Неорганические материалы, 2020, T. 56, № 7, стр. 774-779
Восстановление оксидных соединений циркония кальцием
В. М. Орлов 1, *, М. В. Крыжанов 1
1 Институт химии и технологии редких элементов и минерального сырья им. И.В. Тананаева – обособленное подразделение ФИЦ “Кольский научный центр Российской академии наук”
184209 Мурманская обл., Апатиты, Академгородок, 26а, Россия
* E-mail: v.orlov@ksc.ru
Поступила в редакцию 27.09.2019
После доработки 16.11.2019
Принята к публикации 27.12.2019
Аннотация
Определены адиабатическая температура восстановления ZrO2 и CaZrO3 кальцием (1525 и 1040 K соответственно) и температура начала реакций. В смеси реагентов и атмосфере аргона в реакторе она составляет около 1123 K и обусловлена началом плавления кальция. При использовании в шихте кальция с нанесенной на его поверхность пленкой CaCl2 восстановление начиналось в атмосфере аргона при температуре 1023 K, в вакууме при 973 K. Восстановлением в течение 3 ч при температуре 1023 К получен порошок циркония с содержанием кислорода 0.36% и удельной поверхностью 0.35 м2/г.
ВВЕДЕНИЕ
Мелкозернистые порошки циркония используются в пиротехнике и для производства изделий методами порошковой металлургии. Основными способами их получения являются восстановление гексафторцирконата калия K2ZrF6 натрием [1–4] и восстановление диоксида циркония кальцием [1, 5]. Процесс натриетермического восстановления K2ZrF6 осложняется необходимостью соблюдения строгих мер техники безопасности при работе со щелочным металлом. При восстановлении шихты на воздухе [2] в результате горения натрия в атмосферу выделяется много аэрозолей, а гашение реакционной массы, содержащей большое количество избыточного натрия, взрывоопасно. Осуществление восстановления в замкнутом объеме с последующей отгонкой избыточного натрия [3, 4] более безопасно, однако и в этом случае могут быть сложности с утилизацией образующегося при отгонке натрия жидкого сплава натрия с калием.
В этом плане гораздо технологичнее получать порошок циркония восстановлением его диоксида кальцием по реакции
В простейшем варианте восстановления брикетированную смесь реагентов нагревают в атмосфере аргона до температуры 1273–1373 K и выдерживают в этих условиях в течение 1 ч [1]. Для повышения качества порошка циркония авторы работы [5] осуществляли восстановление в среде расплавленного хлорида кальция. Количество CaCl2 в шихте составляло 444 г на 100 г Ca, что соответствовало необходимому для растворения оксида кальция, образовавшегося в результате реакции. Процесс вели при температуре 1173–1573 K с выдержкой 1–5 ч. Растворение СаО в хлориде кальция способствовало получению порошка циркония с более низким содержанием кислорода. В полученных авторами порошках оно составляло 0.056–0.65%.
Представляло интерес исследовать возможность реализации процесса кальциетермического восстановления диоксида циркония при более низкой, чем общепринято, температуре, а также возможность увеличения удельной поверхности порошков Zr при использовании в качестве прекурсора цирконата CaZrO3, восстановление которого протекает по реакции
ЭКСПЕРИМЕНТАЛЬНАЯ ЧАСТЬ
Определение адиабатической температуры (Тад) реакций (1) и (2) в зависимости от температуры шихты (Т0) и избытка восстановителя (∆mCa) проводили с использованием программного комплекса моделирования химических и фазовых равновесий TERRA [6]. Термодинамическое моделирование взаимодействия в системах ZrO2–Ca и CaZrO3–Ca осуществляли при стехиометрии реагентов соответствующих реакций, а также с избытком кальция 25, 50 и 75% относительно стехиометрического количества. Моделирование проводили в интервале температуры 300–3000 K в среде аргона при давлении 0.1 МПа, ионизированные вещества из расчета исключали. Температура шихты составляла 300–1100 K, шаг изменения 100 K. Подробно методика изложена в работе [7].
В качестве исходного материала для восстановления использовали порошки диоксида циркония квалификации “ч.” по ТУ 6-09-2486-77 с удельной поверхностью 35 м2/г и производства АО “Чепецкий механический завод” с удельной поверхностью 0.7 м2/г, а также порошок цирконата CaZrO3 с удельной поверхностью 0.5 м2/г, предварительно синтезированный методом твердофазного спекания ZrO2 “ч.” и карбоната кальция при температуре 1573 K. Восстановителем служил кальций в виде гранул с размером частиц 0.04–2.0 мм по ТУ 083.5.290-92 производства АО “Чепецкий механический завод”.
