряду с высокой температурой плавления затрудняют спекаемость однофазных керамик ZrB2 и HfB2. Одним из решений по уплотнению керамик на основе диборидов циркония и гафния является введение других компонентов, т.е. получение композитных структур.
Кроме того, создание композитной структуры в керамиках на основе ZrB2 и HfB2 обеспечивает получение новых эксплуатационных характеристик. Так, например, композиты ZrB2–SiC существенно превосходят однофазную керамику ZrB2 по устойчивости в высокотемпературной кислородсодержащей атмосфере. Керамические композиты на основе ZrB2 и HfB2 с добавками MoSi2, SiC, TiC, ZrO2 обладают существенно большей трещиностойкостью в сравнении с однофазными керамиками [8–13].
С позиции практического использования в машиностроительных конструкциях, в пáрах трибосопряжения интерес представляют керамические композиты, содержащие ZrB2, ZrC, ZrO2, SiC. Исследования, посвященные изучению свойств такого рода керамических композитов, как правило, ограничены узким интервалом концентраций компонентов, что не позволяет провести полный анализ влияния количественного содержания компонентов на структуру и свойства композитов.
Целью данной работы является изучение влияния состава керамических композитов ZrB2–SiC–(ZrC/ZrO2) на их микроструктуру и свойства.
ЭКСПЕРИМЕНТАЛЬНАЯ ЧАСТЬ
Исследования проводились на керамических композитах на основе ZrB2–5% SiC с добавками ZrO2 и ZrC от 5 до 20 об. %. В качестве исходных компонентов для получения керамических композитов использованы промышленные порошки ZrB2, 6H-SiC, ZrC и ZrO2. Диоксид циркония был стабилизирован 3 мол. % Y2O3 и находился в тетрагональной модификации (t-ZrO2). Все порошки состояли из частиц нерегулярной формы. Средний размер частиц в порошке ZrB2 составил 〈d〉 = 1.65 мкм (〈d90〉 = 4.14 мкм), в порошке SiC – 〈d〉 = 2.2 мкм (〈d90〉 = 5.84 мкм), в порошке ZrC – 〈d〉 = 1.6 мкм (〈d90〉 = 3.3 мкм). Порошок ZrO2 имел наименьший средний размер частиц 〈d〉 = 0.35 мкм (〈d90〉 = 0.7 мкм).
Приготовление порошковых смесей с их одновременной активацией проводилось в планетарной мельнице-активаторе типа АГО в среде этанола в течение 3 мин при частоте вращения барабана 1820 об./мин. Образцы керамических композитов получали спеканием порошковых смесей при температуре 1600°С под давлением 30 МПа в течение 15 мин в атмосфере аргона.
Плотность композитов ZrB2–6H-SiC–ZrO2 и ZrB2–6H-SiC–ZrC определяли методом гидростатического взвешивания образцов с предварительным закрытием открытой пористости лаком. Теоретическую плотность композитов рассчитывали по правилу смеси.
Фазовый состав композитов анализировали с использованием рентгеновской дифракции на дифрактометре Shimadzu XRD 7000 c Сu Kα-излучением (λ = 1.5405 Å).
Твердость композитов определяли на полированной поверхности образцов индентированием пирамиды Виккерса с нагрузкой 98 Н в течение 10 с.
Трещиностойкость рассчитывали из суммарной длины трещин от индентора Виккерса по формуле KIc = 0.16HVa1/2${{\left( {\frac{c}{a}} \right)}^{{{{ - 3} \mathord{\left/ {\vphantom {{ - 3} 2}} \right. \kern-0em} 2}}}},$ где а – половина диагонали отпечатка, с – длина трещин [14].
Модуль упругости керамических композитов рассчитывали из скорости ультразвука в образцах посредством TDS 220, Tektronix (США) и 5800, Panametrics (Корея).
РЕЗУЛЬТАТЫ И ОБСУЖДЕНИЕ
На рис. 1 приведены рентгеновские дифрактограммы полученных керамических композитов. Согласно результатам анализа, фазовый состав композитов представлен исходными компонентами композитов: ZrB2, 6H-SiC, ZrO2 и ZrC. Диоксид циркония в композитах (об. %) 95ZrB2–5SiC–хZrO2 находился в модификации t-ZrO2.
Рис. 1.
Дифрактограммы композиционных материалов ZrB2–SiC–20 об. % ZrO2 (1) и ZrB2–SiC–20 об. % ZrC (2).
