Неорганические материалы, 2021, T. 57, № 8, стр. 901-909
Влияние условий горячего прессования на микроструктуру и оптические свойства композиционной керамики MgO–Y2O3
Д. А. Пермин 1, 2, *, А. В. Беляев 1, В. А. Кошкин 1, С. С. Балабанов 1, М. С. Болдин 2, И. В. Ладенков 3, И. Г. Федотова 2
1 Институт химии высокочистых веществ им. Г.Г. Девятых Российской академии наук
603137 Нижний Новгород, ул. Тропинина, 49, Россия
2 Нижегородский государственный университет им. Н.И. Лобачевского
603950 Нижний Новгород, пр. Гагарина, 23, Россия
3 АО НПП “Салют”
603950 Нижний Новгород, ул. Ларина, 7, Россия
* E-mail: permin@ihps-nnov.ru
Поступила в редакцию 25.02.2021
После доработки 29.03.2021
Принята к публикации 31.03.2021
Аннотация
Исследовано влияние условий горячего прессования на микроструктуру и оптические характеристики композиционной керамики Y2O3–MgO. Приведены режимы горячего прессования, оптимальные для минимизации рассеяния ИК-излучения 4–5 мкм как на остаточных порах, так и кристаллитах композита. Показано, что отжиг керамик Y2O3–MgO на воздухе при температуре 1100°С в течение 5 ч приводит к исчезновению полосы поглощения с максимумом ~4.94 мкм, связанной с захватом в остаточных порах оксида углерода (II).
ВВЕДЕНИЕ
В последнее десятилетие наблюдается значительный прогресс в разработке и исследовании новых композиционных ИК-материалов для использования в экстремальных температурных условиях и при интенсивных нагрузках, например в аэрокосмической сфере. Согласно данным [1], композиционная керамика Y2O3–MgO выгодно отличается сочетанием оптических, механических и термических свойств от широко применяемых в настоящее время однофазных материалов, таких как ZnSe, ZnS, MgAl2O4, ZnAl2O4 [2–4]. Ключевой задачей для обеспечения высоких микротвердости, трещиностойкости и прозрачности в области 4–5 мкм (одном из окон прозрачности атмосферы) является формирование беспористой структуры композита с однородным распределением субмикронных зерен MgO и Y2O3 по объему образца.
Существуют два основных подхода к получению высокопрозрачной ИК-керамики Y2O3–MgO: предварительное свободное спекание в вакууме с последующим горячим изостатическим прессованием [5] и спекание с приложением внешнего одноосного давления, реализуемое в методах искрового плазменного спекания (ИПС) [6–18] и горячего прессования (ГП) [19–24]. Перспективным методом консолидации керамики Y2O3–MgO также является спекание в условиях микроволнового нагрева [25–27]. Однако толщина ИК-прозрачных образцов Y2O3–MgO, полученных данным методом, в настоящее время ограничена ~0.5 мм и дальнейшее ее увеличение, на наш взгляд, сопряжено со значительными трудностями.
Первый подход к получению композита Y2O3–MgO включает в себя прессование исходных порошков в стальных пресс-формах, холодное изостатическое прессование, предварительный обжиг компакта на воздухе для удаления органических связующих, вакуумное спекание и горячее изостатическое прессование. Второй подход – ГП или ИПС – выгодно отличает меньшее количество технологических операций. Наибольшая производительность консолидации керамики Y2O3–MgO обеспечивается при использовании метода ИПС за счет высоких скоростей нагрева и специфики воздействия электрических полей на уплотняемый компакт. Однако интенсивный нагрев приводит к закрытию пористости до полного удаления адсорбированных газов с поверхности нанопорошков, а низкие значения электропроводности и теплопроводности керамик и сильная зависимость этих параметров от температуры обуславливают возникновение градиента температуры внутри спекаемой заготовки, что затрудняет создание композита с однородной микроструктурой. Лучшие результаты по светопропусканию композита Y2O3–MgO достигнуты к настоящему времени при использовании ГП.