Восстановление проводили в реакторе, представляющем собой реторту из нержавеющей стали с герметичной водоохлаждаемой крышкой. В крышке имелись патрубки для ввода термопары и подсоединения к вакуумной системе. В ряде экспериментов гранулы кальция предварительно смачивали насыщенным раствором CaCl2 в этиловом спирте (из расчета 10–20 г CaCl2 на 100 г кальция), затем его сушили. Навеску исходного материала 10 г смешивали с кальцием, взятым с избытком 50% относительно стехиометрического количества, и загружали в цилиндрический ниобиевый контейнер диаметром 23 мм, высота загрузки составляла 25–40 мм. В ряде случаев загруженную в контейнер шихту уплотняли. Контейнеры размещали в стальном реакционном стакане, после чего готовую сборку помещали в реторту. Принципиальная схема установки и ее подробное описание приведены в работе [8].
Реактор вакуумировали, заполняли аргоном и нагревали до температуры восстановления (Т), при которой выдерживали заданное время. Эксперименты вели либо в атмосфере аргона при температуре 1023–1123 K с выдержкой 1 ч, либо при температуре 973–1073 K и вакуумировании реактора форвакуумным насосом 2НВР-5ДМ.
После выдержки и охлаждения до комнатной температуры реактор дозировано заполняли воздухом до атмосферного давления для пассивации образовавшегося порошка циркония. Продукты восстановления извлекали и дважды обрабатывали 10%-ным раствором соляной кислоты для удаления избытка восстановителя и образовавшегося оксида кальция. Полученный порошок промывали дистиллированной водой до нейтральной реакции раствора и сушили при температуре 323 K.
Фазовый состав полученных продуктов определяли с помощью рентгеновского дифрактометра XRD-6000 фирмы Shimadzu (CuKα-излучение) и базы данных ICDD PDF-2. Величину удельной поверхности измеряли адсорбционным статическим методом БЭТ на приборе Micromeritics TriStar II 3020. Содержание общего циркония в полученных порошках определяли по увеличению массы образца при его окислении. Температуру воспламенения определяли по методике, рекомендованной в ТУ 48-4-376-76 для натриетермического порошка циркония. Концентрацию кислорода в порошках определяли методом газоадсорбционной хромотографии в сочетании с импульсным нагревом на анализаторе К-671. Распределение частиц порошков по крупности анализировали с помощью фотометрического седиментометра ФСХ-6К производства “ООО ЛабНаучПрибор”.
РЕЗУЛЬТАТЫ И ОБСУЖДЕНИЕ
Полученные значения адиабатической температуры реакции кальциетермического восстановления оксидных соединений циркония в зависимости от температуры шихты и избытка Ca представлены на рис. 1. Адиабатическая температура реакции (1) при стехиометрическом соотношении реагентов составляет 1525 K, а реакции (2) в тех же условиях всего 1040 K.
Рис. 1.
Зависимости адиабатической температуры восстановления от температуры шихты в системах: ZrO2–Ca (а), CaZrO3–Ca (б); содержание кальция: стехиометрическое (1), избыток 25 (2), 50 (3), 75% (4).

При начальной температуре реагентов, соответствующей температуре плавления кальция (1115 K [9]), и избытке кальция в шихте 25–75% Tад = 1650–1750 K, что не превышает его температуру кипения. В этих условиях реакция восстановления в смеси реагентов не должна сопровождаться тепловым взрывом.
Эксперименты по восстановлению диоксида циркония показали, что при нагреве в атмосфере аргона смеси реагентов наблюдается резкий кратковременный скачок температуры при 1115–1125 K (кривая 1 на рис. 2), свидетельствующий о начале реакции. Восстановлением свободно насыпанной смеси кальция с ZrO2 партии 1 и CaZrO3 при температуре 1123 K в течение 1 ч и давлении аргона в реакторе 110 кПа были получены порошки циркония с удельной поверхностью на уровне 1 м2/г и содержанием основного вещества (Zr) 97.7%. При использование ZrO2 с большей величиной удельной поверхности (партия 2) удельная поверхность порошка циркония составила 2.9 м2/г, содержание основного вещества 96.5%. Использование в процессе предварительно уплотненной шихты позволило увеличить степень восстановления. Содержание циркония в порошках увеличилось на 1.6% и в порошке, полученном восстановлением ZrO2 партии 1, достигло 99.3%. Поэтому дальнейшие эксперименты вели с уплотненной шихтой.
