Неорганические материалы, 2022, T. 58, № 10, стр. 1134-1140
Синтез порошковых композитов на основе Si3N4 для электроимпульсного плазменного спекания керамики
П. В. Андреев 1, 2, *, Л. С. Алексеева 2, Е. Е. Ростокина 1, П. Д. Дрожилкин 2, С. С. Балабанов 1, А. А. Мурашов 2, К. О. Каразанов 2
1 Институт химии высокочистых веществ им. Г.Г. Девятых Российской академии наук
603951 Нижний Новгород, ул. Тропинина, 49, Бокс-75, Россия
2 Нижегородский государственный университет им. Н.И. Лобачевского
603022 Нижний Новгород, пр. Гагарина, 23, Россия
* E-mail: andreev@phys.unn.ru
Поступила в редакцию 20.08.2021
После доработки 04.08.2022
Принята к публикации 19.08.2022
- EDN: JETWXS
- DOI: 10.31857/S0002337X22100013
Аннотация
Рассмотрены четыре способа нанесения спекающей добавки (Y2O3 : Al2O3 = 3 : 5) на частицы промышленного порошка Si3N4 различного гранулометрического состава: аморфного нанопорошка и кристаллического микронного порошка α-Si3N4. Формирование оксидной фазы спекающей добавки проводилось в два этапа: смешивание исходного порошка Si3N4 с соединениями, содержащими ионы иттрия и алюминия, методами “мокрой” химии и отжиг полученных порошковых композитов при температуре 1000°C на воздухе. Показано, что способ внесения добавки и гранулометрический состав исходного порошка Si3N4 оказывают влияние на состав образующихся в процессе отжига кристаллических фаз. Для получения керамики Si3N4 с улучшенными физико-механическими свойствами оптимальна технология распылительной сушки, позволяющая получать сферические агломераты.
ВВЕДЕНИЕ
Благодаря высоким твердости, прочности на изгиб, трещиностойкости и коррозионной стойкости керамика на основе нитрида кремния (Si3N4) в настоящее время применяется для изготовления режущего и обрабатывающего инструмента, ответственных узлов двигателей в автомобиле- и авиастроении, пар трения в нефтехимической промышленности и др. [1].
Ковалентный тип связи в Si3N4 обуславливает низкую интенсивность диффузионных процессов и процессов вязкого течения, обеспечивающих уплотнение порошков при спекании [2]. По этой причине для спекания керамики на основе Si3N4 широко используют активирующие добавки, которые при температурах ниже температуры разложения Si3N4 образуют между его зернами жидкую фазу и тем самым способствуют повышению интенсивности спекания керамики. В качестве активаторов спекания, как правило, используют оксиды различных металлов [3], причем наибольшее распространение получили добавки на основе оксида иттрия (Y2O3), оксида алюминия (Al2O3), а также оксидов и нитридов редкоземельных элементов и их сочетаний. Широко используются спекающие добавки в виде бинарных и тройных эвтектических соединений на основе системы Y2O3–Al2O3. Один из примеров таких соединений – иттрий-алюминиевый гранат (ИАГ) [4–6]. Утверждается, что применение активаторов спекания приводит к формированию хрупкой аморфной фазы на границах зерен Si3N4, что негативно влияет на механические свойства керамики [7].
Для спекания мелкозернистой керамики, в том числе на основе Si3N4, в последнее время большой интерес представляет технология электроимпульсного (“искрового”) плазменного спекания (ЭИПС) [8].
ЭИПС является одним из наиболее эффективных методов компактирования высокоплотной и мелкозернистой керамики. Быстрый нагрев (до 2500°C/мин) за счет пропускания тока высокой мощности через пресс-форму, в которую засыпается шихта, позволяет значительно ускорить спекание и тем самым исключить рост зерен. При этом для обеспечения однородности и высоких показателей физико-механических свойств керамических образцов на основе Si3N4 необходима качественная шихта. В частности, требуется высокая степень равномерности распределения спекающей добавки в шихте. При этом доля спекающей добавки должна быть сбалансированной с точки зрения эффективности технологии спекания и требуемых физико-механических свойств изделия. Предполагается, что оптимальна шихта, где каждая частица порошка Si3N4 покрыта тонким слоем спекающей добавки.
