Неорганические материалы, 2022, T. 58, № 12, стр. 1312-1319
Восстановление оксидных соединений ниобия парами магния в интервале 540–680°С
В. М. Орлов 1, *, Е. Н. Киселев 1
1 Институт химии и технологии редких элементов и минерального сырья им. И.В. Тананаева – обособленное подразделение Федерального исследовательского центра “Кольский научный центр Российской
академии наук”
184209 Мурманская обл., Апатиты, Академгородок, 26, А, Россия
* E-mail: v.orlov@ksc.ru
Поступила в редакцию 16.05.2022
После доработки 04.10.2022
Принята к публикации 06.10.2022
- EDN: QOJRAC
- DOI: 10.31857/S0002337X22120089
Аннотация
Исследованы особенности пористой структуры порошков, полученных восстановлением Nb2О5 и Mg4Nb2O9 парами магния в интервале 540–680°С. Снижение температуры восстановления замедляет диффузионные процессы, что позволяет предотвратить огрубление первичной структуры восстановленной частицы оксида и тем самым увеличить объем и поверхность пор диаметром менее 5 нм. Восстановлением Nb2О5 при температуре 680°С получен порошок ниобия с удельной поверхностью 83.4 м2/г. При дальнейшем снижении температуры восстановления размеры пор уменьшаются настолько, что большинство из них полностью заполняется естественным оксидом Nb2О5 и удельная поверхность уменьшается. При восстановлении Mg4Nb2O9 в этих условиях размеры пор таковы, что полученный после выщелачивания оксида магния порошок, по существу, представляет собой аморфный оксид Nb2О5.
ВВЕДЕНИЕ
Металлический ниобий благодаря ряду уникальных характеристик нашел широкое применение в ракетостроении, авиационной и космической технике, атомной энергетике, радиотехнике, электронике [1]. Основным способом получения компактного металла является восстановление пентаоксида ниобия алюминием или смесью алюминия с кальцием с последующей электронно-лучевой плавкой образовавшегося сплава ниобия с алюминием [2, 3]. Развитие способов получения ниобия в виде порошка в основном связано с возможностью создания ниобиевых конденсаторов, способных заменить в ряде применений дефицитный тантал [4–9]. Ранее для этих целей использовали порошки с осколочной формой частиц, полученные размолом гидрированных слитков ниобия высокой чистоты [10]. Аноды конденсаторов, изготовленные из таких порошков, отличались небольшим удельным зарядом. Постоянная тенденция к миниатюризации радиоэлектронной аппаратуры делает актуальной разработку способов получения порошков ниобия с удельной поверхностью, обеспечивающей увеличение заряда конденсаторов. Порошки с удельной поверхностью 10–30 м2/г изготовлены путем восстановления пентахлорида ниобия водородом в плазменном реакторе [11]. Мелкодисперсный порошок ниобия с размером частиц менее 1 мкм был получен электрохимическим методом, при котором восстановление ионов ниобия происходило непосредственно в объеме расплава [12]. Значительное количество работ посвящено технологии ниобиевых порошков, пригодных для производства конденсаторов, восстановлением гептафторониобата калия (K2NbF7) натрием [13–17]. В работе [13] процесс вели в расплаве, содержащем K2NbF7 и соли разбавители (галогениды щелочных металлов). Удельная поверхность порошков, полученных при подаче натрия на поверхность расплава, содержащего K2NbF7, достигала 1 м2/г. Она увеличивалась до 3 м2/г, если твердый K2NbF7 загружали на поверхность расплава натрия. В работах [14–17] исходные твердые материалы – K2NbF7, соли разбавители и натрий – загружали в реактор послойно. Нагрев до требуемой температуры вели в атмосфере аргона. Затем расплав выдерживали в течение 2 ч при постоянном перемешивании. Были получены порошки ниобия с размерами частиц в интервале 50–200 нм. Размеры частиц увеличивались с повышением температуры процесса от 720 до 820°С и с увеличением избытка натрия от 0 до 7 мас. %. Недостатком полученных порошков было загрязнение их продуктами коррозии аппаратуры.
