Неорганические материалы, 2021, T. 57, № 7, стр. 762-767
Закономерности синтеза кобальтового сплава в режиме горения при дисперсном и дисперсионном модифицировании
К. В. Захаров 1, Д. Е. Андреев 1, *, В. И. Юхвид 1, Н. Ю. Хоменко 1
1 Институт структурной макрокинетики и проблем материаловедения им. А.Г. Мержанова Российской академии наук
142432 Черноголовка, Московская обл., ул. Академика Осипьяна, 8, Россия
* E-mail: ade@ism.ac.ru
Поступила в редакцию 17.02.2021
После доработки 17.03.2021
Принята к публикации 18.03.2021
Аннотация
Исследованы возможности дисперсного и дисперсионного модифицирования кобальтового сплава в режиме горения под действием центробежных сил. Шихта состояла из Co3O4, Cr2O3, Nb2O5, MoO3, Al с модифицирующими добавками карбида титана и механической смеси порошка титана и сажи. Установлено, что базовая смесь горит в широком диапазоне добавки карбида титана при нормальных условиях, наложение поля центробежных сил позволяет увеличить предел по фазоразделению с 17.5 до 20% содержания добавки. В случае дисперсионного модифицирования система имеет более высокий потенциал как по горению, так и по фазоразделению, а структурные составляющие сплава характеризуются малыми размерами, более тонкой структурой. Предложена цепочка химических реакций, протекающих при модифицировании по дисперсионному механизму, с ведущей ролью разложения Co3O4 c последующим выделением активного кислорода.
ВВЕДЕНИЕ
Характерной особенностью структуры композиционных материалов (КМ) является наличие матрицы с равномерным распределением дисперсной фазы. К материалам с подобной структурой относятся твердые и жаропрочные сплавы, а также функционально-градиентные материалы (ФГМ). В свою очередь ФГМ, представляющие собой композиты, характеризуются плавным детерминированным изменением структуры и свойств по одному из измерений. При этом выбор методики легирования является одним из важнейших вопросов материаловедения. В качестве дисперсной (упрочняющей) фазы могут выступать как MAX-фазы (тройные тугоплавкие соединения, сочетающие достоинства металла и керамики), так и фазы Лавеса (интерметаллиды, обладающие высокой прочностью и достаточной вязкостью) [1, 2]. Образование композиционных материалов, в том числе и в режиме горения, происходит посредством дисперсного или дисперсионного способов модифицирования.
При дисперсном модифицировании добавка вводится уже в готовом виде, позволяя увеличить эксплуатационную температуру материала до 0.85Тпл матрицы [3]. Преимущество состоит не только в получении высоких эксплуатационных характеристик, но и в малой энергозатратности процесса. Дисперсионное модифицирование принципиально отличается тем, что упрочняющая фаза появляется в момент синтеза композиционного материала (in situ) [4, 5]. Фаза для модифицирования выбирается из тугоплавких соединений, не растворяющихся в матричном металле вплоть до температуры плавления [6]. К такой группе относятся КМ на основе Co, Ni и Fe, легированные различными металлами и неметаллами [7–10]. Кобальтовые сплавы сохраняют прочность до температур, близких к точке плавления, ввиду того что кобальт со многими элементами образует широкие области твердых растворов. Сужение области твердых растворов при понижении температуры с образованием соединений при последующей термической обработке позволяет получать кобальтовые сплавы с желаемой структурой.
Целью настоящей работы является синтез КМ на основе кобальта в режиме горения, изучение роли дисперсного и дисперсионного модифицирования основы.
ЭКСПЕРИМЕНТАЛЬНАЯ ЧАСТЬ
В качестве объекта исследования была выбрана экзотермическая смесь на основе кобальтового сплава ХТН-61 с исключением из ее состава вольфрама для предотвращения формирования двойных карбидов системы W–Co–C (табл. 1). Модифицирование в режиме горения организовывалось двумя подходами: готовым продуктом (карбидом титана) и образующейся карбидной фазой в процессе синтеза из смеси Ti (ПТМ) и сажи (Т-804). Экзотермическая смесь для получения целевого сплава состояла из следующих реагентов: Co3O4 (“ч. д. а.”), Cr2O3 (“х. ч.”), Nb2O5 (“т. с.”), MoO3 (“ч. д. а.”), Al (АСД-1). Синтез проводили в кварцевых формах с d = 25 мм и h = 70 мм.