Оксиды иттрия и магния, особенно в высокодисперсном состоянии, неизбежно сорбируют и химически связывают воду и углекислый газ из атмосферы, образуя карбонаты и гидроксиды. В ряде работ рассматриваются вопросы влияния газообразующих примесей на оптическое пропускание керамики Y2O3–MgO [12]. Разложение соединений магния и иттрия приводит к формированию в спекаемом образце пор, обусловливающих повышенное рассеяние ИК-излучения. Динамика удаления летучих соединений при ИПС и ГП является одним из важнейших параметров для достижения высокой оптической прозрачности материала. Режимы консолидации подбираются с таким расчетом, чтобы адсорбированные газы и летучие спекающие добавки максимально удалились на стадии открытой пористости. Скорость нагрева и температура приложения одноосного давления к компакту влияют на эволюцию системы пор и, соответственно, динамику удаления летучих соединений. Эти параметры достаточно подробно исследованы, например, при получении керамик шпинелей, установлено их влияние на механические и оптические свойства материалов [4, 28–30]. Аналогичных данных для композиционной керамики Y2O3–MgO в доступной литературе нами не обнаружено.
Целью данной работы является исследование влияния температуры спекания и момента приложения одноосного давления на микроструктуру и пропускание в инфракрасном диапазоне длин волн композиционной керамики Y2O3–MgO.
ЭКСПЕРИМЕНТАЛЬНАЯ ЧАСТЬ
Для получения исходных порошков Y2O3–MgO была использована глицин-нитратная методика самораспространяющегося высокотемпературного синтеза (СВС), подробно описанная в [15, 28]. Нитратные соли иттрия и магния получали растворением их оксидов в азотной кислоте. В качестве восстановителя (горючего) использовали аминоуксусную кислоту (глицин). Согласно данным [5], оптимальное объемное соотношение оксидов иттрия и магния в ИК-прозрачной керамике составляет 50 : 50%, что примерно соответствует 60 : 40 мас. %. Растворы нитратов иттрия и магния смешивали в заданном соотношении и к полученному раствору добавляли глицин исходя из стехиометрии реакций
Полученный раствор упаривали при 110°С, затем для инициирования СВС кварцевую колбу с прекурсором помещали в печь, предварительно нагретую до 500°С. В результате сгорания происходило образование мягкой пены, состоящей из наноразмерных порошков Y2O3–MgO. После синтеза порошки дополнительно отжигали на воздухе в муфельной печи при температуре 800°С в течение 5 ч.
Рентгенофазовый анализ СВС-порошков выполняли на дифрактометре Shimadzu XRD-7000 (Shimadzu, Япония) в диапазоне углов 2θ = 20°–70°. Шаг сканирования по 2θ составлял 0.04°, время экспозиции 3 с. Средний размер (DXRD) кристаллитов Y2O3 и MgO был рассчитан с помощью уравнения Шеррера DXRD = 0.9λ/(βcosθ), где λ – длина волны излучения CuKα (λ = 0.154 нм), а β – ширина на полувысоте дифракционного пика при угле Брэгга θ.
Перед горячим прессованием отожженные порошки компактировали в пресс-форме из нержавеющей стали диаметром 15 мм под давлением 40 МПа. Сформированные компакты консолидировали ГП в вакууме в графитовой пресс-форме при температурах 1300–1600°С и одноосном давлении 50 МПа на оборудовании собственного производства. Компакты были изолированы графитовой бумагой, чтобы уменьшить взаимодействие материала пресс-формы с керамическим образцом. Нагрев осуществляли графитовыми нагревателями со скоростью 20°С/мин; остаточное давление в камере составляло не более 10 Па. Режим нагрева включал двадцатиминутную изотермическую выдержку при 800°С для десорбции влаги и углекислого газа, подъем до температуры спекания, выдержку в течение 60 мин и свободное охлаждение. Начальное одноосное давление на компакт составляло 3 МПа. Увеличение одноосного давления до максимального проводили со скоростью 1 МПа/мин с момента достижения температуры компакта 800, 900 и 1000°C. Для удаления кислородных вакансий и возможных примесей неокисленного углерода образцы дополнительно отжигали на воздухе при 1100°C в течение 5 ч в муфельной печи. Затем образцы шлифовали и полировали алмазными суспензиями с обеих сторон до толщины 1.5 мм. Инфракрасные спектры композиционной керамики Y2O3–MgO регистрировали с помощью ИК-Фурье-спектрометра ФТ-801 (СИМЕКС, Россия).
