Неорганические материалы, 2022, T. 58, № 10, стр. 1053-1063
Структура, механические свойства, термическая стабильность и химическая устойчивость метастабильного твердого раствора Ti1 – xAlxN (x = 0.03–0.05), сформированного в виде arc-PVD-покрытия на сплавах ВК
И. В. Блинков 1, *, В. С. Сергевнин 1, А. В. Черногор 1, Д. С. Белов 1, А. П. Демиров 1, Ф. В. Кирюханцев-Корнеев 1
1 Национальный исследовательский технологический университет
“МИСиС”
119049 Москва, Ленинский пр., 4, Россия
* E-mail: biv@misis.ru
Поступила в редакцию 23.05.2022
После доработки 28.06.2022
Принята к публикации 05.07.2022
- EDN: GTGNWC
- DOI: 10.31857/S0002337X22100037
Аннотация
Проведены сравнительные исследования химической и термической устойчивости, а также механических свойств arc-PVD-покрытий TiN и Ti0.97Al0.03N. При нагреве покрытий в вакууме до 600 и 700°С происходят рост размеров ОКР, уменьшение значений двухосных макронапряжений, периодов решетки, микродеформаций, что определяется термически активируемыми процессами восстановления структуры, обусловленного аннигиляцией дефектов, возникающих при формировании покрытий. В покрытии Ti0.97Al0.03N релаксация напряжений осуществляется более интенсивно, что связано с большей плотностью дефектов. При 700°С происходит спинодальный распад твердого раствора Ti0.97Al0.03N на TiN и AlN (ГЦК). В отличие от покрытия TiN твердость, параметры H3/E2 и H/E Ti0.97Al0.03N с ростом температуры отжига до 700°С практически не изменяются, что определяется дисперсионным упрочнением в результате спинодального распада. В кислотной и щелочной средах поведение покрытий однотипно, при этом Ti0.97Al0.03N проявляет несколько бóльшую стойкость к окислению на воздухе при 550°С.
ВВЕДЕНИЕ
В равновесных условиях растворимость AlN в TiN в твердом состоянии крайне ограничена и составляет менее 2 ат. % при 1000°С [1]. Авторам [2–4] удалось в виде покрытий получить однофазные ГЦК-нитриды Ti1– xAlxN с x ~ 0.4 и х < 0.6–0.7 соответственно магнетронным распылением и вакуумно-дуговым испарением при температурах подложки 500 и 400–500°C.
Покрытия Ti–Al–N обладают стойкостью к окислению вплоть до 750–800°С против 500–550°С, характерных для TiNx. В результате окисления на поверхности образуется плотный адгезионный слой Al2O3, который защищает покрытия от дальнейшего окисления. При этом покрытия Ti–Al–N характеризуются высокой твердостью – до 37 ГПа, которая сохраняется при температурах отжига до 950°C, что указывает на их повышенную стабильность по сравнению с покрытиями Ti–N и Ti(C,N) [5, 6].
Свойства покрытий TiAlN зависят от их химического состава, условий осаждения, в частности, отрицательного потенциала смещения, подаваемого на подложку [4, 7]. Исследование свойств покрытий Ti1 –xAlxN показало перспективность их использования для самых различных функциональных назначений, в том числе и для упрочнения режущего инструмента [8, 9].
Наиболее широко используются покрытия этой системы с содержанием Al от 20 до 60–70 ат. %, поскольку твердость возрастает с ростом концентрации этого компонента. При этом эксплуатационные возможности данных покрытий ограничены из-за высокой склонности к хрупкому разрушению, что ограничивает применение режущего инструмента на операциях прерывистого резания [10–12].
В работах [13, 14] исследованы возможности упрочнения твердосплавного режущего инструмента покрытиями Ti–Al–N с содержанием алюминия 3–5 ат. %. Увеличение вязкости таких покрытий по сравнению с покрытиями, содержащими от 20 и выше ат. % алюминия, при некотором снижении твердости расширяет область использования режущего инструмента на операции как непрерывного (точение), так и прерывистого резания (фрезерование, строгание). Данный вывод был подтвержден стойкостными испытаниями твердосплавного режущего инструмента WC–Co (6 мас. %), упрочненного покрытием Ti–Al–N с содержанием алюминия ~3 ат. %, при фрезеровании сплава ЭИ 698-ВД, при точении стали 45 и серого чугуна.
В настоящей работе продолжено изучение функциональных возможностей покрытия Ti–Al–N с содержанием алюминия ~3 ат. %, их термической и химической устойчивости в сравнении с покрытиями TiN.
