Неорганические материалы, 2022, T. 58, № 11, стр. 1249-1260
Ультрапористая субмикронная керамика на основе β-Ca3(PO4)2
О. У. Тошев 1, *, Т. В. Сафронова 1, Ю. С. Миронова 1, А. С. Матвеева 1, Т. Б. Шаталова 1, Я. Ю. Филиппов 1, А. В. Кнотько 1, М. Р. Ахмедов 1, Е. В. Кукуева 2, Ю. С. Лукина 3
1 Московский государственный университет им. М.В. Ломоносова
119991 Москва,
Ленинские горы, 1, Россия
2 Национальный исследовательский центр “Курчатовский институт”
123182 Москва, пл. Академика Курчатова, 1, Россия
3 Национальный медицинский исследовательский центр травматологии
и ортопедии им. Н.Н. Приорова
127299 Москва, ул. Приорова, 10, Россия
* E-mail: otabektoshev0995@mail.ru
Поступила в редакцию 06.05.2022
После доработки 18.07.2022
Принята к публикации 22.07.2022
- EDN: SSPNTY
- DOI: 10.31857/S0002337X22110148
Аннотация
Керамика на основе β-трикальциевого фосфата β-Ca3(PO4)2 с относительной плотностью 20–21%, размером зерна 200–600 нм и прочностью на сжатие 1.6–1.8 МПа получена обжигом при 1000°С цементного камня, приготовленного из порошковой смеси с мольным соотношением Са/Р = 1.5, включающей гидроксиапатит Ca10(PO4)6(OH)2, тетрагидрат цитрата кальция Ca3(C6H5O7)2·4H2O и моногидрат дигидрофосфата кальция Ca(H2PO4)2·H2O. В качестве жидкости затворения, инициирующей реакцию химического связывания в этой порошковой смеси, использовали дистиллированную воду. Фазовый состав цементного камня был представлен брушитом CaHPO4·2H2O, а также исходными компонентами, не вступившими реакцию. Присутствие пластинчатых частиц пирофосфата кальция Ca2P2O7, образовавшихся из пластинчатых частиц брушита CaHPO4⋅2H2O, сдерживало уплотнение керамики при обжиге, обуславливая формирование ультрапористой структуры. Субмикронная микроструктура и фазовый состав керамики на основе β-Ca3(PO4)2 сформировались в основном как результат гетерофазных взаимодействий между продуктами термического разложения компонентов цементного камня. Ультрапористая субмикронная биосовместимая и биорезорбируемая керамика на основе β-Ca3(PO4)2, обладающая достаточной прочностью, может быть рекомендована для применения в регенеративной медицине для лечения дефектов костной ткани.
ВВЕДЕНИЕ
Создание биосовместимых неорганических материалов на основе фосфатов кальция для костных имплантатов в настоящее время остается актуальным направлением научных исследований [1, 2]. Гидроксиапатит Ca10(PO4)6(OH)2 (ГАП), трикальциевый фосфат β-Ca3(PO4)2 (β-ТКФ) и пирофосфат кальция β-Са2Р2О7 (β-ПФК) являются основными компонентами биосовместимой кальцийфосфатной керамики, применяемой при лечении дефектов костной ткани [3–6]. Материалы на основе β-ТКФ представляют большой практический интерес для использования в регенеративной медицине [7, 8]. Растворимость β-ТКФ существенно выше, чем растворимость ГАП, и материалы на основе β-ТКФ способны резорбироваться при имплантации [2, 9, 10].
Существуют четыре полиморфных модификаций ТКФ: α, α', β и γ (фаза высокого давления) [11, 12]. Фаза α' не представляет практического интереса, поскольку существует только при температурах выше 1430°C, а при охлаждении ниже этой температуры переходит в α-ТКФ. Фаза β-ТКФ стабильна при комнатной температуре, а при ~1125°C переходит в более высокотемпературную модификацию α-ТКФ [13]. Материалы на основе α-ТКФ и β-ТКФ в настоящее время находят применение в стоматологии, челюстно-лицевой хирургии и ортопедии; β-ТКФ является компонентом нескольких коммерческих моно- или двухфазных керамических материалов, а α-ТКФ входит в состав порошковых смесей для получения различных костных цементов гидравлического твердения [14–16]. Использование керамических материалов (как плотных, так и пористых) на основе α-ТКФ нежелательно, поскольку при гидролизе α-ТКФ, обладающего большей растворимостью чем β-ТКФ, происходит образование фосфорной кислоты и среда вокруг такого имплантата приобретает рН, не приемлемый для живого организма [17, 18].
Существуют два подхода к синтезу ТКФ. ТКФ может быть получен в результате термической конверсии или гетерофазной реакции при нагревании. Так, например, ТКФ может быть получен разложением аморфного фосфата кальция или Са-дефицитного ГАП с мольным соотношением Са/Р, равным 1.5 [19–21]. В диапазоне температур 700–800°С Ca-дефицитный ГАП в процессе дегидратации теряет воду и переходит в β-ТКФ в соответствии с реакциями (1) или (2) [22]:
(1)
${\text{C}}{{{\text{a}}}_{{\text{9}}}}\left( {{\text{HP}}{{{\text{O}}}_{{\text{4}}}}} \right){{\left( {{\text{P}}{{{\text{O}}}_{{\text{4}}}}} \right)}_{{\text{5}}}}{\text{OH}} \to {\text{3C}}{{{\text{a}}}_{{\text{3}}}}{{\left( {{\text{P}}{{{\text{O}}}_{{\text{4}}}}} \right)}_{{\text{2}}}}{\text{ + }}{{{\text{H}}}_{{\text{2}}}}{\text{O}}{\kern 1pt} \uparrow ,$(2)
$\begin{gathered} {\text{C}}{{{\text{a}}}_{{10 - x}}}{{\left( {{\text{HP}}{{{\text{O}}}_{{\text{4}}}}} \right)}_{x}}{{\left( {{\text{P}}{{{\text{O}}}_{{\text{4}}}}} \right)}_{{6 - x}}}{{\left( {{\text{OH}}} \right)}_{{2 - x}}} \to \\ \to \left( {1 - x} \right){\text{C}}{{{\text{a}}}_{{{\text{10}}}}}{{\left( {{\text{P}}{{{\text{O}}}_{{\text{4}}}}} \right)}_{{\text{6}}}}{{\left( {{\text{OH}}} \right)}_{2}} + \\ + \,\,3x{\text{C}}{{{\text{a}}}_{{\text{3}}}}{{\left( {{\text{P}}{{{\text{O}}}_{{\text{4}}}}} \right)}_{{\text{2}}}} + x{{{\text{H}}}_{{\text{2}}}}{\text{O}}{\text{.}} \\ \end{gathered} $ТКФ [23] можно получить из порошковой смеси с заданным мольным соотношением Са/Р = 1.5, включающей компоненты-прекурсоры, для каждого из которых мольное соотношение Са/Р больше и меньше 1.5. ТКФ может быть получен из двухкомпонентных порошковых смесей, включающих CaO(Са/Р = ∞) и Ca2P2O7(Са/Р = 1); CaO(Са/Р = = ∞) и Ca(PO3)2(Са/Р = 0.5); Ca4P2O9(Са/Р = 2) и Ca2P2O7(Са/Р = 1); Ca4P2O9(Са/Р = 2) и Ca(PO3)2(Са/Р = 0.5). ТКФ может быть получен и из порошковых смесей, включающих ГАП (Са/Р = 1.67) и фосфаты кальция с мольным соотношением Са/Р меньше 1.5: Ca10(PO4)6(OH)2 и Ca2P2O7; Ca10(PO4)6(OH)2 и Ca(PO3)2. В качестве прекурсоров СаО при сочетании с Ca2P2O7 или Ca(PO3)2 могут быть использованы следующие соли кальция: CaCO3, Ca(NO3)2, Ca(CH3COO)2 и др. Прекурсорами оксида фосфора при сочетании с СаО, Ca4P2O9 или ГАП могут быть различные фосфорные кислоты: ортофосфорная H3PO4, метафосфорная HPO3 и пирофосфорная H4P2O7, а также соответствующие соли аммония [23].