Рис. 2.
Изменение температуры в процессе восстановления шихты с кальцием в состоянии поставки (1), с использованием смачивания хлоридом кальция: в атмосфере аргона (2) и в вакууме (3).
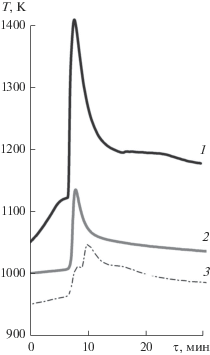
Поскольку скачок температуры, обозначающий начало реакции, соответствует температуре плавления кальция, можно было полагать, что контакт между реагентами связан с разрушением поверхностного оксида СаО. Представляло интерес исследовать возможность обеспечения контакта между кальцием и восстанавливаемым соединением при более низкой температуре. Известно, что присутствие галогенидов способствует разрушению поверхностной пленки СаО. Поэтому для составления шихты в дальнейшем использовали гранулы кальция, смоченные насыщенным раствором CaCl2 в этиловом спирте.
При нагреве такой шихты в атмосфере аргона резкое увеличение температуры до 1100–1150 K, свидетельствующее о начале реакции, наблюдалось уже при 980–1030 K (кривая 2 на рис. 2). Затем следовало плавное охлаждение. Характеристики порошков, полученных после часовой выдержки в этих условиях, приведены в табл. 1. Для сравнения там же приведены характеристики порошков, полученных с использованием гранул кальция без предварительного смачивания (порошки 1–3, табл. 1). Смачивание гранул кальция его хлоридом позволило повысить степень восстановления, особенно цирконата кальция и ZrO2 партии 2. Присутствие CaZrO3 в порошке 2 (табл. 1) является следствием незавершенности процесса восстановления промежуточного продукта. Аналогичное явление наблюдалось при восстановлении пентаоксида ниобия магнием [10]. Большая удельная поверхность порошка 2 – следствие присутствия в нем мелкодисперсного CaZrO3. Более низкая температура воспламенения порошков 2 и 3 (табл. 2), несмотря на большое содержание оксидной фазы, возможно, объясняется каталитическим действием на процесс окисления цирконата.
Таблица 1.
Характеристики порошков, полученных восстановлением при температуре 1073 K с выдержкой 1 ч
Порошок | Прекурсор | Фазовый состав | S, м2/г | СZr, % | Tв, K |
---|---|---|---|---|---|
1 | ZrO2 (партия 1) | Zr, ZrO2, γ-ZrH | 0.76 | 98.0 | 547 |
2 | ZrO2 (партия 2) | Zr, ZrO2, CaZrO3 | 12 | 85.8 | 506 |
3 | CaZrO3 | Zr, ZrO2, CaZrO3 | 3.6 | 86.4 | 508 |
Смачивание CaCl2 | |||||
4 | ZrO2 (партия 1) | Zr, δ-ZrH2, γ-ZrH, ZrO2* | 0.41 | 98.6 | 569 |
5 | ZrO2 (партия 2) | Zr, δ-ZrH2, γ-ZrH, ZrO2 | 3.4 | 92.9 | 566 |
6 | CaZrO3 | Zr, δ-ZrH2, γ-ZrH, CaZrO3 | 1.2 | 97.0 | 537 |
Таблица 2.
Характеристики порошков, полученных восстановлением кальцием, смоченным CaCl2, при температуре 1023 K
Порошок | Прекурсор | Фазовый состав | S, м2/г | СZr, % | Tв, K |
---|---|---|---|---|---|
1 | ZrO2 (партия 1) | Zr, δ-ZrH2, γ-ZrH | 0.54 | 98.3 | 562 |
2 | ZrO2 (партия 2) | Zr, δ-ZrH1.66, ZrO2* | 2.6 | 96.5 | 525 |
3 | CaZrO3 | Zr, δ-ZrH1.66, CaZrO3 | 1.3 | 95.0 | 503 |
Выдержка в вакууме 2 ч | |||||
4 | ZrO2 (партия 1) | Zr, γ-ZrH | 0.35 | 99.8 | 540 |
5 | ZrO2 (партия 2) | Zr, ZrO2, γ-ZrH | 1.3 | 98.5 | 545 |
6 | CaZrO3 | Zr, γ-ZrH | 1.2 | 99.6 | 534 |
* Следы. |
Снижение температуры восстановления шихты с участием кальция, смоченного CaCl2, до 1023 K не привело к уменьшению содержания циркония в порошках (порошки 1–3, табл. 2). После последующей двухчасовой выдержки с вакуумированием реактора восстановление цирконата кальция и диоксида циркония партии 1 прошло практически полностью (порошки 4, 6, табл. 2). Содержание кислорода в порошке 4 с удельной поверхностью 0.35 м2/г было всего 0.36 мас. %. Более высокое содержание кислорода в порошке 6 – 0.74 мас. % – следствие в 3 раза большей удельной поверхности. Эти результаты свидетельствуют о важной роли паров кальция в процессе восстановления, особенно если процесс реализуется при температуре ниже его температуры плавления.