Для решения задачи получения частиц со структурой ядро/оболочка в последнее время применяют методы “мокрой” химии, позволяющие наносить тонкие слои активирующих добавок на поверхность частиц порошка. В частности, это различные варианты методов осаждения, обеспечивающие более высокий уровень однородности смеси по сравнению с механическим перемешиванием [9–12].
Целью работы являлось исследование фазового состава и микроструктуры порошковых композитов, синтезированных при различных методах осаждения спекающей добавки (Y2O3–Al2O3) на нанодисперсные и микронные частицы порошков Si3N4.
ЭКСПЕРИМЕНТАЛЬНАЯ ЧАСТЬ
В качестве исходного материала использовались порошки Si3N4 с начальным размером частиц <5 мкм (серия 1) и <15 нм (серия 2) производства abcr Gmb (Германия). По спецификации производителя микронный порошок содержал не менее 90% α-Si3N4, а нанопорошок являлся полностью рентгеноаморфным. Здесь и далее содержание указано в мас. %. Расчетный состав порошковых композитов был выбран из соотношения 91.5% Si3N4 и 8.5% Y2O3–Al2O3, причем мольное соотношение компонентов оксидной системы составляло 3 : 5, что соответствует стехиометрии ИАГ [13]. Для получения порошковых композитов были использованы следующие методы.
1 – Метод соосаждения, который представляет собой совместное осаждение гидроксидов иттрия и алюминия из растворов нитратов Y(NO3)3 и Al(NO3)3. Порошок Si3N4 при тщательном перемешивании добавляли к водному раствору нитратов при комнатной температуре. К полученной суспензии при постоянном перемешивании по каплям добавляли водный раствор аммиака до достижения pH 8. Полученную смесь высушивали при температуре 80°C.
2 – Метод Печини [14], суть которого состоит в образовании цитратных гелей из растворов нитратов Y(NO3)3 и Al(NO3)3 при добавлении лимонной кислоты. К водному раствору нитратов иттрия и алюминия добавляли раствор лимонной кислоты в таком количестве, чтобы ее мольное отношение к суммарному содержанию нитрат-ионов было 1 : 1. К полученному гелю при постоянном перемешивании добавляли порошок Si3N4. Далее проводили сушку при постоянном перемешивании до состояния густого геля. Затем гель последовательно отжигали при 350 и 500°C в течение 2 ч.
3 – осаждение в желатиновой матрице (создание густого геля на основе желатина). К горячему раствору (80°C) нитратов иттрия и алюминия добавляли желатин (из расчета ~2 г на 1 г конечного продукта) и выдерживали при этой температуре в течение 2 ч с непрерывным перемешиванием. К образовавшемуся раствору добавляли порошок Si3N4. Полученную смесь охлаждали до 4°C (до образования геля), разрезали на фрагменты размером 3–5 мм, заливали водным раствором аммиака и выдерживали в течение 24 ч при 4°C. После этого гель промывали сначала дистиллированной водой, затем этанолом и высушивали при 100°C в течение 8 ч.
4 – нанесение спекающей добавки методом распылительной сушки, который основан на использовании смеси золей Y(OH)2(CH3COO) и Al5(NO3)3(OH)12 с порошком Si3N4. Состав водной суспензии рассчитывался таким образом, чтобы масса дисперсной фазы (в пересчете на Si3N4, Y2O3, Al2O3) составляла 52.5%. Для стабилизации суспензии вводилось 1.5% полиакрилата аммония. После перемешивания в планетарной мельнице суспензию высушивали методом распылительной сушки при 150°C.
В результате использования методов 1–4 на поверхность частиц исходных порошков Si3N4 двух типов была осаждена спекающая добавка. Для формирования оксидной фазы на поверхности частиц проводился последовательный отжиг порошковых композитов на воздухе при 300 (2 ч), 500, 800 и 1000°C (по 6 ч) с диспергированием в агатовой ступке между стадиями.