ТКФ можно получить из порошковой смеси, включающей монетит CaHPO4 (прекурсор ПФК) и карбонат кальция CaCO3 (прекурсор СаО) (реакция (3)) [2, 24], или из порошковой смеси, включающей ПФК и карбонат кальция CaCO3 (реакция (4)) в ходе твердофазного синтеза [25–27]:
(3)
${\text{CaC}}{{{\text{O}}}_{{\text{3}}}}{\text{ + 2CaHP}}{{{\text{O}}}_{{\text{4}}}} \to {\text{C}}{{{\text{a}}}_{{\text{3}}}}{{\left( {{\text{P}}{{{\text{O}}}_{{\text{4}}}}} \right)}_{{\text{2}}}}{\text{ + }}{{{\text{H}}}_{{\text{2}}}}{\text{O}}{\kern 1pt} \uparrow ,$(4)
${\text{CaC}}{{{\text{O}}}_{{\text{3}}}}{\text{ + C}}{{{\text{a}}}_{{\text{2}}}}{{{\text{P}}}_{{\text{2}}}}{{{\text{O}}}_{7}} \to {\text{C}}{{{\text{a}}}_{{\text{3}}}}{{\left( {{\text{P}}{{{\text{O}}}_{{\text{4}}}}} \right)}_{2}} + {\text{C}}{{{\text{O}}}_{2}}{\kern 1pt} \uparrow .$ТКФ также может быть получен в результате взаимодействия гидрофосфата аммония (NH4)2HPO4 и карбоната кальция CaCO3 в соответствии с реакцией [28]
(5)
$\begin{gathered} 3{\text{CaC}}{{{\text{O}}}_{{\text{3}}}}{\text{ + 2}}{{\left( {{\text{N}}{{{\text{H}}}_{{\text{4}}}}} \right)}_{{\text{2}}}}{\text{HP}}{{{\text{O}}}_{{\text{4}}}} \to \\ \to \,\,{\text{C}}{{{\text{a}}}_{{\text{3}}}}{{\left( {{\text{P}}{{{\text{O}}}_{{\text{4}}}}} \right)}_{2}} + 4{\text{N}}{{{\text{H}}}_{{\text{3}}}}{\text{ + 3}}{{{\text{H}}}_{{\text{2}}}}{\text{O + 3C}}{{{\text{O}}}_{{\text{2}}}}{\kern 1pt} \uparrow . \\ \end{gathered} $Пористые керамические материалы можно классифицировать по пористости и плотности на низкоплотные (пористость 30–45%), легковесы (пористость 45–75%) и ультрапористые (пористость ≥75%) [29]. Современные керамические материалы для регенеративной медицины должны обладать значительной общей (≥40–50%) и при этом бимодальной пористостью. Первая мода пор (≥100 мкм) необходима для обеспечения остеокондуктивности материала [30]. Вторая мода (≈1–10 мкм) необходима, чтобы костные клетки могли закрепиться на шероховатой поверхности импланта. Существует несколько методов [31] получения макропористых материалов для костных имплантов: 1) метод удаляемых добавок [32]; 2) метод реплики, предполагающий пропитку органической (полиуретановой) пены суспензией неорганического порошка и последующий обжиг [33]; 3) метод вспенивания суспензий [34, 35]; 4) спекание порошков стекла, которые содержат порообразующие добавки (карбонаты) в количестве 1–5 мас. % [36, 37]. Для создания шероховатой (микропористой) поверхности керамического материала используют незавершенное спекание [38], химическое травление [39], а также порошковые смеси, включающие столбчатые [40] или пластинчатые [41] частицы, из-за своей формы и расположения препятствующие уплотнению при спекании.
Существуют различные подходы к получению керамики с субмикронным размером зерен. Наследование микроструктурой керамики микроструктуры исходного порошка предполагает использование тонкого химического синтеза для получения наноразмерных порошков [42]. Для получения керамики, микроструктура которой сложена субмикронными зернами, используют порошки эвтектического состава [43]. Кроме того, возможно применение специальных методов спекания, таких как горячее прессование [44] или электродуговое спекание [45]. Сдерживание роста зерен возможно при введении в состав исходного порошка высокотемпературных поверхностно-активных веществ [46–48]. Наиболее известным способом сдерживания роста зерен в керамических материалах является создание условий, при которых на поверхности зерен происходит гетерофазная (твердофазная) реакция [27, 33, 49].
Преимуществом пластического формования является возможность создания керамических изделий сложной формы. Пластическое формование может быть осуществлено c применением экструзии [50]. Подвижные пластические пасты могут быть использованы для экструзионного послойного формования предкерамических порошковых заготовок [51, 52]. Твердеющие водные суспензии, в которых протекают реакции химического связывания, также могут быть использованы для пластического формования предкерамических образцов сложной формы [53–57]. В этом случае синтез частиц брушита и монетита (прекурсоров керамической фазы ПФК) в структуре предкерамического образца происходит непосредственно при формовании из пасты, включающей β-ТКФ и Ca(H2PO4)2⋅H2O [53] или Ca3(C6H5O7)2⋅4H2O и Ca(H2PO4)2⋅H2O [54–56]. Керамика в двухкомпонентной системе Ca2P2O7–Ca(PO3)2 [53–56], фазовый состав которой в основном представлен β-ПФК, была получена обжигом цементного камня, сформованного из таких паст.
Цель настоящей работы заключалась в получении биосовместимой высокопористой субмикронной керамики на основе β-ТКФ обжигом цементного камня, включающего частицы с пластинчатой морфологией, способные сдерживать уплотнение при спекании керамики для создания микропористости. Для сдерживания роста зерен и сохранения их субмикронного размера в микроструктуре керамики было запланировано создание условий для протекания гетерофазных реакций на их поверхности.
ЭКСПЕРИМЕНТАЛЬНАЯ ЧАСТЬ
Исходные компоненты. В качестве исходных компонентов были использованы порошковые смеси, включающие тетрагидрат цитрата кальция Ca3(C6H5O7)2⋅4H2O (CAS № 5785-44-4, puriss. p.a. ≥ ≥ 85%, Sigma-Aldrich, Германия), моногидрат дигидрофосфата кальция Ca(H2PO4)2·H2O (CAS № 10031-30-8, puriss. 99%, Sigma-Aldrich, Германия) и ГАП Ca10(PO4)6(OH)2 (CAS № 1306-06-5, puriss. p.a. ≥ 90%, RiedeldeHaen, Sigma-Aldrich Laborchemikalien, 04238, lot 70080, Германия). Каждый порошок до приготовления исходной смеси дезагрегировали в планетарной мельнице. Порошки Ca3(C6H5O7)2⋅4H2O, Ca(H2PO4)2⋅H2O и Ca10(PO4)6(OH)2 помещали в емкости из диоксида циркония. К каждому порошку добавляли мелющие тела из диоксида циркония при соотношении масса порошка : масса мелющих тел, равном 1 : 5. После добавления ацетона (ГОСТ 2603-79) емкости закрывали и закрепляли в планетарной мельнице. Продолжительность дезагрегации порошков при скорости вращения 600 об./мин составила 15 мин. После завершения обработки в планетарной мельнице порошки сушили на воздухе при комнатной температуре в течение 24 ч. После сушки порошки пропускали через сито с размером ячеек 400 мкм.
Подготовка порошковой смеси для получения образцов цементного камня. Количество компонентов порошковой смеси для получения образца цементного камня рассчитывали по реакции
(6)
$\begin{gathered} {\text{C}}{{{\text{а}}}_{{{\text{10}}}}}{{{\text{(P}}{{{\text{O}}}_{{\text{4}}}}{\text{)}}}_{{\text{6}}}}{{{\text{(OH)}}}_{{\text{2}}}}{\text{ + C}}{{{\text{a}}}_{{\text{3}}}}{{{\text{(}}{{{\text{C}}}_{{\text{6}}}}{{{\text{H}}}_{{\text{5}}}}{{{\text{O}}}_{{\text{7}}}})}_{2}}{\kern 1pt} \cdot {\kern 1pt} 4{{{\text{H}}}_{{\text{2}}}}{\text{O}} + \\ + {\text{ }}2{\text{Ca(}}{{{\text{H}}}_{{\text{2}}}}{\text{P}}{{{\text{O}}}_{{\text{4}}}}{{)}_{2}}{\kern 1pt} \cdot {\kern 1pt} {{{\text{H}}}_{{\text{2}}}}{\text{O}} + 9{{{\text{O}}}_{2}} \to \\ \to 5{\text{C}}{{{\text{a}}}_{{\text{3}}}}{{{\text{(P}}{{{\text{O}}}_{4}})}_{2}} + \,\,12{\text{C}}{{{\text{O}}}_{2}}{\kern 1pt} \uparrow + \,\,16{{{\text{H}}}_{{\text{2}}}}{\text{O}}{\text{.}} \\ \end{gathered} $Порошковая смесь для получения предкерамического образца цементного камня содержала компоненты, в которых мольное соотношение Са/Р отличалось от соотношения Са/Р = 1.5 для ТКФ в бóльшую (Cа10(PO4)6(OH)2, Са/Р = 1.67; Ca3(C6H5O7)2·4H2O, Са/Р = ∞) и меньшую сторону (Ca(H2PO4)2·H2O, Са/Р = 0.5).
Гомогенизацию порошковой смеси осуществляли многократным пересыпанием дозированных компонентов через сито с размером ячеек 400 мкм.
