Неорганические материалы, 2021, T. 57, № 2, стр. 163-172
Синтез нанокристаллических порошков в системе CеO2〈ZrO2〉–Al2O3 цитратным золь–гель-методом
Л. В. Морозова *
Институт химии силикатов им. И.В. Гребенщикова Российской академии наук
199034 Санкт-Петербург, наб. Макарова, 2, Россия
* E-mail: morozova_l_v@mail.ru
Поступила в редакцию 02.03.2020
После доработки 20.09.2020
Принята к публикации 22.09.2020
Аннотация
Цитратным золь–гель-методом в системе CeO2〈ZrO2〉–Al2O3 получены высокодисперсные слабо агрегированные порошки-прекурсоры, площадь удельной поверхности которых составляет 350–360 м2/г. При термической обработке прекурсоров в интервале температур 700–1000°С синтезированы порошки на основе флюоритоподобного твердого раствора Ce0.7Zr0.3O2 с размером кристаллитов <30 нм. Установлено, что оксид алюминия замедляет процесс роста кристаллитов Ce0.7Zr0.3O2. Методом низкотемпературной адсорбции азота исследованы текстурные характеристики порошков (1000°С): их удельная поверхность составляет в зависимости от состава 90 и 105 м2/г, удельный объем пор достигает 0.380 см3/г, распределение пор по размерам является мономодальным и лежит в интервале 2.5–10 нм. Изучено влияние термического “старения” при температуре 1000°С (50 ч) на структуру и дисперсность порошков. На основании экспериментальных результатов предложена технология синтеза нанокристаллических мезопористых порошков в системе CeO2〈ZrO2〉–Al2O3 для получения носителей активной фазы (Pt, Pd, Rh) в трехмаршрутных катализаторах.
ВВЕДЕНИЕ
Развитие современных технологий в химической и нефтехимической отраслях промышленности тесно связано с использованием современных наноструктурированных катализаторов, обладающих высокой каталитической активностью, термостабильностью, небольшим количеством благородных металлов (<0.12 мас. %). В настоящее время актуальны исследования по разработке и созданию катализаторов для двигателей внутреннего сгорания, чтобы защитить окружающую среду от токсичных выбросов автотранспорта. Для нейтрализации продуктов сгорания углеводородного топлива используют трехмаршрутные катализаторы, которые обеспечивают одновременную конверсию всех основных примесей, содержащихся в выхлопных газах автомобилей (остатки углеводородов, угарный газ (CO), оксиды азота (NOx)), до экологически допустимых продуктов – диоксида углерода, воды и азота [1–3].
Основными активными компонентами в таких катализаторах являются высокодисперсные металлы платиновой группы (Pt, Pd, Rh), нанесенные на носители, содержащие диоксид церия [4, 5]. Использование СеО2 в качестве базового компонента носителя катализаторов связано с уникальной способностью ионов церия действовать как кислородный буфер: накапливать кислород в кристаллической решетке диоксида церия, а также выделять его в результате превращения Се4+ ↔ Се3+, сохраняя при этом стабильную F‑структуру в которой облегчен перенос ионов О2– [6, 7].
Следует отметить, что введение в CeO2 изовалентного катиона Zr4+ увеличивает количество дефектов кристаллической решетки как на поверхности, так и в объеме, повышая подвижность кислорода и облегчая его диффузию в решетке твердого раствора Ce1 – xZrxO2, в результате чего происходит повышение каталитической активности [8]. Предотвратить структурную трансформацию в CexZr1 – xO2 (F-CexZr1 –xO2 → T-CexZr1 –xO2), возникающую при температурах выше 1000°С, можно путем введения в твердый раствор CexZr1 – xO2 промотирующей добавки (например, Al2O3), которая будет создавать диффузионный барьер на границах кристаллитов CexZr1 – xO2, что позволит повысить удельную поверхность порошка и сдержать рост частиц [9].