ЭКСПЕРИМЕНТАЛЬНАЯ ЧАСТЬ
Для нанесения покрытий Ti0.97Al0.03N и TiN применяли установку ионно-плазменного вакуумно-дугового напыления с тремя испаряемыми катодами, оснащенную сепараторами капельной фазы, аналогичную используемой в работе [15] за исключением того, что в данном исследовании для осаждения покрытий использовались соответственно катоды из сплава Ti–Al (6 ат. %) и из титана (ВТ1). В качестве реакционного газа применялся азот марки ВЧ6.0. Парциальное давление азота $\left( {{{p}_{{{{{\text{N}}}_{{\text{2}}}}}}}} \right)$ поддерживалось на уровне 0.5 Па. Время осаждения составляло 60 мин, толщина покрытий – 4–4.5 мкм. В качестве подложек были использованы твердосплавные пластины ВК6 и ВК8. Потенциал смещения (Us) на подложке был –120 В при токе дуги, испаряющей материал катода, ~120 А.
Морфологию и состав покрытий изучали с применением растрового электронного микроскопа JSM-7600F с приставкой для энергодисперсионной спектрометрии JED-2300F (JEOL, Япония). Для определения фазового состава покрытия использовали дифрактометр Ultima 4 (Rigaku, Япония): излучение СоKα, графитовый монохроматор на дифрагированном пучке в асимметричной геометрии (угол между падающим лучом и поверхностью образца составлял α = 5°). Количественный фазовый анализ выполнялся с использованием метода Ритвельда. Для определения размера областей когерентного рассеяния (ОКР) (D) по методу Селякова–Шеррера [16] (D = Kλ/β cos θ, где K – коэффициент формы частиц (K = 0.9 для сферических частиц), λ – длина волны рентгеновского излучения, β – ширина рефлекса на полувысоте (в радианах и в единицах 2θ), θ – угол дифракции (брэгговский угол)), величины микродеформаций решетки (ε), параметров решетки TiN и Ti0.97Al0.03N выполнялась съемка отражений 111 и 222 в симметричной геометрии.
Выделение физического уширения проводилось совместной аппроксимацией двух порядков отражений эталона и образца псевдофункциями Фойгта. В качестве эталона использовался порошок мелкозернистого германия (10–20 мкм).
Химический состав и энергия связи элементов фаз покрытия были исследованы на рентгеновском фотоэлектронном спектрометре (РФЭС) PHI 5500 ESCA (Perkin-Elmer, США). Для проведения структурных исследований покрытий применялся просвечивающий электронный микроскоп (ПЭМ) JEM 2100 высокого разрешения (JEOL, Япония).
Твердость (H), модуль упругости (E), относительную работу пластической (Wp) и упругой деформации (We) покрытий определяли методом измерительного индентирования при малых нагрузках (Оливера и Фарра), который осуществляли на микроиндентометре MicroHardnessTester (CSM Instruments, Швейцария). Индентирование проводили в динамическом режиме при постоянно возрастающей нагрузке с шагом 10 мН до максимального значения 200 мН. Результаты измерения, представленные в виде графических зависимостей твердости–модуль упругости от глубины проникновения индентора, давали возможность определить значения физико-механических характеристик на глубине проникновения индентора, соответствующей порядка 10% от толщины покрытия согласно требованиям стандарта [17].
Для определения термической стабильности покрытий проводился отжиг в вакууме (5 × 10–3 Па) в алундовых тиглях при температурах 400, 500, 600°С для TiN и 500, 600, 700°С для Ti0.97Al0.03N в течение 1 ч с последующим анализом морфологии, фазового состава и характеристик структуры.
Для изучения распределения элементного состава покрытий по толщине слоя после проведения окислительного отжига при анализе жаростойкости использовали метод высокочастотной оптической эмиссионной спектроскопии тлеющего разряда (GDOES/ВОЭСТР) [18]. Исследования проводили на приборе Profiler 2 (HoribaJobinYvon, Франция). Разрешение по концентрации химических элементов, содержащихся в покрытии, составляло 0.01 ат. %, разрешение по глубине исследуемого слоя не менее 20 нм.