Получение образцов цементного камня. К гомогенизированной смеси, включающей Ca3(C6H5O7)2⋅4H2O, Ca(H2PO4)2·H2O и Ca10(PO4)6(OH)2, добавляли жидкость затворения (дистиллированную воду) при соотношении порошковая смесь : жидкость затворения = 1 : 1. Данное соотношение обеспечивало равномерное заполнение формы пастой.
Пластическое формование образцов цементного камня в форме балочек размером 30 × 10 × 10 мм из высококонцентрированных суспензий (паст) осуществляли с использованием латексных форм. Для определения прочности керамики готовили образцы цементного камня в форме цилиндров с отношением диаметра к высоте 1 : 2 (диаметр 6 мм, высота 12 мм) с использованием тефлоновой формы.
После формования образцы цементного камня сушили в течение недели. После сушки образцы взвешивали и обмеряли с использованием штангенциркуля для определения геометрической плотности и усадки при сушке относительно размеров формы.
Получение керамики. Образцы цементного камня после сушки обжигали в интервале 800–1100°С с выдержкой при конечной температуре 2 ч. Скорость нагрева 5°C/мин, охлаждение с печью.
Методы исследования. Рентгенофазовый анализ (РФА) образцов цементного камня после формования и сушки и образцов керамики после обжига проводили на дифрактометре Rigaku D/Max-2500 с вращающимся анодом (Япония) с использованием CuKα-излучения. Для определения фазового состава образцов использовали базу данных ICDD PDF2 [58], а также программу Match!3 (https://www.crystalimpact.com/). Программа Match!3 была использована для определения количественного соотношения фаз в образцах керамики после обжига при различных температурах.
Синхронный термический анализ (ТА) и дифференциальную сканирующую калориметрию (ДСК) выполняли на термоанализаторе NETZSCH STA 449 F3 Jupiter (NETZSCH, Германия) в интервале температур 40–1000°С при скорости нагрева 10°С/мин. Масса образца составляла не менее 10 мг. Состав образующейся при разложении образцов газовой фазы определяли при помощи квадрупольного масс-спектрометра QMS 403 Quadro (NETZSCH, Германия), совмещенного с термоанализатором NETZSCH STA 449 F3 Jupiter. Масс-спектры (МС) записывали для массовых чисел 18 (Н2О) и 44 (СО2).
Микроструктуру образцов цементного камня и керамики исследовали методом растровой электронной микроскопии. При использовании электронного микроскопа LEO SUPRA 50VP (Carl Zeiss, Германия; автоэмиссионный источник) съемку осуществляли при ускоряющем напряжении 3–21 кВ во вторичных электронах (детектор SE2), а на поверхность образцов напыляли слой хрома (до 15 нм). При использовании электронно-ионного микроскопа Helios Nanolab 600i (FEI, США) исследования проводили на образцах без напыления при ускоряющем напряжении 2 кВ.
Линейную усадку и геометрическую плотность образцов керамики определяли, измерив их массу и размеры (с точностью ±0.05мм) до и после обжига.
Механические испытания проводили, используя цилиндрические образцы керамики с отношением диаметра к высоте 1 : 2 после обжига при 1000°С. Образцы подвергали одноосному (вдоль оси цилиндра) сжатию со скоростью деформации 1 мм/мин. Испытания проводили на универсальной испытательной машине Р-05, снабженной многоканальной измерительной системой Spider (Германия).
РЕЗУЛЬТАТЫ И ОБСУЖДЕНИЕ
Данные РФА для исходных компонентов и образца цементного камня на их основе представлены на рис. 1. Основной фазой цементного камня после формования и сушки являлся брушит CaHPO4⋅2H2O, что связано с протеканием реакций химического связывания
(7)
$\begin{gathered} {\text{C}}{{{\text{a}}}_{{{\text{10}}}}}{{{\text{(P}}{{{\text{O}}}_{{\text{4}}}}{\text{)}}}_{{\text{6}}}}{{{\text{(OH)}}}_{{\text{2}}}}{\text{ + 4Ca(}}{{{\text{H}}}_{{\text{2}}}}{\text{P}}{{{\text{O}}}_{{\text{4}}}}{{{\text{)}}}_{{\text{2}}}}{\kern 1pt} \cdot {\kern 1pt} {{{\text{H}}}_{{\text{2}}}}{\text{O + }} \\ {\text{ + }}\,\,{\text{22}}{{{\text{H}}}_{{\text{2}}}}{\text{O}} \to 1{\text{4CaHP}}{{{\text{O}}}_{{\text{4}}}}{\kern 1pt} \cdot {\kern 1pt} {\text{2}}{{{\text{H}}}_{{\text{2}}}}{\text{O,}} \\ \end{gathered} $(8)
$\begin{gathered} {\text{C}}{{{\text{a}}}_{{\text{3}}}}{{{\text{(}}{{{\text{C}}}_{{\text{6}}}}{{{\text{H}}}_{{\text{5}}}}{{{\text{O}}}_{{\text{7}}}}{\text{)}}}_{{\text{2}}}}\cdot4{{{\text{H}}}_{{\text{2}}}}{\text{O + 3Ca(}}{{{\text{H}}}_{{\text{2}}}}{\text{P}}{{{\text{O}}}_{{\text{4}}}}{{)}_{2}}\cdot{{{\text{H}}}_{{\text{2}}}}{\text{O}} + \\ + \,\,5{{{\text{Н}}}_{{\text{2}}}}{\text{О}} \to 6{\text{CaHP}}{{{\text{O}}}_{4}}\cdot2{{{\text{H}}}_{{\text{2}}}}{\text{O}} + 2{{{\text{C}}}_{{\text{6}}}}{{{\text{H}}}_{{\text{8}}}}{{{\text{O}}}_{7}}. \\ \end{gathered} $Рис. 1.
Дифрактограммы исходных компонентов и образца цементного камня, полученного при добавлении жидкости затворения (воды) к порошковой смеси, включающей Ca10(PO4)6(OH)2, Ca3(C6H5O7)2⋅4H2O и Ca(H2PO4)2⋅H2O: ⚪ – Ca10(PO4)6(OH)2 (карточка PDF 9-432), c – Ca3(C6H5O7)2·4H2O (карточка PDF 28-2003), * – Ca(H2PO4)2·H2O (карточка PDF 9-347), b – CaHPO4·2H2O (карточка PDF 9-77).
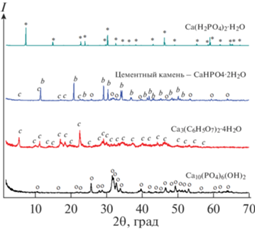
Для данных реакций соотношение Са/Р составляет 1. В настоящей работе соотношение Са/Р в порошковой смеси было задано как 1.5, что предполагает сохранение в образце цементного камня Ca10(PO4)6(OH)2 и Ca3(C6H5O7)2·4H2O. Данные РФА подтверждают присутствие этих компонентов в образцах цементного камня.
Паста, включающая ГАП Ca10(PO4)6(OH)2, Ca3(C6H5O7)2·4H2O, Ca(H2PO4)2·H2O и воду, обладала подвижностью в течение продолжительного периода (30–40 мин) до начала схватывания. Следует отметить, что обычно формирование брушитного цементного камня после добавления воды к цементному порошку происходит достаточно быстро, в течение 5–10 мин [59]. Увеличение сроков схватывания цементной пасты, использованной в данной работе, по всей видимости, связано с образованием комплексов между цитрат-ионом ${{{\text{C}}}_{{\text{3}}}}{{{\text{H}}}_{{\text{5}}}}{\text{O}}\left( {{\text{COO}}} \right)_{3}^{{3 - }}$ и ионом кальция Ca2+ [60, 61]. Ранее возможность увеличения продолжительности периода схватывания была показана для цементной пасты, в состав которой входили Ca3(C6H5O7)2⋅4H2O и Ca(H2PO4)2⋅H2O [54–56].
После пластического формования из высококонцентрированных суспензий, включающих ГАП Ca10(PO4)6(OH)2, Ca3(C6H5O7)2·4H2O и Ca(H2PO4)2·H2O, и сушки линейная усадка образцов цементного камня относительно размеров использованной формы составила ~1%. Были получены образцы цементного камня с плотностью 0.68–0.70 г/см3.
Микроструктура образца цементного камня, полученного в результате взаимодействия порошковой смеси, включающей Ca10(PO4)6(OH)2, Ca3(C6H5O7)2⋅4H2O и Ca(H2PO4)2⋅H2O, и жидкости затворения (дистиллированной воды) представлена на рис. 2. На микрофотографиях можно видеть в основном частицы с пластинчатой морфологией, характерной для брушита CaHPO4·2H2O [62, 63], частицы достигают в длину 5–10 мкм и в толщину 300–500 нм. Кроме пластин, на микрофотографиях присутствуют агломераты размером 4–5 мкм, состоящие из частиц размером 200–250 нм. По всей видимости, это частицы ГАП Ca10(PO4)6(OH)2.