Материалы, используемые в качестве носителей катализаторов, должны отвечать следующим требованиям: дисперсность порошка в нанометровом диапазоне, площадь удельной поверхности ~50–100 м2/г, наличие мезопор (2–20 нм), объем которых более 0.20 см3/г, мономодальное распределение пор по размерам, термическая стабильность. Совокупность данных параметров позволит осуществить равномерное распределение активной фазы как на поверхности, так и в порах носителя, что даст возможность избежать ее спекания и достигнуть высокой эффективности катализатора.
Важным этапом при создании трехмаршрутных катализаторов является разработка технологии синтеза материалов, используемых в качестве носителей активной фазы. Композиционные оксидные нанопорошки наиболее часто синтезируют методами “мягкой химии” – совместным осаждением гидроксидов и гидротермальным способом [10–12]. Следует отметить, что особого внимания также заслуживает цитратный метод (метод Печини) [13, 14], который дает возможность получать порошки оксидов металлов заданного состава с размером кристаллитов 10–30 нм при температурах ≤500°С [15]. Преимуществами данного метода также является то, что его осуществление не требует сложной аппаратуры, а в качестве исходных материалов чаще всего используются доступные реактивы. Цитратный метод синтеза оксидных материалов обеспечивает равномерное распределение компонентов в растворе, что позволяет избежать разделения катионов на последующих стадиях процесса.
Целью работы являлось получение нанокристаллических порошков CeO2〈ZrO2〉–Al2O3 цитратным золь–гель-методом, а также исследование их структуры и текстурных характеристик.
ЭКСПЕРИМЕНТАЛЬНАЯ ЧАСТЬ
Синтез порошков-прекурсоров в системе CeO2〈ZrO2〉–Al2O3. Базовым компонентом для синтеза порошков в системе CeO2〈ZrO2〉–Al2O3 выбран состав 70 мол. % СеО2–30 мол. % ZrO2 (Ce0.7Zr0.3O2), при таком соотношении оксидов, согласно диаграмме фазовых соотношений [16], образуется однофазный твердый раствор на основе СеО2 со структурой флюорита. Были приготовлены оксидные смеси с массовым соотношением Ce0.7Zr0.3O2 : Al2O3, равным 90 : 10 (СZA-1) и 80 : 20 (СZA-2). Количество оксида алюминия выбрано с учетом данных [17], что Al2O3 тормозит процесс роста кристаллитов флюоритоподобного твердого раствора на основе диоксида циркония.
Синтез порошков в системе CeO2〈ZrO2〉–Al2O3 проводили методом Печини, для этого использовали химические реактивы, приведенные в табл. 1. Из азотнокислых солей церия, цирконила и алюминия были приготовлены водные растворы с концентрацией ~0.2 М. На первом этапе синтеза составляли реакционную смесь путем смешивания водных растворов нитратов в соответствии со стехиометрией (составы СZA-1 и СZA-2) с раствором 5%-ной лимонной кислоты (10 мл), в результате чего получали коллоидный раствор – золь, состоящий из металл-цитратных комплексов: M(NO3)3 + 3C6H8O7 → M(C6H8O7)3 ⋅ (NO3)3. Затем коллоидный раствор объединяли с этиленгликолем (3 мл) для того, чтобы гидроксильные группы С2H4(OH)2 стабилизировали в растворе металл-цитратные комплексы [15]:
Таблица 1.
Исходные реагенты для синтеза порошков в системе CeO2〈ZrO2〉–Al2O3
Исходный реагент | Квалификация реактива | ГОСТ |
---|---|---|
Азотнокислый церий Ce(NO3)3 ∙ 6H2O | “ч. д. а.” | ТУ 6-09-4081-84 |
Азотнокислый цирконил ZrO(NO3)2 ∙ 2H2O | “ч. д. а.” | ТУ 6-09-1406-76 |
Азотнокислый алюминий Al(NO3)3 ∙ 9H2O | “х. ч.” | 3757–75 |
Лимонная кислота C6H8O7 | “ч. д. а.” | 908-2004 |
Этиленгликоль C2H4(OH)2 | “х. ч.” | 10164-76 |
На втором этапе полученный золь медленно упаривали при 100°С (8 ч) в сушильном шкафу SNOL, при этом молекулы лимонной кислоты и этиленгликоля вступали в реакцию поликонденсации, которая приводила к образованию полимерного геля с включенными в него молекулами цитратов. Затем образовавшийся гелеобразный продукт подвергали обработке при температуре ~200°С (10 ч), в процессе нагрева происходило образование хелатных комплексов, имеющих свободные гидроксильные группы, за счет которых протекала реакция этерификации [18].