Плотность спеченных образцов (ρ) измеряли гидростатическим взвешиванием в дистиллированной воде на весах Sartorius CPA (Sartorius, Германия) с точностью 0.005 г/см3, что составляет 0.1% от теоретической плотности композита. Теоретическую плотность композита Y2O3–MgO (4.307 г/см3) рассчитывали аддитивным методом, предполагая плотности оксидов иттрия и магния 5.03 и 3.58 г/см3 соответственно.
Морфологию синтезированных порошков и микроструктуру спеченной керамики исследовали с помощью растрового электронного микроскопа (РЭМ) Auriga CrossBeam (Carl Zeiss, Германия) при напряжении ускоряющего пучка EHT = = 3 кэВ с детектором вторичных электронов. Средний размер зерен оценивался путем измерения ширины не менее 200 зерен.
РЕЗУЛЬТАТЫ И ОБСУЖДЕНИЕ
Для изготовления беспористой керамики Y2O3–MgO требуются слабоагломерированные нанопорошки с высокими химической и фазовой чистотой, а также однородным распределением компонентов. Как показано в наших работах [15, 28] и в работах других групп [10, 16, 21–24], одним из лучших методов получения таких порошков является СВС с использованием глицина в качестве горючего и нитратов металлов в качестве окислителя.
Полученные СВС-порошки Y2O3–MgO имеют характерную для этого метода морфологию, обусловленную вспениванием расплавленной массы глицина и нитратов металлов выделяющимися в ходе горения газами (рис. 1). Порошки были однородными, какой-либо сегрегации в них не наблюдалось. Быстрое протекание реакции СВС и большой объем газообразных продуктов предотвращают спекание порошка, поэтому пена рассыпается практически до первичных частиц при незначительном механическом воздействии.
Рентгенограмма порошка Y2O3–MgO, дополнительно прокаленного при 800°C в течение 5 ч для удаления возможных углеродсодержащих примесей, показана на рис. 2. Все наблюдаемые рефлексы на рентгенограмме относятся к кубическим фазам Y2O3 (пр. гр. Ia, карточка PDF #00-041-1105) и MgO (пр. гр. $Fm\bar {3}m,$ карточка PDF #00-004-0829). Средний размер кристаллитов (DXRD) Y2O3 и MgO составил 13 и 12 нм соответственно.
Оксиды иттрия и магния имеют практически нулевую взаимную растворимость, что существенно затрудняет диффузию металлов во время спекания и сдерживает рост зерен. За счет этого становится возможным получение практически беспористой керамики Y2O3–MgO с субмикронными размерами зерен. На рис. 3 приведены микроснимки поверхности разлома керамических образцов Y2O3–MgO, полученных при различных условиях ГП СВС-порошков, а в табл. 1 дополнительно представлены их плотность, средние размеры зерен и оптическое пропускание. Разница в атомных массах оксидов обеспечивает хорошую контрастность на РЭМ-снимках темных зерен оксида магния и светлых оксида иттрия. Можно видеть, что структура всех керамических образцов плотная и однородная, однако в композитах, полученных при температуре спекания 1300°С (см. рис. 3a, 3г, 3ж), наблюдаются крупные остаточные поры, размер которых превышает средние размеры зерен. Плотность таких образцов заметно ниже теоретической. При температурах ГП 1400°С и более плотность композита в пределах чувствительности используемого метода гидростатического взвешивания не отличается от теоретического предела. Средние размеры зерен композита линейно возрастают с увеличением температуры горячего прессования и не зависят от момента приложения одноосного давления.
Рис. 3.
РЭМ-изображения сколов образцов Y2O3–MgO, полученных при разных температурах начала приложения одноосного давления/спекания: a – 800°С/1300°С, б – 800°С/1400°С, в – 800°С/1500°С, г – 900°С/1300°С, д – 900°С/ 1400°С, е – 900°С/1450°С, ж – 1000°С/1300°С, з – 1000°С/1400°С, и – 1000°С/1600°С.