Рис. 2.
Микрофотографии образца цементного камня, полученного при взаимодействии жидкости затворения (дистиллированной воды) с порошковой смесью, включающей ГАП Ca10(PO4)6(OH)2, Ca3(C6H5O7)2⋅4H2O и Ca(H2PO4)2⋅H2O.
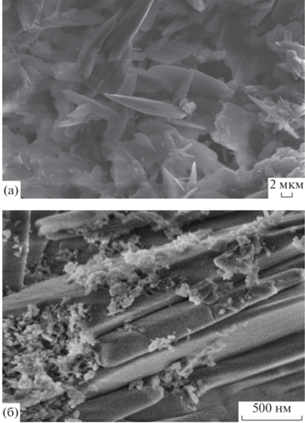
Кривые ТГ и ДСК исследуемого образца цементного камня при нагревании от 40 до 1000°С представлены на рис. 3. Кривые МС выделяющихся при нагревании образца цементного камня газов (m/Z = 18 (H2O) и m/Z = 44 (CO2)) представлены на рис. 4.
Рис. 3.
Результаты ТА образца цементного камня, полученного взаимодействием жидкости затворения (дистиллированной воды) с порошковой смесью, включающей ГАП Ca10(PO4)6(OH)2, Ca3(C6H5O7)2⋅4H2O и Ca3(C6H5O7)2⋅4H2O.
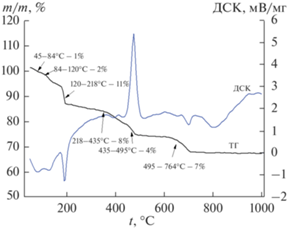
Рис. 4.
Масс-спектры выделяющихся газов с m/Z = 18 и m/Z = 44 при нагревании образца цементного камня, полученного взаимодействием жидкости затворения (дистиллированной воды) с порошковой смесью, включающей ГАП Ca10(PO4)6(OH)2, Ca3(C6H5O7)2⋅4H2O и Ca3(C6H5O7)2⋅4H2O.
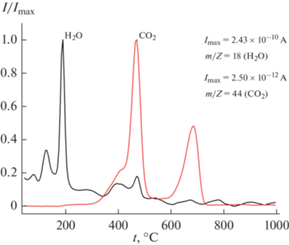
Общая потеря массы образца цементного камня при нагревании до 1000°С составила 33%. На кривой потери массы есть шесть заметных ступеней. Потеря массы на первой ступени оценивается в 1% (45–84°С), на втором этапе – в 2% (84–120°С); на третьем – в 11% (120–218°С), на четвертом – в 8% (218–435°С); на пятом – в 4% (435–495°С); на шестом – в 7% (495–764°С).
На кривой МС для m/Z = 18 (H2O) можно наблюдать три пика при тех же температурах, что и на кривых ДСК (в интервале 50–300°С). На кривой ДСК присутствуют три эндотермических пика: при 76, 124 и 190°С, соответствующих пикам на кривой МС. В этом интервале температур возможно протекание термического разложения Ca3(C6H5O7)2·4H2O и CaHPO4·2H2O с образованием безводного цитрата кальция Ca3(C6H5O7)2 и монетита CaHPO4:
(9)
$\begin{gathered} {\text{C}}{{{\text{a}}}_{{\text{3}}}}{{{\text{(}}{{{\text{C}}}_{{\text{6}}}}{{{\text{H}}}_{{\text{5}}}}{{{\text{O}}}_{{\text{7}}}})}_{2}}\cdot4{{{\text{H}}}_{{\text{2}}}}{\text{O}} \to \\ \to \,\,{\text{C}}{{{\text{a}}}_{{\text{3}}}}{{{\text{(}}{{{\text{C}}}_{{\text{6}}}}{{{\text{H}}}_{{\text{5}}}}{{{\text{O}}}_{{\text{7}}}})}_{2}}\cdot2{{{\text{H}}}_{{\text{2}}}}{\text{O}} \to {\text{C}}{{{\text{a}}}_{{\text{3}}}}{{{\text{(}}{{{\text{C}}}_{{\text{6}}}}{{{\text{H}}}_{{\text{5}}}}{{{\text{O}}}_{{\text{7}}}})}_{2}}, \\ \end{gathered} $(10)
${\text{CaHP}}{{{\text{O}}}_{4}}\cdot2{{{\text{H}}}_{{\text{2}}}}{\text{O}} \to {\text{CaHP}}{{{\text{O}}}_{4}} + 2{{{\text{H}}}_{{\text{2}}}}{\text{O}}{\text{.}}$По литературным данным, термическое разложение Ca3(C6H5O7)2·4H2O (реакция (9)) происходит с отщеплением воды на каждой ступени, т.е. при 85 и 145°С [64], а термическое разложение брушита CaHPO4·2H2O – при 200°С (реакция (10)) [65].
В интервале температур от 400 до 450°С монетит CaHPO4 подвергается дегидратации с образованием ПФК γ-Ca2P2O7, что подтверждается пиком (425°С) на кривой МС (рис. 4)
(11)
${\text{CaHP}}{{{\text{O}}}_{4}} \to {\text{C}}{{{\text{a}}}_{{\text{2}}}}{{{\text{P}}}_{{\text{2}}}}{{{\text{O}}}_{7}} + {{{\text{H}}}_{{\text{2}}}}{\text{O}}{\text{.}}$Термическое разложение безводного цитрата кальция Ca3(C6H5O7)2 с образованием карбоната кальция CaCO3 происходит с выделением тепла (пик при ~460°С, кривая ДСК, рис. 3) по одной из следующих реакции:
(12)
${\text{C}}{{{\text{a}}}_{{\text{3}}}}{{\left( {{{{\text{C}}}_{{\text{6}}}}{{{\text{H}}}_{{\text{5}}}}{{{\text{O}}}_{{\text{7}}}}} \right)}_{2}} \to {\text{3CaC}}{{{\text{O}}}_{3}} + 5{{{\text{H}}}_{{\text{2}}}}{\text{O}} + 9{\text{C,}}$(13)
$\begin{gathered} {\text{C}}{{{\text{a}}}_{{\text{3}}}}{{\left( {{{{\text{C}}}_{{\text{6}}}}{{{\text{H}}}_{{\text{5}}}}{{{\text{O}}}_{{\text{7}}}}} \right)}_{{\text{2}}}} + {\text{9}}{{{\text{О}}}_{2}} \to \\ \to 3{\text{CaC}}{{{\text{O}}}_{3}} + 5{{{\text{H}}}_{{\text{2}}}}{\text{O}} + 9{\text{C}}{{{\text{О}}}_{{\text{2}}}}. \\ \end{gathered} $На кривой МС для m/Z = 44 в интервале 435–495°C присутствует пик при 465°С, отражающий выделение СО2, для m/Z = 18 (H2O) – пик при 470°С в интервале 440–510°С.
Если бы углерод образовывался в результате реакции (12), то естественным образом не мог бы оставаться в элементарной форме при такой высокой температуре (выше 340°C), особенно в присутствии атмосферного кислорода. Следовательно, он должен был превратиться в CO и/или CO2, как это отражено реакцией (13).
На кривой МС для m/Z = 44 в интервале температур 585–764°C присутствует пик при 685°С (рис. 4). На кривой ТГ (рис. 3) в этом интервале наблюдается уменьшение массы образца, которое, по всей видимости, связано с разложением CaCO3 с образованием оксида кальция и CO2
Одновременное присутствие в образце CaCO3 и Ca2P2O7 позволяет предположить и возможность протекания реакции, сопровождающейся выделением СО2.
(15)
${\text{CaC}}{{{\text{O}}}_{{\text{3}}}} + {\text{C}}{{{\text{a}}}_{{\text{2}}}}{{{\text{P}}}_{{\text{2}}}}{{{\text{O}}}_{7}} \to {\text{C}}{{{\text{a}}}_{{\text{3}}}}{{{\text{(P}}{{{\text{O}}}_{4}})}_{2}} + {\text{C}}{{{\text{O}}}_{{\text{2}}}}.$В отсутствие ПФК Ca2P2O7 разложение CaCO3 происходит при более высоких температурах – в интервале 615–845°С с пиком потери массы при 800°С [66].