На третьем этапе синтеза гель нагревали при 300°С (0.5 ч), что способствовало удалению физически связанной воды и оксидов азота. При разложении геля образовывались первичные частицы простых оксидов, которые затем взаимодействовали между собой с образованием сложного оксидного порошка-прекурсора [13].
Методы исследования. Седиментационный анализ (лазерный анализатор Horiba LB–5502) применяли для оценки размера агрегатов частиц (Dа) синтезированных порошков-прекурсоров. Погрешность измерения Dа составляла 5–15 нм в зависимости от размеров агрегатов, что соответствует относительной погрешности 3–8%.
Рентгенофазовый анализ (РФА, дифрактометр D8–Advance фирмы Bruker с монохроматическим CuKα-излучением) использовали для определения структуры и фазового состава порошков. Съемку проводили в интервале углов 2θ от 20° до 60° при комнатной температуре. Средний размер кристаллитов (dкр) рассчитывали из уширения дифракционных максимумов по формуле Селякова–Шеррера [19]. Величина погрешности при расчете dкр составляет ±1–3 нм. Идентификация фаз осуществлялась с помощью международной базы данных IСDD-2006.
Микроструктуру порошков-прекурсоров изучали методом электронной микроскопии (электронный микроскоп ЭМ–125 с Uуск = 75 кВ). Перед съемкой порошки фиксировали на опорной сетке с помощью коллоидной пленки.
Термическую обработку порошков проводили в электрической печи фирмы Naberterm в диапазоне 300–1200°С, точность определения температуры ±10°С.
Текстурные характеристики порошков исследовали методом низкотемпературной адсорбции азота (анализатор сорбции газа Quantachrom NOVA 1200e), образцы перед измерениями дегазировали при 40°C в течение 5 ч. На основании полученных данных рассчитана удельная поверхность (Sуд) образцов с использованием многоточечного метода БЭТ, относительная погрешность при измерении Sуд не превышала 4%. Удельный объем пор определен по предельному заполнению (р/р0 = 0.99), относительная погрешность составляла 6% [20]. Распределение пор по размерам рассчитывали на основании изотерм десорбции азота по методу Баррета–Джойнера–Халенды (BJH). Тип поровой структуры и форма пор синтезированных нанопорошков определены путем анализа вида полученных для них изотерм адсорбции и из формы петель капиллярно-конденсационного гистерезиса согласно международной классификации ИЮПАК [21].
РЕЗУЛЬТАТЫ И ОБСУЖДЕНИЕ
Методом РФА показано, что порошки-прекурсоры СZA-1 и СZA-2 после термической обработки гелей при 300°С являются рентгеноаморфными (рис. 1), вероятно, данная температура является недостаточной для формирования кристаллической структуры. Синтезированные порошки-прекурсоры состояли из “рыхлых” агрегатов, образованных частицами обтекаемой формы без четких границ с размерами менее 10 нм (рис. 2).
Рис. 2.
Микрофотографии, полученные с помощью ПЭМ, порошков-прекурсоров после термообработки при 300°С: CZA-1 (а), CZA-2 (б).