Испытания на стойкость покрытий TiN и Ti0.97Al0.03N в кислотной и щелочной средах были осуществлены с помощью измерения потенциала динамической поляризации по ГОСТ 9.914–91 со скоростью развертки потенциала 0.2 мВ/с при 25°С. Анодные поляризационные кривые снимались после достижения стационарных потенциалов образцов. Электрохимическое поведение покрытий исследовалось с использованием потенциостата IPC-ProMF
Поскольку возможное применение данных покрытий связано с упрочнением режущего инструмента, эксплуатация которого в ряде случаев предусматривает применение смазочно-охлаждающих жидкостей, обладающих различным рН (2.5–10), в качестве коррозионно-активной среды использовали растворы следующих составов: I – 100 см3 (20 г FeCl3⋅6H2O + 5%-ная HNO3) + 19 г/см3 HCl; II – 0.12 г/л NaOH. Раствор I содержит сильные окислители (Fe3+ и азотную кислоту), оказывающие пассивирующее действие, и активирующие анионы Cl−, необходимые для активации поверхности при изучении склонности покрытий к питтинговой коррозии.
РЕЗУЛЬТАТЫ И ОБСУЖДЕНИЕ
Изображения поверхности всех полученных образцов сплавов ВК6 и ВК8 с покрытиями TiN и TiAlN представлены на рис. 1. Она имеет “ячеистую” структуру, обычную для arc-PVD-покрытий и связанную с повторением ими рельефа поверхности подложки после газоабразивной обработки. Шероховатость покрытий характеризуется значением параметра Ra порядка 0.1 мкм, на поверхности наблюдается относительно небольшое количество капельной фазы. Морфология покрытий не зависела от материала используемой подложки.
Исследования по термостабильности структуры и состава покрытий показали, что в процессе отжига морфология покрытий не претерпевает существенных изменений (рис. 2, 3).
Микроструктура покрытия TiN до и после термической обработки имеет плотное столбчатое строение (рис. 4) со средним диаметром столбцов до отжига ~70 нм. После отжига при 600°С он увеличился до ~120 нм. В случае покрытия Ti0.97Al0.03N средний диаметр столбцов до отжига составлял ~100 нм. После отжига при 700°C в покрытии образуется мелкозернистая структура, состоящая из зерен со средним размером ~40 нм (рис. 5).
При анализе электронограмм покрытий TiN и Ti0.97Al0.03N (рис. 6а, 7а) установлено, что до отжига в их составе присутствует одна фаза – TiN со структурой B1–NaCl. Этот же состав сохраняется в покрытии TiN после отжига при 600°С (рис. 6б). При этом наблюдается текстурированность исходных покрытий, выражающаяся в неоднородности интенсивности дифракционных колец и сохраняющаяся после отжига. После отжига при 700°С на электронограммах покрытия Ti0.97Al0.03N наряду с дифракционными линиями, характерными для фазы TiN (B1), были обнаружены линии, соответствующие AlN с ГЦК-решеткой (рис. 7б) [19]. Появление нитрида алюминия свидетельствует о спинодальном распаде метастабильного твердого раствора Ti–Al–N. Этот эффект описан в литературе для покрытий Ti1– xAlxN с большим содержанием алюминия [20, 21]. Кроме того, в данном покрытии после отжига, судя по характеру электроннограмм, пропадают признаки наличия текстуры, присущие как покрытию TiN, так и исходному образцу покрытия TiAlN.
Как следует из исследований характеристик субструктуры, макронапряжений и физикомеханических свойств покрытий TiN и Ti0.97Al0.03N (табл. 1, 2), исходные образцы имеют большие значения двухосных сжимающих напряжений (σ): –2.2 и –3.7 ГПа соответственно. Их значения уменьшаются после отжига. По мнению ряда исследователей [22, 23], это уменьшение связано с активируемыми термически процессами пластической деформации и восстановлением структуры, обусловленной аннигиляцией дефектов, возникающих при формировании покрытий и являющихся причиной появления в них структурной составляющей макронапряжений [24, 25]. При этом следует отметить, что в покрытии Ti0.97Al0.03N релаксация напряжений происходит более интенсивно, т. к. плотность дефектов в нем значительно выше. Об этом можно судить по величинам микродеформаций (ε), природа которых определяется концентрационными неоднородностями в объеме кристаллита и наличием дислокаций [26]. О восстановлении структуры покрытий обоих составов свидетельствует также уменьшение периодов их решеток. Одновременно с изменением структурных характеристик происходит изменение твердости покрытий, а также показателей H3/E2 и H/E, определяющих их сопротивление пластической и упругой деформациям [27]. Для покрытия TiN их значения уменьшаются, что объясняется процессом восстановления с аннигиляцией возникших при осаждении дефектов и рекристаллизацией. Для покрытия Ti0.97Al0.03N значения твердости практически сохраняются, как и параметров H3/E2 и H/E, что определяется дисперсионным упрочнением в результате спинодального распада [20, 28].