На кривой ДСК в области 750–850°С присутствует эндотермический пик. В этом интервале температур возможно протекание гетерофазного взаимодействия между продуктами термической деструкции компонентов цементного камня, а именно, CaO c Ca2P2O7 с образованием β-ТКФ, что согласуется с данными [67]:
(16)
${\text{C}}{{{\text{a}}}_{{\text{2}}}}{{{\text{P}}}_{{\text{2}}}}{{{\text{O}}}_{7}} + {\text{CaO}} \to {\text{C}}{{{\text{a}}}_{{\text{3}}}}{{{\text{(P}}{{{\text{O}}}_{4}})}_{2}}.$Данные РФА образцов керамики после обжига в диапазоне температур 800–1100°C показаны на рис. 5. Количественное соотношение фаз в керамике после обжига в интервале температур 800–1100°С, определенное с использованием программы Match!3 (https://www.crystalimpact.com/), представлено на рис. 6.
Рис. 5.
Данные РФА для образцов керамики после обжига при 800, 900, 1000, 1100°C: + – β-Ca3(PO4)2 (карточка PDF 9-169), v – β-Ca2P2O7 (карточка PDF 9-346), @ – CaO (карточка PDF 37-1497).
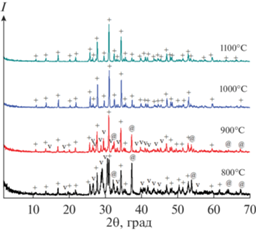
Рис. 6.
Температурные зависимости массового содержания фаз в образцах керамики, полученных обжигом цементного камня.
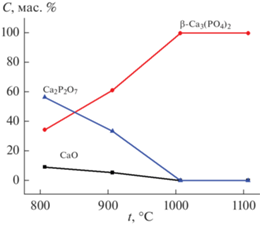
В температурном интервале 800–900°С, по данным РФА, присутствовали фазы: β-ТКФ, β-ПФК и CaO. С ростом температуры обжига от 800 до 1000°С содержание β-ТКФ в керамике увеличивалось, а содержание β-ПФК и СаО уменьшалось. Образование β-Ca2P2O7 происходило в результате фазового перехода из γ-Ca2P2O7, который, по данным [68], протекает при ~700°С. Фаза β‑Ca3(PO4)2 в интервале 800–1000°С формировалась в результате взаимодействия продуктов термической деструкции компонентов цементного камня, а именно, в результате взаимодействия СаО и β-ПФК. Образование β-ТКФ происходило в соответствии с реакциями (16) и (17). При этом, как было показано ранее [68], взаимодействие ГАП и ПФК в соответствии с реакцией
(17)
$\begin{gathered} {\text{C}}{{{\text{a}}}_{{{\text{10}}}}}{{{\text{(P}}{{{\text{O}}}_{{\text{4}}}}{\text{)}}}_{{\text{6}}}}{{{\text{(OH}})}_{2}} + {\text{C}}{{{\text{a}}}_{{\text{2}}}}{{{\text{P}}}_{{\text{2}}}}{{{\text{O}}}_{7}} \to \\ \to \,\,4{\text{C}}{{{\text{a}}}_{{\text{3}}}}{{{\text{(P}}{{{\text{O}}}_{4}})}_{2}} + {{{\text{Н}}}_{{\text{2}}}}{\text{О}}{\kern 1pt} \uparrow \\ \end{gathered} $В диапазоне температур 1000–1100°C фазовый состав образцов керамики, полученных обжигом цементного камня, был представлен только β-ТКФ.
Геометрическая плотность керамических материалов показана на рис. 7. После обжига при 800°С плотность керамики составляла 0.51 г/см3. Плотность керамики по сравнению с плотностью цементного камня уменьшилась, что обусловлено уменьшением массы образца из-за разложения компонентов цементного камня при нагревании при незначительном уменьшении его геометрических размеров (рис. 8). При увеличении температуры обжига от 900 до 1100°С плотность керамики возрастала от 0.55 до 0.70 г/см3 (17.6—22.4% относительно плотности β-ТКФ, равной 3.14 г/см3), при этом усадка образцов составила 5.5–14.1%.
Рис. 7.
Геометрическая плотность образцов керамики, полученных обжигом цементного камня в интервале температур 800–1100°C.
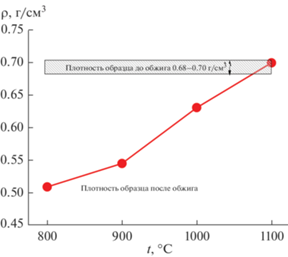
Рис. 8.
Линейная усадка образцов цементного камня после формования относительно размеров формы, образцов керамики после обжига в интервале 800–1100°C и общая усадка после формования и обжига относительно размеров формы.
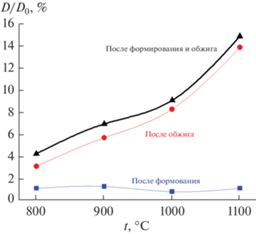
Образцы керамики после обжига при 900°С не обладали достаточной прочностью, а, по данным РФА (рис. 5), формирование β-ТКФ было не завершено, поскольку присутствовали β-Ca2P2O7 и CaO.
Микроструктура образцов керамики, фазовый состав которых представлен β-ТКФ, показана на рис. 9 (температура обжига 1000°С) и на рис. 10 (температура обжига 1100°С). Микроструктура керамического образца, обожженного при 1000°С (рис. 9), состояла из поликристаллических пластинчатых и дугообразных листов толщиной 1.5–2 мкм, образованных плотно спеченными зернами с размером 200–300 нм. Ажурная структура керамики содержит поры размером 4–10 мкм. Некоторые слои и пластины содержали незначительное количество пор размером ~200 нм.
Рис. 9.
Микрофотографии скола образца керамики, фазовый состав которой представлен β-Ca3(PO4)2, после обжига при 1000°C.
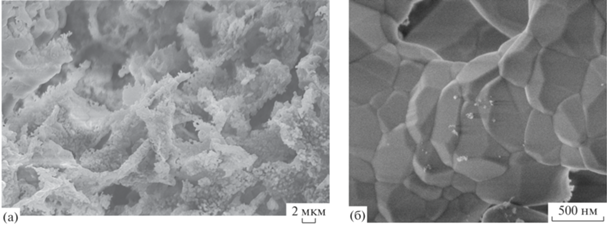
Рис. 10.
Микрофотографии скола образца керамики, фазовый состав которого представлен β-Ca3(PO4)2, после обжига при 1100°C.
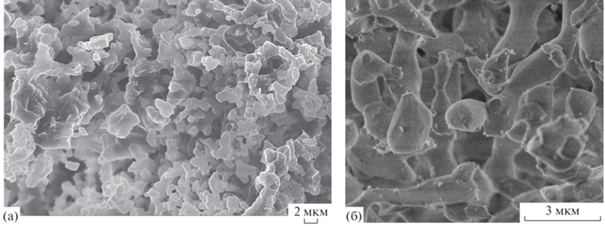
По всей видимости, формирование субмикронной микроструктуры стало возможным благодаря сдерживанию роста зерен из-за гетерофазных взаимодействий между компонентами, имеющими разное мольное соотношение Са/Р, а именно: CaO (Са/Р = ∞), СаСО3 (Са/Р = ∞), ГАП (Са/Р = 1.67) и β-ПФК (Са/Р = 1), приводящих к формированию β-ТКФ (реакции (15)–(17)). Присутствие пластинчатых частиц брушита CaHPO4⋅2H2O и монетита CaHPO4 в структуре цементного камня, а также протекание гетерофазных реакций образования β-ТКФ сдерживали уплотнение керамики в обжиге. Можно предположить, что образование фазы β-ТКФ осуществлялось на поверхности микроразмерных пластинчатых частиц брушита CaHPO4⋅2H2O/монетита CaHPO4/ПФК Ca2P2O7.
Микроструктура керамики, фазовый состав которой представлен β-ТКФ, после обжига при 1100°С (рис. 10), сложена зернами с размером 2–5 мкм. Размер зерен при увеличении температуры обжига с 1000 до 1100°С вырос существенно, примерно в 10 раз. В микроструктуре присутствует значительное количество пор с размерами в интервалах 4–8 и 1–3 мкм.
Диаграммы деформация–напряжение при испытании на сжатие для образцов керамики на основе β-Ca3(PO4)2, полученных обжигом цементного камня при 1000°С, представлены на рис. 11. Диаграмма для каждого образца представляет собой кривую, составленную из двух участков – с восходящим и нисходящим трендом, при этом оба участка имеют заметную случайную составляющую. Восходящая часть соответствует этапу нарастания усилия, когда образец сохраняет достаточную целостность и оказывает сопротивление. На втором этапе образец фактически разрушен на несколько крупных частей и нести нагрузку не способен.
Рис. 11.
Диаграммы деформация–напряжение при испытании на сжатие для образцов керамики на основе β-ТКФ, полученных обжигом цементного камня при 1000°С.