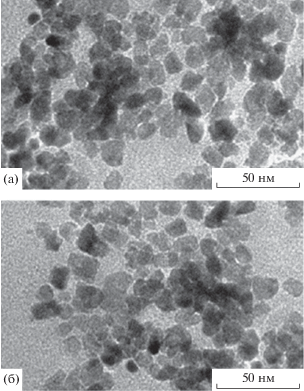
С помощью седиментационного анализа установлено мономодальное распределение агрегатов по размерам, которое лежит в диапазоне 50–180 нм (рис. 3). Удельная поверхность синтезированных порошков-прекурсоров СZA-1 и СZA-2 составляет 350–360 м2/г.
Рис. 3.
Распределение частиц по размерам (Dа) в порошках-прекурсорах после термообработки при 300°С: CZA-1 (а), CZA-2 (б).
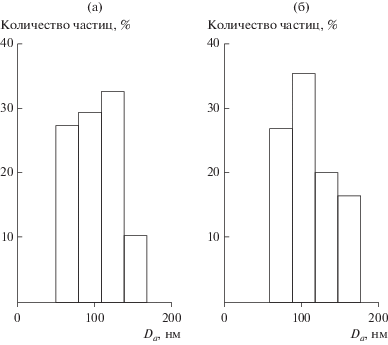
Изотермический обжиг синтезированных порошков СZA-1 и СZA-2 при 500°С (1 ч), по результатам РФА, приводит к образованию фазы твердого раствора Ce0.7Zr0.3O2 с кубической структурой типа флюорита (Fm3m) (рис. 4). Наличие широких дифракционных максимумов свидетельствует о невысокой степени окристаллизованности частиц Ce0.7Zr0.3O2 при данной температуре, средний размер кристаллитов твердых растворов CeO2〈ZrO2〉–Al2O3, рассчитанный из уширения дифракционного максимума 111 (2θ = 28.7°), равен 5 нм.
Рис. 4.
Дифрактограммы порошков в системе CeO2〈ZrO2〉–Al2O3 после термообработки при 500°С: CZA-1 (а), CZA-2 (б).
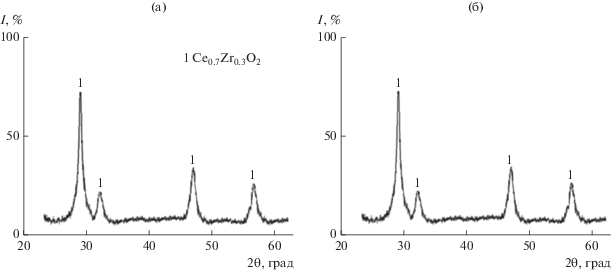
Для удаления углерода, возможно, оставшегося в порошках после синтеза, проводили обжиг при 700°С (1 ч) [22]. На дифрактограммах порошков СZA-1 и СZA-2 в этом случае (рис. 5а, 5в) идентифицируются только дифракционные максимумы, соответствующие кристаллической фазе Ce0.7Zr0.3O2 со структурой флюорита. Фаза оксида алюминия не регистрируется, это позволяет предположить, что в системе CeO2〈ZrO2〉–Al2O3 происходит формирование неравновесных твердых растворов с переменной концентрацией ионов Al3+ в кристаллической решетке Ce0.7Zr0.3O2 [23]. Средний размер кристаллитов твердого раствора Ce0.7Zr0.3O2 в порошках СZA-1 и СZA-2 составляет 10 и 8 нм соответственно.
Рис. 5.
Дифрактограммы порошков CZA-1 (а, б), CZA-2 (в, г) после термообработки при 700 (а, в) и 1000°С (б, г).