Гораздо более перспективно для получения порошков ниобия с большой удельной поверхностью восстановление его пентаоксида Nb2O5 кальцием и, особенно, магнием. Авторы [18–20] исследовали характеристики порошков ниобия, полученных восстановлением оксидов ниобия кальцием. Процесс вели при температуре 880–950°С в расплаве СаСl2, в котором растворялись как исходный кальций, так и образующийся в процессе восстановления СаО. При использовании в качестве прекурсора Nb2O5 или Nb(OН)5 полученный порошок ниобия представлял собой субмикронные частицы с кораллоподобной (coral-like) морфологией [18, 19]. Если прекурсором служил ниобат кальция (CaxNb2Oy), образовывались в основном частицы с ветвистой (branch) морфологией [20].
Поскольку реакция восстановления пентаоксида ниобия магнием сопровождается выделением большого количества тепла (адиабатическая температура реакции 2385°С [21]), взаимодействие в смеси компонентов протекает в режиме теплового взрыва [22]. Поэтому восстановление обычно ведут парами магния (кальция) при температуре 800–1000°С и различном давлении инертного газа в реакторе, что позволяет регулировать скорость поступления паров к поверхности реагирования [23–31]. В ряде работ восстановление вели при небольшом избыточном давлении инертного газа (аргона) в реакторе, используя в качестве переносчика паров магния ток инертного газа, подаваемого через сопло в нижней части реактора. В таких условиях при температуре восстановления 1000°С получен порошок ниобия с удельной поверхностью 20 м2/г [23]. Можно вести процесс и при давлении инертного газа в реакторе ниже атмосферного, используя для уменьшения потерь магния герметизированный реакционный стакан [30]. Восстановлением Nb2O5 при температуре 830°С и остаточном давлении аргона в реакторе 10 кПа был получен порошок ниобия с удельной поверхностью 32 м2/г. Авторы [31] исследовали влияние температуры восстановления на гранулометрический состав порошков. Процесс вели в течение 20 ч при давлении в реакторе 110 кПа без использования транспортирующего тока аргона. В этих условиях увеличение температуры восстановления с 800 до 950°С привело к росту размера частиц с 200 до 600 нм.
Влияние упругости паров магния на характеристики получаемого порошка ниобия показано в работе [26]. При восстановлении специально подготовленных прессовок из смеси Nb2O5 и флюса (СаСО3) авторы в качестве источника паров Mg использовали сплав Mg–Ag (50 мол. %), что позволило снизить упругость паров магния при температуре 1000°С с 55 до 8.9 кПа. Размеры частиц порошка ниобия при этом уменьшились с 1 до 0.1 мм.
Так же, как и порошки тантала [32], порошки ниобия, полученные восстановлением его оксидных соединений парами магния, характеризуются мезопористой структурой [33]. Следовательно, восстановление протекает по тому же механизму во всем объеме частицы оксида с образованием тонкой полосчатой структуры, представленной перемежающимися пластинчатыми частицами металла и оксида магния. В дальнейшем структура огрубляется в результате диффузионных процессов [34]. После выщелачивания оксида магния частица металла характеризуется губчатой структурой, а величина ее поверхности, по существу, равна поверхности внутренних пор. Восстановлением ниобата Mg4Nb2O9 были получены порошки с удельной поверхностью до 150–170 м2/г и средним размером пор на уровне 4.5 нм [30, 33]. При этом отмечалось, что с увеличением времени восстановления удельная поверхность порошков ниобия уменьшается в большей степени, чем тантала, т.е. огрубление структуры протекает более интенсивно [35].
Цель настоящей работы – исследование возможности увеличения удельной поверхности порошков восстановлением Nb2O5 и Mg4Nb2O9 при температуре, близкой и ниже температуры плавления магния. В этих условиях скорость поступления паров магния в зону реакции и диффузионные процессы сведены к минимуму. Это позволит в значительной степени избежать огрубления первичной структуры восстановленных частиц оксида.