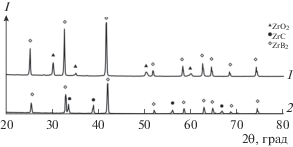
Параметры элементарных ячеек компонентов в исследуемых композитах близки к приведенным в картотеке JCPDS: для ZrB2 – а = 3.167 ± ± 0.002 Å, с = 3.531 ± 0.001 Å (а = 3.168 Å, с = 3.530 Å, JCPDS, карта № 34-0423), для ZrC – а = 4.695 ± ± 0.002 Å (а = 4.694 Å, JCPDS, карта № 65-0332), для t-ZrO2 – а = 3.625 ± 0.002 Å, с = 5.198 ± 0.001 Å (а = 3.629 Å, с = 5.197 Å, JCPDS, карта № 89-7710). По причине малой интенсивности дифракционных максимумов карбида кремния на рентгенограммах композитов расчет параметров его ячейки был проведен только в порошке: 6H-SiC – а = = 3.072 Å, с = 15.081 Å (а = 3.073 Å, с = 15.080 Å, JCPDS, карта № 29-1131).
На рис. 2 представлены зависимости относительной плотности ρотн керамических композитов ZrB2–SiC–ZrC от объемного содержания ZrC и композитов ZrB2–SiC–ZrO2 от объемного содержания ZrO2. Согласно полученным данным, относительная плотность образцов композитов ZrB2–SiC–ZrO2 возрастала пропорционально увеличению объемной доли диоксида циркония. Для керамики ZrB2–5 об. % SiC без добавки диоксида циркония ρотн составляла 0.85 ± 0.05, а при содержании 20 об. % ZrO2 ρотн = 0.96 ± 0.2. Экстраполяция зависимости ρотн от объемного содержания ZrO2 в композитах на беспористое состояние показала, что плотность композита ZrB2–SiC–ZrO2, полученного спеканием под давлением 30 МПа при температуре 1600°С в течение 15 мин, будет близка к его теоретической плотности при содержании в нем более 25 об. % ZrO2. Диоксид циркония – наиболее легкоплавкий компонент композитов ZrB2–SiC–ZrO2, увеличение его объемного содержания приводит к уменьшению температуры плавления смеси ZrB2–SiC–ZrO2 (увеличению гомологической температуры α = 1600°С/tпл) и, как следствие, увеличению плотности композитов.
Рис. 2.
Влияние добавки ZrO2 и ZrC на относительную плотность композитов ZrB2–SiC–ZrO2 (1) и ZrB2–SiC–ZrC (2).
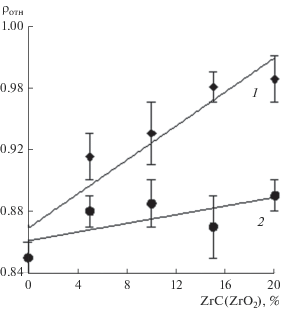
Относительная плотность образцов ZrB2–SiC–ZrC превышала таковую для образцов ZrB2–5% SiC, но весьма незначительно. Относительная плотность композитов с содержанием ZrC более 5% в среднем составляла 0.88 ± 0.05.
На рис. 3 представлена микроструктура композитов на основе ZrB2–SiC с разным содержанием ZrC и ZrO2. Увеличение объемной доли как ZrC, так и ZrO2 в композитах сопровождалось увеличением размеров зерен. Средний размер зерен измеряли методом случайных секущих по изображениям микроструктуры композитов [15]. Так, средний размер зерен в керамике ZrB2–SiC–5% ZrO2 составил 2.5 мкм, в композите с 15% ZrO2 – 4.2 мкм. В композите ZrB2–SiC–ZrC с наименьшим содержанием ZrC средний размер зерна составил 2.57 мкм, а при содержании 15% ZrC – 5.2 мкм.
Рис. 3.
Микроструктура композитов ZrB2–SiC–5% ZrO2 (а), ZrB2–SiC–15% ZrO2 (б), ZrB2–SiC–5% ZrC (в), ZrB2–SiC–15% ZrC (г).