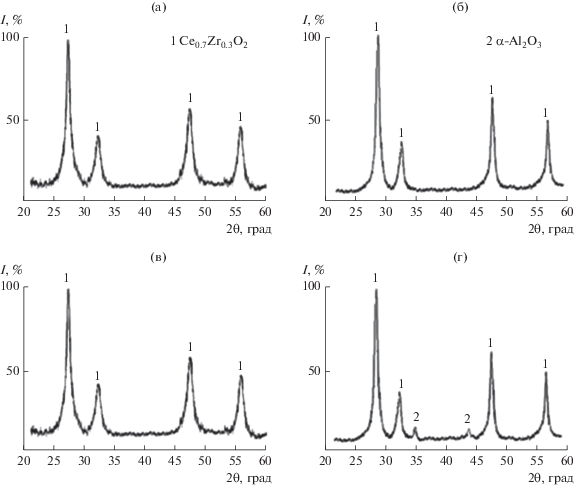
С использованием РФА установлено, что после термообработки при 1000°С структура порошка СZA-1 (рис. 5б) остается однофазной, т.е. оксид алюминия полностью растворяется в твердом растворе Ce0.7Zr0.3O2. На дифрактограмме порошка СZA-2 регистрируются два небольших максимума, соответствующие фазе α-Al2O3 (рис. 5г), появление которой можно объяснить частичным распадом неравновесного твердого раствора в системе CeO2〈ZrO2〉–Al2O3 и выделением α-Al2O3, что, вероятно, связано с более высоким содержанием оксида алюминия в порошке СZA-2 по сравнению с порошком СZA-1.
Обжиг порошков в интервале температур 700–1000°С приводит к монотонному увеличению среднего размера кристаллитов до 28 и 23 нм (рис. 6). Выше 1000°С наблюдался более интенсивный рост dкр, и при 1200°С размер кристаллитов достигал 55 нм для СZA-1 и 46 нм для СZA-2. На дифрактограммах порошков, обожженных при 1200°С, идентифицируется незначительное количество тетрагональной фазы стабилизированного диоксида циркония T-ZrO2 (~5–7 мас. %) (рис. 6). В порошке СZA-2 рост кристаллитов твердого раствора Ce0.7Zr0.3O2 в интервале 700–1200°С происходил медленнее, чем в порошке СZA-1 (рис. 7), при увеличении содержания Al2O3 до 30 мас. % наблюдалось нарушение однофазности синтезируемого продукта. Технологическая схема синтеза порошков в системе CeO2〈ZrO2〉–Al2O3 представлена на рис. 8.
Рис. 7.
Изменение среднего размера кристаллитов твердого раствора Ce0.7Zr0.3O2 в порошках CZA-1 (1) и CZA-2 (2) в интервале 700–1200°С.
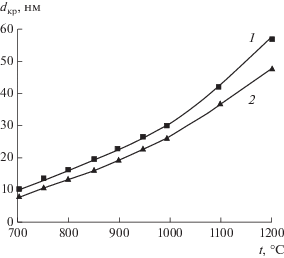
Порошки СZA-1 и СZA-2 (1000°С) исследованы методом БЭТ, изотермы низкотемпературной адсорбции–десорбции азота для порошков приведены на рис. 9. Сорбционный процесс сопровождался капиллярно-конденсационным гистерезисом, при этом для обоих порошков конденсация адсорбата начиналась при р/р0 ~ 0.45. Форма изотерм, полученных для порошков СZA-1 и СZA-2, соответствует IV типу (по классификации ИЮПАК) – изотермы с четко выраженной капиллярной конденсацией, что характерно для мезопористых материалов с размером пор от 2 до 50 нм [21]. Профиль петли гистерезиса для порошка СZA-1 (рис. 9а) с практически симметричными кривыми адсорбции и десорбции совпадает с профилем гистерезиса для капиллярной конденсации и десорбции в открытых цилиндрических порах (тип Н1 по ИЮПАК). Для изотермы адсорбции азота порошка СZA-2 (рис. 9б) характерна некоторая несимметричность по отношению к кривой десорбции, на кривой десорбции наблюдается небольшая волна с точкой перегиба при р/р0 ∼ 0.80, т.е. петля гистерезиса в данном случае занимает промежуточное положение между типами Н1 и Н3, что позволяет предполагать наличие в порошке СZA-2 не только цилиндрических, но и щелевидных пор. Эта особенность поровой структуры порошка СZA-2 связана с тем, что фаза α-Al2O3 не полностью переходит в твердый раствор Ce0.7Zr0.3O2 (рис. 5г), а поскольку частицы α‑Al2O3 имеют форму монокристаллических пластин [24], то происходит образование некоторого количества щелевидных пор.