ЭКСПЕРИМЕНТАЛЬНАЯ ЧАСТЬ
Реактором для восстановления служила реторта из нержавеющей стали внутренним диаметром 100 мм с рубашкой водяного охлаждения вакуумного уплотнения и крышкой, имеющей патрубки для ввода термопары и подсоединения к вакуумной системе. Внутри реторты устанавливали реакционный стакан с плотно закрывающейся крышкой. В крышке реакционного стакана имелось отверстие для ввода чехла термопары с минимальным зазором между ними. Контейнер с магнием помещали на дно реакционного стакана, выше на 5 мм находился контейнер с восстанавливаемым материалом. Для измерения температуры использовали хромель-алюмелевую термопару, подключенную к прибору ТЕРМОДАТ-13К5. После сборки реторту-реактор устанавливали в шахтную печь электросопротивления СШОЛ-1.1.16 мощностью 2.5 кВт, вакуумировали форвакуумным насосом 2НВР-5ДМ и нагревали до температуры 200–250°С для более полной дегазации загрузки и рабочего объема. После дегазации реторту заполняли аргоном до давления 110 кПа и продолжали нагревать до требуемой температуры (540–680°С). Затем реактор вакуумировали при открытом отверстии крышки реакционного стакана, термопару опускали в реакционный стакан до уровня загрузки оксида и проводили выдержку в течение заданного времени при постоянном вакуумировании. После завершения выдержки реактор заполняли аргоном и охлаждали до комнатной температуры. Далее реактор вакуумировали и дозированно заполняли воздухом до атмосферного давления для пассивации образовавшегося порошка ниобия. Обработку продуктов реакции проводили 15%-ным раствором HNO3 в течение 1 ч при постоянном перемешивании. Операцию повторяли, затем порошок ниобия отмывали дистиллированной водой до нейтральной реакции раствора и сушили на воздухе при 85°С.
В качестве исходных материалов использовали пентаоксид ниобия марки В производства ОАО “Соликамский магниевый завод”, который дополнительно термообрабатывали при температуре 1200–1300°С в течение 2–3 ч, магний металлический марки Мг 95 (ГОСТ 804-93), а также ниобат Mg4Nb2O9, синтезированный спеканием пентаоксида ниобия со стехиометрическим количеством оксида магния квалификации “ч.д.а.” при температуре 1300°С [35]. Масса разовой загрузки Nb2O5 составляла 3 г, Mg4Nb2O9 – 4 г, толщина слоя – 7 и 4 мм соответственно.
Величину удельной поверхности порошков измеряли адсорбционным статическим методом БЭТ, а параметры пористости – методом BJH на приборе Micromeritics TriStar II 3020. Термический анализ выполняли на приборе NETZSCH STA 409 PC Luxx: скорость нагрева 10°С/мин, атмосфера – воздух, расход 100 мл/мин.
РЕЗУЛЬТАТЫ И ОБСУЖДЕНИЕ
Для восстановления 3 г Nb2O5 или 4 г Mg4Nb2O9 по стехиометрии требуется соответственно 1.7 и 1.13 г магния. Рассчитанная по уменьшению массы магния в ходе экспериментов скорость его испарения при температурах 680 и 550°С составила около 0.1 и 0.03 г/мин соответственно. Упругость паров магния при этих температурах отличается в 15 раз (4.5 и 0.3 торр). Относительно небольшая разница в скоростях испарения объясняется тем, что восстановление вели в замкнутом объеме, а улетучивание магния через неплотности между крышкой и реакционным стаканом было незначительным.
Зависимость удельной поверхности порошков ниобия от температуры восстановления приведена на рис. 1. Снижение температуры восстановления пентаоксида ниобия с 830 до 680°С, как и ожидалось, привело к увеличению удельной поверхности порошка до 83.4 м2/г. Это в 2 раза больше удельной поверхности порошка, полученного в оптимальном высокотемпературном режиме – 830°С, остаточное давление аргона 10 кПа [30]. При дальнейшем снижении температуры удельная поверхность порошков уменьшается (рис. 1а). У порошков, полученных восстановлением ниобата магния, уже при температуре восстановления 680°С удельная поверхность в 2 раза меньше, чем у порошков, полученных восстановлением в оптимальном высокотемпературном режиме [33, 35]. При дальнейшем снижении температуры восстановления уменьшение поверхности было еще более значительным. При температуре 870°С ее величина составляла всего около 20 м2/г (рис. 1б). Эта особенность изменения удельной поверхности порошков ниобия в исследованном интервале температур, мы полагаем, определяется двумя одновременно действующими факторами: уменьшением размера пор, образующихся после выщелачивания прослоек оксида магния, как следствие сохранения более тонкой полосчатой структуры восстановленной частицы с понижением температуры; образованием на поверхности металлических частиц ниобия пленки естественного аморфного оксида Nb2O5, толщина которой на компактном металле около 2 нм [36].