Таблица 1.
Характеристики субструктуры и физико-механические свойства покрытия TiN до и после термической обработки
Температура отжига, °С | До отжига | 400 | 500 | 600 |
---|---|---|---|---|
Размер ОКР (D), нм | 48 ± 4 | 54 ± 3 | 59 ± 2 | 67 ± 3 |
Период решетки (а), Å | 4.2478 ± 0.0013 | 4.2450 ± 0.0004 | 4.2446 ± 0.0002 | 4.2441 ± 0.0009 |
Микродеформации (ε), % | 0.15 ± 0.02 | 0.12 ± 0.01 | 0.09 ± 0.01 | 0.07 ± 0.02 |
Макронапряжения (σ), ГПа | –2.2 | –2.1 | –1.8 | –1.6 |
Твердость (H), ГПа | 25.1 ± 1.0 | 24.5 ± 1.0 | 22.6 ± 0.9 | 17.7 ± 0.8 |
Модуль Юнга (E), ГПа | 441 ± 18 | 423 ± 17 | 399 ± 16 | 345 ± 14 |
H3/E2, ГПа | 0.08 | 0.08 | 0.07 | 0.05 |
H/E | 0.06 | 0.06 | 0.06 | 0.05 |
Таблица 2.
Характеристики субструктуры и физико-механические свойства покрытия Ti0.97Al0.03N до и после термической обработки
Температура отжига, °С | До отжига | 500 | 600 | 700 |
---|---|---|---|---|
Размер ОКР (D), нм | 16 ± 2 | 17 ± 1 | 19 ± 2 | 19.5 ± 2 |
Период решетки (а), Å | 4.2386 ± 0.0003 | 4.2366 ± 0.0002 | 4.2321 ± 0.0002 | 4.2306 ± 0.0002 |
Микродеформации (ε), % | 0.6 ± 0.1 | 0.6 ± 0.1 | 0.4 ± 0.2 | 0.1 ± 0.2 |
Макронапряжения (σ), ГПа | –3.7 | –3.1 | –2.5 | –2.1 |
Твердость (H), ГПа | 29 ± 1.2 | 30.5 ± 1.2 | 25.1 ± 1.0 | 28.3 ± 1.0 |
Модуль Юнга (E), ГПа | 454 ± 18 | 463 ± 18 | 403 ± 16 | 480 ± 19 |
H3/E2, ГПа | 0.12 | 0.13 | 0.1 | 0.1 |
H/E | 0.06 | 0.07 | 0.06 | 0.06 |
Стойкость покрытий к воздействию кислотной и щелочной сред определялась в процессе электрохимических испытаний. Анодные поляризационные кривые, снятые в кислотной среде (рис. 8а), характеризуются наличием активационных пиков. Активационный пик для покрытия TiN наблюдается в пределах потенциала от 0 до 650 мВ, покрытие в пассивном состоянии находится в пределах потенциалов от 650 до 1000 мВ, дальнейшее увеличение потенциала приводит к окислению покрытия. Для покрытия Ti0.97Al0.03N активационный пик находится в пределах от 250 до 1000 мВ. Покрытие в пассивном состоянии находится в пределах потенциалов от 1000 до 1250 мВ. Дальнейшее увеличение потенциала приводит к окислению покрытия. Исходя из того, что анодные поляризационные кривые в целом повторяют друг друга, т.е. динамика окисления покрытий сходная, можно сделать вывод, что введение Al в небольших количествах (2–3 ат. %) незначительно влияет на электрохимические характеристики в кислотной среде. Однако добавка Al увеличивает ток коррозии с 80 до 180 мкА/см2. Это косвенно свидетельствует о большей подверженности коррозии покрытий TiAlN в кислотной среде по сравнению с покрытиями TiN.
В щелочной среде анодные поляризационные кривые (рис. 8б) характеризуются отсутствием активационных пиков. Этот факт говорит о самопассивации исследуемых покрытий. При анализе поляризационных кривых установлено, что при увеличении потенциала от 1000 до 1500 мВ для TiN и от 800 до 1500 мВ для Ti0.97Al0.03 N плотность тока увеличивается незначительно, токи коррозии для обоих покрытий составляют порядка 3 мкА/см2, что говорит об их близкой скорости коррозии в щелочной среде без приложения потенциала. Интенсивного окисления исследуемых покрытий не происходит, оба покрытия обладают стойкостью в щелочной среде.