Рис. 9.
Изотермы низкотемпературной адсорбции–десорбции азота для порошков CZA-1 (а), CZA-2 (б) после термообработки при 1000°С.
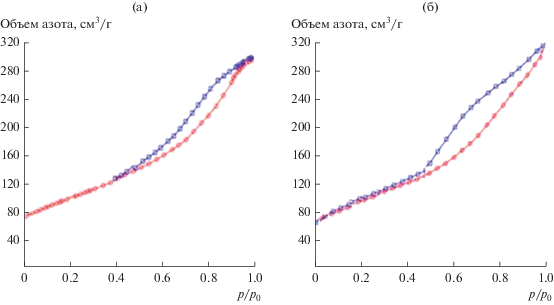
Следует отметить, что при одном и том же относительном давлении р/р0 ширина петли гистерезиса для порошка СZA-2 несколько больше, чем для порошка СZA-1, т.е. порошком СZA-2 поглощается большее количество адсорбата (N2), что указывает на его более развитую поверхность. Данный факт коррелирует с расчетами удельной поверхности порошков (табл. 2), выполненными по предельному заполнению азотом (р/р0 = 0.99) порового пространства порошков: для СZA-1 и СZA-2 92 и 105 м2/г соответственно.
Таблица 2.
Текстурные характеристики порошков в системе CeO2〈ZrO2〉–Al2O3 после термообработки при 1000°С (1 ч)
Порошок | CZA-1 | CZA-2 |
---|---|---|
Кристаллическая структура | F | F + следы α-Al2O3 |
Средний размер кристаллитов dкр, нм | 28 | 23 |
Удельная поверхность Sуд, м2/г | 92 | 105 |
Удельный объем пор Vпор, см3/г | 0.358 | 0.382 |
Средний диаметр пор Dпор, нм | 6.5 | 4.5 |
Пористая структура порошков СZA-1 и СZA-2 характеризуется мономодальным распределением пор по размерам с единственным узким максимумом в интервале 3–10 нм (рис. 10а) и в интервале 2.5–7.5 нм (рис. 10б). В табл. 2 приведены текстурные характеристики порошков в системе CeO2〈ZrO2〉–Al2O3, полученных при 1000°С (1 ч).
Рис. 10.
Дифференциальные кривые распределения пор по размерам в порошках CZA-1 (а) и CZA-2 (б) после термообработки при 1000°С.
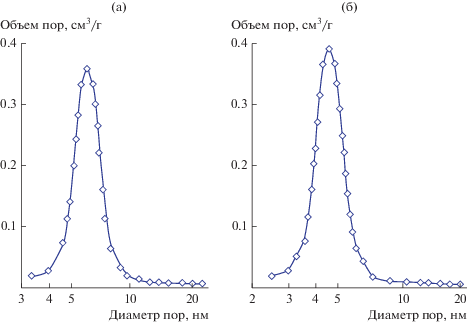
Актуальным свойством каталитической системы, используемой для трехмаршрутных катализаторов, является стабильность носителя катализатора при рабочей температуре, в связи с чем было исследовано влияние изотермического “старения” на кристаллическую структуру и дисперсность порошков СZA-1 и СZA-2. Термическую обработку порошков проводили при температуре 1000°С в течение 50 ч. В процессе обжигов внешний вид и структура исследуемых порошков не изменились. Средний размер кристаллитов, по данным РФА, увеличился до 40–50 нм в зависимости от состава порошков (рис. 11), значения удельной поверхности уменьшились на 15–20%.