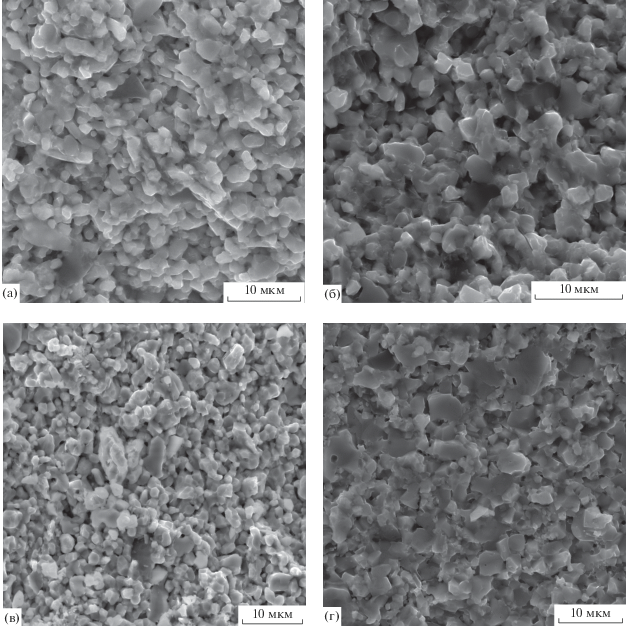
Величина модуля упругости Е, рассчитанная из скорости прохождения ультразвука, для керамики ZrB2–SiC составила 373 ± 25 ГПа. При этом модуль упругости композита ZrB2–SiC, рассчитанный по правилу аддитивности, был равен 458 ГПа. Разница в величинах модуля упругости, фиксируемого экспериментально и рассчитанного, главным образом связана с наличием в керамике ZrB2–SiC остаточной пористости.
Введение ZrC в керамическую матрицу из ZrB2–SiC не оказало значительного влияния на величину модуля упругости композитов (рис. 4). Для композитов ZrB2–SiC–ZrO2 величина модуля упругости возрастала с увеличением объемного содержания оксида циркония. Так, для композита с 5% ZrO2Е ≈ 387 ± 5 ГПа. Поскольку модуль упругости ZrO2 меньше E ZrB2 и E SiC, то очевидно, что основной причиной наблюдаемого увеличения модуля упругости композитов ZrB2–SiC–ZrO2 связано с уменьшением пористости [16–18].
В табл. 1 приведены данные по твердости HV и трещиностойкости KIc исследуемых композитов. Согласно полученным данным, увеличение содержания карбида циркония в композитах ZrB2–SiC–ZrC не оказало существенного влияния на их твердость. Так, например, HV керамики ZrB2–SiC составила 12.7 ± 0.2 ГПа, а твердость композита ZrB2–SiC–20% ZrC – 13.5 ± 0.4 ГПа. В целом, твердость полученных композитов ZrB2–SiC–ZrC ниже ожидаемых значений, что связано с наличием остаточной пористости.
Таблица 1.
Твердость HV и трещиностойкость KIc композитов ZrB2–SiC–ZrO2 и ZrB2–SiC–ZrC
Композит | HV, ГПа | KIc, МПа м1/2 | Композит | HV, ГПа | KIc, МПа м1/2 |
---|---|---|---|---|---|
ZrB2–SiC | 12.7 ± 0.2 | 4.6 ± 0.3 | ZrB2–SiC | 12.7 ± 0.2 | 4.6 ± 0.3 |
ZrB2–SiC–5% ZrO2 | 13.4 ± 0.3 | 3.1 ± 0.3 | ZrB2–SiC–5% ZrC | 12.5 ± 0.2 | 4.5 ± 0.3 |
ZrB2–SiC–10% ZrO2 | 14.2 ± 0.3 | 4.5 ± 0.4 | ZrB2–SiC–10% ZrC | 12.8 ± 0.3 | 4.3 ± 0.3 |
ZrB2–SiC–15% ZrO2 | 14 ± 0.4 | 5.8 ± 0.3 | ZrB2–SiC–15% ZrC | 13 ± 0.4 | 4.1 ± 0.2 |
ZrB2–SiC–20% ZrO2 | 14.3 ± 0.4 | 7.3 ± 0.4 | ZrB2–SiC–20% ZrC | 13.5 ± 0.4 | 4.1 ± 0.3 |
Твердость композитов ZrB2–SiC–ZrO2 возрастала с увеличением содержания ZrO2. Оксид циркония имеет наименьшую твердость в сравнении другими компонентами композитов – карбидом кремния и боридом циркония, поэтому причиной наблюдаемого увеличения твердости является уплотнение композитов.
Рассчитанная из суммарной длины трещин от отпечатка Виккерса трещиностойкость KIc полученной керамики ZrB2–5% SiC составила 4.6 ± ± 0.3 МПа м1/2, что сопоставимо с трещиностойкостью композитов с бöльшим содержанием карбида кремния ZrB2–20% SiC (KIc ≈ 4–6 МПа м1/2) и больше KIc монолитной керамики ZrB2 [19–21]. Основным механизмом увеличения трещиностойкости керамических композитов с дисперсными включениями является изменение траектории распространения трещин на межфазных границах [22, 23]. Можно предположить, что высокое значение KIc для керамики ZrB2–5% SiC (с малым содержанием включений карбида кремния) обусловлено присутствием остаточной пористости – поры сдерживают распространение трещин.