Элементный состав покрытий, полученный методом РФЭС, свидетельствует о том, что в процессе электрохимических испытаний в кислотной среде покрытия TiN и Ti0.97Al0.03N разрушаются. В составе поверхностного слоя присутствуют Co и W, находящиеся в составе подложки ВК6. В щелочной среде образцы обоих покрытий характеризуются высокими защитными свойствами. В поверхностных слоях образцов Co и W отсутствуют, т.е. вскрытия покрытий не происходит. Основная часть энергетических спектров фотоэлектронов Ti2p (68–73%) в образцах покрытий (Ti,Al)N и TiN, подвергнутых обработке щелочью, локализована на Есв(Ti2p3/2) = 454.8 эВ и отвечает энергии связи титана с азотом (рис. 9а, 9в) [29]. Одновременно в высокоэнергетической части спектра (порядка 458.8 эВ) имеется плечо, которое может быть отнесено к оксиду и оксинитриду титана [30], доля которых составляет в сумме до 10%. В покрытиях после обработки в кислотной среде в энергетическом спектре Ti2p фотоэлектронов (рис. 9б, 9г) имеется дублет пиков Ti2p1/2 и Ti2p3/2 (1, 1' и 2, 2'), отвечающих состоянию титана с энергиями связи 458.8 и 464.7 эВ, что соответствует оксиду титана TiO2 (2, 2'), а также с энергиями связи 454.7 и 461.1 эВ, соответствующими нитриду титана (1, 1'). Его доля не превышает 5%.
Рис. 9.
РФЭС Ti2p образцов покрытий Ti0.97Al0.03N (а, б) и TiN (в, г) после обработки в щелочной (а, в) и кислотной (б, г) средах.
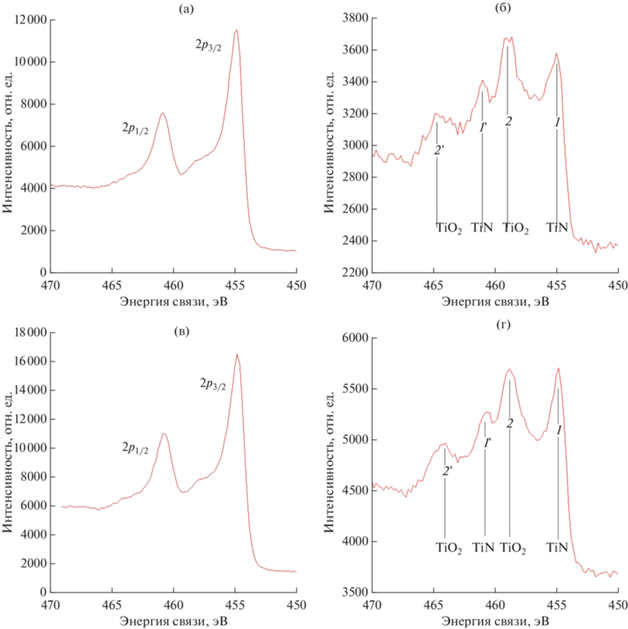
Исследование морфологии поверхности образцов покрытий TiN и Ti0.97Al0.03N (рис. 10а, 10б) также свидетельствует об их разрушении в процессе электрохимических испытаний в кислотной среде, сопровождающемся появлением рыхлой структуры. В щелочной среде сохраняется плотная структура, характерная для исходного состояния покрытий (рис. 10в, 10г).
Рис. 10.
Морфология поверхности покрытий TiN (а, в) и Ti0.97Al0.03N (б, г) после электрохимических испытаний в кислотной (а, б) и щелочной (в, г) средах.
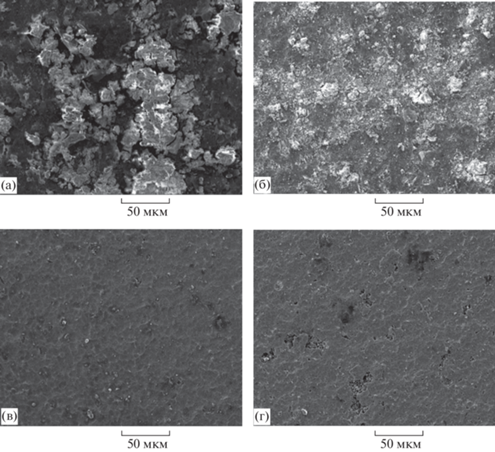
Методом ВОЭСТР были получены концентрационные профили распределения элементов по толщине покрытий TiN и Ti0.97Al0.03N (рис. 11) после их окисления при температуре 550°С в течение 45 мин. Выбор данной температуры определяется тем, что она соответствует заметной скорости окисления покрытий из нитрида титана [31, 32]. Известно, что образование оксидной фазы при термообработке керамики TiNx на воздухе контролируется объемной диффузией кислорода из газовой среды через первоначально образующийся слой рутила TiO2 [33]. Проникновение кислорода в покрытия TiN и Ti0.97Al0.03N происходит на глубины более 0.35 и 0.25 мкм соответственно. Об относительных количествах кислорода в окисленном материале обоих покрытий судили по площадям под соответствующими концентрационными кривыми, определенными методом Симпсона.