Полученные порошковые композиты исследовались с использованием растрового электронного микроскопа (РЭМ) JEOL JSM-6490, просвечивающего электронного микроскопа (ПЭМ) JEOL JEM-2100 и методом рентгенофазового анализа (РФА) на дифрактометре Shimadzu XRD-7000. Качественный фазовый анализ проводился с использованием банка данных PDF-2 (2012). Количественный состав оценивался методом корундовых чисел [15].
РЕЗУЛЬТАТЫ И ОБСУЖДЕНИЕ
На рис. 1 представлены электронные микрофотографии исходных порошков Si3N4, а на рис. 2 – результаты их рентгенодифракционного исследования. Аттестация исходных порошков методом РФА подтвердила, что микронный порошок (рис. 2а (0)) представляет собой смесь α- и β-фаз Si3N4 (PDF 01-071-6479 и PDF 01-071-0623 соответственно). Дифрактограмма нанопорошка Si3N4 (рис. 2б (0)) не содержит дифракционных пиков и отличается наличием характерного гало. Количественный состав кристаллических фаз микронного порошка и изготовленных на его основе порошковых композитов представлен в табл. 1.
Рис. 2.
Дифрактограммы порошковых композитов серии 1 (а), 2 (б): 0 – исходный порошок, 1–4 – метод синтеза (см. табл. 1).
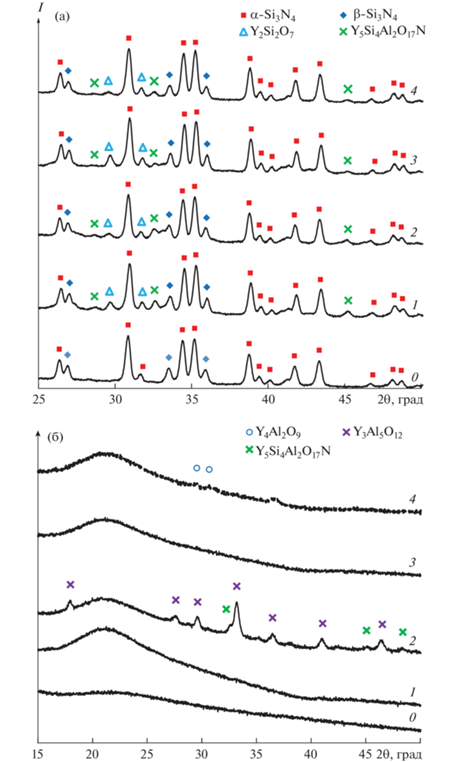
Таблица 1.
Фазовый состав порошковых композитов
Метод синтеза | Содержание*, мас. % (серия 1) | ||||
---|---|---|---|---|---|
α-Si3N4 | β-Si3N4 | Y2Si2O7 | Y5Si4Al2O17N | ||
Исходный Si3N4 | 90 | 10 | – | – | |
1 | 80 | 12 | 2 | 6 | |
2 | 81 | 12 | 2 | 5 | |
3 | 78 | 10 | 1 | 11 | |
4 | 85 | 10 | 1 | 4 | |
Метод синтеза | Содержание*, мас.% (серия 2) | ||||
Y3Al5O12 | Y4Al2O9 | Y5Si4Al2O17N | |||
Исходный Si3N4 | Рентгеноаморфное состояние | ||||
3 | 74 | – | 26 | ||
4 | – | 100 | – |
На рис. 2а также приведены дифрактограммы изготовленных порошковых композитов после завершающего этапа синтеза – высокотемпературного отжига, проводимого с целью формирования фазы спекающей добавки. Дифрактограммы композитов до отжига и после его промежуточных этапов идентичны друг другу и соответствуют дифрактограмме исходного порошка Si3N4.