Композиты ZrB2–SiC–ZrC с разным содержанием ZrC весьма слабо отличались величиной KIc. Так, например, трещиностойкость композита с содержанием карбида циркония 5% составила 4.5 ± 0.3 МПа м1/2, а композита с 20% карбида циркония – 4.7 ± 0.3 МПа м1/2.
Для композитов ZrB2–SiC–ZrO2 увеличение содержания оксида циркония привело к увеличению KIc, так, например, для композита с 20% ZrO2 трещиностойкость составилa 7.3 ± 0.4 МПа м1/2. При меньшей пористости эти композиты имели бóльшую трещиностойкость. Для композитов с дисперсными включениями диоксида циркония в тетрагональной модификации, испытывающей мартенситное превращение под действием механической нагрузки, увеличение трещиностойкости помимо отклонения трещин на межфазных границах возможно еще и за счет диссипации энергии трещин на тетрагонально-моноклинное превращение в частицах t-ZrO2 [24–26].
ЗАКЛЮЧЕНИЕ
Показано, что добавка ZrC в керамическом композите ZrB2–5% SiC, получаемом спеканием под давлением при температуре 1600°С, не привела к заметному увеличению плотности и не оказала значительного влияния на свойства. Добавка ZrO2, напротив, способствовала увеличению плотности керамических композитов на основе ZrB2–5% SiC, возрастанию твердости и трещиностойкости. Так, например, KIc керамики ZrB2–SiC составил 4.6 ± 0.3 МПа м1/2, а для композита с 20% ZrO2 – 7.3 ± 0.4 МПа м1/2.
Список литературы
Rangaraj L. et al. Processing of Refractory Metal Borides, Carbides and Nitrides // Key Eng. Mater. 2009. V. 395. P. 69–88. https://doi.org10.4028/www.scientific.net/KEM.395.69
Monteverde F. Ultra-High Temperature HfB2–SiC Ceramics Consolidated by Hot-Pressing and Spark Plasma Sintering // J. Alloys Compd. 2007. V. 428. № 1–2. P. 197–205. https://doi.org/10.1016/j.jallcom.2006.01.107
Zimmermann J.W., Hilmas G.E., Fahrenholtz W.G., Monteverde F., Bellosi A. Fabrication and Properties of Reactively Hot Pressed ZrB2–SiC Ceramics // J. Eur. Ceram. Soc. 2007. V. 27. № 7. P. 2729–2736. https://doi.org/10.1016/j.jeurceramsoc.2006.11.074
Squire T.H., Marschall J. Material Property Requirements for Analysis and Design of UHTC Components in Hypersonic Applications // J. Eur. Ceram. Soc. 2010. V. 30. P. 2239–2251. https://doi.org/10.1016/j.jeurceramsoc.2010.01.026
Fahrenholtz W.G., Hilmas G.E., Chamberlain A.L., Zimmermann J.W., Fahrenholtz B. Processing and Characterization of ZrB2 Based Ultra-High Temperature Monolithic and Fibrous Monolithic Ceramics // J. Mater. Sci. 2004. V. 39. P. 5951–5957.
Melendez J.J., Dominguez-Rodriguez A., Monteverde F., Melandri C., Portu G. Characterisation and High Temperature Mechanical Properties of Zirconium Boride-Based Materials // J. Eur. Ceram. Soc. 2002. V. 22. P. 2543–2549. https://doi.org/10.1016/S0955-2219(02)00114-0
Kalish D., Clougherty E.V., Kreder K. Strength, Fracture Mode and Thermal Stress Resistance of HfB2 and ZrB2 // J. Am. Ceram. Soc. 1969. V. 52. P. 30–36. https://doi.org/10.1111/j.1151-2916.1969.tb12655.x
Buyakov A.S., Kulkov S.N. Porous Ceramic Composite ZrO2(MgO)–MgO for Osteoimplantology // IOP Conf. Ser.: Mater. Sci. Eng. 2017. V. 175. P. 012025. https://doi.org/10.1088/1757-899X/175/1/012025
Fahrenholtz W.G., Hilmas G.E., Talmy I.G., Zaykoski J.A. Refractory Diborides of Zirconium and Hafnium // J. Am. Ceram. Soc. 2007. V. 90. P. 1347–1364. https://doi.org/10.1111/j.1551-2916.2007.01583.x
Guo S.Q. Densification of ZrB2-Based Composites and Their Mechanical and Physical Properties: A Review // J. Eur. Ceram. Soc. 2009. V. 29. P. 995–1011. https://doi.org/10.1016/j.jeurceramsoc.2008.11.008
Zhang S.C., Hilmas G.E., Fahrenholtz W.G. Mechanical Properties of Sintered ZrB2–SiC Ceramics // J. Eur. Ceram. Soc. 2011. V. 31. P. 893–901. https://doi.org/10.1016/j.jeurceramsoc.2010.11.013
Guo W.M., Yang Z.G., Zhang G.J. Comparison of ZrB2–SiC Ceramics with Yb2O3 Additive Prepared by Hot Pressing and Spark Plasma Sintering // Int. J. Refract. Met. Hard Mater. 2011. V. 29. P. 452–455. https://doi.org/10.1016/j.ijrmhm.2011.02.001
Zhou P., Hu P., Zhang X., Han W. Laminated ZrB2–SiC Ceramic with Improved Strength and Toughness // Scr. Mater. 2011. V. 64. P. 276–279. https://doi.org/10.1016/j.scriptamat.2010.10.005
Evans A.G., Charles E.A. Fracture Toughness Determination by Indentation // J. Am. Ceram. Soc. 1976. V. 59. P. 371–372. https://doi.org/10.1111/j.1151-2916.1976.tb10991.x
Салтыков С.А. Стереометрическая металлография. М.: Металлургия, 1976. 271 с.