Таблица 1.
Расчетный химический состав КМ
Компоненты смеси | Содержание, мас. % | Компоненты сплава | Содержание, мас. % |
---|---|---|---|
Сo3O4 | 43.8 | Co | 59.0 |
Cr2O3 | 16.8 | Cr | 21.1 |
Nb2O5 | 13.0 | Nb | 16.7 |
MoO3 | 1.7 | Mo | 2.1 |
Al | 24.7 | Al | 1.1 |
Эксперименты включали в себя три серии, смеси для которых содержали базовую и модифицирующую составляющие в соотношениях: 100/0, 95/5, 90/10, 85/15 и 80/20%. Первая серия экспериментов проводилась при нормальных условиях (p = 1 атм, a = 1g) с введением в экзотермическую смесь готового карбида титана. Во второй серии также использовали готовый карбид титана, но сжигания проводили под действием перегрузки 50g на центробежной установке, величина которой задавалась по показаниям тахометра (рис. 1) исходя из следующего равенства: a = ω2R = 4π2N2R, где а – центробежное ускорение, ω – угловая скорость, R – радиус вращения реакционной формы и N – частота вращения. В третьей серии легирующая составляющая карбида титана была заменена на механическую смесь порошка титана и сажи, сжигание проводили при перегрузке 50g. С помощью программы Thermo была оценена адиабатическая температура горения, среднее значение которой составило 2200°C [11]. Продуктами горения являлись как целевой кобальтовый сплав, так и оксидный материал на основе корунда с примесями недовосстановленных исходных оксидов.
Рис. 1.
Внешний вид (а) и схема (б) центробежной установки с системой видеофиксации процесса: 1 – тахометр; 2, 3 и 4 – ременная передача; 5 – скользящие контакты; 6 – тоководы; 7 – реакционная форма со смесью; 8 – защитный экран с фотофильтром; 9 – видеокамера.
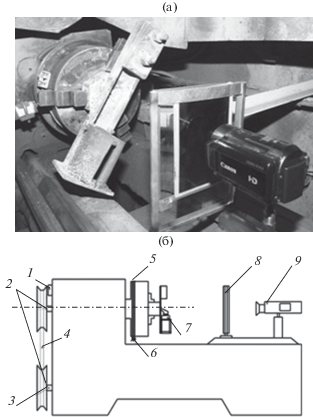
Характеристики процесса горения – скорость горения (u), разброс продуктов горения (η1) и выход целевого продукта (η2) – рассчитывали по формулам:
Для исследования химического состава и структуры продуктов синтеза использовали автоэмиссионный сканирующий электронный микроскоп Carl Zeiss Ultra Plus на базе Ultra 55. Фазовый состав конечных продуктов горения определяли на дифрактометре ДРОН-3М, в качестве источника излучения использовалась рентгеновская трубка типа БСВ–27 с медным анодом (λ = = 1.54178 Ǻ).
РЕЗУЛЬТАТЫ И ОБСУЖДЕНИЕ
С увеличением содержания карбида титана в экзотермический смеси процесс характеризовался снижением скорости горения с 0.55 до 0.4 см/с для нормальных условий и аналогичной тенденцией при перегрузке a = 50g – с 7.8 до 0.7 см/с. При достижении содержания TiC 15% был достигнут предел по фазоразделению при a = 1g; в случае наложения поля центробежных сил предел по фазоразделению был сдвинут в область бóльших концентраций TiC. В интервале содержания TiC от 5 до 10% процесс сопровождался увеличенным разбросом продуктов горения в обоих случаях (рис. 2 и 3).