Рис. 11.
Концентрационные профили распределения элементов в приповерхностном слое покрытий TiN (а) и Ti0.97Al0.03N (б).
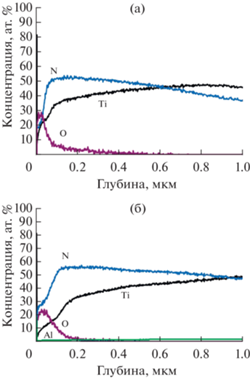
Относительное содержание кислорода в окисленном слое покрытия TiN выше на 5–7%. Полученные результаты свидетельствуют о незначительном улучшении жаростойкости покрытий Ti0.97Al0.03N в области температуры 550°С.
ЗАКЛЮЧЕНИЕ
Морфологических изменений поверхности покрытий TiN и Ti0.97Al0.03N при нагреве в вакууме до 600 и 700°С соответственно не обнаружено. Происходящие структурные изменения в покрытиях обоих составов проявляются в росте размеров ОКР, уменьшении двухосных макронапряжений, периодов решетки, микродеформаций. Эти явления определяются активируемыми термически процессами восстановления структуры, обусловленного аннигиляцией дефектов, возникающих при формировании покрытий. В покрытии Ti0.97Al0.03N релаксация напряжений происходит более интенсивно, что связано с большей плотностью дефектов.
При отжиге покрытия TiN происходит уменьшение твердости (H) и параметров H3/E2 и H/E, определяющих сопротивление пластической и упругой деформациям. Данное явление объясняется процессом восстановления структуры с аннигиляцией возникших при осаждении покрытия дефектов и рекристаллизацией. Для покрытия Ti0.97Al0.03N значения Н, как и параметров H3/E2 и H/E, практически не изменяются по отношению к состоянию до отжига, что определяется дисперсионным упрочнением покрытий Ti0.97Al0.03N в результате спинодального распада.
Покрытия TiN и Ti0.97Al0.03N показывают однотипное поведение в процессе электрохимических испытаний. Они разрушаются в кислотной среде, в щелочной среде происходит их самопассивация. Покрытие Ti0.97Al0.03N характеризуется лучшей жаростойкостью при 550°С, что проявляется в меньшей толщине окисленного слоя.
Список литературы
Schuster J.C., Bauer J. The Ternary System Titanium-Aluminum-Nitrogen // J. Solid State Chem. 1984. V. 53. № 2. P. 260–265. https://doi.org/10.1016/0022-4596(84)90100-2
Wahlstrom U., Hultman L, Sundgren J.-E., Adibi F., Petrov I., Greene J.E. Crystal Growth and Microstructure of Polycrystalline Ti1−xAlxN Alloy Films Deposited by Ultra-High-Vacuum Dual-Target Magnetron Sputtering // Thin Solid Films. 1993. V. 235. № 1–2. P. 62–70. https://doi.org/10.1016/0040-6090(93)90244-J
Tanaka Y., Gur T.M., Kelly M., Hagstrom S.B., Ikeda T., Wakihira K., Satoh H. Properties of (Ti1 –xAlx)N Coatings for Cutting Tools Prepared by the Cathodic arc Ion Plating Method // J. Vac. Sci. Technol., A. 1992. V. 10. № 4. P. 1749–1756. https://doi.org/10.1116/1.577742
Ikeda T., Satoh H. Phase Formation and Characterization of Hard Coatings in the Ti–Al–N System Prepared by the Cathodic arc Ion Plating Method // Thin Solid Films. 1991. V. 195. № 1–2. P. 99–110.