ЗАКЛЮЧЕНИЕ
Цитратным золь–гель-методом синтезированы порошки-прекурсоры в системе CeO2〈ZrO2〉–Al2O3 с распределением агрегированных частиц по размерам в интервале от 50 до 180 нм, термическая обработка которых при 700 и 1000°С приводила к формированию порошков твердого раствора Ce0.7Zr0.3O2 с размером кристаллитов <30 нм. Установлено, что оксид алюминия замедляет рост кристаллитов твердого раствора Ce0.7Zr0.3O2. Методом низкотемпературной адсорбции азота определено, что порошки СZA-1 и СZA-2, синтезированные при 1000°С, имеют удельную поверхность 92 и 105 м2/г, мезопористую структуру с мономодальным распределением пор, размер которых не превышает 10 нм, удельный объем пор в порошках составляет 0.358 и 0.382 см3/г.
Установлено, что изотермическое “старение” порошков в системе CeO2〈ZrO2〉–Al2O3 при температуре 1000°С (50 ч) не приводит к существенным изменениям их кристаллической структуры, при этом размер кристаллитов твердого раствора Ce0.7Zr0.3O2 сохраняется в нанометровом диапазоне (до 55 нм), что является важным факторам при прогнозировании продолжительности службы катализатора.
Экспериментальные результаты, представленные в работе, свидетельствуют о перспективности использования нанокристаллических мезопористых порошков в системе CeO2〈ZrO2〉–Al2O3 в качестве носителей активной фазы при создании трехмаршрутных катализаторов.
Список литературы
Anderson J.A., Daley R.A., Christou S.Y., Efstathiou A.M. Regeneration of Thermally Aged Pt-Rh/CexZr1 – xO2–Al2O3 Model Three-Way Catalysts by Oxychlorination Treatments // Appl. Catal., B: Envir. 2006. V. 64. № 3–4. P. 189–200. https://doi.org/10.1016/j.apcatb.2005.12.007
Ozawa M., Okouchi T., Haneda M. Three Way Catalytic Activity of Thermally Degenerated Pt/Al2O3 and Pt/CeO2–ZrO2 Modified Al2O3 Model Catalysts // Catal. Today. 2015. V. 242. Part B. P. 329–337. https://doi.org.10.1016 /j.cattod.2014.06.013
Monte R.D., Fornasiero P., Kašpar J., Rumori P., Gubitosa G., Graziani M. Pd/Ce0.6Zr0.4O2/Al2O3 as Advanced Materials for Three-Way Catalysts: Part 1. Catalyst Characterisation, Thermal Stability and Catalytic Activity in the Reduction of NO by CO // Appl. Catal., B: Envir. 2000. V. 24. № 3–4. P. 157–167. https://doi.org/10.1016/S0926-3373(99)00102-2
Li J., Liu X., Zhan W. Preparation of High Oxygen Storage Capacity and Thermally Stable Ceria-Zirconia Solid Solution // Catal. Sci. Tech. 2016. V. 6. P. 897–907. https://doi.org/10.1039/C5CY01571E
Priya N.S., Somayaji C., Kanagaraj S. Optimization of Ce0.6Zr0.4 – xAl1.3xO2 Solid Solution Based on Oxygen Storage Capacity // J. Nanopart. Res. 2014. V. 16. № 2. P. 2214–2215. https://doi.org/10.1007/s11051-013-2214-0
Иванова А.И. Физико-химические и каталитические свойства систем на основе CeO2 // Кинетика и катализ. 2009. Т. 50. № 6. С. 831–849.
Кузнецова Т.Г., Садыков В.А. Особенности дефектной структуры метастабильных нанодисперсных диоксидов церия и циркония и материалов на их основе // Кинетика и катализ. 2008. Т. 49. № 6. С. 886–905.
Monte R., Kaspar J., Bradshaw H., Norman C. Rationale for the Development of Thermally Stable Nanostructured CeO2–ZrO2-Containing Mixed Oxides // J. Rare Earths. 2008. V. 26. № 2. P. 136–140.
Иванов В.К., Полежаева О.С., Копица Г.П., Федоров П.П., Pranzas K., Рунов В.В. Особенности высокотемпературного роста наночастиц диоксида церия // Журн. неорган. химии. 2009. Т. 54. № 11. С. 1767–1775.