Рис. 1.
Зависимости удельной поверхности порошков, полученных восстановлением Nb2O5 (а) и Mg4Nb2O9 (б), от температуры восстановления.
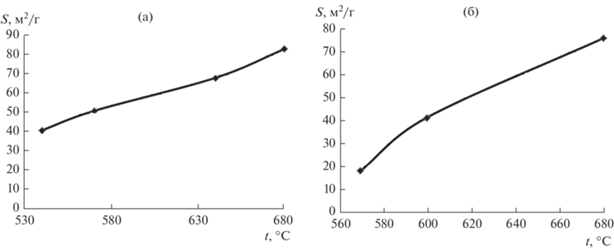
Удельная поверхность порошков в случае восстановления при температуре 830°С, остаточном давлении аргона в реакторе 5 кПа и использовании в качестве прекурсора Mg4Nb2O9 в 5 раз превышала поверхность порошков, полученных восстановлением Nb2O5, за счет увеличения общего объема пор в 1.5 раза и преобладания мезопор диаметром менее 5 нм [33]. Снижение температуры приводит к уменьшению концентрации атомов магния в парах, а также замедляет диффузионные процессы. Оба этих фактора позволяют сохранить первичную структуру восстановленных частиц оксидного соединения. В результате должен наблюдаться рост удельной поверхности получаемых порошков ниобия, что и произошло в случае снижения температуры восстановления Nb2O5 с 830 до 680°С. Однако дальнейшее снижение температуры привело к уменьшению удельной поверхности, особенно значительному у порошков, полученных восстановлением ниобата Mg4Nb2O9 (рис. 1). Уже при температуре 680°С удельная поверхность порошка, полученного восстановлением этого прекурсора, в 2 раза меньше, чем при 830°С [33]. О причинах, вызвавших это, можно судить по данным об изменении пористой структуры порошков, которые приведены в табл. 1.
Таблица 1.
Удельная поверхность и пористая структура порошков, полученных восстановлением Nb2O5 и Mg4Nb2O9
Прекурсор | t, °С | S, м2/г | Dср, нм | Объем пор | ||||
---|---|---|---|---|---|---|---|---|
V, см3/г | V1 | V2 | ||||||
см3/г | % | см3/г | % | |||||
Nb2O5 | 830 [33] | 32 | 15.1 | 0.115 | – | – | – | – |
680 | 83.4 | 7.09 | 0.153 | 0.077 | 51 | 0.036 | 23 | |
640 | 64.3 | 8.54 | 0.130 | 0.079 | 61 | 0.022 | 17 | |
570 | 53.1 | 6.72 | 0.088 | 0.039 | 44 | 0.021 | 24 | |
540 | 41.5 | 4.31 | 0.041 | 0.008 | 20 | 0.023 | 56 | |
Mg4Nb2O9 | 830 [33] | 150 | 4.5 | 0.173 | – | – | – | – |
680 | 76 | 3.43 | 0.044 | 0.007 | 17 | 0.031 | 71 | |
600 | 41.3 | 6.39 | 0.062 | 0.027 | 44 | 0.019 | 31 | |
570 | 18 | 6.96 | 0.032 | 0.017 | 53 | 0.009 | 28 |
Анализ приведенных в табл. 1 данных показывает, что рост поверхности порошка, полученного восстановлением Nb2O5 при температуре 680°С, обусловлен увеличением объема пор почти в 1.5 раза и уменьшением их среднего размера в 2 раза. Уменьшение удельной поверхности при дальнейшем снижении температуры восстановления связано с уменьшением объема пор. Последнее отчасти компенсируется увеличением доли пор менее 5 нм. Изменения в пористой структуре порошков сказываются на виде изотерм сорбции.