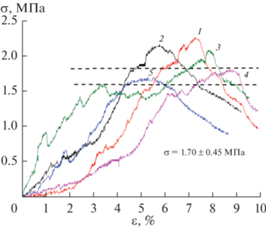
Заметная пилообразность диаграмм свидетельствует о происходящих во время нагружения локальных разрушениях, после каждого из которых напряжения в образце перераспределяются за счет, пусть и небольшой, упругой податливости материала, а также за счет упругости контактной поверхности испытательной машины. После каждого такого события образец не утрачивает целостности и готов воспринимать более высокую нагрузку.
Локальные разрушения образца происходят, как правило, в зоне его контакта с рабочими поверхностями испытательной машины и носят отчасти случайный характер, поскольку из-за малого размера образца флуктуации напряжения на его микроструктуре и шероховатостях становятся существенными. Случайность локальных разрушений определяет случайный характер всего процесса нагружения, в результате чего восходящие части диаграмм от образца к образцу в целом сильно отличаются. Тем не менее, в любом случае наступает стадия, когда очередное перераспределение нагрузки не дает увеличения несущей способности образца и небольшая серия локальных разрушений при практически одном и том же усилии завершается расколом образца на несколько крупных частей. Данное усилие можно было бы считать предельным, однако его величина сильно разнится для испытанных образцов, поэтому пределом прочности предлагается считать другую величину, несколько меньшую.
На диаграмме большинства образцов можно выделить “полочку” – относительно горизонтальный участок, предшествующий этапу полного разрушения (рис. 11). Обращает на себя внимание, что разброс высоты этого участка от образца к образцу сравнительно невелик. Его наличие свидетельствует о том, что при сравнительно одинаковой для всех образцов нагрузке происходит накопление большого количества локальных, но критических разрушений еще до окончательного разрушения. Величина указанной нагрузки является барьером, который преодолевают только некоторые образцы, и можно предположить, что преодоление происходит во многом за счет сцепления фрагментов образца шероховатыми поверхностями сколов.
Указанный предел прочности для испытанных образцов 1–5 принимается равным соответственно 1.50, 1.60, 1.70, 1.85, 1.90 МПа (см. рис. 11). Его среднее значение равно 1.7 МПа, а доверительный интервал ±0.45 МПа. Последняя величина получена как утроенное среднеквадратичное отклонение в предположении, что отклонения подчиняются нормальному закону распределения.
Таким образом, предел прочности материала на сжатие считается равным 1.70 ± 0.45 МПа.
ЗАКЛЮЧЕНИЕ
В работе описан оригинальный подход к получению субмикронной ультрапористой керамики с фазовым составом, представленным β‑ТКФ (β-Ca3(PO4)2). Данный подход предполагает подготовку порошковой смеси компонентов с заданным соотношением Са/Р = 1.5, способных вступать в реакцию химического связывания, и подготовку подвижной пасты (высококонцентрированной водной суспензии) на ее основе; формование образцов цементного камня; обжиг образцов цементного камня для получения керамики.
Образцы цементного камня были приготовлены из порошковой смеси с мольным соотношением Са/Р = 1.5, включающей ГАП Ca10(PO4)6(OH)2, тетрагидрат цитрата кальция Ca3(C6H5O7)2·4H2O и моногидрат дигидрофосфата кальция Ca(H2PO4)2· ·H2O. В качестве жидкости затворения, обеспечивающей возможность пластического формования и инициирующей реакцию химического связывания в этой порошковой смеси, использовали дистиллированную воду. Паста, включающая Ca10(PO4)6(OH)2, Ca3(C6H5O7)2·4H2O, Ca(H2PO4)2·H2O и воду, обладала подвижностью и продолжительным периодом (30–40 мин) до начала схватывания.
Фазовый состав цементного камня был представлен брушитом CaHPO4⋅2H2O, а также исходными компонентами, не вступившими реакцию. Компоненты цементного камня с заданным мольным соотношением Ca/P = 1.5 подвергались при нагревании дегидратации и разложению. Продукты термического разложения и дегидратации затем принимали участие в гетерофазных реакциях, в результате которых после обжига при 1000 и 1100°С формировался целевой фазовый состав керамики, представленный β-Ca3(PO4)2.
Реакция β-ПФК (β-Ca2P2O7) с равномерно распределенным по образцу оксидом кальция, образовавшимся в результате термической конверсии цитрата кальция Ca3(C6H5O7)2·4H2O, рассматривается в настоящей статье как причина формирования ультразернистой керамики с размером зерен 200–600 нм при 1000°С.
Присутствие пластинчатых частиц брушита CaHPO4·2H2O в структуре цементного камня, превращающихся при нагревании в монетит CaHPO4, а затем γ-ПФК и β-ПФК, сдерживало уплотнение керамики при обжиге и обусловило формирование ультрапористой (пористость до 78–80% при 1100–1000°С) структуры с размером микропор около 4–10 мкм. Кроме того, ажурные слои и пластины, образующие керамический материал, содержали некоторое количество пор размером ~200 нм. Присутствие в керамическом материале микропор, образованных пластинами, и нанопор в структуре самих пластин позволяет делать вывод о формировании бимодальной (микро/нано) размерной пористости.
Ультрапористая субмикронная биосовместимая и биорезорбируемая керамика на основе β-ТКФ с относительной плотностью 20–21%, размером зерна 200–600 нм и прочностью на сжатие 1.6–1.8 МПа, полученная обжигом при 1000°С цементного камня, приготовленного из порошковой смеси с мольным соотношением Са/Р = 1.5, включающей ГАП Ca10(PO4)6(OH)2, Ca3(C6H5O7)2·4H2O и Ca(H2PO4)2·H2O, может быть рекомендована для применения в регенеративной медицине для лечения дефектов костной ткани.
Список литературы
Tavoni M., Dapporto M., Tampieri A., Sprio S. Bioactive Calcium Phosphate-Based Composites for Bone Regeneration // J. Compos. Sci. 2021. V. 5. № 9. P. 1–27. https://doi.org/10.3390/jcs5090227
Баринов С.М., Комлев В.С. Биокерамика на основе фосфатов кальция. М.: Наука, 2005. С. 204.
Dorozhkin S.V., Epple M. Biological and Medical Significance of Calcium Phosphates // Angew. Chem. Int. Ed. 2002. V. 41. № 17. P. 3110–3146. https://doi.org/10.1002/1521-3773(20020902)41:17<3130: :AID-ANIE3130>3.0.CO;2-1
Putlyaev V.I., Safronova T.V. A New Generation of Calcium Phosphate Biomaterials: the Role of Phase and Chemical Compositions // Glass Ceram. 2006. V. 63. № 3–4. P. 99–102. https://doi.org/10.1007/s10717-006-0049-1
Putlyaev V.I., Safronova T.V. Chemical Transformations of Calcium Phosphates During Production of Ceramic Materials on Their Basis // Inorg. Mater. 2019. V. 55. № 13. P. 1328–1341. https://doi.org/10.1134/S0020168519130028
Safronova T.V., Kiselev A.S., Selezneva I.I., Shatalova T.B., Lukina Y.S., Filippov Y.Y., Toshev O.U., Tikhonova S.A., Antonova O.S., Knotko A.V. Bioceramics Based on Calcium Pyrophosphate // Materials. 2022. V. 15. № 9. P. 1–24. https://doi.org/10.3390/ma15093105
Bohner M., Santoni B.L.G., Döbelin N. β-Tricalcium Phosphate for Bone Substitution: Synthesis and Properties // Acta Biomater. 2020. V. 113. P. 23–41. https://doi.org/10.1016/j.actbio.2020.06.022
Tikhonova S.A., Evdokimov P.V., Prosvirnin D.V., Putlyaev V.I. Formation of Porous Ca3(PO4)2-Based Ceramic from Photocurable Emulsions // Inorg. Mater. Appl. Res. 2022. № 13. P. 205–210. https://doi.org/10.1134/S2075113322010361
Kalita S.J., Bhardwaj A., Bhatt H.A. Nanocrystalline Calcium Phosphate Ceramics in Biomedical Engineering // Mater. Sci. Eng., C. 2007. V. 27. № 3. P. 441–449. https://doi.org/10.1016/j.msec.2006.05.018
Suchanek W., Yoshimura M. Processing and Properties of Hydroxyapatite-Based Biomaterials for Use as Hard Tissue Replacement Implants // J. Mater. Res. 1998. V. 13. № 1. P. 94–117. https://doi.org/10.1557/JMR.1998.0015
Каназава Т. Неорганические фосфатные материалы; Пер. с яп. Киев: Наукова думка, 1998. С. 17–109.
Elliot J.C. Structure and Chemistry of the Apatites and Other Calcium Orthophosphates. Amsterdam: Elsevier, 1994.