Морозова Л.В., Калинина М.В., Арсентьев М.Ю., Шилова М.В. Влияние криохимической и ультразвуковой обработки на текстуру, термическое разложение ксерогелей и свойства нанокерамики в системе ZrO2〈Y2O3〉–Al2O3 // Неорган. материалы. 2017. Т. 53. № 6. С. 654–661. doi: 17060112https://doi.org/10.7868/S0002337X
Гусев А.И. Наноматериалы, наноструктуры, нанотехнологии. Изд. 2-е. М.: Наука–Физматлит, 2007. 416 с.
Альмяшева О.В., Федоров Б.А., Смирнов А.В., Гусаров В.В. Размер, морфология и структура частиц нанопорошка диоксида циркония, полученного в гидротермальных условиях // Наносистемы: физика, химия, математика. 2010. Т. 1. № 1. С. 26–37.
Pechini M. Method of Preparing Lead and Alkaline Earth Titanates and Niobates and Coating Method Using Thesame to Forma Capacitor: US. Patent № 3330697.
Tai L.W., Lessing P.A. Modifide Resin–Intermediate Processing of Perovskite Powders. Part II: Processing for Fine,Nnonagglomerated Sr-doped Lanthanum Chromite Powders // J. Mater. Res. 1992. № 7. P. 511–519.
Worayingyong A., Worayingyong A., Kangvansura P., Ausadasuk S., Praser-thdam P. The Effect of Preparation: Pechini and Schiff Base Methods, on Adsorbed Oxygen of LaCoO3 Perovskite Oxidation Catalysts // Colloids Surf., A. 2008. V. 315. № 1–3. P. 217–225.
Tani E., Yoshimura M., Somiy S. Revised Phase Diagram of the System ZrO2–CeO2 below 1400°C // J. Am. Ceram. Soc. 1983. V.66. № 7. P. 506–510. doi.org/https://doi.org/10.1111/j.1151-2916.1983.tb10591.x
Panova T.I., Arsent’ev M.Yu., Morozova L.V., Drozdova I.A. Synthesis and Investigation of the Structure of Ceramic Nanopowders in the ZrO2–CeO2–Al2O3 System // Glass Phys. Chem. 2010. V. 36. № 4. P. 470–477.
Моррисон Р., Бойд Р. Органическая химия. М.: Мир, 1974. 1132 с.
Гусев А.И., Курлов А.С. Аттестация нанокристаллических материалов по размеру частиц (зерен) // Металлофизика и новейшие технологии. 2008. Т. 30. № 5. С. 679–694.
Sing K.S.W., Everett D.H., Haul R.A.W. Reporting Physisorption Data for Gas/Solid Systems with Special Reference to the Determination of Surface Area and Porosity // Pure Appl. Chem. 1985. V. 57. P. 603–619.
Gregg S.J., Sing K.S.W. Adsorption, Surface Area and Porosity. N.Y.: Acad. Press, 1982.
Симоненко Н.П., Сахаров К.А., Симоненко Е.П., Севастьянов Г.В., Кузнецов Н.Т. Гликоль–цитратный синтез высокодисперсного цирконата лантана // Журн. неорган. химии. 2015. Т.60. № 12. С. 1588–1595. https://doi.org/10.7868/S0044457X15120235
Королев П.В., Князев А.В., Гаврилов И.Р., Гаврилов М.Р., Королев А.В. Рентгеновское и калориметрическое исследование порошковых нанокристаллических систем на основе ZrO2(Y) и Al2O3 со вторым нерастворимым компонентом // Физика твердого тела. 2012. Т. 54. Вып. 2. С. 252–257.
Иванова А.С. Оксид алюминия и системы на его основе: свойства, применение // Кинетика и катализ. 2012. Т. 53. № 4. С. 446–460.
Дополнительные материалы отсутствуют.
Инструменты
Неорганические материалы