РФА порошковых композитов серии 1 (рис. 2а) свидетельствует о появлении в процессе отжига при 1000°C новых кристаллических фаз. Для всех случаев синтеза характерно появление фазы иттриевого сиалона Y5Si4Al2O17N (PDF 00-048-1631) и двойного оксида иттрия-кремния Y2Si2O7 (PDF 00-038-0223). При этом для последнего не исключено появление твердого раствора замещения (Y,Al)2Si2O7 [16]. Согласно результатам РФА, образования ожидаемых стехиометрических кристаллических фаз системы Y–Al–O [17] не происходит. Результаты, приведенные в табл. 1, свидетельствуют о том, что после отжига доля кристаллических иттрийсодержащих фаз в порошковых композитах, полученных различными методами, различается в пределах 5–12 мас. % (с учетом только кристаллической составляющей смеси). Согласно [18], фаза Y5Si4Al2O17N может образоваться при температуре ~1000°C в системе Si3N4–Y2O3–Al2O3–SiO2 в среде с содержанием азота, при этом слой SiO2 всегда присутствует на поверхности частиц порошка Si3N4 [16, 19]. Фаза Y2Si2O7, согласно предыдущим исследованиям [20, 21], может образоваться в системе Y2O3–SiO2 при температурах от 750 до 1000°С.
РФА порошковых композитов серии 2 (рис. 2б) свидетельствует об отсутствии ожидаемых стехиометрических кристаллических фаз системы Y–Al–O при использовании методов 1 (соосаждения) и 2 (метод Печини). Их дифрактограммы не содержат пиков и соответствуют дифрактограмме исходного аморфного порошка Si3N4 (дифрактограммы 1 и 2 на рис. 2б).
Результаты количественного РФА образцов серии 2 представлены в табл. 1 (данные приведены только для образцов, на дифрактограммах которых были идентифицированы кристаллические фазы). В образце серии 2, полученном методом осаждения в желатиновой матрице (метод 3), отжиг при 1000°С привел к формированию фаз ИАГ (PDF 01-082-0575) и Y5Si4Al2O17N (дифрактограмма 3 на рис. 2б). По нашему мнению, появление фазы Y5Si4Al2O17N является следствием частичного растворения наночастиц Si3N4 в YAlO3.
В образце, полученном методом распылительной сушки (метод 4), наблюдается образование кристаллической фазы Y4Al2O9 (PDF 01-083-0933), доля которой незначительна по сравнению с долей аморфной фазы.
РЭМ-снимки свидетельствуют о высокой степени однородности порошковых композитов и об отсутствии крупных агломератов спекающей добавки (рис. 3). Морфология исходных порошков Si3N4 и композитов, полученных методами 1–3, идентична (рис. 1 и 3).
Рис. 3.
РЭМ-изображения синтезированных порошковых композитов на основе нано (а, б) и микродисперсных порошков (в, г), полученных методами 3 (а), 4 (б, г) и 2 (в).
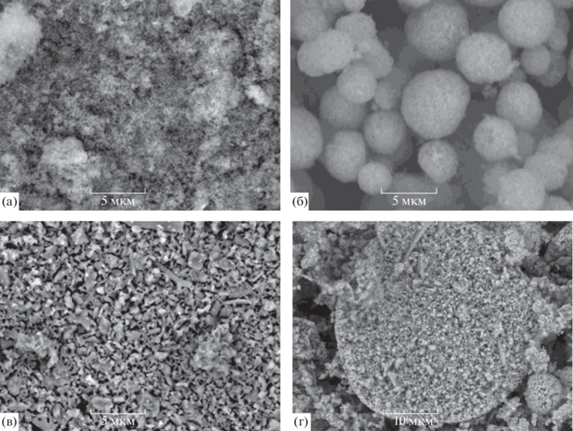
Порошковые композиты, полученные методом распылительной сушки (метод 4), представляют собой сферические агломераты. Размер сферических агломератов в композитах на основе микронного порошка Si3N4 (серия 1) находится в интервале 5–50 мкм (рис. 3а, 3б). Размер агломератов в композитах на основе нанопорошка Si3N4 (серия 2) варьируется в интервале от 1 до 5 мкм (рис. 3в, 3г). Таким образом, полученные методом распылительной сушки сферические агломераты после отжига при 1000°C представляют собой частицы Si3N4, соединенные между собой аморфной фазой оксидной добавки с включениями кристаллических частиц: Y4Al2O9 в случае нанопорошков, Y5Si4Al2O17N и Y2Si2O7 в случае микронных порошков (см. табл. 1).