Изотермы адсорбции–десорбции и распределение пор по размерам в порошках ниобия, полученных восстановлением Nb2O5 при температуре 680 и 540°С, приведены на рис. 2. Что касается порошков, полученных восстановлением Mg4Nb2O9, то уменьшение удельной поверхности при снижении температуры восстановления с 830 до 680°С в 2 раза обусловлено уменьшением объема пор в 4 раза. При дальнейшем понижении температуры восстановления, в отличие от восстановления Nb2O5, общий объем пор изменился незначительно, но резко снизилась доля пор с размерами менее 5 нм. В результате наблюдается более значительное уменьшение поверхности.
Рис. 2.
Изотермы адсорбции–десорбции (а, б) и распределение пор по размерам (в, г) в порошках ниобия, полученных восстановлением Nb2O5 при температуре 680 (а, в) и 540°С (б, г).
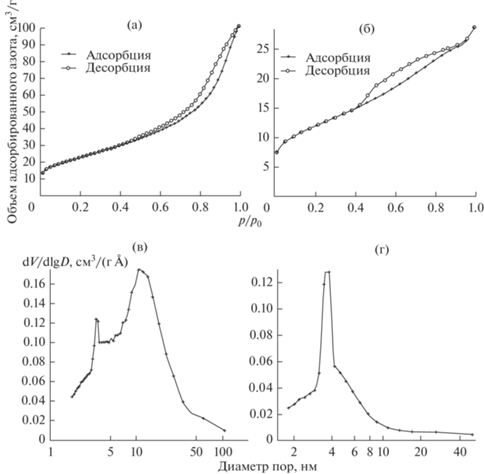
Наблюдающаяся “аномалия” в изменении пористой структуры объясняется действием второго фактора. При выщелачивании оксида магния на поверхности частиц ниобия образуется пленка естественного оксида, которая уменьшает, а при особо малых размерах и полностью заполняет объем образовавшихся пор. Это подтверждается результатами термического анализа. На рис. 3 приведены кривые ТГ и ДСК, полученные при нагреве на воздухе порошков – продуктов восстановления Nb2O5 и Mg4Nb2O9 при температуре 680°С (удельная поверхность 87 и 64 м2/г соответственно).
Рис. 3.
ТГ- и ДСК-кривые окисления порошков, полученных восстановлением Nb2О5 (а), Mg4Nb2O9 (б) (температура восстановления 680°С).
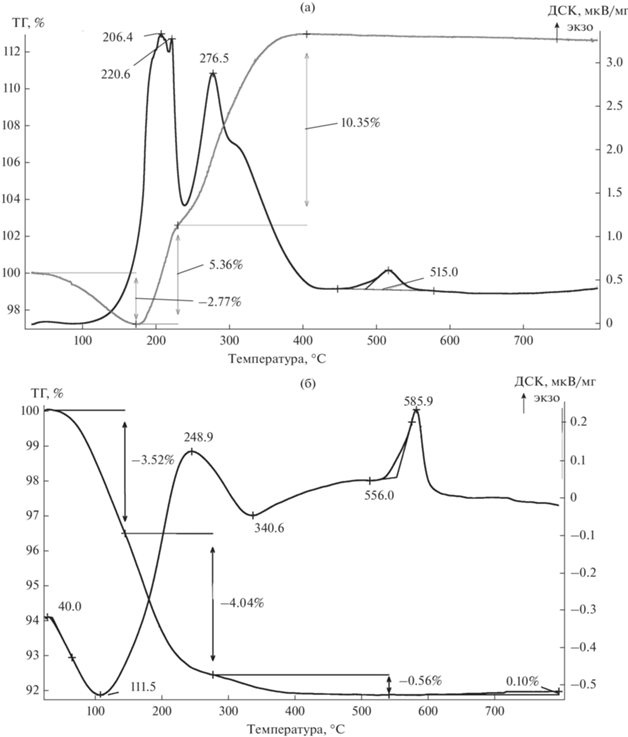
Уменьшение массы на первом этапе нагрева, наблюдавшееся до температуры 180°С у порошка, полученного восстановлением Nb2O5 (рис. 3а), связано с удалением сорбированной влаги. На ТГ-кривой порошка ниобия, полученного восстановлением ниобата (рис. 3б), этот процесс продолжается до температуры около 280°С. Дальнейшая потеря массы, скорее всего, обусловлена удалением водорода, образовавшегося при выщелачивании продуктов реакции и поглощенного ниобием. Этим потерям массы соответствуют эндопики на кривых ДСК при 111.5 и 340.6°С. При этом прирост массы, связанный с окислением металлической части порошка, практически не наблюдается. Возможно, процессу окисления соответствует небольшой излом на ТГ-кривой, соответствующий экзопику при температуре 248.9°С.