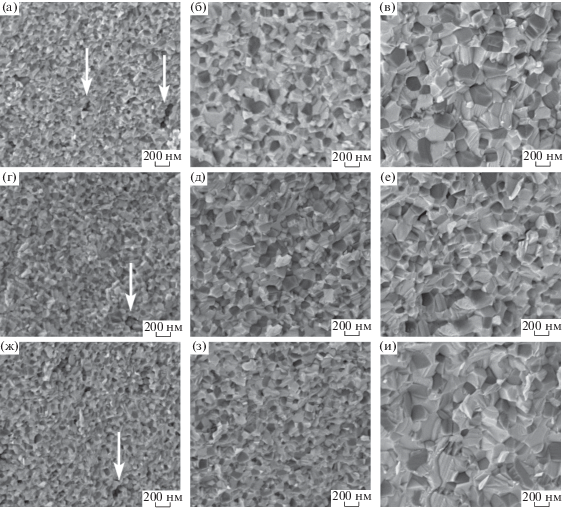
Таблица 1.
Условия ГП, микроструктура и оптические свойства композитов Y2O3–MgO
Температура начала приложения одноосного давления, °C | Температура ГП, °C | Плотность, г/см3 (%) | Средние размеры зерен, нм | Пропускание на 2.5 мкм, % | Пропускание на 6 мкм, % |
---|---|---|---|---|---|
800 | 1300 | 4.275 (99.4) | 140 | 1 | 46 |
1400 | 4.298 (99.9) | 174 | 66 | 77 | |
1450 | 4.297 (99.9) | 196 | 68 | 78 | |
1500 | 4.301 (>99.9) | 245 | 51 | 75 | |
900 | 1300 | 4.246 (98.7) | 147 | 2 | 26 |
1350 | 4.295 (99.8) | 156 | 12 | 68 | |
1400 | 4.305 (>99.9) | 187 | 68 | 78 | |
1450 | 4.307 (>99.9) | 205 | 69 | 78 | |
1000 | 1300 | 4.232 (98.4) | 127 | 1 | 22 |
1400 | 4.298 (99.9) | 170 | 61 | 82 | |
1450 | 4.301 (>99.9) | 200 | 61 | 82 | |
1550 | 4.299 (99.9) | 257 | 31 | 81 | |
1600 | 4.305 (>99.9) | 300 | 7 | 79 |
В композитах с увеличением температуры ГП происходит постепенное снижение рассеяния на остаточных порах и увеличение рассеяния за счет роста средних размеров зерен. На рис. 4 представлены спектры ИК-пропускания полученных керамических образцов Y2O3–MgO. Независимо от температуры начала приложения одноосного давления наибольшее пропускание в области 4–5 мкм (~80%) имеют образцы, полученные при температурах ГП 1400–1450°С. Этой температуры достаточно для достижения полной плотности, но при этом средние размеры зерен более чем в 20 раз меньше длины волны проходящего излучения (λ). Существенное, в два раза, снижение пропускания наблюдается при длинах волн около 2 мкм, когда средний размер зерен становится ~λ/10. Увеличение температуры ГП до 1500°С и выше практически не сказывается на пропускании в районе 6 мкм, однако приводит к снижению пропускания в области целевых длин волн 4–5 мкм.
Рис. 4.
ИК-спектры образцов Y2O3–MgO, полученных при температурах начала приложения одноосного давления 800 (а), 900 (б), 1000°C (в).