Порошковый композит серии 1, полученный методом распылительной сушки (метод 4), был исследован методом ПЭМ. На снимке (рис. 4) хорошо различимо ограненное кристаллическое зерно Si3N4 и распределенная по его поверхности спекающая добавка (указана стрелкой). Таким образом, подтверждена принципиальная возможность нанесения спекающей добавки на каждую частицу порошка Si3N4.
Обобщая представленные результаты исследований порошковых композитов на основе микронного порошка Si3N4 (серия 1), отметим, что различия образцов, изготовленных методами 1–3, незначительны, что может обеспечить одинаковый процесс спекания. Выделяется композит, изготовленный методом распылительной сушки (метод 4), в процессе отжига которого образуется меньшее количество кристаллических фаз на основе спекающей добавки. Это может свидетельствовать о более равномерном характере ее распределения. С практической точки зрения важно отметить, что полученные методом распылительной сушки частицы образуют крупные сферические агломераты. Потенциально это может позволить ускорить процесс низкотемпературного спекания за счет более высокой насыпной плотности композита.
Среди порошковых композитов серии 2 различий в составе образцов, изготовленных методами 1 (соосаждения) и 3 (осаждения в желатиновой матрице), не обнаружено. В композите, изготовленном методом 2 (Печини) (рис. 2б), в процессе отжига сформировалась фаза ИАГ. По нашему мнению, это свидетельствует о присутствии крупных агломератов спекающей добавки.
ЗАКЛЮЧЕНИЕ
Рассмотрены четыре способа изготовления порошковых композитов для спекания керамики методом ЭИПС путем внесения спекающей добавки состава Y2O3–Al2O3, соответствующего иттрий-алюминиевому гранату, в порошок нитрида кремния (Si3N4) различной дисперсности: соосаждение в воде, метод Печини, осаждение в желатиновой матрице и метод распылительной сушки.
Показано, что фаза ИАГ не образуется в процессе поэтапного отжига (до 1000°C) в порошковых композитах, изготовленных на основе микронного порошка α-Si3N4, но формируются фазы иттриевого сиалона (Y5Si4Al2O17N) и дисиликата иттрия (Y2Si2O7) независимо от метода внесения добавки.
В композите на основе нанопорошка кристаллические фазы не формируются в достаточном для их идентификации методом РФА объеме независимо от метода внесения добавки. Исключение составляет метод Печини (осаждение в присутствии лимонной кислоты), в случае применения которого в порошковых композитах обнаруживаются фазы ИАГ и иттриевого сиалона.
Список литературы
Knoch H., Heinrich J. Mechanical Properties of Silicon Nitride // Material. Werkstofftech. 1980. V. 11. № 10. P. 361–367. https://doi.org/10.1002/mawe.19800111006
Самсонов Г.В. Нитриды. Киев: Наук. думка, 1969. С. 380.
Deeley G.G., Herbert J.M., Moore N.C. Dense Silicon Nitride // Powder Metall. 1961. V. 4. № 8. P. 145–151. https://doi.org/10.1179/pom.1961.4.8.011
Richerson D.W. Historical Review of Addressing the Challenges of Use of Ceramic Components in Gas Turbine Engines // Proc. of the ASME Turbo Expo. American Society of Mechanical Engineers Digital Collection. 2006. V. 2. P. 241–254. https://doi.org/10.1115/GT2006-90330
Pyzik A.J., Carroll D.F. Technology of Self-Reinforced Silicon Nitride // Annu. Rev. Mater. Sci. 1994. V. 24. № 1. P. 189–214.
Loehman R.E., Rowcliffe D.J. Sintering of Si3N4–Y2O3–Al2O3 // J. Am. Ceram. Soc. 1980. V. 63. № 3–4. P. 144–148. https://doi.org/10.1111/j.1151-2916.1980.tb10679.x
Podobeda L.G. Effect of Impurities on the Properties of Silicon Nitride Materials // Sov. Powder Metall. Met. Ceram. 1979. V. 18. № 1. P. 59–63.