Окисление порошка, полученного восстановлением пентаоксида (рис. 3а), начинается при более низкой температуре. Судя по наличию двух экзопиков (206.4 и 276.5°С) окисление происходило в два этапа. Вероятно, первоначально окислению подвергалась часть порошка с более крупными порами, а затем уже с размерами пор, затрудняющими доступ кислорода к поверхности частиц ниобия. Рассчитанное по изменению массы образцов содержание в порошках металлического ниобия (CМ), поверхностного оксида (Cоксид) и кислорода (CО) в зависимости от температуры восстановления приведено в табл. 2.
Эти данные подтверждают, что причиной уменьшения удельной поверхности порошков ниобия, восстановленных в рассмотренном интервале температур, является изменение первичной пористой структуры восстановленных частиц в результате заполнения образовавшихся пор естественным оксидом Nb2О5. В рассматриваемых условиях размеры частиц ниобия и пор таковы, что у порошков, полученных восстановлением Mg4Nb2O9, практически вся масса металла израсходована на образование естественного оксида, а подавляющее количество пор заполнено этим оксидом. По существу, полученный материал представляет собой аморфный пентаоксид ниобия, который кристаллизуется при нагреве до температуры 580–590°С (экзопик 585.9°С, рис. 3б).
Порошки, полученные восстановлением Nb2О5, характеризуются в целом более крупнопористой структурой. Снижение температуры восстановления до 680°С привело к увеличению количества пор меньших, но не достигших критического, размеров и, соответственно, к значительному росту удельной поверхности. При дальнейшем снижении температуры восстановления размеры пор уменьшались, степень их заполнения естественным оксидом увеличивалась. В результате удельная поверхность порошка уменьшалась.
ЗАКЛЮЧЕНИЕ
Исследован процесс восстановления Nb2О5 и ниобата Mg4Nb2O9 парами магния в интервале температур 540–680°С. Проанализированы и объяснены изменения в пористой структуре полученных порошков.
Замедление диффузионных процессов, обусловленное снижением температуры восстановления, приводит к сохранению более тонкой полосчатой структуры восстановленных частиц оксидного соединения. Об этом можно судить по увеличению количества и объема пор, размеры которых менее 5 нм. Соответственно, должна увеличиться удельная поверхность полученных порошков. Восстановлением Nb2О5 при температуре 680°С получен порошок ниобия с удельной поверхностью 83.4 м2/г, которая в 2.5 раза превышает удельную поверхность порошка, полученного ранее при 830°С [33]. При дальнейшем снижении температуры восстановления удельная поверхность порошков уменьшается.
С другой стороны, при восстановлении в этом интервале температур частиц ниобата Mg4Nb2O9 образуется и сохраняется настолько тонкая полосчатая структура, что большинство образовавшихся пор порошка, полученного уже при температуре восстановления 680°С, заполнено слоем естественного оксида. Порошок, по существу, представляет собой аморфный пентаоксид ниобия с небольшим содержанием металлической составляющей. Удельная поверхность порошка в 2 раза меньше, чем у полученного при температуре 830°С [33]. При дальнейшем снижении температуры размеры пор еще больше уменьшаются, соответственно, увеличивается степень их заполнения естественным оксидом и уменьшается удельная поверхность полученного порошка.
Список литературы
Никишина Е.Е., Дробот Д.В., Лебедева Е.Н. Ниобий и тантал: состояние мирового рынка, области применения, сырьевые источники. Ч. 1 // Изв. вузов. Цв. металлургия. 2013. № 5. С. 28–34. https://doi.org/10.17073/0021-3438-2013-5-28-34
Kumar T.S., Balaji T., Kumar S.R., Kumar A., Prakash T.L. Issues and Challenges in the Preparation of Niobium for Strategic Applications // Int. J. Chem. Stud. 2013. V. 1. № 2. P. 86–89. https://doi.org/10.1007/978-3-319-67870-2_2
Gorkunov V., Munter R. Calcium–Aluminothermal Production of Niobium and Mineral Composition of the Slag // Proc. Est. Acad. Sci., Chem. 2007. V. 56. № 3. P. 142–156.