Hill W.L., Faust G.T., Reynolds D.S. The Binary System P2O5–2CaO⋅P2O5 // Am. J. Sci. 1944. V. 242. № 9. P. 457–477. https://doi.org/10.2475/ajs.242.9.457
Bohner M. Calcium Orthophosphates in Medicine: from Ceramics to Calcium Phosphate Cements // Injury. 2000. V. 31. D37–D47. https://doi.org/10.1016/S0020-1383(00)80022-4
Kokubo T., Kim H.-M., Kawashita M. Novel Bioactive Materials with Different Mechanical Properties // Biomaterials. 2003. V. 24. № 13. P. 2161–2175. https://doi.org/10.1016/s0142-9612(03)00044-9
Dorozhkin S.V. Calcium Orthophosphates // J. Mater. Sci. 2007. V. 42. № 4. P. 1061–1095. https://doi.org/10.1007/s10853-006-1467-8
Hing K.A. Bioceramic Bone Graft Substitutes: Influence of Porosity and Chemistry // Int. J. Appl. Ceram. Technol. 2005. V. 2. № 3. P. 184–199. https://doi.org/10.1111/j.1744-7402.2005.02020.x
Safronova T.V., Selezneva I.I., Tikhonova S.A., Kiselev A.S., Davydova G.A., Shatalova T.B., Larionov D.S., Rau J.V. Biocompatibility of Biphasic α, β-Tricalcium Phosphate Ceramics in Vitro // Bioactiv. Mater. 2020. V. 5. № 2. P. 423–427. https://doi.org/10.1016/j.bioactmat.2020.03.007
Eanes E.D. Thermochemical Studies on Amorphous Calcium Phosphate // Calcif. Tissue. Res. 1970. V. 5. № 1. P. 133–145. https://doi.org/10.1007/BF02017543
Safronova T.V., Putlyaev V.I., Avramenko O.A., Shekhirev M.A., Veresov A.G. Ca-Deficient Hydroxyapatite Powder for Producing Tricalcium Phosphate-Based Ceramics // Glass Ceram. 2011. V. 68. № 1–2. P. 28–32. https://doi.org/10.1007/s10717-011-9315-y
Gibson I.R., Rehman I., Best S.M., Bonfield W. Characterization of the Transformation from Calcium-Deficient Apatite to β-Tricalcium Phosphate // J. Mater. Sci.: Mater. Med. 2000. V. 11. № 9. P. 533–539. https://doi.org/10.1023/a:1008961816208
Villet-Regi M., Rodriguez L.M., Salinas A.J. Synthesis and Characterization of Calcium Deficient Apatite // Solid State Ionics. 1997. V. 101–103. P. 1279–1285. https://doi.org/10.1016/S0167-2738(97)00213-0
Сафронова Т.В. Неорганические материалы для регенеративной медицины // Неорган. материалы. 2021. Т. 57. № 5. С. 467–499. https://doi.org/10.31857/S0002337X21050067
LeGeros R.Z. Properties of Osteoconductive Biomaterials: Calcium Phosphates // Clin. Orthop. 2002. V. 395. P. 81–98. https://doi.org/10.1097/00003086-200202000-00009
Евдокимов П.В., Путляев В.И., Иванов В.К., Гаршев А.В., Шаталова Т.Б., Орлов Н.К., Климашина Е.С., Сафронова Т.В. Фазовые равновесия в системах трикальциевый фосфат – смешанный фосфат кальция и натрия (калия) // Журн. неорган. химии. 2014. Т. 59. № 11. С. 1462–1471. https://doi.org/10.7868/S0044457X14110087
Rey C., Combes C., Drouet C., Grossin D. Bioactive Ceramics: Physical Chemistry // Compr. Biomater. 2011. P. 187–221. https://doi.org/10.1016/b978-0-08-055294-1.00178-1
Pan Y., Huang J.-L., Shao C.Y. Preparation of β-TCP with High Thermal Stability by Solid Reaction Route // J. Mater. Sci. 2003. V. 38. № 5. P. 1049–1056. https://doi.org/10.1023/a:1022354015226
Safronova T.V., Putlyaev V.I., Ivanov V.K., Knot’ko A.V., Shatalova T.B. Powders Mixtures Based on Ammonium Hydrophosphate and Calcium Carbonate for Preparation of Biocompatible Porous Ceramic in the CaO–P2O5 System // Refract. and Ind. Ceram. 2016. V. 56. № 5. P. 502–509. https://doi.org/10.1007/s11148-016-9877-x
Гузман И.Я. Химическая технология керамики. М.: ООО РИФ “Стройматериалы”, 2003. С. 496.
Woodard J.R., Hilldore A.J., Lan S.K., Park C.J., Morgan A.W., Eurell J.A.C., Wagoner Johnson A.J. The Mechanical Properties and Osteoconductivity of Hydroxyapatite Bone Scaffolds with Multi-Scale Porosity // Biomaterials. 2007. V. 28. № 1. P. 45–54. https://doi.org/10.1016/j.biomaterials.2006.0
Studart A.R., Gonzenbach U.T., Tervoort E., Gauckler L.J. Processing Routes to Macroporous Ceramics: a Review // J. Am. Ceram. Soc. 2006. V. 89. № 6. P. 1771–1789. https://doi.org/10.1111/j.1551-2916.2006.01044.x
Madhavi S., Ferraris C., White T.J. Synthesis and Crystallization of Macroporous Hydroxyapatite // J. Solid State Chem. 2005 V. 178. № 9. P. 2838–2845. https://doi.org/10.1016/j.jssc.2005.06.039
Krut’ko V.K., Maslova L.Yu., Musskaya O.N., Safronova T.V., Kulak A.I. Calcium Phosphate Ceramic Foam Obtained by Firing a Hydroxyapatite – Monocalcium Phosphate Monohydrate Powder Mixture // Glass Ceram. 2022. V. 78. № 11–12. P. 476–480. https://doi.org/10.1007/s10717-022-00435-y
Sepulveda P., Ortega F.S., Innocentini D.M., Pandolfelli V.C. Properties of Highly Porous Hydroxyapatite Obtained by the Gelcasting of Foams // J. Am. Ceram. Soc. 2000. V. 83. № 12. P. 3021–3024. https://doi.org/10.1111/j.1151-2916.2000.tb01677.x
Liu D.-M. Preparation and Characterization of Porous Hydroxyapatite Bioceramic Via a Slip-Casting Route // Ceram. Int. 1998. V. 24. № 6. P. 441–446. https://doi.org/10.1016/s0272-8842(97)00033-3
Spiridonov Y.A., Orlova L.A. Problems of Foam Glass Production // Glass Ceram. 2003. V. 60. № 9/10. P. 313–314. https://doi.org/10.1023/B:GLAC.0000008234.79970.2c
Beletskii B.I., Mastryukova D.S., Vlasova E.B. Development of Implant Materials with a Gradient Porous Structure for Neurosurgery // Glass Ceram. 2003. V. 60. № 9/10. P. 270–273. https://doi.org/10.1023/B:GLAC.0000008225.96109.90
Safronova T.V., Putlyaev V.I., Shekhirev M.A., Kuznetsov A.V. Disperse Systems in Calcium Hydroxyapatite Ceramics Technology // Glass Ceram. 2007. V. 64. № 1–2. P. 22–26. https://doi.org/10.1007/s10717-007-0006-7
Orlov N.K., Putlayev V.I., Evdokimov P.V., Safronova T.V., Klimashina E.S., Milkin P.A. Resorption of Ca3–xM2x(PO4)2 (M = Na, K) Calcium Phosphate Bioceramics in Model Solutions // Inorg. Mater. 2018. V. 54. № 5. P. 500–508. https://doi.org/10.1134/S0020168518050096
Сафронова Т.В., Белокозенко М.А., Яхёев Ш.О., Шаталова Т.Б., Казакова Г.К., Перанидзе К.Х., Тошев О.У., Хасанова С.С. Керамика на основе порошка CaSO4⋅2H2O, синтезированного из Ca(NO3)2 и (NH4)2SO4 // Неорган. материалы. 2021. Т. 57. № 8. С. 910–917. https://doi.org/10.31857/S0002337X21080273
Safronova T.V., Chichulin S.N., Shatalova T.B., Filippov Ya.Yu. Powder Mixture for the Production of Microporous Ceramics Based on Hydroxyapatite // Ceramics. 2022. V. 5. № 1. P. 108–119. https://doi.org/10.3390/ceramics5010010
Беляков А.В. Методы получения наноразмерных порошков из неорганических неметаллических материалов. М.: Российский химико-технологический университет, 2011. С. 191. https://www.elibrary.ru/item.asp?id=19613430