Zhang G.-J., Deng Zh.-Y., Kondo N., Yang J.-F., Ohji T. Reactive Hot Pressing of ZrB2–SiC Composites // J. Am. Ceram. Soc. 2000. V. 83. № 9. P. 2330–2332. https://doi.org/10.1111/j.1151-2916.2000.tb01558.x
Zhu T., Li W., Zhang X., Hu P., Hong Ch., Weng L. Damage Tolerance and R-Curve Behavior of ZrB2–ZrO2 Composites // Mater. Sci. Eng., A. 2009. V. 516. P. 297–301. https://doi.org/10.1016/j.msea.2009.03.023
Hussainova I., Voltšihhin N., Cura E., Hannula S.-P. Densification and Characterization of Spark Plasma Sintered ZrC–ZrO2 Composites // Mater. Sci. Eng., A. 2014. V. 597. P. 75–81. https://doi.org/10.1016/j.msea.2013.12.058
Zamora V., Ortiz A.L., Guiberteau F., Nygren M. In Situ Formation of ZrB2–ZrO2 Ultra-High-Temperature Ceramic Composites from High-Energy Ball-Milled ZrB2 Powders // J. Alloys Compd. 2012. V. 518. P. 38–43. https://doi.org/10.1016/j.jallcom.2011.12.102
Li W., Zhang X., Hong Ch., Han W., Han J. Preparation, Microstructure and Mechanical Properties of ZrB2–ZrO2 ceramics // J. Eur. Ceram. Soc. 2009. V. 29. P. 779–786. https://doi.org/10.1016/j.jeurceramsoc.2008.06.033
Zhang X., Li W., Hong C., Han W. Microstructure and Mechanical Properties of ZrB2-Based Composites Reinforced and Toughened by Zirconia // Int. J. Appl. Ceram. Tech. 2008. V. 5. № 5. P. 499–504. https://doi.org/10.1111/j.1744-7402.2008.02199.x
Faber K.T., Evans A.G. Crack Deflection Process-1, Theory // Acta Metall. 1983. V. 31. № 4. P. 565–76. https://doi.org/10.1016/0001-6160(83)90046-9
Faber K.T., Evans A.G. Crack Deflection Process II, Experiment // Acta Metall. 1983. V. 31. № 4. P. 577–584. https://doi.org/10.1016/0001-6160(83)90047-0
Porter D.L., Evans A.G., Heuer A.H. Transformation-Toughening in Partially-Stabilized Zirconia (PSZ) // Acta Metall. 1979. V. 27. № 10. P. 1649–1654. https://doi.org/10.1016/0001-6160(79)90046-4
Loganathan A., Gandhi A.S. Effect of Phase Transformations on the Fracture Toughness of Yttria Stabilized Zirconia // Mater. Sci. Eng., A. 2012. V. 556. P. 927–935. https://doi.org/10.1016/j.msea.2012.07.095
Mamivand M., Zaeem A.M., Kadiri E.H. Phase Field Modeling of Stress-Induced Tetragonal-to-Monoclinic Transformation in Zirconia and Its Effect on Transformation Toughening // Acta Metall. 2014. V. 64. P. 208–219. https://doi.org/10.1016/j.actamat.2013.10.031
Дополнительные материалы отсутствуют.
Инструменты
Неорганические материалы