Hörling A., Hultman L., Odén M., Sjölén J., Karlsson L. Mechanical Properties and Machining Performance of Ti1 –xAlxN-Coated Cutting Tools // Surf. Coat. Technol. 2005. V. 191. № 2–3. P. 384–392. https://doi.org/10.1016/j.surfcoat.2004.04.056
Kutschej K., Mayrhofer P.H., Polcik P., Kathrein M., Tessadri R., Mitterer C. Structure, Mechanical and Tribological Properties of Sputtered Ti1 –xAlxN Coatings with 0.5 < x < 0.75 // Surf. Coat. Technol. 2005. V. 200. № 7. P. 2358–2365. https://doi.org/10.1016/j.surfcoat.2004.12.008
Wang D.-Y., Li Y.-W., Ho W.-Y. Deposition of High (Ti,Al)N Hard Coatings by Vacuum arc Evaporation Process // Surf. Coat. Technol. 1999. V. 114. № 2–3. P. 109–113. https://doi.org/10.1016/S0257-8972(99)00020-1
Bressan J.D., Hesse R., Silva E.M., Jr. Abrasive Wear Behavior of High Speed Steel and Hard Metal Coated with TiAlN and TiCN // Wear. 2001. V. 250. № 1–12. P. 561–568. https://doi.org/10.1016/S0043-1648(01)00638-X
Bouzakis K.-D., Michailidis N., Skordaris G., Bouzakis E., Biermann D., M’Saoubi R. Cutting with Coated Tools: Coating Technologies, Characterization Methods and Performance Optimization // CIRP Ann. 2012. V. 61. № 2. P. 703–723. https://doi.org/10.1016/j.cirp.2012.05.006
Sui X., Lin G., Qin X., Yu H., Zhou X., Wang K., Wang Q. Relationship of Microstructure, Mechanical Properties and Titanium Cutting Performance of TiAlN/TiAlSiN Composite Coated Tool // Ceram. Int. 2016. V. 42. № 6. P. 7524–7532. https://doi.org/10.1016/j.ceramint.2016.01.159
Vereschaka A.A., Grigoriev S.N., Sitnikov N.N., Batako A.D. Delamination and Longitudinal Cracking in Multi-Layered Composite Nanostructured Coatings and Their Influence on Cutting Tool Life // Wear. 2017. V. 390–391. P. 209–219. https://doi.org/10.1016/j.wear.2017.07.021
Beake B.D., Ning L., Gey Ch., Veldhuis S.C., Komarov A., Weaver A., Khanna M., Fox-Rabinovich G.S. Wear Performance of Different PVD Coatings during Hardwet Endmilling of H13 Tool Steel // Surf. Coat. Technol. 2015. V. 279. P. 118–125. https://doi.org/10.1016/j.surfcoat.2015.08.038
Анкин В.Н., Блинков И.В., Волхонский А.О., Соболев Н.А., Кратохвил Р.В., Фролов А.Е., Царева С.Г. Ионно-плазменные покрытия Ti–Al–N на режущем твердосплавном инструменте, работающем в условиях постоянных и знакопеременных нагрузок // Изв. вузов. Порошковая металлургия и функциональные покрытия. 2009. № 1. С. 44–52.
Blinkov I.V., Belov D.S., Volkhonskiy A.O., Chernogor A.O., Sergevnin V.S. Hardening ion plasma coatings (Ti, Alx)N (x = 3 at. %) for Carbide Cutting Tools // J. Phys.: Conf. Ser. 2020. V. 1713. P. 012011. https://doi.org/10.1088/1742-6596/1713/1/012011
Блинков И.В., Волхонский А.О., Белов Д.С., Блинков В.И., Скрылёва Е.А., Швындина Н.В. Наноструктурирование и модифицирование свойств вакуумно-дуговых покрытий TiN введением в их состав никеля // Неорган. материалы. 2015. Т. 51. № 2. С. 163–170.
Вайнштейн Б.К. Современная кристаллография (в четырех томах). Т. 1. Симметрия кристаллов. Методы структурной кристаллографии. М.: Наука, 1979. 384 с.
ISO/FDIS14577-1:2002 Металлические материалы – инструментальное индентирование для определения твердости и механических свойств.
Кирюханцев–Корнеев Ф.В. Анализ элементного состава покрытий с использованием высокочастотной оптической эмиссионной спектроскопии тлеющего разряда // Физикохимия поверхности и защита материалов. 2012. Т. 48. № 5. С. 488–494.