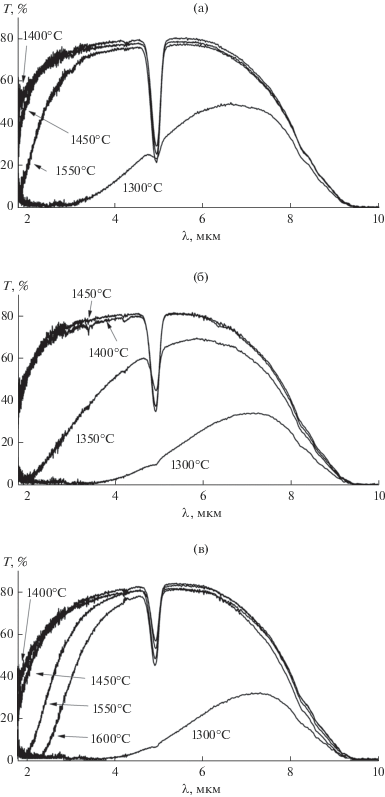
На рис. 5a представлены спектры пропускания композитов Y2O3–MgO, полученных ГП при 1450°С, в зависимости от температуры начала приложения одноосного давления. Видно, что при практически идентичном пропускании на длине волны 4 мкм интенсивности линии поглощения с максимумом в области 4.94 мкм существенно различаются. Данное поглощение обусловлено наличием оксида углерода (II) в остаточных порах в керамике. Источником углерода в композите Y2O3–MgO являются как материалы горячей зоны пресса, так и карбонаты магния и иттрия, образующиеся при контакте исходных нанопорошков оксидов с атмосферой. Увеличение температуры начала приложения одноосного давления обеспечивает более полное разложение карбонатов, а также снижает общий объем пор за счет начала спекания, уменьшая таким образом количество газов, захватываемых при формировании закрытой пористости. Дальнейшее увеличение температуры начала приложения одноосного давления приводит к консолидации пор, самые большие из которых становятся термодинамически равновесными, не удаляются при ГП и снижают пропускание композита во всем диапазоне его прозрачности. Однако полоса поглощения CO попадает в целевой диапазон длин волн 4–5 мкм, и даже при оптимальной температуре начала приложения одноосного давления 1000°С поглощается около 20% излучения 4.94 мкм при толщине образца 1.5 мм.
Рис. 5.
ИК-спектры образцов Y2O3–MgO, полученных ГП при 1450°С с температурами начала приложения одноосного давления от 800 до 1000°С (a); ИК-спектры образца Y2O3–MgO после ГП при 1400°С (1), после дополнительного прокаливания на воздухе при 1100°С в течение 5 ч (2) (б).
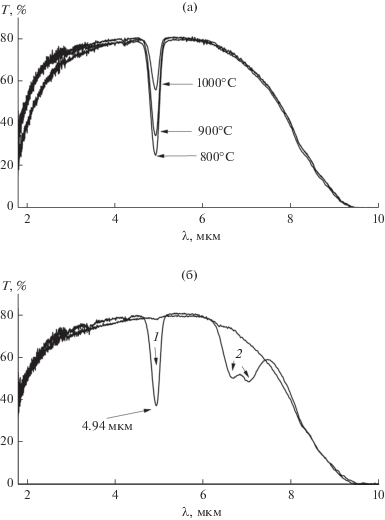
В работах [10, 16, 17] для снижения интенсивности полосы поглощения на 4.94 мкм порошки предварительно прокаливали на воздухе при 1000°С в течение 4 ч. Это приводило к более полному разложению карбонатов, значительному снижению дисперсности порошков и, следовательно, уменьшению скорости поглощения ими углекислого газа из атмосферы. Кроме этого, увеличивалась плотность прессовки и уменьшался захват остаточных газов при закрытии пористости. Однако предварительное прокаливание порошков при высоких температурах приводит к снижению их спекаемости, и пропускание полученных образцов не превышало 90% от теоретического. В работе [24] предложено использовать спекающую добавку фторида лития (до 0.5 мас. %) для уменьшения содержания в керамике углеродсодержащих примесей. Фториды образуют с ними летучие соединения типа CxFy, которые эффективно удаляются на стадии открытой пористости. Однако известно [4], что использование фторида лития при горячем прессовании приводит к значительному росту среднего размера зерна спекаемого материала. У однофазных материалов это не отражается на общем пропускании, но для композита Y2O3–MgO сохранение средних размеров зерен на уровне 200 нм и менее является критически важным для его практического использования в ИК-технике.
Представляется, что наиболее рациональным решением для устранения линии поглощения около 4.94 мкм в композите после ГП является его высокотемпературный отжиг на воздухе. Как видно из рис. 5б, после прокаливания керамики при температуре 1100°С в течение 5 ч оксид углерода(II) полностью окисляется; образовавшийся углекислый газ при остывании образца взаимодействует с оксидами иттрия и/или магния с формированием соответствующих карбонатов. Об этом свидетельствует появление после отжига двух перекрывающихся полос поглощения в области 7 мкм, которые могут быть отнесены как к карбонату магния, так и к карбонату иттрия. Данные полосы не попадают в окна прозрачности атмосферы, поэтому не влияют на функциональные характеристики композита для большинства перспективных применений.