Schtazel A., Khight H.F. An Investigation of Columbium as an Electrolytic Capacitor Metal // J. Electrochem. Soc. 1961. V. 108. № 4. P. 343–347.
Jackson N.F., Handy J.C. These of Niobium as an Anode Material in Liquid Filled Electrolytic Capacitors // Electrocomponent Sci. Technol. 1974. V. 1. № 1. P. 27–37.
Pozdeev Y. Comparison of Tantalum and Niobium Solid Electrolytic Capacitors // T.I.C. Bull. 1998. № 94. P. 2–5.
Serjak W.A., Scheckter L., Tripp T.B. et al. Niobium, a New Materials for Capacitors // Passive Comp. Ind. 2000. Nov./Dec. P. 17–20.
Zillgen H., Stenzel M., Lohwasser W. New Niobium Capacitors with Stable Electrical Parameters // Act. Passive Electron. Compon. 2002. V. 25. P. 147–153. https://doi.org/10.1080/0882751021000001528
Fischer V., Starmer H.D., Gerthsen M. et al. Niobium as New Material for Electrolyte Capacitors with Nanoscale Dielectric Oxide Layers // Proc. 7th lnt. Conf. Properties and Applications of Dielectric Materials. 2003. Nagoya. s20-2.
Елютин А.В., Патрикеев Ю.Б., Воробьева Н.С. и др. Материал для анодов электролитических и оксидно-полупроводниковых конденсаторов: Пат. РФ 1 556 420. 1994.
Grabis J., Munterb R., Blagoveshchenskiy Yu. et al. Plasmochemical Process for the Production of Niobium and Tantalum Nanopowders // Proc. Est. Acad. Sci. 2012. V. 61. № 2. P. 137–145. https://doi.org/10.3176/proc.2012.2.06
Yuan B., Okabe T.H. Electrochemically Assisted Formation of Fine Niobium Powder in Molten Salt // J. Electrochem. Soc. 2007. V. 154. № 1. P. E1–E7. https://doi.org/10.1149/1.2364842
Колосов В.Н., Мирошниченко М.Н., Орлов В.М. и др. Влияние условий натриетермического восстановления на характеристики ниобиевых порошков // Расплавы. 2008. № 5. С. 89–94.
Yoon J.S., Cho S.W., Kim Y.S., Kim B.Il. The Production of Niobium Powder and Electric Properties of Niobium Capacitors // Met. Mater. Int. 2009. V. 15. № 3. P. 405–408. https://doi.org/10.1007/s12540-009-0405-0
Yoon J.S., Goto Sh., Kim B.Il. Characteristic Variation of Niobium Powder Produced under Various Reduction Temperature and Amount of Reductant Addition // Mater. Trans. 2010. V. 51. № 2. P. 354–358. https://doi.org/10.2320/matertrans.M2009192
Yoon J.S. The Fabrication of Niobium Powder by Sodiothermic Reduction Process // Int. J. Refract. Met. Hard Mater. 2010. V. 28. № 2. P. 265–269. https://doi.org/10.1016/j.ijrmhm.2009.10.009
Yoon J.S., Lee G.H., Hong S.J. et al. Characteristics of Niobium Powder Used Capacitors Produced by Metallothermic Reduction in Molten Salt // Curr. Nanosci. 2014. V.10. № 1. P. 131–134.
Baba M., Ono Y., Suzuki R.O. Tantalum and Niobium Powder Preparation from Their Oxides by Calciothermic Reduction in the Molten CaCl2 // J. Phys. Chem. Solids. 2005. V. 66. № 2–4. P. 466–470. https://doi.org/10.1016/j.jpcs.2004.06.042
Baba M., Kikuchi T., Suzuki R.O. Niobium Powder Synthesized by Calciothermic Reduction of Niobium Hydroxide for Use in Capacitors // J. Phys. Chem. Solids. 2015. V. 78. P. 101–109. https://doi.org/10.1016/j.jpcs.2014.11.014
Suzuki N., Suzuki R.O., Natsui S., Kikuchi T. Branched Morphology of Nb Powder Particles Fabricated by Calciothermic Reduction in CaCl2 Melt // J. Phys. Chem. Solids. 2017. V. 110. P. 101–109. https://doi.org/10.1016/j.jpcs.2017.05.032
Крыжанов М.В., Орлов В.М., Сухоруков В.В. Термодинамическое моделирование магнийтермического восстановления тантала и ниобия из пентаоксидов // ЖПХ. 2010. Т. 83. Вып. 3. С. 380–385.