Xia Q., Xia H., Ruoff A.L. Pressure Induced Rocksalt Phase of Aluminum Nitride: A Metastable Structure at Ambient Condition // J. Appl. Phys. 1993. V. 73. P. 8198. https://doi.org/10.1063/1.353435
Horling A., Hultman L., Oden M., Sjolen J., Karlsson T. Thermal Stability of arc Evaporated Highaluminum-Content Ti1 –xAlxN Thin Films // J. Vac. Sci. Technol. A. 2002. V. 20. P. 1815–1823. https://doi.org/10.1116/1.1503784
Mayrhofer P.H., Horling A., Karlsson L., Mitterer C., Hultman L. Self-Organized Nanostructures in the Ti–Al–N System // Appl. Phys. Lett. 2003. V. 83. № 10. P. 2049. https://doi.org/10.1063/1.1608464
Donohue L.A., Lewis D.B., Munz W.-D., Stack M.M., Lyon S.B., Wang H.-W., Rafaja D. The Influence of Low Concentrations of Chromium and Yttrium on the Oxidation Behaviour, Residual Stress and Corrosion Performance of TiAlN Hard Coatings on Steel Substrates // Vacuum. 1999. V. 55. № 2. P. 109–114. https://doi.org/10.1016/S0042-207X(99)00135-9
Suh C.-M., Hwang B.-W., Murakami R.-I. Behaviors of Residual Stress and Hightemperature Fatigue Life in Ceramic Coatings Produced by PVD // Mater. Sci. Eng. A. 2003. V. 343. № 1–2. P. 1–7. https://doi.org/10.1016/S0921-5093(02)00327-1
Jaros M., Musil J., Haviar S. Interrelationships among Macrostress, Microstructure and Mechanical Behavior of Sputtered Hard Ti(Al,V)N Films // Mater. Lett. 2019. V. 235. P. 92–96. https://doi.org/10.1016/j.matlet.2018.09.173
Thornton J.A., Hoffman D.W. Stress-Related Effects in Thin Films // Thin Solid Films. 1989. V. 171. № 1. P. 5–31. https://doi.org/10.1016/0040-6090(89)90030-8
Kim J.H., Gu G., Kwon M.-H., Koo M., Kim E.-Y., Kim J.-K., Lee J.S., Suh D.-W. Microstructure and Tensile Properties of Chemically Heterogeneous Steel Consisting of Martensite and Austenite // Acta Mater. 2022. V. 223. P. 117506. https://doi.org/10.1016/j.actamat.2021.117506
Leyland A., Matthews A. On the Signification of the H/E Ratio in Wear Control: a Nanocomposite Coatings Approach to Optimized Tribological Behaviour // Wear. 2000. V. 246. № 1–2. P. 1–11. https://doi.org/10.1016/S0043-1648(00)00488-9
Mannling H.-D., Patil D.S., Moto K., Jilek M., Veprek S. Thermal Stability of Superhard Nanocomposite Coatings Consisting of Immiscible Nitrides // Surf. Coat. Technol. 2001. V. 146–147. P. 263–267. https://doi.org/10.1016/S0257-8972(01)01474-8
Bertoti I. Characterization of Nitride Coatings by XPS // Surf. Coat. Technol. 2002. V. 151–152. P. 194–203. https://doi.org/10.1016/S0257-8972(01)01619-X
Burke A.R., Brown C.R., Bowling W.C., Glaub J.E., Kapsch D., Love C.M., Whitaker R.B., Moddeman W.E. Ignition Mechanism of the Titanium–Boron Pyrotechnic Mixture // Surf. Interface Anal. 1988. V. 11. P. 353–358. https://doi.org/10.1002/sia.740110614
Munz W.-D. Titanium Aluminum Nitride Films: A New Alternative to TiN Coatings // J. Vac. Sci. Technol. A. 1986. V. 4. P. 2717–2725. https://doi.org/10.1116/1.573713
Chen L., Paulitsch J., Du Y., Mayrhofer P.H. Thermal Stability and Oxidation Resistance of Ti–Al–N Coatings // Surf. Coat. Technol. 2012. V. 206. P. 2954–2960. https://doi.org/10.1016/j.surfcoat.2011.12.028
Ковалёв И.А., Огарков А.И, Шокодько А.В., Шевцов С.В., Коновалов А.А., Канныкин С.В., Ашмарин А.А., Кочанов Г.П., Чернявский А.С., Солнцев К.А. Структурные и фазовые превращения в компактной керамике на основе нитрида титана в прцессе высокотемпературного нагрева в газовых средах // Неорган. материалы. 2019. Т. 55. № 8. С. 903–907.
Дополнительные материалы отсутствуют.
Инструменты
Неорганические материалы