ЗАКЛЮЧЕНИЕ
Исследовано влияние условий ГП нанопорошков Y2O3–MgO на микроструктуру и оптические характеристики получаемых материалов. Температуры 1400–1450°С оптимальны для получения композитов с плотностью более 99.9% от теоретической и средними размерами зерен около 200 нм. Более низкие температуры недостаточны для достижения полной плотности керамики, а более высокие приводят к увеличению средних размеров зерен. В обоих случаях снижается пропускание композитом излучения в ИК-области за счет повышенного рассеяния.
Показано, что увеличение температуры начала приложения одноосного давления к компакту с 800 до 1000°С в несколько раз снижает интенсивность полосы поглощения с максимумом ~4.94 мкм, относящейся к оксиду углерода (II), захваченному остаточными порами. Отжиг образцов на воздухе при температуре 1100°С в течение 5 ч позволяет полностью окислить оксид углерода (II) и обеспечить пропускание композита на уровне 79% в области целевых длин волн 4–5 мкм.
Список литературы
Jiang D.T., Mukherjee A.K. Spark Plasma Sintering of an Infrared-Transparent Y2O3–MgO Nanocomposite // J. Am. Ceram. Soc. 2010. V. 93 № 3. P. 769–773. https://doi.org/10.1111/j.1551-2916.2009.03444.x
Goldstein A., Krell A. Transparent Ceramics at 50: Progress Made and Further Prospects // J. Am. Ceram. Soc. 2016. V. 99. № 10. P. 3173–3197. https://doi.org/10.1111/jace.14553
Belyaev A.V., Lelet M.I., Kirillova N.I., Khamaletdinova N.M., Boldin M.S., Murashov A.A., Balabanov S.S. Sol-Gel Synthesis and Characterization of ZnAl2O4 Powders for Transparent Ceramics // Ceram. Int. 2019. V. 45. № 4. P. 4835–4839. https://doi.org/10.1016/j.ceramint.2018.11.179
Balabanov S.S., Belyaev A.V., Novikova A.V., Permin D.A., Rostokina E.Ye., Yavetskiy R.P. Densification Peculiarities of Transparent MgAl2O4 Ceramics–Effect of LiF Sintering Additive // Inorg. Mater. 2018. V. 54. P. 1045–1050. https://doi.org/10.1134/S0020168518100023
Harris D., Cambrea L., Johnson L. et al. Properties of an Infrared-Transparent MgO:Y2O3 Nanocomposite // J. Am. Ceram. Soc. 2013. V. 96. № 12. P. 3828–3835. https://doi.org/10.1111/jace.12589
Xu S., Li J., Kou H., Shi Y., Pan Y., Guo J. Spark Plasma Sintering of Y2O3–MgO Composite Nanopowder Synthesized by the Esterification Sol-Gel Route // Ceram. Int. 2015. V. 41. № 2. P. 3312–3317. https://doi.org/10.1016/j.ceramint.2014.10.120
Xie J., Mao X., Li X., Jiang B., Zhang L. Influence of Moisture Absorption on the Synthesis and Properties of Y2O3–MgO Nanocomposites // Ceram. Int. 2017. V. 43. № 1. P. 40–44. https://doi.org/10.1016/j.ceramint.2016.08.117
Yong S.M., Choi D.H., Lee K., Ko S.Y., Cheong D.I. Influence of the Calcination Temperature on the Optical and Mechanical Properties of Y2O3–MgO Nanocomposites // Arch. Metall. Mater. 2018. V. 63. № 3. P. 1481–1484. https://doi.org/10.24425/123834
Seyedrazi S.S.H., Taheri-Nassaj E. Effects of Y2O3 Additive Percentage on MgO Ceramic by Co-Precipitation and SPS Methods // Mater. Chem. Phys. 2018. V. 219. P. 96–108. https://doi.org/10.1016/j.matchemphys.2018.08.005