Рис. 2.
Зависимости скорости горения (u), разброса (η1) и выхода целевого продукта (η2) от содержания TiC в экзотермической смеси: p = 1 атм, a = 1g.
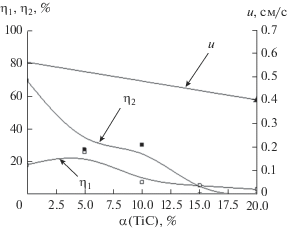
Рис. 3.
Зависимости скорости горения (u), разброса (η1) и выхода целевого продукта (η2) от содержания TiC в экзотермической смеси: a = 50g.
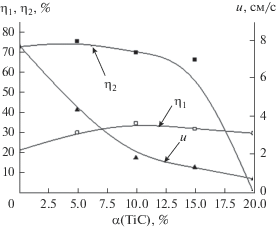
На рис. 4 представлены результаты для третей серии экспериментов, в рамках которой наблюдается провал по выходу целевого продукта (η2), коррелирующий с увеличенным разбросом в окрестности α = 5%. Скорость горения с ростом α снижается, пределы горения и фазоразделения сдвигаются в область высоких концентраций α, система имеет больший потенциал по введению модифицирующей составляющей – смеси Ti + C.
Рис. 4.
Зависимости скорости горения (u), разброса (η1) и выхода целевого продукта (η2) от содержания Ti и сажи в экзотермической смеси: a = 50g.
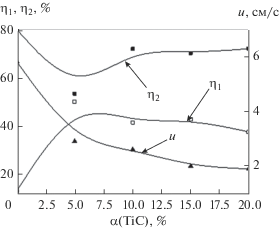
КМ при α = 0% в случае как a = 1g, так и a = 50g представляет собой сплав на основе интерметаллического соединения Co3Nb и твердого раствора CoCr (рис. 5). В зависимости от метода модифицирования и величины α меняется состав целевого продукта. В случае дисперсного модифицирования карбид титана идет на формирование титан-ниобиевого карбида, титан-хромового карбида, а также их сложного карбида. С ростом α в целевом продукте фиксируется повышенное содержание фазы Al2O3, свидетельствующее о неполном фазоразделении металлоподобной и оксидной фаз. При дисперсионном модифицировании целевой продукт представляет собой КМ на основе хром-кобальтового алюминида, индивидуальных карбидов Cr и Co, а также титан-ниобиевого карбида. Фазы на основе молибдена при дисперсном и дисперсионном модифицировании не зафиксированы ввиду его малых концентраций (рис. 6).
Рис. 6.
Дифрактограммы целевого продукта: а – дисперсное, б – дисперсионное модифицирование: α = = 10%, a = 50g.
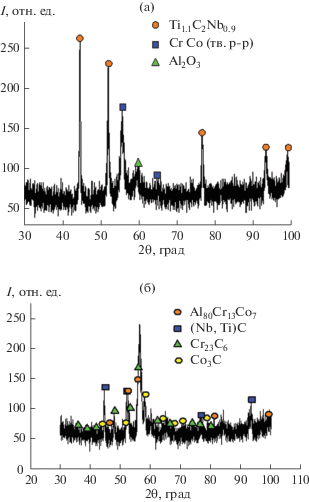
На рис. 7 представлены характерные микроструктуры для образцов, полученных при дисперсном (рис. 7а, 7б) и дисперсионном модифицировании (рис. 7в) с α = 10%. В случае дисперсионного модифицирования образцы характеризуются более тонкой структурой эвтектики в пределах блоков зерен по сравнению с дисперсным, преимущественно состоящей из фаз на основе Co, Сr и титан-ниобиевого карбида. Наибольшая концентрация остаточного кислорода в образцах, по результатам энергодисперсионного анализа, была зафиксирована для целевого продукта при дисперсном модифицировании (табл. 2).
Рис. 7.
Микроструктура целевого продукта при α = 10%: а, б – дисперсное модифицирование, a = 1g (а), 50g (б); в – дисперсионное модифицирование, a = 50g.