Oelgardt C., Anderson J., Heinrich J.G., Messing G.L. Sintering, Microstructure and Mechanical Properties of Al2O3–Y2O3–ZrO2 (AYZ) Eutectic Composition Ceramic Microcomposites // J. Eur. Ceram. Soc. 2010. V. 30. № 3. P. 649–656. https://doi.org/10.1016/j.jeurceramsoc.2009.09.011
Hosoi K., Hashida T., Takahashi H., Yamasaki N., Korenaga T. New Processing Technique for Hydroxyapatite Ceramics by the Hydrothermal Hot-Pressing Method // J. Am. Ceram. Soc. 1996. V. 79. № 10. P. 2771–2774. https://doi.org/10.1111/j.1151-2916.1996.tb09048.x
Orlov N., Kiseleva A., Milkin P., Evdokimov P., Putlayev V., Günster J., Biesuz M., Sglavo V.M., Tyablikov A. Sintering of Mixed Ca–K–Na Phosphates: Spark Plasma Sintering vs Flash-Sintering // Open Ceram. 2021. V. 5. P. 100072. https://doi.org/10.1016/j.oceram.2021.100072
Abyzov A.M. Research on the Development of High-Quality Aluminum Oxide Ceramic (Review). Part 1. Sintering with Additives, Reactive Sintering, Production of Reinforced Composites // Glass Ceram. 2018. V. 75. № 7–8. P. 8–19. https://doi.org/10.1007/s10717-018-0074-x
Сафронова Т.В., Третьяков Ю.Д., Путляев В.И., Шехирев М.А., Кузнецов А.В. Нанокерамика на основе гидроксиапатита // Конструкции из композиционных материалов. 2007. № 1. С. 22–31. https://istina.msu.ru/publications/article/434590/
Safronova T.V., Putlyaev V.I., Shekhirev M.A., Tretyakov Y.D., Kuznetsov A.V., Belyakov A.V. Densification Additives for Hydroxyapatite Ceramics // J. Eur. Ceram. Soc. 2009. V. 29. № 10. P. 1925–1932. https://doi.org/10.1016/j.jeurceramsoc.2008.12.012
Fang Z.Z., Wang H. Densification and Grain Growth During Sintering of Nanosized Particles // Int. Mater. Rev. 2008. V. 53. № 6. P. 326–352. https://doi.org/10.1179/174328008X353538
Elbadawi M., Wally Z.J., Reaney I.M. Porous Hydroxyapatite-Bioactive Glass Hybrid Scaffolds Fabricated Via Ceramic Honeycomb Extrusion // J. Am. Ceram. Soc. 2018. V. 101. № 8. P. 3541–3556. https://doi.org/10.1111/jace.15514
Musskaya O.N., Krut’ko V.K., Kulak A.I., Filatov S.A., Batyrev E.V., Safronova T.V. Calcium Phosphate Compositions with Polyvinyl Alcohol for 3D Printing // Inorg. Mater.: Appl. Res. 2020. V. 11. № 1. P. 192–197. https://doi.org/10.1134/S2075113320010268
Buswell R.A., Leal de Silva W.R., Jones S.Z., Dirrenberger J. 3D Printing Using Concrete Extrusion: A Roadmap for Research // Cem. Concr. Res. 2018. V. 112. P. 37–49. https://doi.org/10.1016/j.cemconres.2018.05.006
Safronova T.V., Korneichuk S.A., Shatalova T.B., Lukina Yu S., Sivkov S.P., Filippov Ya.Yu., Krut’ko V.K., Musskaya O.N. Ca2P2O7–Ca(PO3)2 Ceramic Obtained by Firing β-Tricalcium Phosphate and Monocalcium Phosphate Monohydrate Based Cement Stone // Glass Ceram. 2020. V. 77. № 5–6. P. 165–172. https://doi.org/10.1007/s10717-020-00263-y
Сафронова Т.В., Лукина Ю.С., Сивков С.П., Тошев О.У., Казакова Г.К., Шаталова Т.Б., Филиппов Я.Ю., Малютин К.В., Азизян-Каландараг Я. Керамика на основе пирофосфата кальция, полученная обжигом цементного камня // Техника и технология силикатов. 2020. Т. 27. № 1. С. 17–20. https://www.elibrary.ru/item.asp?id=44820756
Safronova T.V., Shatalova T.B., Filippov Ya.Yu., Krut’ko V.K., Musskaya O.N., Safronov A.S., Toshev O.U. Ceramics in the Ca2P2O7–Ca(PO3)2 System Obtained by Annealing of the Samples Made from Hardening Mixtures Based on Calcium Citrate Tetrahydrate and Monocalcium Phosphate Monohydrate // Inorg. Mater.: Appl. Res. 2020. V. 11. № 4. P. 777–786. https://doi.org/10.1134/S2075113320040334
Toshev O.U., Safronova T.V., Kaimonov M.R., Shatalova T.B., Klimashina E.S., Lukina Y.S., Malyutin K.V., Sivkov S.P. Biocompatibility of Ceramic Materials in Ca2P2O7–Ca(PO3)2 System Obtained via Heat Treatment of Cement-Salt Stone // Ceramics. 2022. V. 5. № 3. P. 516–532. https://doi.org/10.3390/ceramics5030039
Toshev O.U., Safronova T.V., Kazakova G.K., Shatalova T.B., Boytsova O.V., Lukina Yu.S., Sivkov S.P. Ceramics Based on Sodium Rhenanite CaNaPO4, Obtained via Firing of Composite Cement-Salt Stone // J. Compos. Sci. 2022. V. 6. P. 1–10. https://doi.org/10.3390/jcs6100314
PDF-4+ Database. Newtown Square: International Centre for Diffraction Data, 2010. https://www.icdd.com/pdf-2/
Hurle K., Oliveira J.M., Reis R.L., Pina S., Goetz-Neunhoeffer F. Ion-Doped Brushite Cements for Bone Regeneration // Acta Biomater. 2021. V. 123. P. 51–71. https://doi.org/10.1016/j.actbio.2021.01.004
Sarda S., Fernández E., Nilsson M., Balcells M., Planell J.A. Kinetic Study of Citric Acid Influence on Calcium Phosphate Bone Cements as Water-Reducing Agent // J. Biomed. Mater. Res. 2002. V. 61. № 4. P. 653–659. https://doi.org/10.1002/jbm.10264
Bohner M., Lemaitre J., Ring T.A. Effects of Sulfate, Pyrophosphate, and Citrate Ions on the Physicochemical Properties of Cements Made of Beta-Tricalcium Phosphate-Phosphoric Acid-Water Mixtures // J. Am. Ceram. Soc. 1996. V. 79. № 6. P. 1427–1434. https://doi.org/10.1111/j.1151-2916.1996.tb08746.x
Safronova T.V., Shatalova T.B., Tikhonova S.A., Filippov Y.Y., Krut’ko V.K., Musskaya O.N., Kononenko N.E. Synthesis of Calcium Pyrophosphate Powders from Phosphoric Acid and Calcium Carbonate // Inorg. Mater. Appl. Res. 2021. V. 12. P. 986–992. https://doi.org/10.1134/S2075113321040353
Zhou H., Yang L., Gbureck U., Bhaduri S.B., Sikder P. Monetite, an Important Calcium Phosphate Compound – Its Synthesis, Properties and Applications in Orthopedics // Acta Biomaterial. 2021. V. 127. P. 41–55. https://doi.org/10.1016/j.actbio.2021.03.050
Seham A.A. Mansour. Thermal Decomposition of Calcium Citrate Tetrahydrate // Thermochim Acta. 1994. V. 233. № 2. P. 243–256. https://doi.org/10.1016/0040-6031(94)85118-2
Dosen A., Giese R.F. Thermal Decomposition of Brushite, CaHPO4⋅2H2O to Monetite CaHPO4 and the Formation of an Amorphous Phase // Am. Miner. 2011. V. 96. № 2–3. P. 368–373. https://doi.org/10.2138/am.2011.3544
Safronova T.V., Putlyaev V.I., Filippov Ya.Yu., Knot’ko A.V., Klimashina E.S., Peranidze K.Kh., Evdokimov P.V., Vladimirova S.A. Powders Synthesized from Calcium Acetate and Mixed-Anionic Solutions, Containing Orthophosphate and Carbonate Ions, for Obtaining Bioceramic // Glass Ceram. 2018. V. 75. № 3. P. 118–123. https://doi.org/10.1007/s10717-018-0040-7
Jinlong N., Zhenxi Z., Dazong J. Investigation of Phase Evolution during the Thermochemical Synthesis of Tricalcium Phosphate // J. Mater. Synt. Proc. 2001. V. 9. № 5. P. 235–240. https://doi.org/10.1023/A:1015243216516
Safronova T., Putlayev V., Shekhirev M. Resorbable Calcium Phosphates-Based Ceramics // Powder Metall. Met. Ceram. 2013. V. 52. № 5. P. 357–363. https://doi.org/10.1007/s11106-013-9534-6
Дополнительные материалы отсутствуют.
Инструменты
Неорганические материалы