Kryzhanovska O.S., Safronova N.A., Balabanov A.E., Yavetskiy R.P., Dobrotvorskaya M.V., Li J., Petrushenko S., Tolmachev A.V., Matveevskaya N.A., Shulichenko E.N., Mayorov V.Yu., Sofronov D. Y2O3–MgO Highly-Sinterable Nanopowders for Transparent Composite Ceramics // Funct. Mater. 2019. V. 26. № 3. P. 829–837. https://doi.org/10.15407/fm26.04.829
Yong S.-M., Choi D.H., Lee K., Ko S.-Y., Cheong D.-I. Influence of the SPS Heating Rate on the Optical and Mechanical Properties of Y2O3–MgO Nanocomposites // J. Ceram. Process. Res. 2019. V. 20. № 1. P. 59–62. https://doi.org/10.36410/jcpr.2019.20.1.59
Yong S.-M., Choi D.H., Lee K., Ko S.-Y., Cheong D.-I., Park Y.-J., Go S.-I. Study on Carbon Contamination and Carboxylate Group Formation in Y2O3–MgO Nanocomposites Fabricated by Spark Plasma Sintering // J. Eur. Ceram. Soc. 2020. V. 40. № 3. P. 847–851. https://doi.org/10.1016/j.jeurceramsoc.2019.10.035
Liu L., Morita K., Suzuki T. S., Kim B.-N. Evolution of Microstructure, Mechanical, and Optical Properties of Y2O3–MgO Nanocomposites Fabricated by High Pressure Spark Plasma Sintering // J. Eur. Ceram. Soc. 2020. V. 40. № 13. P. 4547–4555. https://doi.org/10.1016/j.jeurceramsoc.2020.05.046
Liu L., Morita K., Suzuki T.S., Kim B.-N. Synthesis of Highly-Infrared Transparent Y2O3–MgO Nanocomposites by Colloidal Technique and SPS // Ceram. Int. 2020. V. 46. № 9. P. 13669–13676. https://doi.org/10.1016/j.ceramint.2020.02.153
Permin D.A., Boldin M.S., Belyaev A.V., Balabanov S.S., Novikova A.V., Koshkin V.A., Murashov A.A., Ladenkov I.V., Popov A.A., Lantsev E.A., Khamaletdinova N.M. IR-Transparent MgO–Y2O3 Ceramics by Self-Propagating High-Temperature Synthesis and Spark Plasma Sintering // Ceram. Int. 2020. V. 46. № 10. Part B. P. 15786–15792. https://doi.org/10.1016/j.ceramint.2020.03.124
Safronova N.A., Kryzhanovska O.S., Dobrotvorska M.V. et al. Influence of Sintering Temperature on Structural and Optical Properties of Y2O3–MgO Composite SPS Ceramics // Ceram. Int. 2020. V. 46. № 5. P. 6537–6543. https://doi.org/10.1016/j.ceramint.2019.11.137
Safronova N.A., Yavetskiy R.P., Kryzhanovska O.S., Dobrotvorska M.V., Balabanov A.E., Vorona I.O., Tolmachev A.V., Baumer V.N., Matolínová I., Kosyanov D.Yu., Shichalin O.O., Papynov E.K., Hau S., Gheorghe C. A Novel IR-Transparent Ho3+:Y2O3–MgO Nanocomposite Ceramics for Potential Laser Applications // Ceram. Int. 2021. V. 47. № 1. P. 1399–1406. https://doi.org/10.1016/j.ceramint.2020.08.263
Liu L., Morita K., Suzuki T.S., Kim B.-N. Effect of Volume Ratio on Optical and Mechanical Properties of Y2O3–MgO Composites Fabricated by Spark-Plasma-Sintering Process // J. Eur. Ceram. Soc. 2021. V. 41. № 3. P. 2096–2105. https://doi.org/10.1016/j.jeurceramsoc.2020.10.074
Xu S., Li J., Li C., Pan Y., Guo J. Hot Pressing of Infrared Transparent Y2O3–MgO Nanocomposites Using Sol–Gel Combustion Synthesized Powders // J. Am. Ceram. Soc. 2015. V. 98. № 3. P. 1019–1026. https://doi.org/10.1111/jace.13375