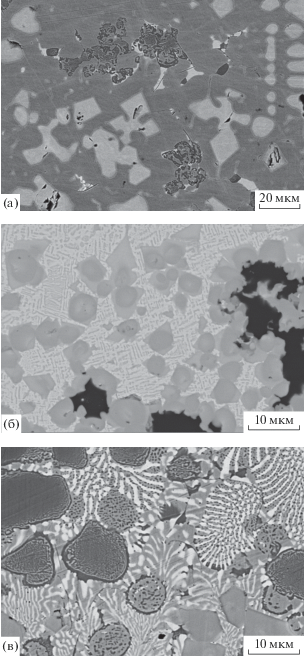
Таблица 2.
Локальный химический состав целевого продукта
Элемент | C, мас. % | ||
---|---|---|---|
дисперсное модифицирование | дисперсионное модифицирование | ||
a = 1g | a = 50g | a = 50g | |
C | 14.6 | 12.9 | 10.6 |
O | 0.6 | 0.9 | 0.1 |
Al | 3.9 | 2.5 | 2.4 |
Ti | 7.3 | 22.8 | 8.4 |
Cr | 14.7 | 16.1 | 14.8 |
Co | 40.3 | 27.8 | 45.9 |
Nb | 17.0 | 15.9 | 15.6 |
Mo | 1.6 | 1.1 | 2.2 |
Анализируя экспериментальные результаты по горению экзотермических смесей при дисперсионном модифицировании с учетом термодинамического расчета и фазового состава продуктов горения, можно сформировать схему химического превращения в волне горения:
(1)
$\begin{gathered} {{{\text{C}}{{{\text{o}}}_{{\text{3}}}}{{{\text{O}}}_{{\text{4}}}}} \mathord{\left/ {\vphantom {{{\text{C}}{{{\text{o}}}_{{\text{3}}}}{{{\text{O}}}_{{\text{4}}}}} {{{{\text{C}}{{{\text{r}}}_{{\text{2}}}}{{{\text{O}}}_{{\text{3}}}}} \mathord{\left/ {\vphantom {{{\text{C}}{{{\text{r}}}_{{\text{2}}}}{{{\text{O}}}_{{\text{3}}}}} {{{{\text{N}}{{{\text{b}}}_{{\text{2}}}}{{{\text{O}}}_{5}}} \mathord{\left/ {\vphantom {{{\text{N}}{{{\text{b}}}_{{\text{2}}}}{{{\text{O}}}_{5}}} {{\text{Mo}}{{{\text{O}}}_{{\text{3}}}}}}} \right. \kern-0em} {{\text{Mo}}{{{\text{O}}}_{{\text{3}}}}}}}}} \right. \kern-0em} {{{{\text{N}}{{{\text{b}}}_{{\text{2}}}}{{{\text{O}}}_{5}}} \mathord{\left/ {\vphantom {{{\text{N}}{{{\text{b}}}_{{\text{2}}}}{{{\text{O}}}_{5}}} {{\text{Mo}}{{{\text{O}}}_{{\text{3}}}}}}} \right. \kern-0em} {{\text{Mo}}{{{\text{O}}}_{{\text{3}}}}}}}}}}} \right. \kern-0em} {{{{\text{C}}{{{\text{r}}}_{{\text{2}}}}{{{\text{O}}}_{{\text{3}}}}} \mathord{\left/ {\vphantom {{{\text{C}}{{{\text{r}}}_{{\text{2}}}}{{{\text{O}}}_{{\text{3}}}}} {{{{\text{N}}{{{\text{b}}}_{{\text{2}}}}{{{\text{O}}}_{5}}} \mathord{\left/ {\vphantom {{{\text{N}}{{{\text{b}}}_{{\text{2}}}}{{{\text{O}}}_{5}}} {{\text{Mo}}{{{\text{O}}}_{{\text{3}}}}}}} \right. \kern-0em} {{\text{Mo}}{{{\text{O}}}_{{\text{3}}}}}}}}} \right. \kern-0em} {{{{\text{N}}{{{\text{b}}}_{{\text{2}}}}{{{\text{O}}}_{5}}} \mathord{\left/ {\vphantom {{{\text{N}}{{{\text{b}}}_{{\text{2}}}}{{{\text{O}}}_{5}}} {{\text{Mo}}{{{\text{O}}}_{{\text{3}}}}}}} \right. \kern-0em} {{\text{Mo}}{{{\text{O}}}_{{\text{3}}}}}}}}}} + {\text{Al}} + {\text{Ti}} + {\text{С}} \to \\ \to \,\,{\text{Co}}{\kern 1pt} --{\kern 1pt} {\text{Cr}}{\kern 1pt} --{\kern 1pt} {\text{Nb}}{\kern 1pt} --{\kern 1pt} {\text{Mo}}{\kern 1pt} --{\kern 1pt} {\text{Ti}}{\kern 1pt} --{\kern 1pt} {\text{C}}{\kern 1pt} --{\kern 1pt} {\text{Al}} + {\text{A}}{{{\text{l}}}_{{\text{2}}}}{{{\text{O}}}_{3}} + gas, \\ \end{gathered} $Определяющими кинетику процесса с учетом концентраций исходных веществ будут химические реакции алюмотермического восстановления оксидов Co, Nb и Cr. Конкуренцию алюминию в восстановительных процессах может составить титан, который будет расходоваться не только на формирование сложных карбидов. Помимо экзотермических реакций, могут протекать и эндотермические с участием углерода. Ведущей реакцией будет разложение Co3O4 до CoO выше температуры плавления алюминия при t = 900°C с последующим взаимодействием с Al
(2)
$2{\text{C}}{{{\text{o}}}_{{\text{3}}}}{{{\text{O}}}_{4}} \to 6{\text{CoO}} + {{{\text{O}}}_{2}},$(3)
$4{\text{Al}} + 4{{{\text{O}}}_{2}} \to 2{\text{A}}{{{\text{l}}}_{{\text{2}}}}{{{\text{O}}}_{3}}.$Выделившийся кислород при разложении Co3O4 также может вступить в реакцию с титаном, создавая конкуренцию алюминию
Далее протекает ряд параллельных и последовательных реакций
(5)
${\text{CoO}} + {\text{Al}} \to {\text{Co}} + {\text{A}}{{{\text{l}}}_{{\text{2}}}}{{{\text{O}}}_{{\text{3}}}},$(6)
${\text{N}}{{{\text{b}}}_{{\text{2}}}}{{{\text{O}}}_{5}} + {\text{Al}} \to {\text{Nb}} + {\text{A}}{{{\text{l}}}_{{\text{2}}}}{{{\text{O}}}_{3}},$(7)
${\text{C}}{{{\text{r}}}_{{\text{2}}}}{{{\text{O}}}_{3}} + {\text{Al}} \to {\text{Cr}} + {\text{A}}{{{\text{l}}}_{{\text{2}}}}{{{\text{O}}}_{3}}.$Пренебрегая эндотермическими реакциями взаимодействия углерода с исходными оксидами и промежуточными соединениями ввиду его неучастия в восстановительных реакциях, мы полагаем, что углерод расходуется лишь на формирование карбидных соединений
(8)
$\begin{gathered} {\text{Co}}{\kern 1pt} --{\text{Cr}}{\kern 1pt} --{\kern 1pt} {\text{Nb}}{\kern 1pt} --{\kern 1pt} {\text{Ti}}{\kern 1pt} --{\kern 1pt} {\text{Mo}}{\kern 1pt} --{\kern 1pt} {\text{Al}} + {\text{C}} \to \\ \to \,\,{\text{Co}}{\kern 1pt} --{\kern 1pt} {\text{Cr}}{\kern 1pt} --{\kern 1pt} {\text{Nb}}{\kern 1pt} --{\kern 1pt} {\text{Ti}}{\kern 1pt} --{\kern 1pt} {\text{Mo}}{\kern 1pt} --{\kern 1pt} {\text{C}}{\kern 1pt} --{\kern 1pt} {\text{Al}}. \\ \end{gathered} $Восстановленные металлы и Al2O3 в волне горения образуют двухфазный расплав, в металлической фазе которого происходит растворение остаточного Al, образовавшегося при недовосстановлении Cr2O3 ввиду невысокой температуры горения и низкой конверсионной способности перехода оксида хрома в хром. Образующиеся при горении газообразные продукты, CO, низшие (Al2O, CrO) и пары́ металлов (Al и Co) образуют пузырьки и покидают расплав под действием Архимедовой силы, что приводит к разбросу продуктов горения.