Tokita M. Progress of Spark Plasma Sintering Ceramics Applications and Industrialization // Ceramic. 2021. V. 4. № 2. P. 160–198. https://doi.org/10.3390/ceramics4020014
Vrolijk J.W.G.A., Willems J.W.M.M., Metselaar R. Coprecipitation of Yttrium and Aluminium Hydroxide for Preparation of Yttrium Aluminium Garnet // J. Eur. Ceram. Soc. 1990. V. 6. № 1. P. 47–51. https://doi.org/10.1016/0955-2219(90)90034-D
Sordelet D.J. et al. Synthesis of Yttrium Aluminum Garnet Precursor Powders by Homogeneous Precipitation // J. Eur. Ceram. Soc. 1994. V. 14. № 2. P. 123–130. https://doi.org/10.1016/0955-2219(94)90100-7
Manalert R., Rahaman M.N. Sol-Gel Processing and Sintering of Yttrium Aluminum Garnet (YAG) Powders // J. Mater. Sci. 1996. V. 31. № 13. P. 3453–3458. https://doi.org/10.1007/BF00360748
Li J.-G. et al. Co-Precipitation Synthesis and Sintering of Yttrium Aluminum Garnet (YAG) Powders: the Effect of Precipitant // J. Eur. Ceram. Soc. 2000. V. 20. № 14–15. P. 2395–2405. https://doi.org/10.1016/S0955-2219(00)00116-3
Zhang N., Ru H.Q., Cai Q.K., Sun X.D. The Influence of the Molar Ratio of Al2O3 to Y2O3 on Sintering Behavior and the Mechanical Properties of a SiC–Al2O3–Y2O3 Ceramic Composite // Mater. Sci. Eng. A. 2008. V. 486. P. 262–266. https://doi.org/10.1016/j.msea.2007.09.052
Sunde T.O.L., Grande T., Einarsrud M.A. Modified Pechini Synthesis of Oxide Powders and Thin Films // Handbook of Sol-Gel Science and Technology. 2016. P. 1–30.
Dinnebier R., Billinge S. Powder Diffraction. Theory and Practice. Cambridge: RSC Publishing, 2008. P. 605.
Ziegler G., Heinrich J., Wötting G. Relationships between Processing, Microstructure and Properties of Dense and Reaction-Bonded Silicon Nitride // J. Mater. Sci. 1987. V. 22. № 9. P. 3041–3086. https://doi.org/10.1007/BF01161167
Abell J.S. et al. An Investigation of Phase Stability in the Y2O3-Al2O3 System // J. Mater. Sci. 1974. V. 9. № 4. P. 527–537. https://doi.org/10.1007/BF02387524
Dolekcekic E., Pomeroy M.-J., Hampshire S. Influence of Amount of Nitrogen on Crystallisation of Y-Sialon Glasses: in-situ XRD Analysis // Key Eng. Mater. 2005. V. 287. P. 293–298. doi: 10.4028/www.scientific.net/KEM.287.293
Kroll P., Milko M. Theoretical Investigation of the Solid State Reaction of Silicon Nitride and Silicon Dioxide forming Silicon Oxynitride (Si2N2O) under Pressure // Z. Anorg. Allg. Chem. 2003. V. 629. P. 1737–1750.
Попович Н.В., Орлова Ю.Е., Аненьева А.С. и др. Низкотемпературный синтез покрытий в системе Y2O3–Al2O3–SiO2 // Изв. ВолгГТУ. 2011. Т. 75. № 2. С. 160–164.
Kahlenberg V., Wertl W., Tobbens D.M. et al Rietveld Analysis and Raman Spectroscopic Investigations on α-Y2Si2O7 // Z. Anorg. Allg. Chem. 2008. V. 634. P. 1166–1172.
Дополнительные материалы отсутствуют.
Инструменты
Неорганические материалы