Более интенсивному испарению должно способствовать проведение процесса в вакууме. При нагреве шихты с участием CaCl2 в вакууме начало реакции отмечалось при температуре 950–970 K (рис. 2, кривая 3), которую можно считать минимальной для восстановления оксидных соединений циркония кальцием. Для уменьшения потерь кальция в дальнейшем нагрев вели в атмосфере аргона до температуры 973 K, после чего реактор вакуумировали. Сопровождающий начало реакции подъем температуры на 50–60 K наблюдался сразу. Снижение температуры начала реакции – следствие более раннего нарушения сплошности поверхностного оксида и повышения интенсивности реакции за счет увеличения количества паров кальция. Характеристики порошков циркония, полученных в ходе восстановления при температуре 973 K и последующем вакуумировании, приведены в табл. 3. Уже после часовой выдержки при весьма низкой, по сравнению с общепринятой, температуре достигнута довольно высокая степень восстановления, увеличение выдержки до 3 ч позволило снизить содержание кислорода в порошке 4 до 0.78 мас. %. Продукты реакции в отличие от образовавшихся при более высокой температуре представляли собой рыхлую массу, извлечение которой не вызывало затруднений.
Таблица 3.
Характеристики порошков, полученных восстановлением в вакууме при температуре 973 K
№ | Прекурсор | Фазовый состав | S, м2/г | СZr, % | Tв, K |
---|---|---|---|---|---|
Выдержка 1 ч | |||||
1 | ZrO2 (партия 1) | Zr, ZrH, ZrO2 | 0.58 | 95.9 | 556 |
2 | ZrO2 (партия 2) | Zr, δ-ZrH1.66, ZrO2* | 5.0 | 95.3 | 517 |
3 | CaZrO3 | Zr, δ-ZrH1.66, CaZrO3 | 2.1 | 94.0 | 522 |
Выдержка 3 ч | |||||
4 | ZrO2 (партия 1) | Zr | 0.64 | 99.2 | 543 |
5 | ZrO2 (партия 2) | Zr, ZrO2* | 0.57 | 99.4 | 558 |
6 | CaZrO3 | Zr, γ-ZrH | 1.4 | 98.8 | 509 |
* Следы. |
Удельная поверхность порошков, полученных восстановлением диоксида циркония при температуре 973 K в вакууме, находится на уровне 0.6 м2/г. Кривая распределения частиц в этих порошках приведена на рис. 3. При использовании в качестве прекурсора цирконата кальция удельная поверхность увеличилась всего до 1.4 м2/г. Для сравнения при восстановлении пентаоксидов тантала и ниобия магнием в интервале температуры 973–1100 K удельная поверхность порошка тантала достигает 15 м2/г, а ниобия 30 м2/г [11]. Использование в качестве прекурсора танталата Mg4Ta2O9 и ниобата Mg4Nb2O9 позволило увеличить удельную поверхность получаемых порошков Та и Nb до 80 и 160 м2/г соответственно [8, 12]. В процессе восстановления оксидных соединений тугоплавких металлов V и VI группы [8, 12, 13 ] пары восстановителя проникают внутрь частиц оксида и восстановление происходит в объеме с образованием слоистой структуры из частиц металла и оксида восстановителя. После выщелачивания оксида восстановителя образуется мезопористая структура порошка металла. Такой механизм, вероятно, является следствием высокой адиабатической температуры реакции восстановления этих соединений, приводящей в результате теплового удара к трещиноватости частиц оксида.
Рис. 3.
Распределение частиц в порошке циркония, полученном восстановлением ZrO2 при температуре 973 К.