Xu S., Li J., Li C., Pan Y., Guo J. Infrared Transparent Y2O3–MgO Nanocomposites Fabricated by the Glucose Sol–Gel Combustion and Hot Pressing Technique // J. Am. Ceram. Soc. 2015. V. 98. № 9. P. 2796–2802. https://doi.org/10.1111/jace.13681
Ma H.J., Jung W.K., Baek C., Kim D.K. Influence of Microstructure Control on Optical and Mechanical Properties of Infrared Transparent Y2O3–MgO Nanocomposite // J. Eur. Ceram. Soc. 2017. V. 37. № 15. P. 4902–4911. https://doi.org/10.1016/j.jeurceramsoc.2017.05.049
Ma H.J., Jung W.K., Park Y., Kim D.K. A Novel Approach of an Infrared Transparent Er:Y2O3–MgO Nanocomposite for Eye-Safe Laser Ceramics // J. Mater. Chem. C. 2018. V. 6. № 41. P. 11096–11103. https://doi.org/10.1039/C7TC05991D
Ma H.J., Jung W.K., Yong S.-M., Choi D.H., Kim D.K. Microstructural Freezing of Highly NIR Transparent Y2O3–MgO Nanocomposite via Pressure-Assisted Two-Step Sintering // J. Eur. Ceram. Soc. 2019. V. 39. № 15. P. 4957–4964. https://doi.org/10.1016/j.jeurceramsoc.2019.07.029
Ma H.J., Kong J.H., Kim D.K. Insight into the Scavenger Effect of LiF on Extinction of a Carboxylate Group for Mid-Infrared Transparent Y2O3–MgO Nanocomposite // Scr. Mater. 2020. V. 187. P. 37–42. https://doi.org/10.1016/j.scriptamat.2020.05.001
Sun H., Zhang Y., Li T., Gong H., Li Q. High Reactive MgO–Y2O3 Nanopowders via Microwave Combustion Method and Sintering Behavior // Int. J. Appl. Ceram. Technol. 2016. V. 13. № 2. P. 367–372. https://doi.org/10.1111/ijac.12484
Mathew C.T., Solomon S., Koshy J., Thomas J.K. Enhanced Infrared Transmission Characteristics of Microwave-Sintered Y2O3–MgO Nanocomposite // Bull. Mater. Sci. 2017. V. 40. № 6. P. 1171–1178. https://doi.org/10.1007/s12034-017-1474-1
Mathew C.T., Jijimon K.T., Swapna Y.V., Koshy J., Solomon S. A Comprehensive Analysis of the Influence of Resistive Coupled Microwave Sintering on the Optical, Thermal and Hardness Properties of Infrared Transparent Yttria-Magnesia Composites // Ceram. Int. 2017. V. 43. № 18. P. 17048–17056. https://doi.org/10.1016/j.ceramint.2017.09.117
Permin D.A., Boldin M.S., Belyaev A.V., Balabanov S.S., Koshkin V.A., Murashov A.A., Ladenkov I.V., Lantsev E.A., Smetanina K.E., Khamaletdinova N.M. IR-Transparent MgO–Gd2O3 Composite Ceramics Produced by Self-Propagating High-Temperature Synthesis and Spark Plasma Sintering // J. Adv. Ceram. 2021. V. 10. № 2. In press. https://doi.org/10.1007/s40145-020-0434-1
Belyaev A.V., Evdokimov I.I., Drobotenko V.V., Sorokin A.A. A New Approach to Producing Transparent ZnAl2O4 Ceramics // J. Eur. Ceram. Soc. 2017. V. 37. № 7. P. 2747–2751. https://doi.org/10.1016/j.jeurceramsoc.2017.02.041
Алексеев М.К., Куликова Г.И., Русин М.Ю., Саванина Н.Н., Балабанов С.С., Беляев А.В., Гаврищук Е.М., Иванов А.В., Ризаханов Р.Н. Прозрачная керамика, полученная методом SPS, из особо чистых нанопорошков алюмомагниевой шпинели // Неорган. материалы. 2016. Т. 51. № 3. С. 367–373. https://doi.org/10.7868/S0002337X16030027
Дополнительные материалы отсутствуют.
Инструменты
Неорганические материалы