ЗАКЛЮЧЕНИЕ
При синтезе кобальтового сплава в режиме горения как при дисперсном модифицировании карбидом титана, так и при дисперсионном механической смесью на основе титана и сажи получен КМ с желаемым набором фаз и химическим составом. Использование центробежных сил позволяет расширить пределы горения и фазоразделения для целевого продукта. Разработана химическая схема синтеза кобальтового сплава при дисперсионном модифицировании с учетом термодинамики и анализа продуктов синтеза. Синтезированный сплав при данном подходе имеет перспективы для применения в установках, работающих при высоких температурах.
Список литературы
Rabadia C.D., Liu Y.J., Chen L.Y., Jawed S.F., Wang L.Q., Sun H., Zhang L.C. Deformation and Strength Characteristics of Laves Phases Intitanium Alloys // Mater. Des. 2019. V. 179. https://doi.org/10.1016/j.matdes.2019.107891
Горшков В.А., Милосердов П.А., Лугинина М.А., Сачкова Н.В., Беликова А.Ф. Высокотемпературный синтез литого материала с максимальным содержанием MAX-фазы Cr2AlC // Неорган. материалы. 2017. Т. 53. № 3. С. 260–266. https://doi.org/10.31857/S0002337X20030045
Ловшенко Ф.Г., Ловшенко Г.Ф. Критерии выбора легирующих компонентов и базовых композиций для производства механически легированных дисперсно-упрочненных материалов на основе металлов // Наука и техника. 2016. Т. 15. № 3. С. 173–182. https://doi.org/10.21122/2227-1031-2016-15-3-173-182
Аникеев А.Н., Бигеев А.В., Гордеев Е.Н., Чуманов В.И., Чуманов И.В. О возможности введения твердых тугоплавких частиц при получении трубной заготовки методом центробежного литья // Вестн. ЮУрГУ. Сер.: металлургия. 2009. № 39(169). С. 24–27.
Портной К.И. Дисперсноупрочненные материалы. М.: Металлургия, 1974. 368 с.
Orowan E. Condition for Dislocation Passage of Precipitation // Proc. Symp. on Intern Stresses in Mettals. 1948. P. 451–454.
Reed R.C. The Superalloys Fundamentals and Applications. N.Y.: Cambridge Univ. Press, 2008.
Григорьев С.Н., Тарасова Т.В., Назаров А.П. Влияние термообработки на структурно-фазовый состав и свойства жаропрочных кобальтовых сплавов, полученных методом селективного лазерного плавления // Перспективные материалы. 2014. № 7. С. 73–80.
Давыдов Д.И., Казанцева Н.В., Ежов И.В., Попов Н.А. Исследование структурно-фазовых превращений в кобальтовых жаропрочных сплавах // Тезисы междунар. междисциплинарного симп. “Иерархические материалы: разработка приложения для новых технологий и надежных конструкций”. 2020. С. 253–254.
Sato J., Omori T., Oikawa K., Ohnuma I., Kainuma R., Ishida K. Cobalt-Base High-Temperature Alloys // Science. 2006. V. 7. P. 90–91.
Shiryaev A.A. // Int. J. Self-Propag. High-Temp. Synth. 1995. V. 4. № 4. P. 351.
Дополнительные материалы отсутствуют.
Инструменты
Неорганические материалы