Орлов В.М., Сухоруков В.В. Магниетермическое получение порошков ниобия // Металлы. 2010. № 2. С. 16–22.
Shekhter L.N., Tripp T.B., Lanin L.L. Method for Producing Tantallum/Niobium Metal Powders by the Reduction of Their Oxides with Gaseous Magnesium: US Pat. 6171363. 2001.
Shekhter L.N., Tripp T.B., Lanin L.L. et al. Metal Powders Produced by the Reduction of the Oxides with Gaseous Magnesium: US Pat. 6558447. 2003.
Schnitter C., Merker U., Michaelis A. New Niobium Based Materials for Solid Electrolyte Capacitors // Proc. 22nd Capacitor and Resistor Technol. Symp. New Orleans. 2002. P. 26–31.
Okabe T.H., Iwata S., Imagunbai M. et al. Production of Niobium Powder by Preform Reduction Process Using Various Fluxes and Alloy Reductant // ISIJ Int. 2004. V. 44. № 2. P. 285–293. https://doi.org/10.2355/isijinternational.44.285
Haas D., Schnitter C. Production of Capacitor Grade Tantalum and Niobium Powders Using the New Magnesium Vapour Reduction Process // Proc. EMC. Dresden. 2005.
Luidold S., Antrekowitsch H., Ressel R. Production of Niobium Powder by Magnesiothermic Reduction of Niobium Oxides in a Cyclone Reactor // Int. J. Refract. Met. Hard Mater. 2007. V. 25. № 5–6. P. 423–432. https://doi.org/10.1016/j.ijrmhm.2006.11.00
Kumar T.S., Kumar S.R., Rao M.L., Prakash T.L. Preparation of Niobium Metal Powder by Two-Stage Magnesium Vapor Reduction of Niobium Pentoxide // J. Metall. 2013. V. 2013. Article ID 629341. https://doi.org/10.1155/2013/629341
Орлов В.М., Крыжанов М.В., Калинников В.Т. Восстановление оксидных соединений ниобия парами магния // Докл. АН. 2015. Т. 465. № 2. С. 182–185.
Park S.J., Hwang S.M., Wang J. et al. Metallic Niobium Powder Reduced by Atmospheric Magnesium Gas with Niobium Pentoxide Powder // Mater. Trans. 2021. V. 62. № 1. P. 34–40. https://doi.org/10.2320/matertrans.MT-M2020241
Орлов В.М., Крыжанов М.В., Князева А.И. Порошки тантала с мезопористой структурой // Физикохимия поверхности и защита материалов. 2016. Т. 52. № 5. С. 500–504. https://doi.org/10.7868/S0044185616050181
Орлов В.М., Крыжанов М.В., Князева А.И., Осауленко Р.Н. Порошки ниобия с мезопористой структурой // Физикохимия поверхности и защита материалов. 2018. Т. 54. № 5. С. 444–449. https://doi.org/10.1134/S0044185618050297
Müller R., Bobeth M., Brumm H. et al. Kinetics of Nanoscale Structure Development During Mg-vapour Reduction of Tantalum Oxide // Int. J. Mater. Res. 2007. V. 98. № 11. P. 1138–1145. https://doi.org/10.3139/146.101567
Орлов В.М., Крыжанов М.В. Влияние состава прекурсора и условий восстановления на характеристики магниетермических порошков ниобия // Металлы. 2016. № 4. С. 20–26.
Delheusy M., Stierle A., Kasper N. et al. X-ray Investigation of Subsurface Interstitial Oxygen at Nb/Oxide Interfaces // Appl. Phys. Lett. 2008. V. 92. P. 101911. https://doi.org/10.1063/1.2889474
Дополнительные материалы отсутствуют.
Инструменты
Неорганические материалы