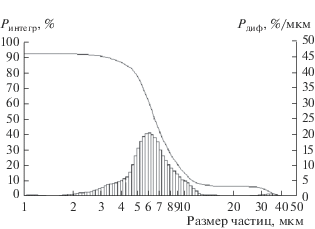
Адиабатическая температура восстановления диоксида циркония значительно ниже (на 1000–1100 K). В то же время диоксид циркония более тугоплавкое и термоустойчивое соединение. В связи с этим нарушения сплошности частиц оксида при инициировании реакции не происходит. Фронт реакции движется равномерно от поверхности вглубь. В результате порошок циркония состоит из беспористых плотных частиц. По этой же причине использование в качестве прекурсора двойного оксида CaZrO3 не привело к значительному увеличению удельной поверхности.
ЗАКЛЮЧЕНИЕ
Показана возможность достаточно полного восстановления оксидных соединений циркония ZrO2 и CaZrO3 кальцием при температуре ниже его температуры плавления. Присутствие на поверхности частиц кальция пленки СаCl2 позволяет уменьшить температуру начала реакции восстановления в атмосфере аргона с 1123 до 1023 K без ухудшения качества порошка циркония. В вакууме температура начала реакции снизилась до 973 K. Удельная поверхность порошков с содержанием циркония более 99%, полученных восстановлением в течение 3 ч при температуре 973–1023 K, находится на уровне 0.5 м2/г, содержание кислорода 0.36–0.78 мас. %, температура воспламенения 540–560 К. Восстановление при температуре ниже температуры плавления кальция осуществляется исключительно его парáми, поэтому относительно небольшая поверхность порошков по сравнению с порошками тугоплавких металлов V и VI группы, полученных восстановлением их оксидных соединений в аналогичных условиях, свидетельствует о разных механизмах роста частиц этих металлов.
Список литературы
Зеликман А.Н., Коршунов Б.Г. Металлургия редких металлов. М.: Металлургия, 1991. 432 с.
Вакс А.Ш., Пепеляева Е.А., Ведяшкина Л.А. Получение циркония восстановлением фтороцирконата калия металлическим натрием // Сб. науч. трудов Гиредмет (1931–1956 гг.). Т. 1. Технология. М.: Металлургиздат, 1959. С. 518–519.
Орлов В.М., Федорова Л.А. Получение порошка циркония натриетермическим восстановлением из фторцирконата калия // Химическая технология. 2004. № 7. С. 26–29.
Орлов В.М., Федорова Л.А., Калинников В.Т. и др. Натриетермическая технология производства порошков циркония // Цв. металлы. 2012. № 8. С. 72–76.
Abdelkader A.M., El-Kashi E. Calciothermic Reduction of Zirconium Oxide in Molten CaCl2 // ISIJ International. 2007. V. 47. № 1. P. 25–31.
Трусов Б.Г. Программная система ТЕРРА для моделирования фазовых и химических равновесий в плазмохимических системах [Электронный ресурс] 4 Международный симпозиум по теоретической и прикладной плазмохимии (Иваново, 13–18 мая 2005 г.): режим доступа: http://main.isuct.ru/files/ konf/ISTAPC2005/proc/2-11.pdf, свободный (дата обращения: 06.06.19).
Орлов В.М., Крыжанов М.В. Термодинамическое моделирование процесса магниетермического восстановления танталатов магния и лития // Неорган. материалы. 2015. Т. 51. № 6. С. 680–684.
Орлов В.М., Крыжанов М.В. Получение нанопорошков тантала магниетермическим восстановлением танталатов // Металлы. 2015. № 4. С. 93–97.
Волков А.И., Жарский И.М. Большой химический справочник. Мн.: Современная школа, 2005. 608 с.
Орлов В.М., Сухоруков В.В. Магниетермическое получение порошков ниобия // Металлы. 2010. № 2. С. 16–22.
Хаас Х., Бартманн У., Комея Т., Сато Н., Штарк Х.К. Способ получения ниобиевых и танталовых порошков: Пат. 2397843 РФ. Б.И. 24.
Орлов В.М., Крыжанов М.В., Князева А.И., Осауленко Р.Н. Порошки ниобия с мезопористой структурой // Физикохимия поверхности и защита материалов. 2018. Т. 54. № 5. С. 444–449.
Орлов В.М., Колосов В.Н. Магниетермическое восстановление оксидных соединений вольфрама и молибдена // Доклады АН. 2016. Т. 468. С. 282–292.
Дополнительные материалы отсутствуют.
Инструменты
Неорганические материалы